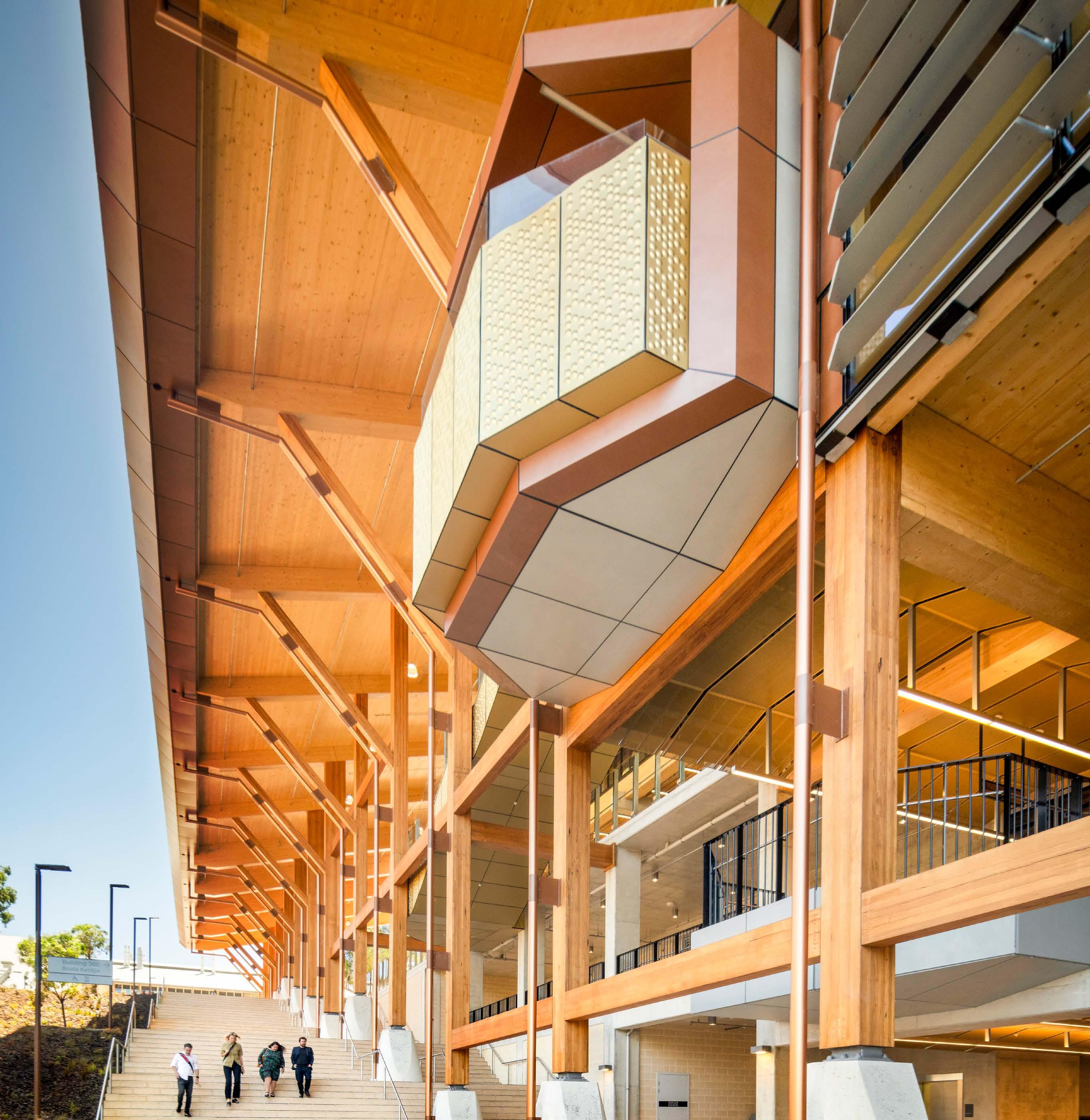

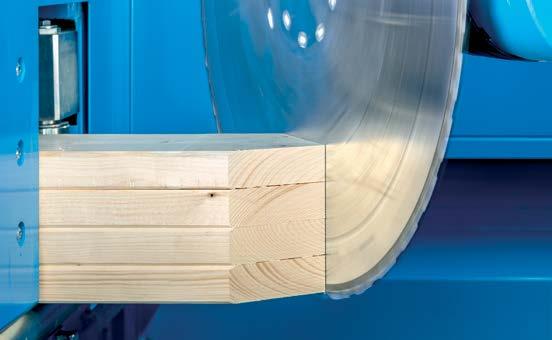
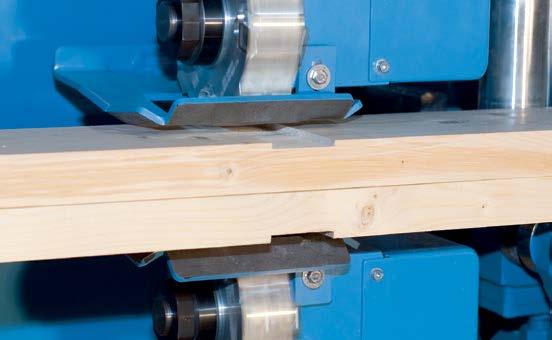
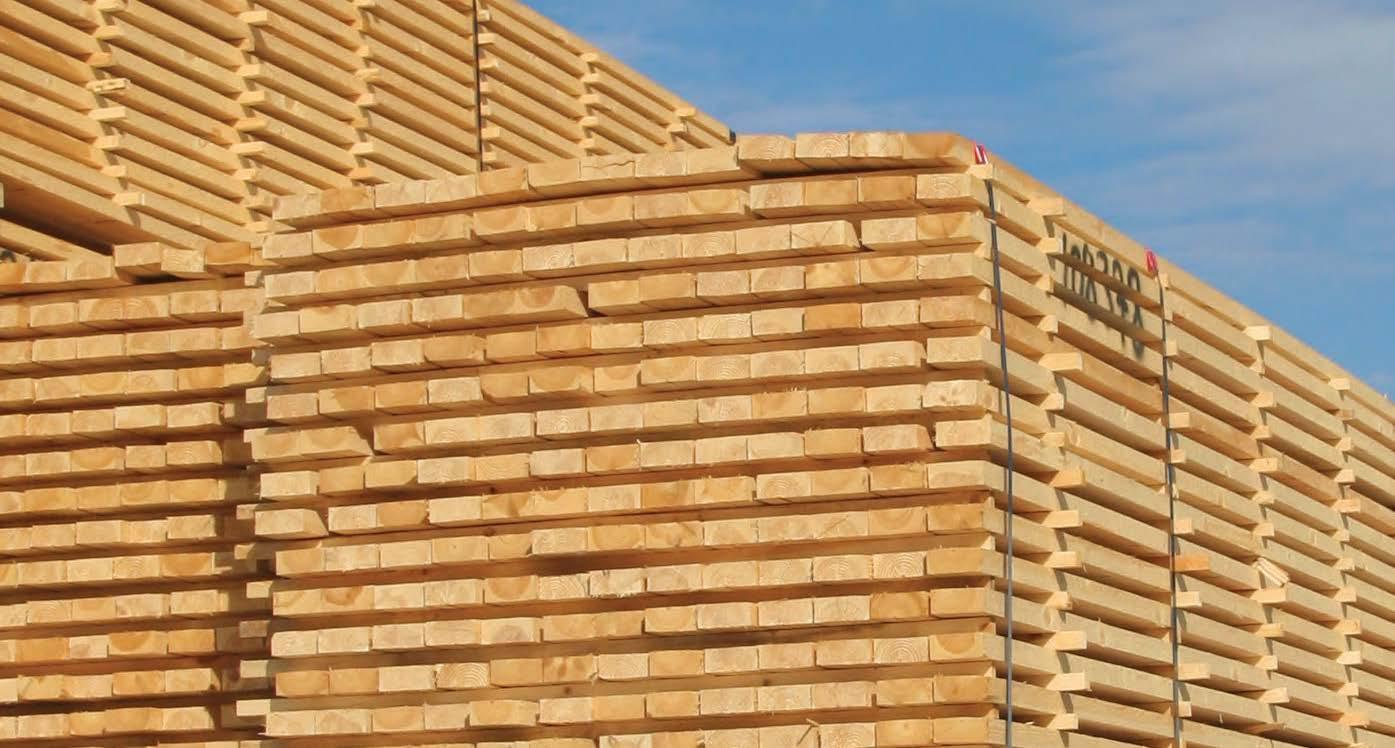
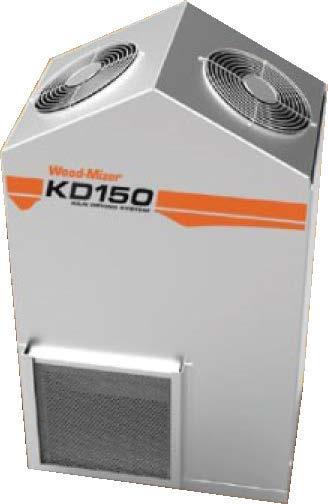


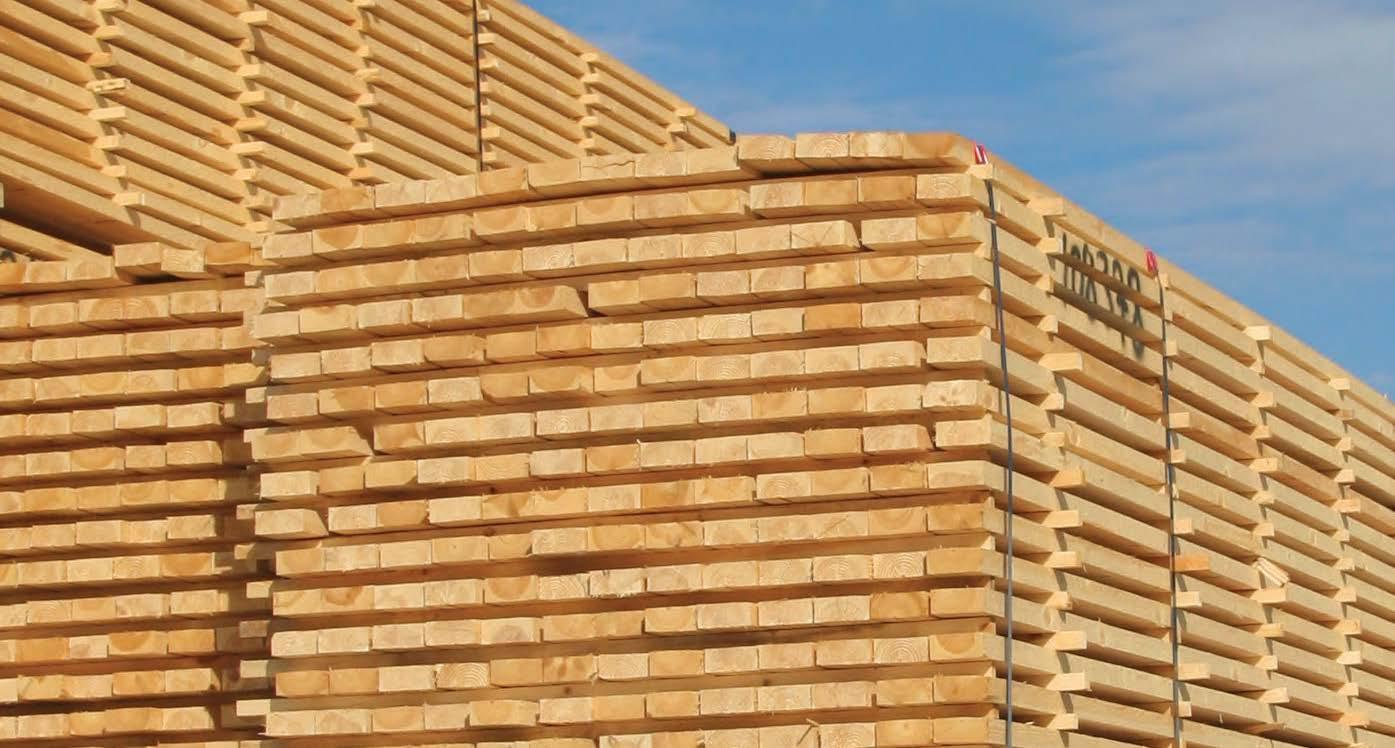
PHILIP HOPKINS
VICTORIA’S native forest industry has officially closed, but Radial Timber in Yarram is not going anywhere.
The company, which has been building its own plantation estate for about 18 years, was relying on timber from VicForests for another six years until its own supply was ready to harvest.
Now, it’s in survival mode.
“We’re looking to source what local plantation material we can get – we’ve got two signed up at the moment and one should be starting to harvest,” Radial’s managing director, Chris McEvoy, said.
“These are managed blue gum plantations planted in the late 1990s - almost 25plus years old. They have sawlogs 40-45cm in diameter - small end- so that will be the first material that will go through our Radial mill for over 14 months, so that’s one thing.
“We are also sourcing a few plantations in southern NSW – not the land but the timber. They are not quite ready yet, but they will be ready before our own plantations.”
Mr McEvoy said Radial was making plans due to the shut down six years earlier than planned.
“We have to try to get by and survive for the next six years. Our Radial mill will be running at 25 per cent capacity. We can run it that way for the next six years; our own timber will come on board by 2030,” he said.
“That is enough to keep the doors open, but it has given us the ability to look at a lot more innovation. We have been pushing hard.”
Radial began establishing hardwood plantations on planned 30-year rotations in 2004. The plan is still to make the business self-sufficient in the long term. The new plant, which uses radial cutting technology, has now been operating for more than five years. Radial sawing cuts a log like a cake, which creates less waste and processes smaller logs than conventional sawing.
In the interim, in the absence of larger logs, Radial
will concentrate on its new peeling plant and its bioenergy plant, which operates by pyrolysis.
“That’s burning timber waste in zero oxygen; it produces biochar, but also heat and energy. That plant is being installed now and should be commissioned this year,” he said. “We are also looking at, beside heat, energy and biochar, a thing called ‘wood vinegar’. It’s interesting – an extract from pyrolysis oils used as an organic herbicide replacement for Roundup. This is the new bioeconomy - refining wood fibre products into other products.”
A small log line is part of the peeler plant, which can peel a small log down to a 20-30 millimetre core – basically down to a broomstick. This process has a 60 per cent recovery rate, unlike traditional sawlogs at 30-35 per cent. The round log is peeled into veneer sheets, dried, glued and pressed. This engineered timber can theoretically be
used to make mass panels.
Mr McEvoy picked up a piece of timber a metre or so long with a moulded groove down one side. “That is the future of Radial. It’s nice and solid, yellow stringy bark, plantation grown, 12 years old. It’s potentially manufactured from a tree in the forest, to a round logs, to a peeled log to dried veneer, to pressed veneer to moulded product within 24 hours,” he said.
“We peeled it, dried it and sent it to Queensland; they pressed it, sent it back here; and we moulded it. It does not look like manufactured timber.”
This technology enables Radial to make laminated veneer lumber (LVL). “I’ve always been interested in LVL, but LVL is still a commodity product from overseas that is generally softwood. Could we value add more? We already have a cladding market; people want long cladding, and we can’t supply it. But we have lot of ‘thinnings’ from
NO jarrah or karri will be commercially harvested in Western Australia under the new Forest Management Plan although some timber will still be available from mine site clearing and ecological thinning for forest health.
However at this stage quantities are unknown and the State’s plantation area is declining.
The State’s forestry industry is now looking towards a restructured future to meet the community’s demand for timber and timber products.
While the State Government’s decision to end native forestry does not align with State or Federal carbon targets or sustainable forest management objectives, according to Forest Industries Federation WA (FIFWA) Chief Executive Officer Adele Farina, the industry is firmly focused on the future.
“We have made it abundantly clear that we disagree with the State Government’s decision to end native forestry, however our industry is doing what it does best, and that’s focusing on meeting the ever-increasing demand for timber and timber products, albeit in an altered environment,” Ms Farina said.
our plantations. If you can get a product out of 12-15-yearold plantations and turn it into this,” he said, indicating the timber).
“Our lathe is 3.2m wide; what we are thinking is, we could do an end-matched cladding in set-length packs.
In a one-storey place, use the three-metre pack; if two storeys, use two together and that’s six metres. We already have the customers, we don’t have solid wood anymore, we have engineered timber.”
Mr McEVoy said Radial would not be competing with pine LVL, which would need to be treated to become a cladding product.
“We have access to a lot of timber. We thin at six and 12 years - our final thinning is at 12. If that can go into a product – we might decide - why grow trees for 30 years? Why not do three rotations over 36 years?” he said. Continue
“We face a restructured future, there is no doubt about that, but we remain passionate advocates for the active management of our forests and the expansion of the plantation industry.”
Ms Farina acknowledged it had been a difficult period since 2021 as many businesses operating within the native forestry sector had to close their doors.
“It has been painful, there is no denying it,” Ms Farina said.
“We do not want that pain made worse by seeing our forests suffer as a result of neglect, which is why our ongoing objective remains as it was, to see healthy forests and sensible management, with timber sourced from sustainable management practices.
“For a low carbon future, ensuring we have an adequate supply of sustainably sourced local timber rather than increasing imports, is vital.”
Issue 1 – Volume 33
Incorporating Australian and New Zealand Timberman. Established 1977.
News 3-8
Training 10
Flooring 14-15
Associations 17-18
FRONT Cover:
The exterior of Boola Katitjin at Murdoch University in Perth, the first large-scale mass engineered timber building in Western Australia and winner of the 2023 Australian Timber Design Award for the best Engineered Wood Product Project.
Page 6
PUBLISHER and Chief Executive: Hartley Higgins
General Manager: Robyn Haworth
Editor: Bruce Mitchell
b.mitchell@ryanmediapl.com.au
Adelaide Office (08) 8369 9512
Advertising: Jon Andryciw j.andryciw@ryanmediapl.com.au
Adelaide Office (08) 8369 9517
Creative Services: Sudapa Rattanonda
Publication Design: Sudapa Rattanonda
Timber classifieds: j.andryciw@ryanmediapl.com.au
Adelaide Office (08) 8369 9517
Subscriptions: subs@forestsandtimber.com.au
Adelaide Office (08) 8369 9522
Subcription rates
One-year (8 editions) $59.50
Two-years (16 editions) $103.50
Accounts: ar@winetitles.com.au
Phone: (08) 8369 9500
Postal Address: 630 Regency Road, Broadview South Australia 5083
Phone: (08) 8369 9555
Melbourne Office: Suite 2262, 442 Auburn Rd, Hawthorn VIC 3122 Phone: (03) 9810 3262
SEVERAL Gippsland hardwood timber processors have vowed to continue operating despite being barred from access to the region’s native forest.
The chief executive of the Victorian Forest Products Association, Deb Kerr, said the start of 2024 marked the end of harvesting wood fibre from Victoria’s public forests, but not the end of Victoria’s sustainable native hardwood industry.
“The Victorian government’s decision last May created chaos with some businesses across the native hardwood supply chain being forced to either close permanently or diversify their business,” she said.
“However, a small number of processors will continue
TIMBER processors in Gippsland are clearly a resilient lot.
Despite their access to native hardwoods being shut down by the State Government six years earlier that initially expected, some are battling on.
Some, sadly, have not survived. The white paper line at Opal’s Maryvale Mill in the Latrobe Valley, which relied on native hardwood residues and woodchips, ceased production last year.
It has been a case of diversify or shut down.
processing the native timbers that consumers love, sourcing this wood from private sources in Victoria, from other states and from overseas. Hardwood timbers are highly valued by consumers where appearance or durability are important purchase considerations, be it stairs, decks, windows, furniture, or external applications.”
In Gippsland, Australian Sustainable Hardwoods
(ASH) at Heyfield began importing hardwood timber from the US some time ago as the state government began restricting hardwood supplies from Gippsland forests. ASH, which employs more than 200 people, is going to import more US hardwoods to make up some of the shortfall.
Radial Timber in Yarram will go into ‘survival mode’, sourcing what local plantation timber it can get until its own plantations grow. The company, which has been growing its own plantation estate for 18 years, had been relying on timber from VicForests for another six years.
The Radial mill will run at 25 per cent capacity in the intervening six-year period.
The white paper line at Opal’s Maryvale Mill in the Latrobe Valley, which relied on native hardwood residues
and woodchips, ceased production last year, throwing 150-200 people out of work, but the company will still require timber for its packaging production.
Ms Kerr said she did not have full confirmation of how many mills had closed, but 11 mills in Victoria took compensation payments from the first round of exists before the May 2023 announcement that timber harvesting in native forests would close at the end of 2023.
“Some of those closing have drying stocks of timber that will last between one-tothree years. The full effects won’t be realised until probably 2026,” she said.
Ms Kerr said while the government had closed native forestry, Victoria’s forests still needed to be managed for the health and resilience of the forest.
Australian Sustainable Hardwoods at Heyfield began importing hardwood timber from the US some time ago.
In 2017, Australian Sustainable Hardwoods at Heyfield lost half its Vic Ash volume, which gradually diminished further to only three per cent of its supply in 2023.
ASH, which employs more than 200 people, now imports US hardwoods to make
up some of the shortfall.
In Yarram Radial Timber has gone into ‘survival mode’, sourcing what local plantation timber it can get until its own plantations grow.
The company, which has been growing its own plantation estate for 18 years, had been relying on timber from VicForests for another six years. The Radial mill will run at 25 per cent capacity in the intervening six-year period and will concentrate on its new peeling plant and its bioenergy plant.
However, it is the small op-
erators - firewood, fence post and specialty timber cutters –which will be shut down.
Fifty licensees were told last May they had until June 30 this year to wrap up their operations. But court action scuttled that plan.
The early phase out means about 500,000 tonnes of windblown trees will be left lying on the Wombat forest floor, despite warnings it is a ticking fire bomb set to engulf nearby towns.
AUSTRALIA began construction of just 23,058 new houses in the September Quarter 2023, the weakest quarter in over a decade and down by 21.6 per cent on the same quarter last year.
The ABS in January released its building activity data for the September Quarter 2023. This data provides estimates of the value of building work and number of dwellings commenced, completed and under construction across Australia and its states and territories.
The data reveals there were 103,707 detached houses that commenced construction in the twelve months to September 2023, down by 17.0 per cent on the 124,940 commenced in the previous twelve-month period.
“This points to a slow start to National Cabinet’s ambition to build 1.2 million homes over the next five years start-
ing mid2024,” HIA Senior Economist Tom Devitt said.
“Since the RBA’s first cash rate increase in May 2022, sales of new homes have tumbled. A number of earlier projects are also being cancelled, with banks withdrawing finance in the face of soaring building costs and shrinking homebuyer borrowing power.”
He said this lack of new work entering the construction pipeline was expected to produce a trough in new house commencements in 2024, when Australia will start construction on just 95,400 new houses, the weakest year in over a decade.
There was also a decline in the number of multi-unit projects commencing construction, down by 9.6 per
cent in the September Quarter 2023 to just 13,916, one of the weakest quarters in over a decade.
“Multi-unit commencements are mounting a recovery on the back of population growth and land constraints, with Australia expected to commence 84,400 new multiunits in 2024,” Mr Devitt said.
“This would still put total detached and multi-unit commencements at less than
180,000 in 2024, far below the 240,000 per annum required to meet National Cabinet’s target.
“As fewer new projects begin construction, the pipeline of work that Australia’s home builders have under construction is expected to shrink rapidly this year,” he said.
“Meeting National Cabinet’s target will be largely dependent on the delivery of ade-
quate private housing across the housing continuum. This will also have the biggest impact on the cost of housing and rental availability.
“Holding all levels of government to account for improving planning regimes, reducing red tape, and supporting the development of appropriate infrastructure and a skilled construction workforce, must be a priority this year,” Mr Devitt said.
Experience the perfect synergy of technology and craftsmanship with Cheyenne brush sanders, enhancing timber aesthetics by highlighting wood grain for a rened, unique appearance. Complementing this, the Apache range of flow coaters from Sarmax, introduces unparalleled precision to coating processes Suitable for various timber profiles and coatings, Apache flow coaters are designed to optimise time and costs, ensuring optimal efficiency and a perfect application. Get in touch with our team today on 1800 077 862. shes with d geofflow
BOOLA Katitjin for Murdoch University in Perth is the first large-scale mass engineered timber building in Western Australia, and it has been described as a skyscraper, just on its side.
Boola Katitjin, which means “many facets and many levels of learning” in the Noongar language, is a 180m long, four-storey, 16,000sq m timber building constructed from glulam and cross laminated timber sourced from sustainable suppliers in Australia that accommodates up to 60 per cent of the university’s teaching requirements.
Last year it racked up a host of awards including the 2023 Australian Timber Design Award for the best Engineered Wood Product Project as well as the People’s Choice Award.
A total of 1,500 m³ of glulam was delivered including some of the largest glulam beams in all of Australia, measuring 26 m in length and weighing over 7 tonnes each.
The building also leads in environmental sustainability with solar panels, stormwater harvesting and active design features that mean it can operate on 100 per cent renewable energy.
Laminated timber beams and columns are used in conjunction with cross-laminated timber floor panels, to utilise plantation-grown timber as a replacement for traditional concrete and steel structure for the majority of the building. With its lower carbon footprint and increased opportunities for natural ventilation, the timber structure contributes to the environmental sustainability of the building and will receive a World Leadership 6 Star Green Star rating.
Murdoch University required design for disassembly for Boola Katitjin, in line with circular design principles, to reduce waste at endof-life. Circular, sustainable approaches included:
• Standardised sections/ sizes were used and each connection uses a simple bolted/ pin connection, meaning members can simply be disassembled at the end of its life and re-used elsewhere,
• 93 per cent of construction and demolition waste was diverted from landfill during construction and any waste/offcuts were repurposed as wayfinding signage.
Aurecon was also engaged by Murdoch University as
their Innovation Partner to deploy a fully autonomous robot as a trial to install screw fittings in the building – a world-first achievement.
The deployment of robotics on Boola Katitjin was led by Aurecon, leveraging an Aurecon Design Academy research thesis on robotics in timber construction.
The world-first robotics technology trial was used to install up to 100 timber screw
Architect: Lyon Architecture
Structural Engineer: Aurecon
Builder: Multiplex
Fabricator: Hess Timber, Xlam Dolomiti
Photographer: Aurecon, Lyons, Multiplex
Sponsors: Design Pine4, Pentarch Forestry
Location: Perth, WA
fixings as part of a proof of concept. There were between 200,000 and 300,000 screw fixings required for Boola Katitjin which is an important, but labour-intensive task.
The robotics trial, a collaboration between Aurecon, Murdoch University and the University of Technology Sydney (UTS), aimed to determine if automation of some on-site construction activity would
help to increase productivity and drive efficiency of the construction programme, thereby reducing cost. Importantly, the trial aimed to demonstrate how workers’ OH&S could be improved, and advance innovation in the construction industry. The modular nature of timber construction particularly lends itself to the automation of some construction processes.
THE next World Conference on Timber Engineering will be held in Brisbane in 2025.
The WCTE is the world’s leading scientific forum for the presentation of the latest technical and architectural solutions and innovations in timber construction. It is considered the most prestigious international event in the field of timber technology for construction, timber structures, and the design of timber architecture.
WCTE 2023 was held in June in Oslo, Norway and at-
tracted over 850 delegates.
WCTE 2025 will offer the Queensland and Australian industry an opportunity to showcase Australia’s research and development status and expertise in timber product design and durability. Additionally, it will serve as a significant platform for networking with internationally recognized research groups across various timber design and research fields.
WCTE 2025 will also present as an opportunity to highlight the advances and carbon benefits of timber
construction, particularly for Queensland Government Stakeholders as they plan the 2032 Olympic venues and athlete accommodation.
Submissions are sought for both oral and poster presentations, which must address the principal conference theme of Advancing Timber for the Future Built Environment.
The WCTE 2025 technical program will have a focus on the importance of research and development undertaken by the timber design and construction community in
response to the increased demand from engineering and architectural firms, developers and investors, now emphasising timber engineering as a preferred solution for many projects.
WCTE 2025 themes:
• Material Performance & Durability
• Sustainability and Timber in a Circular Economy
• Timber Engineering & Structural Performance
• Timber Architecture & Biophililc Design
• Education, Innovation & Challenges
• Exemplars & Construction Case Studies
Abstract submissions are invited on the above themes in the focused areas of:
1. Architectural Focus
2. Engineering Focus
3. Practitioner Focus
The submission deadline is 30 April 2024.
The University of Queensland, along with the support of the ARC Advance Timber Hub, will host the conference from 22 June 2025 to 26 June.
AUSTRALIA has seen a steady build-up of timber in timber yards across the country because the country is not making progress towards those housing targets, according to Australian Forest Products -Association NSW chief executive James Jooste.
Slow release of land, slow approval rates for loans and houses and economic factors including high interest rates have all had a major impact on timber supplies for some months.
“What’s emerged is we’ve got these ambitious targets, that we need housing, yet we’ve got timber sitting in mills, which is an indicator that that things are moving,” Mr Jooste said.
“It came on very quickly. It was probably predictable
once we started to see those rate rises kick in.
“But was it sharp? Absolutely.
“We need a roadmap and a steady plan for how we’re going to get to these housing targets, we need to make sure that we get out of these boom and bust cycles for the industry, because we’re seeing significant capital investment being made by mills.
“The timber industries continues to be a strong employer of local workers in our regional areas, in our manufacturing areas, in the downstream employment that created our construction sector, but in order to retain those workers, to enable a steady platform for business investment, and for that capital investment, we need to make sure we have a steady increase in the housing con-
struction market, and not go back to these boom and bust cycles,” he said.
AKD Softwoods chief executive Shane Vicary said the company’s Tumut mill at Tumut was processing 500,000 cubic metres of logs but that had fallen to 250,000 cubic metres.
AKD is the largest sawmill company in the country, producing about a quarter of the nation’s timber consumption.
“This mill is doing half the volume that it used to do, and it’ll do half for the next 20plus years, based on the fact that those logs got burnt,” Mr Vicary tole The Australian recently.
Despite this dramatic reduction in production, timber continued to sit on the shelf without being sold, he said.
“We can’t get enough peo-
ple to buy the timber,” he said.
“At the moment, most of our employees are earning less because there’s less activity: we’ve got overtime bans, we’ve got employment freezes.”
The federal government has previously laid out ambitions to build 1.2 million new homes in the next five years but NSW Premier Chris Minns has already admitted the state would not meet its target this year.
Mr Jooste said that New South Wales carried the lion’s share of the of the housing construction industry.
“So, we feel the boom and bust cycle because as a state, we’re most exposed to it.
“But these handbrakes that have been put on the economy are nationwide, and those timber mills, across the coun-
try will all be seeing a similar picture, as we are in New South Wales.
“So what’s the circuit breaker going to be?
“We’ll have to wait and see what the Reserve Bank and others do.
But we need to make sure we continue to keep a focus on fixing, working hand-inhand between local government and state government around how we’re getting the planning process right.
“And we’ve got to give credit to the state government in New South Wales for doing that and identifying those issues, and then making sure we have a stable business and operating platform for our meals to continue to produce the timber that we rely on.”
Automate for speed and efficiency to eliminate labour shortage problems.
The manufacturing world we live in now post COVID-19 has seen international setbacks and problems with delays in importing and increases across the board in prices of goods. Australia has also seen a growing problem with shortages in labour, causing further delays in local manufacturing. This poses great challenges for the economy as a whole, but also for individual businesses. Producing economically while maintaining quality standards is becoming a real challenge for many businesses. One solution to this problem is to expand the automation of individual work processes or entire production lines.
The BeA Group, headquartered in Germany, with APAC headquarter in Sydney and warehouse in Brisbane, Sydney and Melbourne, offers excellent automation solutions. BeA partners with local and world leading automation specialists in timber construction and wood processing, to provide tailored automation solutions across the entire production line in industries such as furniture, production of pallets, house frame and truss, and windows and doors and like manufacturing. With its „Autotec“ division, the BeA Group is one of the world‘s leading manufacturers of equipment for automated production. In this field, BeA cooperates with the world market leaders for wood processing equipment and is a reliable partner with over 100 years of competence and know-how in this field. Autotec equipment is available in a wide variety of versions and for almost any application. Should a very special solution be required, BeA can also offer special solutions with its internal engineering department.
Phone: 1300 232 287 or +61 438 841 708
Email: apac@bea-group.com
www.bea-group.com
Borg Manufacturing is seeking council approval for multi-million-dollar alterations and additions to its existing timber processing facility in Mount Gambier. It includes a warehouse expansion, an automated panel picking and packing line, a MDF moulding processing and painting equipment, a Joinery product shelving line, additional laminating, cut to size and paper treatment equipment and an automated strapping and particleboard flooring processing line.
Albioma has purchased the Tuan wood pellet plant in Queensland.
The plant, which has been in operation since 2014, produces 60,000 tonnes of highquality wood pellets each year.
The transaction also includes a 35,000-tonne storage facility in the port of Bundaberg and a 57 ha site in South Australia, near Mount Gambier, for a prospective wood pellet plant that could produce 300,000 tonnes per year. A construction permit has been secured for the site.
The Egger Group has acquired a 25.1% stake in the Thai wood-based material manufacturer Panel Plus. The purchase agreement was signed on 30 Nov 2023 and the closing took place on 3 Jan 2024. The parties have agreed not to disclose the purchase price and further details of the transaction.
Metsä Group is currently considering the construction of a carbon capture facility at one of its pulp or bioproduct mills. This exploration is an extension of the work initiated in the spring, where Metsä Group and Fortum collaborated to study the capture of woodbased carbon dioxide and its potential applications in the chemical industry and hydrogen economy.
PHILIP HOPKINS
ASH at Heyfield is still open for business. With the closure of the native forest industry, the manufacturer has lost its cherished Victorian Ash timber, but the company is not panicking – it is in expansion mode.
Each month, thirty 40-foot containers carrying American hardwood from the country’s north-east arrive in Heyfield.
“We aim to be growing that,” ASH’s managing director, Vince Hurley, told the Gippsland Times/Express.
“It’s the prince of hardwoods – regarded as that everywhere, not just in the States. It’s the timber that everything is compared to, it’s why England conquered the world with their oak boats. Oak is the king that everything is compared to.
“It is a really good outcome; we import a raw material, a very basic raw material, and we manufacture in Australia – a bit un-Australian really, isn’t it? - importing a raw material and manufacturing it in Australia?” he quipped.
Mr Hurley said ASH had branded the timber ‘Glacial Oak’.
“The reason is, the wood is extremely consistent and blond in colour, it doesn’t contain any pink. Often pink oak has variations – and pink doesn’t sell,” he said.
“Glacial Oak has been one of our star performers and we originally started with Glacial Oak nearly four years ago, off the back of trying to grow a market, we actually started before we knew what was happening with the Victorian supply,” he said.
In 2017, ASH lost half its Vic Ash volume, which gradually diminished further to only three per cent of its supply in 2023. The dwindling supply prompted a strategic rethink in 2017, with a few aims: look after the company’s people, diversify the fibre input, have a greater emphasis on advanced manufacturing and tighten the supply chain to the end user.
“We had no relationships in the US – they couldn’t be developed overnight,” Mr Hurley said, so ties with US suppliers began in 2019. The company also targeted greater use of plantation hardwood from the Strzelecki Ranges that was available through HVP (previously Hancock Victorian Plantations).
“As it happens, we developed markets and products and a good supply of the US hardwood,” he said. With the government’s announcement in May to close the industry, ASH turbo-charged its US ties.
Trucks from the Port of Melbourne laden with the US timber arrive in Heyfield.
“We unload; we have an 85-tonne container forklift
we got it when we were exporting a lot, now we are importing a lot,” Mr Hurley said.
“We are using it (Glacial Oak) to supply the market we have developed and as a replacement for some of our Vic Ash as well. It has been really good in that space –staircases, windows, doors and furniture. We also have a new engineered flooring line; we’re also going to have an engineered floor made of it as well.”
It was important that the engineered floor match the ASH staircase.
“Home builds, interior designers involved - they want to match the stair with the floor, and now we have an exact match,” he said.
Mr Hurley emphasised this point.
“We are not importing something and re-selling it; we are importing raw product, manufacturing it in Australia as a finished product - not a sawn board, but as finished products,” he said. These included stair treads, stringers, stair rises, window styles, window sashes, door moulds, furniture components, kitchen bench tops and furniture tabletops.
“It’s a balancing act. Part of our solution is to ensure we have a good long-term growing company with access to a long-term certified supply of sustainable timber,” he said.
“These are private forests, but they are grown as forests.
That’s their business; they want it to be there forever. There are weekly auctions for wood – it’s a massive industry.”
Mr Hurley said the US hardwood all came from mixed hardwood forests selectively harvested.
Such selective harvesting meant ASH paid more for the timber than if the wood was from a clear-felled coupe.
“You’re effectively paying for social licence, to make sure you are looking after everything in the forest,” he said.
Mr Hurley said ASH had also developed shining gum plantation from HVP as a registered brand called ‘Plantation Oak’.
“We have developed a social housing solution that meets Victorian government objectives - somewhere that’s nice to live, not a concrete box; it has to be energy efficient, carbon positive, not concrete and steel but timber – carbon positive as it stores carbon. The housing can be deconstructed – it can be pulled down and put up elsewhere,” he said.
“It’s extremely cost effective to build, maintain and live in. Really importantly, we can construct these very quickly; they can go up threeto-four times faster than a concrete building. It’s a social housing solution.”
AT COP28 in Dubai the Australian Government, with 16 other countries committed to increase the use of timber in the built environment by 2030.
The Forest and Climate Leaders’ Partnership Coalition on Greening Construction with Sustainable Wood made the announcement yesterday.
“AFPA congratulates the Australian Government for signing up to this Coalition and its commitment today. Wood from sustainably managed forests provides climate solutions within the construction sector,” Natasa Sikman, Acting CEO of the Australian Forest Products Association said.
“This is an important step in the right direction by the Australian Government to build confidence in the timber construction market. We look forward to continuing our work with the Government on developing enabling policies which will turbo charge
a greater use of wood in the built environment.”
The 17 member Coalition, of which Australia is a member, has committed to advance policies and approaches that increase the use of wood in the built environment by 2030.
The Coalition recognises that such policies and approaches will result in reduced Greenhouse Gas Emissions and an increase in stored carbon.
“Ministers from Kenya and Costa Rica announced the need to increase the use of wood in the built environment in the race to net zero,” Ms Sikman said.
“Speakers made clear that the products from sustainably
managed forests have multiple benefits for the building sector, replacing plastics, and delivering positive outcomes for local communities.
“Sustainably managed forests also help protect nature and biodiversity from deforestation and the threats from climate change.”
The announcement builds on the recognition in the latest report from the Federal Government’s own Climate Change Authority (CCA) which cited the ‘carbon stored in trees’ as well as ‘harvested wood products’ helped reduce Australia’s greenhouse emissions in the year to June 2023.
This at a time when total national emissions increased to 467 million tonnes, an increase of 4 million on the previous year.
It is timely the Government has announced a commitment to ramp up the use of timber in the built environment.
AN Apprentice and Trainee Safety Committee has been set up by the South Australian Government with apprenticeship safety a key area of focus for 2024.
The Department for Education, in partnership with the Skills Commissioner spoke to more than 1700 employers to educate them on their responsibilities in relation to their apprentices and trainees, an increase of 3% on the previous year.
They also investigated 36 employers for non-compliance with their obligations, an increase of 29 from the previous year and imposed 18 sanctions upon non-compliant employers, an increase of 11 from the previous year.
The main types of non-compliances investigated in 2023 include:
• Failures to provide adequate and/or appropriate supervision, including issues associated with bullying and
harassment.
• Failures to release apprentices for training or to adequately progress them in their training, including not letting them attend off-job training and/or not providing on-job requirements.
• Failure to provide full scope of work to enable the apprentice to achieve competency across all aspects of
Skills, Knowledge, Performance
the trade or vocation, including issues with licensing.
The most common regulatory response is applying conditions to an employers registration.
Common conditions include requirements for the employer to provide evidence of appropriate supervision and/or training, to limit employers from taking
on new apprentices or hosting apprentices without a risk assessment by the department first, and ensuring the apprentice understands their rights and obligations and where to seek assistance if required.
Additional sanctions have included prohibiting an employer from employing apprentices and cancelling
their registration, suspending an employer’s registration, sometimes until further notice or specific compliance issues are addressed, and issuing compliance notices requiring employers to take specific actions to correct non-compliances.
South Australia skills commissioner Cameron Baker will chair the new committee, which will be made up of organisations that have responsibilities for oversight of apprentice and trainee training, safety and wellbeing, including SafeWork SA.
The committee will work to ensure additional quality onjob training and safe workplace initiatives for the state’s over 28,000 apprentices and trainees, and they will begin work in March. It will also include representatives of those who will be impacted by the work providing an avenue for direct guidance from apprentices and trainees.
IN the pursuit of workplace safety, ensuring compliance with hi-vis workwear standards is paramount.
Certificates II, III and IV
Wood Machinist s Saw Technicians
Sawmilling, including portable sawmilling Grading
Timber Drying
Truss Fabrication and Design
Forest Operations
Forest Prod uct s Diploma
Workplace Assessment s
OH&S and Environmental Care
Chainsaw Courses
Pole saw
SES and Fire Ser vicesChainsaws, Rescue Saw, Pole Saw
For Course Programs 03 5345 2018
www.timbertrainingcreswick.com.au
RTO ID 4168
Employers bear a moral and legal responsibility to safeguard their workforce, with adherence to these standards being not only imperative but a legal requirement.
Non-compliance, as reported by Safe Work Australia, has been a contributing factor in over 300 workplace fatalities and numerous injuries over the past five years alone.
In high-risk settings high-visibility workwear serves as the first line of defence for workers.
Total Image Group (TIG), renowned for its expertise in branded uniforms, understands that when applied effectively, this workwear becomes a crucial component of workplace safety. Its proper implementation not only averts minor mishaps but also plays a pivotal role in preventing catastrophic incidents.
Whether you are an employer, an employee, or a safety professional, TIG has assembled a thorough checklist to assist you in crafting and procuring high-visibility workwear that aligns with the Australian standard - AS/NZS 4602.1:2011.
Key considerations when designing Hi-Vis workwear for safety include:
1. Industry and Context: Understanding the specific industry and context is the foundation for designing a safety-
oriented uniform range. Varying safety requirements exist across industries, and uniforms should be tailored accordingly. For instance, construction sites necessitate high-visibility clothing for visibility, while healthcare settings require materials that withstand frequent, high-temperature washing.
2. Material Selection: The choice of materials directly impacts safety. Consider flame-resistant fabrics for those dealing with open flames, while moisture-wicking materials are crucial for high-temperature environments. Materials should prioritise comfort, allowing for ease of movement, breathability, and temperature regulation without compromising safety.
3. Visibility and Reflectivity: In low-visibility environments, such as construction zones, incorporating reflective elements is essential. Strategic placement of reflective tapes or patches enhances visibility in lowlight conditions, mitigating the risk of accidents.
By considering these factors, organisations can create uniforms that not only reflect their identity but also prioritise the well-being and safety of employees. Balancing safety, functionality, and aesthetics is the hallmark of a successful uniform design, fostering a secure and comfortable work environment.
For further information on how to acquire compliant branded workwear visit www.totalimagegroup.com.au
Mandy Parry-Jones
FORWARDS, backwards, sideways the Combilift CUBE will even dance an Irish jig, which the company proved during a demonstration at its manufacturing facility in Monaghan, Ireland.
Immediately noticeable though is the new vibrant colour on the CUBE, a brighter green than the traditional Combilift green. It is intended that this bold Combi-green will contribute to improved safety as the forklift will be easily visible in an operational environment. Aside from being more noticeable in its new garb, the CUBE features a number of refinements some in the cabin and some under its skin.
Inside the cabin the driver’s position in the centre of the cab offers generous room and excellent all-round visibility. The angle of the telescopic steering column can be adjusted and the Grammer MSG65 seat,
combined with hydraulic cabin mounts guarantees a comfortable ride. An adjustable arm rest is mounted to the seat suspension which incorporates a multi-function joystick and an LCD colour touch screen.
The CUBE’s swivel seat automatically swivels 15 degrees to the left or right with the selected direction of travel to maximise driver visibility and reduce strain when travelling in reverse.
This bright green little machine is a mighty versatile counterbalance forklift that is made for confined spaces as it can drive right and left as well as forwards and backwards so any aisle even those that are very narrow is easy to navigate.
In other small forklifts the wheels of the truck turn while it is stationary which causes the tyres to wear prematurely but the Combi-CUBE has the problem solved with its dynamic 360-degree steering system, which was introduced
first on the Combi MR4.
A joystick control in addition to the steering wheel enables the driver to change direction while the forklift is moving, so it takes less time and less rubber.
Martin McVicar Combilift Managing Director described it as a hovercraft.
“It very much operates like a hovercraft that can pretty much manoeuvre in all directions without having to stop and change wheel positioning,” he said. “You may wonder why we call it the CombiCUBE … it’s almost a cube in shape it’s the same length and width.”
This is a surprising agile forklift and with its 3-tonne lifting capacity the CUBE can handle a large number of different warehousing operations, add to that a wide range of mast types that provide lifting from four to six metres and it’s a handy employee.
The Combilift range of multidirectional forklifts and pedestrian reach trucks will allow you to maximize the storage, efficiency and safety of your warehouse when handling timber
ACHIEVING New Zealand’s net carbon zero goals by 2050 requires looking at every aspect of life – even the roads New Zealanders drive on.
And work that Waka Kotahi New Zealand Transport Agency is doing with support from Scion and other industry partners could help bridge the gap between where New Zealand is and where it needs to be by 2050.
Waka Kotahi chief engineer Sulo Shanmuganathan says the organisation’s vision is for a low carbon, safe and healthy land transport system and Scion’s knowledge about the durability and longevity of Glulam – glue laminated timber made by gluing layers of boards together –has been key to informing the timber bridge pilot and helping achieve its wider vision.
Scion’s Tripti Singh and Dave Page advised Waka Kotahi on the durability of preservative-treated Glulam in New Zealand. Preservativetreated, radiata pine, glue laminated bridge beams have been in service for 60 years in New Zealand and show few problems with durability associated with decay.
Shanmuganathan says these findings gave Waka Kotahi confidence in Glulam and the ability to press ahead with its wooden bridge pilot.
“Long term we want to see Glulam readily available and designers capable of using the product and timber like they use other conventional materials. Raising awareness in the sector for designers and construction is crucial for us as we transition to a low carbon, climate resilient transport system that will create a better tomorrow for us all,” she says.
A timber bridges focus group has been formed with Scion, the Scion-managed Timber Unlimited brand, Timber Design Society, and government ministries.
THE Centre for Timber Durability and Design Life at the University of the Sunshine Coast recently initiated a cooperative project with Forest and Wood Products Australia, supported by a consortium of timber producers, chemical suppliers and timber users to identify alternative pathways for treated timber and engineered wood products.
The overall goal is to identify environmentally and economically sound opportunities for reuse/recycling treated timber and EWP.
Preservative-treated timbers and wood-based composites have low embodied carbon and renewability, but become problematic at endof-life because of the biocides and resins they contain.
Many authorities require these materials be transported under stringent regulations, restrict disposal in landfills and impose higher disposal costs.
These issues are driving timber users to examine alternative materials such as steel or plastic that have much higher overall environmental footprints.
However, a number of potential strategies for reuse/ recycling of treated timber and composites could markedly reduce volumes going to landfill while providing novel products. These strategies would fit well within the growing concept of the circular economy.
The circular economy has many aspects, but essentially
it tries to ensure that materials are designed for long service life with minimal environmental impact and that they can be repurposed at their end-of-life.
Timber should be an ideal candidate for the circular economy, but there are many unknowns in relation to repurposing chemically treated materials.
What the project will do:
• Establish current volumes, forecast future volumes and determine geographic distribution of the different treated timber/ EWP’s entering the waste stream,
• Assess condition of material in terms of residual chemicals and potential for reuse/repurposing,
• Identify local, state and
federal regulatory hurdles that affect transport and reuse options,
• Develop models to estimate transport costs for specific products across the country,
• Hold a Reuse Strategies Scoping and Assessment Summit with invited international experts to identify the most appropriate reuse/ recycling strategies based on global experiences but framed in an Australian context,
• Develop a program that uses material characteristics, volumes, and location to identify the most attractive reuse options for a given treated timber/EWP in a specific geographic area,
• Develop a small-scale reuse/recycling program
with one treated timber/EWP product to assess feasibility of the approach and explore the logistical hurdles
What the project expects to deliver:
• What treated timber/ EWP materials are being disposed of across the country by location,
• The condition of the treated timber/EWP materials in terms of reuse/recycling,
• The most appropriate reuse/recycling options by product and location,
• Whether a “take back” program is feasible with at least one treated wood product.
For more information or to participate in the project, contact Professor Mark Brown at mbrown2@usc.edu.au
TIMBER Unlimited, TDS, SESOC and CLT Toolbox (Australia) have teamed up to develop NZ-specific design software that will make it easier to carry out structural designs in accordance with the new Standard NZS AS 1720.1:2022 and international best practice for mass timber, engineered wood products and connections.
The announcement comes hot on the heels of CLT Toolbox announcing in October that the first tranche of their software offering relevant to designers within the Austral-
ian market was launched. One of the long-standing obstacles to making it easier to choose and use more timber in the built environment has been the steep learning curve required to understand the required design methods and material-specific properties of timber to carry out robust member and connection design confidently and on time.
The new, New Zealandspecific part of the software is presently under development through this collaboration will provide a new suite of design tools and local sup-
plier grades and sizes, facilitating efficient design to the latest Standards.
A very important additional feature will be the inclusion of the CLT Toolbox core principle of “embedded learning” – the calculators are not presented in the all too familiar “black-box” format, meaning that you get outputs without knowing what formulas or Standards were used; rather, the calculators and routines identify the expressions, factors and Standards being applied so it’s easy to identify the basis and relevance of the calculated outputs.
Timber Unlimited has also teamed up with the NZ Timber Design Society (TDS) and the Structural Engineering Society NZ (SESOC), who will assist with the review and validation parts of the programme. It’s the power of this four-way collaboration that will help unlock the benefits of timber to the New Zealand design and specification community and make it easier to use more timber in the built environment.
The target is to have NZrelevant part of the software available to NZ designers by the end of April 2024.
THERE are many benefits to drying your own timber. First of all, properly dried timber typically sells for more than 30 percent higher than prices for green timber.
Kiln-dried timber is also better to work with: it machines better, has more holding power when glued together, finishes easier, and nails and screws have higher holding power in kiln-dried timber. In addition, dry timber weighs more than 50 percent less than green timber and is more than twice as strong and stiff.
Plus, timber dried to below 22 percent moisture content has no risk of developing fungal stain, decay, mold, or rot, while kiln-drying kills infestations, hardens pitch, preserves color, and controls shrinkage.
Timber that is not dried under controlled conditions in a kiln is prone to warping and other degrade that diminishes its selling price and workability.
Air-drying timber — relying on the sun and a natural breeze — has numerous drawbacks. Air-drying poses real problems with damage and degrade and is often the most expensive way to dry timber once you include interest on material investment, labor, land costs, and especially loss from timber degrade. In addition, for timber that will be used in furniture or some other finished product that requires drying to 6-8 percent moisture content, air-drying is not sufficient.
Kiln-drying, with the timber placed in a chamber, allows control of air flow, temperature, and humidity in order to dry the wood as rapidly as possible without increasing defects. There are several types of kilns. However, solar kilns and dehumidification kilns provide many benefits with only a low investment. Wood-Mizer offers kits for solar kilns and dehumidification kilns to make drying timber easy, affordable, and
profitable for virtually any size company.
Solar kilns generally rely on some type of solar collector to provide the heat energy that evaporates the water in the timber. Yet, drying times for a solar kiln still depend on the weather, so they are unpredictable. However, a solar kiln is very affordable for entry-level drying operations and often will pay for itself after drying just three or four loads of timber.
A dehumidification kiln uses a heat pump system to produce heat and remove the water from timber. One primary advantage of this type of system is that it recycles heat continuously instead of venting away heated air like a conventional kiln; a dehumidification kiln therefore is more energy efficient, and operating costs usually are lower. In a dehumidification kiln, heated air is circulated over the timber while separate circulating fans evaporate the water contained in the wood.
The hot, moist air then is cooled at a cold refrigeration coil, and the heat removed from the air is immediately used by the system to heat the air back up again. Dehumidification kilns are very easy to operate and are popular with beginning timber dryers as well as experienced operators who want a system that requires minimum attention yet produces kiln-dried timber with zero defects. Dehumidification kilns are more expensive than solar kilns, but they can
provide top quality kiln-dried timber year-round regardless of the weather. Also, the cost of operating a dehumidification kiln compared to the value added by drying timber often makes the return on investment nearly 20 percent or more.
Wood-Mizer offers dehumidification and solar kiln kits with capacities ranging from 300 to 35,000 board feet. For more information, visit www.woodmizer.com/ kilns.
KULUNI Millaniyage has always admired nature – both in a physical and literary sense.
A PhD candidate currently studying at the University of Tasmania’s Centre for Sustainable Architecture with Wood (CSAW) based in Launceston, Kuluni had previously studied a bachelor’s degree in forestry and environmental science and had worked in wood science and timber processing.
Following the completion of her bachelor’s degree at the University of Sri Jayewardenepura, Kuluni was employed for two years on a maiden project which processed pre-finished engineered timber flooring, from log to final product.
“The timber utilised was Sri Lankan Teak and I was in charge of conducting necessary testing, research, and development – as well as quality assurance of the production line,” Kuluni said.
“This experience inspired me to conduct my higher studies on timber product development, which brought me to this beautiful island of Tasmania.”
Kuluni’s research examines the potential of developing a new generation of Tasmanian engineered timber flooring products for in-state manufacturing and is part of a project headed up by Australian Forests and Wood Innovations (AFWI) – formerly the National Institute for Forest Product Innovation (NIFPI). The project
focuses on developing a new generation of Tasmanian appearance hardwood products.
Working alongside a research team at CSAW under the supervision of Dr Louise Wallis, Dr Nathan Kotlarewski, Dr Assaad Taoum and Prof Greg Nolan, Kuluni studies wood science and material properties aligning with the interests and requirements supporting Tasmanian timber industry.
“My research is focused in developing a novel engineered timber flooring product using Tasmanian plantation Eucalyptus nitens: a value-added application to the plantation forests.
“ short rotation plantation species can generate more return to plantation owners
"My research outcomes developed a number of prototypes using plantation timber in engineered flooring products with the potential for a future commercial reality,” she said.
Kuluni said that with access to native high-density timbers becoming challenging in Australia and globally, the timber processing industry now requires alternative timber resources to facilitate the increasing market demand and sustainable operations.
“Identifying value added applica-
• Kuluni Millaniyage works on new flooring development at Tasmania’s Centre for Sustainable Architecture with Wood.
tions for short rotation plantation species can generate more return to plantation owners and provide alternatives to the upcoming native log supply,” Kuluni said.
“As part of my doctoral degree, I was able to develop several engineered flooring prototypes which were subjected to testing in laboratories and in-service conditions. I have published three international journal articles based on the findings of my research.”
Further to this achievement, Kuluni was a recipient of the UTAS Vice Chancellor’s Innovation Award in 2022, for the contribution of research to incorporate Tasmanian solid timber flooring above heated floor slabs in the newly built River’s Edge building at Inveresk, as part of the Transformation and CSAW Pro-
ject Team.
Kuluni’s academic success and commitment to helping others saw her recently nominated by Study Tasmania as a finalist for International Student of the Year Award.
As a research scientist, Kuluni hopes to develop her career in the field of new product development using timber; something she believes will greatly benefit the Tasmanian timber industry.
“I believe that there is a significant requirement for skills and research in forestry and timber sector and I look forward to using my expertise to support this industry,” she said.
“The Tasmanian timber industry is keen on identifying value added applications to plantation E. nitens as this novel timber resource is currently available in high volumes."
From page 3
“There are still durability issues, weather issues, to test. However, it’s exciting from the point of view; we could grow trees as a crop and turn them into engineered product in a third of the time it takes to grow saw logs for solid timber. The beauty of engineered wood and veneers is, they are a lot more stable. They are also easier to dry; the LVL board does have glue in there, but there’s a lot of timber in there, not like plastic wood, which is 80pc plastic and some wood fibre; this is 90pc wood and 10pc glue.
“All at the mill are excited by the potential. To have the veneers working with our moulding
profile, physically it will look no different from our solid wood product. If that can weather like our solid wood product and maintain its durability, it’s great - we don’t have to start a new market, just convert people over.”
Financially, the company is relying on the compensation money that VicForests is paying because it cannot provide timber to fulfill its contract. Radial’s licence is for timber supply until 2024 but was extended by VicForests until 2030 under the original closure deadline.
Radial still produces its long, well-known ‘wavey’ boards.
“Again, it’s harder to get that resource – it’s generally a big big-
ger, native forest log. We have got some logs from interstate that will produce that,’’ he said.
The Radial group has 1600 hectares of plantations in total across 32 properties, all in South Gippsland and the Strzelecki Ranges. “The ultimate aim is 2000ha, which gives us a sustainable yield over 30 years repeatable. We have not got the whole 1600 planted yet – we still have some blue gums being harvested by others on land we own – and we need to buy a bit more land. I’m not sure that’s going to happen, with rural land being so expensive,” he said.
Mr McEvoy said land prices since COVID had doubled. “We were paying per ha $5000-6000
TIMBER strip flooring is a popular choice for its natural aesthetic and durability, but its success is contingent upon the stability and integrity of the underlying support structure.
Timber flooring underlay is the essential layer between the subfloor and the timber floorboards. Its primary purpose is to provide stability, insulation, and a smooth, level surface for the flooring to be installed upon.
Timber flooring underlay may not be the most visible part of your flooring project, but it plays a vital role in its long-term success.
Adhesion strength, the underlay’s ability to bond securely to the timber strip flooring, is a critical factor that can impact the overall performance and durability of your timber floor. By choosing a high-quality underlay and following proper installation procedures, you can ensure that your timber flooring not only looks great but also stands the test of time. Don’t underestimate the importance of this oftenoverlooked component in your flooring project – it’s the foundation that makes your timber floor shine.
ADHESION STRENGTH: THE BACKBONE OF A RELIABLE UNDERLAY
The adhesion strength of flooring underlay is of paramount importance when installing timber strip floor-
ing. Timber strip flooring, characterised by its elegant and timeless appeal, relies heavily on a stable and secure base for longevity and performance.
A strong adhesion between the underlay and the timber strips ensures that the flooring remains securely in place, preventing unsightly gaps, warping, and squeaks over time. Furthermore, a robust bond between the underlay and the timber provides ad-
• A high adhesion strength in the underlay preserves the structural integrity of the timber strip flooring.
ditional sound insulation and insulation against temperature fluctuations, enhancing the overall comfort and energy efficiency of the space. A high adhesion strength in the underlay not only preserves the structural integrity of the timber strip flooring but also contributes to its aesthetic, acoustic, and thermal qualities, making it an indispensable consideration for any successful installation.
pre-COVID; now it’s $10,000$12,000, and that’s in the Strzeleckis. Around Warragul, rich dairy country, it’s more like $20,000-25,000 per ha. We’re talking marginal farmland at $10,000 per hectare,” he said.
The Radial mill has a capacity to process about 10,000 cubic metres of timber a year. Mr McEvoy calculated that at a conservative average, the sustainable yield at the final harvest was about 150 stems per ha, with each stem about one cubic metre or one tonne. That’s based on a 40cm-diameter tree that is six metres long. With 150 stems over 2000 ha, that means
300,000 tonnes over 30 years, or 10,000 tonnes per year over 30 years.
“That’s a final harvest; it does not take into account peeling, LVL plant or biofuel,” he said.
With experience, Radial has changed its plantation model; the emphasis is still on durable hardwoods, but the species mix has grown from four to about six or seven - yellow stringybark, silver top, spotted gum, coastal grey box (class1), red iron bark, (“another class 1 from Gippsland”) and southern mahogany.
“We also do a lot more random establishment – still
STRUCTApanel H2 12mm panels provide a smooth, uniformly thick, solid base free of knots, voids or grain which means they can be bonded to timber strip flooring with a glue adhesive, which spreads easily and evenly over the panel surfaces for greater tensile bond strength and without any sanding required.
STRUCTApanel H2 12mm is a high-density particleboard underlay engineered to meet and exceed the demanding requirements of timber strip flooring installations. It is constructed with precision, using sustainably sourced materials, making it an environmentally responsible choice.
The key features of STRUCTApanel H2 12mm include its consistently flat surface with no internal delamination which gives it exceptional adhesion strength. When it comes to choosing the right underlay for your timber strip flooring, adhesion strength is a critical factor to consider. STRUCTApanel H2 12mm excels in this regard, providing the reliability and durability needed for a long-lasting and high-performing flooring system.
STRUCTApanel H2 12mm is Australian Made from sustainable certified plantation forestry, and easily sourced with strong sales support throughout our national supply partners.
TIMBERLINK’s decision to build its new $59 million state-of-the-art Cross Laminated Timber and Glue Laminated Timber manufacturing facility at Tarpeena in South Australia has been widely welcomed.
The facility - the first plant in Australia to produce both types of timber product - will built next to its existing mill which currently employees more than 200 people and contributes $150m to the local economy.
Construction is due to begin this year with a completion date of 2023. A site in Victoria was also considered for the project.
After 44 years with Hyne Timber, John McDonald -aka Macca -- has signed off for the last time. However, with an ongoing love of timber, his ‘timber turning’ pen hobby will now take precedence as he retires at the age of 60.
planting in rows but mixing up the species. We do internal R and D, to determine which species grow best with each other’ we try different permutations and combinations, and improve genetics, get seed, pick the best of the seed from trees, that’s important,” he said.
Nature had provided interesting lessons. “What we found – Darwin’s natural section showed us how forests work. The stronger survive and the weakest don’t. Also, it’s really good for biodiversity; there is no sterile monoculture forest. It’s similar to a mixed species native forest.”
• A close-up of Radial Timber's engineered plantation timber.
According to Hyne Timber’s CEO Jon Kleinschmidt, Macca was a valued member of the Hyne Timber team, a hardworking and incredibly organised mentor for the warehouse and customer service staff. “Macca has been with the business for over 44 years and I’ve enjoyed working closely with him especially during our time building and growing the Tuan Mill,” he said
Imports of wood products to Australia for the combined March and June quarters of 2012 were valued at around $2.0 billion, which is around the same value as the same quarters over the previous two years, according to ABARES in its Australian Forest and Wood Products Statistics report.
Historical data on the value of imports suggests seasonal trends, resulting in higher values of imports during the first half of most financial years.
WITH research proving our built environment has a significant effect on our overall wellbeing there has been a steady increase in the use of decorative timber in both commercial and residential spaces.
The materials surrounding us on a daily basis that offer a deeper connection to earth and nature, such as the natural beauty and uniqueness of wood are being embraced by designers for this reason.
While some building materials can look hard and cold, the warmth of timber brings a sense of nature and wellbeing into public buildings, and offers a certain luxury.
Materials and patterns mimicking nature can help achieve a sense of comfort and happiness, which is at the core of biophilic design.
Rather than a trend, architects are incorporating biophilic design as the next standard in commercial buildings.
By leveraging natural materials such as wood and stone, designers can achieve a sense of wellbeing and visual connections with nature without necessarily having outdoor spaces.
This can also be done by utilising organic and biomorphic shapes and forms, live plants, earthy textures and colours, natural lighting and ventilation.
“Commercial developers are not only looking for sustainable design, but an all-encompassing holistic approach to style and functionality, as well as health and wellness,” says Stuart McGonagle, Sales & Marketing Manager – Panels, at Big River Group.
“According to a recent study, those in environments featuring natural wooden surfaces, reported higher personal mood, clarity, confidence and optimism on average.
“In response to this, we are seeing a rise in the use of decorative timbers on walls and ceilings being specified as part of the design element to enhance the commercial and retail space,” he said.
“There’s a myriad of timbers with different textures and colours available, that can be utilised to improve the ambience of a venue,”
The natural visual appeal of timber in commercial and retail spaces aids in lowering stress levels, creating a healthier environment.
What’s more, due to its natural insulation timber reduces internal heat gain in summer and loss of warmth in winter, and can store and release moisture which help to regulate humidity and air quality in an indoor environment.
The extensive use of Big River Group’s own native hoop pine plywood for interior walls, ceilings and
cabinetry, provides a clean, natural look, and can merge interiors throughout a public space.
The premium decorative plywood is predominantly used in the commercial sectors and is popular with architects due to its warm, blonde varied tones with a clean grain and smooth texture.
Plywood ceiling and exposed timber trusses are a celebration of light, material and craftmanship, and are ideal for appearance and structural grade applications.
A stunning and smart choice for cabinetry and joinery applications that achieves a natural aesthetic is Big River’s ArmourCab, a new generation of engineered Australian decorative wood panelling.
Available in Blackbutt, Spotted Gum and Hoop Pine timber finishes, each with its own natural colour and markings, ArmourCab adds harmonious design and plays an important role in marrying the indoor and outdoor spaces.
Combining the stunning intimacy of native timbers with the rugged durability of a precision-engineered structural product, Big River’s Armourpanel is a decorative plywood and another popular choice due to its distinctly natural appeal.
“In maintaining the natural characteristics of the selected wood species, every Armourpanel sheet offers an individual and natural look, with
the species’ unique grain structures being preserved so no two sheets look alike,” McGonagle says.
Also available in a range of native species including Blackbutt, Flooded Gum, Spotted Gum and Sydney Blue Gum, its durability makes it ideal for use in hardwearing areas, including flooring, wall panelling, screening, cabinetry, ceiling linings and joinery.
The new Warrnambool Library and Learning Centre, in regional Victoria, designed by Kosloff Architecture, realises a vision to bring together education, community and the arts to the city.
With end user engagement the ultimate objective, Kosloff Architecture sought to ensure the dynamic new space incorporated expansive areas for research, study and socialising through a warm and inviting environment.
Drawing on the appeal of native timber, its striking interior elements work to fulfil this intention. Internally the incorporation of natural timber lends itself to a biophilic intent while instilling a sense of comfort and inclusion.
The interior is punctuated by a dramatic timber staircase, which leads up the three levels through a circular void, and has been clad in Big River Group’s premium plywood products ArmourPanel and Armourfloor in Blackbutt.
“The warmth of the Big River Blackbutt products with rich tones provides a sense of comfort and connection to
nature within the interiors of the project,” says Lance Van Maanen, Associate Director of Kosloff Architecture.
Setting the tone for a warm and inviting atmosphere, Big River’s decorative plywood products, Armourpanel and Armourfloor are also a popular choice for architects and builders in residential projects because of their durability, versatility and aesthetic appeal. Project 12 Architecture was recently commissioned to transition a muchloved double fronted heritage listed Victorian terrace, into a generous inner-city dwelling.
Big River Group’s premium plywood products in Spotted Gum were specified all through the interior of the home, with the natural beauty of the species adding textural depth and richness to the overall design.
“Use of Big River’s timber profiles throughout creates a sense of flow and cohesion,” says Aimee Goodwin, Director at Project 12.
“Spotted Gum timber has been used for the flooring, wall panelling, joinery cabinetry and stairs to establish a subtle but undeniable connection between the various rooms and levels.” Armourpanel, ArmourCab and Hoop Pine is manufactured in Australia under the Plywood Association of Australia’s third party audited quality control program and Milled from managed regrowth and plantation forest hardwoods and is PEFC certified.
OUR upcoming 2024 National Conference is being held in Geelong on the 18 & 19 March, 2024. This is the first time out of Queensland in 10 years and the first time we have gone to the regions.
The conference is designed to expand our members’ perspectives by thinking beyond the conventional. We have invited professionals who will guide attendees in understanding future housing scenarios, highlight potential threats to our market position, provide strategies for navigating the industrial environment, offer advice on defending your business from work cover claims, and shed light on future framing possibilities. These are just some of the subjects we will cover at the conference. We are thrilled to announce the esteemed speakers who will join us at the conference. IndustryEdge’s Tim Woods, WoodSolutions’ Karl-Heinz Weiss, Arboralis’ Nick Hewson, Brenda Garrard-Forster from HR Anywhere, and Dr. Alastair Woodard will all be attending. Each will bring their professional expertise and unique perspectives to our gathering.
Our keynote speaker, sponsored by our Principal Partner MiTek, is the renowned adventurer and environmentalist, Tim Jarvis. He is known for his challenging expeditions that raise awareness of environmental issues. At the conference, he will talk about the importance of leadership in adversity, a topic that carries significant relevance in our current global scenario. We can assure you that the knowledge and insights gained from our speakers will be well worth your time and participation.
The innovative concept of the FTMA Art Show is a unique way to showcase our valued partners and sponsors. Instead of a traditional trade exhibit, these stakeholders are invited to submit a piece of art that embodies their business ethos and reflects their identity. This approach provides a deeper understanding of who our partners are, what they stand for, and why delegates should engage with them.
Following the conference, the pieces will be gathered
KERSTEN
into a stunning art book. This book, which will be sent to every fabricator in Australia, serves as a tangible and lasting reminder of our partners’ commitment to the industry.
The Red Activities Day is an integral part of the conference, serving as both a networking opportunity and a day of relaxation and fun before the more formal proceedings commence. Delegates can choose from a variety of activities, including golf, horse riding, fishing, a winery tour, or surfing. This day, generously sponsored by our Principal Partner Pryda, offers an excellent chance for delegates to network in a more relaxed setting while enjoying their chosen activities.
Following the day’s activities, the Red Activities IceBreaker will be held at the historic Events 1915, situated in the old Federal Mill buildings. Sponsored jointly by Pryda, Meyer Timber & Vekta Automation, the Ice-Breaker promises to be an unforgettable evening with excellent food, an exclusive wine collection presented by a private sommelier, and top-notch entertainment, setting the perfect tone for the conference to follow.
The 2024 National Conference dinner, with the theme “Disco Cats,” promises to be a spectacular evening filled with merriment and celebration. Held at the GMBHA Stadium, it offers attendees an opportunity to unwind while enjoying delicious food, refreshing beverages, and compelling conversations. The night will be more than just good food and company, as it will also include the presentation of several prestigious industry awards. Sponsored by our Principal Partner Multinail, the dinner is an integral part of the conference experience and is not to be missed.
As stated, we have a number of prestigious awards. First and foremost, the Clive Martella Service to Industry Award, an established honour in our industry, will be presented as it has in previous years. This award celebrates individuals who have shown significant dedication and provided exceptional service to our industry.
Additionally, we’re introducing three new award categories this year. The FTMA Community Award is designed to recognise members who are significantly involved in their local communities, embodying our organisation’s values through their actions.
The Jackson Kidd Wellbeing Award salutes businesses that make outstanding efforts to ensure the wellbeing of their employees, a crucial aspect of modern business practice.
Lastly, the Employee Recognition of Service Award will be granted to members’ employees who have remained loyal to one employer for 10, 15, 20, or more than 25 years. This award is a testament to the importance we attach to dedication and longevity in employment.
Registration for the FTMA Conference is exclusive to fabricators, supplier members, and sponsors. Non-member suppliers are reminded that they are ineligible to attend our events. In an effort to promote maximum participation from fabricators, we have implemented a cap on supplier registrations until late February. The number of registrations is distributed among Principal Partners (10 registrations), Strategic Partners (6 registrations), Supporting Partners (4 registrations), Conference Sponsors (4 registrations), and Supplier Members (2 registrations).
These limitations serve to create an environment conducive to meaningful exchanges and networking. Should there be availability towards the end of February, we will consider increasing supplier registrations. If you want further information on the conference please visit www.conference@ftmanews. com
FTMA is recognised as the trusted representative body and unified voice for all timber frame and truss manufacturers in Australia, whilst strengthening the connection with the broad supply chain.
FTMA thanks our dedicated partners and encourages you to support those who support your industry
a full list of the conditions of membership and a downloadable application form visit:
SWINBURNE Univer-
sity’s Advanced Manufacturing and Design Centre, known as the Factory of the Future, is a dedicated space for research and teaching in manufacturing and design-led innovation. There are five studios in the complex, located in the Melbourne suburb of Hawthorn.
According to a Swinburne spokesperson, “the future is now and timber is shaping the future”. The focus of the Factory is a two-storey timber ball, built from a curved frame of LVL, clad with a panelised curved plywood skin.
The plywood skin, faced with hoop pine veneer, mimics the construction technology used for submarines and space shuttles, forming a structural shell over the curved LVL. The LVL beams were modelled using computer aided design and cut to the required curve by computer guided cutters.
The timber ball’s ribbed substructure and curved plywood skin were flat packed and transported to site for assembly. While the plywood
PETER LLEWELLYN
Technical representative, Timber Veneer Association of Australia
panels that form the skin of the timber ball were fabricated by automated processes, Swinburne emphasises that the assembly required human ingenuity and skill. Enclosing a two-storey space, the ball expresses the decorative and functional characteristics of timber panels. The structural design permitted an upper-level meeting room over the lower computer hub, while the hoop pine veneered plywood skin, comprised of 180 fitted and curved panels, gives it the appearance of a beautifully crafted spun timber ball.
The outside panels of the timber ball were tinted and
sealed with a pinkish glaze resembling the colour and appearance of an egg, prompting questions of whether it was made by man, or by machine or by nature.
An important factor in the choice of hoop pine as the face veneer was its light colour and even grain, well suited to the desired light-
coloured pinkish finish. Sustainability issues were also important, particularly waste minimisation by pre-fabricating the curved LVL’s and plywood panels.
The reduced carbon footprint of the structure, arising from the use of wood products from Australian forests with consequent “low carbon
WITH Easter fast approaching readers are reminded that the holiday weekend begins with Good Friday falling on 29 March 2024.
How do you calculate penalty rates for an employee who works on a public holiday? Read more on penalty rates and public holidays below.
The use of the term “double time and a half” in connection with work performed on a public holiday means that an employee receives the ordinary rate of pay for the day and, in addition, time and a half for all time worked on the holiday.
That is, the employee receives a total of double time
and a half for time worked on a public holiday – NOT double time and a half in addition to their ordinary pay for the holiday.
Do you get double time and a half on public holidays?
For example, a full-time employee covered by the Timber Industry Award 2020. The employee is called into work for four hours on a public holiday to deal with an emergency. They would receive payment of 7.6 hours pay for the day at ordinary rates, plus four hours in addition at time-and-a-half.
This in effect is the same as double time and a half rates for the four hours worked plus 3.6 hours pay at ordinary rates, being the balance of
Brian
Beecroft CEO, TTIA
one full day’s normal hours, which the employee was not required to work, but for which he or she is entitled to be paid.
Most modern awards provide for a minimum pay-
ment when an employee is required to work on a public holiday. For example, the timber award prescribes a minimum payment of three hours of work at double time and a half. A casual employee would receive an additional 25% based on the ordinary hourly rate.
An employee is entitled to be paid at their base rate of pay when a holiday falls on a day the employee normally works. Under the Fair Work Act (s12), ‘base rate of pay’ means the rate of pay payable to an employee for their ordinary hours of work, but NOT including the following:
• incentive-based payments and bonuses
• Ground floor computer hub with cantilevered meeting room above.
Pictures: Trevor Mein Photography.
• Meeting room with exposed structural elements.
miles”, was also a factor in the design process. And not least was the attractive appearance of the hoop pine skin, sealed with natural waterbased finishes.
For more information on the innovative use of timber veneers, visit the Projects section of our website at www.timberveneer.asn.au.
• monetary allowances
• overtime or public holiday penalty rates, and
• any other separately identifiable amounts.
The base rate of pay under the National Employment Standards applies to all national system employees unless a more beneficial entitlement is prescribed by the applicable modern award, enterprise agreement, or individual contract of employment.
The TTIA Timber Hotline operates nationally on unlimited calls. Contact (02) 9264 0011 or email ttia@ttia.asn. au if you are not already a Member and are interested in learning more.
The Stacker is the perfect solution to continuously stack timber into packs all day long without any supervision. This machine is ideally suited to any moulding, finger jointing or docking line and will improve productivity and safety. The automated Stacker is a robust, reliable, economical and user friendly solution to stacking timber.
The Vacuum Lifter can be used to unload and load timber one piece, or a layer, at a time. When unloading a fillet sweeper can be incorporated to automatically clear the fillets in between the layers. The vacuum lifter is an extremely versatile piece of equipment that is a must for any high speed, heavy lifting, long piece, or repetitive applications.