
6 minute read
Batch plant: Siemens and Zippe
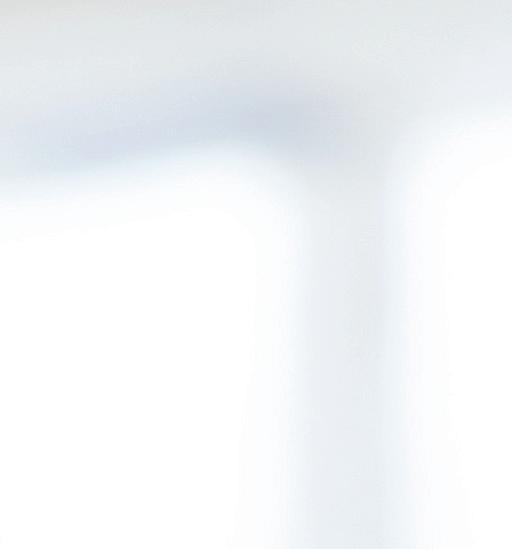


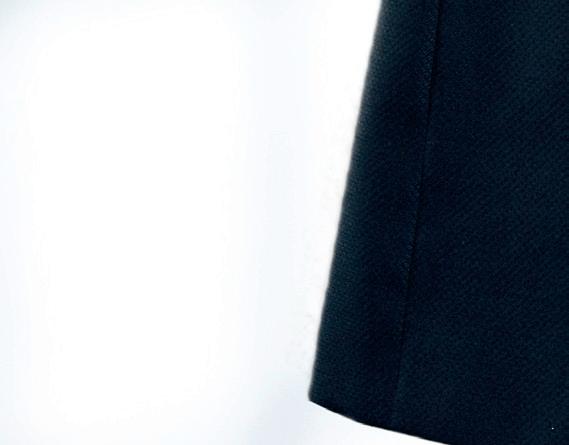
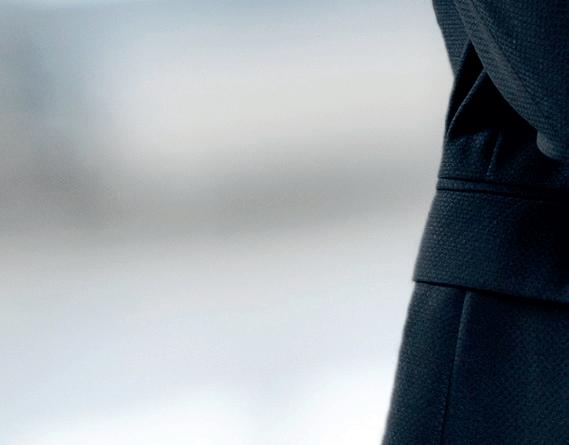
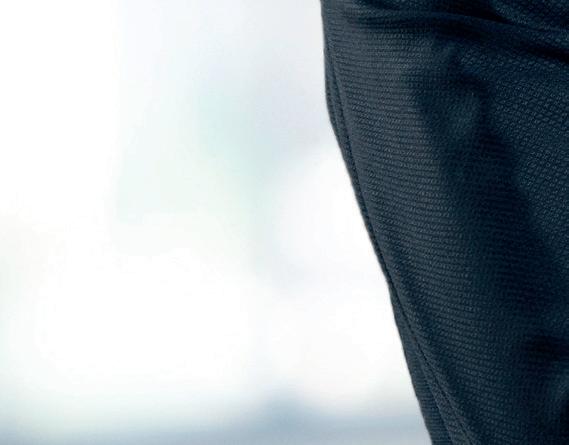
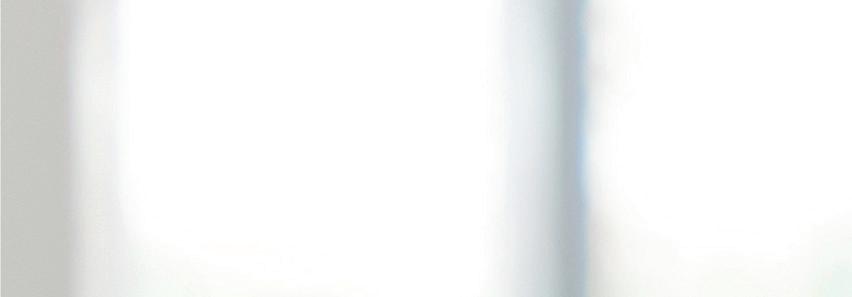

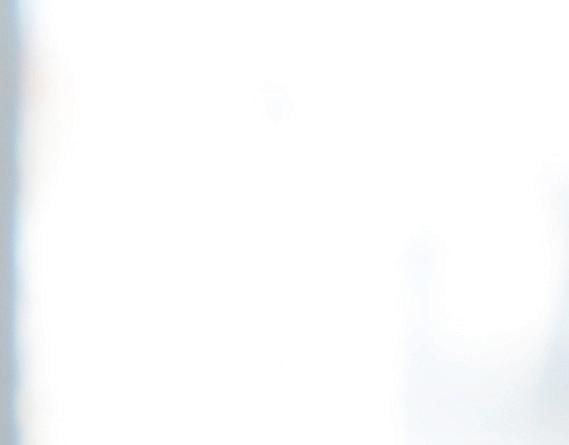

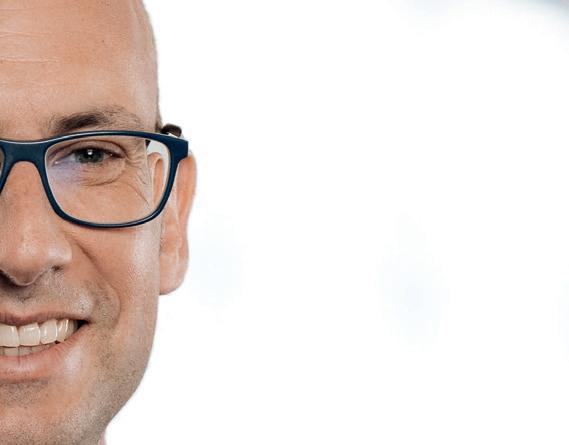
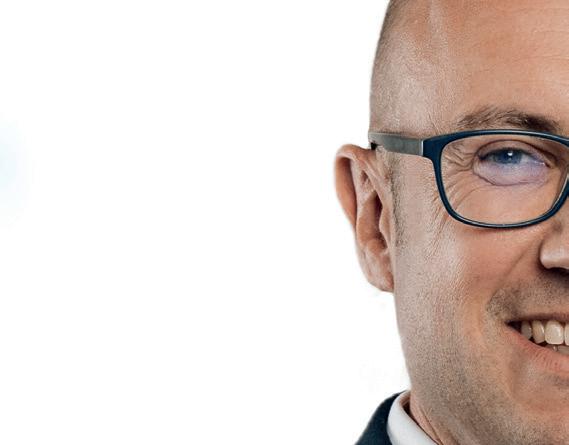
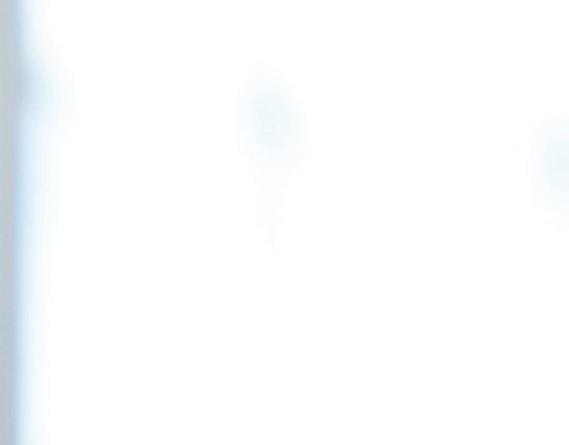
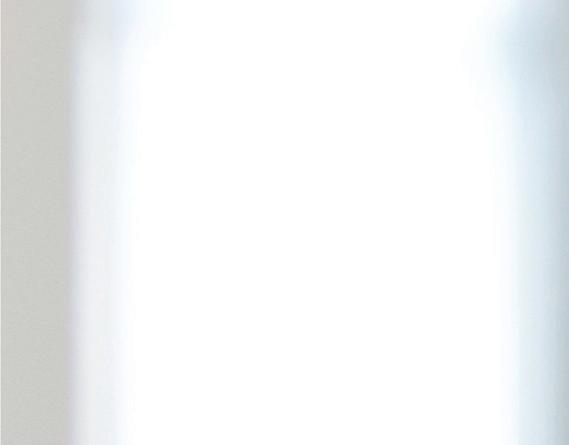

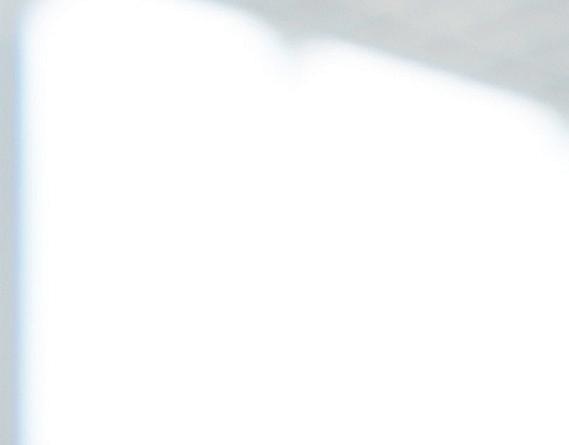
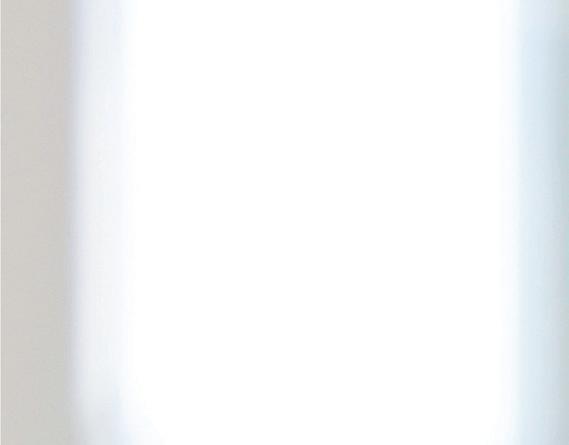
A partnership for unsettled times
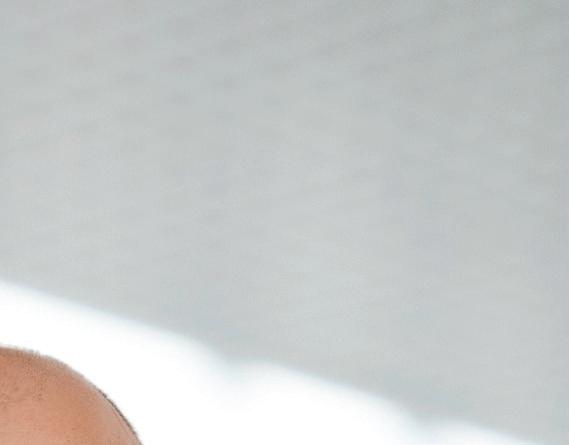
Joachim Ullrich*, Director of Electrical and Process Automation, provides an insight into how the partnership between Zippe and Siemens can help manufacturers during unsettled times.
Zippe had reason to celebrate in 2020, when it marked its 100th anniversary. Tell us about some of the milestones you’re most proud of.
Ullrich: There are quite a few. We’re proud of having put the fi rst fully automatic container glass plant into operation in 1960. The fi rst fl oat glass plant followed in 1984. The more than 1,300 batch feeders we have supplied are also important. In the fi eld of cullet systems, we’re known for our scraper conveyors, which some of our customers also refer to as ‘le Zippe’. That makes us proud. We were also one of the fi rst companies to construct plants for heat recovery (batch and cullet pre-heating). In addition to our technical achievements, we’re pleased to be an independent company that’s still family-owned. But we’re particularly happy about the fact we’re a reliable and professional contact for our customers.
Have there been any highlights in the more recent past? As we know, the times have been challenging.
Ullrich: That’s right. Even during the pandemic, we were able to continue with our customer projects and bring them to a successful conclusion. That was important to us. A particular challenge involved continuing our assembly and commissioning activities in distant locations in other countries, mainly
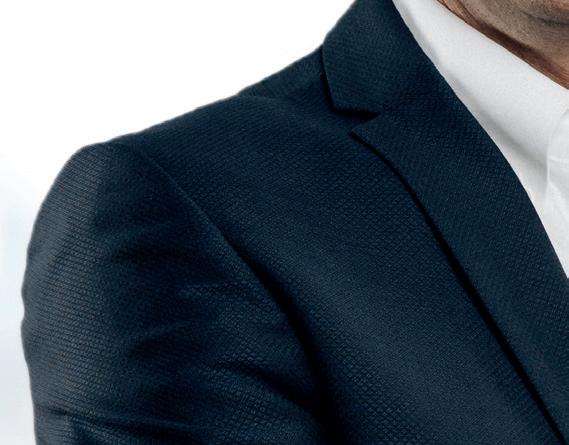
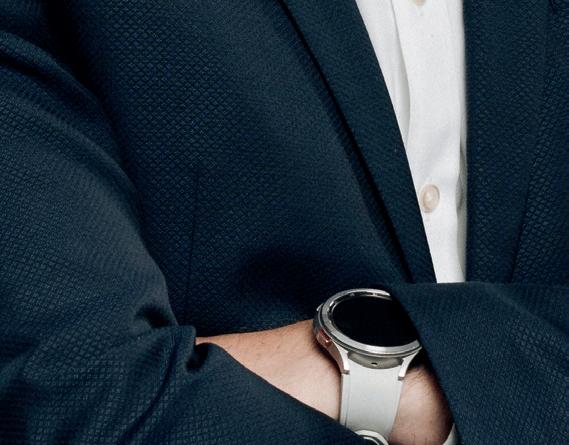
Joachim Ullrich, Director of
� Electrical and Process Automation at Zippe Industrieanlagen.

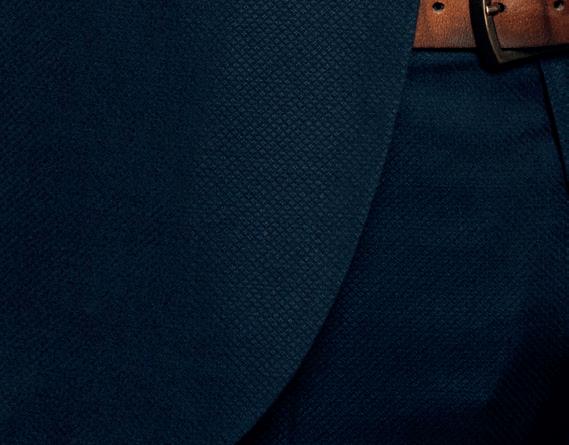
by remote. We considered ourselves fortunate to also have local fl agship projects in Germany which it was easier to travel to. Good examples are the projects for Wiegand-Glas in Schleusingen and for Noelle + von Campe in Boffzen, whose systems are now all in operation. fl agship projects?
Ullrich: Wiegand-Glas is a prominent customer with a particularly large and extensive plant in Germany. It has two independent weighing lines, a silo feed, a very extensive cullet return system with multiple scraper conveyors and a batch/ cullet transporting system with 12 Zippe
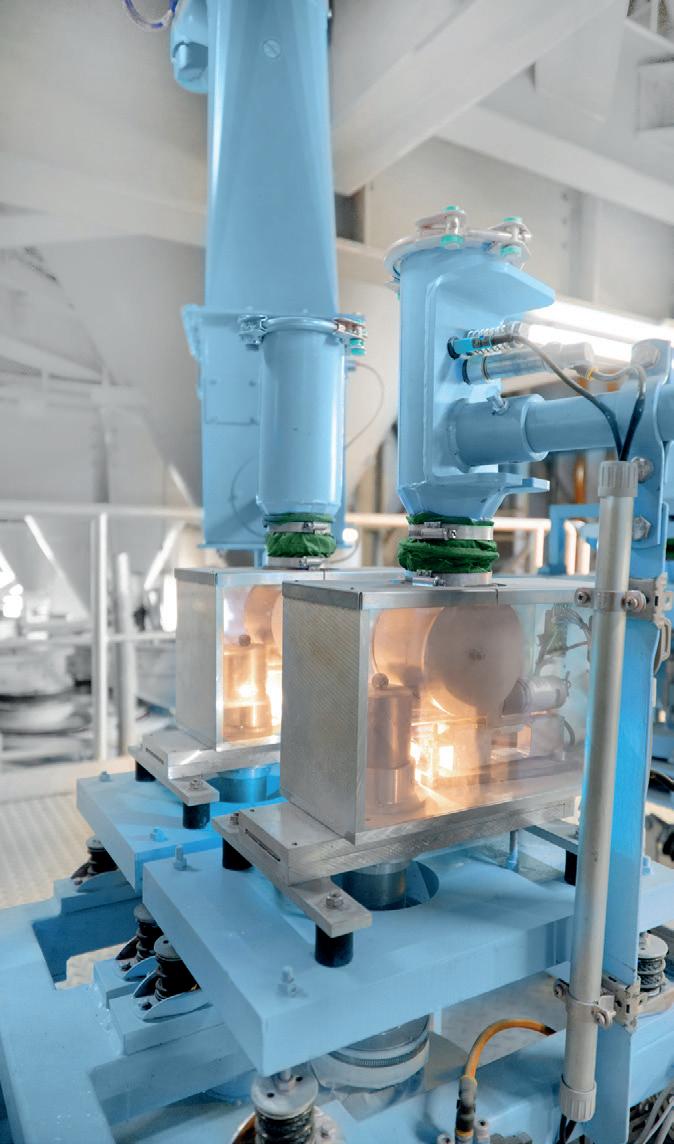
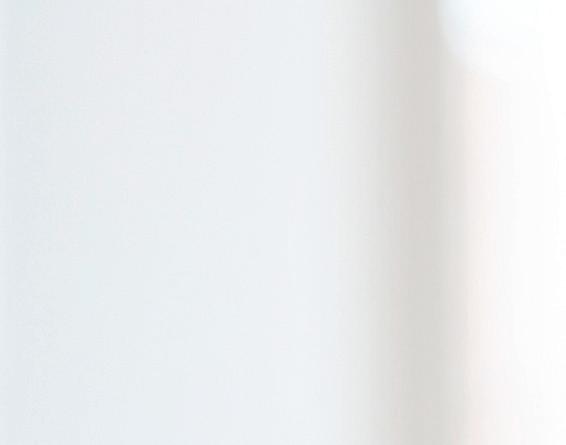
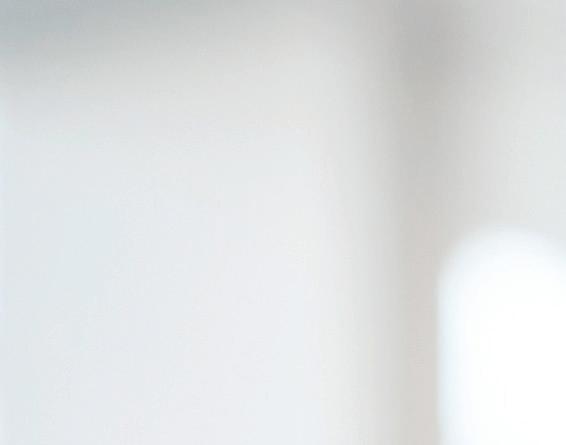
belt scales, which were equipped with Siemens weighing technology. Working closely with Siemens, we fi nally put in place a very comprehensive and consistent automation and control concept.
At Noelle + van Campe, in turn, the new weighing line was put into operation, including the premix unit, cullet weighing, batch and cullet transport to the bath, and also the cullet return system, using the standard method with the Simatic PCS 7 process control system. For the safety system, S7 1500-series safety controllers were put in place for the individual areas. The OS control panels were virtualised by Siemens using SIVaaS (Simatic Virtualisation as a Service) so they didn’t have to depend on specifi c hardware.

What do you believe is the common thread running through all these projects?
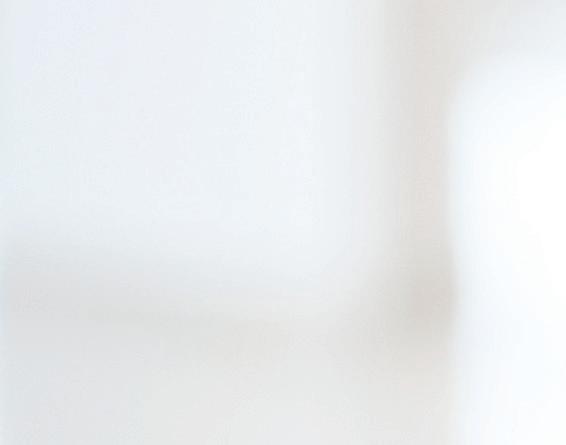
Ullrich: As a Siemens Solution Partner we are pleased that our customers have taken on board the philosophy of plantwide, end-to-end automation and are going down the path of innovation with us. One common thread is that Zippe has represented continuity, reliability, and innovation through many generations. That creates trust. A lot of people also appreciate the extent of our vertical integration and our great fl exibility.

What do you like about Siemens?


Ullrich: For us, Siemens is an important, reliable, and professional supplier and solution provider, which we’ve been working with successfully and on a partnership basis for many years. The top-quality consulting it provides enables us to make versatile technological solutions available. As a Siemens Solution Partner, we aim to build up a wealth of expertise among our employees. Sophisticated customer projects are the best way to do that. Siemens also supports us with workshops and recertifi cation seminars. When we start using new technical solutions, sales employees and experienced technicians are there to help. And in the current global situation we can also count on Siemens.
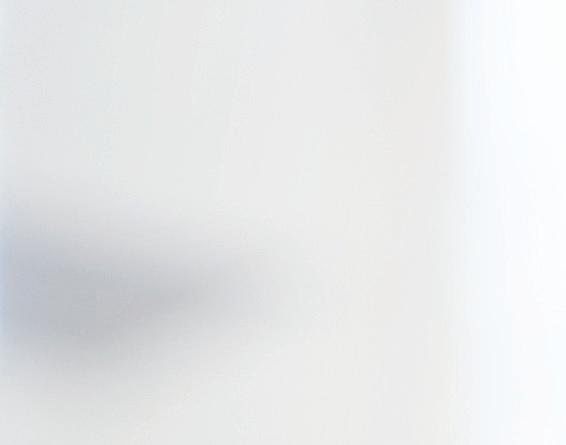
What are the customer requirements that it’s particularly important to satisfy at the moment? have a role to play, now more than ever. Some security principles need to be implemented even more rigorously. From the perspective of controller technology, that means network architecture and the selection of control systems and components enjoy higher priority as a way of being armed against potential cyber attacks.
In addition, there are energy and sustainability aspects which enable us to concentrate on resource-saving and energy-effi cient solutions. These include preheating technology and batch feeding systems for electrically heated baths.
We are constantly improving the electricity and energy consumption of our products. In the future, we will be adapting to all kinds of furnace heating technology to be best prepared for the future. That relates to our batch feeder technology for various furnaces and melters, in particular. Then there are the opportunities for digitalisation. We interpret digitalisation as meaning the implementation of plant-wide automation with a uniform operation and control concept. The result is a cross-departmental “look and feel,” and it also makes the process control system more user-friendly. We were also able to implement mobile control concepts for projects here and there. Optimising the control system for our batch and cullet preheaters makes these increasingly energy-effi cient.
� Precise dosing and weighing solutions.
Where does Zippe get this ability to adapt from?
Ullrich: That comes from our 100% focus on batch and cullet plants – which we’ve done for decades now. The experience built up by our long-term employees gives us a solid foundation for developing innovations in these areas. Right at the offer stage, we talk with the customers about the solution that’s ideal for them, based on highly reliable and advanced technology. Our customers appreciate the fact that Zippe, as a supplier in the batch and cullet plant sector, can develop the entire process chain in-house – from consulting and engineering to software development, electrical and mechanical production, commissioning, maintenance, and service �
*Zippe, Wertheim, Germany www.zippe.de Siemens, Karlsruhe, Germany www.siemens.com/glass
� Zippe’s batch plant with external raw material feeds.