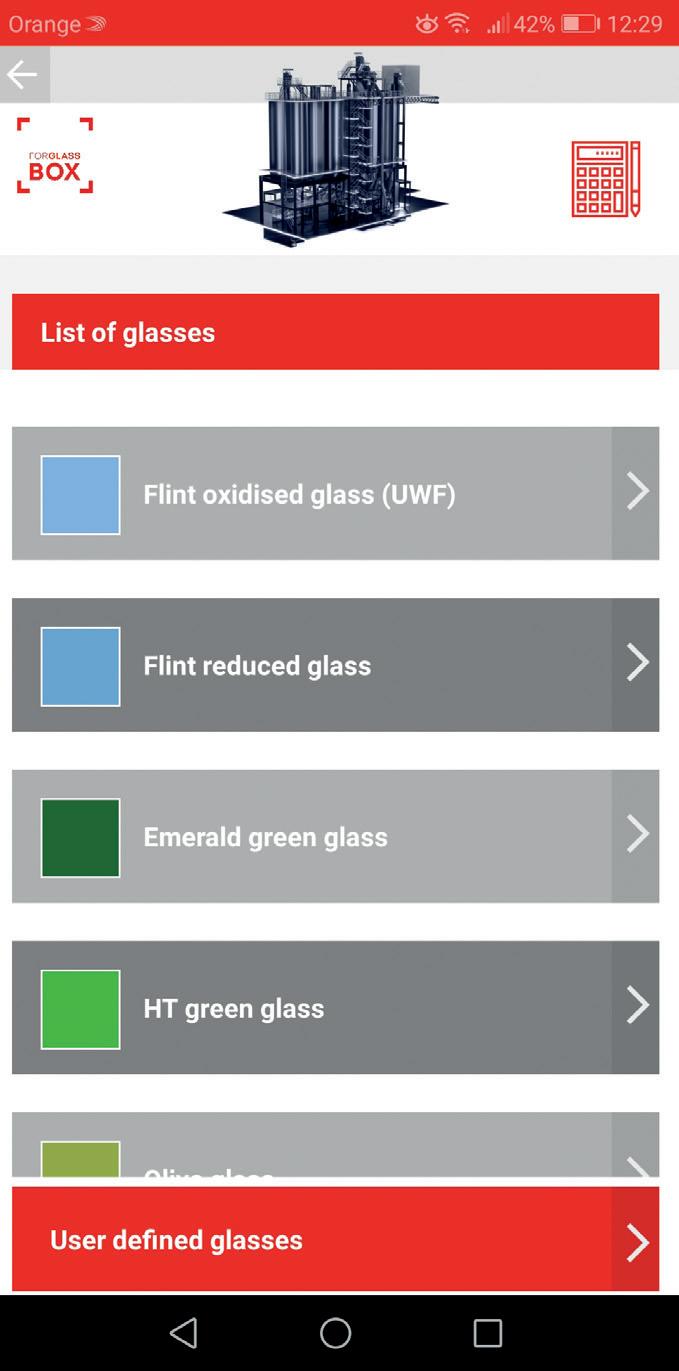
6 minute read
Batch plant Forglass
ForglassBox – 21st century technological support for producers
Piotr Knast* and Marian Klisch** explain how the company designed an engine that can make complex calculations at the tap of a button via a smartphone app.
What if it were possible to perform complex, sophisticated calculations and select raw materials of defined chemical composition for a batch, from which flint (colourless), amber, green and olive glasses with desired properties could be melted – and to do it anywhere, anytime, on a smartphone?
Forglass, the Polish glass melting technology supplier, has answered this question and created the first calculating engine that takes advantage of the powerful processors on modern mobile devices and enables the glassworks technologists to perform complex, sophisticated calculations on a smartphone that is always in their pocket. The application, called ForglassBox, allows the user to select specific raw materials and assumptions (limits) for batch and glass according to its colour requirements, and it calculates the technological and physicochemical properties of these glasses, including: � Temperatures at which the glass reaches desired viscosity; � Liquidus temperature; � Cooling time; � WRI, RMS, RGT, linear thermal expansion coefficient; � Density; � Specific electrical conductivity; � Heat capacity and; � Effective thermal conductivity.
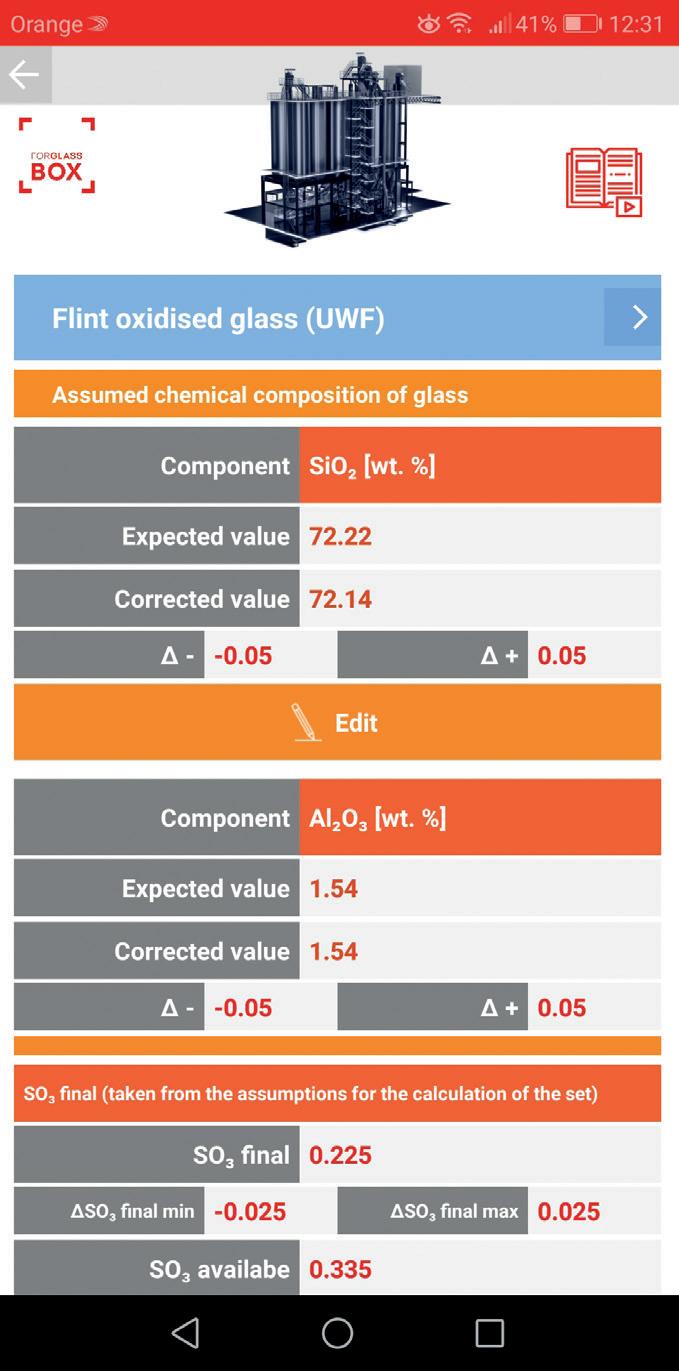
Continued>>
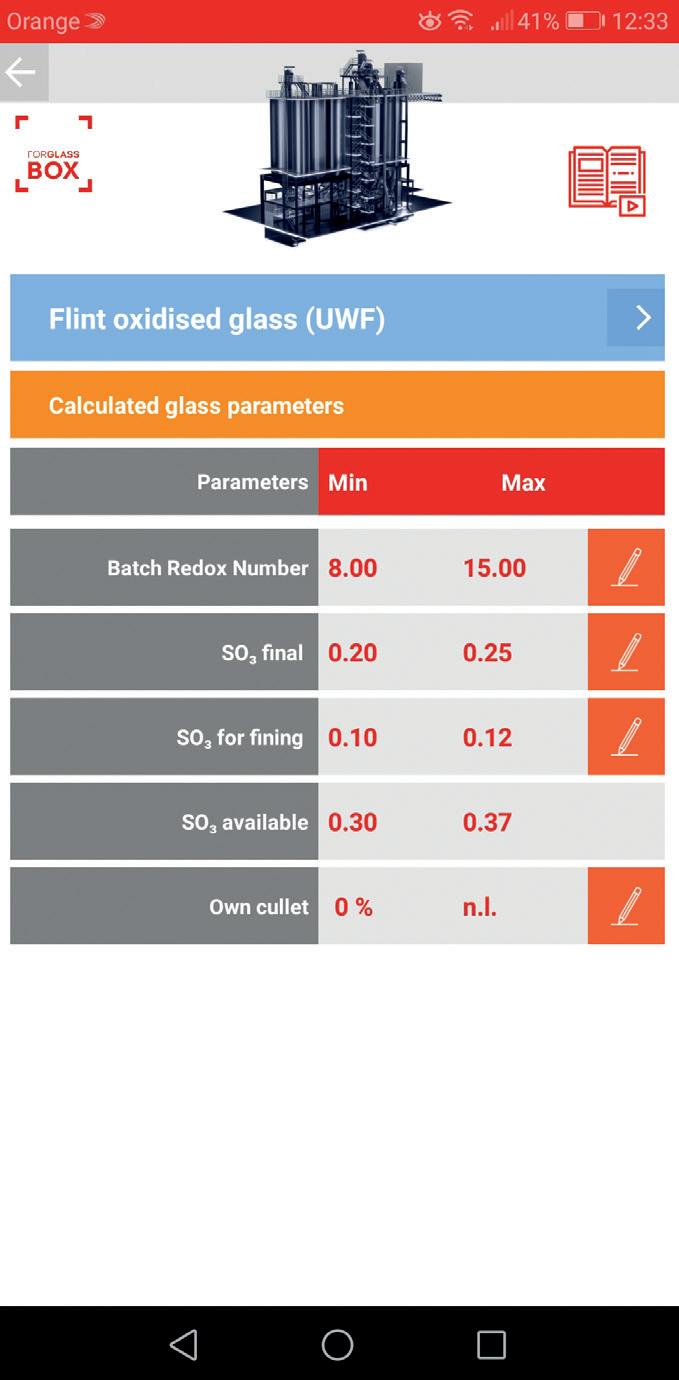

The ForglassBox application has builtin “intelligence”, which also corrects the chemical composition of the glass selected for calculations, if the selected raw materials make it impossible to obtain the assumed concentrations.
The aim of the developers of the application was to turn the modern smartphone into a handheld computing centre for the technologist.
Unlike the computer, smartphone is a device that all people involved in the manufacture and processing of glass, as well as designers of equipment for the glass industry carry in their pocket and can access anywhere and at any time.
The application is “smart”, which means that when calculating the proportions of individual raw materials, it takes into account not only the given chemical composition, but also the Redox Number of the batch, necessary to obtain the expected colour of glass and optimises the amount of sulphates, taking into account the needs of fining and SO3 saturation concentration in the glass of the given colour after forming.
The application compares the chemical composition of the glass selected for calculations with the compositions of the raw materials selected for the batch
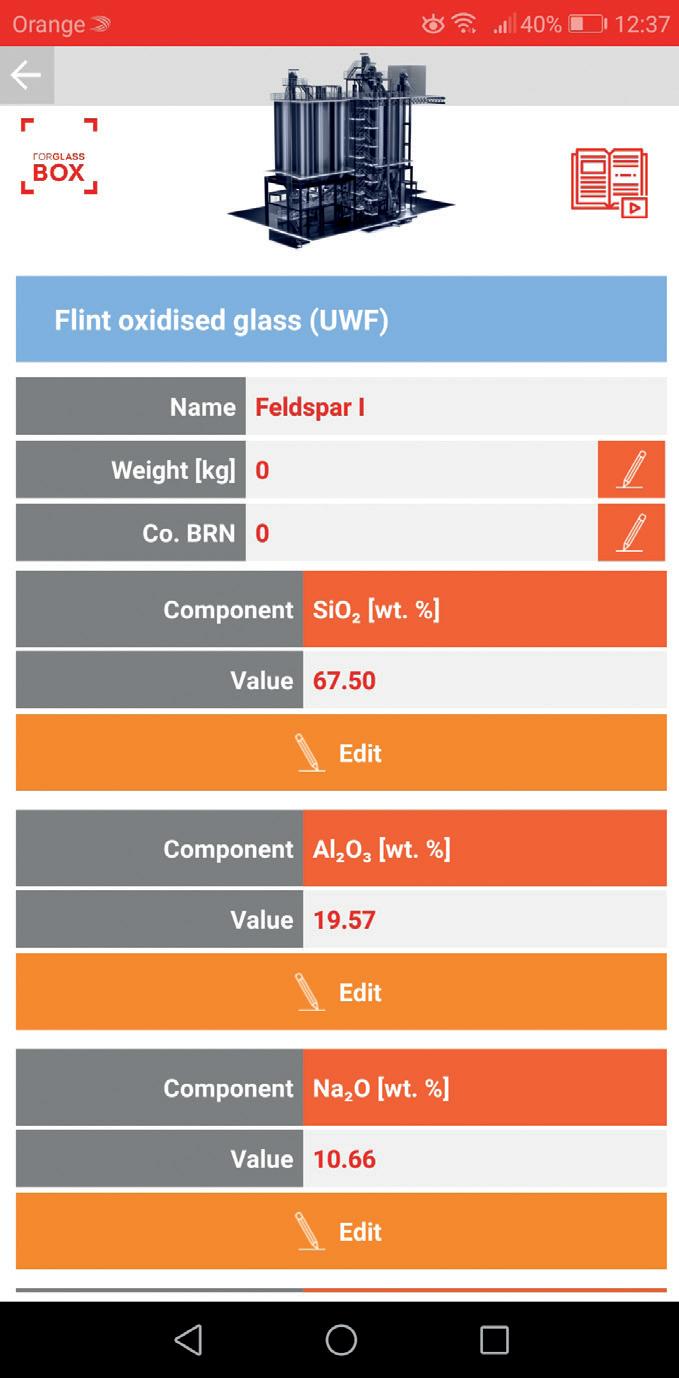
� Figs 4, 5 and 6
and suggests the necessary corrected proportions of Al2O3/Al2O3+SiO2, K2O/ (K2O+Na2O) and MgO/(MgO+CaO).
The calculated glass properties can be used to design temperature profiles for melting, fusing, tempering and annealing, optimising the furnace’s thermal power requirements from combustion space and boosting, as well as furnace geometry.
Application architecture
The architecture of the application is userfriendly, offering less advanced users the option to select any of the ready-made packages from an extensive list, while advanced technologists can modify most of the parameters in order to adapt them to the specific requirements of the production facility, local raw materials and their own habits.
For the first group, a glossary of terms used in the application and in glass practice is included. For the second group of users (although certainly not limited only to them), the application provides a constantly updated list of innovative and tested solutions from Forglass.
Both above and below are the examples of calculations that can be performed with the ForglassBox application, including screen shots that intuitively guide the user through the steps.
Fig.1 shows that the user can select from the list of glasses [flint reduced glass, flint oxidised glass (UWF), olive glass, amber glass, emerald green glass, HT green glass], for which he needs to calculate the batch.
Perform additional or new calculations/ operations on glasses, for which calculations had already been made and saved them in user-defined glasses collection, the user can access them at the bottom of the screen.
Fig.2 contains the fields to select the concentration (as [wt %]) of glass components: SiO2, Al2O3, Na2O, K2O, MgO, CaO, MnO, Fe2O3, TiO2, Cr2O3, CeO2 i SO3 and the maximum allowable deviation of those oxides (down ?- or up ? +) in the glass melted from the batch calculated with the boundary conditions for selected raw materials.
The user can modify the concentration of a specific component by clicking the ‘edit’ button below the data section of a given oxide.
The assumptions for calculations can be edited by the user after clicking ‘edit’

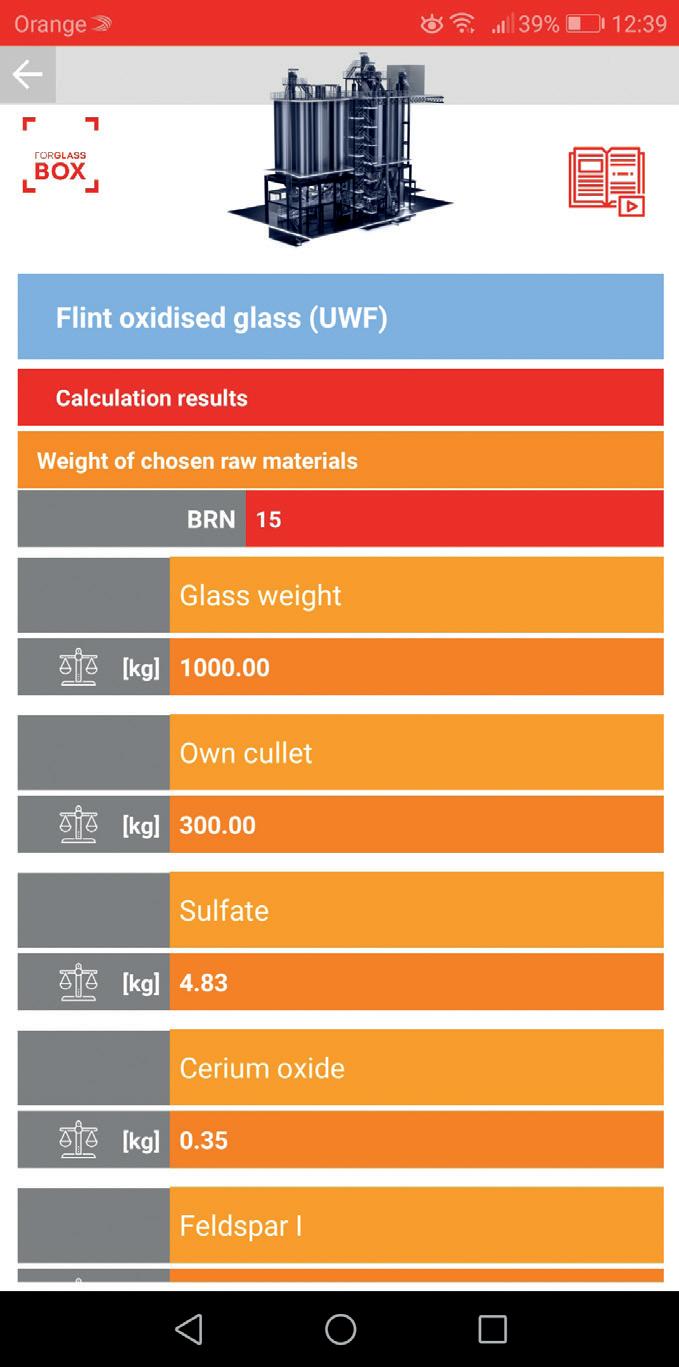

� Figs 7, 8 and 9.

button to the right of the selected set of values.
The default values in each set are the most typical ranges of BRN, final SO3 and fining SO3 for the selected glass type. While the user can modify the values for BRN, final SO3 and fining SO3, setting values outside of the typical range for a given colour of glass can make it impossible to achieve.
Also, setting values for SO3 that are tool low or too high may result in technological problems such as underfining or foam on glass surface.
The application informs the user of these conditions if it detects that they may occur (Fig.3).
Fig.4 contains the list of raw materials selected for batch calculation.
The user can modify the name and composition of selected raw materials by clicking the > symbol to the right of the name of the material.
Materials with alternatives have the additional button that can be clicked to reveal another screen, which allows the user to choose alternate material.
Properties of a raw material selected for batch calculation are also shown. User can change its name, source, etc. User can also adjust (change) the concentration of various oxides, according to the chemical composition of the raw material to be used in the batch (Fig.5).
After making all the necessary changes in 1) chemical composition of glass; 2) limits (boundary conditions); 3) raw materials selected for the batch; and 4) their names and chemical composition, user can start batch calculation on this screen (see fig.6).
The results are shown on the screen with the batch calculated for the userdefined amount of glass/batch/sand (Fig.7).
Fig.8 shows the chart for chemical composition of glass: � IN: selected by user for calculations � IN corr.: selected by user after correcting the concentration of Al2O3, K2O and MgO to levels possible to achieve from selected raw materials � OUT: resulting from the batch calculated by the application
Additional screens (fig.9) show the list of calculated technological properties: � Temperatures relative to viscosity - 100 dPas (lgh=2) - 1 000 dPas (lgh=3)
- 10 000 dPas (lgh=4) - 100 000 dPas (lgh=5) - 1 000 000 dPas (lgh=6) - 10 000 000 dPas (lgh=7) - Littleton Point (LP = 44 668 359,2 dPas; lgh=7,65)* - Annealing Point (AP = 25 118 864 315 095,9 dPas; lgh=13,4)*
� Cooling time (CT)* � Working Range Index (WRI)* � Relative Machine Speed (RMS)* � Rigid gob temperature (RGT)* � Liquidus temperature (Tliq)* � Primary phase crystallisation field (most probable crystalline phase appearing during glass crystallisation)* � Variance between rigid gob temperature - RGT and liquidus temperature (? RGT – Tliq)* � Variance between temperature corresponding to viscosity for lg?=3 and liquidus temperature (?Tlg?=3 – Tliq)* * – definitions of terms used can be found in the Glossary of terms �
*CEO, ** Head of R&D, Forglass, Kraków, Poland https://www.forglass.eu/en/forglassbox