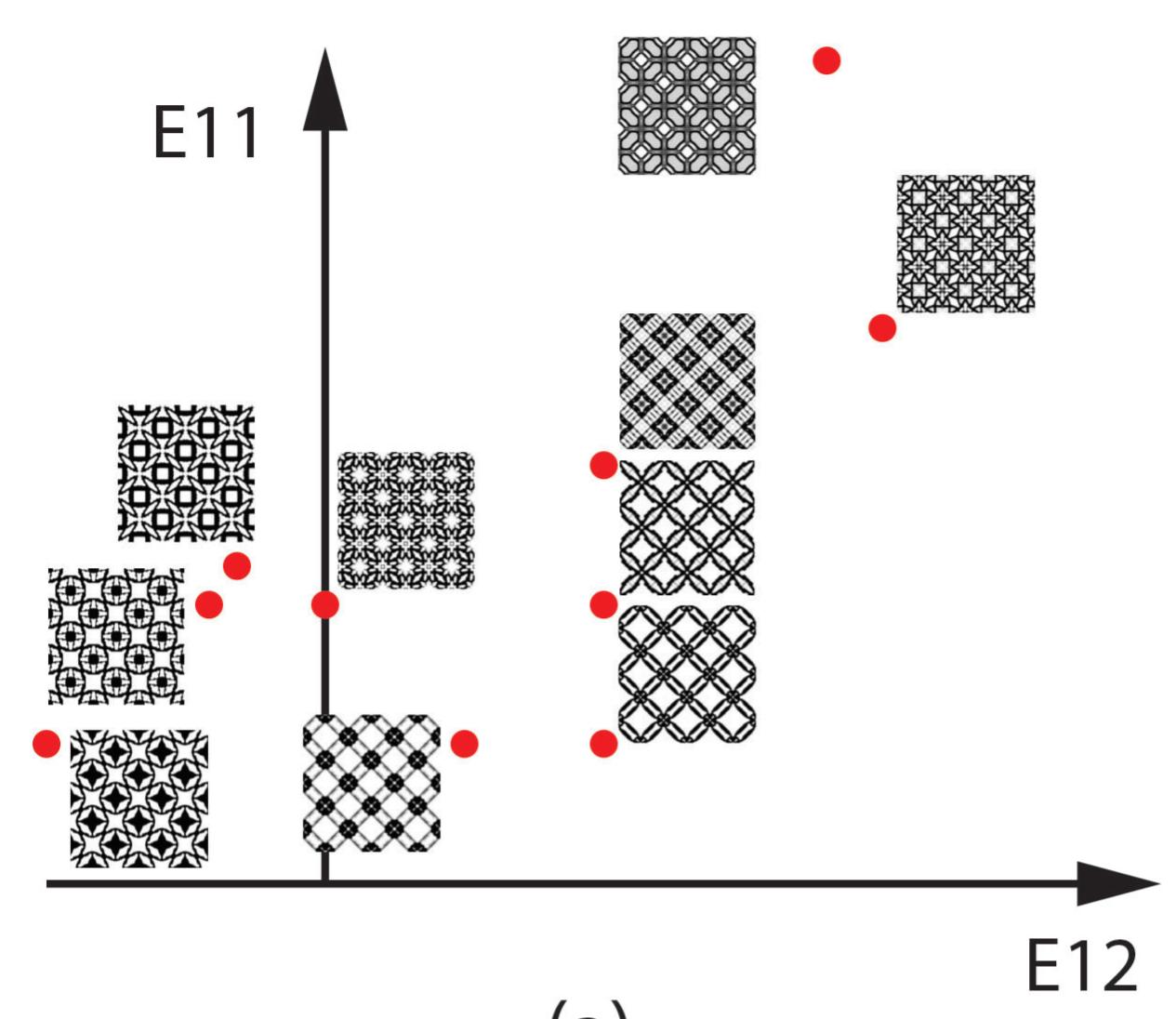
3 minute read
Prevailer Mba
Mentor: Jaejong Park Mechanical Engineering
Introduction: Bone defects can develop from various situations such as trauma, infections, tumor, surgery, etc. In some cases where the defect is large, making bone not being able to regenerate itself, the defect site needs to be replaced for functional requirements and aesthetic reasons. Bone grafting is one of such methods available for such purposes. This method includes repurposing another bone in the body (or using a substitute) by modifying it to fit into the affected area. Metal-based bone implants are another option. Titanium and its alloys are widely used in reconstruction surgeries. Since the design and fabrication are done using virtually Ex vivo, metal-based bone implants have geometric freedom compared to bone grafts. However, one of the main shortcomings of metal-based bone implants is their inherent strong mechanical properties. A substantial mismatch in mechanical properties between the metal implant and the bone may lead to a failure in the long run. The property gap between the metal implant and neighboring bone needs to be closed to avoid stress shielding. This study aims to focus on various techniques for stiffness control by changing the geometry of the overall structure confined in a design domain. We are studying how to make the structures ‘porous’ to control the stiffness of the structures. While making structures porous intuitively reduces the stiffness of the structure, the study explicitly pursues algorithms where the stiffness can be systematically controlled. Various internal structuring techniques, such as lattice structures with different geometric configurations, architectural materials, and auxetics, are being investigated. Methods and Materials: In our review of published manuscripts, we identified different methods for stiffness control. This summer, we decided to focus our efforts on understanding two of these methods. They include creating pores on implants and creating lattice structures. To effectively control the creation of the pores, software was needed that could create designs from an algorithm. Using this software ensured creativity and flexibility in design. We utilized the combination of Rhino and Grasshopper to learn the basics of creating new designs from an algorithm. For the lattice structures, Crystallon was considered as an excellent choice for the work. It was to be used as a plug-in to Rhino for the creation of the lattice structures. Results and Discussion: In the last progress document, we reported some technical issues that hampered us from editing imported designs, such as .stl files of previously optimized bone-implant geometries in Rhino. We have partially addressed this issue, and now we can create porous structures with geometric primitives such as squares and cylinders. This was completed using a combination of Tecplot, Paraview, etc., without having control over creating functionally graded porosity. The technique is being taught to a student. We are currently looking into this capability using various avenues as this would provide greater flexibility in controlling stiffness, as shown in Figure 1.
Fig 1. Left: Different internal structures leading to different macroscopic properties, right: generated multiscale structure using simple mesoscale structure [1].

Conclusion: The issue encountered with Rhino is currently being mitigated and more practice is being put in to understand the local code import and how to implement it properly. Upon successful completion, this will provide a simpler way of creating controlled porosity in any target object for stiffness control. Partial findings of this research have been included in a recent publication [1].
References
Park, J., et al., A two-scale multiresolution topologically optimized multi-material design of 3D printed craniofacial bone implants. Micromachines, Biology and Biomedicine B, 2020.