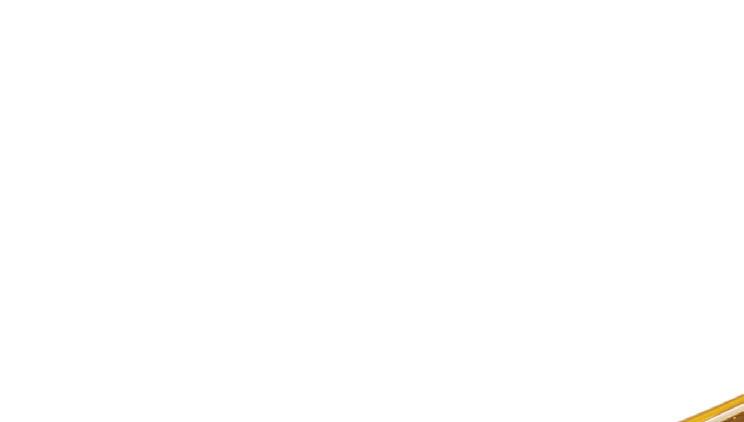
10 minute read
From past to future

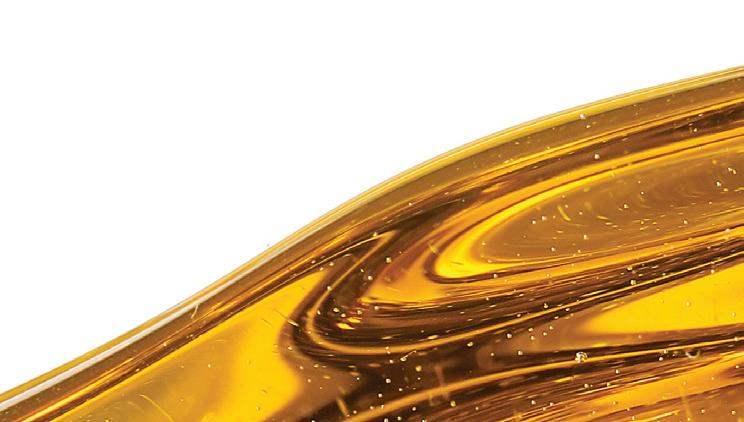
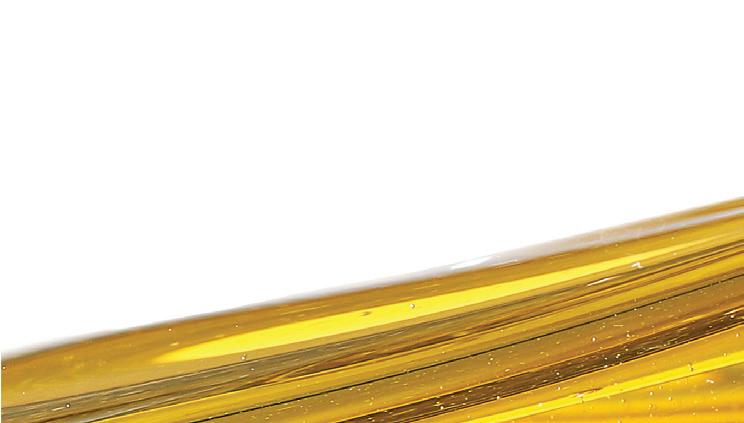
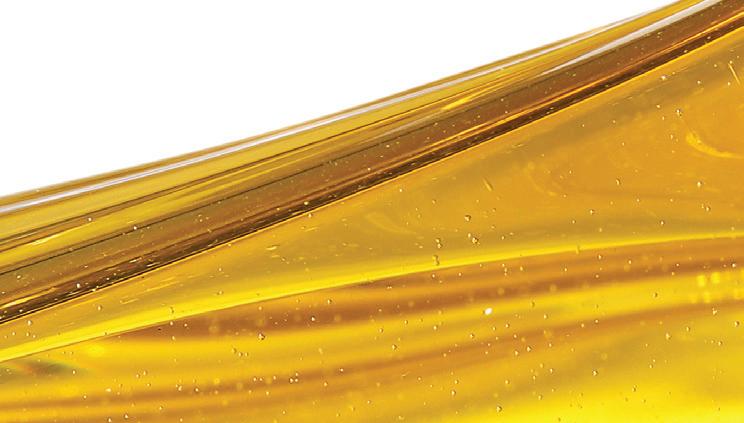
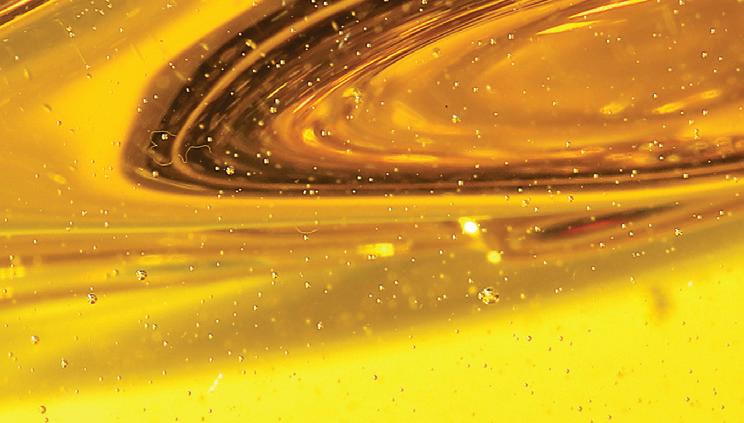
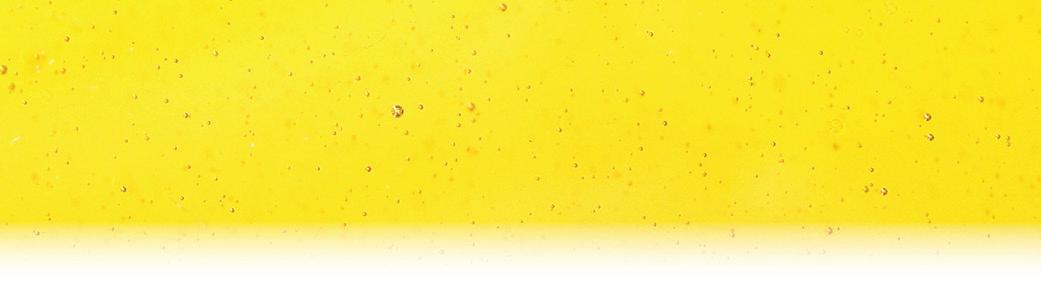
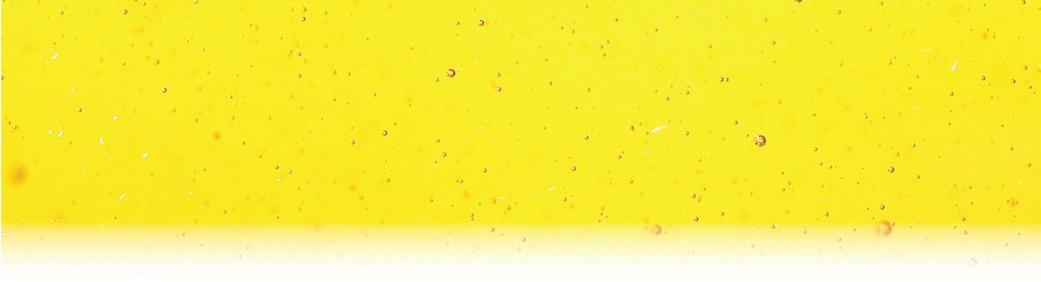
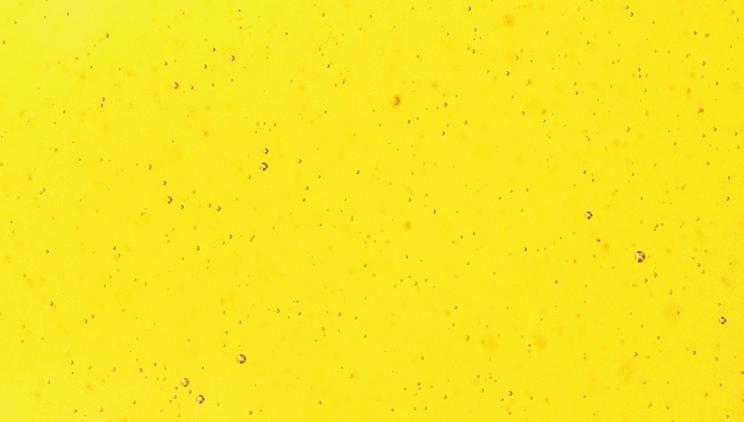
Optimising Optimising filtration filtration

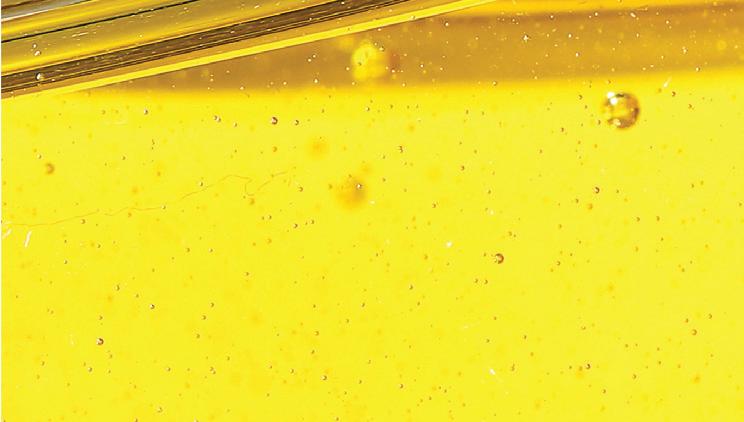
Filtration is an important step in the bleaching process of edible oils which depends on factors such as the oil being processed, bleaching temperature, the amount of impurities in the oil and the type of bleaching earths and ltration aids used Rick Veldkamp
Filtrati on is an important step in the bleaching process of edible oils and is an intensive operati on in terms of manual acti vity and constant surveillance by operators.
The length of the fi ltrati on cycle is criti cal and is dependant on the oil being processed, the bleaching earth used, bleaching temperature, and the amount of soaps, gums and moisture in the oil. The frequency of fi lter changes aff ects the cost of bleaching, with a longer fi lter cycle lowering the cost. A pre-coati ng agent will extend fi ltrati on cycles and reduces stress on fi lter screens, minimising their chemical cleaning. Filter aids also allow less frequent changes of polishing fi lters and can enhance fi lter cake release.
Filter selection and size
to be moved, and capital and operati onal expenditures.
Feedstocks before fi ltrati on will contain certain pollutants including 0.1% H20. The water is evaporated during vacuum bleaching and other contaminants like phosphati des will be removed with the bleaching clay. In physically refi ned oil, the maximum phosphati de level should not exceed 25ppm.
Causti c or chemically refi ned oil should be fi ltered with a maximum of 0.1% H2O, 25ppm soap and 5ppm phosphati des.
Contaminant levels have a signifi cant eff ect on fi lterability and even more on the frequency of washing fi lter leaves.
In all cases, it is important that when choosing a fi lter type and supplier, a dedicated design that uses only a specifi c clay, adsorbent, fi lter aid or fi lter that makes the use of other products impossible should be avoided.
Filtration options
Filtrati on opti ons can be divided into conti nuous fi lters (centrifuges and decanters, vacuum belt fi lters, vacuum drum fi lters, conti nuous sett lers, hydro cyclones and belt presses) (see Figure 1, p22) and disconti nuous fi lters (sand and media fi lters, fi lter presses, cartridge, bag and other disposable element fi lters, pressure leaf/tube type fi lters and single plate Nutsch fi lters) (see Figure 2, p22).
Process fi lters (pressure leaf or tube fi lters) (see Figure 3, p22) can be used for applicati ons ranging from 0.001-5% solids, up to a maximum of 15%. With 0.3% solids or higher, oil can be fi ltered directly on screen or cloth. Below 0.3% solids, a precoat or body feed is required. The fl ow rate ranges from 0.02-2.5m3/m2/h.
Polishing/police fi lters are safety fi lters which inform the processor that the main fi ltrati on is working correctly. They can have disposable elements such as bags or cartridges for applicati ons with around 1-100ppm solids and work most economically at <25ppm solids.
There are good reasons to avoid or minimise the use of disposable elements as replacing bags, cartridges or paper sheets requires the fi lter to be opened, which requires operator ti me to change them and can also result in health/quality issues. Bags and catridges will also be soaked in oil, resulti ng in oil loss.
The answer are pulse type fi lters using fi lter cloths as the fi lter media, which can be retained for 12-24 months.
Choice of bleaching systems
In the bleaching process of edible, vegetable, animal and fi sh oils, there has been a conti nuous quest for improved performance, bigger fi lters and higher yields. In the early stages of oil bleaching, such as Hercules fi ltrati on in 1939, the industry was already focused on lowering bleaching clay consumpti on or obtaining bett er yields from clays. Refi ning and removal of the substances that caused high clay consumpti on were the fi rst improvements and major steps were also made with improved designs of centrifuges used in refi ning.
The relati on between the presence of factors – such as phosphati des, soap,
Continuous - Centrifuges /Decanters
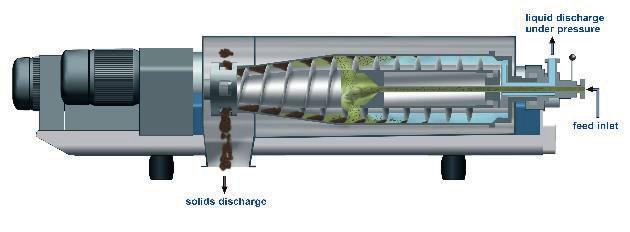
6
Figure 1: Conti nuous – centrifuges/decanters
Discontinuous / Batch – (membrane) Filter Press

Figure 2: Disconti nuous fi lters
Discontinuous – Pressure leaf or tube type filters For batch or continues process

7
Vertical Tank Process Filters
Pulse Filter 2.5 – 100 m2
(up to 200 candles)
Leaf Filter 5.0 – 125 m2
(150m2) (up to 24 leaves) Double cake discharge vibrators For leaf filters 78m2 and above
Figure 3: Process (pressure leaf or tube) fi ltersStandard Continuous Bleaching
12
BLEACHING EARTH
SLURRY TANK VACUUM BLEACHER BLEACHING FILTER
SPENT EARTH BLEACHING FILTER
SPENT EARTH POLISHING FILTERS
STORAGE
Source: PMI-Tech (Europe) BV
Source: PMI-Tech (Europe) BV
Source: PMI-Tech (Europe) BV
Source: PMI-Tech (Europe) BV free fatt y acids (FFAs), sulphur, oxidati on products and moisture – and bleaching and fi lter performance paved the way for bett er bleaching clays. Acid-acti vated clays became the standard.
The additi on of water in the initi al stages of the leaching process was a major breakthrough in the late 1970s.
Removal of residual oil from bleaching clays was the next move with the introducti on of ‘Thompson Washing’ – the washing with hot water of fi lter cake aft er completi on of the fi lter cycle resulted in 10-12% residual oil. However, this was a messy and expensive process to run.
It was the tallow/soap industries that had to deal with poor feedstocks and they discovered that if bleaching clay could be used two to three ti mes more effi ciently, there was sti ll 40-50% residual bleaching strength left in the clay.
However, it was quickly discovered that if the clay-loaded fi lter cake/residue was shift ed to the feed of the bleacher, only very short fi ltrati on ti mes could be achieved because the substances that needed to be removed – such as phosphati des, soap and oxidati on products – resulted in almost instant blockage of the clay layer. This, however, would become the most effi cient way to work with improved adsorbents.
The counter-current bleaching process is another variati on in the more effi cient use of bleaching clay (see Figure 5, p24).
The secret in this process is the avoidance of any contact between the used clay with air or moisture before it is re-introduced in a second bleacher. This way the oil is in contact with the clay twice and up to 40% clay reducti on can be achieved with high clay-consuming oils such as coconut, palm and rapeseed.
US speciality chemicals fi rm WR Grace, then promoted the use of silica under the name of Trisyl. Initi ally silica was added to conventi onal clay but, at later stages, the best results were obtained when the feedstock was bleached under atmospheric conditi ons at no more than 700C. Trisyl was used to remove the majority of gums (phosphati des), soap and oxidati on products before the actual bleaching process. If the conventi onal bleaching clay was limited on the fi lter, and the fi lter was used for pre-bleaching, this layer removed the solids, substanti ally lowering the amount of potenti al clay used.
The system became known as Tri-Clear (WR Grace), Combiclean (Desmet Ballestra) or DoublePass Bleaching (Crown Iron
Works) and is the most commonly used industry system today (see Figure 6, p24). 28 The use of diff erent processes and
adsorbents, less bleaching clays, the reuse and more opti mal use of clays, are all being practi ced within modern refi neries.
Selecting the right lter screen
When selecti ng a screen for bleached oil fi ltrati on, it is important to remember that it is not the screen which is doing the fi ltering, but the initi al layer of clay or precoat. The screen only supports this fi rst layer of solids but it plays a very important role. The refi ner’s nightmare is to have found the most opti mal bleaching clay only to fi nd out it will not fi lter properly.
The most common fi lter screens for oils and fats fi ltrati on are the Reversed Plain Dutch Weave (PZ-80 RPDW), the Plain Dutch Weave (PDW) and the Square Weave (60 mesh SW) (see Figure 7, p24).
The Square Weave has the highest permeability, with a low blockage tendency and easy cake drop and is clean aft er cake discharge.
For the PZ-80 RPDW and PDW, a fi lter aid pre-coat is opti onal, but for the 60 mesh SW, a fi lter aid pre-coat is necessary at a rate of 0.5-1kg of dry fi lter aid per square metre of fi lter area. The pre-coat prevents the screen from coming into contact with the bleaching clay and possible gluey or slimy solids in the bleached oil. This will make vibrati ondriven cake discharge easier, and less frequent fouling of fi lter leaves and subsequent washing.
Dirty fi lter screens result in unevenly formed fi lter cakes, poor fi lter performance, higher consumpti on of processing aids, and therefore higher product losses. Dirty fi lter screens are the result of over-drying of fi lter cakes. This leads to blocking of fi lter screens with parti cle residues that get stuck in fi lter pores or in between warp and weft wires.

Bleaching earths and lter aids
Processing aids can be divided into bleaching earths/adsorbent products and fi lter aids (see Table 1, above right)
Bleaching earths and adsorbents such as silica and acti vated carbon are used to remove unwanted matt er such as colouring substances (chlorophyll, carotenoids), metals, soaps, pro-oxidants, some alfatoxins, some heavy polycyclic aromati c hydrocarbons (PAH) and some pesti cides and herbicides.
Bleaching earths are generally composed of up to three types of clay minerals: bentonite, att apulgite and sepiolite. Oil is placed in contact with the clay so that impuriti es are adsorbed on the clay’s surface and the clay with contaminants is removed by fi lters.
Filter aids include diatomatheous earth, Forvegetableandanimaloilsandfats
Filter Aids Adsorbents FilterableAdsorbents
Mineral Organic Mineral Organic Mineral Organic
Perlite Cellulose Bleaching Earth Activated Carbon Functionalized Diatomite Functionalized Cellulose
Diatomite Wood Synthetic Silica Natural Silica
Table 1: Processing aids – Bleaching earths & adsorbents + Filter aids
In Europe, Diatomite is hardly used any more for oi perlite and cellulose. The main objecti ve l and fat processing. Reasons for this: high specific weight of Diatomite of fi lter aids is to provide a pre-coat layer and the associated high oil loss in the spent Diato or septum which is “ti ght” enough to mite filter cake. retain all the suspended solids from the liquid being fi ltered. The solids (bleaching earth and/or fi lter aid) will be re-circulated over the fi lter to build a thin layer of fi lter cake (0.5-1kg/m2) in which the actual fi ltrati on takes place. The size of the solids should not be too
www.jrsfiltration.com
Why PZ-80 (RPDW) and 24x110 mesh (PDW) filter screens block during cake formation and 60 mesh (SW) filter screens do not ! Slide 3
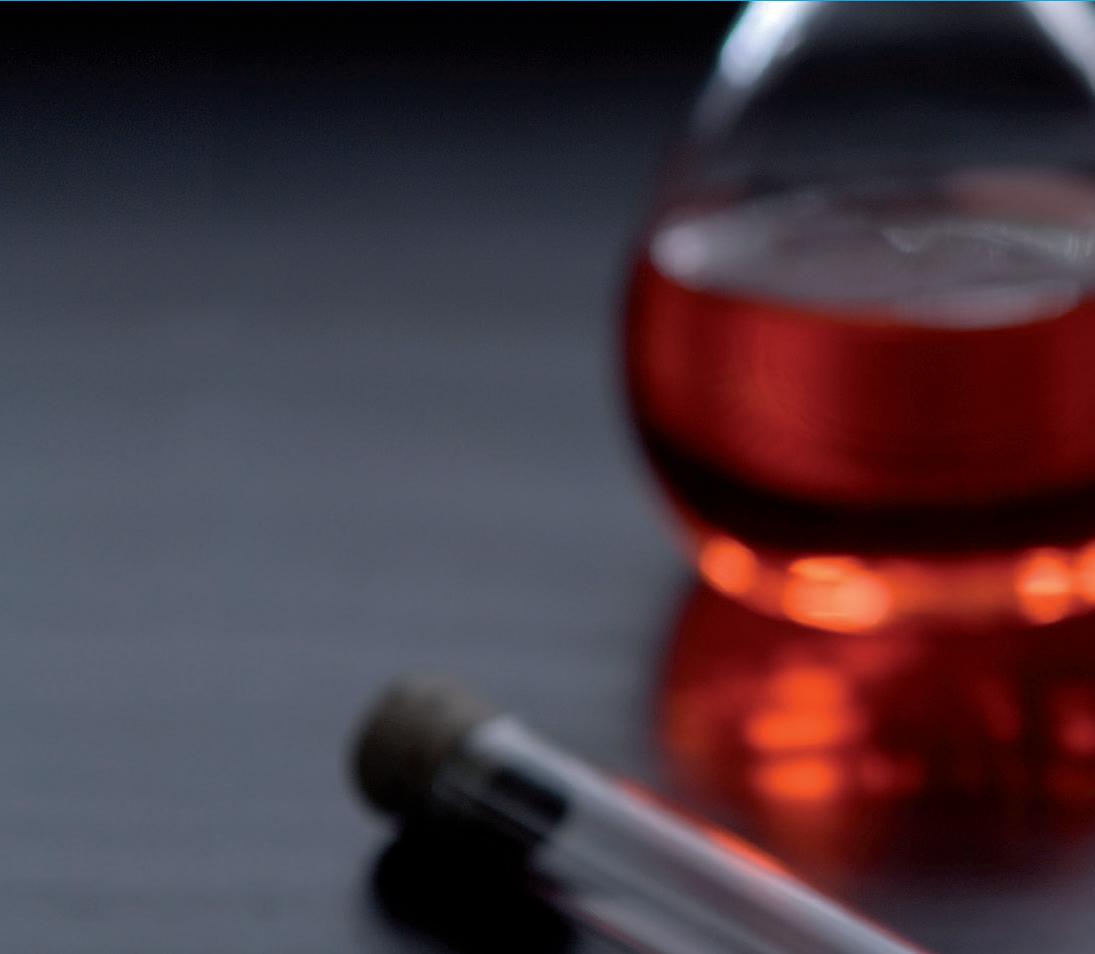
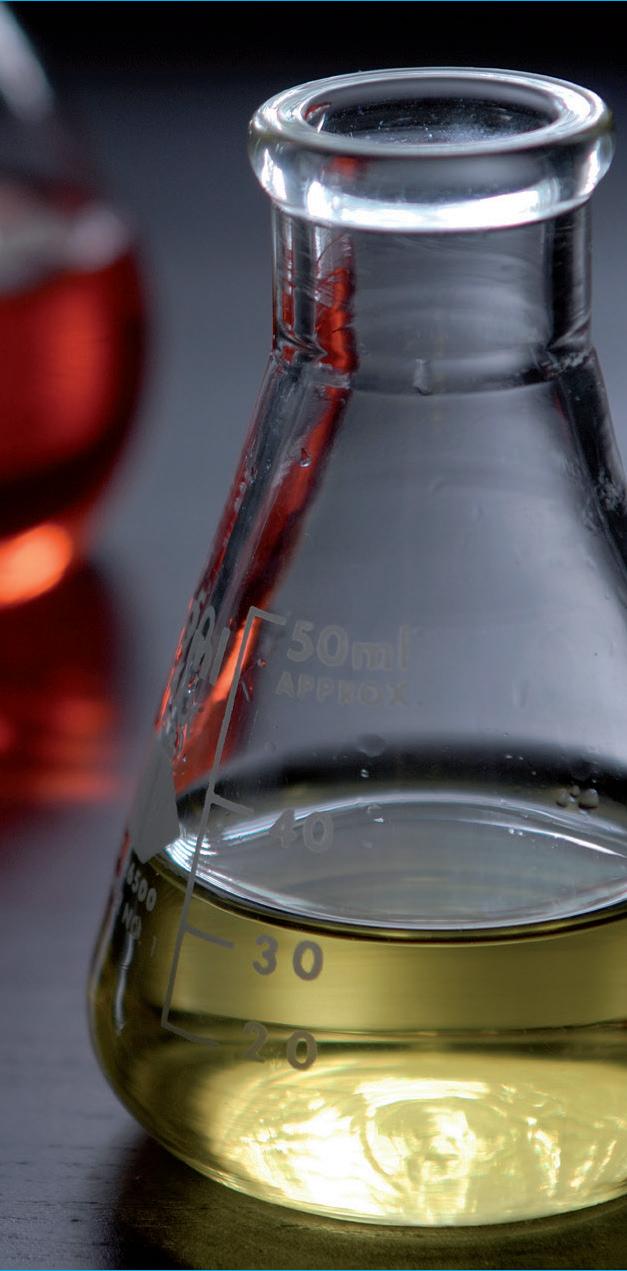
