
13 minute read
Aluminium use in the aerospace and automotive industries in USA
By Richard McDonough*
This photo shows the Earth Surface Mineral Dust Source Investigation (EMIT) instrument before the enclosure panels were attached. According to a statement from the National Aeronautics and Space Administration (NASA) of the United States, “The long tube in the foreground is the EMIT telescope baffle. The telescope resides in the large aluminium cube behind the baffle, and the spectrometer assembly is attached to the back of the telescope.” (The photograph was provided courtesy of the Jet Propulsion Laboratory of NASA, May 20, 2022.)
Aluminium is a critical piece in both the aerospace and automotive industries in the United States of America. This news column details activities among several key entities producing and utilising aluminium in these two industries as well as some of the more modest players that provide critical elements using aluminium within the automotive and aerospace industries in the U S.
“Over the past decade, the aluminium industry has invested more than (US) $6.5 billion in US manufacturing to support growing demand for the metal,” according to a statement from The Aluminum Association. “Aluminium is the fastest growing material used by automakers and is expected to grow to 514 pounds per
*Do you have questions about the aluminium industry? Governmental regulations? Company operations? Your questions may be used in a future news column. Contact Richard McDonough at aluminachronicles@gmail.com. © 2022 Richard McDonough
vehicle by 2026 – up more than 25% in just ten years.”
Among recent developments cited by The Aluminum Association is an expansion project announced by Novelis in January of 2022, that includes “…a (US) $365 million investment to build a highly advanced recycling centre for automotive in North America near its automotive finishing plant in Guthrie, Kentucky. The project is expected to be completed by 2024.”
In addition, the trade organisation for the American aluminium industry highlighted an announcement in May of 2022 from Novelis for “…a (US) $2.5 billion investment to build a fully integrated aluminium manufacturing facility including recycling/casting, hot rolling, and finishing for beverage can and automotive markets in Bay Minette, Alabama. The facility will be powered by renewable energy, use recycled water, and operate as a zero-waste facility.”
The State of Alabama welcomed this development located in Baldwin County.
“With this massive investment and these large-scale hiring plans, Novelis will launch a high-tech aluminium mill that will generate significant economic impacts throughout the region for generations,” said Kay Ivey, Governor of Alabama. “Novelis is a world-class company, and we know that it has selected a prime location in Sweet Home Alabama and specifically Baldwin County as home for its growth plans.”
Whilst the Baldwin County facility will primarily serve the growing beverage can market, according to a news release issued on May 11, 2022, from the Office of the Governor of Alabama, “the plant will also serve the automotive market, where aluminium is the fastest growing material, as automakers make plans to achieve their sustainability goals. Aluminium produced by Novelis can be found in more than 225 vehicle models produced by leading automakers around the globe.”
A number of other investments were announced in 2021, according to The Aluminum Association, that will also expand aluminium operations in the automotive industry. These developments included an expansion of a rolling mill in Kentucky and the upgrading of a hot mill in Pennsylvania.
“Aluminium offers the fastest, safest, most environmentally-friendly and valueadded way to decrease mass and increase vehicle performance, boost fuel efficiency, extend battery range, and reduce emissions,” according to a statement from The Aluminum Association. “Aluminium builds a better vehicle...period. Aluminium is the fastest growing material in the automotive market today, expected to grow around 12% on a per vehicle basis by 2026. And, by extending battery range, low-weight aluminium will play a key role in the electric vehicle revolution. The most innovative vehicles of today and tomorrow are designed with aluminium.”
Earlier this year, the trade organisation issued a news statement highlighting the 2022 Roadmap for Automotive Aluminum, a document that it indicated identifies pathways and prioritises opportunities for critical collaboration among aluminium suppliers, recyclers, automakers, policymakers, nongovernmental organisations, and other industry stakeholders to drive innovation throughout the next decade.
“The Roadmap for Automotive Aluminum lays out the value-driven steps needed to make large-scale closed-loop aluminium recycling a reality,” said Charles Johnson, President and Chief Executive Officer of The Aluminum Association. “As aluminium use continues to grow, more efficient ways to separate, recover, and reuse aluminium scrap in automotive components is of utmost importance, particularly in support of aggressive net zero goals put forth by automotive customers.”
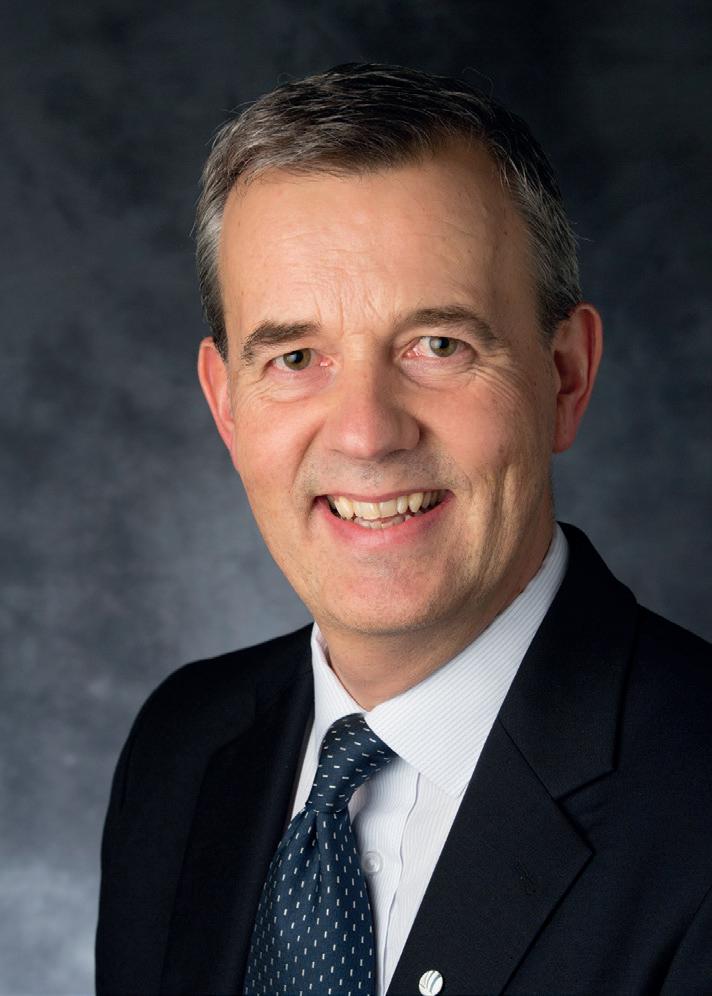
Trond Gjellesvik is President of Hydro Aluminium Metals, North America. (The photograph was provided courtesy of Hydro Aluminium Metals.)
The news statement continued by noting that “Members of The Aluminum Association are eager to work with automakers on focused projects to transform manufacturing processes and deliver the vehicle solutions that will drive efficient transportation for years to come. The 2022 Roadmap for Automotive Aluminum is a unified blueprint that lays a foundation for the industry to grow and diversify within the automotive market and will serve as an actionable, living document, that will be revisited over the next decade.”
In the area of aerospace, a statement from this trade organisation noted that “Aluminium powers flight – aluminium alloys are the overwhelming choice for commercial planes and military cargo/ transport aircraft. And, NASA spacecraft and space shuttles…rely on aluminium to enable space exploration.”
“Entering mainstream use during and after World War II, it is no exaggeration to say that modern aviation and aerospace exploration would not have been possible without aluminium,” the statement from The Aluminum Association continued. “Lightweight, strong, and durable, aluminium launches flight and sends us to the moon...and beyond.”
Hydro
“Hydro Aluminium Metals (Hydro Aluminium) manufactures 3000 and 6000 series aluminium extrusion ingot that is utilised in a number of automotive applications,” stated Trond Gjellesvik, President of Hydro Aluminium Metals, North America. The firm is a division of Norsk Hydro ASA, a global company headquartered in Norway. “This includes heat exchange products and tubing applications; crash management systems, battery tray components, rocker sills, and other structural components; as well as a number of other non-structural applications such as trim pieces, sunroof rails, and the like.”
“In addition, we provide primary foundry alloy used in casting applications, including aluminium wheels, brake calipers, and other cast automotive applications,” Mr. Gjellesvik continued. “In Europe, Hydro Aluminium produces aluminium sheet ingot that is transformed into automotive sheet which is exported to the United States for use by several leading OEMs.”
The firm indicated that its customers include aluminium extrusion companies located throughout the US as well as suppliers to the automotive industry located in Canada and Mexico. In addition, the firm also indicated that it supplies some material to Hydro’s Extrusion division.
According to Mr. Gjellesvik, Hydro Aluminium “…provided over 65,000 metric tonnes of aluminium extrusion ingot and foundry alloy ultimately consumed by the US automotive industry. In addition, our colleagues in Hydro Extrusions also supplied significant amounts of material
to the industry.”
Hydro Aluminium, like many manufacturers, saw impacts from restrictions related to the COVID-19 Pandemic in recent years.
“We saw activity level in 2021 increase, following the COVID-related downturns seen in 2020,” said Mr. Gjellesvik. “In general, the market for aluminium products grew by between 13% and 15% in 2021 over the levels seen in 2020, and Hydro Aluminium saw similar growth.”
“The global semiconductor shortage also created well-documented difficulties for automakers, which of course trickled down to our activities as well,” continued Mr. Gjellesvik. “We also see two key growth factors gaining steam – electrification and interest in low-carbon products. Because of the properties of aluminium – light weight, corrosion resistant, formability, and strength – it is almost tailor-made for use in Battery Electric Vehicles [BEV].”
He explained that “as BEV production ramps up in the US, we see very high interest from automakers in using aluminium in their vehicles. At the same time, we also see OEMs having an increased focus on the carbon footprint of their products. Again, aluminium has a key role to play, particularly aluminium produced from recycling. Hydro is a leader in the production of low-carbon aluminium, and our CIRCAL product, which we have now begun production of in 2022 in the U S, has the lowest carbon footprint in the industry as it contains at least 75% post-consumer scrap.”
Airbus
Aluminium is a critical component for many of the world’s aerospace companies, including those with operations in the US. Airbus SE (Airbus) is one of the largest global aerospace firms with 180 locations worldwide. The firm’s head office is in Blagnac, a suburb of Toulouse in France, whilst headquarters for the Americas is in a Virginia suburb of Washington, District of Columbia.
“Airbus uses aluminium as a major material for its product design, leveraging its characteristics of strength combined with light weight,” according to a statement from Airbus. “Aluminium is mainly used for aerostructure elements such as fuselage or wing skins and mechanical parts.”
“Since last decade, aluminium has increasingly been competing with carbon fiber-reinforced polymers (CFRP) as a material of choice for aerospace,” the statement from Airbus continued. “The aluminium material share on our products is typically between 25% and 70%, depending on the aircraft type and mission.”
The COVID-19 Pandemic affected the aviation and aerospace industries throughout the world.
“Despite aluminium supply having faced some challenges since 2021 (for various reasons including a magnesium shortage, lack of resources due to COVID, and logistics constraints, among others), Airbus managed to secure its supply successfully,” according to the statement from Airbus. “In 2022, Airbus will fully restore its pre-COVID aluminium consumption due to industry recovery, and Airbus’ ramp-up plans due to the high demand for Airbus’ leading product portfolio. The aerospace industry will continue to use aluminium for many years to come.”
Sustainability is part of the operations of this aerospace firm.
“Airbus and the industry will further work to improve its performance in terms of sustainability,” according to the statement from Airbus. “Also, leveraging aluminium’s high recycling potential.”
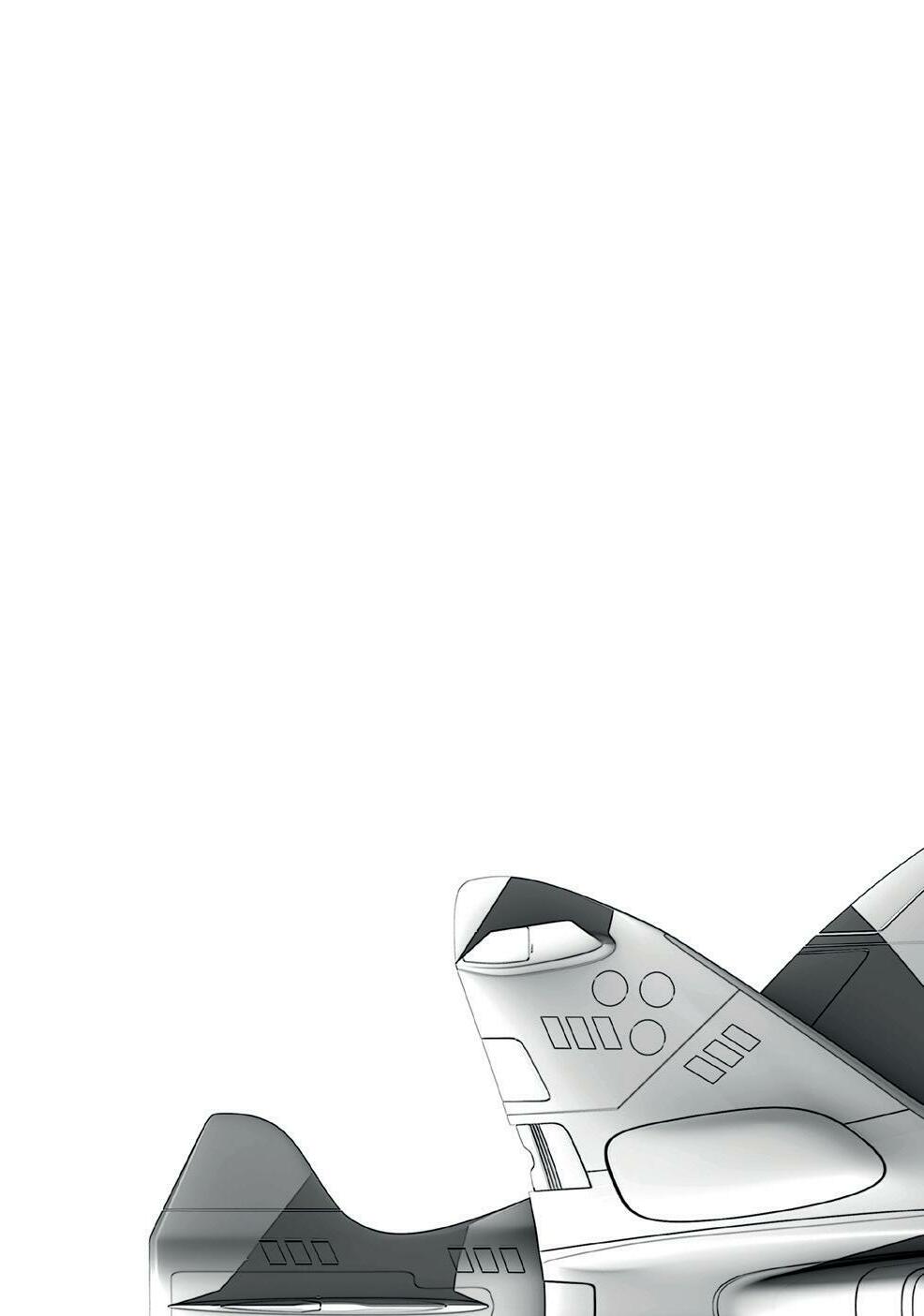
Boeing
One of the largest aerospace companies in the world is The Boeing Company (Boeing). The firm recently moved its headquarters from Chicago, Illinois, to Arlington, Virginia, a community just across the Potomac River from Washington, District of Columbia. The 2021 Annual Report for Boeing described the firm as a leading global aerospace company that develops, manufactures, and services commercial airplanes, defense products, and space systems for customers in more than 150 countries.
“Boeing utilises a wide range of aluminium parts from large machined parts such as frames, webs, and ribs, to fuselage and wing structures, to small detail parts and brackets,” according to a spokesperson from Boeing. “Fuselage skin material is also aluminium for our commercial airplanes, except for the 787 Dreamliner.”
The business is a large purchaser of aluminium for itself and for its suppliers.
“We have a buy-sell strategy for aluminium raw material for plate, sheet, and extrusion,” explained the spokesperson from Boeing. “We aggregate our demand and purchase from aluminium producers and sell to our machine part suppliers.”
The recent years have seen many changes in the economic climate throughout the world.
“Our aluminium-related business is tied to our airplane production rates,” stated the spokesperson from Boeing. “Rates in 2021 have been lower than before the COVID-19 Pandemic, but are recovering. The impact of COVID-19 on air travel reduced demand and slowed down production. We expect steady growth as production rates ramp up.”
Sustainability at Boeing includes “…a bigger focus on recycling and recycled content in aerospace alloys,” according to the spokesperson from Boeing.
Jones Metal Products
Jones Metal Products of West Lafayette, Ohio, is one of a number of American businesses that utilise aluminium to manufacture products for the aerospace and automotive industries.
“In the aerospace market, we make deep drawn aluminium parts for aircraft seats and body frames, leading edge wing parts, and light reflectors,” stated Dan Erb, President of Jones Metal Products. “We work with all the major business
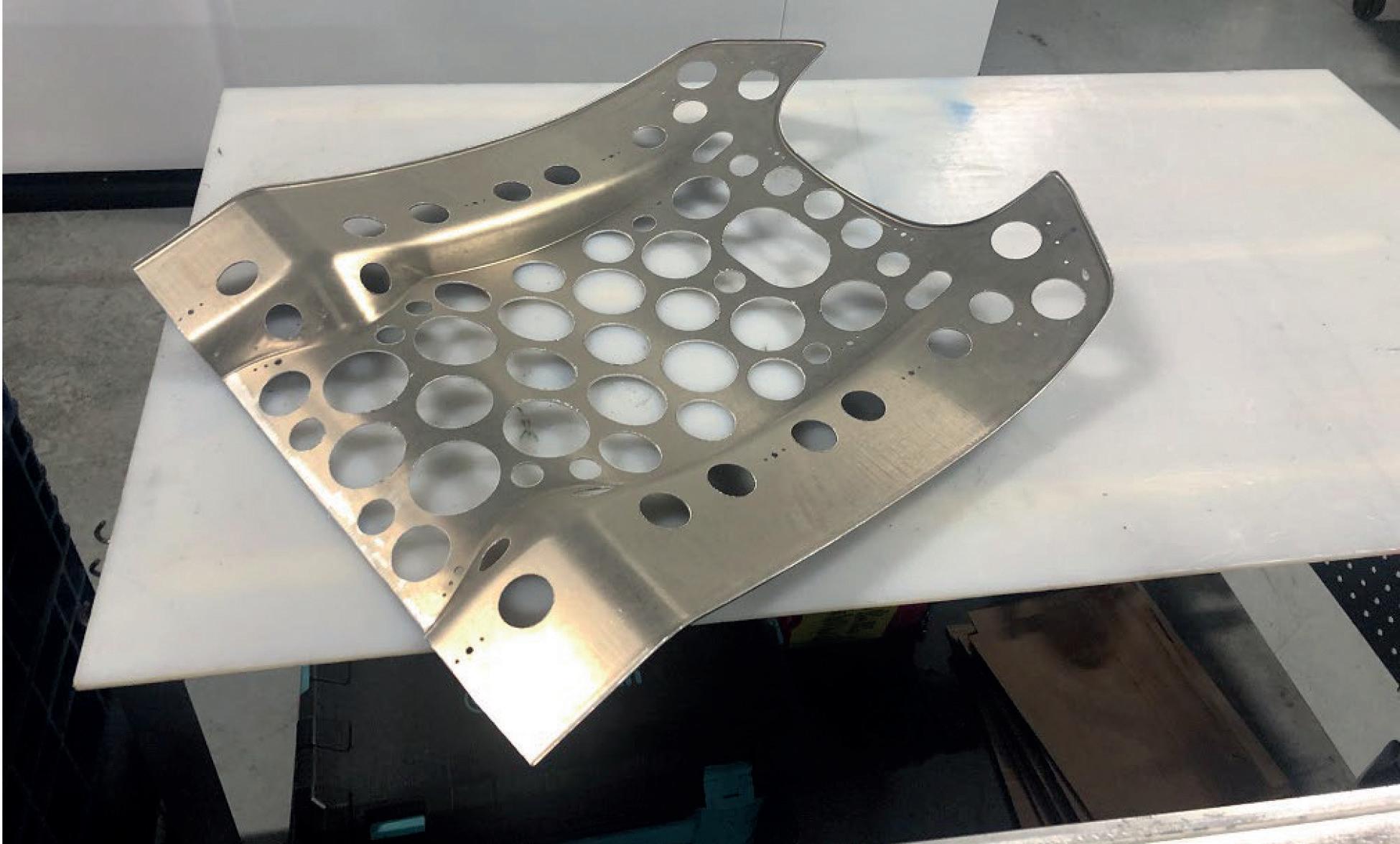
Part of an .040 inch thick 6061-T6 aluminium seat frame for a Cessna aircraft. (Photograph was provided courtesy of Jones Metal Products.)
aircraft companies, repair stations, Boeing parts, and Airbus parts.”
The level of sales dipped during the COVID-19 Pandemic, but is rebounding in 2022. Mr. Erb indicated that 2019 was a strong year for aerospace sales, with (US) $7 million in sales. He noted that sales dropped to about (US) $5 million in 2020 and the same amount in 2021.
“Everything negative over the last two years can be directly tied to COVID 19,” explained Mr. Erb. “People quit flying. Airlines didn’t need as many planes, our orders were reduced or pushed out. As COVID receded, the next issue became the availability of material. This happens at the end of any economic slowdown. People start placing orders and material suppliers have very little inventory. It also takes time for mills to ramp up production. Lead times that were once 30 days have become 180-360 days out.”
Sales are anticipated to see a substantial increase in 2022.
“We are currently forecasting over (US) $8 million in sales in 2022 if this year stays positive in the second half,” said Mr. Erb. “We will end the year up 40% over last year.”
The biggest challenge continues to revolve around the supplies needed to manufacture the finished goods of Jones Metal Products.
“Material availability remains the biggest issue in aerospace,” noted Mr. Erb. “We have countered this by buying more inventory and keeping a safety stock. The quality of our material has been a huge issue. Many of our parts require a high visual quality standard. We are getting sheets every day with more scratches, dings, and dents. This has driven our scrap of raw material to at least double what it used to be.”
Stellantis
Stellantis, a global automotive manufacturer, produces a variety of vehicles in the US, including vehicles under the Chrysler, Jeep, Dodge, and Ram nameplates. Aluminium is used in such products as hoods, doors, fenders, lift gates, and tail gates, according to a representative of the firm.
“In 2021, Stellantis’ North American plants produced more than 1.8 million vehicles under the aforementioned brand names,” according to a representative of Stellantis. “Production in 2021 compared to 2020 was flat.”
Stellantis has found aluminium to be an important part of its sustainability efforts. “Scrap is separated and recycled,” noted the representative of the firm. “Use of aluminium supports light weighting of vehicle platforms…” which help to meet the Corporate Average Fuel Economy (CAFE) standards. These standards are set by the National Highway Traffic Safety Administration of the US Department of Transportation to regulate how far vehicles must travel on a gallon of fuel.
TAPCO
Beyond using aluminium in automotive vehicles, there are a number of industries in the broader transportation industry that utilise aluminium.
One of those industries that may be overlooked, yet is critical to the auto industry, includes signage and traffic devices along roadways, parking lots, and garages. Much of the raw material used in these signs is aluminium.
TAPCO is an American business based in Brown Deer, Wisconsin. The company indicated that it utilises aluminium to manufacture such items as safety signs, flashing beacons, dynamic message signage, cabinets for traffic signals and Intelligent Warning Systems (IWS), poles and bases for traffic signals and IWS, and parking gates, among other products.
Customers for these items include, according to TAPCO, local governmental departments of public works and state departments of transportation; schools, universities, hospitals, and other institutions; large manufacturing, industrial, mining, and corporate campus facilities; military bases, national parks, and other Federal governmental facilities; airports, seaports, and freight terminals; and parking facility operators.
“Unit volume for our aluminium products has been on the rise along with the rest of our IWS business,” stated Michael Long, Manager of Product Management at TAPCO. “Sales revenue has increased at an even higher rate as a result of raw material price increases being passed along to the customer.” �
TAPCO utilises aluminium to manufacture pedestrian crossing signage. (Photograph was provided courtesy of TAPCO, July 22, 2019.)
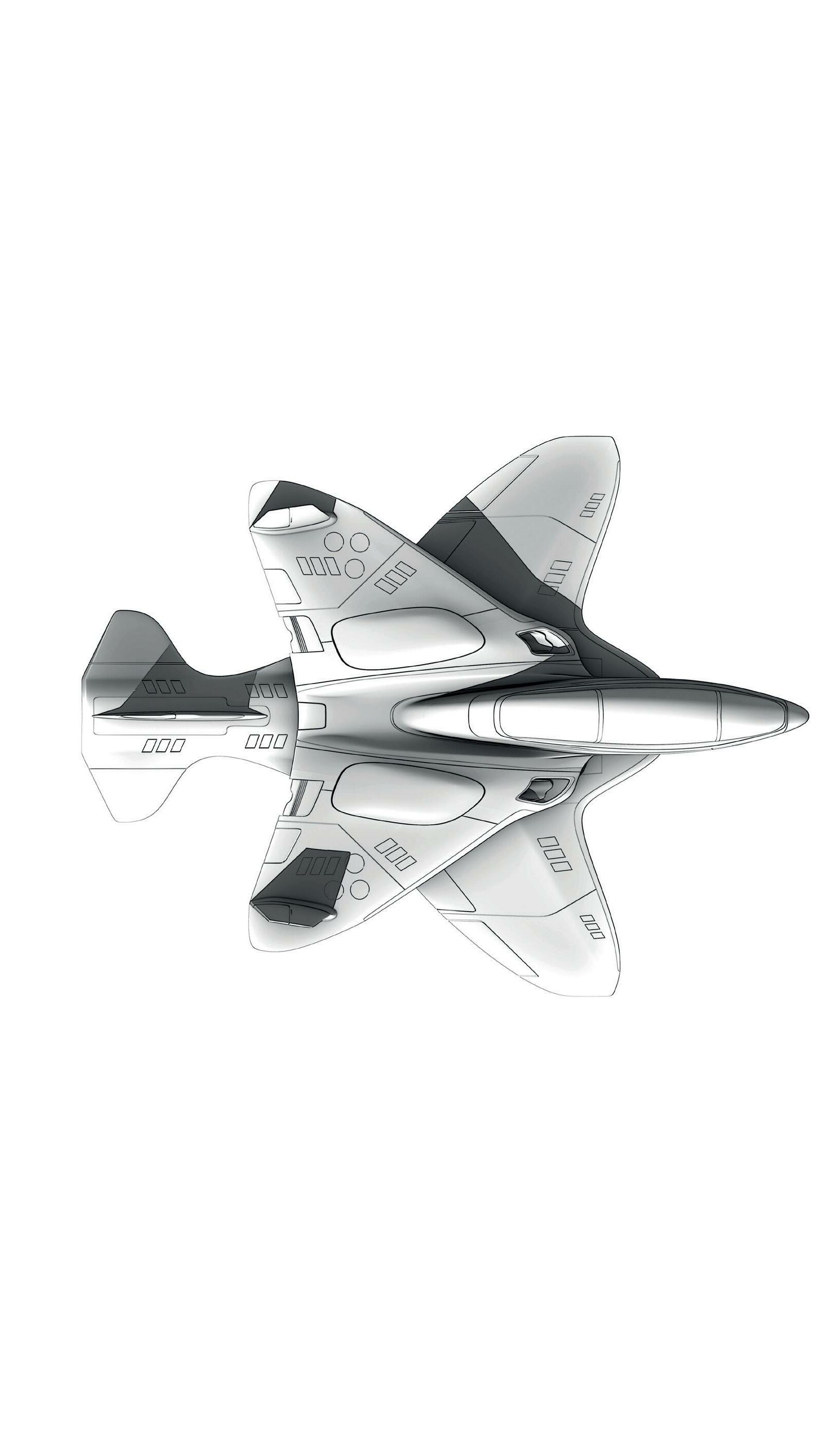