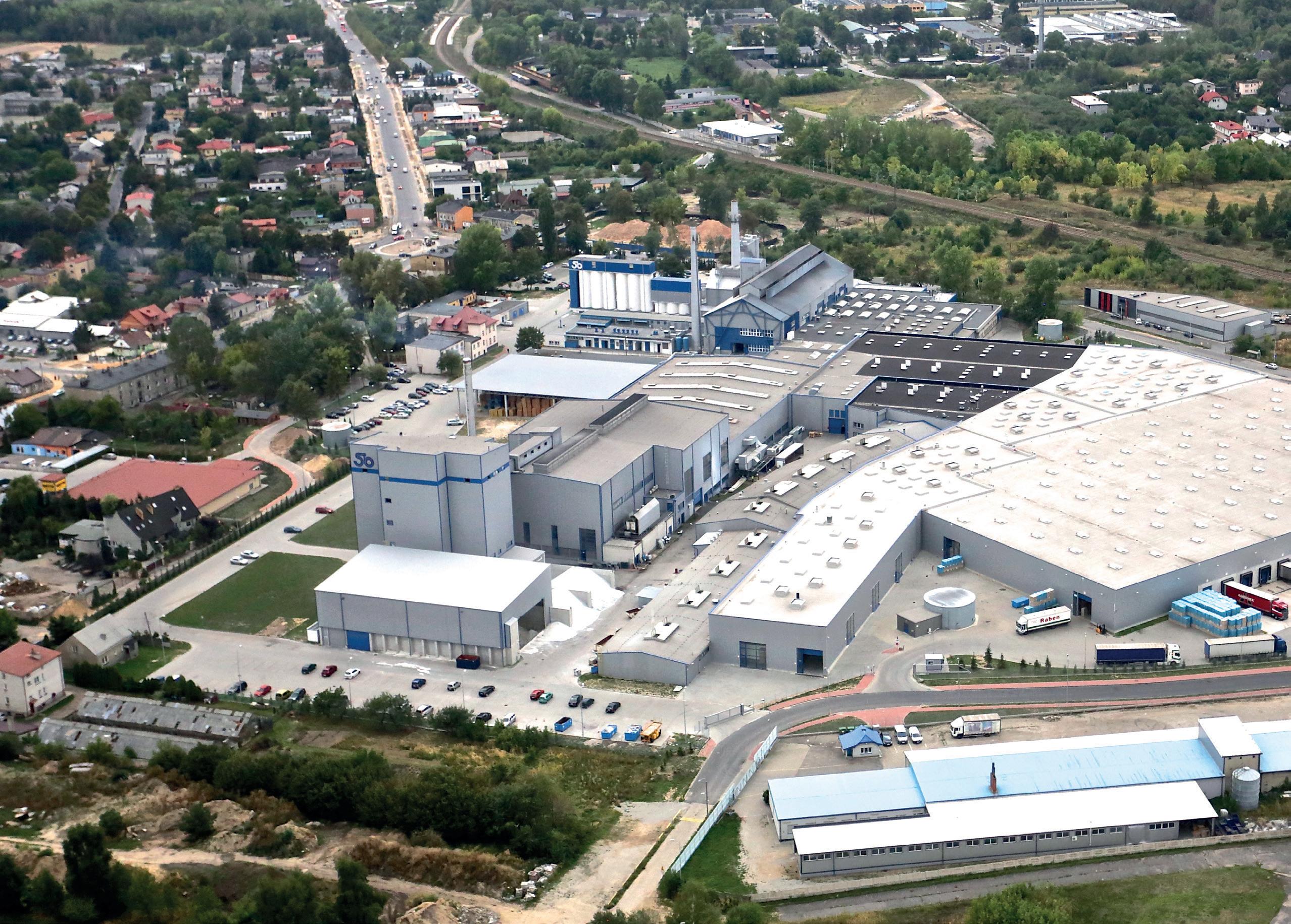
6 minute read
Decoration: Stoelzle
� Stoelzle Czestochowa plant
High-speed spraying line brings immediate benefits at Czestochowa
A recent investment in a high-speed spraying line at Stoelzle’s Czestochowa, Poland glass decoration site has reaped immediate benefits as the company responds to an increase in demand for glass. Andreas Herzog* describes the spraying line while, inset, Maciej Lubas**, describes some of the proudest creations crafted at the site.
We started decoration operation at our production site in Czestochowa, Poland in 2007, with three second-hand machines and 35 people. Since then we have grown constantly in terms of machinery and staff.
Step by step, we introduced new decoration processes and machinery.
In the past 15 years our group has invested more than €35 million into the growth of our decoration department.
We are now working on 16 modern and automatic lines, including all common decoration processes. More than 250 million bottles are decorated per year in Czestochowa.
Some of the techniques offered by Stoelzle are screen printing, spraying, frosting, decals, Quali Glass Coat 2.0, digital printing, hot foil stamping, and accessory application.
At Stoelzle Czestochowa we decorate all kind of glass containers. We serve the Prestige Spirits market as well as the Perfumery & Cosmetics sector and pharmaceutical products.
Tableware articles such as the 1lt mug for the Octoberfest in Munich complete the portfolio. Practically we are brightening up our high quality glass from 5 ml miniatures up to 1.75 litre bottles on automatic machines.
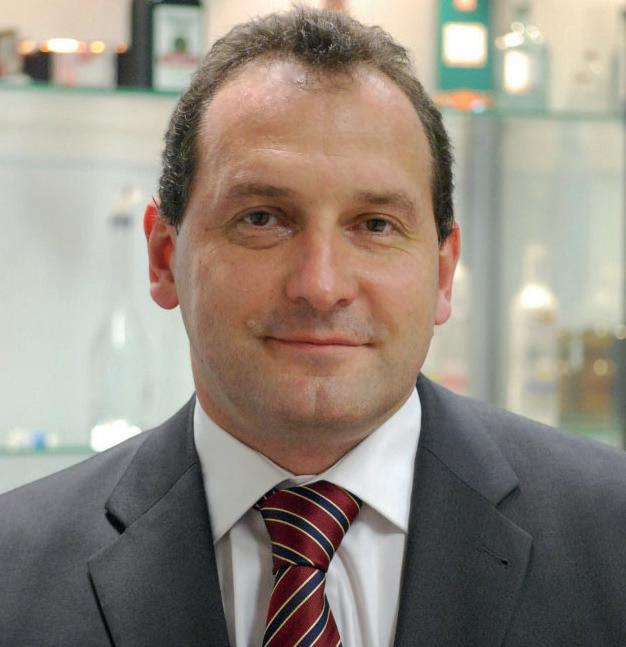
� Andreas Herzog
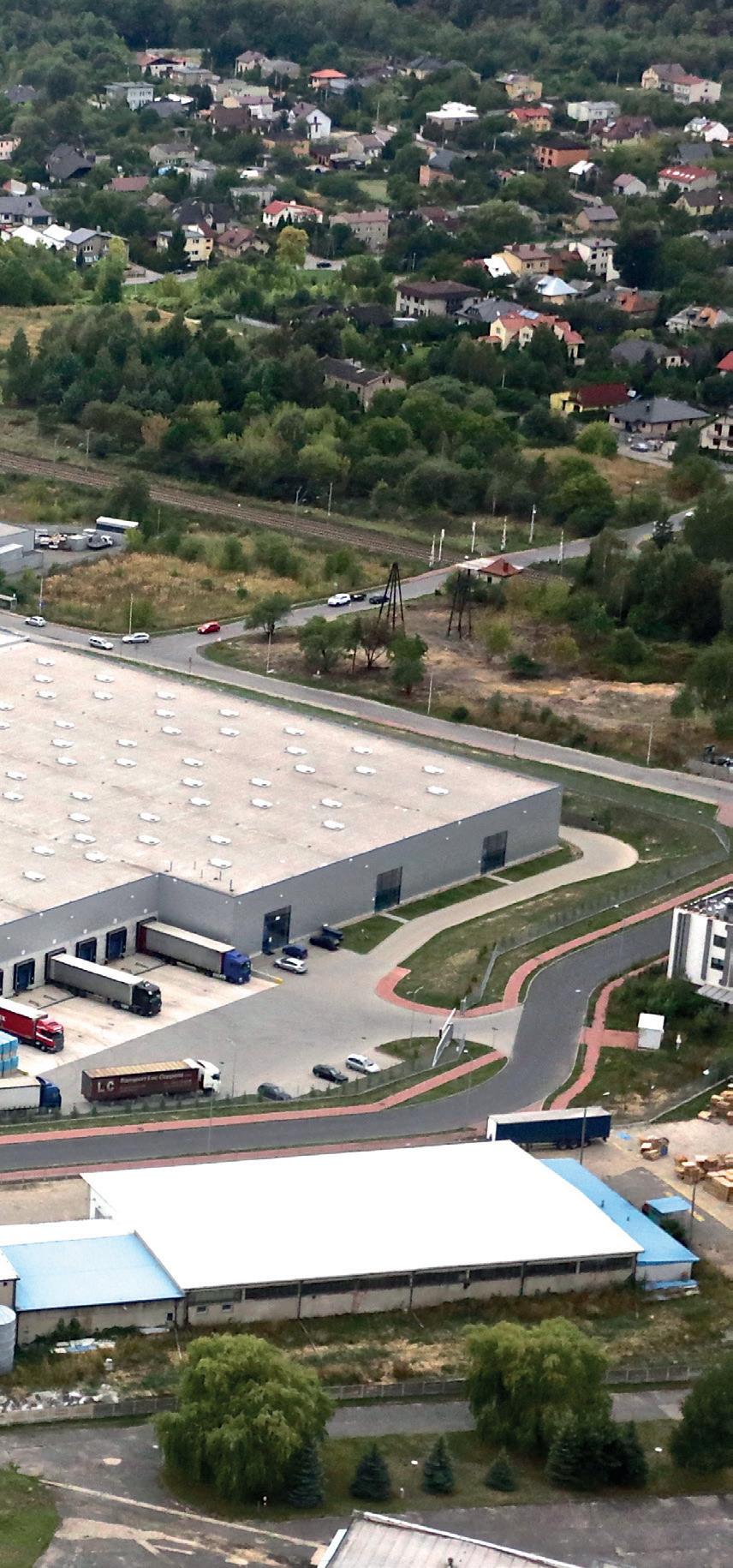
Fig 1
Our new high-speed spraying line (figures 1, 2 and 3) offers outstanding performance, efficiency and automation to our customers.
It is equipped with an automatic loading and unloading system and also takes advantage of fast curing by infrared lamps, which further enhances the production capacity.
As the demand for decorated glass containers has grown over the past few
Maciej Lubas (right): Product and Sales Deco Development Manager at Stoelzle Czestochowa has more than 12 years expertise in the decoration department. He describes some of hs favourite bottles he has helped create in that time.
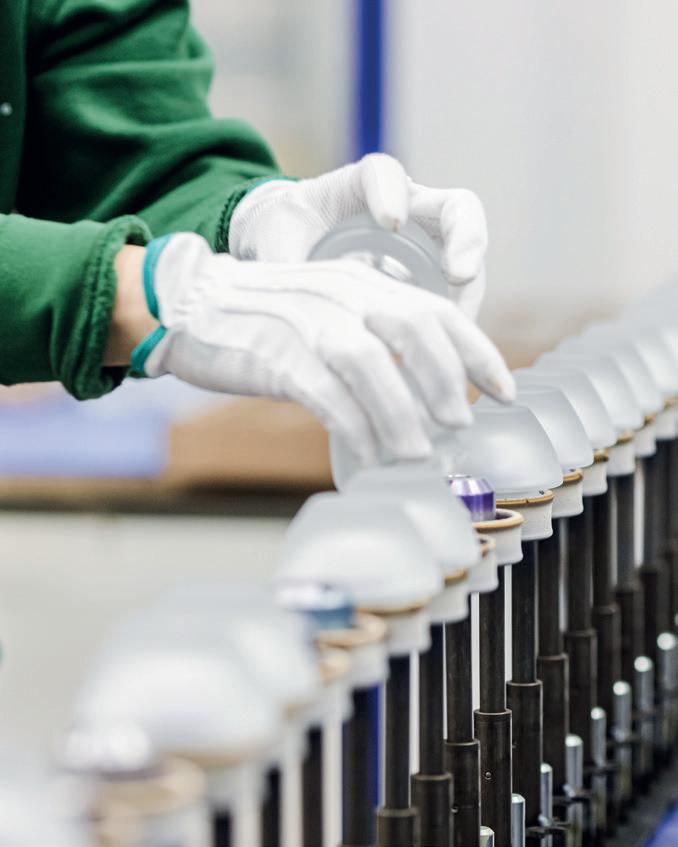
a) Ciroc bottles – a range of bottle sizes and different flavours, all with a special decoration, in various decoration steps (pictured below). We can proudly say that the Ciroc range was one of our initial projects in decoration, so the basis of further growth. STC started with a standard decoration (spraying, badging) for four-five flavours in 2011. Every flavour has been characterised by a certain basis colour (green = apple). Year after year, more standard decorations were successfully developed, reaching a total of 10-11 flavours so far. We also developed the demanding decoration for at least seven special editions, such as the Ciroc Blue Steel featured in the movie Zoolander, which were even more demanding. b) 30ml Make-up bottle Double Ware by Estee Lauder: this bottle was decorated in three steps, which are frosting, screen printing on the front and back, and gold hot foil stamping. This was one of the first items we decorated via hot foil stamping. We invested in a hot foil stamping machine and started to learn this completely new decoration process fast. It took us just a couple of weeks to overcome all technical difficulties and decorate this demanding bottle technically perfectly. Nowadays, we still decorate this item at a very high level of efficiency and quality, reaching an output of 10-12 million pieces per year. c) 50-100ml Paco Rabanne Pure XS bottle: this item combines two decoration processes, gradient spray and gold hot foil stamping on the sharp edge of the facetted body. It took us almost six months to develop the automated decoration process for this demanding bottle. Other suppliers failed to successfully reach the target within a two year development time.
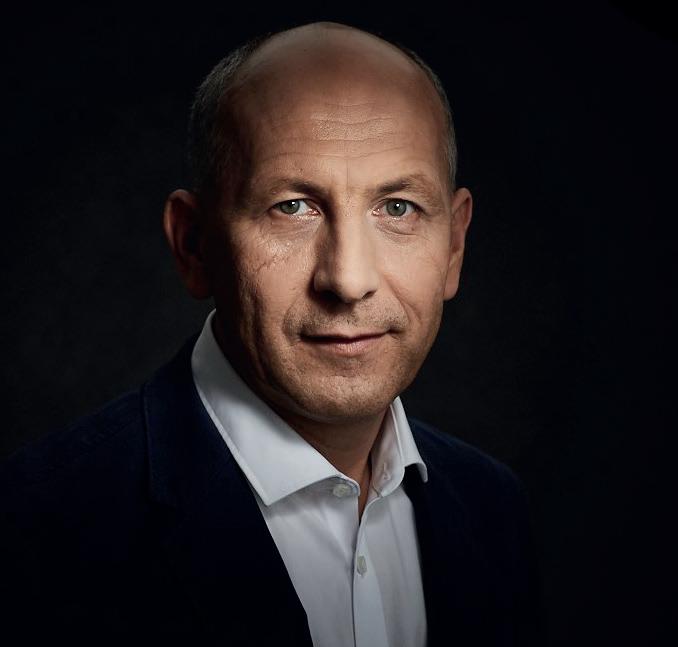
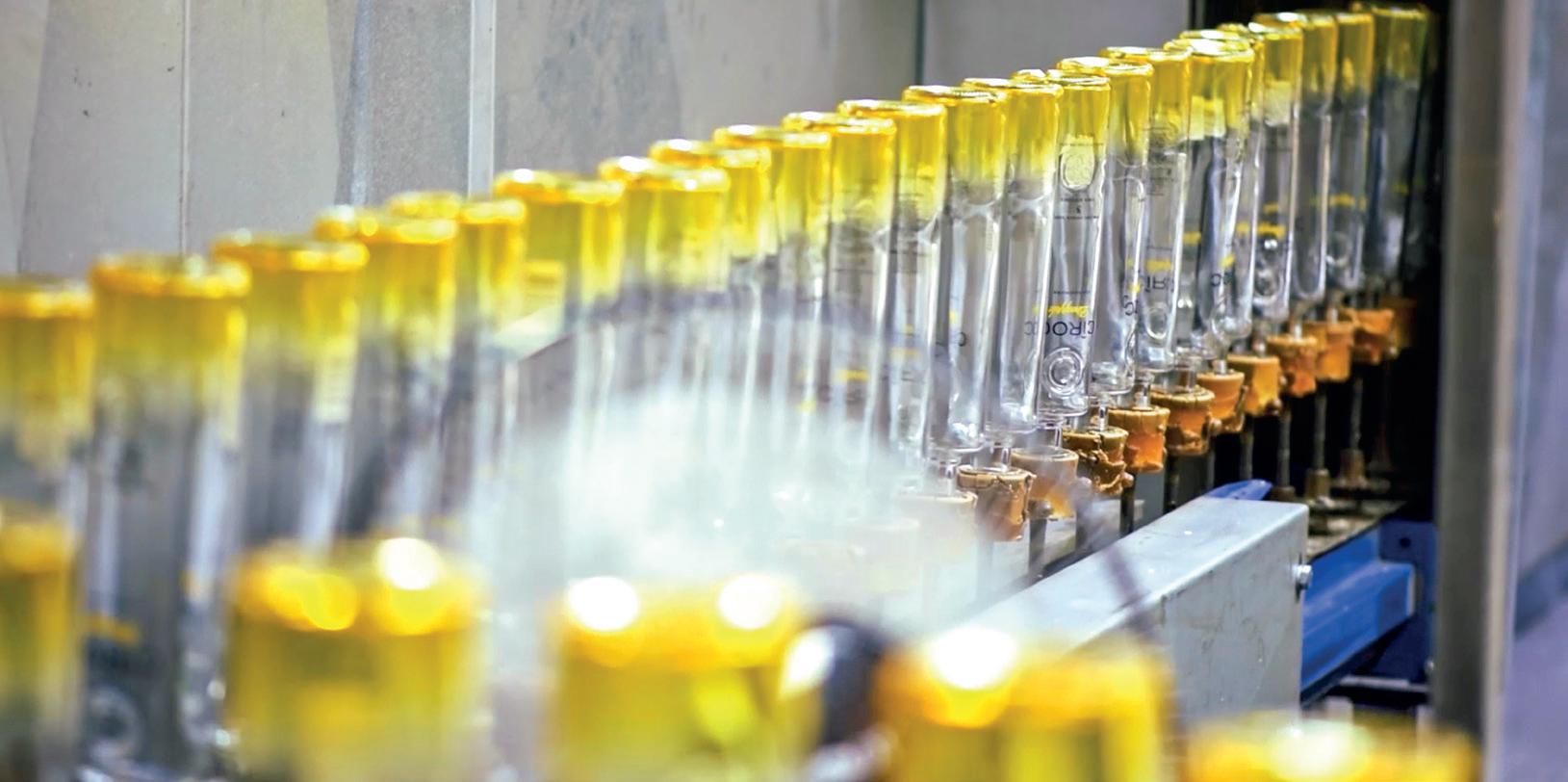
years, Stoelzle will now be able to offer increased capacities and shorter leadtimes. It can do all kind of spraying effects such as multicolour and vignette even faster.
For the opening of the new line we have invited our owner and our board to see the new machine running as we believe an investment of this size is always a big sign of trust from our owner.
In my opinion, decoration is incredibly important to a glass container. A bottle is a bottle, but a decorated bottle is outstanding!
With decoration you can tell a story and perfectly convey the emotions and ideas promised by the precious content. Decoration adds value to the bottles. Choosing standard bottles and making them unique by decoration is also a
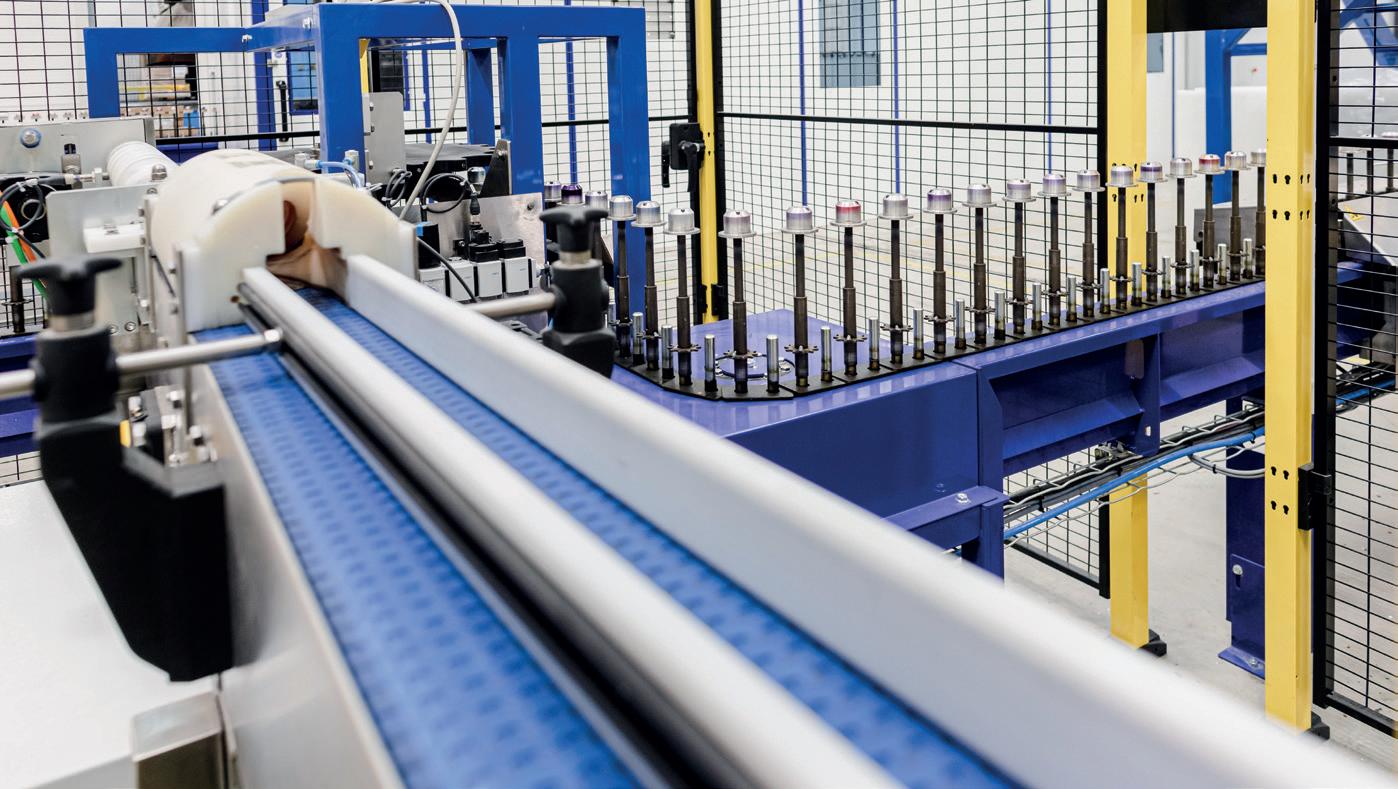
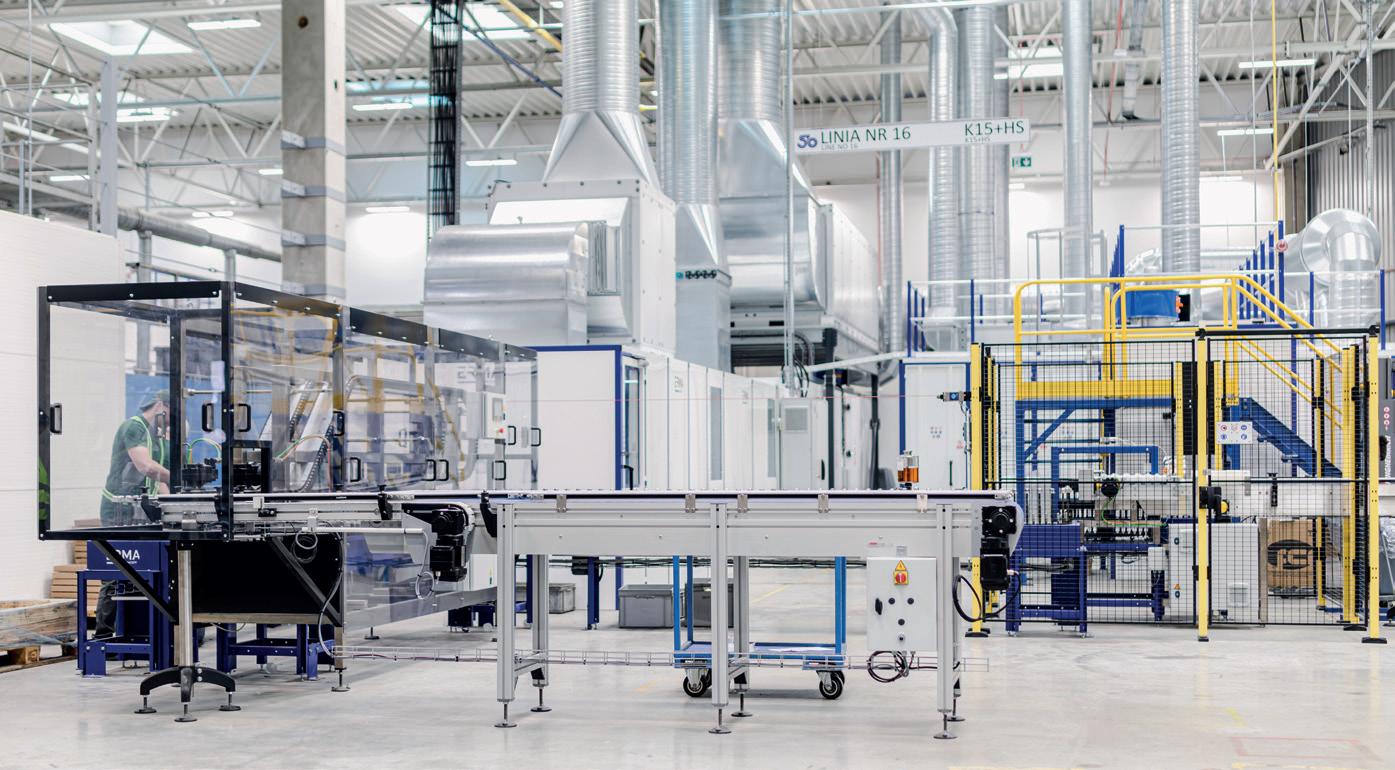
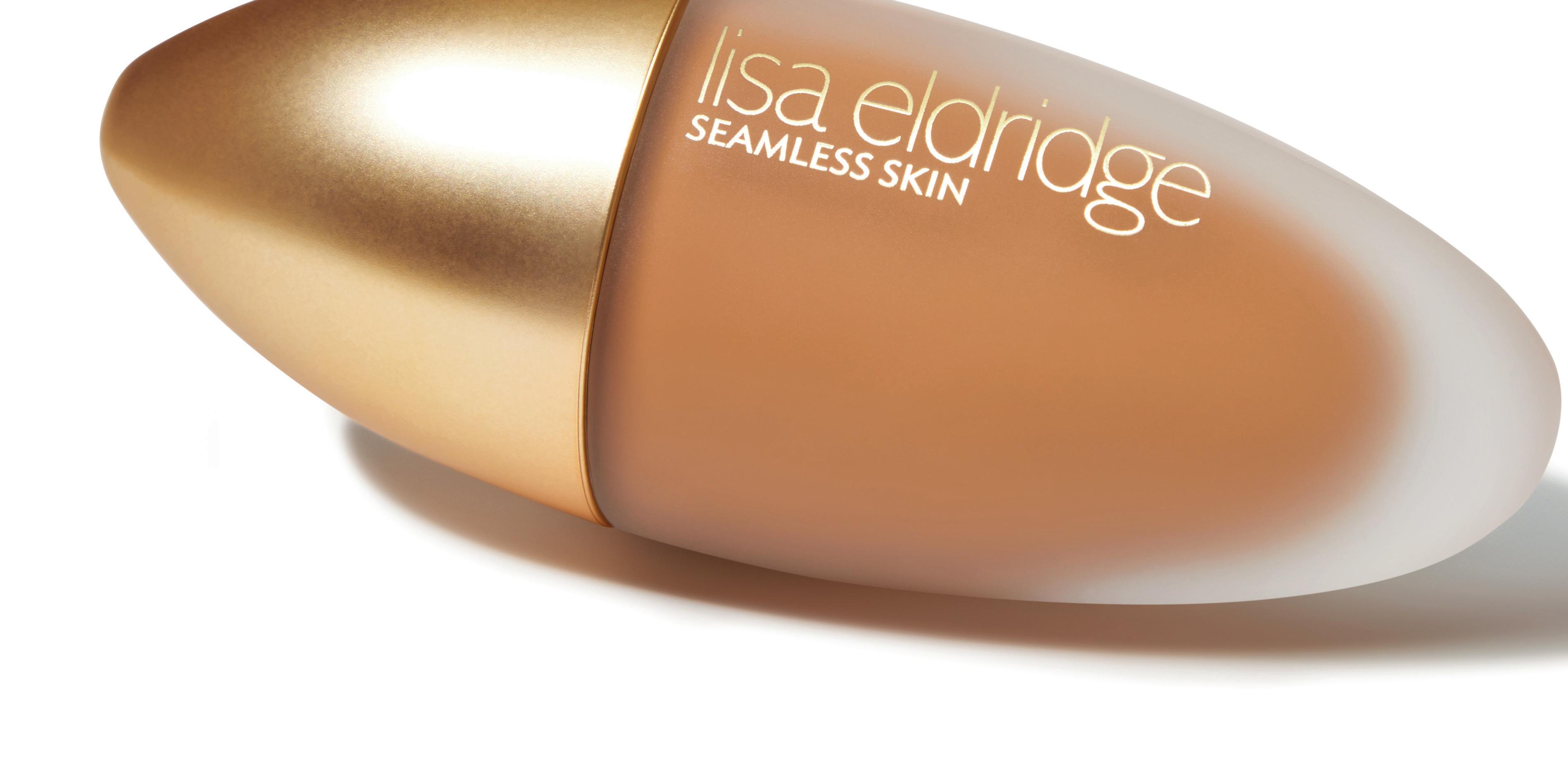
Perfumery & cosmetics bottle� frosted and hot foil stamped.
� Figure 2 above and figure 3 below.
convenient choice to reduce costs of glass packaging. The main current customer trends in glass decoration is sustainability.
All processes and all operations are being evaluated for their environmental footprint. So, we constantly strive to develop more sustainable techniques and processes. For example: the powder coating technique Quali Glass Coat 2.0 saves 77% of CO2 emissions compared to standard lacquering (liquid paints).
The latest innovation is the recycled ink, which is developed exclusively for Stoelzle, from rubber waste. The carbon black used in colour pigmentations derives from end-of-life tyres, which now have a sustainable purpose.
Based on its CSR strategy Stoelzle has committed themselves to use only eco-friendly, water-based inks and to withdraw from solvent-based colours, in all of its three decoration sites. In addition to this we are developing with our partners the use of new ink generations, such as low curing inks, or inks made out of waste.
Our new line is equipped with fast curing Infrared lamps. This results
In terms of digital technology, Industry 4.0 is standard and absolutely necessary in all manufacturing processes such as decoration.
We measure and analyse performances, downtimes and several other important production parameters automatically.
Two years ago we started a group-wide digitalisation initiative based upon an internally developed software.
The goal is to improve the manufacturing process by tracing and recording data. All manufacturing machines and quality inspection machines are connected to the same network and forward information to a centralised database. The main target is to boost reaction time and gain flexibility by maximising knowledge about processes.
For this new line we worked with our supplier for the first time. To do so, a mutual partnership and trust must be created from the beginning. Every line is a tailor-made machine, a symbiosis between the supplier’s technology and the customer’s expectations and requirements. �
Fig 2
in a much higher energy efficiency and a considerable reduction of gas consumption.
In the whole Stoelzle Group we have recently implemented a process and energy data management system where the decoration sites and their production lines are also included.
More than 5000 check points have been implemented throughout the Stoelzle Glass Group to collect and evaluate energy data to further improve all processes. *Head of Group Decoration , **Product and Sales Deco Development Manager Stoelzle Czestochowa, Poland www.stoelzle.com
Fig 3
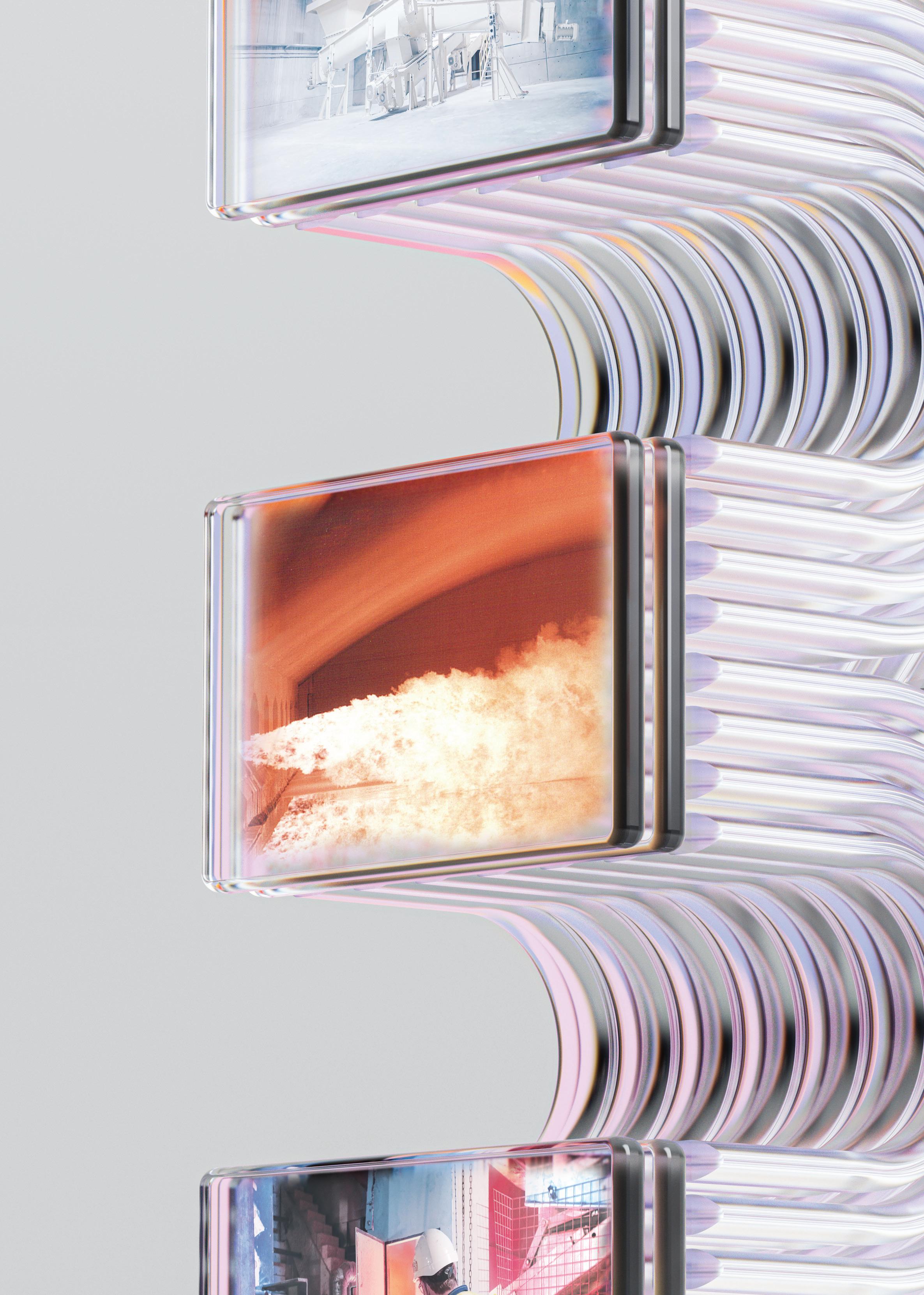