
2 minute read
Moulds: Offi cine
Sara Leoncini* highlights how the use of industry 4.0 can improve the production process of mould making.
The moulds for the production of tableware and technical articles present many complexities in the standardisation of production cycles.
The range of sizes of the articles -from perfume bottles or glass stem to insulators for power lines- and the various production processes used -press, blown, centrifuges, etc.- make it difficult to identify a common manufacturing process.
It is essential, therefore, to analyse each project with the utmost attention before starting the construction so that you can draw up a correct machining cycle that can allow you to realise the series of moulds with a good productivity.
To analyse the project it is necessary to have an integrated data management that can allow Production Managers to process work cycles that are based on historical data of similar processes and, at the same time, make it possible to check the progress of the work corresponds to what has been planned.
For production, it is essential to have multi-axis machine tools that are versatile and that allow to perform complex processing phases in a small number of placements with the aim of eliminating unproductive preparation times.
In fact, the company project of Officine concerns the innovation of the production process and aims to group various stages of machining on 5-axis machine tools that, reducing the time of equipment, have a longer automatic production time.
In this context, Officine is also equipped with data management systems that keep information under control, both from production and to production according to the principles of Industry 4.0.
The company’s goal is to achieve high productivity in a sector where standardisation and repeatability are critical, thus developing the automation needed to be competitive in an increasingly selective market.
In the following photos, we can see the results with application examples of this project.
From a piece of raw material (the mould in photo 1), we directly obtain the finished mould (mould in photo 2) thanks to the union of various automated processing steps.
The work cycle includes turning, drilling and milling operations carried out in sequence on a 5-axis Machine Tool with double spindle in a single placement. Working at high feed and cutting speeds, makes the choice of the tools used very important. These must perform both for the removal of material and for the duration and must allow the operator to
� Pic 1.
� Pic 2.

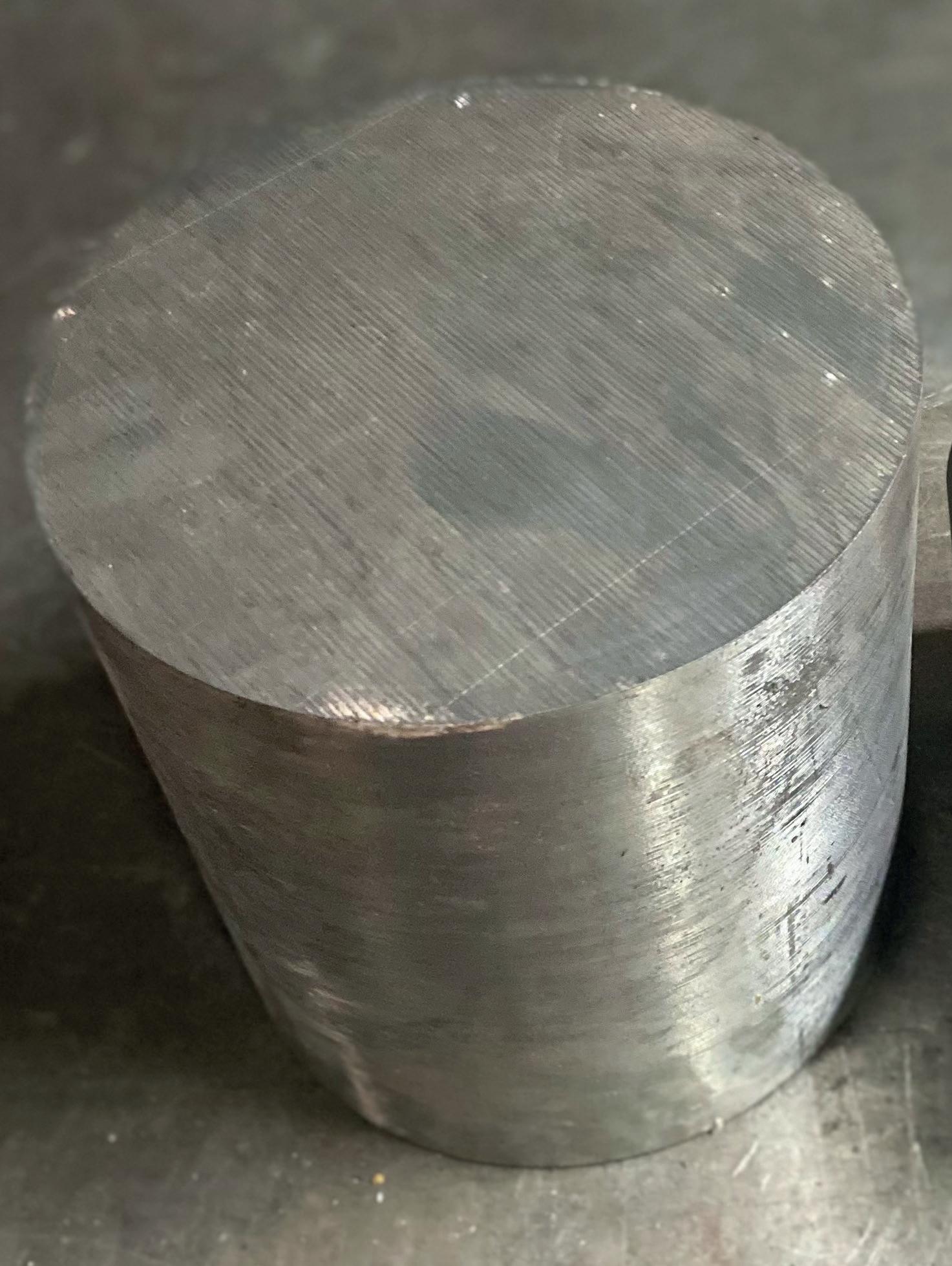
make the best use of the potential of the machine tool.
It has been calculated that the time taken to make the moulds with the new production cycle is 30% less than the time spent with the traditional machining cycle.
In this case, the piece of raw material is cut from the bar without further preparation (piece on top in photo 2).
The result is the finished mould holder ready for assembly (piece on bottom in photo 2).
Also in this case, the sequence of phases of drilling, turning and milling carried out at high speed allows to reduce the production time by about 30% compared to traditional processes.
The use of the new 5-axis Machine Tools in Industry 4.0 allows the review and often improves the production process of each series of moulds, regardless of the type of glass production to which they are addressed. �
*General Manager, Officine, Siena, Italy https://www.officinesl.com/en www.glass-international.com