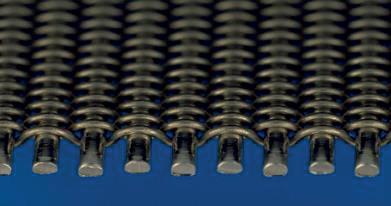
4 minute read
Tackling new contaminants

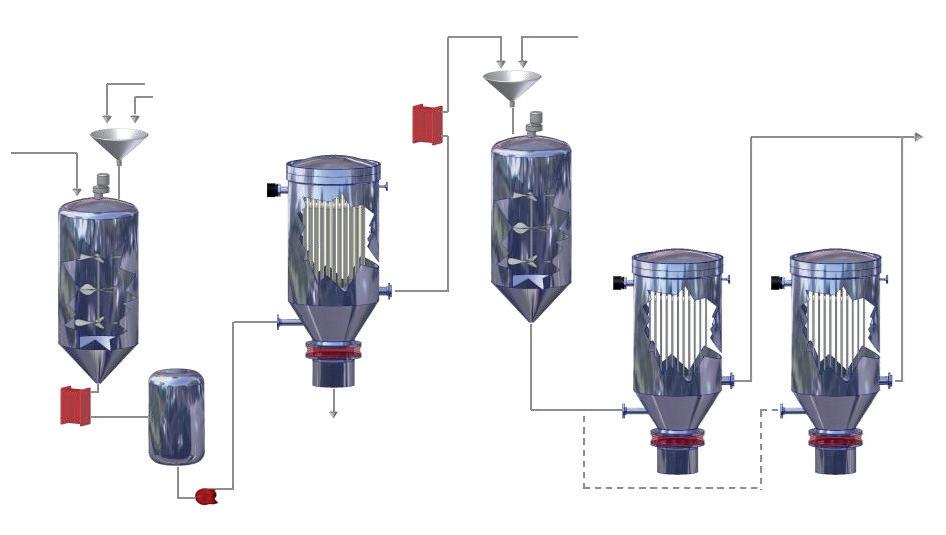
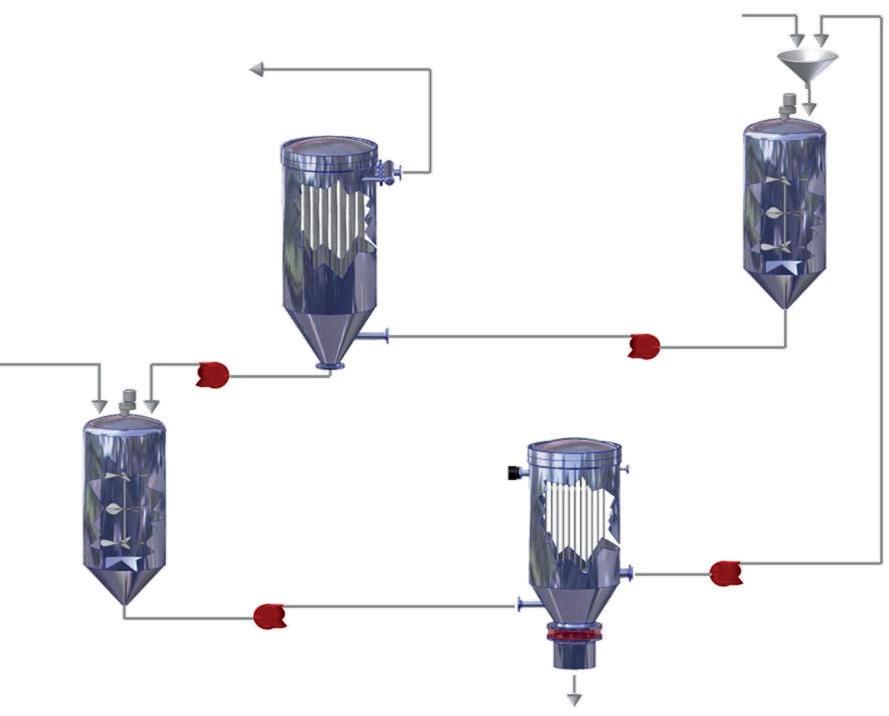
FRESH CLAY
BLEACHED FILTERED OIL
RPP PULSE FILTER
OPTIONAL SILICA BLEACH
VACUUM BLEACHER
FILTERED OIL
BLEACHER
CONVENTIONAL LEAF FILTER
CAKE BACK TO MEAL PROCESS Figure 5: Counter Current bleaching process Tri-Clear ® Double bleach ® or Combi-Clean ® Process
(with pre-filtration and or silica purification)
REDUCED CLAY
REFINED OIL SILICA
H2O (OIL)
SILICA BLEACHER 120-130°C
90°C VACUUM BLEACHER
BLEACHED CLEAN OIL
STAND-BY
70°C Bleaching Filtration
(pre-coated application)
90°C
VACUUM DRYER
CAKE BACK TO MEAL PROCESS24 x 110 Dutch Weave Filter Screen • Wire thickness 0.26 – 0.36 mm Figure 6: Tri-Clear, Combiclean process or DoublePass bleaching • Retention approx. 120 microns nominal
Bleaching Filtration
Bleaching fi ltrati on (with standard carbon or fine clays, (pre-coated applicati on) pre-treated with silica and pre-coated application) 24x110 Dutch Weave Filter Screen Wire thickness 0.26-0.36 mm PZ80 (Strong) Panzer Weave Filter Screen Retenti on approximately 120 microns nominal • Wire thickness 0.2 – 0.4 mmPre-coat Filter Screen • Retention approx. 80 microns nominal
Bleaching fi ltrati on (with standard carbon on fi ne clays, pre-treated 60 Mesh (Plain Weave) Filter Screen with silica and pre-coated applicati on • Wire thickness 0.19 mm PZ280 (strong) Panzer Weave Filter Screen • Retention approx. 200-240 microns nominal Wire thickness 0.2-0.4mm Retenti on approximately 80 microns nominal
Pre-coat fi lter screen 60 mesh (Plain Weave) Filter Screen Wire thickness 0.19mm Retenti on approximately 200-240 microns nominal

Figure 7: Filtrati on screens
fi ne as to go through the fi lter screen, nor too big as to block the screen.
When the applicati on requires a conti nuous dosage of fi lter aid during the enti re cycle, this is called body feed. The body feed will keep the cake open and will give enough porosity so that the maximum quanti ty of suspended solids can be retained before the septum becomes blocked. When the septum is
Source: PMI-Tech (Europe) BV
Source: PMI-Tech (Europe) BV blocked, cleaning becomes necessary which, in turn, causes an interrupti on in fl ow. Most bleaching clays will act as a body feed and are made with excellent fi ltrati on characteristi cs.
In bleaching, the amount of bleaching clay and fi lter aid used is an important cost factor. The amount of oil in the fi lter cake is also important as any oil in the cake will be synonymous with additi onal loss.
Because fi ltrati on takes place via the cake built on the screen, cake drying is an important step as drying which takes place for too long or at too high a temperature will bake the cake on the screen.
Automation options
36 The processing industry has been looking for more effi cient opti ons to fi lter or clean bleached oil for many years. Increased capaciti es and increased number of fi lters has resulted in bigger units to provide more fi lter area per fi lter, less operator involvement, and more automati on.
Filter areas in verti cal tank and verti cal leaf fi lters have increased from 50m2 to 125m2 per unit. Horizontal tank fi lters are available at 225m2 per fi lter but require a much larger footprint and create housekeeping problems when opened for cleaning.
Pressure leaf fi lters are disconti nuous and need to be taken off -line to be cleaned, whereas a conti nuous process requires more than two fi lters, requiring more and bett er automati on as there is no ti me to open fi lters for visual inspecti on.
Cake discharge has always been a point of concern as it was not always known if the fi lter cake had left the fi lter aft er the vibrati on cycle, with cake accumulati on potenti ally resulti ng in damaged fi lter leaves. The soluti on is the use of load cells that measure the weight of the empty fi lter tank. If the cake is not fully discharged, the fi lter will not be able to go back on-line. The selected and chosen screen is also an important part of successful fi lter performance.
Source: PMI-Tech (Europe) BV
Filtration trends
37 38
Filtrati on is heading towards bigger capaciti es with multi ple fi lters in service, which will demand more automati on and bett er uti lisati on of installati ons.
Waste management is also becoming increasingly important and special att enti on should be paid to spent clay and carbon; and the disposal of consumables such as fi lter bags and cartridges. This will require the implementati on of special screens and cake discharge systems to improve cake discharge in bleached oil. ●
Rick Veldkamp is the European sales manager of PMI-Tech (Europe), Netherlands
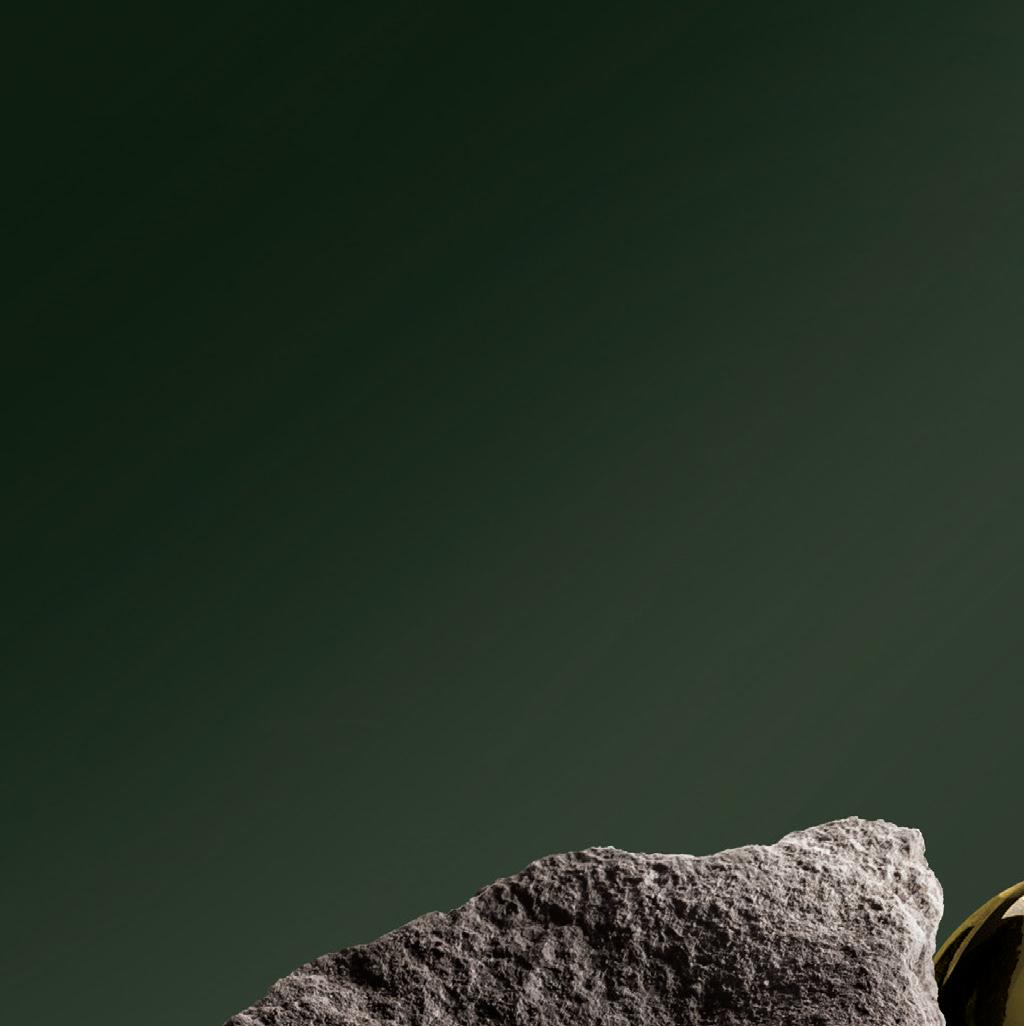
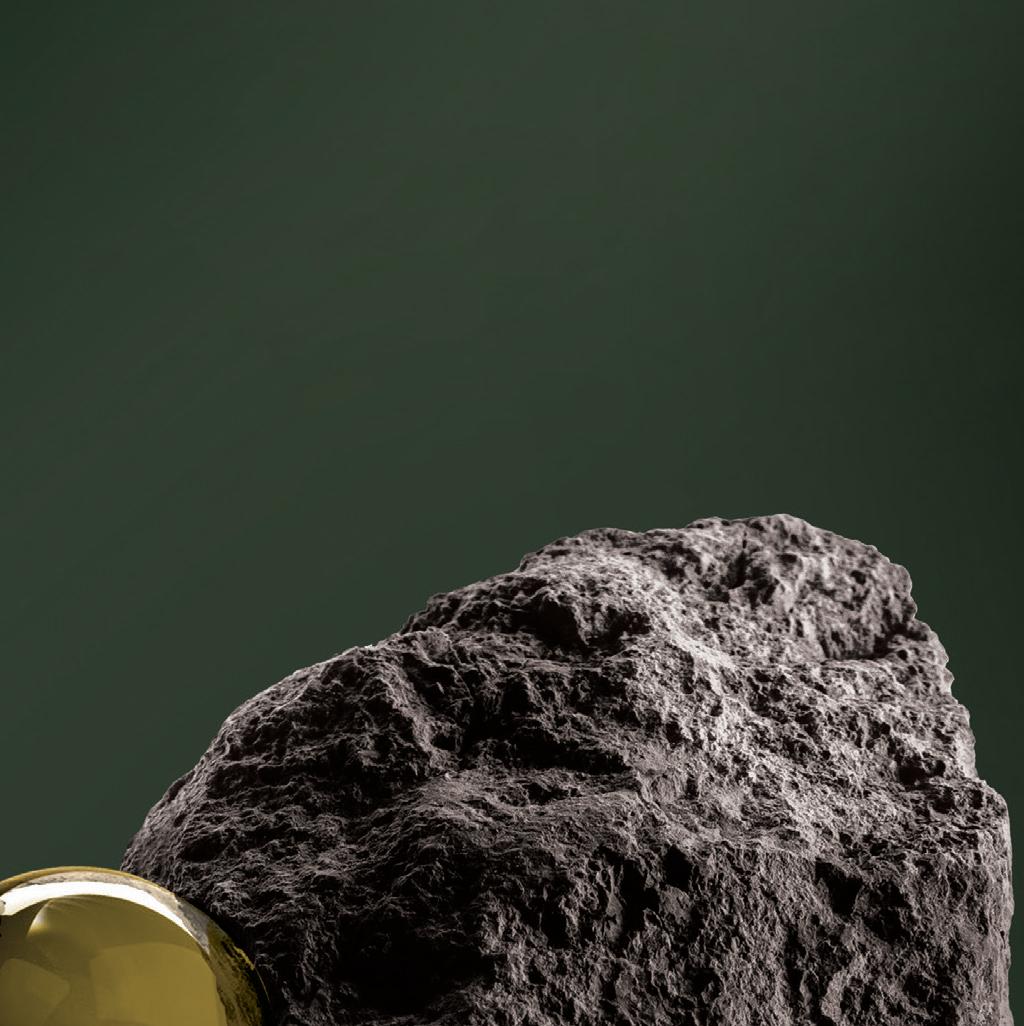
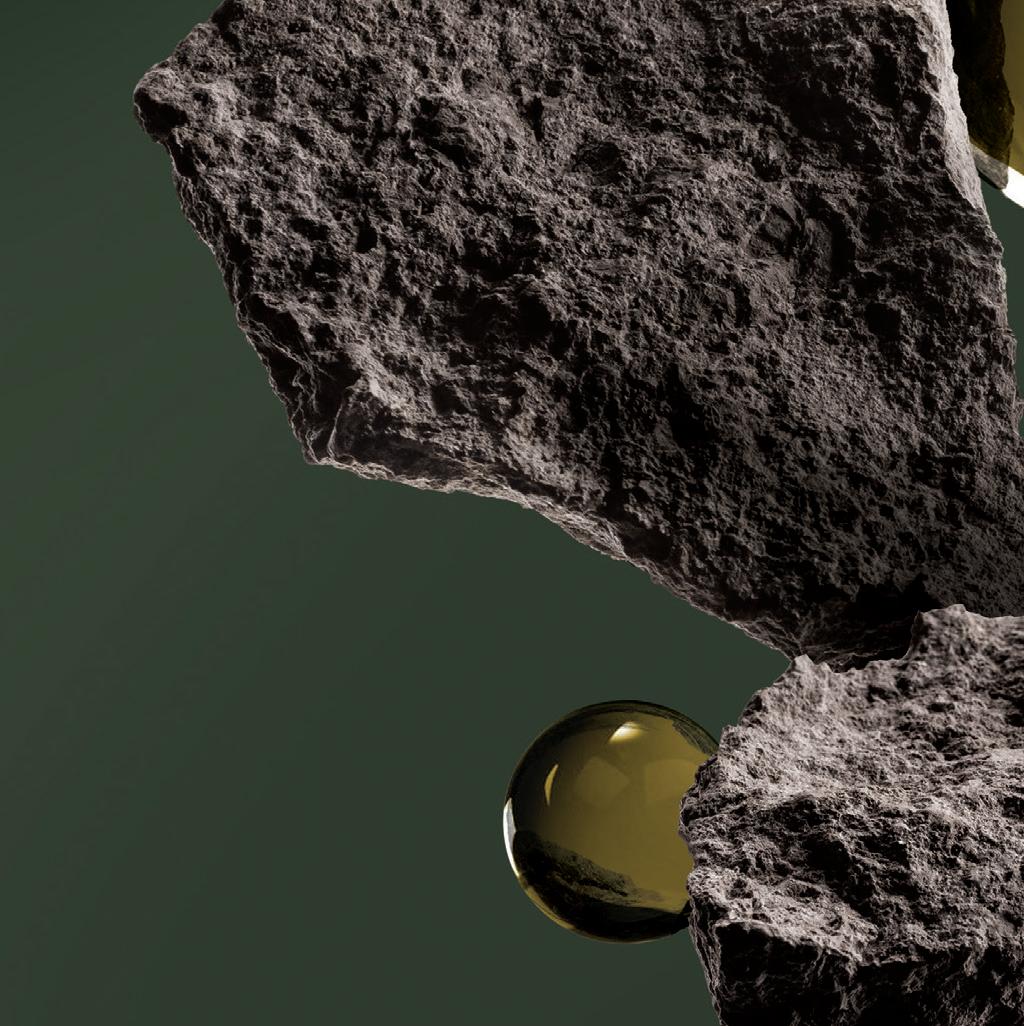
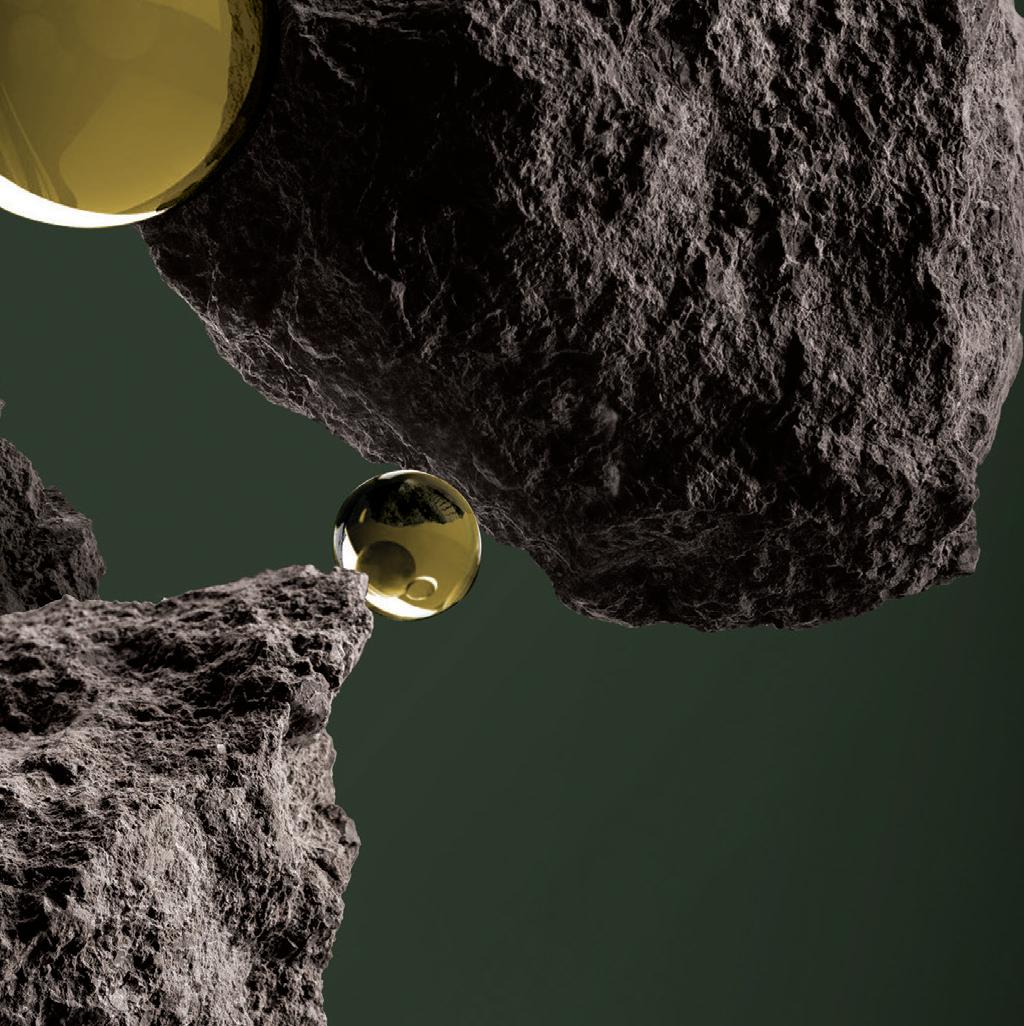
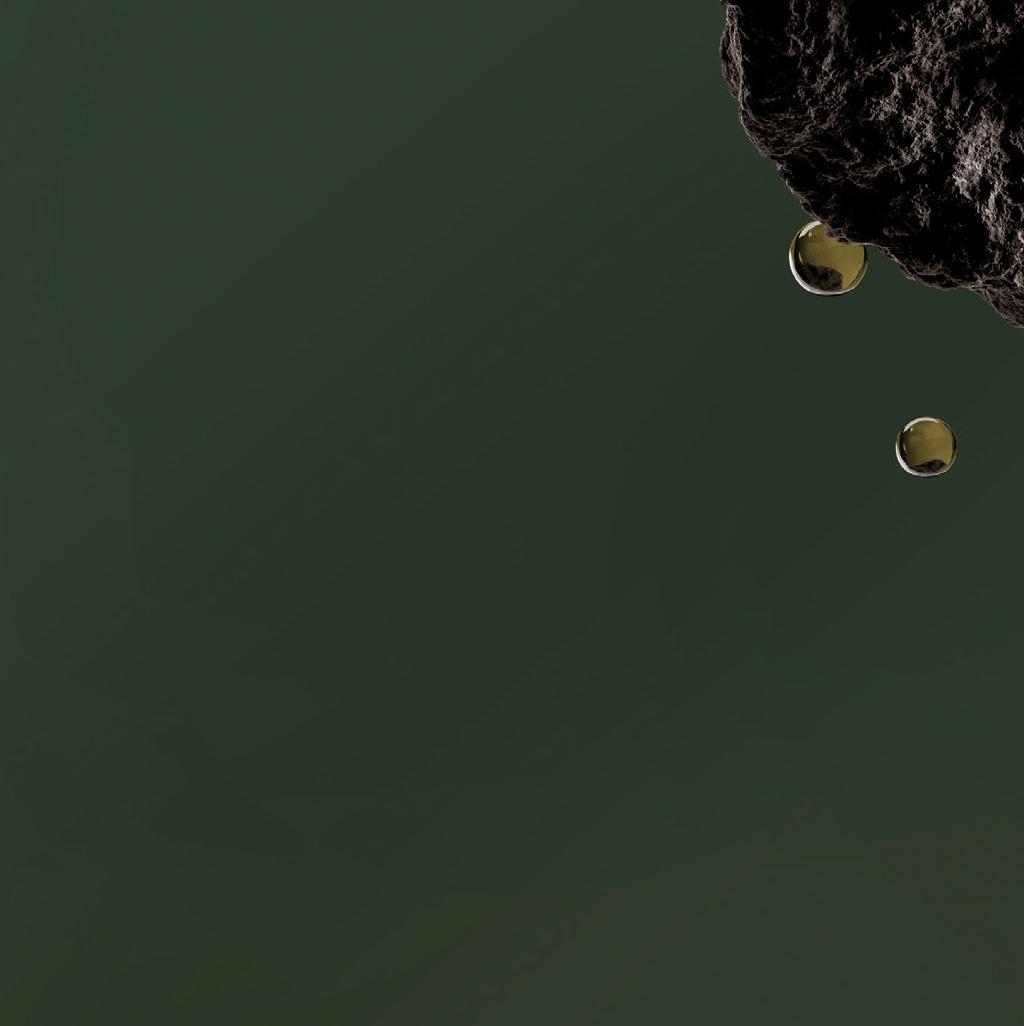
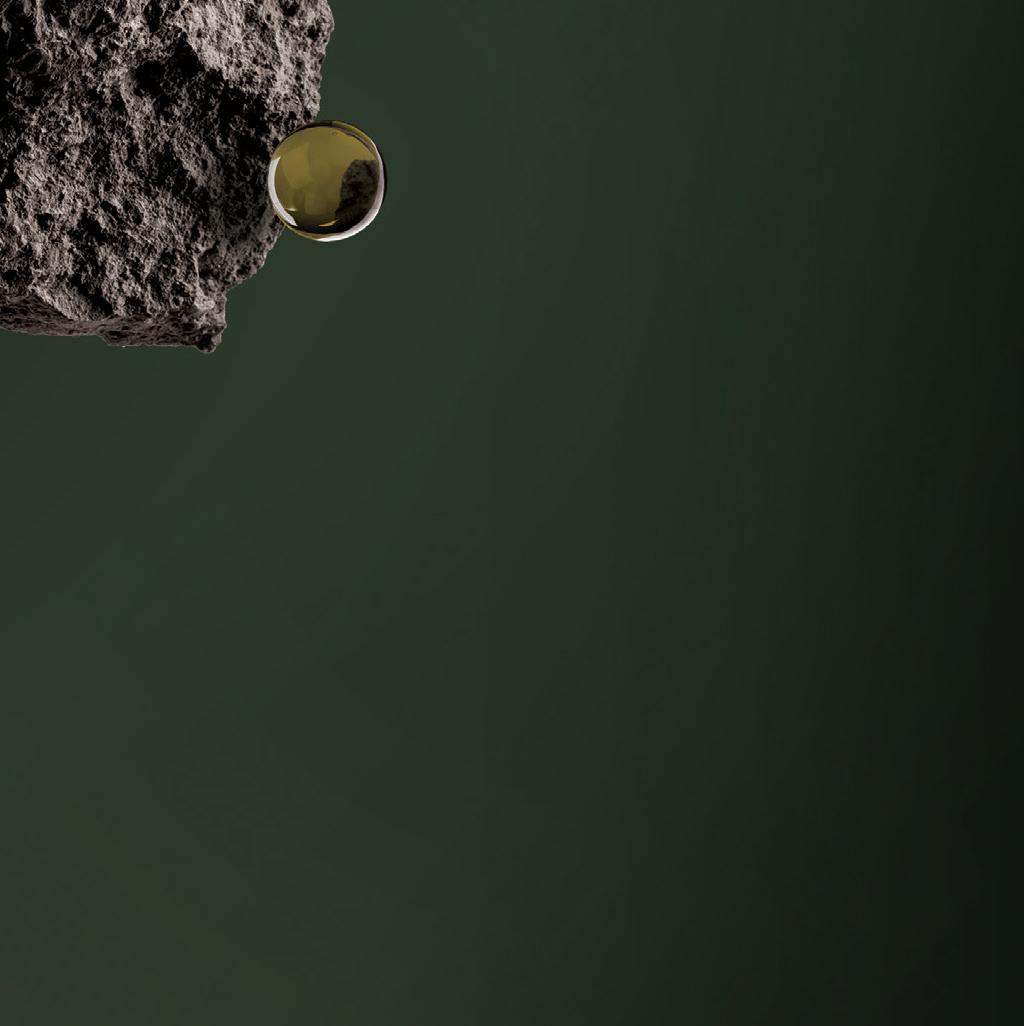
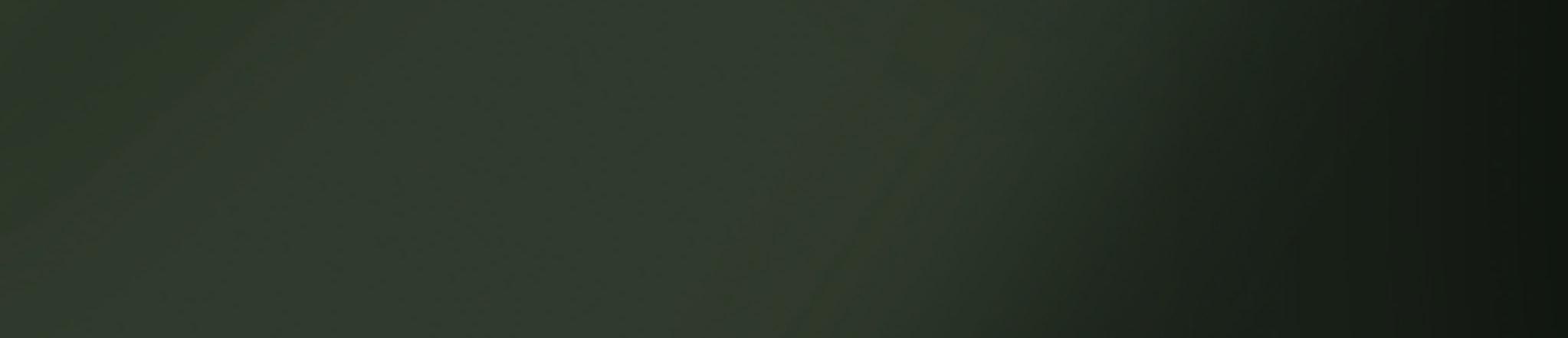