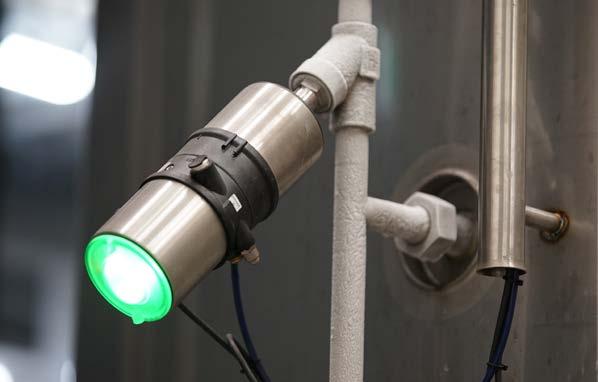
11 minute read
Exploring the total cost of tank automation systems
A dollar in line saves nine… or maybe twelve
Exploring the total cost of tank automation systems
Chris Hoey, managing director of Bürkert Fluid Control Systems, delves into the potential of ‘smarter field connection technology’ to provide cost savings and greater efficiencies in winery operations.
We hear a lot about digital connectivity and how it is making our old hard-wired systems obsolete, but what value does it deliver to us in the field?
In this article, we explore the significant savings that can be realised with smarter field connection methods and how these can deliver more flexibility for our everchanging environment. We will look deeper into the overall cost in dollars, time and ease of maintenance in a real application. You may feel that this type of technology is suited to highly automated sites like dairies and breweries; however, you will learn how the physical requirements of fermentation and storage tanks really lend themselves to a smarter connection technology.
The visible and hidden costs
Too often, we rely on a project tender to source our components and then our install costs or we anchor our pricing against previous systems we have built. Of course, any engineer will consider newer technologies, but the challenge is determining whether these new technologies actually deliver value. Experienced project engineers understand that the actual component costs in an automation system amount to around 15% of the overall project cost. The 85% comprises additional hardware required, engineering, installation, cable runs, termination at both ends, commissioning, training, life-cycle, safety, servicing, and more. Newer technology hardware may cost a little more, however it can significantly reduce the hidden costs and complexity of a project, and most importantly the time it takes to deliver a working system. Winery installations in particular can save significant costs due to their inherent physical layout and the distances involved.
Figure 1. Field Wiring Options
What are my wiring options?
There are three types of wiring methodology, as shown in Figure 1; however, this was not the case in years gone by. Original control systems, or controller panels, were ‘centralised’ and all field components wired back to a large control panel. The cost of such systems was prohibitive and only larger producers were able to get a viable return on investment. Smaller wineries installed stand-alone controllers wherever they could and had no central control. As technology progressed, we saw things like multiplexers or microPLC controllers that could collect our IO from a group of tanks, maybe 24 or so, and then transmit these back to a SCADA or PLC system. This was the onset of a ‘distributed’ installation. Whilst there was no central point, there was still a lot of individual wiring in the tank clusters and unless designed into the original system, there was little flexibility for expansion or change. If we continue along the technology timeline, add another 15 years or so, we see completely new methods of field termination enabling infinitely flexible and expandable systems that simply plug together in the field. These systems are truly ‘decentralised’.
Example system for comparison
Let us consider a small winery project where there are 32 tanks in four groups of eight. On each tank, there is one temperature transmitter, a brine/glycol valve, and two process butterfly valves. Each of the valves is fit for purpose and has open/close feedbacks as well as visual indication of status. The temperature sensor has either a 4-20mA transmitter installed in the connection head, or is digitally connected. We have chosen PLC control and SCADA visualisation, in-line with the ‘fictitious’ site standards. Our goal is to install these devices in the simplest and lowest cost way. If we wire in our distributed method, the first thing we have to do is engineer and specify our bespoke IO enclosure. This enclosure has to connect all the cables from the individual devices (128 of them) and provide DC power and control components to put these items into the PLC network. This will be a quite sizeable enclosure. Cable tray will need to be installed that can handle the 128 cables, which should be separated from any power cables. The estimated number of individual terminations is ~1,300 considering both the devices in the field and the panel. Using standard contractor calculations, this alone will take 130 hours to complete (around 16 person-days). If your electrical contractor charges you ~$70/ hour for site work, this will amount to well over $10K, and still does not include the running and strapping of a single cable, installation of cable trays or any consumables. Considering 5m of cable at the tank, tanks 5m apart and spurs 30m apart you are looking at over 15 kilometres of cable for this installation. Considering the cheapest overall screened PVC sheathed instrument cables with the right number of pairs, you need to allow around $34,000, more if you want a higher specified cable. It would not be unreasonable to consider a total install cost as high as $100,000 for this project. The major limitations of this type of installation is the flexibility to alter or change the system after installation. As an example, the winemaker decides he wants a pressure transmitter added to 16 of the tanks, with the other 16 to follow next vintage. Unless you designed the original panel with over 100% spare analogue capacity in this case, you will have to add another panel. Even then, you are back to running cables in trays and all the associated terminations.
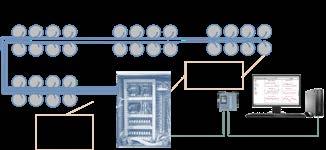
There is often an argument that such installations are ‘simple’ and easy to fault find. However, one has to consider with all that cable and 1,300 terminations, isolation relays and all the IO cards, there is quite a lot of potential failure points, not to mention those caused by incorrect wiring. Such system installations are still quite standard in today’s wineries and there
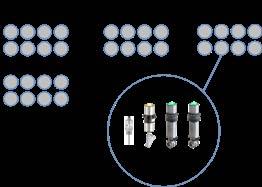
Figure 2. Example System
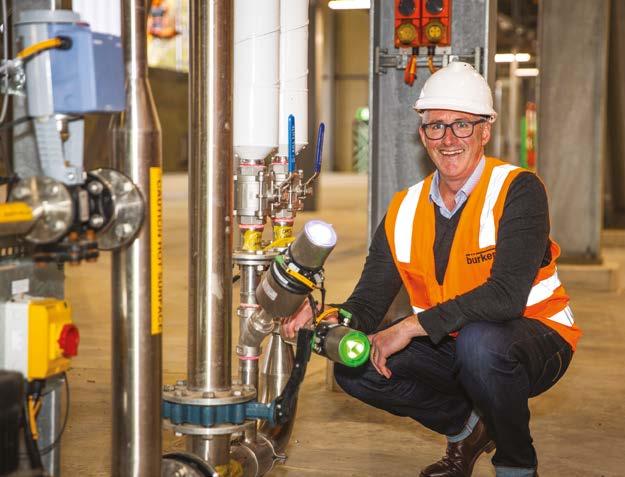
Winemakers prefer to partner with Bürkert
Save on installation costs > up to 40% Improve ongoing operating costs > up to 20% Flexibility of production processes > 100%
Request a quote
Type 8805/2671
ELEMENT On/Off Hygienic Butterfly Valve for decentralised automation, IP65/67/NEMA4X, easy integrated control top (IO-LInk, ASi, DeviceNet, CANopen)
may be specific reasons that it remains a viable solution. These systems however are not fully compatible with, or able to upgrade to, a fully digitalised system with asset management and diagnostics capabilities.
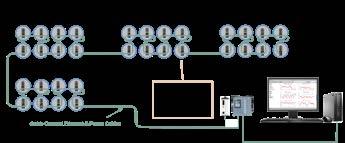
The game changers
One low technology advance in the last years has been the adoption of quickconnectors. You now find these on valves, sensors and IO blocks, on the DC power connections and even the Ethernet cable that runs back to the PLC. They meet documented standards, which makes them multi-vendor and cross compatible. Now entire field wiring systems are installed without the need for any bespoke engineering, junction boxes or terminals, and without the use of a screwdriver. Most importantly, they ensure the termination of all devices is correct, safe, waterproof, easily replaceable and simple. Now we complete the same project in a decentralised format using digital connectivity. The first thing you will note is that there is no IO or distribution enclosure to be designed, built or wired. As you can see in Figure 6, we are using an IP67 connection block per tank. In this case we will have 50% spare ports available at each tank for future expansion and we keep cabling to an absolute minimum. Individual sensors and valves are connected directly to the blocks with a single IP67 quickconnector, which includes power and digital communications. From the block we daisy chain the Ethernet and power cables with IP67 quick-connectors, between the tanks. In comparison to the distributed design, there is no cable tray to be run and the 128 cables have been reduced to two. These could be tied under a walkway or in a piece of tube or conduit. The distance limitations are 100m between blocks (Ethernet standard) and 20m between the block and any device. In this instance there is sufficient power, however if more was required then a field supply could be added at any point in the installation to boost the energy available. If we allow 5m of cable from block to each device (as we did on the distributed example) then this entire installation is now completed with 1040m of cable in total, versus the over 15 kilometres in the traditional installation. But the biggest savings and value comes from the fact that there are zero field or panel terminations, all connections are completed with the M12 quick-connectors. We would still recommend that the cables are well routed and marked, so allowing the same contractor rates we do for terminations, we would estimate around $3,000. This is so drastically reduced as the time to install has now come down to just four person-days. Having terminations reduced to plug-in connections, also eliminates the possibility of incorrect wiring, mistakes, loose terminations, and any chance of equipment damage. Whilst cables with quick-connectors on board are more expensive than raw cable, the cables for this installation would be around $13,000, a saving of $17,000. Considering all the data above, we could roughly estimate that the project could be completed for around $30,000. Adding the extra cost of digital capable devices (valves and sensors) at around $13,000 and the blocks in the field at $20,000, we
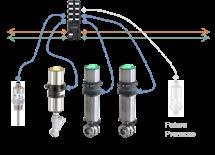
Pros:
Field equipment slightly lower cost
All technology in one enclosure
Cons:
Bespoke control panel, requires enginnering Considerably longer time to implement Considerably higher installation cost
Many potential points of possible failure
240V in the field, personnel safety issue
Inflexible to changed IO requirements Not a a future-proof solution (compatible with i4.0 or IIOT, asset management, diagnostics, etc.)
Figure 5. Tank Connections
Figure 6. Decentralised System
still have a project saving of $37,000 and can compete it at least four times faster. Now consider the winemaker’s postproject addition of pressure transmitters as we did before. As visible in Figure 5, this is as simple as plugging in a new sensor in the field, and then addressing it in the software. Even if there were no spare ports, another block could be added at minimal cost. In this example, even if the devices on the tank were doubled, the only addition required would be an IP67 power supply booster, at around $800.
What if something fails?
It is 10pm, a cellar hand yanks on a hose and clean snaps off a temperature transmitter. They can go to the store, grab a replacement, install it and plug it in. As the programmed device configurations are held in the field blocks, the device is recognised as missing and once a new one is connected it immediately reassigns it and downloads any configuration. You are up and running in seconds. The installation of a new digital connection system will require some local training on the configuration and maintenance of the system. Most equipment or automation vendors can support with this.
Pros:
Lower project overall cost
Faster to implement the project Significantly reduced engineering and fiield labour
All field equipment 24VDC (extra-low voltage) Fully compliant with new digital standards
Asset management and diagnostics available
Easy to add devices post project Fast and easy to repair with selfconfiguration Easily scaleable from very small sites to larger ones
Cons:
May require some site training of personnel
How do I integrate into my automation system?
In the above examples, I have purposely just used the term ‘Ethernet’ however; these systems exist in every form or Ethernet, or for every automation vendor. Therefore, no matter what system you have on site, there will be little challenge in connecting to the system. It will also be pleasing to know that these systems are built to accepted IEC standards and are generally available from many vendors without fear of connection issues. One other key advantage is that these systems can be installed cost effectively in very small wineries, and then be expanded easily as the need arises.
Future proof?
The above shows how the installation and wiring is considerably cheaper and faster, but this is not the only advantage that digital connectivity adds. This decentralised installation has also delivered a completely digitally connected system, a system that is fully compliant with newer Industry 4.0 or IIOT standards. From the PLC, SCADA or a maintenance PC, you now have full asset management and diagnostic capabilities. This data can be used locally or in the cloud to prevent possible downtime and deliver even more value to the plant.

Bürkert is the leading partner in fluid control systems. For over 70 years, they have partnered with large and small wineries all over the world. Their passion for wines and winemaking has given them a deep respect and understanding of the complexities of crafting great brands. Strength in their partnerships stems from a comprehensive range of German designed and manufactured products, coupled with local experience in winery engineering. Creating better processes for wineries helps to improve efficient running costs and ensures sustainable solutions for a better bottom line.