


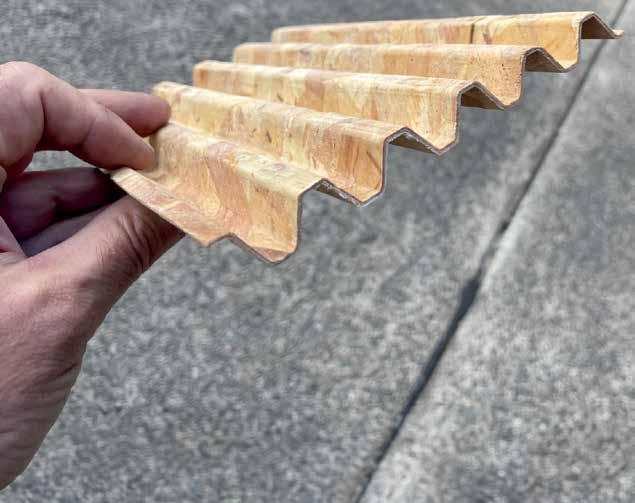

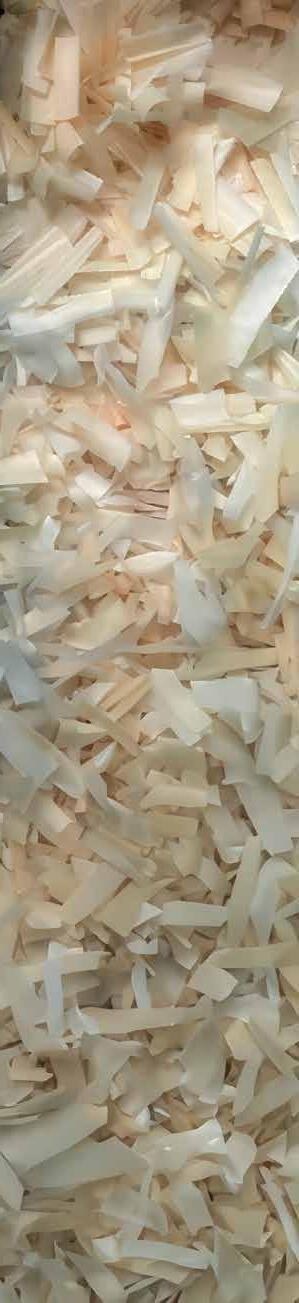




THE Green Triangle’s hardwood plantation sector is proving it could have the solution to meeting Australia’s future structural timber needs.
Celebrating National Forestry Day yesterday, hardwood plantation companies Australian Bluegum Plantations, Midway Limited, and New Forests, supported by plantation managers PF Olsen and SFM, showcased the industry’s new engineered wood product – a Glue Laminated Timber prototype made exclusively from Eucalyptus Globulus (Bluegum) grown in the Green Triangle.
The collective has revealed its plan to evaluate the viability of building an integrated timber manufacturing hub in the Glenelg Shire, close to its hardwood resource to commercialise the first-ofits-kind product, working in partnership with the Green Triangle Forest Industries Hub (GTFIH) and Victorian Forest Products Association (VFPA).
The mass timber product is an output of the GTFIH’s Splinters to Structure project, delivered in conjunction with Forest and Wood Products Australia, which used both softwood and hardwood fibre, with no specific domestic application as the core product base.
Generated after two-year manufacturing trials, the
new hardwood product is equivalent to structural steel in building construction, with work currently testing the product durability and domestic and export market opportunities.
With global demand for timber set to quadruple by 2050, Australian Bluegum Plantations CEO Russ Hughes said the new product would support the imbalance between supply and demand, supplementing the reduction of Victoria’s native hardwood market.
“A portion of our existing resource would be utilised in this potential new product, which would support highly skilled jobs, increasing local and export income, ultimately strengthening the forestry sector value chain,” he said.
“Importantly, this product will provide additional domestic timber supply, supporting the Victorian State Government in its plan to supply more housing stock. Our early research suggests the development of a hardwood timber manufacturing hub could generate up to 110 jobs in construction with 40 ongoing.”
Midway Limited managing director Tony McKenna said the hardwood product would diversify the market base, providing a new domestic product with a low carbon profile.
“While our core business
Midway Limited managing director Tony McKenna, and Australian Bluegum Plantations CEO Russ Hughes with the new GLT hardwood prototype.
will remain export, mass timber has grown from being an emerging technology to a structural building solution. Importantly, this is a sustainable building product which can be used in place of steel or concrete to create durability with less embodied carbon,” Mr McKenna said.
PF Olsen managing di-
rector Nathan Windebank, representing New Forests, said the proposed feasibility study would support a comprehensive business case to understand how to best commercialise the product and attract investor attention.
“This study would evaluate how to best construct an integrated manufactur-
ing facility, considering both physical and logistical infrastructure needs. It will identify the best location near existing complementary industries, where space can be shared amongst industry partners, to support this new and sustainable hardwood timber product market,” Mr Windebank said.
AUSTRALIA’S housing crisis is predicted to continue towards 2030, and prefabricated housing may hold the key. However, this presents another question: How best to handle such unusual loads across the supply chain?
Australia’s National Housing Supply and Affordability Council has predicted a total shortfall in housing supply of more than 39,000 dwellings by 2030.
This has been influenced by factors such as skills shortages, lack of diversity in construction, climate, policy, interest rate rises, and lagging building approvals.
Fortunately, prefabricated housing – the concept of constructing larger pieces like walls and roofing offsite for completion onsite – has the po-
tential to mitigate several of these issues.
Researchers from the University of Melbourne have weighed in on this game-changing construction method.
“Due to the diminishing availability of skilled labour and the demand for quicker construction, prefab is fast becoming a necessity more than an option,” Dr Tharaka Gunawardena, a Principal Coordinator for the University’s Department of Infrastructure Engineering said.
“It can allow construction with minimum on-site congestion, waste generation and pollution by moving away from a labour-oriented onsite operation to a more process-oriented offsite manufacturing and assembly process.”
However, the concept of prefabrication comes with its own issues, like the handling of significantly larger loads.
This is where Combilift’s range can greatly benefit the construction industry. In fact, Combilift is already working with partners that provide modular housing solutions in Australia including Fleetwood in New South Wales, the Queensland government’s QBuild Modern Methods of Construction (MMC) program, and Offsite in Western Australia.
“We’ve been working with organisations in the modular housing space for several years already in Australia,” says Combilift Country Manager, Chris Littlewood.
“We make customised machines that can handle all types of loads,
includng bulky and oversized loads, and in many cases that has been key for those who need to move prefabricated, modular components.”
Meanwhile, Combilift has again been recognized as a Best Managed Company by Deloitte for the 12th consecutive time in the award's 16-year history.
The Deloitte Best Managed Company award acknowledges the achievements of management teams, and not just individuals. The accolade recognises overall business performance based on the criteria of Strategy, Capability and Innovation, Culture and Commitment as well as Governance and Financial Performance. Judges examine every company based on these four equally weighted pillars to select a winner.
SEPTEMBER / OCTOBER 2024
Issue 4 – Volume 34
Incorporating Australian and New Zealand Timberman. Established 1977.
News 3-13
Timber Construct 2024 6-9
Milestones 14-15 Technology 16 Training 17 Associations 18-19
FRONT Cover:
An artist’s rendering of the the $1.5 billion 39-storey Atlassian Central Tower under construction in Sydney will include about 2000 square meters of timber floor plate.
Story Page 6
PUBLISHER and Chief Executive: Hartley Higgins
General Manager: Robyn Haworth
Editor: Bruce Mitchell
b.mitchell@ryanmediapl.com.au
Adelaide Office (08) 8369 9521
Advertising:
Andrew Everett
a.everett@ryanmediapl.com.au
Adelaide Office (08) 8369 9517
Creative Services
Robyn Haworth
Production: Robyn Haworth
Timber classifieds:
a.everett@ryanmediapl.com.au
Adelaide Office (08) 8369 9517
Subscriptions:
subs@forestsandtimber.com.au
Adelaide Office (08) 8369 9500
Subcription rates
One-year (6 editions) $44.65
Two-years (12 editions) $77.65
Accounts: ar@winetitles.com.au
Phone: (08) 8369 9500
Postal Address:
630 Regency Road, Broadview South Australia 5083
Phone: (08) 8369 9500
Melbourne Office: Suite 2262, 442 Auburn Rd, Hawthorn VIC 3122 Phone: (03) 9810 3262
Website www.timberbiz.com.au
NEW home sales nationally fell by 1.3 per cent in August which leaves sales in the three months to August 2024 higher by 4.6 per cent compared to the previous year.
The HIA New Home Sales report is a monthly survey of the largest volume home builders in the five largest states and is a leading indicator of future detached home construction.
“Increasing activity in other states, particularly in Queensland, are counteracting weak new home sales in the two largest markets of NSW and Victoria,” HIA Economist Maurice Tapang said.
“New home sales in Queensland increased by a further 3.8 per cent in the month of August, after recording a strong 15.6 per cent increase in July.
“This leaves new home sales in Queensland over the three months to August 2024 higher by 53.5 per cent compared to the same period in the previous year,” he said.
Strong population growth, particularly from those moving from other states into Queensland, were supporting demand for new homes.
However sales of new homes in South Australia and Western Australia fell in August from strong levels.
“It is possible that investor activity in Western Australia is slowing down as it moves through a cycle of strong house price growth and low vacancy rates,” Mr Tapang said.
“In Victoria, new home sales have been very bumpy in recent months. The drawforward of sales in April
continues to affect sales in the months that followed.
“New home sales in NSW remains weak as the cost of delivering a new ‘house and land’ package in Greater Sydney remains elevated by regulatory changes and land prices.”
Mr Tapang said it had been more than 10 months since the last rate increase. The continued undersupply of homes and robust labour market conditions were assisting a return of consumers to the new home market.
“It is increasingly evident
that an increase in home building activity, expected towards the end of this year and into early next year, will be driven by those markets outside of Sydney and Melbourne,” he said.
New home sales in the three-month period to August 2024 increased in Queensland by 53.5 per cent
compared to the same time in the previous year, followed by South Australia (+25.0 per cent), New South Wales (+12.0 per cent). Western Australia recorded a 14.2 per cent decline over the same period, followed by Victoria (-11.3 per cent).
• Strong population growth in Queensland is supporting demand for new homes.
GLUED laminated timber has become a significant asset to the Australian timber industry, contributing value across multiple sectors such as construction, infrastructure, and sustainable design.
Its increasing adoption reflects both the demand for sustainable building materials and the timber industry’s shift towards high-perfor-
mance products.
For the Australian construction industry, which frequently deals with challenging environments, glulam offers a reliable and adaptable solution that maintains the integrity of
structures over time.
It is little wonder then that Parkside Timber as well as the Green Triangle’s hardwood plantation sector - Australian Bluegum Plantations, Midway Limited, and New Forests, supported by plantation managers PF Olsen and SFM – are getting on board.
Parkside is looking to use spotted gum, the Green Tri-
angle collective has plans to evaluate the viability of building an integrated timber manufacturing hub to use Bluegum to produce glulam. Both show a commitment to the timber industry that many will be keeping their eyes on for the future.
THE Victorian State Government is backing Victoria’s prefabricated construction industry, with a new directory making it easier and more accessible for local manufacturers to work on projects across the state.
Minister for Jobs and Industry Natalie Hutchins has launched the latest edition of the Victorian Prefabricated Construction Directory, which features 24 businesses delivering residential, commercial, and infrastructure
projects across Victoria.
First released in 2019, the directory showcases the range of products and capabilities of each business, making it easy to find manufacturers that can meet specific project requirements.
The directory also highlights innovative examples of the Labor Government’s use of prefabricated construction in building projects, including the two-storey mental health facility extension at the Sunshine Hospital and an affordable regional housing project in Horsham.
Prefabricated construction is a modern method of construction (MMC) where buildings and components are manufactured off-site before being transported to a permanent location. This
approach can result in lower costs and faster delivery times compared to conventional construction methods. By manufacturing buildings in a controlled factory environment, prefabricated construction minimises delays caused by disruptive weather, reduces waste, and creates safer, more accessible jobs.
As the fastest-growing state in Australia, Victoria’s increased adoption of prefabricated construction will play an important role
in increasing the supply of residential housing stock by enhancing the productivity and competitiveness of our construction sector.
Victoria’s $33.5 billion manufacturing sector is a significant contributor to the economy, generating $23 billion in exports and supporting over 260,000 jobs.
The Victorian Prefabricated Construction Supply Chain Directory can be downloaded at djsir.vic.gov.au/made-invictoria
Designed and engineered for high accuracy cutting
Two head saw configuration
Digital controllers allow accurate saw wheel positioning
Automatic blade tension is controlled by hydraulic cylinders
Variable feed speed by hydraulic motor drive
Large horsepower Seimens or equivalent saw wheel motors drive the blades allowing for heavy-duty cutting
The conveyor belt is driven by a high performance hydraulic motor
Adjustable feed speed allows flexibility to saw hard and soft wood
Full wheel and blade lubrication
Low maintenance
Safety cage.
THE world’s largest hybrid building currently under construction in Sydney will use European-sourced crosslaminated timber and glulam beams for its 24 timber levels.
Speaking at this year’s Timber Construct 2024 conference in Melbourne Tim Allen, from structural engineering company Taylor Thomas Whitting, said the timber components for the $1.5 billion 39-storey Atlassian Central Tower would be sourced from Wiehag and Stora Enso.
Mr Allen said that the sourcing of the CLT and glulam was originally designed for an open procurement pathway,
“We tried to leave it open to a competitive tender as best as we possibly could,” he said.
“This could have been either Australian or European supply, but ultimately, decisions were made, and the timber will now come from Europe.
“So the European supply for this project has been appointed to Wiehag, with the CLT being supplied by Stora Enso.”
Mr Allen said the products were currently being fabricated and would start arriving early next year.
Located in Sydney’s new Innovation and Technology Precinct, Atlassian Sydney Headquarters will be 180 metres tall and includes a youth hostel occupying the lower levels. To be completed by 2025 and attracting 25,000 workers, the new 40,000m2
world-first commercial tower is a groundbreaking global first.
The benchmark design of timber, with a glass and steel facade, includes a mix of outdoor and indoor spaces and reaches over 40 storeys high.
Mr Allen described the tower being built next to Sydney’s Central Station as a timber building inside a much, much larger building.
“This hybrid building utilizes the performance
characteristics of different materials, concrete, structured steel work and mass timber throughout the construction,” he said.
“Being a hybrid building, we’re trying to utilize the materials for its benefits and the right application in this aspect.
“So we’ve been able to leverage these benefits and balance of materials combining into an aesthetic and environmental advantages of mass timber with also using the structural performances of benefits of steel and concrete.”
The building has concrete foundations as well as a concrete wall throughout the building with concrete “mega floors’’ from level one to level eight.
Mr Allen said that these would repeat every four floors.
“Next we have the three timber floors that sit between the mega floors.
“And these repeat from level eight to level 32.
He said there was about 2000 square meters of timber floor plate.
“So that adds to quite a bit of timber.
“And finally, we have the structural steel exoskeleton that wraps around the side.”
Mr Allen said he was often asked why do we only have three stories of timber sitting between the mega floors.
“That’s a one of the outcomes of the fire separation strategy,” he said.
Mr Allen said the project had some interesting sustainability goals, including a 50% reduction in up front embodied carbon, 100% renewable energy from day one of operation, and a six star green star rating.
Efficient Saw Machines Designed For Today’s Log Diet
• HewSaw’s single pass machines provide multiple high recovery solutions for logs from 75 to 550 mm in diameter.
• Local customer service and parts from HewSaw’s Australasian subsidiary.
• Over 6 decades of experience with installations in more than 30 countries.
THE shortage of housing in Victoria will be addressed by the State Government which believes another 2.2 million homes will need to be built over the next 25 years.
This will include an increase in townhouse builds, the release of more land under a 10-year Greenfields Plan, an overhaul of the planning system which include the ability for developers to bypass local council and VCAT restrictions, and reducing the financial burden.
Jeroen Weimar, Deputy Secretary of Housing Implementation, Department of Premier and Cabinet, told this year’s Timber Construct 2024 conference in Melbourne the State Government recognized there was some financial levers “we’ve got to pull up as well”.
“I’m sure the Treasurer and Premier will talk about that in the months to come,” Mr Weimar said.
Mr Weimar, who was Victoria’s COVID-19 response commander, was appointed to oversee the Victorian government’s housing policies in February this year.
“I think government has an opportunity to do much more, particularly around land, around planning and around funding,” he told the conference.
“And what the government asked me to do six months ago; come in, kick some tires around, make sure we’re actually doing the right things, talk to industry and engage in industry, and make sure we’re lining things up in the right way.
“So that’s why I’m here. I’m here to try and get things moving and to work with you in partnership to do so.”
Mr Weimar was introduced at the conference by Frame and Truss Manufacturers Association CEO Kersten Gentle who told a session on the housing shortfall that if government wants faster, more affordable housing, firstly they need to streamline their policies and look at the taxes charged to the industry.
“If Government’s wants to bring down costs they need to streamline the planning process and look at government taxes, as it’s estimated
that up to 40% of the cost to build a house is government taxes,” she said.
“Simple steps such as changing townhouses from Class 2 to Class 1 could save up to $20k and ensure faster delivery.”
Mr Weimar conceded that given the challenges facing the building industry “it’s been a really hard time”.
“But what I’d like to talk about this morning is that whilst we might be feel like we’re sometimes in the gutter, I think we are looking at the stars.
“I think there are opportunities and reasons for us to be optimistic about the months, years and decades ahead,” he said.
“We need to start working into our townhouse market.
“We need some looking at our mid-rise apartment particularly that four to 10-story market in around a number of locations.”
Mr Weimar said that the Government would, in the coming months, published its 10-year Greenfield Plan.
“We know the planning system is slow and cumbersome, and we know it’s uncertain,” he said.
“So two things we’ve done; one is that any developer looking to develop a housing project of over $50 million gross value can come straight to the Minister.
“We’ll go through an accelerated planning pathway that takes out local council, the VCAT and all the other dramas that developers have to go through.
“But what we’re also looking at is what we know about activity centres.”
Mr Weimar said that there were 10 locations across Melbourne at the moment, including Frankston and Camberwell, where the government believed it had capacity to significantly uplift zone controls to encourage four story development, six story development, and eight story development.
“We’re going to go out to consultation in a couple of weeks. They’ll be done by
• The Victorian Government plans to tackle the housing crisis by prioritising townhouses.
the end of this year, which will ensure that people who own land in that space can now start to significantly increase the value of that land by going further up than they could before, knowing they won’t get stopped by VCAT,” he said.
“They won’t get stopped by local council concerns.”
“So our job in a planning space is basically faster, clearer and simpler. We’ll put out a plan for Victoria that says, here’s a bunch of homes needed to get built, and here are the changes the planning system that will make that happen.
“And we will need to deal with our public housing towers, 44 of them around Melbourne.
“We’ve committed to replacing them all within the next 25 years.
“So, we really think it’s time to get on and rebuild those towers,” Mr Weimar said
“Again, a huge opportunity. Not only will that be probably a doubling of the total housing capacity in those precincts, but also very different types of built form coming forward. And finally, a lot of work around
the rental space and around building reform space.
“We recognize if we’re going to support the timber industry, if we’re going to support the construction industry, we also need to make sure that our building codes actually make sense, that our building regulator is up to scratch, and we had a few dramas there.
“But I think it’s now in better hands, and we’ve got to make sure that we structure the domestic building contracts in a way that supports the right housing to get built.”
The wood processing industry faces rising pressure to produce high-quality products efficiently while tackling labour shortages, increasing costs, and global competition. Process automation is the solution to streamline operations, boost production speed, improve product quality and reduce waste. Automation has transformed various industries over the past few decades, and wood processing is no exception. From simple mechanisation to fully automated systems, the industry has seen gradual advancements that allow for streamlined operations and smarter workflows. Modern automated systems leverage robotics, artificial intelligence, and machine learning to ensure precision and efficiency at every step of the production process.
Increased Efficiency
Automation speeds up production, allowing you to meet deadlines faster.
Enhanced Product Quality
Advanced technologies ensure consistent and high-quality output.
Reduced Labour Costs
Automation minimises reliance on manual labour, lowering overall costs.
Minimised Waste
Precision equipment reduces material waste, optimising resources.
Improved Safety
Automated systems reduce human involvement in dangerous tasks.
Scalability
Automation allows for easy scaling of production to meet growing demand.
At Stirling Group, we partner with customers to future-proof their wood processing operations by delivering cutting-edge solutions in automation, material handling, and robotics. By collaborating closely with our clients, we create tailored automation systems that address specific challenges and optimise their manufacturing processes for long-term growth, efficiency, and success. Our latest installation is a prime example of this, transforming our client’s operations and paving the way for future automation enhancements. The system’s plug-and-play design enables seamless integration of a grading scanner and other upgrades, empowering them to streamline processes and meet increasing demand.
Our client was struggling with an aging 80 metre per minute high-speed line that required too many operators and was becoming unreliable. To keep up with increasing market demand, they needed a modern system that could reduce labour requirements, increase productivity and create consistent high quality products.
We installed a high-speed moulding line centred around our Stirling S230-7 High-Speed Moulder. This line is designed to process timber directly from the kiln and dress the boards to a semi-finished or finished size. The timber is then graded and packed according to length and grade. The process only requires three operators to complete loading, initial grading, moulding, final grading, vacuum stacking, and strapping the timber.
The solution has maximised uptime, allowing for consistent production without delays caused by manual intervention. It has also improved product quality through enhanced grading precision and better surface finishes. Automation has streamlined the workforce, enabling fewer operators to manage the production line, reducing labour costs while maintaining high productivity and quality. Additionally, less manual handling has lowered the risk of workplace injury. The system is future-ready, designed to meet growing production demands and can be seamlessly integrated with further automation upgrades.
Do you want to watch this High-Speed Moulding Line in action?
PARKSIDE Timber is planning to build a high-impact timber and laminating facility in Wondai, Queensland, contributing to the local timber industry and economy.
It is projected to process up to 6000 tonnes of timber annually once it reaches maximum capacity after five years. It will create 10 fulltime jobs.
South Burnett Regional Council approved the development permit for Parkside Building Supplies Pty Ltd at a general council meeting in August.
The facility at 2-30 Kemp St will focus on manufacturing wooden and laminated products.
The facility’s infrastructure will include a glue lines building for finger-joining spotted gum, a racker and stacker building and car parking facilities with a minimum of 42 spaces.
A site-based management plan prepared by Range Environmental Consultants classified the potential environmental impacts from the operation as ‘low’. The facility will also produce 5000 to 10,000 tonne of reconstituted timber products annually.
Environmental management reviews will be conducted every year.
Parkside acquired its first sawmill at Eungella, Queensland which then lead to Parkside expanding its timber sales and building materials business into Townsville in 1966.In 1972, Parkside acquired a larger and more efficient sawmill in Mackay. With a guarantee of its own timber supply. It later bought sawmills at Builyan, Theodore, Wandoan, Eidsvold and Wondai in South West Queensland.
In 2019, Parkside expanded its milling operations further by acquiring mills and processing plants at Greenbushes and Nannup in Western Australia, and Orbost and Bairnsdale in Victoria.
Parkside is one of Australia’s largest hardwood millers and timber manufacturers producing world class timber products for Australia, Europe, Asia and the Americas.
IN a field on the side of a publicly accessible road on Scion’s Rotorua campus you’ll find tall, power pole-like structures, L-shaped joints sitting on what looks like park benches, decking at various stages of decay, rows of cladding and wooden stakes sticking in the ground.
It isn’t a strange halffinished building site or dilapidated wood storage, it is vital strategic infrastructure for Scion and the whole country. The site is one of four forming the National Wood Performance Archive, and the biggest and most comprehensive.
Collectively, the information gathered from the sites about wood durability provides a foundation for the timber industry and helps inform building practice standards and compliance. The testing is used to establish durability classifications for timber grown here and overseas. They include products from international companies wanting to launch in New Zealand.
Information from the sites combined with information about structural performance established in Scion’s timber engineering lab informs how suitable wood products are for particular purposes.
Scion’s site includes aboveground tests like decking, cladding and joinery, and in-ground stakes, posts and poles while the three remote sites – near Whangārei, Hanmer and Waitarere – only have in-ground stakes. Scion deliberately selected test sites with different environments and soil types to get a range of information.
Scion’s field sites were established in 1947 meaning we hold more than 75 years of wood durability and performance records.
Data is collected from the samples annually. Scion’s site has around 50 trials with different anniversaries, so testing takes place multiple times a month, while the other three sites are only visited once a year.
Dr Tripti Singh, Scion’s leading timber durability expert, says the main purpose is to test timber durability – how long a product
lasts for what purpose.
For Singh, Scion’s site is like “an outdoor lab”.
“We’re looking at product performance … Durability is one side of that, other aspects like structural stability and fitness for purposes are the others. They are correlated and we need data from various sources to establish the product’s performance,” she said.
“Each product has advantages and disadvantages determining its end use and what is the right wood for the right use is the key.
“For any new timber species including hybrid species, we have to define what durability class that species sits in,” Singh says.
Scion also tests new formulations and treatments that protect timber to see if they are effective. Some tests last decades as durability class can only be determined when the last sample fails.
Maintenance is carefully completed. The ground around the tests can’t be mowed by contractors or sprayed with products that could inhibit natural flora and fauna. Weeds are pulled by hand and in summer maintenance can be a “big mission”.
The trials have also produced surprising results, for example one fungus isolated from the site can be used in biotech applications due to
the very specific enzymes it produces.
General Manager, Forest to Wood Products, Dr Henri Baillères says the sites are a “strategic infrastructure used on an everyday basis”.
“For any species not in the building standards … the field test site is a facility enabling us to provide the data to inform whether it is meeting requirements and can be used or not.”
Scion is the only organisation in New Zealand doing this type of testing to inform building standards. Without it, new products would not become compliant or available for construction, Baillères says.
“It’s very strategic for New Zealand, Scion, and our industry and other players across the value chain,”
Baillères says.
Dr Bruce Deam, a senior structural engineer at the Ministry of Business, Innovation & Employment who has been involved with building standards development, says the fact New Zealand has specific building code requirements for durability makes it unique. He says the Wood Performance Archive is an essential way of demonstrating long-term durability and has been hugely worthwhile for both ground contact and exterior exposure testing.
“Over the long-term it helps confirm that durability expectations have been met, showing the in-ground and exterior timber meet the performance requirements for use in buildings.”
TIMBERLINK has launched its Australian-made wood composite products brand, Everdeck, comprised of decking boards, edge boards and concealed fasteners.
Everdeck boards are manufactured in Tasmania from a combination of Australian recycled plastic and plantation pine timber residues such as wood shavings. Everdeck decking boards are currently available in a 137mm width and length of 5.4M, and in a range of six different colours.
“Our Everdeck boards contain at least 50% plantation pine timber residues which are sourced from our Bell Bay facility,” Timberlink’s Chief Sales and Marketing Officer Simon Angove said.
“These residues are combined with Australian recycled plastic to create a
value-added product that is simple to install and easy to care for.”
The Everdeck wood composite products manufacturing facility was announced in 2021 and was supported by a $5.8m coinvestment from the Australian and Tasmanian Governments’ Recycling Modernisation Fund (Plastics) Round 1 Grants Program (RMF).
It is a part of Timberlink’s Bell Bay, Tasmania, plantation pine timber manufacturing site, and is the first facility in Tasmania to manufacture wood composite products.
Everdeck decking boards, edge boards and concealed fasteners are now available in Tasmania with availability in other Australian states to follow.
To support the launch of these products, Timberlink has released a new website at www.everdeck.com.au which features an interactive deck planner tool which allows consumers to explore different layout options and colours for their deck, as well as calculate an estimate of materials. The deck planner is located at www. everdeck.com.au/deck-planner/.
• Timberlink Bell Bay General Manager Scott Freeman, the Federal Member for Lyons Brian Mitchell, Tasmanian Minister for Parks and Environment
Nick Duigan and Timberlink Chief Executive Officer Paul O’Keefe at the new facility.
The Combilift range of
Andrew Kidd has been appointed chairman of the Frame & Truss National Safety Council.
Mr Kidd has an extensive background, spanning over more than two decades at Dahlsens.
His work in varied rolesfrom Transport & Warehouse Manager to Safety Manager - equips him with a holistic understanding of the complexities that frame and truss operations encompass.
He also holds a Diploma of Work Health and Safety and a Certificate IV in Training and Assessment.
The Hyne Group has acquired Pinetec, a pallet and packaging business based in Perth, Western Australia. This is the Hyne Group’s first manufacturing presence in the West in its 142-year history.
Earlier this year, the Hyne Group announced its expansion into pallet manufacturing following the acquisition of Rodpak Pallets & Packaging in Melbourne and Express Pallets & Crates in Brisbane.
The Pinetec business has operated for over 30 years (15 years with the current owners) with an excellent customer base across a range of essential sectors such as mining, industrial chemicals, engineering, building products and the transport industry. The business model is very compatible with the long-term partnership approach that Hyne Group operates under.
WESBEAM AWARD
Wesbeam has been named 2024 Supplier of the Year Award at the Big River Group in Brisbane.
Big River Group holds a national conference every two years, where Supplier of the Year and other internal awards are presented.
Mandating the processing of resource consents to within one year for wood processing facilities and related activities announced by the New Zealand Government as part of the resource management reform proposals has been welcomed by the Wood Processors and Manufacturers Association.
THIS year Pryda celebrated its 60th birthday. If you’re reading this article, chances are you already know a bit about Pryda, but there may be some things you didn’t know.
Established in Napier, New Zealand in 1964 by builder Ray Turner, Pryda began its journey as AR Turner & Company.
With a passion for solving problems, Ray designed and manufactured products such as angle braces and knuckle nailplates from his kitchen table. These remain best-selling and essential products today.
A key figure in the early days was Chris Rogers, who joined the company in 1975 and held several roles including Chief Engineer, General Manager and Managing Director.
“When I joined, there were 12 of us in the company,” says Chris.
“We were breaking new ground, with an incredible level of market and technological development during this period from very humble beginnings.”
One example of the technological advancement was Pryda being the first in Australia and New Zealand to introduce automated machinery with the Omni Computerised Saw, first adopted by Key Building Components (now Dahlsens) and MB Prefab (now Big River Group - Breakwater).
“Back in those days
nobody had computerised saws, so economically it was easy to justify,” says Chris.
“It opened the floodgates, and we sold a dozen saws in the first 12 months!”
There will be some fabricators who can still remember laying out timber on the floor, cutting the webs and doing the calculations by hand using a drawing board.
Pryda’s first wall detailing software, Computa-Wall, introduced in 1994 was ahead of its time, revolutionising the industry as the most powerful wall detailing software in the world, enabling users to see frames taking shape through data input. The software was also integrated with the production software Plant Net, streamlining the production processes in factories.
Greg Hay joined Pryda in 1995 as a detailer, providing support to fabricators by creating truss designs that were beyond the capabilities of the software at the time
“Over the years, software advancements have been remarkable, with one of the most significant improvements being the introduction of 3D views in the mid-2000s,” says Greg.
“This not only benefited fabricators but also their customers.” said Greg.
Pryda Computa-Wall eventually evolved into Pryda Build i with Pryda
also a pioneer in introducing an integrated roof, floor, and wall design software package for fabricators.
HOME BASE
For more than 40 years
Pryda’s manufacturing has remained at Healey Road, in
ENGINEERED Wood Products Association of Australasia’s new office and board room was formally opened by EWPAA Chair Stuart Toakley last week enthusiastically attended by industry and supply chain representatives.
The new office is open and welcoming, showcasing the flexible use of a range of EWPAA member company’s renewable engineered wood products (EWPs).
As you enter EWPAA’s
front door, you’re greeted by a commanding laminated hardwood tabletop, skilfully manufactured by Australian Sustainable Hardwoods (ASH), followed by more ASH laminated stair treads, leading to the new mezzanine office landing. Here you are captivated by a modern aesthetically immaculate feature of Austral Plywood vertical strips, accentuated by a backing charcoal painted wall. The Australian Panels’ particle-
board STRUCTAflor may be easy to miss, as it’s not been used as a flooring product, but makes up the external cladding of the panelised framing sections. The unsung and unsighted heroes but are just as important are the now-clad products, AKD timber framing from the Caboolture sawmill, and Wesbeam e-joist. Two EWPs that do the job well and are a sensible and renewable choice for renovations and lightweight timber framing builds. Where the new office space really comes together is the exquisite interior. Australian Panels Easycraft Easy VJ100 is a simple product, that truly adds extensive value to the room. The softened texture from the floor-to-ceiling profile leads perfectly into the charcoal feature wall. Austral Plywood ceilings, doors, and trimmings are ever present, as they both pop with a flash of colour and grain texture yet are subtle and warming.
Melbourne’s outer east.
It’s where Pryda manufactures all nailplates and bracing and continues with local production of a large proportion of other products in Australia and New Zealand.
Operations Manager, Andrew Skerritt has been with Pryda for 25 years and believes in the benefits of manufacturing locally.
“Nearly everything that goes out our door is sourced and made in Australia / New Zealand before it reaches our customers,” says Andrew.
“From a quality assurance and continuity of supply perspective, to have that stability is one of the things that sets us apart from other businesses.”
While the Pryda team is now dispersed all over Australia and New Zealand and remote working commonplace, stepping into the Healey Road facility still feels special.
“For many people, this business is their life”, says Andrew. “Healey Road is a little bit of an oasis where it’s like being part of a family. You can always buy new machinery and tools
but it’s the people that make it all come together. We’re still lucky to have that in our entire business.”
As Pryda continued to grow, it ventured into new markets, most notably in Malaysia, Thailand and Indonesia.
Each country presented unique challenges from navigating language barriers, understanding cultural nuances, and most significantly, adapting to different construction practices.
years of his career in Thailand, helping to open the first office in Chiang Mai in 1991 and introducing timber trusses and nailplate technology to the local building construction industry. To meet the rapidly growing housing demand, the Pryda team and local fabricators started building temporary truss plants.
“These mobile plants were designed for effective transportation between sites by just a crane while enabling workers to stay dry and out of the sun,” says Bernard.
A major milestone in Pryda’s history was the acquisition by global Fortune 200 company, Illinois Tool Works (ITW) in 2003.
The change of ownership had a transformative effect for Pryda with its decentralised and entrepreneurial culture proving to be a great fit and fueling further growth.
At ITW, a company with more than 19,000 patents, innovation is key for growth. From its early days creating inventions in Ray’s
“ We were breaking new ground, with an incredible level of market and technological development during this period from very humble beginnings.
The Thailand venture holds particularly fond memories for Bernard Kennelly, Marketing Development Engineer and one of Pryda’s longest serving team members.
Bernard dedicated three
kitchen and throughout its 60 year journey, Pryda has maintained an unrelenting commitment to providing safer, faster, easier construction solutions.
As with all Pryda’s innovations, the genesis of
CLT Toolbox has announced the launch of a free version of its groundbreaking software.
Designed to advance the adoption of sustainable timber construction across Australia, this new version of CLT Toolbox offers engineers, students, and timber enthusiasts’ access to cutting-edge tools and educational resources.
In June CLT in partnership with Timber Unlimited in New Zealand, released parts of its advanced design software free to engineers in New Zealand. The construction industry faces a critical challenge in reducing
embodied carbon, a significant contributor to global carbon emissions. Traditional building materials like concrete and steel are major culprits. CLT Toolbox addresses this challenge by providing software solutions that simplify and automate the design of mass timber structures. Mass timber is a sustainable, low-carbon alternative that offers significant environmental benefits.
In Australia, the free version offers essential features for member design, calculating loads, and evaluating the structural integrity of timber elements.
SpeedTruss was based on solving common pain points.
“One of the biggest issues on site is the finish of the roof truss system,” says Nicky Woodward, Pryda Software Product Owner and part of the team responsible for bringing SpeedTruss to market.
“The chippies would install trusses, nail them and then get apprentices to do the truss fixings. With SpeedTruss, the trusses arrive pre-drilled in the factory with the correct screws. All the builder needs to do is drive it home.”
Nearly a decade on, the SpeedTruss roof installation system is a staple across building sites all over the country and remains the
fastest, most controlled method of truss installation in the market.
The development journey considered every part of the truss installation process, including integration with the software, working with fabricators to understand their manufacturing capabilities, educating inspectors and lots of testing!
“It was about bringing along everyone on the journey and showing them the benefits,” says Nicky.
“When they saw the speed of installation, the accuracy and the reductions in call backs to site they were convinced it was a winner. Ultimately for the builders it means they can complete more jobs and get more work.”
A new body, the Timber Framing Collective, has been created with responsibility for the marketing of timber framing in Australia.
It sees previously fierce competitors (local producers and importers, amongst others), join forces for the greater good of the industry to promote, establish and consolidate “Timber Framing The Ultimate Renewable’ as the leading building materials brand in Australia for residential construction
Australia faces a major sovereign capability gap in the production of timber house frames by 2035, according to a landmark new report by Master Builders Australia and the Australian Forest Products Association.
2018
Monash University engineers are examining how modern prefabricated building materials can slash costs and improve efficiency of new developments, while providing a solution to the Australia-wide challenge of housing affordability.
Dr Mehrdad Arashpour from Monash University’s Department of Civil Engineering is working on a collaborative project to minimise risk, optimise production and improve the on-site installation of prefabricated buildings, including homes.
Strong, lightweight and affordable, Dr Arashpour said these constructions could benefit everyone – from first-homebuyers looking to enter the housing market, to retirees looking for more customised residential options, and small business owners wanting greater design flexibility.
2013
The demand for skilled labour in Australia’s residential construction industry is running well below the historical norm, according to the Housing Industry Association, the voice of Australia’s residential building industry.
The HIA Trades Report, a quarterly survey of builders and sub-contractors, shows that the availability of skilled trades increased moderately during the June 2013 quarter. Trade price developments were weak, with the average increase clocking in below the rate of general inflation.
• HewSaw’s SL machines feature multiple processing units for maximum flexibility and yield.
WHEN you look at HewSaw’s equipment offerings, it can initially seem a little challenging to know what you need, but with a little explanation, it can be quite simple. There are really only two types of HewSaws – the R series machines and our SL lines.
R Series machines are the original HewSaw style where the entire process is completed in one machine, also called our “single pass machines”. These machines are either called an R200 or R250.
In both machines, logs are generally delivered to a v-flight scanning conveyor equipped with a 3D or true shape scanner followed by a rotary log positioner that positions the log for the best
recovery or yield based on the scan information.
The log is then chipped on all four sides and the resulting cant is processed through a ripsaw with the top and bottom boards being edged within the machine.
From there, the resulting sawn products are sent off to the trimmer, sorter and stacker. No downstream edging is required.
There are however, two types of R200 and R250 machines. The R200 A.1 is HewSaw’s most basic machine and comes with fixed edging, while the R200 1.1 adds optimized edging, a longer saw stroke, and walk-in maintenance.
In the R250 size, the R250 1.1 offers the same added benefits as the R200 1.1
versus the R250 A.1. The R200 models can process up to a 350 mm log, while the R250 size machines can process up to a 550 mm log.
When it comes to our larger SL lines, the “SL” stands for sawline and these are multiunit lines that allow us to take edged sideboards off all four sides.
HewSaw can configure its chipper canter, cantsaw and ripsaw in various ways to help customers achieve their goals. Each unit is typically connected with conveyors and in some cases the cant is turned between processing units.
Board separators are also used to remove edged sideboards along the way. And like the single pass machines, products produced on the SL
lines generally don’t require any downstream edging. For size, HewSawe’s SL200 lines can process up to a 350 mm log, while the SL250 size lines can process up to a 550 mm log.
The R series lines are more cost-effective and take up less real estate in the mill when compared to the SL lines.
With all the equipment, HewSaw can custom design a solution based on log diet, desired production volume and product output needs. If you would like more information please contact HewSaw’s Australasian subsidiary by emailing peter. haintz@hewsaw.com or calling +61 419 345 037.
KAREN FORMAN
BOMBALA-BASED timber milling company
Dongwha Australia has welcomed a NSW Government Forestry Industry Action Plan designed to outline the path the State will take to ensure a sustainable timber industry that aligns with the Government’s key environmental priorities.
Dongwha Australian Team Leader Neville McInnes said although the company had
not yet been contacted by the new advisory panel, it was pleased the government had committed to the industry and had three key areas it wished to discuss.
They are a commitment to keeping roads open to guarantee the transport of timber between plantations and the mill; a commitment to the continued supply of softwood and a commitment to not losing what supply was already available.
“We welcome the plan, abso-
lutely,” Mr McInnes said.
“We are moving along reasonably well at the moment, but we do need to look at the future and secure supply and infrastructure so that things don’t go down.
"We have 130 direct employees and are always looking for more workers.
"For every one direct job, three come off it, that’s 450 jobs feeding off the mill, without secondary jobs, so we estimate 750 jobs come out of the Dongwha site. You take
that out of Bombala and it’s not a positive picture.”
Korean-owned Dongwha Australia took ownership of a small mill with 20 employees on the current Bombala site in 2011 and built a new saw milling plant which was officially opened for business in 2013.
The company produces a range of softwood timber products for the Australian market. It is not involved in export.
DAVID MCELVENNY
IT is easy to forget that competency-based training (also called accredited training) actually has a relatively short history in Australia. In fact, the national VET (vocational education and training) system itself only began to emerge in the late 1980s.
Prior to that time, companies were much more active in designing their own internal training programs. Where they were unable to provide the training within their own resources, employers would send their workers off to TAFE or a specialist trainer to receive trade or technicianlevel training.
However, units of competency now form the basis of all training in the VET system, and they can only be delivered by registered training organisations such as TAFE colleges or privately-owned RTOs.
In the last edition of Australasian Timber, I published Part 1 of this series of articles under the subtitle: ‘Do you really need an external training provider?’. I discussed some of the pros and cons of nationally accredited training, and contrasted them with the benefits of managing your own in-house training program, tailored to the specific needs of your own workers.
But I did hasten to add that in-house non-accredited training does have its own
set of limitations. Below are some of these issues, along with some possible solutions.
Pitfalls and cautions
One of the most obvious limitations of non-accredited training is the fact that because it isn’t regulated by government agencies in the VET sector, it doesn’t have the official standing of nationally-recognised accredited training. This means that workers who receive internal certificates will not necessarily have their achievements acknowledged outside of the company –such as by other employers if they apply for a job elsewhere, or by RTOs if they decide to undertake further studies.
There are, of course, some companies that might consider this a good thing, especially if they want to avoid the problem of rival businesses poaching their well-trained staff. It’s also likely that companies who train up their employees in specialised work techniques or trade secrets may take the view that what’s taught inside the company stays inside the company.
Nonetheless, any business that wants to maintain good workplace morale needs to take into account the learner’s desire for being in charge of their own career path. Employee loyalty is a two-way street, with workers far more likely to stay with a company that they believe has their
best interests at heart, and is giving them genuine professional development opportunities.
Other potential problems relate to how seriously the company takes its own training system. To be truly effective, an internal training regimen must be well organised, with defined goals and measurable outcomes. It also needs to be supported at all levels of the company, from factory floor workers right through to senior management. I’ve personally seen a training program suddenly lose credibility among workers when management instructed their trainers to ‘tick and flick’ new employees through the training and assessment processes, so that they could put them behind a machine as quickly as possible.
Getting the best from both worlds
There is no reason why an in-house training system can’t combine externallydelivered competencies with internally-delivered modules. Your company training manager would still oversee the whole structure, but only bring in an RTO when you either needed formal accreditations or weren’t equipped to provide the specialist training required. It is even possible to develop your own training materials for particular tasks based on standard operating procedures, safe work method statements and
• Although the concepts of acceptable work practices have changed enormously over the years, the fundamental principles of effective training haven’t changed much at all.
• This fellow is being taught how to cut logs to set lengths under the watchful eye of his trainer, who is standing immediately behind him and ready to intervene at a moment’s notice.
• Obviously, there wasn’t much leeway to let the trainee learn from their mistakes using these sawmilling practices.
other company documents, and ask a visiting RTO to incorporate them into the accredited training they’re delivering for you. This helps to keep the training directly relevant to the work your own employees are doing, rather than being diluted to meet the more generalised specifications of a national competency.
In the next article in this
series, I will discuss some of the techniques that can be used to write high quality internal training and assessment materials.
- David McElvenny is the CEO of Building Learning (www.buildinglearning.com. au) and Workspace Training (www.workspacetraining. com.au).
IN the ever-evolving world of roof construction, staying informed and agile is more critical than ever.
The recent FTMA Australia meeting hosted by the Housing Industry Association (HIA) Western Australia underscored this sentiment, particularly as it relates to the upcoming changes in working from heights legislation.
While the enforcement date may have been delayed from April 2025 to September 2026, industry professionals must not become complacent.
This extension offers a crucial window of opportunity for builders and manufacturers to align their practices with the new requirements, ensuring that both regulatory compliance and workplace safety are achieved.
The meeting, attended by an impressive array of 50 builders, industry specialists, and frame and truss manufacturers, highlighted the urgency of proactive preparation.
Andrew Kidd, Chair of the Frame & Truss National Safety Council, delivered a compelling presentation on height safety in construction, stressing the significance of being knowledgeable about workplace hazards and the incumbent responsibilities of builders.
His stark revelations about the tragic toll of falls in residential construction — five deaths over the last decade in WA — served as a sobering reminder of the stakes involved. Kidd’s message was clear: safety cannot wait for regulations to be enforced; it must be an ingrained aspect of the building process from the outset.
Delegates also gained valuable insights from Nick Steens of Independent Timber Supplies and Clinton Wells of Worldwide Truss & Frames. Steens’ presentation on the installation of roof trusses at 600 centres, as practiced ‘over east,’ shed light on safer working methods that could be adopted more widely in WA.
Wells’ introduction of Trafficable Ceiling Battens illustrated innovative approaches to fall prevention, capturing the audience’s imagination with their practi-
KERSTEN GENTLE Executive Officer
FTMA Australia
cality and safety benefits.
The environmental discourse brought forward by David Rowlinson, former CEO of Planet Ark, added yet another layer to the conversation.
His advocacy for timber as a sustainable building material, capable of storing carbon for its lifetime, provided food for thought in a state where steel lightweight framing is strong. With initiatives like NABERS pushing for a national standard for embodied carbon, the imperative to reduce the environmental footprint of building materials is clear.
Builders must anticipate future regulations that will likely mandate such reductions, making sustainable practices not just preferable but necessary.
The event concluded with a panel discussion. Discoveries about the engineered software behind prefabricated trusses, and its compliance with structural standards, left many delegates reconsidering their current engineering protocols.
The revelation that quality products from FTMA members could remove the need for additional structural sign-offs was particularly impactful.
As an industry, we must recognise that these legislative delays are not a reprieve, but
FTMA is recognised as the trusted representative body and unified voice for all timber frame and truss manufacturers in Australia, whilst strengthening the connection with the broad supply chain.
FTMA thanks our dedicated partners and encourages you to support those who support your industry
a call to action. The present moment is our opportunity to innovate, educate, and adapt. By doing so, we not only comply with forthcoming regulations but more importantly, we save lives and mitigate our environmental impact. FTMA Australia extends its gratitude to all participants and looks forward to continuing this vital dialogue.
• FTMA Members turned up in force for the session, some traveling up from Albany. Drew Ryder (Rainbow Frame & Truss), Clinton Wells (Worldwide Truss & Frame), Kristin Small & Kenny McGonnell (Pinelock Systems), Morad Sharif & Ed Serrano (Vekta Automation)
a full list of the conditions of membership and a
THE TTIA National Timber Members’
Hotline is often asked by Members for clarification on the entitlement due when an employee falls ill on a declared public holiday.
For clarification, according to the Fair Work Act (s98), if the period an employee takes paid personal/carer’s leave includes a day or part day that is a public holiday, the employee is taken to be on the public holiday and not absent on paid personal/carer’s leave. They must therefore be paid for the public holiday.
If a public holiday falls during a period of annual leave, an employee is paid for the public holiday. This includes any hours that fall on a part-day public holiday.
Under the Fair Work Act (s89), if a public holiday (or part-holiday) falls during a period of annual leave, or a period where an employee is eligible for personal/carer’s leave (including compassionate leave) or community service leave, the employee
is taken not to be on annual leave for each day eligible for the other leave or public holiday.
The period of annual leave is not extended by any such absence, but the employee is to be re-credited annual leave for each day of eligible absence.
An employee isn’t paid for any public holiday that falls during a time when the employee is on unpaid leave. hether a public holiday extends a period of long service leave will depend on the relevant Commonwealth, State, or Territory long
service leave legislation.
Under the Fair Work Act (s116), an employee is to be paid at their ‘base rate of pay’ for their ordinary hours of work when absent on a specified public holiday.
Base rate of pay is an employee’s ordinary rate of pay excluding incentive-based
A“BENT” in American English is a rigid frame, according to Wikipedia, more commonly described in Australia as a portal frame. It’s not clear whether BENT Architecture chose their name because of a fondness for portal frames, but in any event their practice has completed a diverse range of projects which have been locally and internationally awarded.
Their BENT Pavilion was shortlisted for the Australian Timber Design Awards in the Timber Veneer category. Located in North Balwyn, Victoria, the project initially involved the design of a garden pavilion at the rear of a suburban site.
Designed from the outside in, the redefined landscape between the pavilion and the house soon pushed its way into the interior of the home, inspiring a rethink of existing living
spaces and their relationship with the outdoors.
PETER LLEWELLYN Technical representative, Timber Veneer Association of Australia
Fundamental to the environmental credentials of this renovation-extension was the use of natural materials, such as timber and wood veneer, transitioning between inside and out. Veneer specified for the project was crown cut ‘Liquid Amber’ from Finewood Ventech. This veneer is a PEFC certified dyed eucalypt, which was selected for its striking visual ap-
pearance. It was considered that the veneer’s dark tone accentuated outward views of the site’s garden setting.
The crown cut of the veneer ensured that grain and texture were evident, despite its almost black appearance. In the architects’ words, “The subtle texture of the crown cut facilitated a more immediate connection between the dwelling’s interior and the surrounding landscape”.
The BENT Pavilion shows how wood products such as timber veneers can help to blur the boundaries between outdoor and indoor spaces and, in doing so, bring a natural warmth to the interior.
For more examples of inspirational uses of timber veneers, visit the Timber Veneer Association’s website and explore the Projects section under the About Veneer tab.
payments and bonuses, loadings, monetary allowances, overtime or penalty rates or any other separately identifiable amounts.
This means an employee will be paid at their ordinary rate of pay excluding the appropriate public holiday penalty payment (had the employee worked) provided by the applicable modern
award or enterprise agreement.
As a Member, should you need any clarification on any award related issues, you are able to speak to one of the TTIA team anytime. If you are interested in knowing more about membership please phone (02) 9264 0011 or email ttia@ttia.asn.au