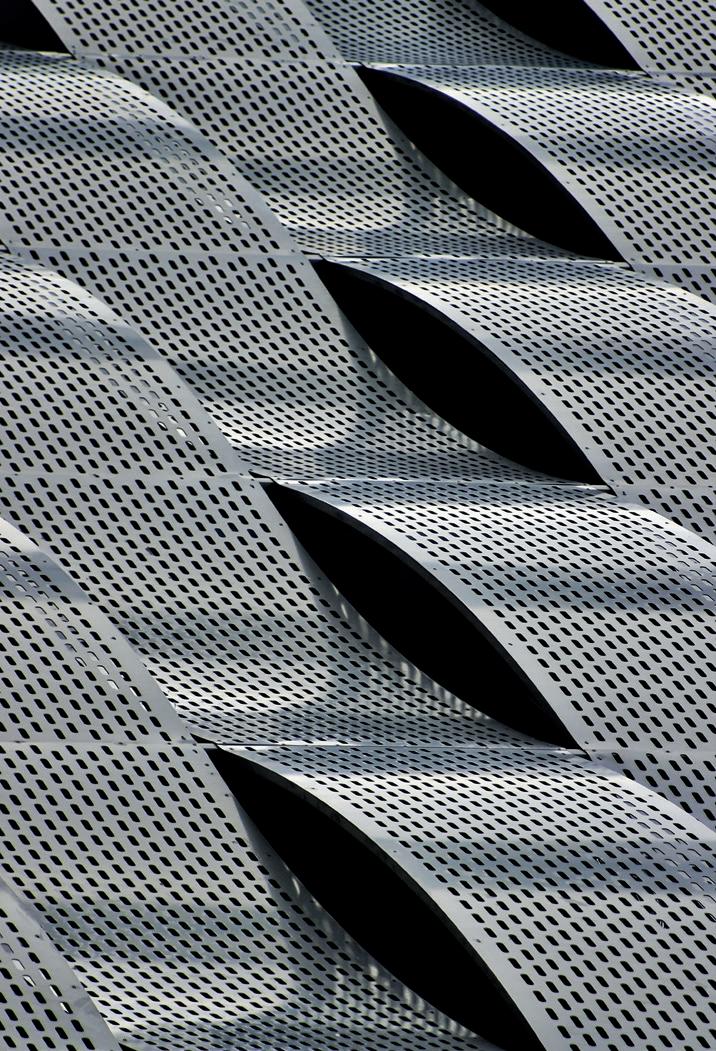
7 minute read
Why inert Anodes are a Capital idea
By Paul Adkins*
The entire primary aluminum industry has been watching carefully for any news from Elysis, the Alcoa/Rio Tinto joint Venture working to develop an inert anode. First announced in 2018, this project created a new level of interest in inert anodes following almost 20 years of speculation, trial and error and most of all, lack of a breakthrough.
Since 2018, Elysis has kept an extremely tight rein on information. Even the usual “leaks” have not materialised. That’s left a vacuum, and as someone once said, speculation loves vacuums. There have been all sorts of expert opinion on the various questions arising from the possibility of an inert anode becoming commercially available.
Technical experts have had plenty of time to consider these questions and challenges. How does a technology which occupies a vertical plane fit into an existing pot that operates on a horizontal plane? What if the raw materials required to make an inert anode generate other unpleasant side effects, or are simply too scarce or require mining in pristine areas? And anyway, who is going to teach potline crews how to deal with the various operating vagaries? Although potrooms look like they are sitting there happily bubbling away generating pure aluminum, that’s because the crews know exactly how to keep things that way.
There’s no doubt the road ahead of the inert anode will be a difficult one. There’s speculation that Rio or Alcoa will retrofit an existing plant with the new technology, to make said plant into a model that Elysis can use to promote and market the technology. The concept of showcase plants is not new in the primary aluminum industry. Even then, we don’t know what market development strategy might get rolled out. The betting appears to be on technology licensing, which is also a very common practice in aluminum. But other options remain. Since the life cycle of an inert anode is said to be many times more than that of a carbon anode, could one centrally-located anode manufacturing plant supply the entire world? (At least until enough smelters switch or new plants are built.) That model would gain synergies in procurement of raw materials, and would partially protect the technology from reverse engineering.
Speaking of which, it’s my bet that whatever market rollout model Elysis decides on, China will not feature anywhere in their plans. Remembering that the Elysis CEO Vincent Christ used to work with Pechiney, and Pechiney got seriously burned by their technology being
illegally copied by some inside China, I can’t imagine any scenario where China will be a customer. Indeed, there are new moves inside China to tackle the inert anode, after previous attempts failed.
So, there are many questions that we are all grappling with on the inert anode. I don’t claim to have any inside information, but I would like to offer one specific thought about this new technology.
To me, it doesn’t matter what your view is on the technology, and it doesn’t matter what outcomes you are looking for if you are examining the technology for your smelter, there’s one overarching fact – inert anodes are a capital idea. But in this case, capital means finance.
The easy aspect of this statement is if you are considering building a new smelter. Your investment is going to be in the billions of dollars, regardless of whether you opt for existing technology or the inert anode. In a new smelter scenario, the only way forward that will deliver a return on investment in a decent time frame is to build a single potline now, and purchase anodes. You save yourself the cost of a full anode plant, though you still need a rodding shop and you still need to deal with spent anodes and any scrap anodes. Once the inert anode is proven and fully understood, you go ahead and build line two. (Naturally your new smelter is running on renewable electricity and green alumina.)
In this scenario, you still have the question of operating costs. You have made your capital cost decisions, and it’s not too difficult to assess the operating costs of a potline that runs on existing prebake technology. Since you have a potline running, you can afford to wait and assess the case for the inert anode. Right now, nobody knows what the real costs will be – whether it is the cost of the raw materials, the cost of manufacturing the anode, the increased cost of electricity, or the cost of disposing of the inert anode at the end of its life. However, it is worth pointing out that these questions apply for those who might consider retrofitting their plant.
Retrofitting is not an easy decision, but whichever way you look at it, it’s a decision involving major capital investment. Even a relatively small plant with say 400 pots will be faced with a major capital decision, since it’s not just the point of electrolysis that shifts. The meeting point where the electricity meets the alumina will shift to a vertical plane, but presumably the rest of the pot will need re-designing. Will centre point feeding still work or will a new feed mechanism be needed? Since the inert
anode is said to produce pure oxygen, shouldn’t that be harnessed, bottled, and re-sold? And what do you do with the fume extraction system? By the way, what do you do with your anode plant? The anode plant takes up a large amount of land when the baking ovens are considered. Do you still need a rodding shop? And what sort of anode cleaning and disposal system will you need once the inert anode has reached its end of life. (Remembering, the new technology is called “inert” but it’s not like these anodes will last forever.)
There’s one other piece of equipment that many people neglect to include in their considerations. When I worked at Tomago Aluminum in Australia, we had to silos located at the Newcastle port, where calcined coke was stored. The site also contained Tomago’s three alumina silos, and came with a conveyor system that brought the material from the ship to the silo. These calcined coke silos were matched by two other silos located at the plant ahead of the anode plant.
There was a coal tar pitch silo by the anode plant as well. If a smelter is considering retrofitting the new technology, will it still need calcined coke silos, and will any new raw material still be delivered in the same form factor, and handle the same way ahead of any manufacturing? Or do we need to build an entirely new storage system? If inert anodes are to be made at some outside location, what does one do with the equipment at the port?
It’s impossible to put a dollar figure on the cost of a retrofit might be, since there are too many variables, but essentially, the question comes down to capital. A project to retrofit the inert anode will be assessed along with every other RFC (Request for Capital).
Most companies use standard decision trees and templates for capital investment – does the investment improve revenue, reduce costs, sustain operations or meet some other strategic imperative? For the inert anode, it may improve revenue if a green premium can be applied to the metal produced, but the problem is, it won’t move most smelters far enough down the carbon emissions tree. What I mean is, the inert anode will reduce your emissions by about 1.5 to 2 tons of CO2 per ton of metal produced. If you are sitting at 8 or 10 tons of CO2 emissions per ton of aluminum produced, the inert anode will not get you down to the threshold of 4t CO2, much less zero to 0.5t CO2 that more and more consumers are demanding.
There may be other considerations that come into play when considering the capital investment, perhaps political or geo-political issues, but on face value, only those companies who currently sit down at 4 tons CO2 will likely ever make the investment. And that’s without knowing what the operating costs will prove to be. Somebody has to be the first mover, but if I were the Board, I would be asking should we be that first mover?
So, regardless your opinion of the inert anode and its ability to transform our industry, it’s going to be a decision that must meet the rules of capital investment. �
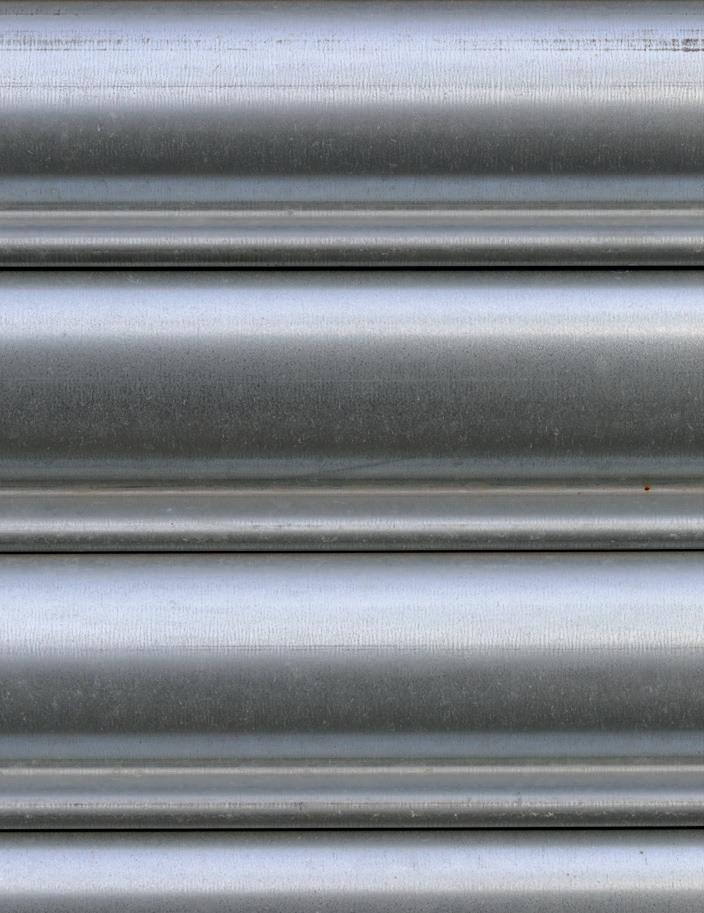
Induction Coil Repair & Refurbishment
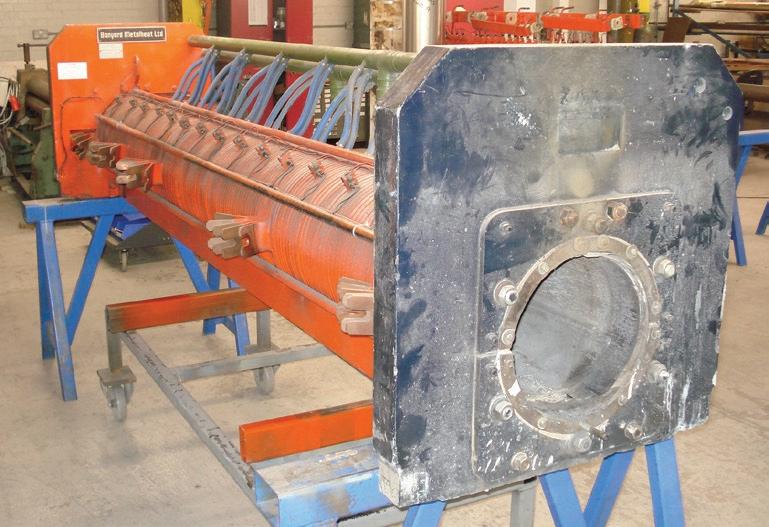
• More Economic than Coil Replacement • Instant Positive Impact on Coil Effi ciency • Refurbish Damaged and Worn Coils • Eco-Friendly Solution - Reduces Waste • Coil Change Out Programme- Rotationally Refurbishing Coils, Minimising Downtime
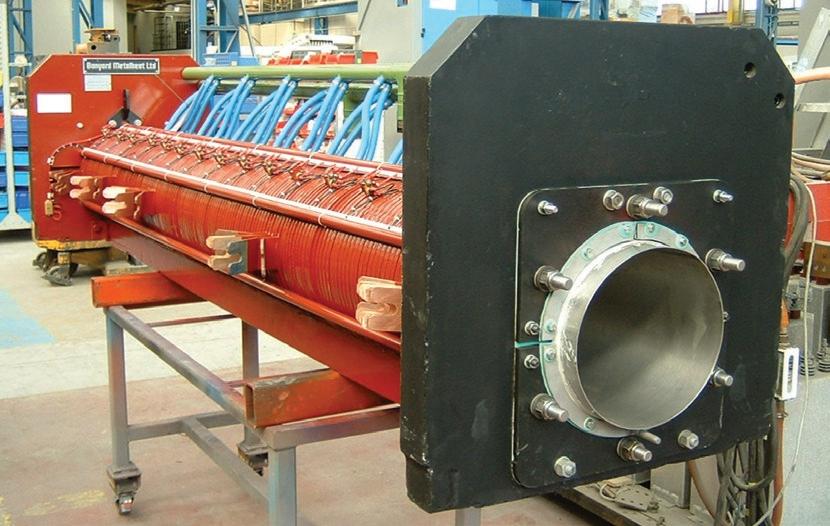