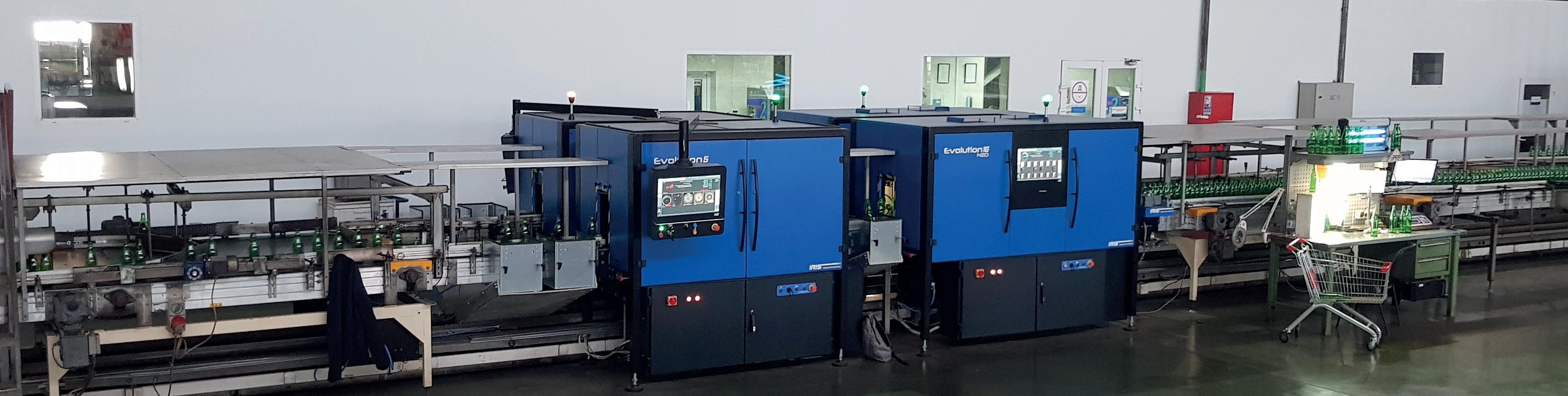
4 minute read
Inspection: Iris Inspection Machines From intelligent machine to collective intelligence
� Evolution NEO machines are able to identify the defect with precision, repeatability and at a high speed.
A new generation of Industry 4.0-focused inspection machines can learn automatically from production, which increases precision and repeatability, reports Jean-Luc Logel*.
Over the past 10 years, new technologies have revolutionised the glass industry. And even if today we no longer speak of Industry but of Industry 4.0 to recall this 4th industrial revolution, we are still far from having exhausted the range of possibilities.
While connected objects have already influenced and changed consumer dayto-day behaviour, they become essential in industrial processes, constituting one of the pillars of Industry 4.0.
By giving life to ‘intelligent factories’, where tools and operators are now interconnected, intelligent machines are shaping Industry 4.0 and providing solutions in terms of productivity, quality and safety.
Iris Inspection machines, one of the main players in glass inspection, is a pioneer in the field of intelligent glassware inspection. Based in Lyon, France, Iris dedicates a third of its workforce to Research and Innovation in the field of glass containers inspection. At the 2018 glasstec trade fair Iris launched the Evolution NEO range, the first generation of inspection machines equipped with artificial intelligence and machine learning.
Reliable data
Where a standard inspection machine relies heavily on the knowledge and skills of the operators pursuing to define what is and is not acceptable, the NEO machines learn automatically from production, increasing the precision and the repeatability. “Glass inspection is a real optical challenge: the defect types are various, container shapes are complex. Glass is a ‘living’ material which makes the inspection even more challenging.
“An operator, thanks to his professional experience, will be able to describe and detect a defect, to distinguish its shape, size, opacity. The full complexity of NEO development was to give machines this smart ability to recognise the defect. Now, Evolution NEO machine is not only able to identify the defect, and its characteristics as the operator would know, but also to do it with more precision, repeatability and at a high speed,” explains Mr. Philippe Volay CTO of the Group in charge of Optical R&D.
Evolution NEO machines are equipped with the latest technologies in terms of software (image processing) and CPU, which can reach a very high level of accuracy in the gathering of production data.
“This is a crucial step in a process based on artificial intelligence. To secure machine learning, it is first necessary to ensure the accuracy and veracity of the data,” comments Mr. Majd Rahmani Iris Technical Director.
Iris is thus developing a technology that breaks with the traditional inspection market, no longer relying on human know-how, but on the defect recognition and its classification.
This first step was the successful launch of the Evolution NEO range in 2018. The Evolution Neo range, brings together the Evolution 12 NEO sidewall inspection machine, the Evolution Neo 5 Neo base and finish inspection machine, as well as solutions for perfume and pharmacy inspection. The Neo machine has been quickly adopted by an increasing number of glass groups internationally including Verallia, Vetropack, Gerresheimer, Bormioli, Vidrala and SGD Pharma.
From individual to collective intelligence
If the concept of digital transformation leading to ‘smart factory’ remains
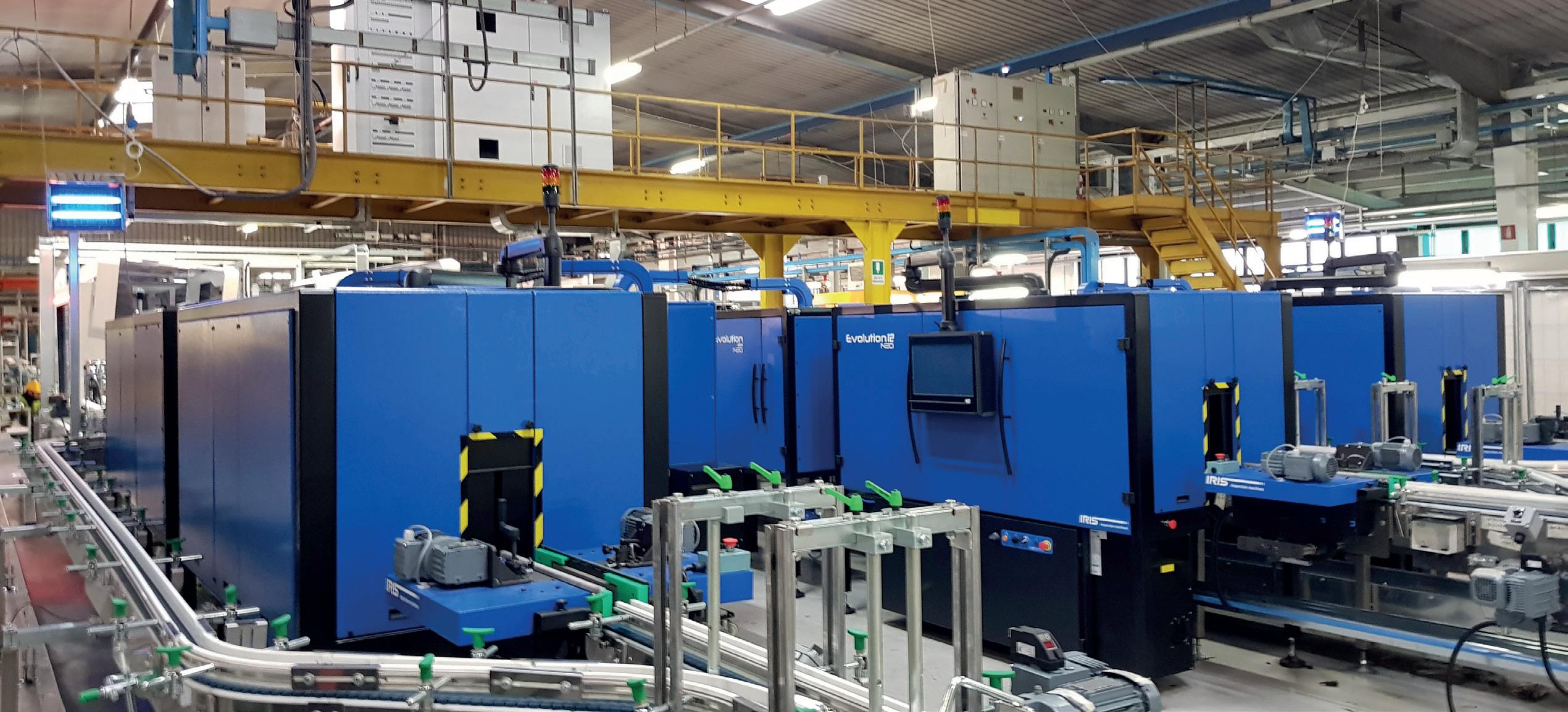
� The NEO machine has been quickly adopted by an increasing number of glass groups including Verralia, Vetropack, Gerresheimer, Bormiolli, Vidrala, SGD, etc ...

difficult to grasp, the objectives are clear: to improve both performance and products quality, and therefore the factory productivity; in short, increase the Pack-to-Melt.
Rejecting defective items is a first step, but the challenge behind is more ambitious: reducing the production of defects.
Defects in glass have various origins, from raw materials to manufacturing or forming processes, at the furnace, IS machine or annealing lehr. The inspection machines are located in the cold part of the factory. In general, between two and four machines inspect the articles of a single production line. Relying on the data coming from a single machine, no matter how intelligent it may be, reveals only a part of the picture.
Iris Inspection Machines R&D team targeted the next level, creating a collective intelligence based on NEO machines
It is not a question of simply interconnecting the machines, as they already are, neither of communicating with a manufacturing tool such as MES. The concept of collective intelligence developed by Iris goes much further. Data collected by each of the EVOLUTION machines are pre-processed, the characteristics of the defects, the sizes, the images and mould numbers are correlated in real time. The solution, called NEO X, combines and cross-analyses inspection data to highlight the production trends and defects’ prediction. This collective intelligence offers a precise overview of the production quality for each line, and trends offer an essential tool for productivity improvements.
NEO X allows, for instance, any software solution, to highlight major defects trends, in real-time, and helps the operators to focus on essentials. NEO X is the necessary intelligence for managers to help taking decisions.
Based on an open data format, NEO X is compatible with the plant’s information system. It has become a valuable source of information for the glassware MES tool, by providing not only relevant and precise data but real-time images of defects as well. �
*CEO, Iris Inspection Machines, Bron, France www.iris-im.com
� NEO X combines and cross analyses data from Evolution NEO machines.