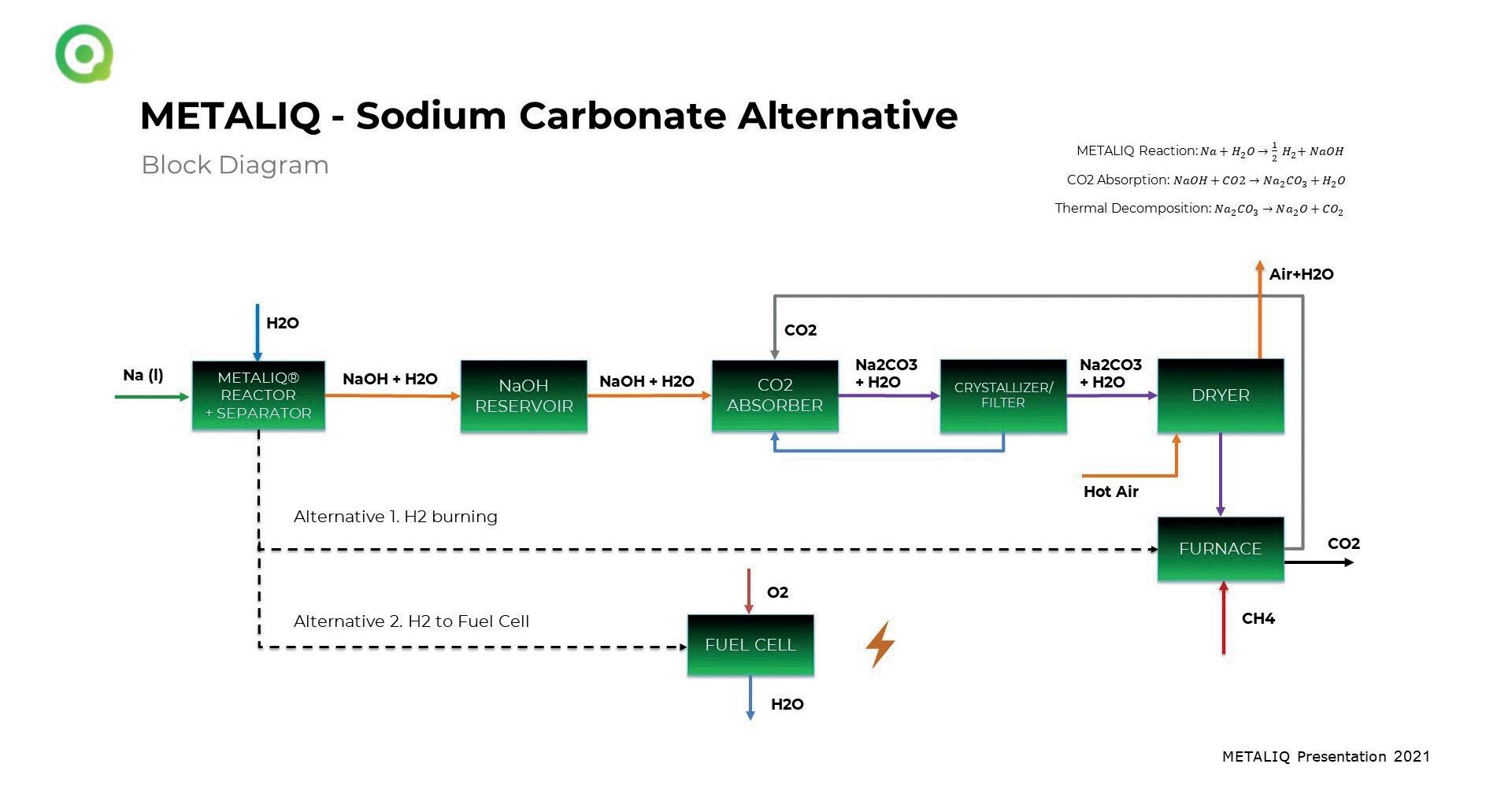
7 minute read
Decarbonisation: IGR
A green way to produce glass
A co-operation between German companies Metaliq and the IGR could help solve a problem of the global glass industry, by using a novel way to produce soda and hydrogen production directly in the glass factory. Hans-Ullrich Werner* and Dirk Diederich** discuss.
� Fig 1. Metaliq’s sodium carbonate route.
What is the biggest problem mankind is facing right now? If not the biggest still definitely one of the top three is the climate change!
What needs to be done in order to stop this or at least slow it down? Reduce the CO2 exhaust. Or even better, remove CO2 from the atmosphere.
We have the technology to do so and it‘s ready to be used now.
Why do we have that technology? Because we have hydrogen for free!
Sodium hydroxide removes CO2 in a natural reaction from glass industry exhausts, if you want. The resulting sodium carbonate is urgently used in Glass industry.
Why do we have this for free instead of having to spend lots of money to create it? Hydrogen is the waste product of a technology, we invented, to produce NaOH on site, to use it for burning together with natural gas or in fuel cells and you don’t have to transport hydrogen anymore, if you’re using our technology.
How do we produce Sodium Carbonate on site? That’s thanks to our patented and already working Metaliq Hydroxide Generator, which uses Sodium, water and later, CO2 too.
Where does Sodium come from? As Sodium (Na) can be found in almost endless amounts in saltwater from the sea, sea water desalination in the future can be the solution for the urgent need for drinking water.
And the waste, the salt, will be split with electrical energy from the sun into sodium and chlorine, which then would be used for PVC Tubes for transporting drinking water and which is needed in big amounts in chemical industry. What is Metaliq? Metaliq is an international patented technology (Escudero, 2014) for the in-situ and on-demand production of green hydrogen for power generation in conjunction with fuel cells or as a substitute for hydrocarbons with complete elimination of the carbon cycle. It is based on the chemical water splitting reaction (CWSR) with alkali/alkaline earth metals (such as Na, Li, Mg, K, etc.) and water.
For industrial applications in glass works, only sodium is used as a raw material. Metaliq (Metaliq, 2021) has applied for further patents on this, focusing on on-demand and in-situ sodium hydroxide production (Fig 1).
How will it be realised? For expansions or adaptations, all plant components are modular, scalable and thus have technical redundancy. This
� Fig 2. Overview of the full cycle.
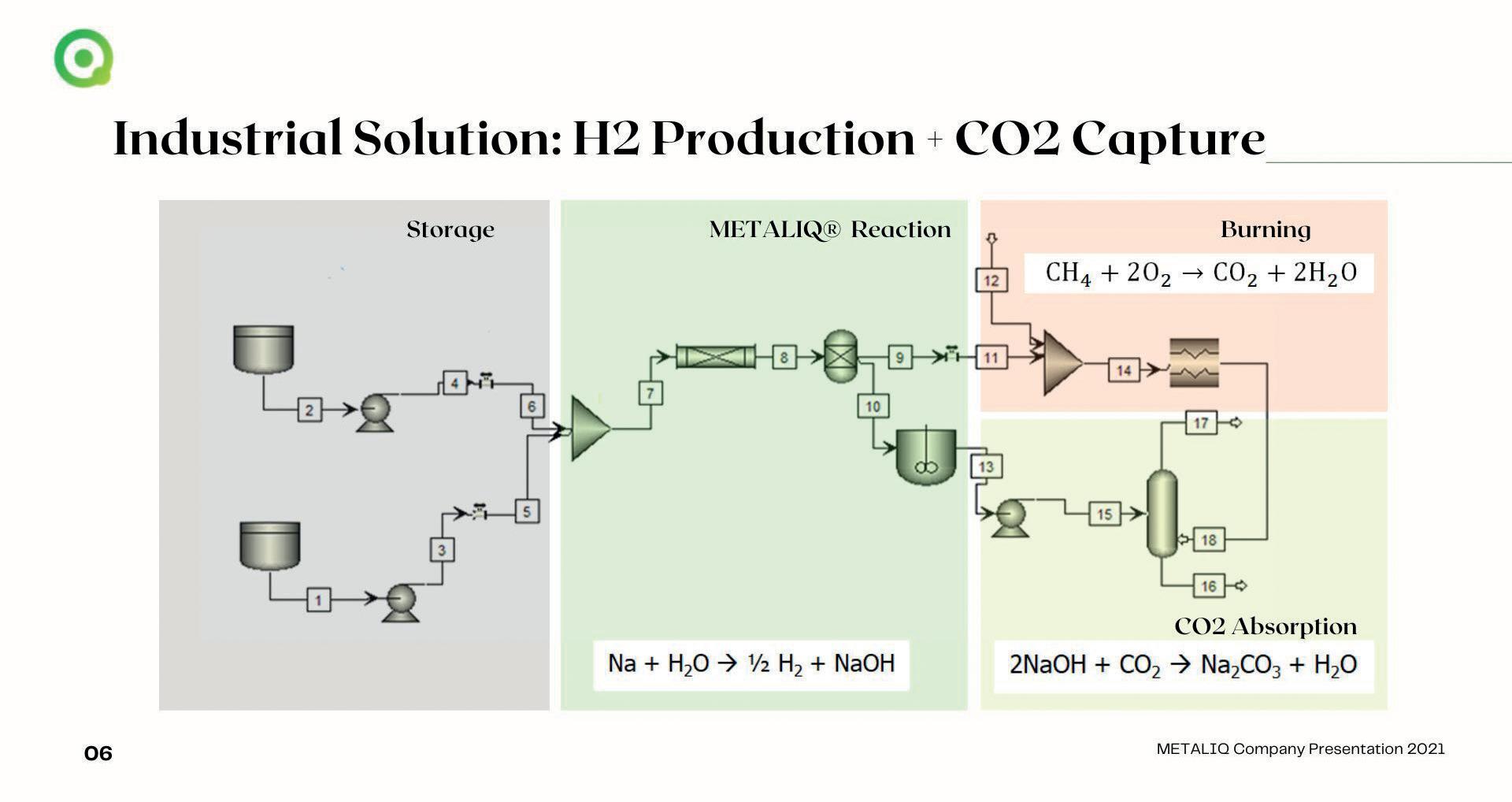
ensures continuous production.
Why using Sodium? Applications are well known in nuclear power plants for countless years already. Sodium is the energy carrier from which sodium hydroxide and, as a by-product, hydrogen, is produced without any further energy input.
Unlike gaseous fuels, solid sodium can now be stored indefinitely as a metal and procured at advantageous market prices.
What about Sodium Hydroxide? Sodium hydroxide is used to capture CO2 in order to produce sodium carbonate (soda ash) in situ. The special feature of this is that the crystal sizes of the salt can be designed for the subsequent batch.
How does it work? Hydrogen as a by-product is produced at atmospheric pressure, mild temperatures and without any significant energy requirement and is used to heat the glass tanks by mixing it with the fuel natural gas (Fig 2).
Which costs will be less than before? Because of the low cost of sodium, the cost of soda ash produced In-Situ is also low. The necessary CO2 is waste from the chimney and free of charge. Due to the reduced consumption of natural gas and the quasi-free hydrogen CO2 emissions are saved, as are the procurement costs for natural gas. technology have? In the next few years, the technology will allow the direct use of sodium hydroxide in batch production, more, soda ash will then no longer be needed. This will eliminate CO2 emissions altogether. Hybrid plants (heating with natural gas and electricity) can be realised. Hydrogen, as a by-product, is produced at atmospheric pressure, mild temperatures and without any significant energy requirement and can be used for electricity generation in conjunction with fuel cells.
Do you have more chemical details? The reaction in equation 1 is carried out safely and smoothly thanks to an advanced algorithm for dosage control and an efficient heat removal system to avoid a temperature rise: Na(s)+H_2 O(l)�NaOH(l)+1/2 H2
The stoichiometric mass ratio is 23 kg sodium and 18 kg water to obtain 40 kg sodium hydroxide, releasing an energy of about 140 kJ/mol Na. The actual performance of the system is excellent, as the yield of the reaction is almost 98 %. In addition to sodium hydroxide (NaOH), 1 kg of hydrogen is produced.
Sodium Hydroxide is really the best CO 2 capturer? Yes, it is. But the market price is high if you have to buy it. But we are producing it ourselves within the glass plant. The reactive absorption of CO2 in NaOH has proven to be an efficient way to retain greenhouse gas emissions in flue gas streams. In fact, the CO2 capture capacity of NaOH is higher than that of conventional amine-based solvents, such as Mono-Ethanol-Amine (MEA), which is currently almost the only commercial process used in most post-combustion plants.
Do you have some more chemical details? This simple reaction is used to make soda ash, equation 2. The stoichiometric mass ratio is 40 kg of Na and 44 kg of carbon dioxide, which produces nearly 53 kg of soda ash and water: CO2 (g)+2NaOH(l)�Na2 CO3 (aq)+H2 O(l) The strong binding energy associated with this reaction offers the potential for high CO2 loads in a wide range of operating conditions and system designs.
What is in summary to say? Each ton saved Carbon Dioxide produce 1.2 t soda ash and ‘Green Glass’. �
More information *Metaliq, Görlitz, Germany https://www.metaliq.de/about/
**IGR Institut fuer Glas- und Rohstofftechnologie, Goettingen, Germany https://www.igrgmbh.de/homepage-en
Promoting healthy packaging
Jane Muncke* explores recent findings on the transmission of chemicals to food and beverages, as well as how glass packaging could a provide healthier and more sustainable alternative to plastics.

Do we truly know what’s in our packaging? With around 100,000 unknown chemicals in packaging materials, and only 12,285 known by scientists, there are some fundamental questions which need answering.
Innate materials like glass, reduce the risk of chemical migration, with only a few dozen chemicals present, and, with the work of manufacturers like Encirc, it also offers a sustainable, safer choice for consumers.
However, plastics, paper, and other materials often contain hundreds, if not thousands, of unknown chemicals that could have adverse side effects on both people and the planet. These form from impurities in those chemicals you start with, which react, creating up to 15 further un-intended chemicals which can further react.
What’s in our food matters, and a lot of scientific and regulatory effort goes into ensuring that it doesn’t contain anything that could be harmful to our health. However, the same level of thought sometimes isn’t given to the packaging that contains it. Perhaps this is because we’re so used to it being something that protects our food and so don’t consider it a source of contamination. This needs to change.
The cost of complexity
The Food Packaging Forum (FPF) is a charitable, not-for-profit foundation created to bring together and communicate knowledge on the effects that food packaging can have on the food inside it.
One of the driving forces behind the creation of the FPF is the determination to uncover the things we don’t know, and how any knowledge gap could be having a harmful effect both on the quality of our food and on our health.
The FPF informs stakeholders across the entire lifecycle of food products of the latest developments in scientific knowledge in the field – even if that means just letting them know how much more work there is still to do.
One of the primary goals of the FPF’s Food Contact Chemicals and Human Health Project1 is to track ‘chemical migration’ – the movement of chemicals from packaging materials into food. It’s a broad term and it needs to be considered across the entire supply chain.
We’re constantly demanding more from our food packaging, more durability, more functionality and more sustainability, and this means more complex manufacturing processes.
When we increase the amount and diversity of chemicals used in manufacturing, impurities in these