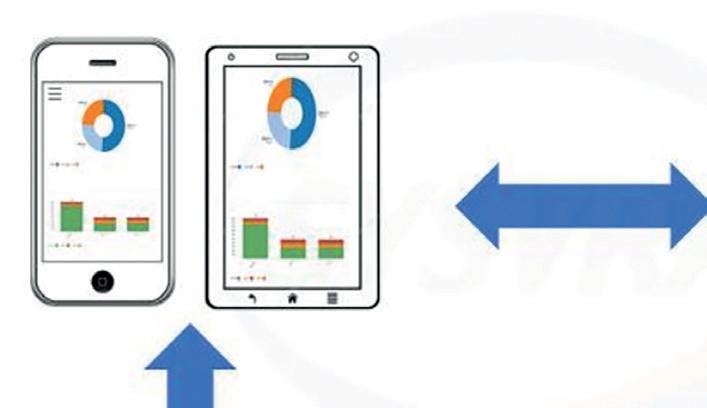
8 minute read
Inspection SYSVRA
The future of inspection
Spanish inspection systems supplier SYSVRA discuss how Industry 4.0 can bring about a new level of machine.
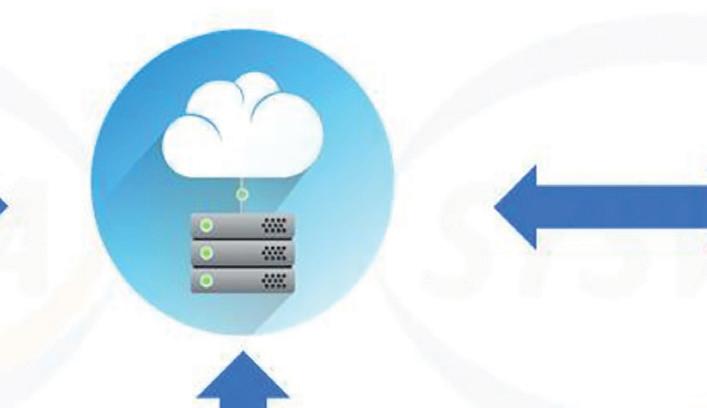
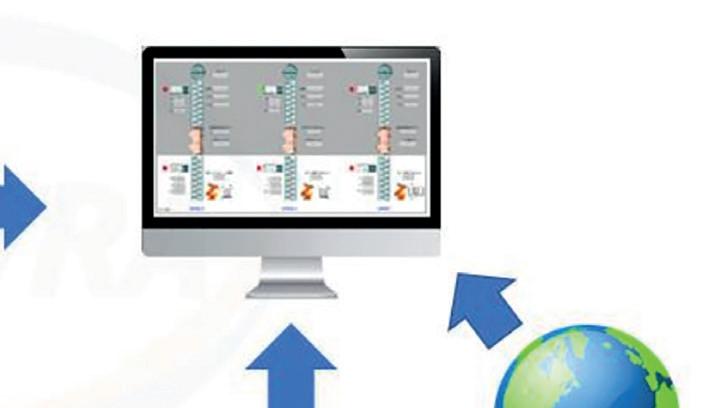
� SYSVRA say its Industry 4.0-ready machines can improve performance and control of a customer’s production process.
Madrid, Spain-based SYSVRA is a technological and innovative company in the glass manufacturing industry that has taken the inspection of glass bottles to another level with its artifi cial vision systems.
The glass industry has grown signifi cantly due to the Covid-19, so container glass and vials manufacturers need technology to supply this high demand.
Due to this demand, SYSVRA has invested all its resources in improving its inspection systems for glass containers and vials manufacturing and integrating the Industry 4.0 concept into all manufacturing processes, from the forming machine to the packaging.
Thanks to the innovation of its systems, more and more customers are opting for SYSVRA, which is why in just one year this Spanish company has systems in production on three continents and has experienced exponential growth.
Industry 4.0
SYSVRA is committed to progress in industry and technology hence why it is linked to the concept of Industry 4.0, offering its customers a solution to improve the performance and control of their production processes.
In addition, SYSVRA supports this technology of centralisation and globalisation of data, even more so in this health crisis, since it is very important that all these production processes continue to help as much as possible to overcome this pandemic.
The products mentioned below have the option of being able to communicate with each other through a central PC.
SYSVRA can communicate any of its equipment with each other whether they are in the same production line or not, thus allowing the following features:
� Acquisition of production data at plant level and uploading them to the cloud. Centralisation of factory data in a single control station. � Shift and work order management. � Creation of production and consumption reports, helping to know the profi tability of � your production process. � Knowledge of the state of the production lines to perform preventive maintenance. � Real-time data visualisation and remote access from anywhere in the world.
The main goals for all of SYSVRA’s inspection systems are to:
Improve manufacturing productivity Thanks to its HOT END GFC system, this company ensures that the forming machine has less than 0.99% of rejection in the glass tube and manufacturers minimise the return of its customers due to defects in the printed silkscreen.
And with its COLD END GSC system, manufacturers will be able to control with guarantees the screen printing, rings and OPCs printed on their bottles.
Easy to set up All systems developed by SYSVRA are focused on and easy confi guration by the user, so that they can be confi gured in a matter of minutes by any operator.
This feature is increasingly in demand as it allows there is no stoppage in production due to the confi guration of these systems.
All SYSVRA systems have production recipes so that the confi guration of a specifi c ampoule format can be saved/ load in a matter of seconds.
Remote setup and support In times of Covid-19, the diffi culty of traveling between countries has been so diffi cult that it slowed down the implementation of this type of systems in any industry.
SYSVRA has made a concerted effort to solve this problem, making it possible to install all its systems remotely thanks to a technical infrastructure that allows connectivity with SYSVRA technicians, achieving a fast installation and a quality after-sales service, a very important part of the company’s philosophy.

The HOT END GFC system is installed on the forming machine.�
� SYSVRA’s GDI system is installed on the forming machine and inspects defects in the glass tube.
� The GDI system can also be installed as an additional functionality on the HOT END GFC itself.
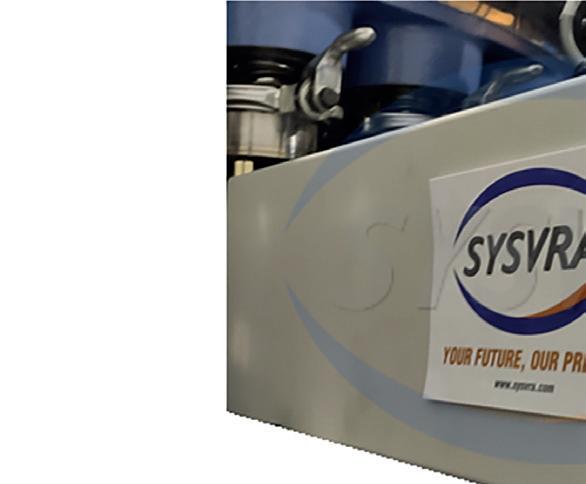

Complete range of inspection systems for glass ampoule manufacture The complete range of SYSVRA inspection systems are increasingly being equipped in new and existing production lines for the manufacture of glass containers.
SYSVRA’s HOT END GFC system is installed on the forming machine and it measures the dimensions of the bottle and at the same time it regulates the oxygen supply to the correction burners.
The glass tube from which the containers are made may vary in diameter along its entire length, or the heat input in the preheating zone may be insuffi cient causing additional rejections.
To compensate for these variations, the HOT END GFC system automatically manages oxygen injection into the correction burners in a precise manner.
The HOT END GFC system has a camera, which measures each part of the ampoule in each chuck (mouth, stem, bulb, neck, body and eccentricity) and depending on the measurement, the system automatically adjusts the oxygen level of the correction burners to get the corresponding measurement as close as possible to its nominal value, achieving a raw material rejection of less than 0.99%.
With this concept of regulation by oxygen supply and not in the position of the fl ame by means of pneumatic cylinders, a longer service life is achieved as there is no stress on the mechanical parts and a much more precise regulation in the manufacture of the ampoule.
Thanks to the graphical interface, operators can detect at a glance the chuck with production problems, allowing them to operate the machine quickly and accurately.
The system also has production histories by work shifts and by measurement, allowing to control the production performance and to know possible stops and anomalies during the shift.
The GDI system is installed on the forming machine and inspects defects in the glass tube, which may be damaged or defective from the factory.
It is equipped with a high-resolution camera and a backlight designed by SYSVRA engineers specifi cally for the inspection of glass defects.
The system inspects defects such as knots, air lines or scratches in the tube and rejects the defective glass bottles automatically.
Thanks to the versatility of SYSVRA systems, it can be installed as an additional functionality on the HOT END GFC itself, having two systems in one or as a separate system having the forming machine fully equipped.
SYSVRA customers have already reduced batch rejections by end customers due to cosmetic defects to 0%.
The OPC system developed by SYSVRA is differentiating due to its backlight and camera layout, specifi cally designed for OPC inspection (point and pre-cut) on glass containers.
It is integrated in the line before the oven where the ampoule is lifted from the chain positioning the neck to perform the pre-cutting.
This ensures that (as long as the neck is within a tolerance of +/-0.5mm) the cut is always the same and the printing of the dot is performed in the same step, thus guaranteeing the alignment between the two.
A camera and backlight are installed after the OPC is performed.
Their main objective is to control that the state of the point and cut of the ampoule is optimal for its correct rupture.
The measurement of point and the pre-cut, stains and breaks as well as the alignment between both are inspected.
And fi nally the COLD END GSC system. This system is installed in the packaging after the oven and inspects the printing, rings and OPC of the manufactured bottles.
Through an easy-to-set mechanical design, an optimal print image of the ampoule is achieved for validation.
Thanks to customer feedback, SYSVRA has ensured that this system can be set up in a matter of minutes when there is

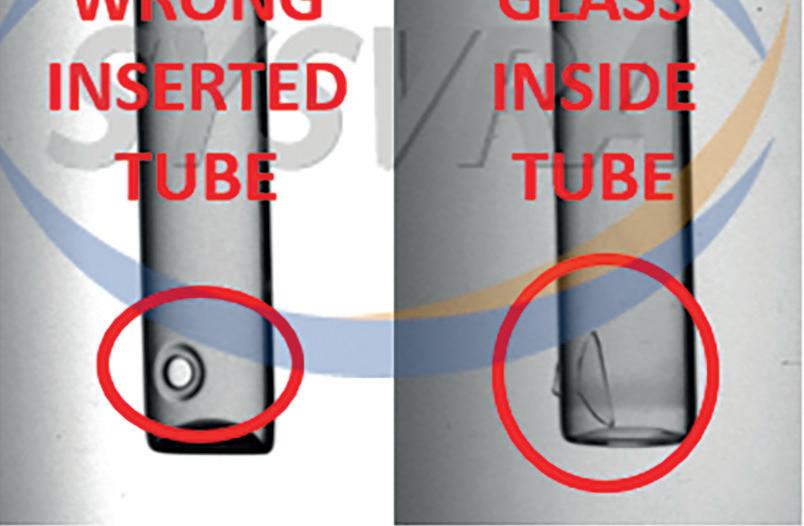
� The OPC system is designed to inspect both the point and pre-cut of glass containers. � The COLD END GSC inspects the printing, rings and OPC of the manufactured containers.
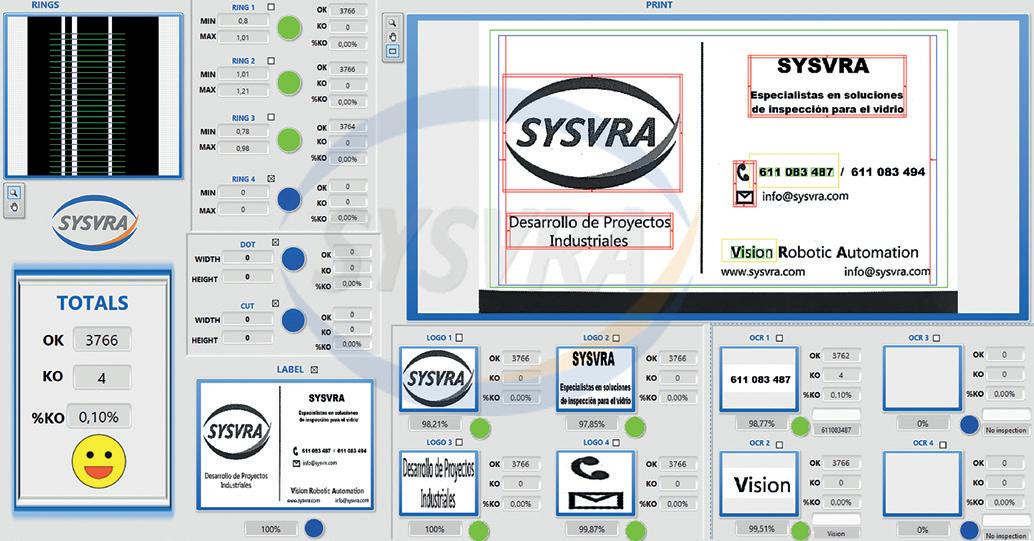
a format change in production (e.g. from 5ml to 10ml).
Each print is compared with a master print. In addition, the system includes OCR (Optical Character Recognition) inspection for thorough validation of batches, expiration dates, etc.
This OCR feature has been a breakthrough in the COLD END GSC system being one of the fi rst companies to bring this functionality to the industry.
Due to the speed of container glass production (100 per minute) and the diffi culty of performing OCR technique in this type of printing, SYSVRA developed a proprietary algorithm to make this functionality a reality in this system.
Conclusion
It is important to note that end customers increasingly rely on companies specialised in quality control systems for the acquisition of these systems, since they provide specifi c remote support for any anomaly.
SYSVRA has technicians who, in addition to possessing expertise in machine vision control tools, have extensive experience in manufacturing processes in the glass industry.
These characteristics and the ease of adapting its systems to the customer’s needs mean that SYSVRA, a dynamic company that began its journey more than four years ago, has great expectations in the glass industry. �
https://www.sysvra.com/en/ Madrid, Spain
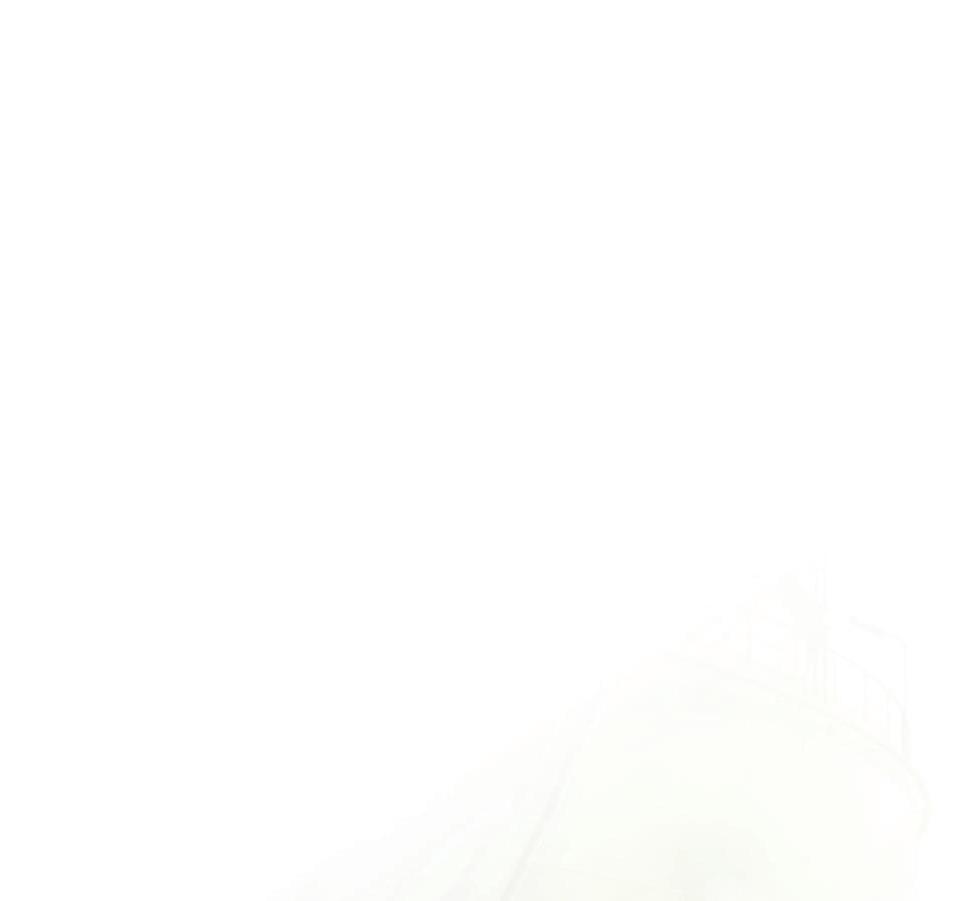

LEADING A CLEANER INDUSTRIAL FUTURE





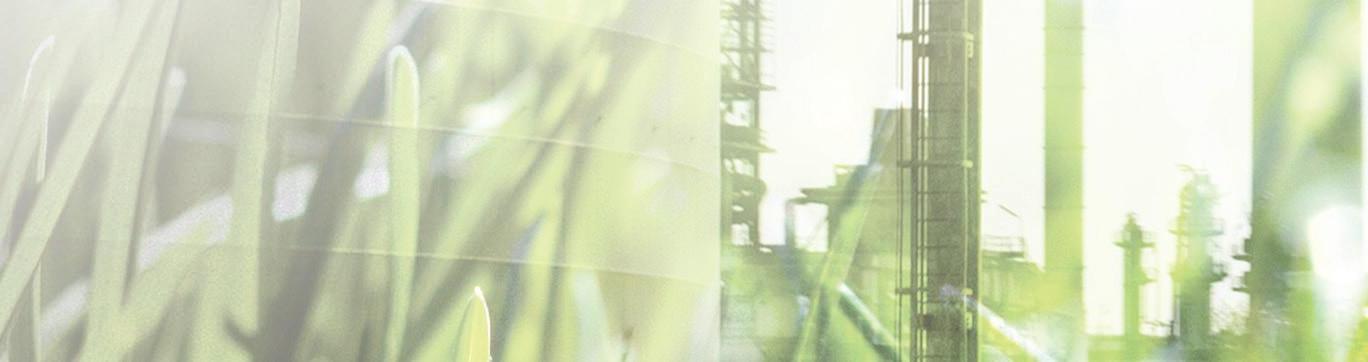

9-10 MARCH 2022, BRUSSELS, BELGIUM
GLASS ALUMINIUM STEEL
CEMENT CHEMICALS
Brought to you by a coalition of industry experts, Sustainable Industrial Manufacturing (SIM) is a global series of regional exhibitions and conferences supporting and facilitating the transition towards cleaner manufacturing around the world.
Stand bookings are now open
Register your interest at: SustainableIndustrialManufacturing.com DOWNLOAD THE
EVENT BROCHURE
Nadine Bloxsome | Event Director nadinebloxsome@quartzltd.com +44 (0)1737 855115
ORGANISED BY: FROM THE PRODUCERS OF: