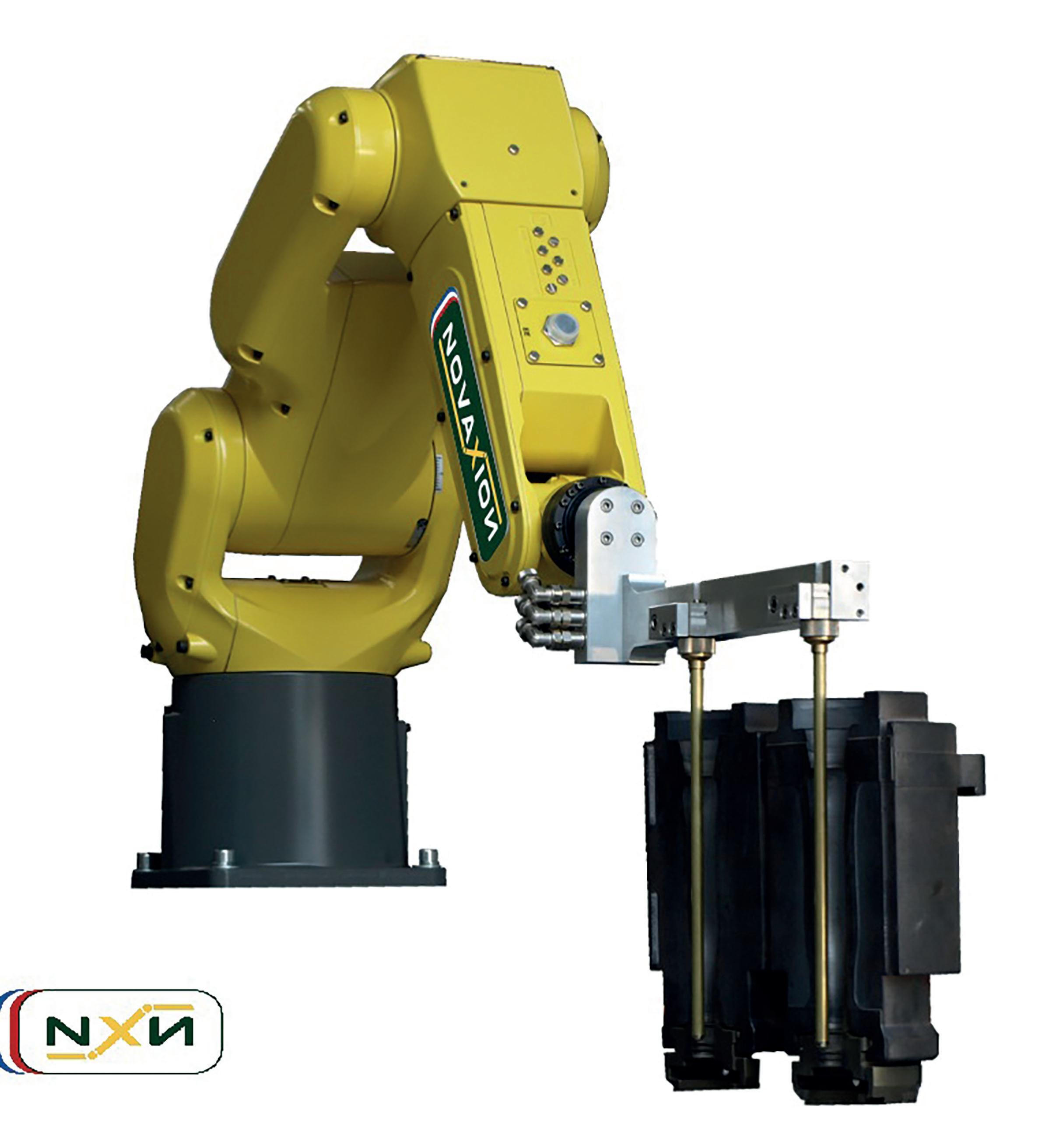
5 minute read
Swabbing: Novaxion Novaxion joins Rondot Group
Novaxion’s swabbing robots partner with Rondot Group
Over the past 15 years, Novaxion SAS France has successfully installed 100 swabbing robots globally. In partnership with Rondot Group, a series of key changes have been implemented in recent times to maximise customer service, as Frédéric Nio* explains.
Recent integration with the Rondot Group has provided expanded manufacturing facilities for Novaxion, in addition to which a series of management changes have been implemented to better serve and respond to the demand of customers.
In January 2021, Frédéric Nio was named the company’s Managing Director. Having worked as a senior Rondot Group SA Company manager for six years, his association with the glass industry extends to more than two decades. Mr Nio’s experience will facilitate the company’s integration within the group and its development of sales.
Robotics technology specialist
Novaxion specialises in robotics technologies for the glass industry, offering solutions for the automatic swabbing of blank moulds and neck rings on IS machines. Innovative developments, an individual approach to each customer, along with professional engineering and management are among the qualities that have positioned the company as a leader in the industry over the last 15 years.
It was in 2005 that Novaxion decided to integrate a reliable industrial model of robot from Fanuc, thereby adding an important example of automation to the production of glass containers.
Initially, the company offered gathering robots for the handcraft and semi-automatic production of glassware but in 2008, a high-performance swabbing robot was introduced to apply a specially engineered swabbing spray to the moulds.
The decision was taken to ‘smartly’ spray the lubricant onto the cavity of the mould, an approach recognised as the ultimate solution to offer both neck ring and mould swabbing.
All other existing carbon sooting or swabbing tool management solutions required a manual swab to the neck ring. Novaxion’s solution provides effective and independent lubrication of the blank moulds and neck rings using a dedicated arm and nozzle.
Under air pressure, the swabbing lubricant (oil) is sprayed inside the mould while the mould is closed, ensuring the even distribution of a very thin film of lubricant. This solution results from an extensive and focused development of the spraying tool, specific nozzle studies and spraying profiles, combined with lubricants and their behaviour. As a result, the pattern of lubrication during automatic mould swabbing can be customised specifically to each production or cavity design.
The Novaxion swabbing
� robot.

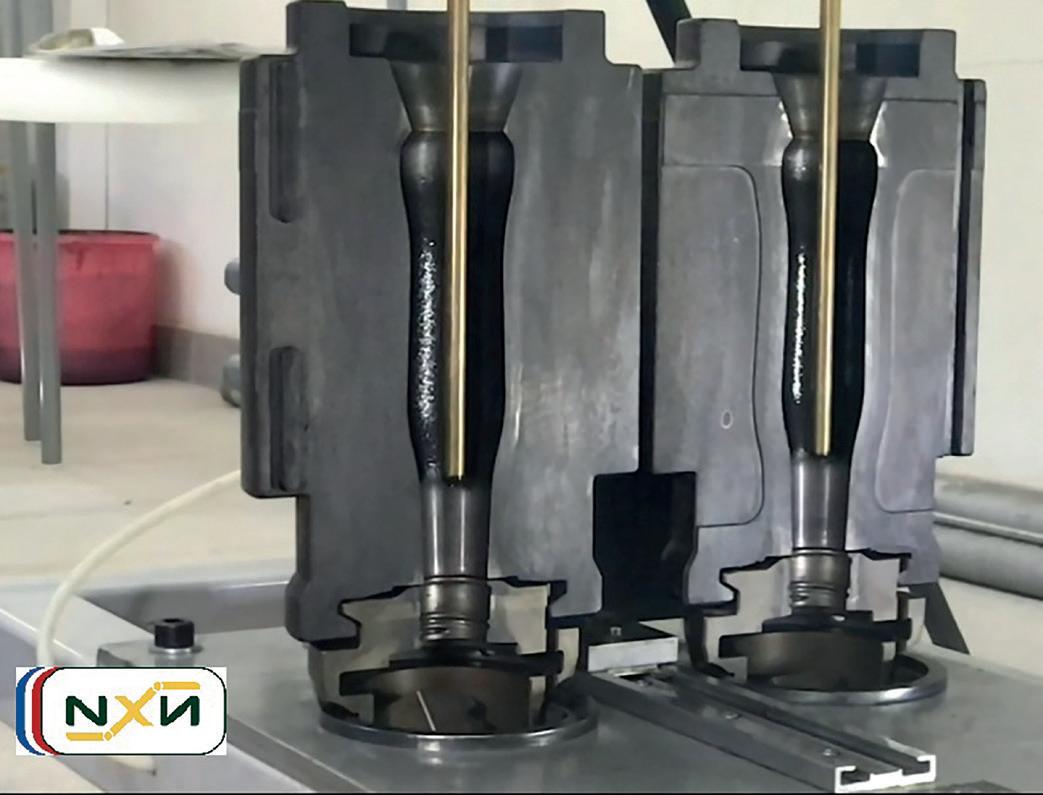
� A typical spraying pattern, equally distributed on the mould walls. � The spaying nozzle extension uses a hollow cone spray.
Automation and lubrication
The swab motion is fully controlled and monitored by the robot control unit, in terms of position and speed. Motion synchronisation is triggered by the IS forming control system.
The swabbing robot is fully automated and all parameters can be configured for each section individually.
This means that each section can have a different swabbing profile, depending on the ware produced (for example, multi gob feature).
The robot is quickly and easily set for a production type and does not use a learning sequence.
Swabbing cycles
There are several swabbing modes that can be combined and selected by the operator: � Normal. � On-the-fly.
In the normal swabbing process, the blank mould and neck ring lubrication mode when combined together will require one ‘section cycle’ and consequently, one section reject.
This combined mode provides both swabbing moulds and swabbing ‘on’ and ‘inside’ the neck ring. The special design of the spray nozzle produces a hollow shape cone, such that the oil does not contaminate the plunger.
With the on-the-fly swabbing process, it is important to highlight that the Novaxion robot alone can provide moulds close ‘on-the-fly’ lubrication. This method significantly improves the process, its efficiency and result.
The very thin layer of lubricant applied to the moulds will deliver no reject and will not require a section to be stopped during swabbing. This significantly reduces the number of defects and oil consumption, extends the mould lifetime and allows a better pack-to-melt ratio.
Safety and health
A multi-level safety system covers the operation of the robot along the IS machine, thus considerably reducing the risk of injury to operators.
Virtual safety barriers offer three safety zones with different safety behaviours of the robot. The robot complies with the CE Machine Directive.
Human impact
The swabbing robot uses much less lubricant than traditional methods (approximately 70% less).
Less lubricant and automatic swabbing generates less fumes, thus keeping the operator away from the area of swabbing, preserving health and improving the local working environment.
The swabbing robot will free the operator from repetitive and dangerous tasks, allowing more time to focus on bottle making supervision and action.
This is where the operator’s added value and knowledge are important, including the determination of bottle shape and dimensions, weight, calibration, cooling capacities, fine tuning of the IS machine etc.
The swabbing robot is not intended to completely replace the operator; it makes the working environment safer and more effective for the glass plant. A close link between the machine and human helps to achieve and maintain higher production rates.
User benefits
implemented in the Novaxion robot concept, it is now possible to significantly improve plant performance, reduce lubricant consumption (>70%), provide a more efficient and highquality lubrication process, reduce rejects, product defects and losses and contribute to a cleaner and safer working environment, while removing the operator from the contaminated area, thereby protecting his/her health.
Automation should be applied where the disruptions in the process are revealed. Swabbing is a process where variations exist by shift, by operator or by the product being used (lubricant type and quantity).
A constant quality of production with high output is achievable with automatic swabbing. With extensive experience, Novaxion is ahead of this technology and can offer the most comprehensive solution to an automatic swabbing project: � Using a spray for smarter and more precise application of lubricant inside the moulds and neck rings � The special nozzle provides smart swabbing to the neck rings, without polluting the plunger equipment � A patented solution for mouldclosed swabbing. � On-the-fly mould closed swabbing with no rejects.
As a proof of the equipment’s success, more than 100 swabbing robots are successfully running on four continents, with projects in Europe, Asia, Africa and the Americas. �
*Managing Director, Novaxion, Saint Rémy de Provence, France www.novaxion.fr