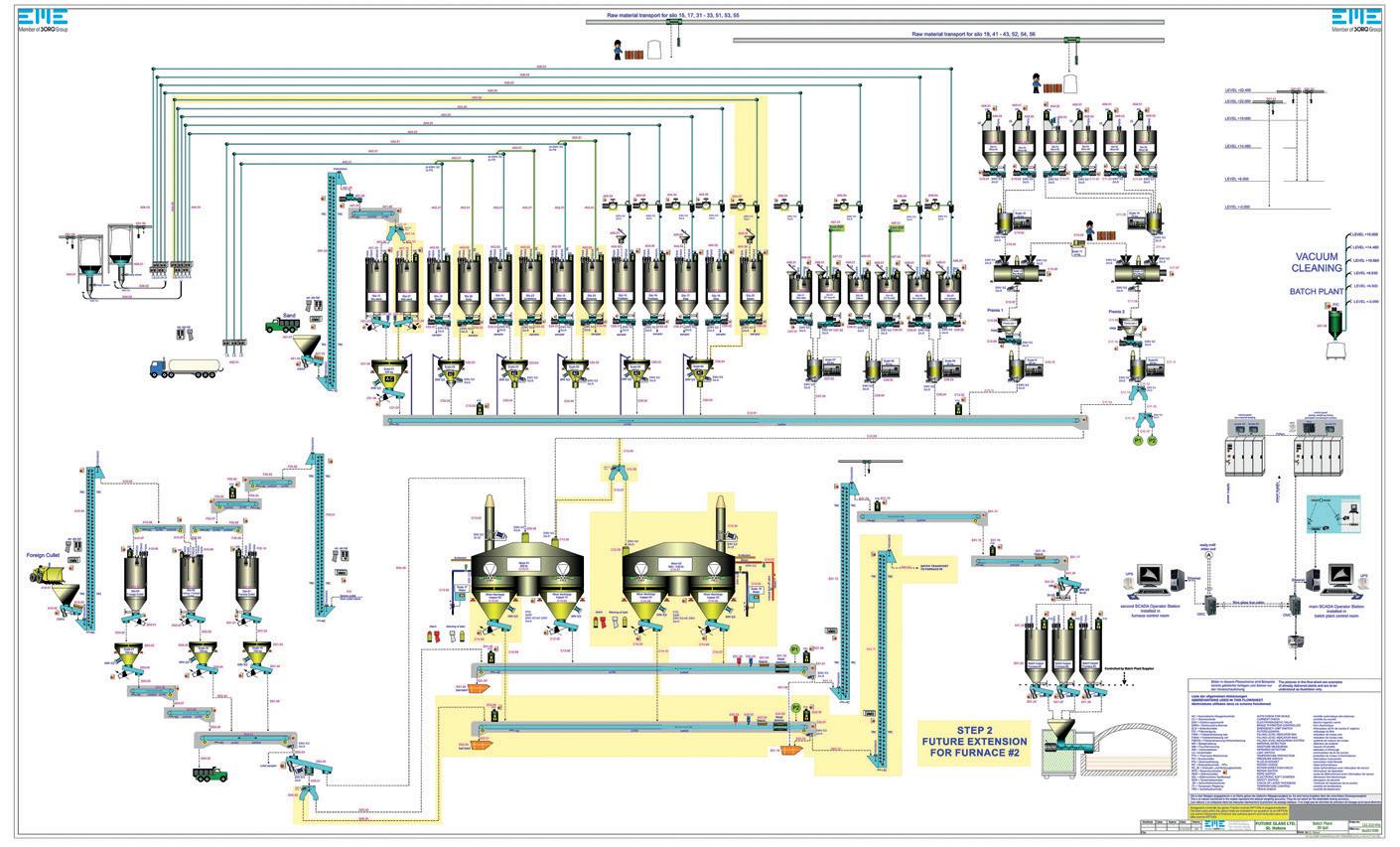
7 minute read
Batch plant EME
Engineering solutions for the future
EME explain how offering a complete range of services has allowed it to be part of the Glass Futures facility design.
In this modern day and age customers are looking for a partner that can offer them a complete range of engineering services.
EME provides everything its customers need, ranging from Feasibility Studies through to fully Engineered Projects. 100 years of experience combined with a passionate and expert team of engineers and specialists allows the company to deliver Innovative Engineering Solutions in line with customers’ requirements.
EME says it is proud to be able to say that not-for-profit, research and technology organisation, Glass Futures is one such customer that needed an innovative and flexible engineering solution for their new Global Centre for Excellence in St Helens, UK.
It believes that one of the most important aspects of developing a solution for a customer is to listen carefully to their needs and allow them to convey the vision they have for their project.
During the bid phase for the Batch
House Specification contract, EME actively engaged with the Glass Futures’ team to understand the end goal of the project as well as the objectives for the first phase, the development of a Detailed
Specification and Design for the Batch Plant.
As a result of this it was able to offer our services to Glass Futures at a competitive price without any compromise!
In the early stages of the project, EME spent many hours in discussions with the expert team that Glass Futures had put together to fully identify their needs.
Due to the Covid-19 pandemic EME and Glass Futures had to make use of online meetings, sharing ideas and concepts remotely, to fine tune all the details.
A clear goal from the onset was to provide a solution that provided full flexibility while at the same time integrating the latest technology and best technical solutions.
In addition to the technology selection, EME engaged with other key stakeholders from the Glass Futures team.
These stakeholders provided input into critical aspect of the design, such as health and safety, structural integration into the main building, utility interfaces as well as day to day operational aspects.
“It is important for Glass Futures to get the design right and include a much greater level of operational flexibility than you would expect in a commercial glass manufacturing batch plant where the expected limits of operation are clearly defined. This has been a significant challenge for Glass Futures and EME throughout this collaboration”, said Peter Liggett, Capital Projects Manager of Glass Futures.
The EME team was presented with an abundance of data and challenges to overcome.
To bring all this together in a

� Pic 1. Unique process flow diagram.
meaningful way, that was easy for the customer to work with while still having complete technical details, EME has developed a unique process flow diagram.
The flow diagram is designed in such a way that it provides a graphical representation of the technology and process of the batch house.
One of the biggest challenges for both Glass Futures and EME was that our design had to allow for the most flexibility possible.
This is because St Helens is a state-ofthe-art research and development facility, therefore it is logically impossible to define exactly all the raw materials and recipes from the start.
Understanding this, EME developed a solution that allows for a variety of materials to be used flexibly within the plant.
Raw material handling and unloading operations are to be carried out using a variety of innovative methods. A wide
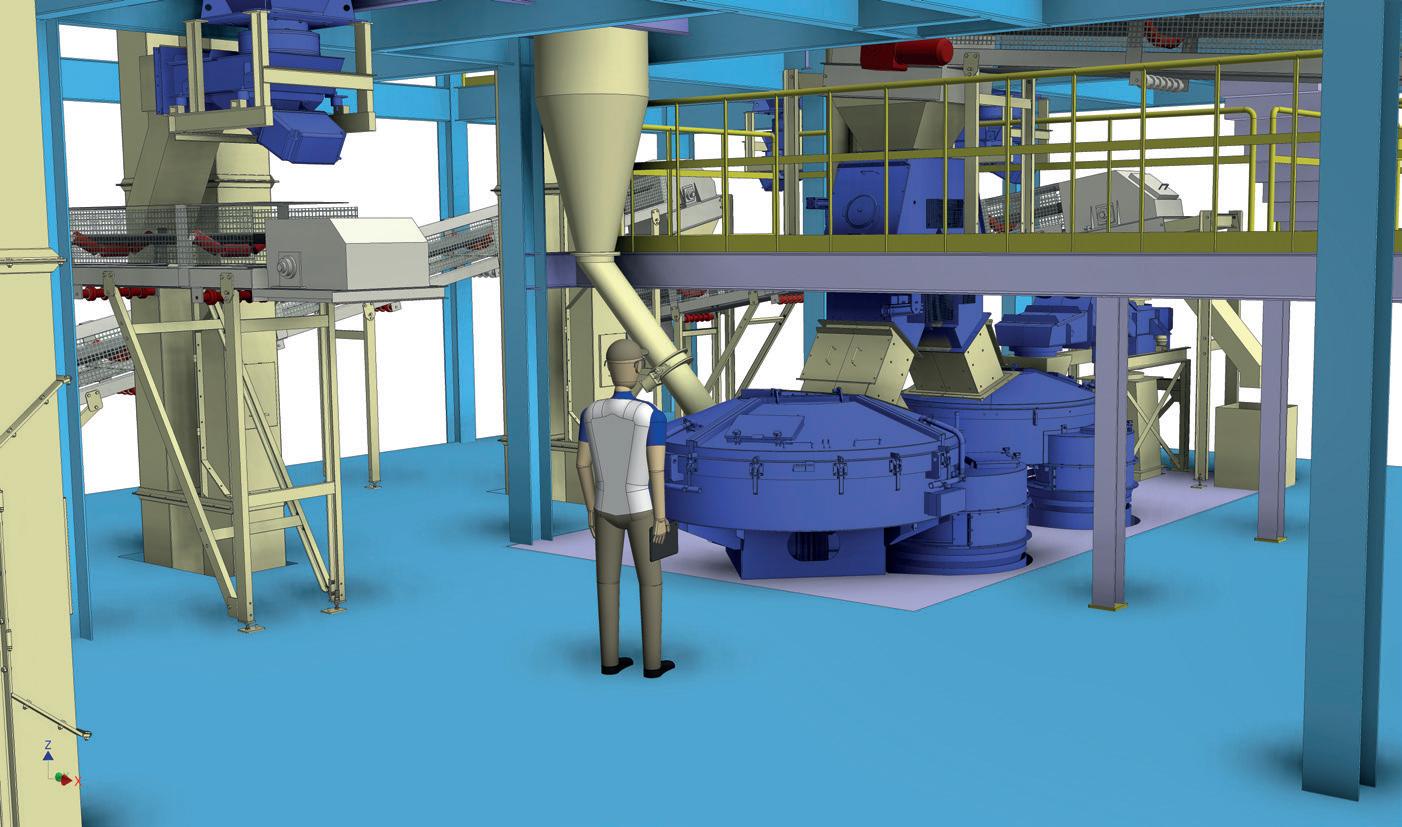
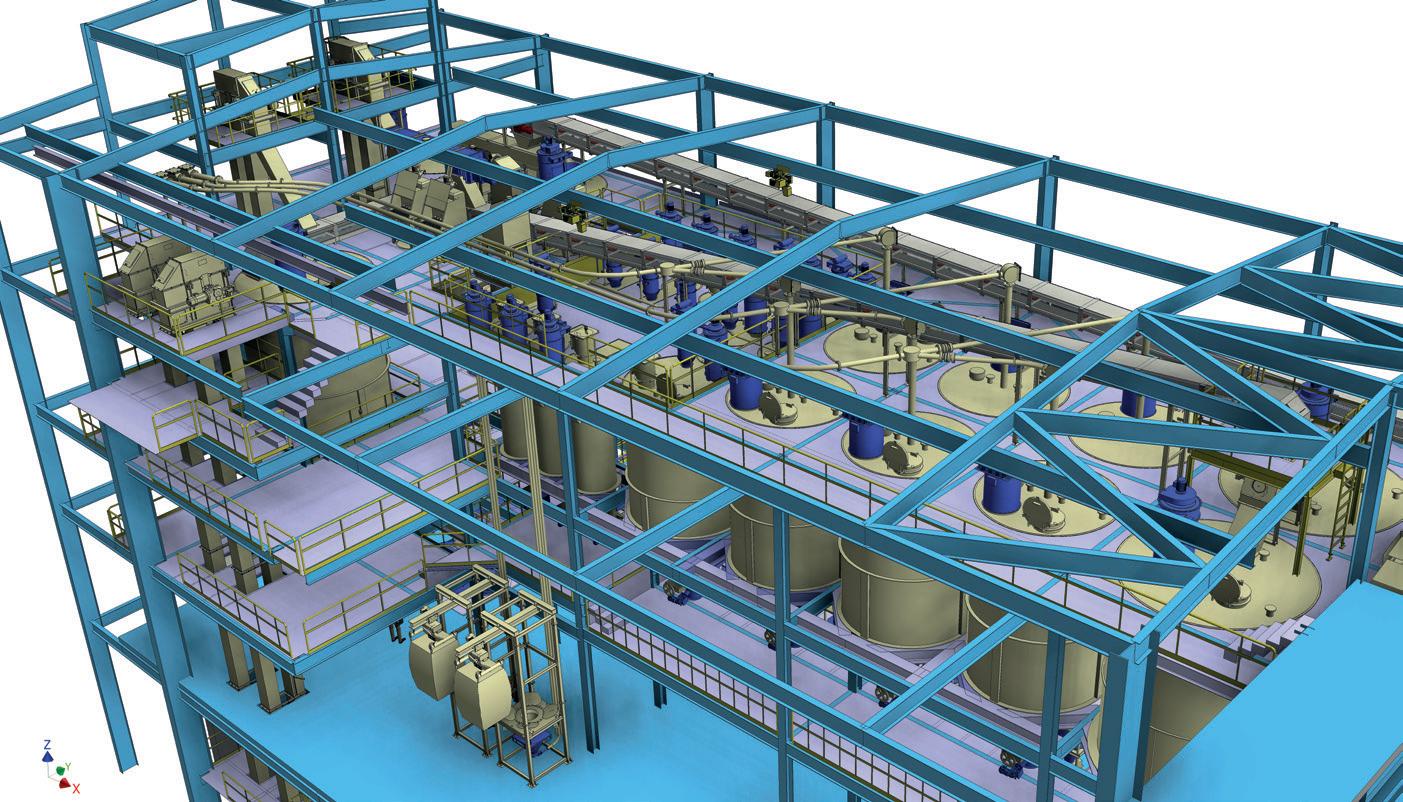
range of silos for storage of various amounts of material have been allowed for.
In addition, different state-of-theart weighing technologies are to be implemented to ensure the ability to create any recipe the experts at Glass Futures dream of.
In parallel to the creation of the process flow diagram, EME’s engineering team developed the layout concept for the equipment.
At Glass Futures it had the challenge of designing the solution into a limited fixed space within a predefined building.
In addition, the solution needed to be designed in such a way that it could be installed into the building once it was already completed.
EME overcame this challenge by applying its experience in innovative planning and modular design. Thus, the design allows for specific technology to be installed at the start of the project with future expansions already being accounted for.
Flexibility being a key driver of the plant design resulted in the implementation of some complex solutions.
The ability to run cullet through the mixer, or bypass it and add the batch after mixing, presented difficulties due to space and height limitations.
This was, however overcome with customised vibratory feeding equipment with diverting capabilities.
While it is always exciting for our engineers to develop complex solutions, they are also acutely aware of the importance of simplicity in design. As such they applied their many years of experience to design the most ergonomic and practical solutions.
Typically, a focus on personal safety and ease of maintenance are important drivers in the design process.
The use of 3D technology is essential to the process of design, not to mention critical to effectively communicate our solutions to the customer.
For the Glass Futures project, EME developed a 3D model for the equipment and relevant maintenance access platforms and then integrated it into the building design model provided by Glass Futures’ structural engineering partner.
Through a process of detailed reviews, the models were checked and updated, not only resolving collisions and potential problems, but also bringing in special specific requests. The result is a truly remarkable solution!
Aston Fuller, General Manager of Glass Futures said: “Specifying projects aiming to carry out research and development in an industry that typically runs 24/7 for decades in a row is a unique challenge.
“I have seen both EME and a large number of other organisations in the glass supply chain rise to the challenge and begin thinking in an innovative way, which is vital to allow the glass industry to build a facility designed to carry out the ground-breaking research that the glass industry needs.
“We look forward to welcoming our members, EME and their Customers to see this plant in action when it opens in late 2022.”
With the process fully defined and the physical design of the plant complete, EME moved on to developing a detailed technical specification for the solution.
The specification considers the need for flexibility, process monitoring and ease of maintenance.
As such, all equipment has been specified taking these factors into account, issues like inspection and sampling openings, level and material presence sensors and advanced handling technology were all considered in detail.
Being a plant designed for the future of glass, it was critical that modern technologies were selected for the process.
The control system will be designed with the most modern philosophy on plant wide automation systems allowing for one of the most modern facilities in the world.
In addition to this, EME has included state-of-the-art custom solutions as part of the specification, such as the implementation of QR and RFID systems that provide automated stock management and integration into ERP systems.
Plant overview and operation from remote devices is a given, a simple and precise recipe for scale management from the palm of your hand goes without saying, as well as a built-in runtime-based maintenance management system.
Pic 2. A birds eye view of the 3D equipment � model integrated into the building design.
� Pic 3. Floor level 3D equipment model included into the building design.
Included in the specification are the design considerations for the plant to ensure that the delivered solution will meet the desired outcomes.
This includes the process flow diagram, site plans, detailed building layouts, 3D model and more.
EME has included details on local regulations relating to construction and health and safety, thus ensuring that this critical aspect will not be overlooked.
In addition, the utility requirements and interface are well defined to ensure problem free integration into the rest of the facility. The installation requirements clearly defined, with details relating to critical items such are laydown areas, contractor access and lift plans being provided.
EME included with the specification, technical documentation and drawings, a preliminary project schedule and budget, providing a Complete Engineering Solution.
The Complete Engineering Solution was reviewed multiple times with Glass Futures to ensure that it embodied the vision that it has for its batch plant and necessary processes. Exceeding Glass Futures expectations, EME is looking forward to seeing the project move into the next phase.
Mr Liggett added: “It has been a pleasure working with the EME team over the last few months to get to a solution for our detailed batch plant design at the Global Centre of Excellence.
“The comprehensive technical specification package will form the basis for our next procurement phases for the supply, installation, commissioning, training and handover of highly specialised equipment at our site in St Helens, Merseyside.” �
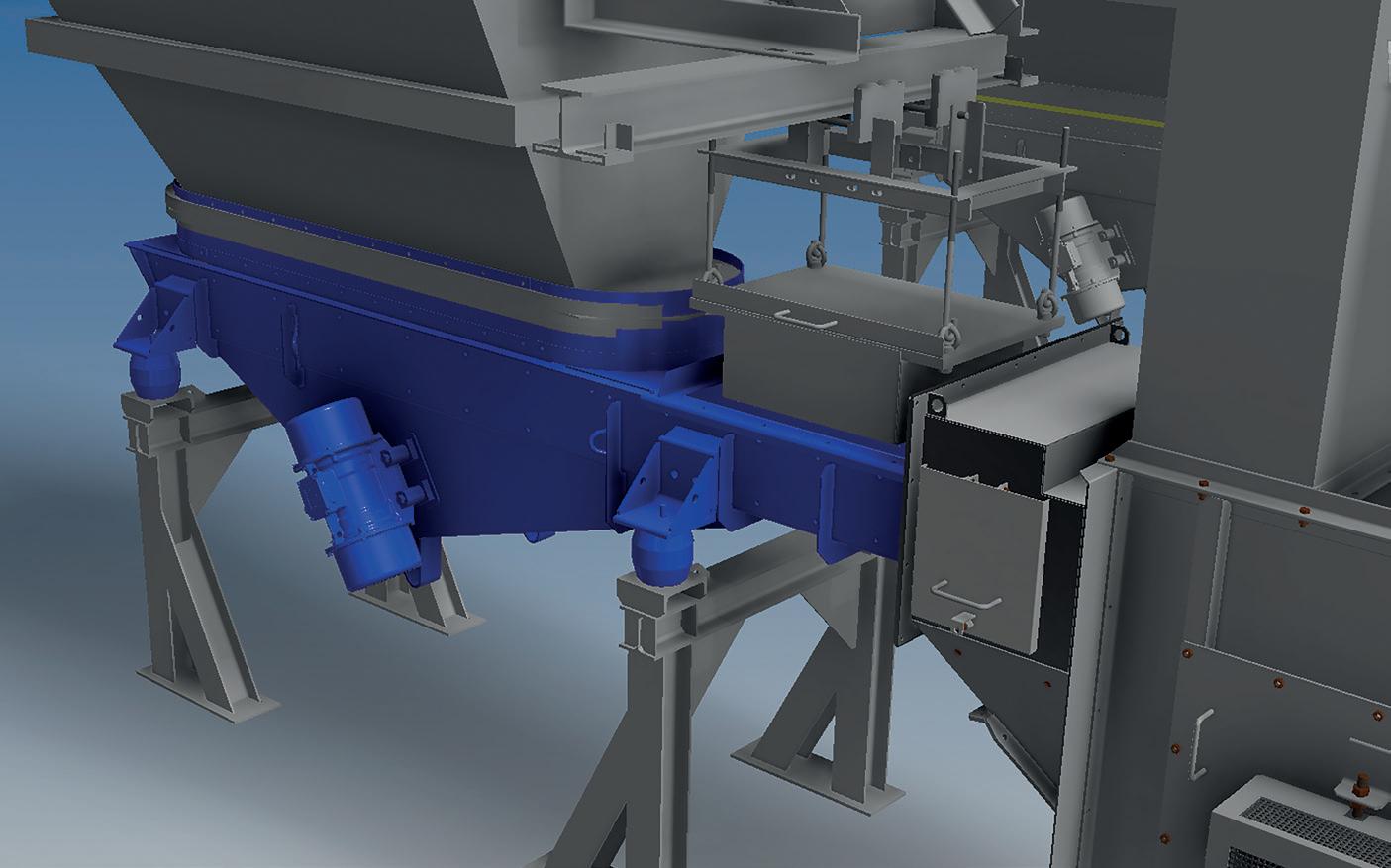
� Pic 4. Example of Installation Detail for a Vibratory Feeder.
EME GmbH, Erkelenz, Germany www.eme.de