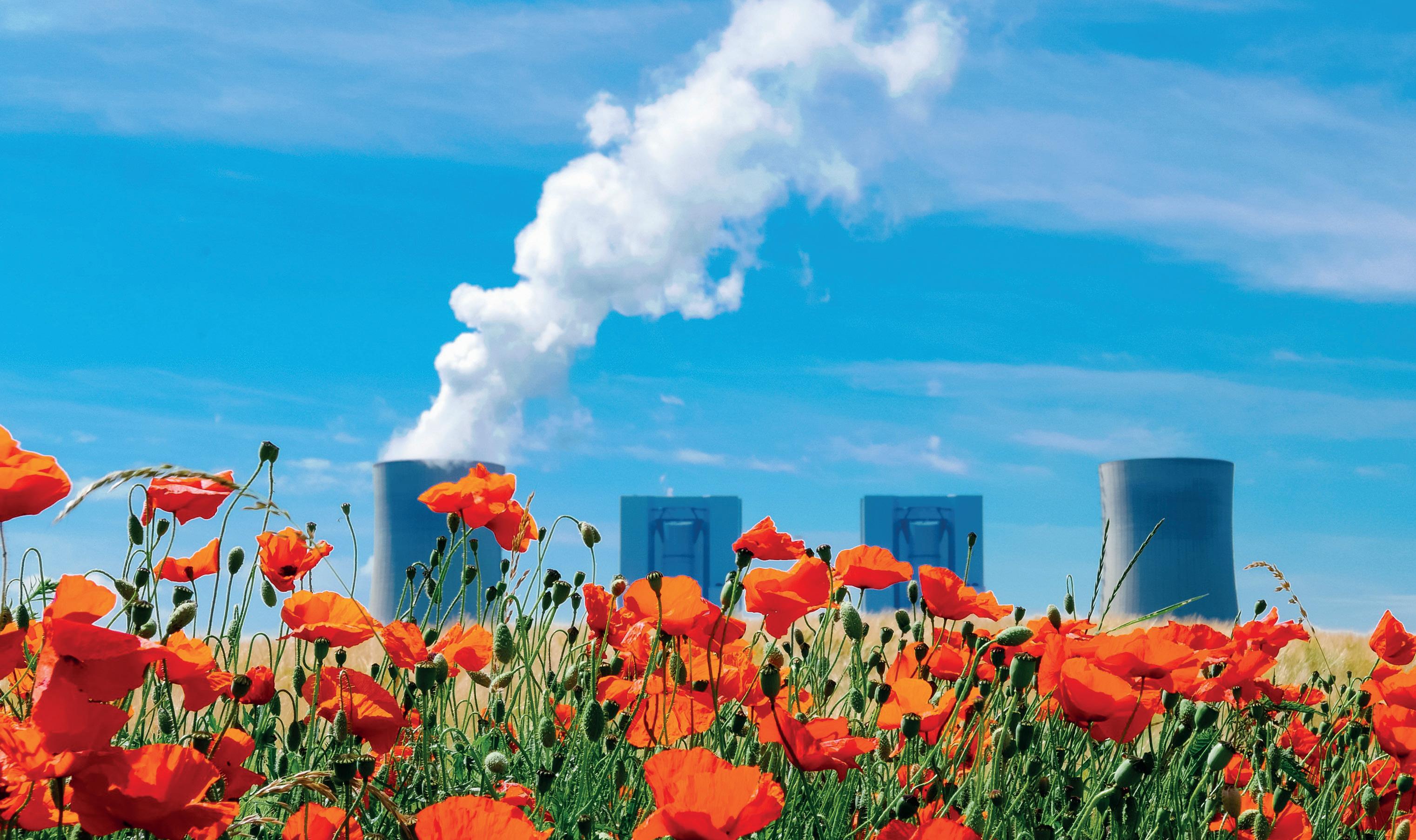
4 minute read
Decarbonisation: ZeroCO2-Glas Aiming for sustainable container production
Aiming for sustainable container production
The ZeroCO2-Glas project aims to develop a hydrogen-fired glass melting tank for CO2-neutral container production. Christian Roos* discusses the work so far and its plans for the future.
Aspecialist group of glass-focused organisations has forged a partnership in a bid to help make the glass manufacturing process more sustainable using renewable energy.
The bold aims of the ZeroCO2-Glas group are to manufacture glass for container production with net zero emissions and substantial energy savings.
Saving energy and CO2 emissions is one of, if not the, major challenge for future generations. The consortium aims to continue the glass industry’s long history in striving for emission reduction and energy savings.
To achieve these goals, several companies decided to form the ZeroCO2 Glas project. These are: RWTH University, furnace technology group Horn Glass Industries, and the International Partners in Glass Research (IPGR). The IPGR consists of 10 glass-related companies:
Continued>>
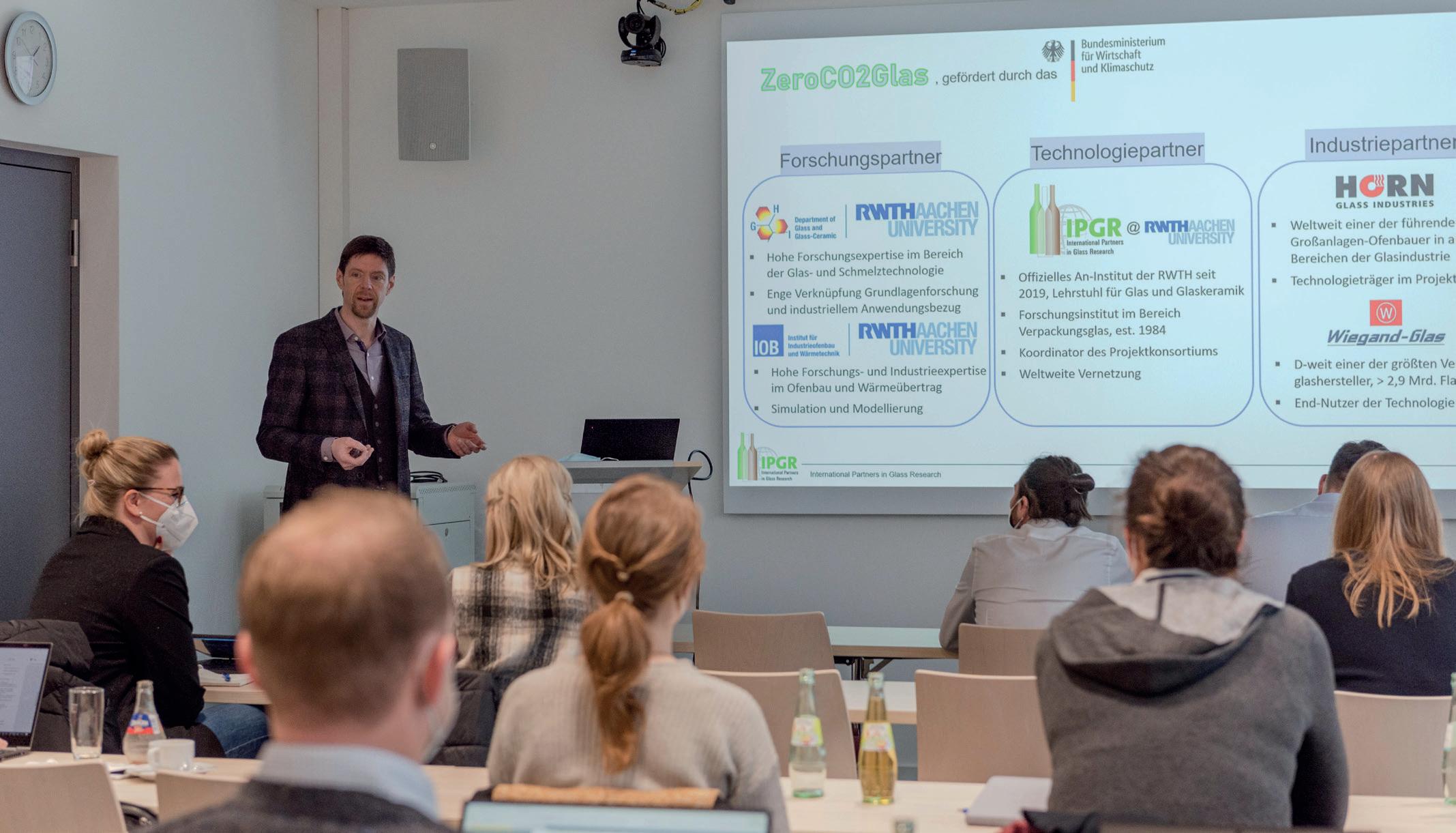
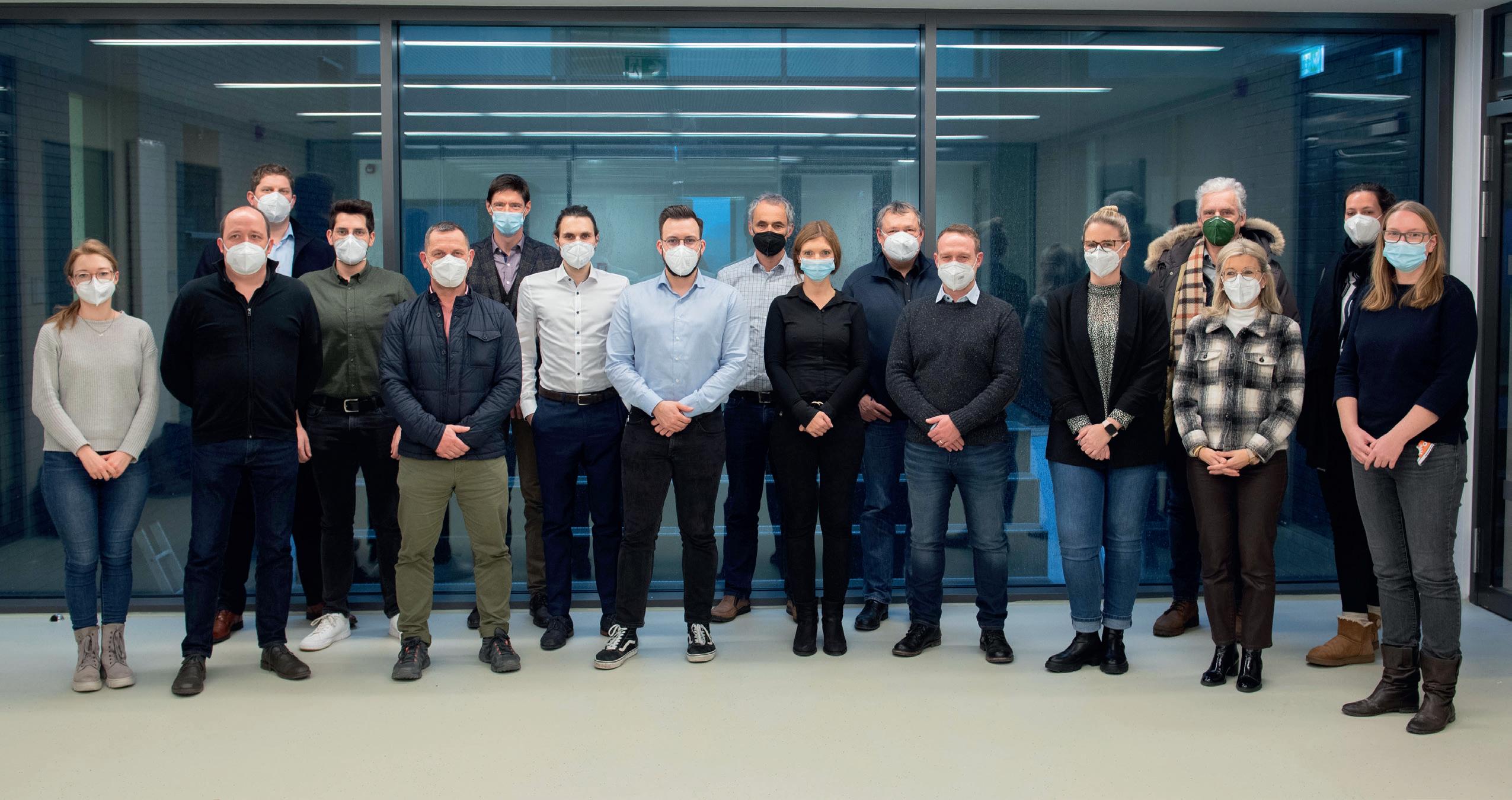
Emhart, Sisecam, Orora, Nihon Yamamura, Fevisa, Gallo, Vetropack, Wiegand-Glas, Stoelzle and Vidrala.
The goal of the project is to use an allencompassing approach to develop a revolutionary glass melting process.
This includes a new type of glass melting tank, which can melt glass for container production with net zero CO2 emissions and energy savings.
The project is funded by the German Ministry for Economy and Climate, BMWK, with a maximum of €8.4 million with a total project volume of approximately €15 million. The funding is in aid of increasing energy efficiency, expanding renewable energies and reducing greenhouse gases significantly.
ZeroCO2-Glas
Pre-work on the project actually started over four years ago, when various melting concepts and hydrogen combustion was evaluated.
Mr Roos said the consortium explored heat recovery technology such as a thermo-chemical regenerator (TCR) on the basis of methane or methanol. But the partners chose hydrogen for the following reasons: both TCR approaches had been examined with more expertise by other institutions, TCR had never been a main focus for them and hydrogen enables a true CO2-free process if generated with renewable resources.
The consortium also explored different furnace designs and firing techniques, as well as multiple investigations on glass combustion interaction. All this helped to finalise the furnace design.
The upscaling stage of the project started January 1 this year and is planned to run for the next three years. The aim is to achieve a glass melting furnace with a lower energy consumption compared to conventional furnaces, which would be in the range of 15%, as well as CO2-free glass melting.
This will be achieved through using alternative, CO2-free raw materials for batch melts that have a lower reaction enthalpy. This will result in energy savings due to avoiding unnecessary humidification of the batch and an additional increase in process efficiency. The latter is due to a special melting process that will reduce the dwell time of glass in the furnace as well as an improved furnace design.
The furnace will be set up in Aachen, Germany, as a hybrid furnace with hydrogen-oxy and natural gas-oxy firing. Additional electrical heating, together with the corresponding peripherals, will represent a fully-fledged container glass site with an IS machine.
The melting tank has high flexibility in using both hydrogen and electricity with a broad mixing ratio. In addition, new glass compositions are being tested within the project, which allow advantages in terms of their emissions and properties of the finished glass. All approaches have already been tested on a laboratory scale.
Partnership
Mr Roos said that each of the partners in the project brought a unique skill to the project. With the departments for Glass and Glass-Ceramics as well as Industrial Furnaces and Heat Engineering, RWTH University has strong scientific knowledge as its basis. IPGR has the perfect network and melting technology know-how. As a renowned furnace manufacturer, Horn Glass brings its high expertise in furnace technology and design. Wiegand-Glas supports forming and quality evaluation of glass as an industry-partner and an end-user of technology.
Glass container manufacturer Stoelzle has also made significant investments in areas such as R&D to achieve targets in the field of energy reduction and boost ecofriendly processes and technologies.
Mr Roos said the project was different to other collaborations, as the consortium is not focusing on generating renewable fuels. The project concerns the glassmelting process and “takes it as a precondition” that hydrogen supplies are available.
He believed that anything else would “enlarge the project to an extent that is not manageable” for the consortium.
Conclusion
Mr Roos said the consortium was “very positive” that they could produce a CO2 free manufactured container by the end of the project. Despite the project being high-risk, he believes that the partners’ commitment, both financially and in their work force, to the project will ensure it succeeds. �
*General Manager of International Partners in Glass Research (IPGR), Aachen, Germany www.ipgr.com