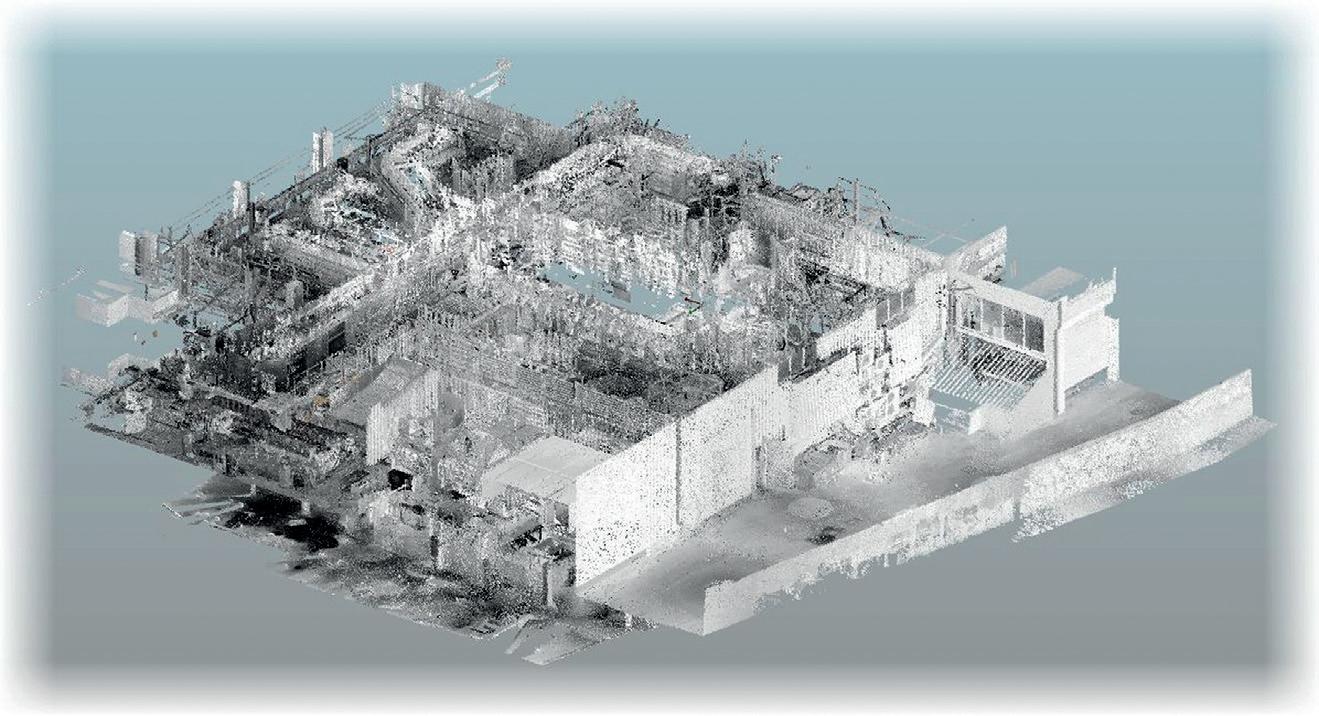
5 minute read
Furnaces: Sorg Laser scanning in plant repairs
The application of laser scanning techniques in plant repairs
Clemens Eidmann* discusses how reusing existing buildings and structures can help in the case of glass plant repairs.
Existing building structures and infrastructures and the demand for ever larger glass melting plants make the handling of so-called Brown Field projects increasingly complex.
Present structures are to be reused to a larger and larger degree not only for cost reasons.
The integration of new stages, entrances, plant components, etc., into the existing systems considering increasingly extensive safety regulations and the positioning of new and also reusable equipment requires a higher degree of coordination effort with the client than was necessary just a few years ago.
Not only the communication with and the involvement of the customer in the solution fi nding process, but also the coordination of the individual technical departments over the different project phases makes a detailed visualisation of the existing plant complex necessary.
For the planning and integration of the new or to be modifi ed plant parts or infrastructures, you need to rely on existing documentation.
If these are still present, they are in paper format due to the age of buildings, etc. This makes the data transfer to the new plans diffi cult or impossible.
Furthermore, very often additions and adjustments have been made over the years so that the existing documents are no longer up to date.
In these cases, it was and is common for employees of the planning company, to be on site for a longer period of time and to record the situation with conventional means, paper drawing, folding rule and laser measuring device, depending on the size of the plant.
Practice shows that these inventories contain inaccuracies and can also be incomplete.
A reasonable alternative to the classical inventory is the method of laser scanning, which has already been used in other areas. Sorg has now introduced laser scanning for the inventory of existing building structures and infrastructures in the glass industry.
Laser scanning captures up to 1,000,000 points/second with the help of a laser beam rotating around two axes.
Each detected point receives among other things two angles and a distance to the set-up laser scanner.
These polar coordinates are then converted into a Cartesian coordinate system. Thus, there is an x, y, and z coordinate for each point.
Furthermore, the entire system can be aligned in 3-dimensional space as desired and thus positioned to newly planned system structures in CAD programs.
The Sorg laser scanning team is able to capture the complete plant situation in a short time.
Therefore, the system is scanned across 400 or more installation sites of the laser scanner across all fl oors. The following
� The measuring points calculated via a 3D point cloud.
� The scanned system structure can be processed digitally in 2D and 3D CAD.


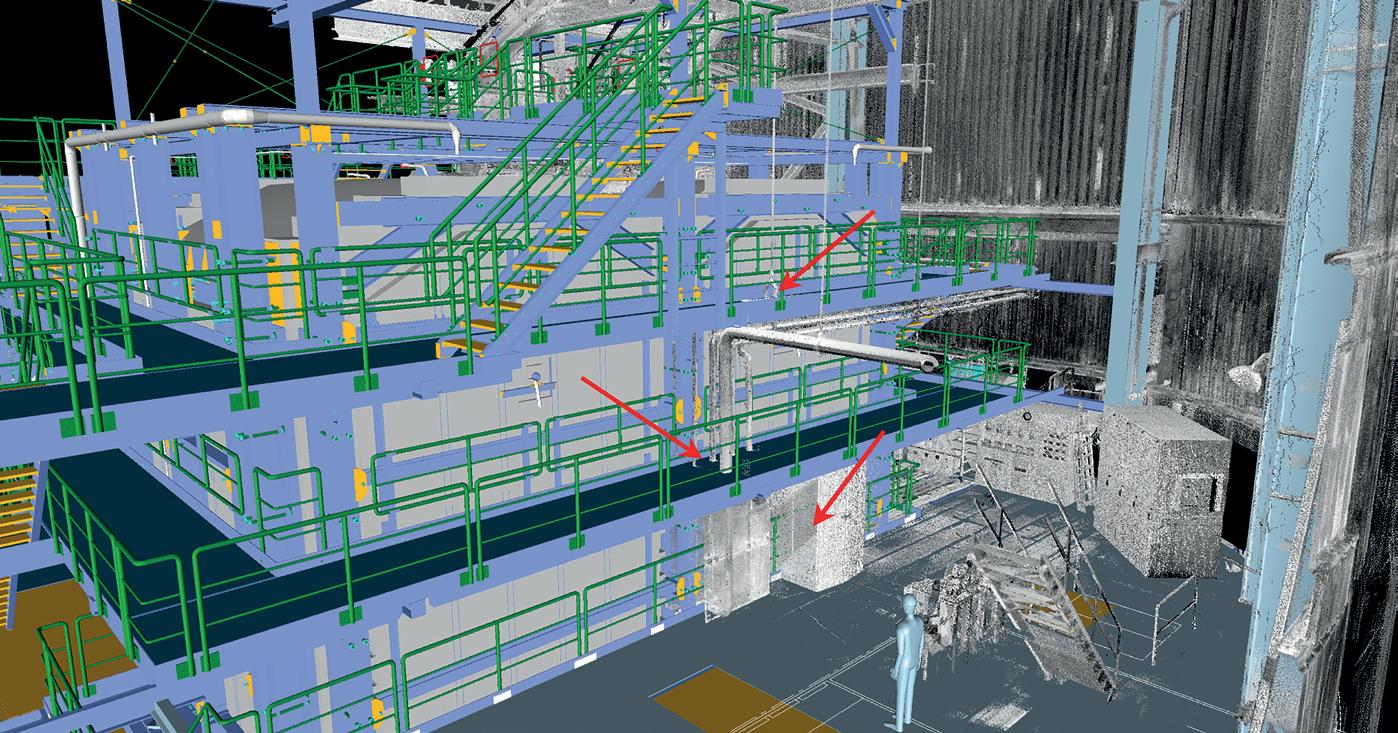
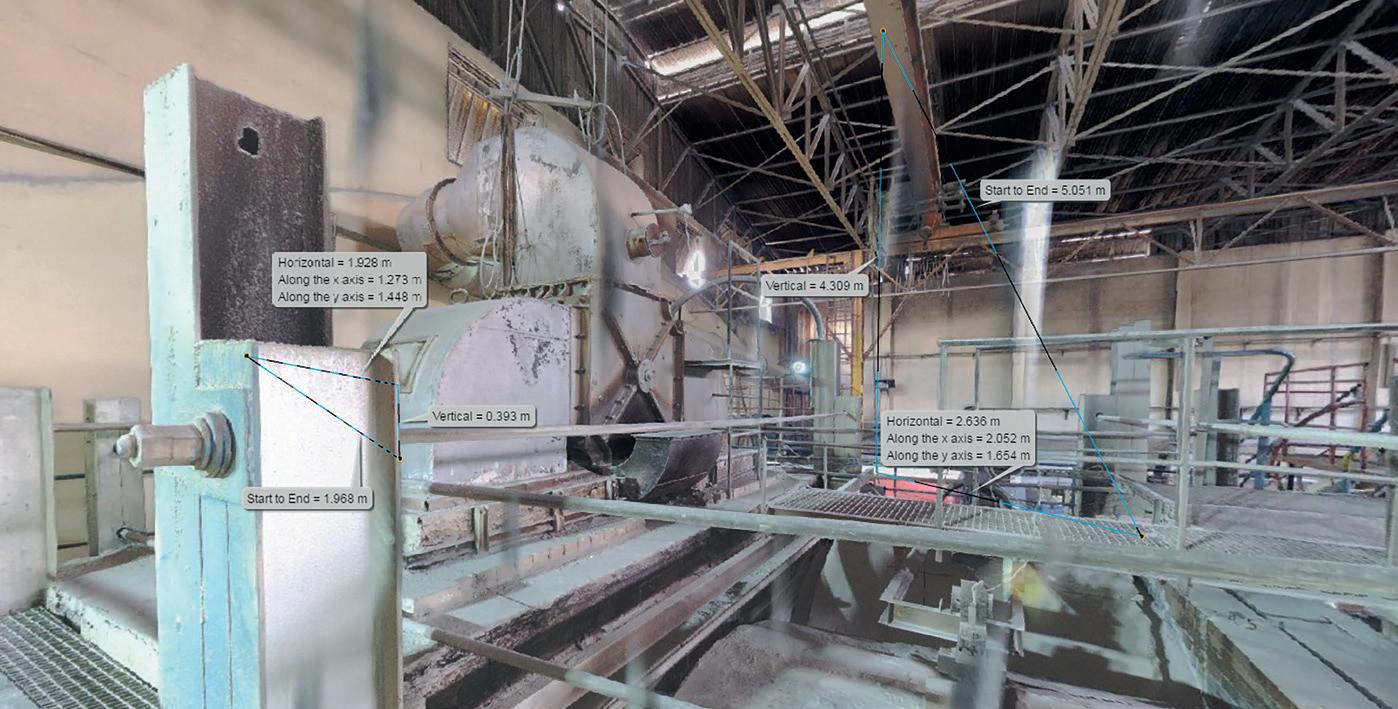
� The measurements of the laser scanning of existing and future systems.
� It can help determine whether a newly planned reversing unit is possible
fi gure shows the measuring points (installation sites for the scanner) (Fig.1).
Subsequently, the entire system with all its details is calculated as a 3D point cloud and made available to the user.
In this point cloud, which of course can also be available in colour, a simple measurement of the existing and required structures is possible.
In addition, it is possible to extract further measurements from the 3D representation, which did not seem superfi cially necessary.
The scanned system structure can be processed digitally, both with 2D CAD and 3D CAD programs.
In addition to the almost complete recording of the existing system with all its pipes, cable trays, stairs, stages, fans and other equipment and the associated ability to measure all these structures and their position to the millimetre, also a much clearer communication with the customer is possible.
A picture is worth a thousand words. For example, the customer can be told very quickly, if there would be collisions with existing components and the system being planned.
Of course, collision control is in the foreground of planning when using new components or components that are to be fi tted to existing plant components.
In this example, a newly planned reversing unit is delivered to the existing structure. In the past, it only became apparent at the building site, whether the unit really fi ts or needs to be adapted on site.
As a basis for planning, it was well known that an oversize and possibly existing original planning documents were used. But it is not known whether these planning documents represent the real state.
The planning quality at Sorg has been further improved by the introduction of the laser scanning process.
With specially trained staff and own equipment, you know exactly what is important when scanning. This ensures that you can reasonably construct with the data later on.
A measurement of the entire system can be realised in a short time, without affecting the operation in any way.
Thus, for example, the forehearth situation of a system can be scanned in just one day and across all building fl oors.
With the help of this data Sorg is then able, for example, to record the real gob point situation and to consider it in the planning.
All this saves adjustment work on the building site and enables a smooth project process.
Conclusion
3D laser scanning is a modern method which allows you to record existing structures quickly and accurately.
The data can be used for further planning, so that the accuracy is increased and possible collisions are already identifi able at the beginning of the planning phase.
Sorg has successfully introduced 3D laser scanning in the glass industry. The company has the equipment and the team of experts to carry out the inventory in a timely manner, tailored to the customers’ needs and the task. �
*Head of Design, Sorg, Lohr am Main, Germany www.sorg.de
� The software can also help integrate new equipment.