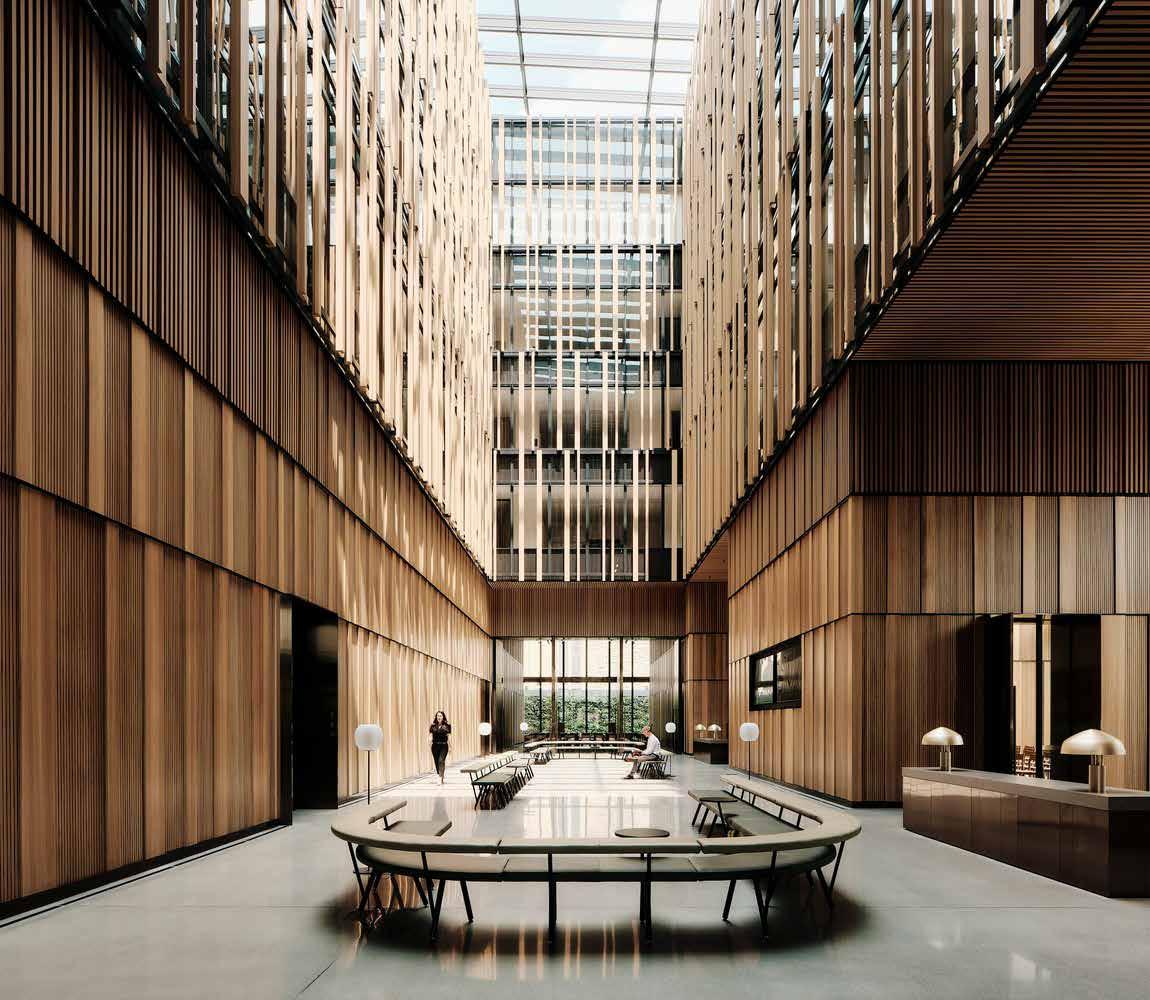
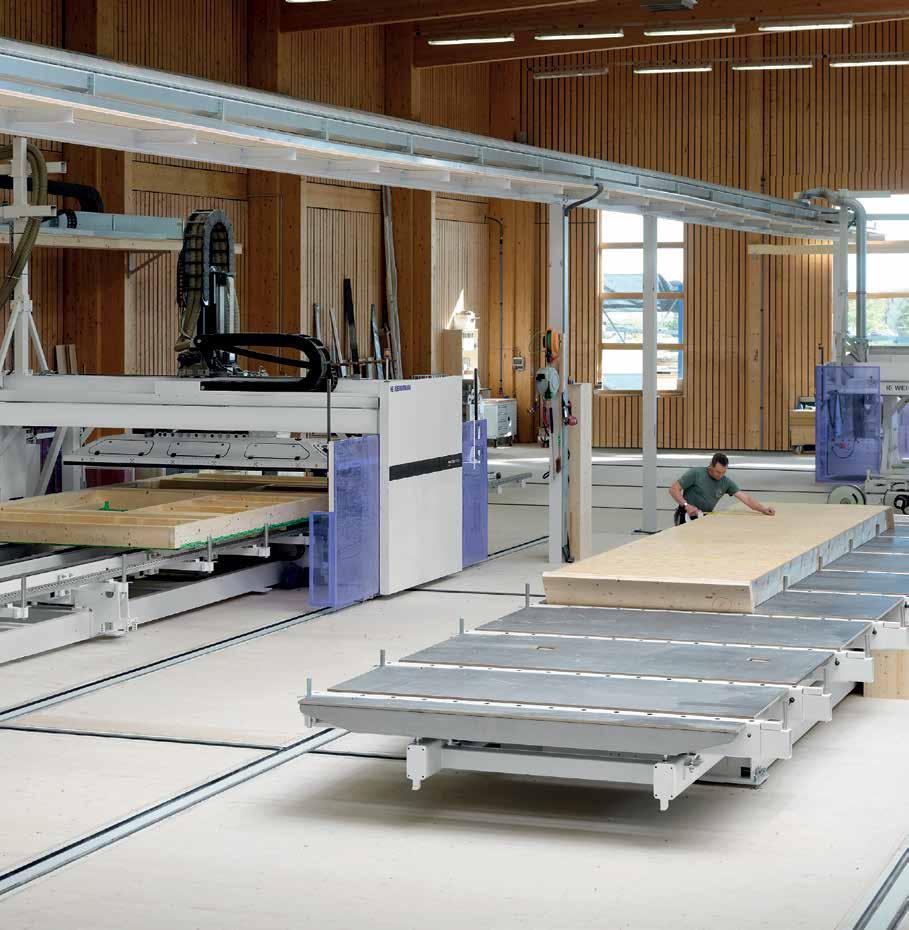
State-of-the-art technologies for prefabrication enable efficient production of the highest quality. Together with the experts from WEINMANN, System TM and Kallesoe, HOMAG Australia offers you the appropriate plant technology for both the joinery and the element construction and develop together with you the production concept that suits you best In this way, you are flexibly positioned - today and tomorrow - with your individual solution.
Volume 34 – Issue 5
Incorporating Australian and New Zealand Timberman. Established 1977. News
Front Cover:
Architects Bates Smart has won the overall Australian Timber Design Award for their outstanding Embassy of Australia in Washington D.C.
Story Page 10.
Publisher and Chief Executive: Hartley Higgins
General Manager: Robyn Haworth
Editor: Bruce Mitchell b.mitchell@ryanmediapl.com.au
Advertising: Andrew Everett a.everett@ryanmediapl.com.au
Adelaide Office (08) 8369 9517
Production & Creative Services: Robyn Haworth
Timber classifieds: a.everett@ryanmediapl.com.au
Adelaide Office (08) 8369 9517
Subscriptions: subs@forestsandtimber.com.au
Adelaide Office (08) 8369 9500
Subcription rates Free Accounts:
Adelaide Office (08) 8369 9500
Postal Address: 630 Regency Road, Broadview South Australia 5083 Phone: (08) 8369 9500
Melbourne Office: Suite 2262, 442 Auburn Rd, Hawthorn VIC 3122
Phone: (03) 9810 3262
Find us on Facebook @AustralasianTimber
Website www.timberbiz.com.au
Printed by Lane Print, Adelaide, SA
Conditions
10 16 24
The opinions expressed in Australasian Timber Magazine are not necessarily the opinions of or endorsed by the editor or publisher unless otherwise stated.
All articles submitted for publication become the property of the publisher. All material in Australasian Timber Magazine copyright 2022 © Ryan Media. All rights reserved. No part may be reproduced or copied in any form or by any means (graphic, electronic, or mechanical including information and retrieval systems) without written permission of the publisher. While every effort has been made to ensure the accuracy of information, the publisher will not accept responsibility for errors or omissions, or for any consequences arising from reliance on information published. 18
elcome to your newlook Australasian Timber Magazine.
After 47 years we are thrilled that Australasian Timber Magazine (formally Timberman) is transitioning to a fully digital magazine format.
Australasian Timber Magazine will continue to expand its unique industry segment’s coverage and promotion of timber manufacturing, technology, design, construction and products as consumers and governments increasingly recognise timber’s carbon saving advantages, Australasian Timber Magazine
This change comes with several exciting benefits for our readers and advertisers alike.
The decision to move from a print magazine to a digital format has been driven by demand from Australasian Timber Magazine readers and advertisers, evolving media consumption trends and the advantages digital platforms offer.
Audiences are increasingly seeking content that is accessible anytime, anywhere, on devices they already use.
A digital magazine meets these needs by offering greater convenience and flexibility, allowing readers to access articles on various devices.
Furthermore, digital platforms provide valuable data analytics, offering insights into reader preferences, engagement patterns, and content performance allowing for more targeted content creation and personalized marketing strategies.
The environmental benefits are another key factor, as digital publishing significantly reduces the carbon footprint associated with paper production, printing, and transportation. This shift aligns with the growing demand for sustainable practices, enhancing the brand’s image among eco-conscious consumers
Finally, a digital format opens opportunities for future innovation such as the potential to incorporate multimedia elements and interactive features.
We hope you like the new Australasian Timber Magazine.
WoodSolutions has launched an updated timber framing campaign with new assets and expanded digital push
The timber framing campaign is now live on the WoodSolutions website with updated resources and assets to boost adoption.
Managed by Forest & Wood Products Australia’s WoodSolutions program, the refreshed and updated page and campaign assets are available free to download by industry to support their timber framing promotional efforts.
The decision to integrate the timber framing campaign under the management of the WoodSolutions program was made to strategically harness its expansive and reputable audience, along with its robust and growing database.
This move aims to maximise the campaign’s reach and
deepen engagement with key stakeholders across the industry, ensuring the messages resonate with a broad and influential audience.
With tens of thousands of users each month, the WoodSolutions website is a powerful platform to promote the pro-timber framing messaging.
The campaign will be supported with a boosted digital campaign that will target key decision makers in large residential building companies and inspire them to embrace the campaign and its co-branding customisation opportunities.
The digital campaign will also engage with proud entrepreneurial tradespeople and share the promotional assets across their platforms and business promotion. The overall aim of these efforts is to support building a better business by promoting the use of renewable timber framing.
As with everything that FWPA and WoodSolutions does, the rebranded creative assets are built on valuable insights gathered over the six years since the campaign’s launch. Key findings from research by the Timber Framing Collective include:
Builders responses:
• More likely to rate sustainability credentials as important in their choice of materials compared to previous year (increase from 27% to 48%)
o The influencers to choose timber framing are:
o Flexibility if plans change
o Easy to renovate
o Renewable and responsibly sourced
• There is an increase in positive sentiment towards the timber industry (74% to 83%) AND about how the timber industry impacts the environment (51% to 72%)
Consumers say:
• Still rate sustainability credentials as an important part of the building process (59%)
• Most consumers would like their builder to provide materials that are good for the environment. However, cost of materials is increasingly important in the decision-making process.
• Influences to choose timber framing are:
o Low cost
o Fast to assemble
o Environmentally Research indicates a strong interest in sustainable building materials among both consumers and builders, presenting our industry with an opportunity to share an impactful sustainability narrative. Specifically, builders favour proof points that highlight forestry replanting practices,
of timber framing. We can effectively communicate through messages such as: “Choose renewable, sustainable timber framing,” “Certified sustainable timber framing is the responsible choice,” and “Your timber framed home stores carbon absorbed from the atmosphere during photosynthesis and helps address climate change.”
It has been found that consumers respond positively to evidence related to sustainability and rejuvenation, particularly statements that are clear and informative such as:
• Timber framing is a natural way to remove greenhouse gases from the atmosphere. Trees grow for around 30 years before they are harvested, allowing them to capture substantial amounts of CO2. Approximately half the dry
timber.
• People have negative perceptions about logging and deforestation and often think cutting down trees is a bad thing. However, when timber comes from a sustainably managed forest, it is one of the most renewable building materials available. In Australia, we replant over 70 million seedlings every year and our softwood plantations grow the amount of timber framing needed for an average home every two and a half minutes.
• Timber has the lowest embodied energy of all mainstream building materials. This means that the entire production process of timber framing—from planting and harvesting to manufacturing, transportation, and installation— uses the least amount of energy.
from each log, decreasing waste, and reducing energy use further.
New assets available for download include:
• A fact sheet which is a quick and easy conversation starter about renewable timber framing.
• A printable poster and pullup banner to promote your sustainable business practices at events.
• A flyer to share with clients to dive deeper into the sustainability benefits of choosing timber framing.
• A white labelled certificate to present your clients with recognition of choosing sustainable timber framing.
• And social media tiles to share across your channels to promote your business’ commitment to sustainability.
Download these resources
Aworld-first engineered wood product made exclusively from locally grown bluegum (Eucalyptus Globulus) timber has been manufactured in Warrnambool, providing a pathway to address Australia’s growing structural timber market demand.
The Green Triangle Forest Industries Hub and Forest and Wood Products Australia, working in partnership with WTIBeam (formerly known as Warrnambool Timber Industries), have unveiled the first of its kind GL18 timber product which can be utilised in everything from flooring to roof framing in both residential and commercial construction.
It is envisaged that the laminated glulam product, produced from glued and finger jointed laminates, will help fill the void from the state’s cessation of native forest harvesting whilst reducing the state’s reliance on imports from volatile offshore markets.
Victoria is Australia’s biggest importer of structural timber sourcing more than 40 per cent of its market base, with demand anticipated to quadruple by 2050 due to population growth and urbanisation.
The Splinters to Structures project, funded by the Federal Government, focused on creating new domestic value from the plantation hardwood trees that are traditionally exported to Asian markets including China and Japan.
Developed after two years of extensive research trials, the GL18 product is capable of being utilised in everything from flooring to rafters in both residential and commercial builds.
Victorian Minister for Jobs and Industry Natalie Hutchins
and Member for Western Victoria Jacinta Ermacora yesterday met with the research group to understand how the product could fit into conventional and modular constructions to fill the state’s housing market demand.
Minister Hutchins said this is an exciting product with wide potential.
“This new world first wood product has the potential to address timber demand and help our booming construction industry who are working around the clock to build more homes across Victoria,” Minister Hutchins said.
Green Triangle Forest Industries Hub CEO Tony Wright said the research group planned to use the findings to undertake commercial trials, building a pathway to commercialisation.
“These commercial trials will help us understand how we best replace native hardwood with plantation hardwoods with a product that already has a broad domestic base. Ultimately, its envisaged that this bluegum GL18 product could be utilised in both domestic and commercial builds and is perfect for use in a prefabricated building, acting as a replacement for concrete or steel,” Mr Wright said.
“The outcome for the sector is reduced reliance on exports, the creation of new local jobs, a costeffective building material with a positive carbon outcome that can fix a shortfall in the domestic market”
WTIBeam owner Edwina Vulcz, whose father Tim Goodall is a key figure in glulam product development and founder of the business, said their team had been “pleasantly surprised” by the trial outcome.
“Historically trials had only looked at structural framing which
failed in a commercial setting because of challenges in sawing. This is a completely different scenario. Bluegum (Eucalyptus Globulus) lends itself to GLT (glue laminated timber) production because of its suitability in a more hands on manufacturing application,” she said.
“This product has the potential to save thousands of dollars in the construction of a home because you have a smaller beam that can be utilised further because of its strength, reducing the need for other materials.”
GTFIH deputy chair and board director of Australian Bluegum Plantations (ABP) Laurie Hein said the low carbon product was paving the way for a more diversified regional market base, addressing the imbalance between supply and demand.
“The Hub has always been
focused on optimising the use of every piece of fibre grown in our region and we see this latest development as an important milestone,” Mr Hein said.
“Whilst we work towards strengthening the intelligence from our existing trials the next major step is to undertake a feasibility study. This will allow us to understand how to take this product to scale through the construction of a manufacturing hub, developing multi-generational jobs and capturing as much economic value in the supply chain as possible.”
The Splinters to Structures project is supported by Green Triangle-based hardwood plantation companies including Australian Bluegum Plantations, Midway Limited, New Forests (SFM Management and PF Olsen).
Increasing reports of imported timber products that could potentially mislead consumers into thinking they’re from sustainable Australian sources, along with recent revelations that up to a quarter of products failed Federal Government inspection – shows the need for stronger protections to inform buyers of where their wood is from, including ‘country of origin’ labelling, according to Australian Forest Products Association CEO Diana Hallam.
“When consumers go into their local hardware store or builders source timber products from wholesalers, they need clear information about what they’re buying, and whether it’s from a sustainable Australian source, or not,” Ms Hallam said.
“We are receiving numerous reports of imported timber and engineered wood products that have been named, presented or marketed in very similar ways to long-standing, leading domestically manufactured products existing in the local Australian market, creating consumer confusion.
“This added to the recent results of the Department of Agriculture, Fisheries and Forestry’s (DAFF) timber testing trial which found around a quarter of imported products tested had an inconsistency with the declared species, the origin, or both – is alarming.
“Earlier this year the Albanese Government sought to strengthen Australian illegal logging laws that AFPA backed
in. Given the recent ramped up reports of dubious products and the result of the DAFF trial, AFPA’s support for the enhanced legislation has been vindicated and we congratulate the Government on its efforts with this issue.
“However, these developments also strengthen AFPA’s argument for timber and wood fibre ‘country of origin’ labelling reforms, similar to our food product labelling regime, that would inform consumers about the origin of the products they’re purchasing.
“The ban on harvesting of Australian native timbers in Victoria and Western Australia has added to the problem with many local furniture and flooring manufacturers now forced to
source timbers from overseas forests that aren’t bound by Australia’s sustainability standards, to continue their businesses. Ensuring these products are clearly labelled has now become urgent.
“When consumers are informed, they make informed choices and it makes sense for timber and wood fibre products to be properly labelled. I look forward to working with the Federal Government on improving consumer information for timber and fibre, and fighting against products that, either intentionally or not, purport to be something they’re not,” Ms Hallam said.
PAGE 9: ATIF members battling illegal imports ATM
The Combilift range of multidirectional forklifts and pedestrian reach trucks will allow
Forest & Wood Products Australia has launched the new FWPA Data Dashboard, an essential tool designed to empower Australia’s forest and wood products industry with access to crucial data, insights and forecasts.
This innovative platform, available as a complimentary benefit exclusively to full levypaying FWPA members, provides a wealth of new information aimed at enhancing decision-making and driving business success across the industry.
“The new dashboard represents a significant upgrade, offering a more advanced platform that enhances usability and functionality.” said Erick Hansnata, Statistics and Economics Program Manager at FWPA.
“With a wealth of new data series added, the new FWPA Data Dashboard is designed to empower our members and industry in their business planning and decision-making processes.”
Key features of the new FWPA Data Dashboard:
• Macroeconomic indicators: Gain insights into GDP and GVA trends, enabling informed economic strategies.
• ABARES Australian Forest and Wood Product Statistics: Access the latest, detailed data specific to the Australian forestry sector.
• FWPA’s softwood data series: Stay ahead with regularly updated industry statistics.
• International forest production and sustainability data: Understand global production metrics and sustainability initiatives
• Monthly trade activities data and forecast: Stay updated with export-import data and forecasts specific to wood products
• Building activities data and forecast: Receive insights on current and projected building activities in the sector
• Detailed research and
analysis: Benefit from regular highlights and updates provided by FWPA’s Statistics and Economics team.
“The FWPA Data Dashboard includes forecast data and comprehensive market analysis, equipping our members with the insights needed to navigate the dynamic landscape of the forest and wood products industry,”
FWPA CEO Andrew Leighton said.
“The platform is designed with future growth in mind, ensuring that we can expand its capabilities based on the evolving needs and interests of our members and the wider industry.” he said.
In addition to its exclusive complimentary availability to full levy-paying members, FWPA will soon introduce a subscription feature, offering FWPA Associate members and other interested users access to the new dashboard for a reasonable annual fee.
FWPA’s public data dashboard will continue to be publicly available via our website.
FWPA’s commitment to enhancing industry competitiveness and sustainability through innovation, research, and reliable data remains at the core of this initiative.
By equipping members with powerful data insights, the FWPA Data Dashboard ensures better decision-making, driving growth and productivity across the sector.
Learn more: https://fwpa.com. au/news/introducing-the-newfwpa-data-dashboard/ and https:// fwpa.com.au/data-dashboardmember-login/
In a world rife with counterfeit or illicit goods, Australian Timber Importers Federation members are facing one of the toughest battles to comply with some of the world’s strictest legislation aimed at combating the trade in illegally logged timber, and they are doing so unapologetically.
“It is a key part of the ATIF Code of Ethics that members not only refrain from dealing with illegally logged timber, but also avoid trading in conflict timber— material that may still be legally imported but is subject to heavy tariffs, such as timber sourced from Russia,” said General Manager Natalie Reynolds.
“Any member found in violation of the Code of Ethics risks their membership in the leading association for timber importers.”
Australia has not adequately invested in planting enough plantation resources to meet the domestic demand for timber. On top of this, insufficient investment in local manufacturing limits our ability to produce many of the timber products we currently import. To reduce inflation and meet the housing needs of the nation, the reality is that we must rely on imports. Simply urging consumers to “buy Australian” isn’t enough — many members of the Australian Timber Importers Federation (ATIF) are also the largest domestic timber suppliers, and for that resource to be used, it must first exist.
“The same regulations apply to domestically processed logs as to imports, and illegal logging is not only an international issue, but also occurs in developed countries, including here,” said Ms. Reynolds.
In making this statement, Ms. Reynolds highlights the repeated instances where forestry companies and
agencies have been caught illegally logging forests — whether by exceeding harvest boundaries, violating regional forest agreements, or breaching other legal requirements. While such violations may often occur unintentionally, the reality remains.
Merely reopening forests closed by State Governments is not a sufficient solution.
These forests do not contain the structural timber needed for house frames, and, moreover, we lack the manufacturing capacity to meet the demand.
To import timber for Australia’s homebuilders, importers are required to perform due diligence and obtain documentation verifying the timber’s source. Under recent legislation, they must also ensure the authenticity of the documentation provided.
However, this can be nearly impossible when the documents are in a foreign language and refer to legal systems abroad. Despite these challenges, ATIF’s importer members do not complain — they make every effort to comply.
“No system designed to prevent organised crime can be effective if enforcement is limited to the point of import. It requires a coordinated, international effort at every stage of the supply chain to truly eradicate it. If addressing organised crime at the import level alone were enough, we would have already eradicated the global drug trade,” said Ms. Reynolds.
Country of origin labelling is also not practically possible. Using the example of the type of board used in every kitchen, there are
• To import timber for Australia’s homebuilders, importers are required to perform due diligence and obtain documentation verifying the timber’s source.
often fibres in those boards from many different sources. So there will not be a single country of origin.
“Australian plantation forest fibre is sent to Asia to be
converted into paper and then affixed to a composite board made up of many different fibres and imported again. This illustrates the country of origin labelling problem to a tee” Ms Reynolds said.
● Structural Engineer: Aurecon
● Fabricators: Embelton, Briggs Veneers, Matilda Veneers, ISEC and RPG
● Builder: Clark Construction
● Photographer: Joe Fletcher
● Location: Massachusetts Ave NW, Washington DC, USA
● Pictures: Joe Fletcher
Architects Bates Smart - one of Australia’s oldest architectural firms - has won the overall Australian Timber Design Award for their outstanding Embassy of Australia in Washington D.C.
The awards – now in their 25th year - were announced on Wednesday night in Sydney with the Professor of Architecture at the University of Tasmania’s School of Architecture and Design and Director of the University’s Centre for Sustainable Architecture with Wood Greg Nolan acting as MC.
The design of the new Embassy of Australia in Washington D.C. was complex,
necessitating a delicate balance between cultural representation, iconic civic presence and practical security considerations.
The inspiration came from Australia’s iconic landscape and embodies the essence of the vast continent.
The building’s transparency was intended to capture the inherent Australian values of
welcomeness and trust, while the interior’s expansive atmosphere embodies the vastness of the Australian landscape.
At the heart of the 20,000 square metre building, a large atrium serves as an orienting space displaying a powerful connection between the ground plane and the sky.
This central atrium establishes
• People’s Choice – Michael Kirby Building - Macquarie University Law School by Hassell Studio and FDC Construction (NSW)
• Sustainability – Berninneit Cultural and Community Centre by Jackson Clements Burrows
• International Projects – Embassy of Australia, Washington D.C. by Bates Smart
• Rising Star – Sarah Shearman from Brother Nature Design for River House
• Residential Class 1 – New Building – Taroona House by Archier
• Residential Class 1 – Alterations & Additions – Verandah Terraces by Phorm architecture + design
• Fit Out - Residential – Northcote House by LLDS and Power to Make
• Standalone Structure – Fernery at Ballarat Botanic Gardens by BALANCE Architecture & Interior Design
• Commercial Building – T3 Collingwood by Hines, AECOM, JCB and Icon
• Public Building – Michael Kirby Building - Macquarie University Law School by Hassell Studio and FDC Construction (NSW)
• Fit Out - Commercial and Public – Embassy of Australia, Washington D.C. by Bates Smart
• Furniture & Joinery - Holocene House by CplusC Architects + Builders
• Australian Certified Timber – Irrawaddy by Incidental Architecture
• Recycled Timber – First Steps Count Child and Community Centre by Austin McFarland Architects
a north south axial arrangement of representational spaces where every visitor is granted an equally immersive experience on entry.
“It’s something all Australians can be proud of”
burn and regrowth. Intricate metallic filigree screens have been sensitively deployed to mediate the interplay of light and shadow in social breakout and office spaces.
The main representational spaces are defined by strong materiality with Australian timber wall panels, that provide both air reticulation and sound absorption, organised around a series of textured horizontal bands that transition from rough to smooth.
This mirrors the protective qualities of the bark during the eucalypt forest’s cycle of growth,
“In a pool of outstanding entrants and finalists, we are proud to present the overall award to the team at Bates Smart. The Embassy of Australia highlights Australian art and culture, with First Nations representation and consideration throughout the design,” Kevin Peachey, Head of Built Environment at Forest & Wood Products Australia and WoodSolutions which sponsored the award, said.
“While an embassy project can present logistical complexities, the execution of this building showcases remarkable creativity and innovation. It’s something all Australians can be proud of. Well done to everyone involved.”
Judges are an integral part of the Awards. Due to the range of applications timber is used for, judges come from a variety of building professions to ensure every aspect of the design is scrutinised and appreciated.
PROFESSOR OF ARCHITECTURE
sustainability judge for the Australian Timber Design Awards. Rebecca is now the Chief Executive Officer of Planet Ark, a position testifying to her dedication to environmental causes. With over 20 years at Planet Ark, she’s been pivotal in championing large-scale environmental projects, such as planting 26 million trees and recycling initiatives. Rebecca’s insights will be invaluable as the organisation pivots to critical environmental challenges like transitioning to renewables and fostering a circular economy. Drawing from her extensive environmental stewardship and her passion for sustainability, Rebecca will undoubtedly bring a unique perspective to the judging panel. The Australian Timber Design Awards welcomes her expertise and commitment.
and a Senior Lecturer in Structural Engineering at the University of Sydney (USyd). He is also an Australian Research Council (ARC) DECRA Fellow. His research expertise includes the development of sustainable methods for recycling wastes (including wood waste), bio-based construction materials, structural health monitoring, and timberconcrete connections. He has secured over three million dollars in research funding and holds various patents for the recycling of composite materials. He has authored two books and published over 120 journal and conference papers. His research has significantly contributed to Australian standards, and he has served on various committees. He currently leads the Smart Materials and Sustainable Structures group at USyd.
pre-construction team, previously at Gensler Australia, working across workplace, sciences and building refurbishments of heritage significance. Over Michele’s 25+ year career she has successfully delivered a variety of workplace projects across Australia, with exposure to projects ranging from up to 60,000m2, has provided opportunities to develop insights into the behaviours and wellbeing of people in workspaces. Working across all aspects of a project she has the design sensibility to guide the team, supporting progressive, sustainable outcomes that align to the client’s brief/budget and programme. Her ability to view projects through multiple lenses enables her teams to thrive through creation and articulation.
Technology Sydney, and host of the TV series
Restoration Australia, and Grand Designs Australia and co-host of Grand Designs Transformations all airing on the ABC. A sought-after host, expert presenter, design judge and regular contributor to academic and popular discourse on architecture, Anthony combines these with his public lectures, curated international tours and architectural experiences, to advocate for the value of good architecture and design.
LISA BARBARA INTERIOR DESIGNER FITZPATRICK + PARTNERS
broad range of commercial and residential projects in diverse sectors. Sustainability and social impact are at the core of her work, both key tenets in her work as an interior designer and now as ESG Manager at furniture retailer, Cult. Her experience in materiality and working with mass timber building interiors, her leadership on Living Building Challenge projects, and her contributions to Architects Declare’s Materials Working Group brings a varied background, view and experience to the awards judging process.
Philip Hopkins
TIMBER dominates the internal design of Phillip Island’s prestigious new multi-dimensional cultural centre in Cowes – and what better place to source much of the timber than Gippsland.
‘Berninneit’ – ‘Gathering Together’ in the Boon Wurrung Indigenous language –encompasses a 260-seat performing arts theatre, a cinema, gallery, library, historical museum, events spaces and community meeting rooms, and was opened late last year.
The project won the Excellence in Timber Design (Sustainability) award at this year’s Australian Timber Design Awards as well as the William Wardell Award for Public Architecture at this year’s Victorian Architecture Awards.
The design cleverly uses space to connect the auditorium,
multi-purpose spaces, library, gallery, museum, meeting rooms, and council offices. These spaces are thoughtfully arranged around a community courtyard formed by retained mature eucalypts. In the two-storey hospitality area, a stunning colonnade of laminated mountain ash complements the interior, which is lined with Spotted Gum flooring and warm, Blackbutt-faced walling.
The Centre’s foyer and auditorium showcase Blackbutt ArmourPanel on walls and joinery, where the rich tones and natural grain of the timber contribute to a warm and inviting atmosphere. This choice not only enhances the visual appeal but also ensures that the space is durable enough to withstand the demands of hightraffic areas, making it a practical and aesthetically pleasing environment for the community.
Sitting at the heart of it is gluelaminated timber (MASSLAM) – huge beams 5.9 metres long and columns 4.2 metres high, all 42cm wide – from Australian Sustainable Hardwoods (ASH) at Heyfield.
“Vic Ash glulam timber is the essential structural element for the building,” said Thom McCarthy, an interior designer with Jackson Clements Burrows, the project architects and designers.
“They form the Grand Hall, the spine of the building connected to all the rooms – the artistic and library at each end, and the function rooms in the centre. They are the three major tenants of the community facility.
“Glulam columns are very striking; we have had tremendous experience with them in student residential projects. We were keen to express them as much as
● Structural Engineer: WGA
● Builder: McCorkell Constructions
● Fabricators: XLam Australia, Australian Sustainable Hardwoods (ASH)
● Photographer: Peter Clarke, Victor Vieaux
● Location: Cowes, Phillip Island, Victoria
possible. They formed a lot of the internal pallet, and at the library end.”
“Regarding the tall columns, a woman came up to me and said, ‘There is steel inside those columns isn’t there?’ No! All are just laminated timber, she couldn’t believe it,” he said, as the columns are so tall,” project architect James Stewart said.
“She thought we had steel columns and capped them.”
The library and offices in the mezzanine floor are all CLT (cross-laminated) mass timber, made from plantation pine, at the X-Lam factory in Wodonga.
Mr McCarthy said the company had experience with CLT in a number of projects.
“We were keen to use Victorian Ash and see these two timber products combined. They are the two key structural components,” he said.
“The devil was in the details – the base plates and how they meet the structural slab. We were keen to do a little timber design solution that expresses all that but defines and emphasises the timber.”
The national business development officer at ASH, Daniel Wright, said ASH was the only Australian producer of mass timber glulam in any volume. MASSLAM 45 is the proprietary strength of ASH’s strong hardwood glulam. According to ASH, European mass timber brands base the name on bending strength; Australian glulam usually follows stiffness. This makes Australian GL17 stronger than European GL28.
“We are competing with imports. MASSLAM 45 clearly shows where we sit in strength,” Mr Wright said.
Mr Wright said ASH did the shop drawings, produced the timber and glued the timber members and profiled them using CNC. CNC (Computer
Numerical Control is a term referring to automated specialised machinery, a process for automating the control of machine tools via software installed in a microcomputer linked to a tool).
“We then delivered to TGA Engineers. TGA did the structural design and purchased the manufactured components from us. They then attached connections, coated them and delivered to the site,” Mr Wright said.
a design perspective, we had a thread and kept building on it,” Mr McCarthy said.
Mr Stewart said one problem occurred with the timber.
“We had the Ash columns, but all these different tones – the acoustic ceilings, the mass timber framing, the library at the end and ceiling and walls mass timber in CLT, the stairs, handrails, so many different wood types – the trick was the ‘pallet’,” he said.
“But it’s quite successful when you go through the space; you feel like it’s all the same, even though there may be Blackbutt here and Ash there, CLT pine … it all fits comfortably together.”
Mr McCarthy said pine has a few more knots and a “bit of attitude”.
first Passive House theatre in Australia,” he said.
“The principle of it is a highly thermally efficient envelope – airtight, high performance glazing, insulation. That works well for the council, which owns it for 50 years, but ongoing energy costs will be very small.”
There was no measure of timber in the building as a carbon store.
“Not in passive house; it’s all about ongoing running costs,” Mr Stewart said.
“Our challenge was to rationalise all the surfaces in a way that expressed that timber without interrupting it too much”
“In terms of design move, it’s free and beautiful. Our challenge was to rationalise all the surfaces in a way that expressed that timber without interrupting it too much,” he said.
Mr Stewart said JCB’s practice was to avoid plaster board at all costs.
“You can’t always do that,” he said.
Design work on the project began in 2015. Several schemes followed before JCB took on the job in 2020. The lockdowns created havoc, but there was still big stakeholder engagement.
Timber’s carbon role was part of the design approach but not as a method of measurement. The timber is both structural and aesthetic. Mr Stewart said the outside of the building was responding to the geology of the island.
“The brick and outside façade are meant to reference the erosion of the cliffs at the Nobbies, the golden beaches … those were the three-dimensional aspect of the façade,” he said.
“The colour hues related to the island’s geology. Go inside, see the obvious relation between the colour of the brick and these beautiful Vic Ash glulam columns.”
TGA, based in Bayswater, specialises in mass timber engineering. Mr Stewart said the columns were spectacular, beautifully finished with brackets and metal plates at the base that were manufactured in their shop. Extra timber was obtained through the Big River Group, which supplied blackbutt that was 15 millimetres thick.
“It creates terrific variation. The visual quality of the timber worked in with the structural columns. This is beautiful timber but put a foot wrong in sealing it can change its appearance. From
“In those discussions, we introduced the notion of a big timber building and the qualities that come with it,” he said. The community got really excited and responded positively to it.
Mr Stewart said the other ambition was to achieve a ‘passive house’ (PassivHaus) building, a style of building from Europe that emphasises energy efficiency that is now increasingly adopted in Australia.
“They are mainly residential buildings, but this is the secondlargest public building in Australia that is ‘passive house’ and the
Mr McCarthy said the local community was very engaged with the ESG (environmental, social and governance) component of the project. Passive house mass timber was important, along with the way building was planned.
“We retained significant eucalypts on site. With the shape of the building, we kept two clusters of trees – native gums, but not heritage listed. Another really nice quality, is with glass here and there, we celebrate the trees, to keep the emphasis on timber,” he said.
“There was no negative feedback on timber, they (the community) were very positive about it. Timber is essential to the entire building.”
- Latrobe Valley Express
The timber framing industry is on the cusp of a major update, with a collaborative research project led by the University of Tasmania and Forest and Wood Products Australia (FWPA).
The Lightweight Timber Framing project funded by Australian Forest and Wood Innovations (AFWI), is part of a broader ‘Future Framing Initiative’ managed by FWPA.
In partnership with over 20 industry stakeholders and eight universities, the project will provide the research and development background to bring contemporary products and systems into the Australian Standards that allow for streamlined design and approvals, with the goal of accelerating house construction across Australia. The Lightweight Timber Framing project is one of eight selected through AFWI’s inaugural $5 million National Open Call for research, which targets sector challenges and promotes innovation. This project has received strong backing, with $1.1 million in contributions from industry partners.
“AFWI is very proud to support this exciting and transformative project, it clearly demonstrates the support of industry, federal government and university sector for collaborative research that targets wood-made, carbonpositive solutions for the needs of the Australian community,” AFWI’s Interim Director, Dr Dean Williams said.
“I am really delighted that AFWI is able to support this highquality project with its enormous potential. Being able to connect our current and future researchers with industry to deliver positive
environmental, economic and social outcomes right across Australia is core to AFWI’s purpose.
“And this is just the start, we have more projects in the pipeline that will deliver positive impacts all along the forestry and forest products value chain.”
Dr Louise Wallis, Research Lead and Deputy Director of The Centre for Sustainable Architecture with Wood (CSAW) at the University of Tasmania said the research project aimed to modernise design and construction practices of timberframed houses.
“We’re focused on making it easier for builders, designers and engineers to work with lightweight timber framing, ultimately speeding up construction while using our forest resources more effectively. This project is all about productivity, there are other stages still to come in future with more universities collaborating,” Dr Wallis said.
Andrew Dunn, CEO of the Timber Development Association and industry champion for this
project, said the current timber framing design and construction practices no longer reflect modern building practices or the use of engineered wood products, making it difficult for timber to remain competitive in the housing market.
“Timber framing is the preferred construction method, but we’re falling behind because builders, carpenters, and engineers need simpler and more straightforward compliance processes,” he said.
“The design and approvals processes are outdated, still based on traditional sawn timber methods, while today’s homes increasingly use engineered wood products. Competing materials don’t face these challenges.”
This research project brings together experts from eight universities and from across the wood products industry with the aim of updating the existing standards to better align with modern construction needs, while ensuring our homes are safe, perform well and are more affordable.
“We’re starting with some straightforward improvements, looking at elements like wall studs, floors, and roofs, and how we can incorporate prefabricated components more effectively onsite,” Dr Wallis said.
“Currently, the construction practices in a deemed-to-satisfy framework, for an easier pathway through design and approvals, aren’t tailored for prefabricated elements, which limits speed and efficiency.
“By removing unnecessary timber elements, such as noggings and ensuring safe work practices that don’t add extra material, we can make the process faster.
“We’ll also explore ways to use more of the current timber resource, which is sometimes rejected, and address issues like timber distortion to keep frames straighter.
“There are a number of innovative solutions identified by the industry, and we’re collaborating with eight universities to tackle these challenges.”
RW Joiners know a thing or two about working with timber.
What started as a small family business 40 years ago has grown into a team of 35 staff and a 4000-square-metre factory.
Now a second-generation family business, RW Joiners are industry leaders, constantly striving to be at the cutting edge of technology while upholding traditional joinery skills that have become a scarcity amongst emerging trades.
While located two hours west of Brisbane in the town of Toowoomba, the team are regularly involved in projects across Australia and often abroad. Recently, RW Joiners were called to provide the joinery for Baillie
Lodge’s newly established luxury accommodation, Southern Ocean Lodge, on the cliffs of Kangaroo Island, South Australia.
The original lodge was destroyed in bushfires that swept across Kangaroo Island in January 2020.
Needing a timber that could withstand the often-tumultuous weather conditions of the island while exuding a sense of luxury, Tasmanian Blackwood was chosen for its durability and alluring timeless beauty.
RW Joiners were thrilled to be working with Tasmanian Blackwood. They worked closely with Britton Timbers, who supplied the 70 cubic metres required to execute the joinery for Southern Ocean Lodge.
“We were looking for a durable timber, and we needed a species that could withstand the fluctuating temperatures often experienced on the island. Many days it’s freezing in the morning, hot by noon and then cool again at night. Blackwood is a very stable timber and can easily withstand this type of temperature change. It was the perfect choice,” says Ross Wilson from RW Joiners.
“Blackwood is a darker timber, which is what we were looking for, but its colour is rich with beautiful variation compared to other timbers similar in strength. It has a lot of character while being warm and inviting, perfect for the lodge,” says Wilson. “It also machines well.”
Selecting the right timber for each application
With extensive experience in using various timber species, Wilson stresses the importance of selecting the right material for the right application.
“The right material must be chosen for the right application. For Southern Ocean Lodge, timber was certainly the hero material, but we wanted to ensure that its use was appropriate depending on the location within the lodge. In wet areas, we opted for a 2-pack finish for durability. In the wine cellar, the space is lined with veneer, but we chose a hardwood where the wine is stacked to ensure the longevity of the timber.”
To ensure consistency
throughout the lodge and in the case of the Flinders Suite, RW Joiners specified Blackwood veneer sheets that matched the timber used in the joinery.
“Britton Timbers provided twenty sheets of Blackwood veneer for the suite, that had a similar tone and texture to the timber used in the joinery.”
“Timber is a natural product, which is what we love about it, so we knew there would be small differences in the timber, but we wanted the timber to blend and to not have too much variation in colour between say the feature wall and the furniture. The veneer provided by Brittons blended beautifully with the joinery features,” says Wilson.
Reflecting on their long history with Britton Timbers, Wilson says Britton’s has remained a consistent, trusted and reliable timber supplier.
“We’ve worked closely with Britton Timbers for 20 years; 90% of the timber we have bought has been through them. In June, we took a trip to Tasmania to look at their mill and the forests, and the trip was fascinating. It was the best work learning trip I’ve ever been on. Seeing the work and care that goes into their whole timber process is mind-blowing,” says Wilson.
Highlighting the importance of sustainability in the timber selection for Southern Ocean Lodge, Wilson says the selection of Tasmanian Blackwood made perfect sense.
“If using sustainable timber is important to you, compared to timbers that have a similar profile to Blackwood found in New Guinea or Malaysia, why wouldn’t you choose Tasmanian Blackwood?”
“Using a local timber was important to the client, and we would have been mad not to choose a local timber. The lodge is very self-sufficient,
environmentally friendly, and celebrates its Australian identity. Tasmanian Blackwood made perfect sense to meet the requirements of the brief.”
Reflecting on the craft of working with timber, Wilson says
a future without timber would be scary.
“A lot of our work involves timber, which we’re proud of. We have a passion for keeping the
“If using sustainable timber is important to you, compared to timbers that have a similar profile to Blackwood found in New Guinea or Malaysia, why wouldn’t you choose Tasmanian Blackwood?”
trade of working with timber going. Our apprentices are all trained on-site as joiners first. It’s a dying trade, but it’s scary to think about a future without timber.”
By Alisa Schoch
If you look at a new housing estate made up of singlefamily houses, you might get the impression that a lot of these houses are like peas in a pod. In contrast to a single-family house off the peg, Engelhardt + Geissbauer sets their focus on individuality. Founded 33 years ago as a small carpentry business in Burgbernheim, in Franconia, Germany, the timber construction company has since become a story of success, with increasing specialization in wood frame construction.
To this day, the innovative solutions from WEINMANN help to equip the company for the future and ensure high quality in timber construction. However, the company is still shaped not only by steadily increasing demand, but also by a turbulent market environment and challenging times.
Together, we discuss major events, superb cooperation and what makes a good partnership. WEINMANN and Engelhardt
“The WEINMANN experts know exactly what they are doing[...]. The solutions are simple for carpenters“
Stefan Bauereiß, Managing Director, Engelhardt + Geissbauer
+ Geissbauer have been working closely together for several years. How did you first come into contact with WEINMANN?
SB (Stefan Bauereiß): Contact was first made in 2012, when we wanted to purchase an assembly table. At that time, we already had two assembly tables from other manufacturers and were thinking about expanding production by one table and broadening our capacities. It was more of a coincidence that we found out about WEINMANN.
This resulted in an appointment with a sales representative from WEINMANN. When we explained our thinking, he looked at us in surprise and said, “It’s not an assembly table you need; you need a multifunction bridge.” Finally, we bought a bridge and at the same time decided that we needed a new hall to house this and the existing assembly tables, which we then built. However, during
the course of the discussions, we also realized that the multifunction bridge only works if the framework conditions also match. Allowing such a machine to fall from the sky into the production hall will not result in an optimal production process. Material supply, disposal and many other factors have to be consistent in order for a specific workflow to occur. It was precisely this issue that became the subject of the first consulting discussion. So that’s how we arrived at our first plant, which was installed in 2013.
After many successful years, the hall fire in 2021 was a major incident. Can you tell us a little more about what happened at the time?
SB: On May 13, 2021, there was a fire in the production hall due to a short circuit on a compressor. Unfortunately, this happened on a public holiday, Father’s Day of that year, which meant that the fire wasn’t
discovered until late. On that day, our wall line, a multifunction bridge and four assembly tables fell victim to the flames. That very evening, we discussed the next steps for the company. We called WEINMANN the same day and explained our problem. It was immediately clear to us that we would not be able to recreate production 1:1, as we were at the absolute capacity limit at the time with 35–40 houses per year. However, we quickly decided to expand production and build a new hall. As a result, we have more than doubled the capacity of the exterior walls. A pure roof line is now installed in the old location that burned down. I wouldn’t wish an experience like this on any colleague with a wood processing business. In the aftermath, you have a great hall and a good production setup — but it’s not a journey you want to go through regularly.
This must have been a very stressful time for you and the team at Engelhardt + Geissbauer. How did WEINMANN support you in these difficult times?
SB: We have always maintained good contact with WEINMANN. We already had a friendly relationship with our
discussions, but we noticed that everyone involved tried to work together rather than against each other. Even when things became really tight and critical, we tried to find joint solutions together with WEINMANN — and always on an equal footing. That was impressive. Assigning blame was never the order of the day. We thus found a solution for every problem, and we eventually achieved the overall goal through these solutions. Looking back, it was even fun.
In your opinion, what are the hallmarks of solid cooperation between two companies?
SB: In a partnership, it’s important to work together on an equal footing. There will always be situations in which one participant is better positioned than the other. But there will also be situations in which it’s the other way around. In my opinion, this balance should not be exploited by either party. In particular, in times of material shortages and the associated price increases, we made note of who we can and cannot work well with. My mantra here is to achieve a certain continuity on a level playing field. It’s also fun to be there for each other every now and then — it means that you can get through anything together.
What do you appreciate about working with WEINMANN?
production support from the WEINMANN Academy. Would you recommend WEINMANN solutions to other companies with regard to the range of products and services, and if so, why?
SB: Yes, I would recommend them, because they work. Ultimately, this also includes the development that WEINMANN has undergone. The WEINMANN experts know exactly what they are doing and have implemented numerous systems for a range of customers. The solutions are simple for carpenters. There are other competitors, but the machines for house construction have to be designed properly and be able to withstand certain loads. It’s not just a table, a bridge or software that brings success — all influencing components in a system must be ideally coordinated with one another, and WEINMANN is streets ahead in this regard.
Your company has developed steadily over the years. What’s the outlook for the future? How will your company continue?
salesperson Stefan Rach — he looked after us very well back then. Without WEINMANN, we would not have been able to rebuild in the time it took. My aim was to be producing again a year after the fire, which included the construction of a
new hall and a new production line. Despite all obstacles, we managed to complete the new hall by Christmas 2021, which meant that WEINMANN was able to begin setting up the system the following January, as agreed. Of course, there were
SB: I appreciate that we act on an equal footing and do not exploit each other. This is fun, and for me, essential for long-term cooperation.
In the past, you have not only relied on systems from WEINMANN, but you have also used services such as
SB: For us, the aim is to continue to grow every year. I still see a lot of potential in multistory residential construction and commercial construction. This is the segment in which we want to be even more active. In general, I think timber construction in Germany still has a long life ahead of it. I think that at Engelhardt + Geissbauer, we are now very well positioned, particularly due to our latest investment in the exterior wall line.
NEVILLE Smith Forest Products is a trailblazer in Tasmania’s forestry sector, renowned for its commitment to sustainability, innovation, and responsible sourcing.
During a visit to NSFP’s Mowbray facility in Tasmania, Matt de Jongh, Sustainability Manager at Responsible Wood, had the opportunity to explore the company’s operations and discuss their approach to sustainable forestry practices with Brett Stevenson, Group Forestry Resource Manager at NSFP. Who is Neville Smith Forest Products?
Neville Smith Forest Products is a leader in the timber industry, with a heritage spanning over 100 years. NSFP is known for producing high-quality hardwood products, all sourced from sustainably harvested regrowth and plantation forests.
guiding principle. The company sources all its timber from Responsible Wood-certified forests, which ensures that the timber is sustainably harvested, and the forests are managed in a way that promotes regeneration and biodiversity.
“NSFP’s approach to sustainability is truly impressive,” notes Matt. “They take responsibility for the entire lifecycle of their products, from how the timber is harvested to how they utilise by-products like sawdust and off-cuts. It’s a zerowaste philosophy that’s setting new standards in the industry.”
our business,” explains Brett. “It’s not just about meeting regulatory requirements; it’s about demonstrating our commitment to sustainability and giving our customers confidence in the products they’re buying.”
For Matt, the certification is a clear signal that NSFP is committed to doing the right thing. “Responsible Wood certification guarantees that NSFP’s products are sourced sustainably. It shows that they’re leading the way in responsible forestry practices, and that’s something to be proud of.”
Certified Quality and Innovation
They were among the first in the timber industry to embrace sustainable forestry practices, holding PEFC certification for their commitment to environmentally responsible harvesting.
“Our focus has always been on sustainability and innovation,” says Brett Stevenson. “We believe in using every part of the tree and finding ways to add value to the timber we harvest. This is at the core of what we do and drives us to continually improve.”
NSFP’s products are used across Australia in building, construction, and consumer sectors, known for their durability and exceptional quality. The company’s ethos revolves around respect for the environment, ensuring that every piece of timber is sourced and processed with care.
Commitment to Sustainability
Sustainability is not just a catchphrase at NSFP; it’s a
One of NSFP’s most innovative initiatives is its pellet processing facility at their Dry Mill in northern Tasmania. This facility converts waste from the milling process into high-value wood pellets for heating and cooking, ensuring that nothing goes to waste. This initiative earned NSFP the EPA Sustainability Award for Tasmania in 2020.
“Our wood pellet facility is a testament to our commitment to reducing waste and maximizing the value of our resources,” says Brett. “By converting sawdust and off-cuts into pellets, we’re not only reducing our environmental footprint but also providing a valuable product for consumers.”
Responsible Wood Certification
NSFP holds Responsible Wood certification, which assures that their timber products are sourced from sustainably managed forests. This certification is part of their long-standing commitment to responsible forestry practices, ensuring that their operations meet the highest environmental, social, and economic standards.
“Having Responsible Wood certification is essential to
NSFP is recognized for its commitment to quality and innovation. The company continuously invests in research and development, finding new ways to enhance the value of their timber products. Their TimberBuild brand, for example, transforms timber shorts—traditionally a byproduct of the milling process— into functional and beautiful timber panels used across Australia.
“We’re always looking for ways to innovate and add value to our timber,” Brett explains. “Our TimberBuild panels are a great example of how we turn what would have been waste into a high-quality product. It’s about making the most of our resources and ensuring that nothing goes to waste.”
NSFP’s ability to combine quality with sustainability has made them a leader in the industry, providing products that not only meet the highest standards but also help protect the environment.
The Importance of Certification
Certification is increasingly important in today’s environmentally conscious marketplace. For NSFP, their Responsible Wood certifications
are a key part of their business strategy, ensuring that their products meet the growing demand for sustainable materials.
“Certification is critical for us,” says Brett. “It gives us credibility in the marketplace and ensures that our customers can trust that the products they’re using are sustainably sourced.”
Matt adds, “As sustainability becomes more central to building and construction projects, having certified products is becoming a competitive advantage. NSFP’s certification under Responsible Wood means they’re wellpositioned to meet this growing demand.”
Collaboration is at the heart of NSFP’s success. The company works closely with local communities, indigenous groups, and other stakeholders to ensure that their forestry operations are not only sustainable but also socially responsible.
“Collaboration is key to what we do,” says Brett. “We work with a range of stakeholders to ensure that our operations benefit everyone involved, from the local communities to the environment.”
For Matt, this collaborative approach is a shining example of how the forestry industry can work together to achieve shared sustainability goals. “NSFP’s partnerships with local communities and other
“Having Responsible Wood certification is essential to our business”
stakeholders are a model for how the industry can work together to create positive outcomes for people and the planet.”
The Role of Responsible Wood Responsible Wood plays a crucial role in NSFP’s operations, providing a framework for sustainable forestry practices and ensuring that their products meet the highest environmental standards.
“Responsible Wood certification gives us the confidence to say that we’re doing the right thing,” says Brett. “It provides a clear set of guidelines that help us manage our forests responsibly and ensure that our products are sustainable.”
Matt adds, “Responsible Wood is about more than just certification—it’s about fostering a culture of sustainability in the
forestry industry. Companies like NSFP are leading the way, showing that responsible forestry is not only possible but also profitable.”
For businesses looking to follow in NSFP’s footsteps, certification under Responsible Wood or PEFC offers a pathway to demonstrate commitment to sustainability. With consumer demand for certified products on the rise, certification can provide a competitive edge in the marketplace.
“If you’re thinking about certification, my advice is to go for it,” says Brett. “It’s a rigorous process, but the benefits are worth it. Not only does it help protect the environment, but it also opens up new opportunities
for your business.”
As Matt reflects on his visit to NSFP, he sums up the experience: “Neville Smith Forest Products is a shining example of how sustainability and innovation can go hand in hand. Their commitment to responsible forestry practices, combined with their dedication to quality, sets them apart in the industry. It’s inspiring to see a company so focused on doing the right thing, both for their customers and for the environment.”
NSFP’s journey showcases the future of sustainable forestry—one where environmental stewardship, innovation, and collaboration come together to create lasting value.
The University of Melbourne recently hosted the International Conference on Decarbonising the Building Industry, bringing together global leaders, researchers and industry professionals, including leaders in forestry, timber production and sustainability.
A standout session of the conference was the panel discussion on “How to Maximise the Use of Australian Forest Resources to Decarbonise the Building Industry.” Moderated by Dr. Bill Leggate from the Department of Primary Industries, the session explored the pivotal role of Australia’s unique and sustainably managed forests in providing timber—a strong, versatile, cost-effective, and carbon-negative building material—to support housing and construction industries in addressing climate challenges.
“Australian forests are not only unique in their biodiversity but also hold the key to achieving significant carbon reductions in our built environment,” Dr. Leggate said. “Our panel today is an incredible lineup of experts who will delve into the innovative ways we can leverage forest resources sustainably.”
Shona Heading from HQ Plantations emphasised the importance of sustainable forest management as the foundation of a low-carbon construction industry. “When forests are responsibly managed, we can achieve a balance that supports biodiversity, produces high-quality timber, and sequesters carbon,” Shona noted. “The first step in decarbonising the building industry is ensuring our forests continue to be well-managed for generations to come.”
Katie Fowden from the Hyne
Group highlighted the role of engineered wood products in replacing emissions-intensive materials like steel and concrete. “Engineered timber products like cross-laminated timber (CLT) are game-changers. They not only reduce embodied carbon but also enable faster and more efficient construction processes,” Katie said. “This was further supported during the recent visit of His Majesty, King Charles III to the XLam supplied Cowper Street Development in Sydney. The King, through the Kings Trust Australia, very much focuses on environmental credentials.”
She urged the construction industry to prioritise homegrown, certified timber products to amplify environmental and economic benefits.
Professor Tripti Singh from the Centre for Timber Durability and Design Life focused on the importance of advancing timber durability and Circularity to increase its adoption in largescale projects. She highlighted how circularity principles, such as designing for reuse, recycling, and minimising waste, can significantly extend the lifecycle of timber products, “Investing in research and innovation to enhance the longevity of timber structures is crucial,” Tripti said. “When we ensure that timber products are durable and adaptable to Australia’s climate conditions, we not only make them a more attractive option for construction on every scale but also align with sustainable practices by reducing environmental impact and supporting a circular economy.”
Chris McEvoy of Radial Timbers offered a perspective on timber’s versatility. “Australian forests provide us with hardwoods and softwoods that meet a wide
• Matt de Jongh (Responsible Wood), Chris McEvoy (Radial Timbers), Katie Fowden (Hyne Group), Shona Heading (HQ Plantations), Professor Tripti Singh (Centre for Timber Durability and Design Life) and Dr Bill Leggate (Department of Primary Industries) during a panel discussion at the International Conference on Decarbonising the Building Industry conference,.
range of construction needs,”
Chris said. “From structural beams to flooring and cladding, our timber products are adaptable to the modern architect’s vision while helping reduce carbon footprints.”
Matt de Jongh from Responsible Wood underscored the importance of certification in ensuring that timber is sourced sustainably and responsibly.
“Certification is not just a label; it’s a commitment to protecting our forests while supporting a sustainable timber industry,” Matt said. “It gives architects, builders, and consumers’ confidence that the materials they’re using contribute positively to the environment.” Matt also highlighted the need for stronger collaboration across the supply chain to address challenges such as embodied carbon measurement and consumer awareness. “Our industry has a tremendous opportunity to lead in sustainability, but it requires all of us—forest managers, manufacturers, researchers, and policymakers—to work together.”
Rhianna Robinson from
the Department of Primary Industries, who played a key role in organising the session, reflected on the importance of the conference in bringing experts together. “This session showcased the best of what Australian forestry and timber sectors have to offer,” Rhianna said. “The insights from the panellists demonstrated we have the capability, skills and the products to significantly decarbonise the building industry today,” she said.
The panel concluded with a resounding call to action: to unlock the full potential of Australian forest resources while maintaining a steadfast commitment to sustainability. “Australia has the resources and expertise, to support decarbonisation in the building sector,” Dr. Leggate said in closing. “If we continue to innovate, collaborate, and champion sustainable practices, our forests can continue to supply strong, versatile, cost effective and carbon negative timber to manufacture residential and commercial buildings.”
Advanced Truss Systems (ATS), a family-owned business based in Morningside, Brisbane, has stood as a beacon of reliability and innovation since 1988.
Specialising in Timber Trusses, Wall Frames, Floor Systems, and Timber Products, ATS has supported builders across SE Queensland for decades.
Last year, the company made a significant investment in the Multinail Automated Roller Plant System to improve their production processes. We sat down with Mark Osmand, the owner of Advanced Truss Systems, to learn more about their decision to invest in the Multinail Automated Roller Plant System and its impact on their operations.
For over ten years, Mark Osmand, owner of ATS, had contemplated the potential benefits of incorporating the Multinail Automated Roller Plant System into his operations. The challenge of finding skilled staff,
the necessity to optimise factory space, and the unwavering pursuit of product quality were all pivotal in choosing this advanced system.
“Skilled jig setters were hard to find, and the quality of the product depended on having them. The Automated Roller Plant System made perfect sense—it eliminated the need for extensive setup time and allowed us to rethink our factory layout,” Osmand explains.
Since its implementation in June 2023, the Multinail Automated Roller Plant System has revolutionised ATS’s production efficiency.
“We’ve managed to amalgamate different processes and streamline production, with setup times reduced from 20 minutes to as little as 10 to 20 seconds,” says Osmand.
This leap in efficiency has not only improved the speed of production but also enhanced the overall quality of the trusses.
Moreover, the system’s ease
of use has been a game-changer for the ATS team. Training was swift, and staff quickly adapted to the new workflow, which now runs smoother than ever. The reduction in the number of staff needed, without compromising output, has made operations safer and more efficient.
One of the standout benefits of the new system has been its impact on workplace safety. The Multinail Automated Roller Plant System significantly reduces manual handling and heavy lifting, leading to fewer workplace injuries and a fresher, more energised workforce at the end of the day.
“Our guys are much fresher, and we have fewer health and safety concerns,” notes Osmand, adding that the system’s improvements might also help attract new staff.
Quality has also seen a noticeable uptick. “Even on the first day, I noticed how well the trusses went together. The joints are tighter, the finish is better, and
customers have provided positive feedback on the enhanced quality,” says Osmand.
Financially, the investment in the Multinail Automated Roller Plant System is already paying dividends. ATS is on track for a return on investment in just three to three and a half years. This rapid ROI, coupled with the system’s durability—”it’s Multinail machinery; it will last”— underscores the soundness of the investment.
The new system has also provided ATS with a competitive edge, particularly in handling larger, more complex commercial jobs. “We used to dread doing commercial jobs because they were bigger, heavier, and slower,” Osmand admits. “But this machinery just eats it up. We look forward to commercial jobs now!” Looking ahead, Osmand hints at the possibility of expanding into floor trusses, which would require additional equipment. However, the immediate focus remains on maximising the potential of the current investment.
The partnership between ATS and Multinail has been a longstanding one, marked by mutual trust and a shared commitment to excellence.
The successful integration of the Automated Roller Plant System is a testament to this relationship and has positioned ATS for continued success in the prefabrication industry. With improved efficiency, enhanced quality, and a safer work environment, Advanced Truss Systems is not just keeping pace with the industry—it’s setting the standard.
Matilda Veneer is a name synonymous with innovation and quality in the timber industry.
As a leading manufacturer of decorative timber veneers, the company has built a strong reputation for sourcing beautiful woods and transforming them into distinctive products used in architectural projects worldwide.
On a recent visit to Matilda Veneer’s headquarters on the Gold Coast, Matt de Jongh, caught up with Anthony Wardrop, General Manager and Meg
Berry, Architectural & Technical Representative, to explore the company’s commitment to responsible sourcing and how their Responsible Wood certification helps their business demonstrate their sustainability credentials.
Matilda Veneer is Australia’s leading producer of native timber veneers and sources high quality veneer from around the world. who have more recently added a selection of specialty plywoods to their product range. The
company works with designers, panel manufacturers, joiners and craftspeople across Australia, offering high-quality products that adorn iconic structures like the Sydney Opera House, Melbourne Cricket Ground, Queensland Performing Arts Centre, Phillip Island Visitor Centre and the Australian Embassy in Washington DC.
“Our ethos is simple,” says Anthony. “We source exceptionally high-quality wood fibre, producing veneers that are not only functional but also stunning. It’s this quality that sets our products apart. We pride ourselves on giving our customers access to something truly natural, unique and beautiful.”
This approach has earned Matilda Veneer a place in awardwinning architectural projects, making them a trusted supplier for prestigious builds across Australia and beyond.
Sustainability isn’t a
greenwashing buzzword at Matilda Veneer - it’s a guiding principle for how they source timber. The company works within an ethical framework that makes sure timber is only sourced from forests that stay forests, where they stay healthy and keep growing.
“Sustainability is embedded in everything we do,” says Anthony. “From the way we source our timber to how we manufacture our products, we’re focused on ensuring that future generations will enjoy the same access to natural resources.”
Matt adds, “I was really impressed with Matilda Veneer’s approach to sustainability. They are very conscious of the perceived environmental impacts of the timber they use, and they actively seek ways to demonstrate their environmental responsibility and reduce their footprint.”
When it comes to optimal use of a forest and wood product, timber veneer is one of the most efficient ways to use wood, with
one cubic metre of log producing approximately 1,000 square metres of veneer. This efficiency, combined with the renewable, recyclable, and biodegradable nature of the material, makes timber veneer a highly sustainable choice.
Matilda Veneer’s commitment to sustainability is underpinned by its chain of custody certification under the Responsible Wood Certification Scheme. This certification guarantees that the timber used in their products comes from sustainably managed forests and controlled sources, ensuring environmental, social, and economic benefits for all stakeholders involved.
“Having the Responsible Wood certification means a great deal to us,” explains Anthony. “It’s a validation of our efforts to source timber responsibly and manage our supply chain in a way that minimises harm to the environment.”
Matt agrees with this sentiment: “Responsible Wood certification isn’t just a label; it’s a promise to uphold high standards. Companies like Matilda Veneer are leading the way in responsible timber production, and their certification ensures that architects, designers, and builders can trust the sustainability of the materials they use.”
At the heart of Matilda Veneer’s operations is their drive to innovate while maintaining the highest levels of quality. They work with Australian hardwood species that are quite difficult to process, but their commitment to excellence in veneer manufacturing means they can offer products that are both beautiful and functional, giving designers the option to select from an extensive range of timber species to compliment other project material selections, many
of which tell a story of the client or location of that project.
“Whether it’s for a commercial build or a residential project, architects & interior designers want something natural, unique and beautiful, and we deliver that,” says Anthony. “But it’s not just about aesthetics—our products meet rigorous quality standards. Our customers know they’re getting veneers that not only look great but are built to last.”
For companies like Matilda Veneer, certification is essential, not only from reputational perspective but also from a business one. Certified products are increasingly specified as both consumers and industries alike look for ways to reduce their environmental impact.
“Responsible Wood certification is crucial in today’s marketplace,” explains Anthony. “It gives our customers confidence that the materials they’re using are sustainable and ethically sourced. We’ve seen a growing demand for certified products from all sectors of the construction industry.”
Matt added: “More and more, we’re seeing sustainability as a core consideration in project specifications. Responsible Wood certification allows companies like Matilda Veneer to demonstrate their commitment to ethical practices, helping them stay ahead in a competitive market.”
Strengthening Collaboration
One of the key takeaways from Matt’s visit was the importance of understanding the market’s needs. By working closely with suppliers, distributors, and Responsible Wood, Matilda Veneer ensures they maintain high standards across the board.
“Matilda Veneer is a great example of how the whole forest products sector can work together to achieve shared goals around sustainability. By fostering strong relationships with all stakeholders,
they ensure that their products meet the highest standards from forest to final product.”
Responsible Wood plays an important role in ensuring that companies like Matilda Veneer can confidently offer certified products that are traceable to an original well managed forest. The certification provides a framework that promotes sustainable forestry practices, ensuring that wood products are sourced responsibly.
“Without Responsible Wood, it would be much harder for businesses like ours to verify the sustainability claims of our supply chains,” says Anthony. “The certification gives us—and our customers confidence in the products we bring to market.”
Interested in Certification?
For businesses exploring chain of custody certification, Matilda
Veneers offers valuable insight. Certification can provide not only a right to play, but a competitive edge in today’s eco-conscious market, ensuring that products meet the increasing demand for sustainability.
“If you’re thinking about getting certified, I’d say go for it,” encourages Anthony. “It’s a rigorous process, but the benefits far outweigh the effort. Not only does it help protect the environment, but it also opens doors to new business opportunities.”
Matt reflected, “It’s inspiring to see a company like Matilda Veneer not only excel in their craft but also embrace their responsibility to the planet. Their commitment to sustainability, innovation, and quality is truly something to be admired.”‘
By David McElvenny1
This is the third article in a series on the principles of designing an internal training system for your employees.
My overall premise is that many workers in the timber industry tend to miss out on good quality training because their employers are unable to find relevant external courses that meet their specific needs.
In lots of cases, this means that the only option left is for employees to work alongside more experienced operators and learn their skills on the job. Sometimes this works well, but more often it doesn’t – since there are no structured plans to guide their progress and no defined performance benchmarks to achieve.
In the first two articles I talked about the pros and cons of managing your own training regimen and the differences between non-accredited training (delivered internally) and accredited training (delivered by an RTO). In this article I will look at the fundamentals of developing training and assessment resources for your in-house system.
I’ll use the term ‘training module’ to describe the materials used to train and assess a worker in a particular task. When you define the scope and depth of learning in your internal training module, you are basically writing your own version of a ‘unit of competency’, which is the nationally-recognised specification that RTOs are required to use when they deliver accredited training.
What should the learning materials look like?
Some companies base their internal learning resources directly on their own standard operating procedures or safe work method statements. If these existing documents already provide all the details you need for a particular task, you might decide to use them as they stand. However, it’s often the case that more information is required to fill in the theoretical knowledge that helps employees to understand why certain jobs must be done in a particular way and what the risks are in not doing them that way.
The extra background information can come from various sources, including manufacturer’s operator manuals, Australian Standards, codes of practice and industry guidelines. It can also come from the vast store of knowledge that your supervisors and key operators are carrying around inside their heads – although extracting this information and converting it into an easy-to-understand set of written procedures can be an onerous task in itself.
I’ll talk more about writing reader-friendly materials for workers with poor literacy skills in the next article in this series.
Is an assessment tool necessary for all training modules?
All training modules should comprise a learning resource plus a well-structured assessment tool. Proper assessment is a very important part of the training process. It lets you specify the benchmarks of performance that are acceptable for the task, and
allows you to gauge whether a learner has achieved the standard you expect from them.
Some companies like to separate the roles of trainer and assessor, so that one person carries out the training function and a second person assesses the learner when the trainer thinks they’re ready. However, you can combine these two roles as long as the trainer/assessor remains objective and diligent when it comes time to make a judgement about whether or not the learner has met the performance requirements.
A common design for an assessment tool would include the following components:
• background knowledge test (either written or verbal) – to be completed by the learner at the beginning of the assessment process
• practical demonstration checklist – to be completed by the assessor as they observe the learner demonstrating each performance element
• supervisor statement – signed off at the end by the learner’s supervisor to confirm that they’re consistently applying their skills and knowledge on the job while doing that task.
The assessment tool should be as specific as possible. For example, the practical demonstration checklist should state exactly what the assessor needs to see the worker perform on-the-job and be free of any generic statements or waffle.
It is possible to develop assessment tools with an eye to the relevant units of competency that would apply if the training
module had been nationally accredited. This makes it easier for the learner to use their completed training modules as evidence towards a ‘recognition of prior learning’ (RPL) application if they enrol in a formal qualification with an RTO at some time in the future.
Has modern technology changed everything? In 2024, this training manager would have a large whiteboard on the wall instead of floorto-ceiling bookshelves, laptop computer instead of a clackety typewriter, and maybe a nicotine patch instead of the pipe.
But what about his thinking processes as he develops the company’s training materials? In my view, no change at all.
The underlying qualities that enable a training resource to hit the mark with learners are the same now as they have always been, regardless of the technology used – sound structure, clear language, relevant content material, and well-defined goals.
Creating public spaces that are both functional and engaging, is a goal for most architects and designers, and timber remains a key element in helping shape these environments.
Timber’s appeal lies not only in its durability and versatility but also in the sensory experience it offers. Research has shown that wood resonates with us on a sensory level – its natural textures, warmth, and even subtle scent evoke a unique feeling that is hard to achieve with other materials. This sensory connection encourages architects and designers to select timber for its ability to create spaces that are both visually striking and deeply engaging.
While timber has long been a staple in design, valued for its natural warmth and aesthetic versatility, we are now witnessing its use in innovative ways not only in residential but increasingly in commercial designs. New techniques and technologies are transforming timber into a medium for creating designs that are not only practical but also aweinspiring in their beauty.
“One of the main challenges in designing public spaces is finding materials that can withstand heavy traffic while still maintaining their aesthetic appeal Timber meets this challenge head-on, offering a solution that is both resilient and visually captivating. Through new technologies, we’re able to push the boundaries of what timber can achieve, which in turn is allowing architects and designers to create environments that not only stand the test of time but also contribute to the user experience through a good blend of practicality and sensory appeal,” said Stuart McGonagle, Sales & Marketing Manager of Big River Group.
Timber plays a unique role in public architecture by providing
a sense of connection and community. Its natural textures and warm tones evoke feelings of comfort and familiarity, drawing people in and encouraging them to linger. Big River Group’s products, such as ArmourPanel and ArmourCab, are known for their ability to create inviting and engaging environments that resonate deeply with individuals.
For instance, the Munro Development and Narrm Ngarrgu Library and Family Services, a key feature of the renewal of the Queen Victoria Market Precinct in Melbourne – designed by the award-winning Six Degrees Architects – uses Spotted Gum ArmourPanel extensively on walls, ceilings, and joinery. This design choice created spaces within the complex that feel harmonious and connected to nature, inviting community members to interact and engage with their surroundings. The warmth and tactility of timber brings with it a sense of belonging, making the library not just a place for books, but a hub for community engagement. Recognised with the
2024 Dimity Reed Melbourne Prize and several accolades for Public Architecture as part of the Victorian Architecture Awards, this project is the perfect example of how timber can enhance the emotional and functional qualities of public spaces.
Timber’s authentic aesthetic qualities make it an ideal choice for enhancing the visual appeal of public architecture. Big River Group’s timber products, such as Blackbutt, Spotted Gum, and Hoop Pine, offer a range of finishes that allow architects to create visually stunning and functionally effective spaces.
Combining the stunning intimacy of native timbers with the rugged durability of a precisionengineered structural product, Big River’s ArmourPanel is a decorative plywood that has become a popular choice due to its distinctly authentic, natural appeal. “Architects appreciate the unique grain and warm tones of our timber products, which provide a sense of intimacy and connection to nature,” said Stuart. Each ArmourPanel sheet, with its preserved unique grain structures, offers an individual and natural look, making no two sheets alike.”
FTMA, in collaboration with Wood Products Victoria, the Gippsland Forestry Hub, and the Department of Agriculture, Fisheries and Forestry, launched an important document on October 18, 2024.
The recently published Steps Towards a Greener Future is a report specifically highlighting what is needed to support an environmental trajectory for the future of Australian housing.
The concise and researched findings within the report, makes 23 recommendations on how Australian government could meet their environmental responsibilities (Net-Zero by 2050), as well as delivering their housing commitment of 1.2 million new homes over the next 5 years (National Housing Accord 2022). It looks at the different issues and provides a solution within four main categories. The report focuses on carbon capturing, sustainable forestry, engineered wood design with offsite prefabrication, and ultimately the important message of ‘if we can build out of timber, we must’. It goes into details about carbon storage and how - like many other countries are fostering - Australia can make the best choices now to protect and contribute to global emission targets, as well as looking after the critical needs of housing its citizens.
The Morwell Innovation Centre (Victoria) hosted the launch which featured FTMA’s CEO Kersten Gentle, Wood Products Victoria’s Dr. Alastair Woodard, and Heartwood Unlimited Managing Director Jon Lambert. Kersten introduced Carbon Warrior, FTMA’s environmental project arm, and talked about the original CW policy proposal 4 Steps Towards a Greener Future, carbon
KAT WELSH EDITOR/COMMIUNICATIONS COORDINATOR
FTMA AUSTRALIA
capturing, investing in renewables, and legislating requirements for bio-based materials in future construction. She exampled other countries that are already legislating the use of renewable materials into construction policies, and the necessity for Australia to follow suit. Alastair introduced the Steps Towards a Greener Future and gave an inspiring outlook over just how simple the answers could be with the right policies in place.
“The building sector has a huge impact. We use 12-20% of the water consumption, 25-40% of energy use, we produce 30-40% of Greenhouse Gas emissions, and 25-40% of solid waste generations,” said Alastair. He spoke about looking at the impact of our choices when it comes to thinking about the bigger picture and the need to account for life cycle assessments in the future of construction - how the materials were mined, produced, shipped, erected, maintained, as well as end-of-life decisions (embodied and operational emissions). The report also focuses on the notions of circular economy and decisions for the beginning and end of intended purpose, that must be accounted for.
‘I can’t tell you what an
opportunity this is at the moment for the forest and wood products sector. We’ve got this global concern about this big bad CO2, and we can do something really positive about it. It’s a once in a generation opportunity,’ he said.
The third presenter, Jon Lambert, gave a realistic insight into the sustainable forestry industry within Australia and the challenges that are faced by the sector when it comes to current government regulations. Currently, up to 40% of Australia’s demand for timber comes from overseaswith a country so vast it begs the question why aren’t we planting more?
A panel discussion followed, particularly focusing on what the contents of this report can do to assist Australia moving into the future - supporting the environment, its people, economy, and industries. It was clear that governments, federal and state, need to drive a significant change.
For FTMA, Steps Towards a Greener Future is a concise way to keep driving awareness and education for initially the frame and truss industry, but a much bigger picture that surrounds us when it comes to sustainable materials.
This was a question that was raised recently on the TTIA Industrial Hotline by a TTIA member seeking clarification about hiring a new worker, and whether there is a specific obligation to make appropriate checks as to the worker’s right to work in Australia.
The law indeed does provide a positive duty for employers to do their due diligence in this situation.
It should be made clear that the Fair Work Commission is on the look-out for employers who don’t comply with this obligation (and the Australian Border Force too!), and, under the Migration Act, employers could be fined up to $255,000.
This article will talk about your obligations, what could happen if you don’t comply and what you could do to avoid the headache of penalties.
It is your responsibility as an employer to check whether your workers can legally work in Australia. This includes employees, contractors and any other workers you source from labour hire arrangement or recruitment agencies.
And it applies to both paid and unpaid work.
But how do you know someone is illegally working in Australia?
Put simply, a person does not have a right to work in Australia if they are one of two things.
First, those who are illegally staying in Australia. They are called “unlawful non-citizens” – foreign citizens without a valid visa in Australia.
Second, those “lawful noncitizens” who have a valid visa to stay in Australia but with workrelated restrictions. If you’re not well-versed in all the different types of visas and their working conditions – don’t fret!
Head over to the Australian
The last thing you want is the headache of an investigation and heavy fines facing your business.
Under the Migration Act, employers must take “reasonable steps” to check the working status of their employees and contractors.
This includes keeping records of your employees’ working status and making the necessary enquiries.
Don’t turn a blind eye if you suspect a worker doesn’t have the requisite visa status!
rights when they start work with you
• Review any contracts you have with third-party labour hire or recruitment companies to make sure they are also checking the rights of suggested workers
If you have any employees who are on temporary visas, be sure to schedule regular check-ups of their working status.
You need the worker’s permission to access their VEVO details, so make sure you get this permission as part of your onboarding process!
What Happens If You Don’t Comply?
As an employer, you could face penalties if you employ a person who does not have a valid right to work in Australia.You can be fined up to $102,000 (and, for more “aggravated” breaches such as forced or exploitative labour, this number can go up to $255,000).
In 2013, the law was changed to introduce stricter provisions.
Employers could still face penalties even if they unknowingly employed a person without valid working rights. This new law places a positive obligation on every employer to actively make sure that their employees have valid working rights.
Employers who fail to comply with this obligation could be liable for fines up to $76,500.
It’s also worthy to note that even executive officers could be held personally liable if they:
1. were aware of the breach,
2. influenced the employer in the breach, or
3. failed to take reasonable steps to prevent the breach.
Particularly, if you are employing someone who has a temporary working visa, you are obliged to continue to check their work rights until their employment contract ends.
So – how do employees prove that they have valid working rights in Australia?
To prove they have a right to work in Australia, your employees can provide the following documents:
• Australian birth certificate and a photo ID
• Australian citizenship certificate
• Australian passport
• New Zealand passport
• New Zealand Birth Certificate and a photo ID
• Certificate of evidence of resident status
• Valid visa with relevant work rights
To avoid penalties, it’s a good idea to make sure you are proactive about checking your employees’ work rights from the very beginning.
For example, you can:
• Post job advertisements specifying that they must have valid working rights in Australia before applying
• Introduce employee screening processes with compulsory reviews of employees’ work
If you have further questions around employing (or sponsoring) visa-holders, the Department of Home Affairs has a handy resource here.
For any questions about other obligations you have before taking on a new employee, you can view a checklist here.
The Bottom Line
The duty for a business to check whether your workers have the right to work in Australia is something that can often be forgotten.
While you might be employing a person in good faith, you are required by the law to take reasonable steps to check their working status.
It’s a good idea to be proactive because “not knowing” is no longer an excuse.
Investigations are a headache; fines are heavy and the last thing you want is finding out a valuable employee is illegally working for you.
Please call the TTIA Legal Department on (02) 9264 0011 if you need more clarification on this issue.
On behalf of myself and the staff at the TTIA, best wishes for a safe and happy holiday from us all to Members and readers of this industry publication. We look forward to being of service to you in 2025.
Heyfield’s Australian Sustainable Hardwoods is set to become the first company in Australia to manufacture engineered plantation floorboards.
The mill and three other businesses across Gippsland will share in more than $2.3 million in grants through the State Government’s Timber Innovation Fund.
ASH has received $1.6 million to install a new manufacturing line to produce engineered flooring made from plantation shining gum and radiata pine plywood and to expand both its online and retail outlet.
This will make ASH the only company in the country to manufacture this kind of high-value plantation product.
A new retail outlet will sell the floorboards as well as some of their existing products, such as staircase and furniture components. It will also create a market and secure the supply chain for ASH’s expanded line of plantation-based products into the future.
This will help to open new markets as ASH prepares to transition from native timber joinery to products manufactured from plantation timber.
2018
WHEN Hyne Timber released its new Glue Laminated Timber (GLT) campaign earlier this year it wasn’t exactly what you’d expect from an Australian softwood processor.
Playing on the love story Hyne Timber has with Australian pine, and with a focus on building relationships at every stage of the design and construction journey, the new campaign featured plenty of cheeky puns and innuendo… and it certainly got to the heart of discerning clients!
It’s all part of Hyne Timber’s service-based marketing strategy which sees the company working closely with both the specification and construction supply chains.
2013
INNOVATION was the overriding theme at the 2013 WoodEXPO. Held over three days at the Albury Entertainment Centre in Albury, NSW, industry leaders and experts gathered to discuss the future of the wood industry.
Some 15 speakers shared their thoughts on the future of timber processing and its global use on the second day of the expo which was dedicated to the Summit
Summit chair Ross Hampton said the timber industry’s biggest challenge was changing the public’s perspective of the timber industry.
To support the use of timber in construction, Forest & Wood Products Australia is introducing a new industry standard aimed at streamlining compliance for exterior timber wall cladding.
The current complex regulatory landscape often leads to increased time and costs for projects, making timber a less attractive option for builders and designers.
The proposed FWPA Standard introduces a nonmandatory Deemed-to-Satisfy (DTS) solution specifically for exterior timber wall cladding systems. This innovative Standard provides a clear compliance pathway for meeting the condensation and weatherproofing provisions of the National Construction Code (NCC).
“By simplifying compliance requirements, we’re not only reducing costs and project delays but also empowering builders and designers to choose timber as a preferred material,” said Boris Iskra, National Codes and Standards Manager at FWPA.
For commercial projects under NCC Volume One, this standard provides the first-ever compliant DTS solution, significantly reducing reliance on costly customised Performance Solutions where external timber cladding is permitted to be used. For residential projects under Volume Two, it accommodates modern cladding systems and updated installation methods, further streamlining the compliance process.
This new standard aims to minimise project delays, reduce construction costs, and promote the broader adoption of timber as a sustainable material, enhancing its appeal
• The new standard aims to minimise project delays, reduce construction costs, and promote the broader adoption of timber as a sustainable material.
and opening new market opportunities. FWPA is committed to industry-wide engagement in developing this standard. Consultations are being held with timber cladding manufacturers, suppliers, distributors, and building associations. To achieve NCC recognition, the standard is being developed in alignment with the Australian Building Codes Board’s Protocol for the Development of National Construction Code Referenced Documents. An open public comment period from November 13, 2024, to February 7, 2025, invites industry members to provide feedback and help shape the standard.
If referenced in the NCC, the new Standard will deliver several benefits to industry stakeholders:
• Streamlined Compliance: Architects, building designers, and builders will gain a straightforward pathway to meet NCC requirements, reducing the complexities of compliance navigation.
• Cost Savings: Detailed design and installation guidelines will aid building surveyors and certifiers in minimising the need for costly Performance Solutions, especially beneficial for commercial projects and minor residential variations.
• Faster Approvals: The simplified compliance process aims to decrease project delays, allowing projects to progress more swiftly and meet client deadlines effectively.
• Flexibility and Choice: The new Standard provides an additional compliance option while allowing professionals to utilise existing pathways, enhancing timber’s adaptability in a competitive market. For more information on how to provide feedback on the draft standard, please visit: https://fwpa.com.au/standardsactivities/draft-standard-designinstallation-of-exterior-timberwall-cladding/