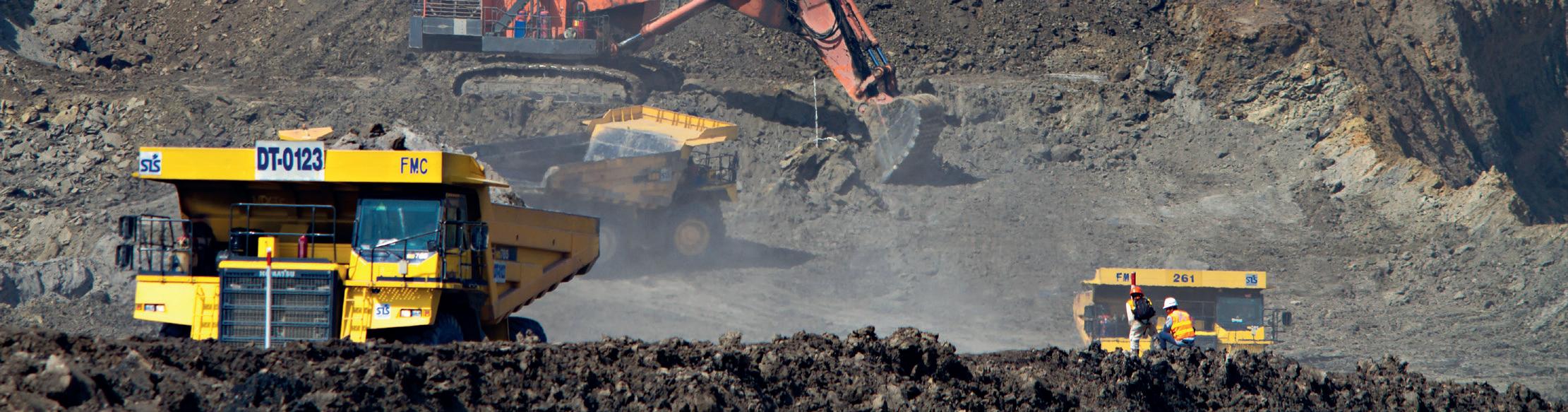
7 minute read
Possibilities of urban mining in relation to aluminium

By Dr Subodh Das*
Urban Mining denotes the process of using the anthropogenic stock as a source for the exploration, extraction, and refining of various raw materials, i.e., treating the anthroposphere as a ‘mine’. The anthropogenic stock is the sum of all materials used or stored by humans over time. This may include buildings, infrastructure, industries, products (in and out of use), Electrical and Electronic Equipment (EEE), waste tailings, and landfills.
The potential material recovery from the urban mine depends on the outflow of materials from these sources into the waste stream, along with tailings and landfills. Although there is an overlapping of the concepts of recycling and landfill mining with urban mining, the formers are indeed a part of an urban mine. Quantitatively, urban mining is a sum of end-of-life recycling of various products and some scarce material recovery from landfills and tailings.
Urban mining is an integral part of the circular economy principles. The circular economy rejects the linear ‘‘take-makewaste” business models. It promotes longer use of products by reusing and repairing them, reducing waste generation, and using more secondary raw materials in production cycles for resource conservation and economic growth.
Urban mining and the metal sector
The metal economies, especially nonferrous metals are the most significant beneficiaries of urban mining, supported by the fact that the metals are often 100% recyclable and most of the landfilled and discarded wastes contain metals. With the growing awareness about a circular economy and reclamation of waste, the concept of urban mining is gaining ground from the point of view of metal and rare earth element recovery.
An urban mine mostly comprises the below sources that contribute to the recovery of metal: � Building and construction � Automotive � Packaging (beverage packaging such as UBCs) � Electrical and Electronic Equipment (EEE) � Mine tailings � Process wastes in refineries and smelters (red mud, fly ash, spent pot lining, dross) � Landfills
Recovery from landfills, mine tailings, and process wastes is scarce and is gaining ground on an experimental basis. Nonferrous metals contribute the most to the recovery from urban mining in value terms. No-ferrous metals are usually less prone to corrosion and have a longer life. Nonferrous metals can be recovered, segregated, and processed as new metals and can also be commercialised directly as a mixed nonferrous scrap. In both ways, non-ferrous metals, especially copper, aluminium, and lead continue to dominate the urban mining space.
Potential reclamation of aluminium from urban mines
Aluminium is one of the highly recycled non-ferrous metals and has the maximum potential to be reclaimed through urban mining.
A large amount of automotive and construction scraps is recycled across the world from urban mines. However, the recycling rate of aluminium packaging wastes especially, used beverage cans (UBC) is still far lower than expected and has the potential to rise to a much higher level.
As an instance, the current consumer UBC recycling rate in the United States is hovering around 45%. The industry recycling rate increased in 2020 to 59.7%. For an industry that produces more than one hundred billion aluminium cans per year translating into the consumption of about one can per day for every American, this is undeniably low. This compares to a much higher rate of 97% in Brazil and close to 80% in Scandinavia, and Japan. Aluminium cans are a leading example of closed-loop recycling, with a high recycled
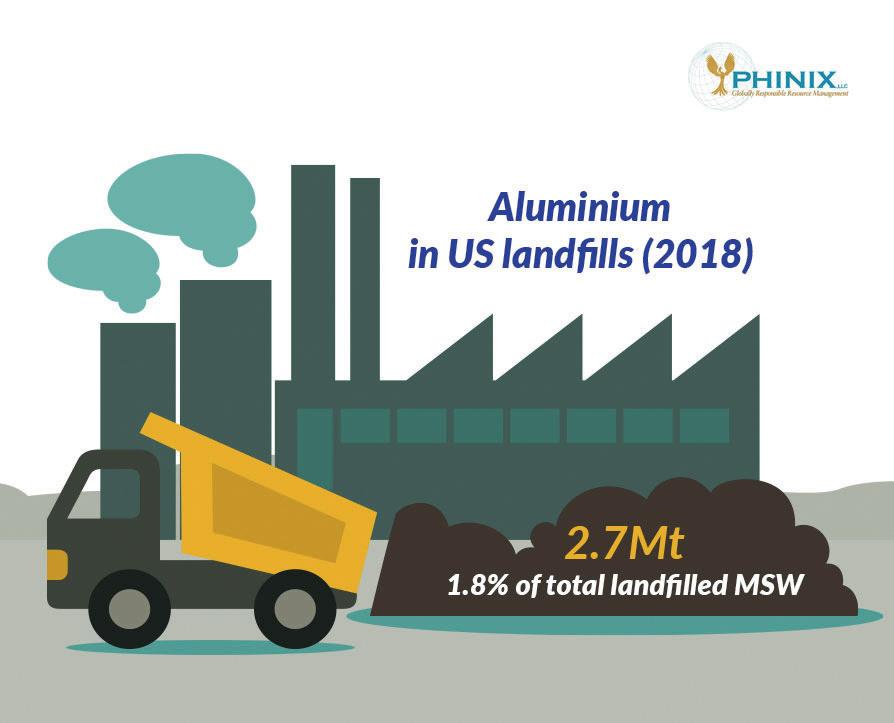
Management Pathway 2000 2005 2010 2015 2017 2018
Generation 3,190
Recycled Composted 860
Combustion with Energy Recovery 390 Landfilled 1,940
Source: https://www.epa.gov/ 3,330 690
410 2,230
Aluminium Metals in MSW by Weight (in thousands of U.S. tons)
3,510 680
440 2,390 3,670 670
510 2,490 3,820 600
550 2,670 3,890 670
560 2,660
aluminium content and the ability to be back on store shelves as fresh cans within 60 days. Notwithstanding that, more than 50 billion cans, around $800 million worth of aluminium – were diverted from the recycling stream in 2020 to the landfill that could have otherwise been responsibly recycled and made into new cans. This loss has a significant negative impact on the environment as well as on the economy.
As per the latest data from EPA, in 2018, aluminium waste generation was 1.3% of total MSW generation at 3.9 million tons. This included 1.9 million tons of aluminium containers and packaging and two million tons of durable and nondurable goods. Further, as per the EPA data, in 2018, the total recycling rate of aluminium containers and packaging was 34.9%. Within this number, the most recycled category of aluminium was beer and soft drink cans, at 50.4% or 0.67 million tons.
The total amount of aluminium combusted in 2018 was roughly 0.6 million tons, about 1.6% of all MSW combusted with energy recovery. In 2018, landfills received about 2.7 million tons of aluminium or about 1.8% of all MSW landfilled that year. This is a huge volume to be ended in landfills every year. Table
1.
As CMI has pointed out, if the aluminium UBC recycling rate were 70% in 2020 instead of 45%, more than 25 billion cans would have been recycled. These 25 billion fresh cans would have generated revenue of more than $400 million for the US recycling system and the saved energy could power more than one million US homes for a year. The figure for the lost value of UBCs gets bigger if we look at the current (2021-22) market price of aluminium.
Aluminium beverage cans contribute just 3% of the weight of all recyclable wastes generated at US homes. Yet, UBCs account for nearly half of the revenue from recyclable materials from singlefamily homes.
These statistics come from the landmark study published by The Recycling Partnership’s 2020 State of Curbside report and justifies the significance of an effective recycling loop for the UBCs
The fate of the landfilled UBCs
The recycling possibilities of UBCs go beyond curbside recycling to reclaim all the cans that have been landfilled in the US for decades. As per the last estimate, more than 30 million tons of aluminium scraps are buried in the nation’s landfills over the past three to four decades. If recovered and processed, they can compensate for a large volume of freshly mined metals. As the US is increasingly focusing on secondary sourcing of aluminium and closing most of its primary smelters, the country’s landfills can be the next best source for reclaiming the aluminium mostly buried in the form of UBCs.
Challenges
Landfill mining is a complicated process and can be expensive enough to consume about 80% of the project budget. The cost of excavating trash, sorting out the materials such as metals, and then reburying the rest tends to exceed the revenues from selling recovered materials. Boring into a landfill will release the methane generated inside it and this will be counterproductive if the gas is being used as a fuel. Increasingly, this methane is being combusted for steam generation and to heat large institutional buildings. Also, the material recovered from a landfill will certainly be more contaminated than end-of-life wastes. They might not be an attractive option to the remelt operators.
Not only lack of profitability but also regulatory hurdles for accessing and processing the landfilled material are a hindrance to raw material recovery from landfills. This comes with numerous political, economic, environmental, and legal liabilities.
These are some of the factors that pose challenges in extending urban mining to reclaim resources from landfills. At present, urban mining centers around recycling and diverting wastes from ending in landfills. Landfill mining is still in the experimental stage and needs further research and development to be standard practice.
The bottom line
There is a gap between the raw material production potential given by the urban mine and the recovered raw material volumes. This follows from numerous challenges, ranging from organizational to technological to economic – facing the recovery of raw materials from a highly diverse and highly complex resource base across the world.
There is an urgent need to develop technology to clean and beneficiate the waste from urban mines. Without technical innovations, urban mining remains just wishful thinking. It is a practical concept that must be strongly structured within a circular economy strategy. The concept needs to be addressed scientifically with regard to terminology, targets, technologies, challenges, and opportunities. The extraction and processing of materials during urban mining are based on economic feasibility. There is a standard mechanism for enhancing the concentration and extraction of given elements. Therefore, the process needs a pragmatic approach rather than an ideological one. A planned urban mining ecosystem can reduce dependence on organic raw materials, cut carbon emissions considerably in industrial production, fortify recycling supply chains and finally strengthen the circular economy goals. �
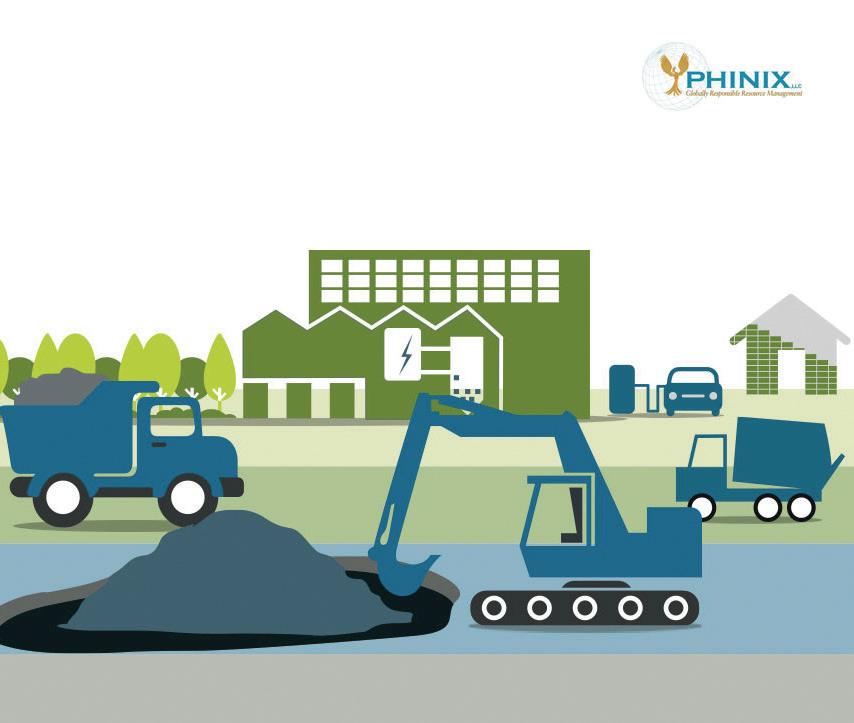
Reference:
1. https://www.epa.gov/sites/default/ files/2016-03/documents/land-rcl.pdf 2. https://www.urbanmining.it/public/ documents/simposio/editorial-wastemanagement-2015.pdf 3. https://eurelco.org/wp-content/ uploads/2018/09/p5.pdf 4. https://secat.net/wp-content/uploads/ Recovering-Aluminum-from-Used-BeverageCans.pdf 5. https://www.rts.com/blog/what-is-urbanmining/ 6. https://www.isi.fraunhofer.de/content/ dam/isi/dokumente/ccn/2020/Fraunhofer_ISI_ Urban_Mining.pdf 7. LANDFILL MINING: Process, Feasibility, Economy, Benefits and Limitations, July 2009, René Møller Rosendal 8. 2020 State of Curbside Recycling Report, THE RECYCLING PARTNERSHIP 9. Defining a Closed-Loop U.S. Aluminum Can Supply Chain Through Technical Design and Supply Chain Innovation, JACK BUFFINGTON, RAY PETERSON (TMS)