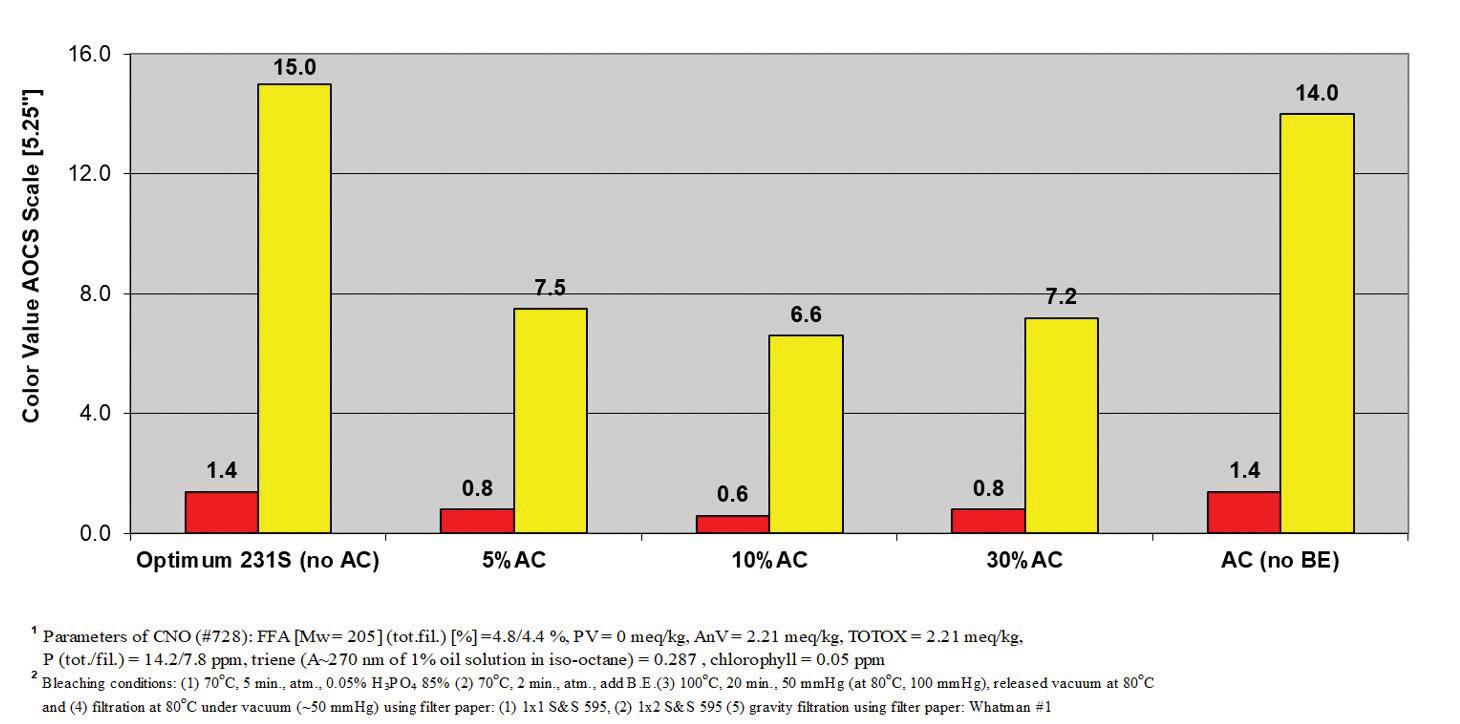
2 minute read
BLEACHING EARTHS
Colour
Relative density at 400C/200C
Refractive index at 400C
Moisture & other volatiles at 1050C
Free fatty acids, calculated as lauric acid % by mass (maximum)
Peroxide value (millequivalents of active oxygen per kg)
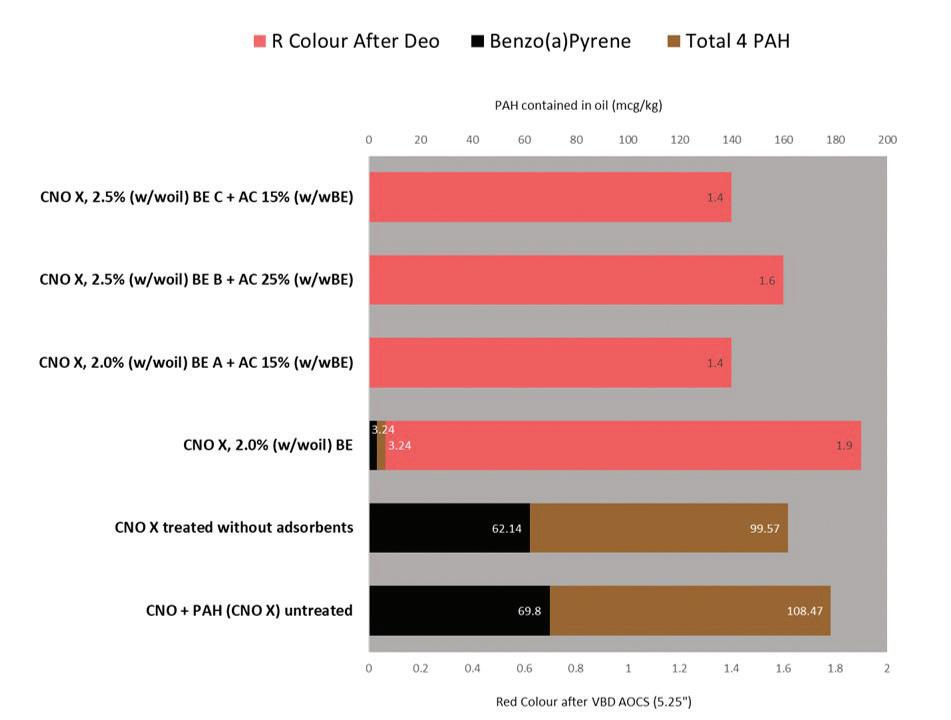
Iodine value
Saponification value
Unsaponifiables, % by mass, maxiumum g/kg
Reichert value
Polenske value contaminants in coconut oil products intended for direct human consumption, or for use as an ingredient in food.
For example, EU regulation No 835/2011 addresses PAH content in coconut oil intended for direct human consumption or for use as an ingredient in food and it defines the maximum limits as: 2.0 mcg/kg for benzo(a)pyrene; and 20.0 mcg/kg for total benzo(a)pyrene, benz(a)anthracene, benzo(b)fluoranthene and chrysene (PAH4).
Polycyclic aromatic hydrocarbons (PAHs) are chemical compounds comprised of carbon and hydrogen molecules in a cyclic arrangement. PAHs are associated with risks to human health, especially carcinogenesis. Contamination with PAHs can be caused by:
• Environmental pollution of the vegetable raw material
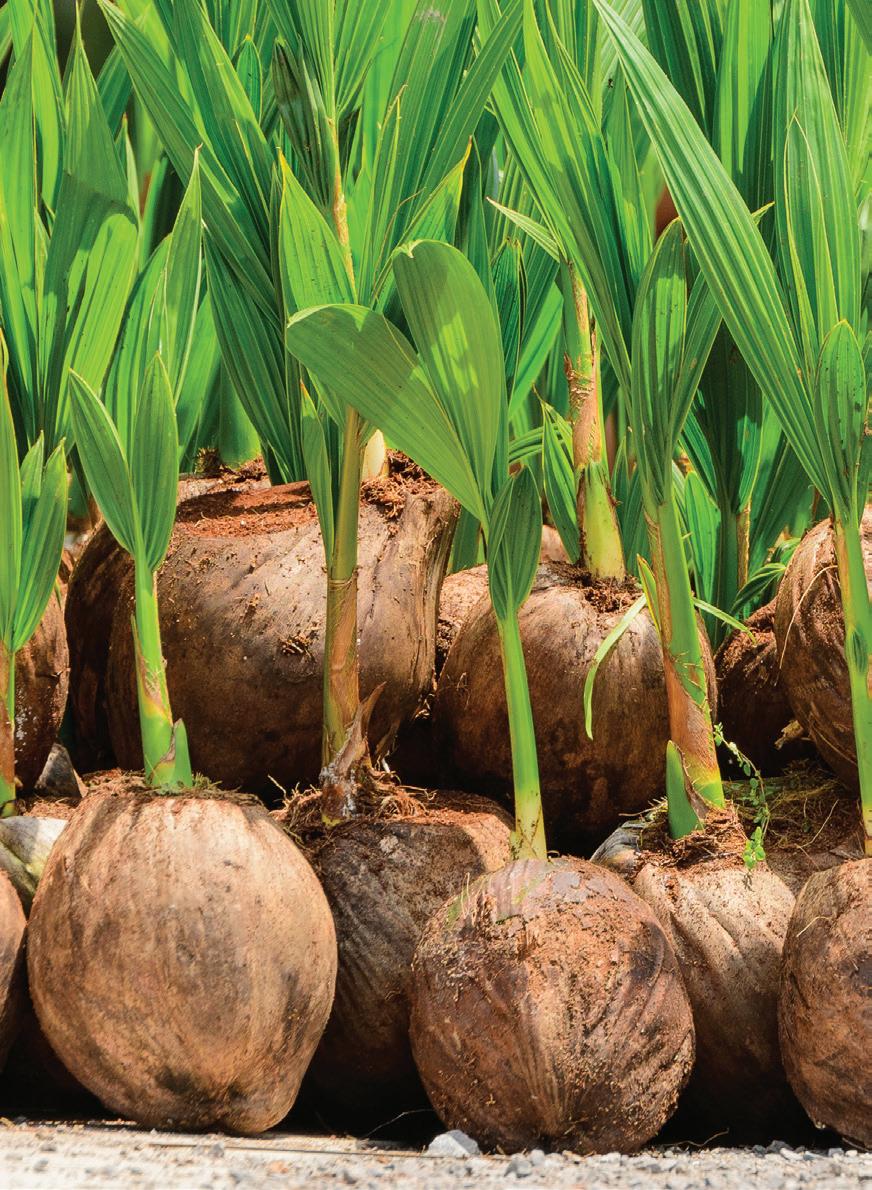
• Unfavourable seed drying (particularly through combustion gases)
• Extraction with solvents
• Burning of soil
• Packaging material
• Mineral oil residues
• Contact with contaminated water or soil
Impurity removal
Each step in the refining process of coconut oil is intended to remove specific impurities. During neutralisation, most impurities are reduced, hence the load for subsequent steps is lighter. Next, degumming removes phospholipids (gums), while the bleaching stage removes most of the residual contaminants to safe levels. The final deodorisation step eliminates any remaining volatile impurities and odours.
The bleaching process plays an important role in “perfecting” impurity removal following these refinement steps. In this stage, bleaching earth is used to remove colour bodies, peroxides, soap, remaining gums, chlorophyll, carotene, water and other impurities, such as PAH compounds.
Typically, activated carbon is also added during the bleaching process to remove PAHs – particularly heavy PAHs, such as benzo(a)pyrene – and to improve the colour of refined coconut oil.
However, it is important that the interplay between bleaching earth and activated carbon are optimised to ensure efficient impurity removal and colour enhancement (see Figure 3, left, previous page) while optimising the total cost of ownership.
With bleaching earth and activated carbon, quality is particularly critical. Not only does it impact the physiochemical properties of the refined coconut oil, but also its appearance, which is usually measured against the Lovibond colour scale.
Moreover, the dosages of activated carbon and bleaching earth should be in an optimum ratio to achieve the desired performance.
An optimum blend ratio is implemented in premium-grade bleaching earths, such as Clariant’s Tonsil Optimum 231S, where the correct dosage ratio of activated carbon relative to bleaching earth has a considerable impact on coconut oil colour. It should be noted that increased activated carbon content is not necessarily better (see Figure 4, below left, previous page).
Conclusion
Coconut oil is a highly valuable ingredient in the food and oleochemical industries, thanks to its unique physiochemical properties and lipid profile.
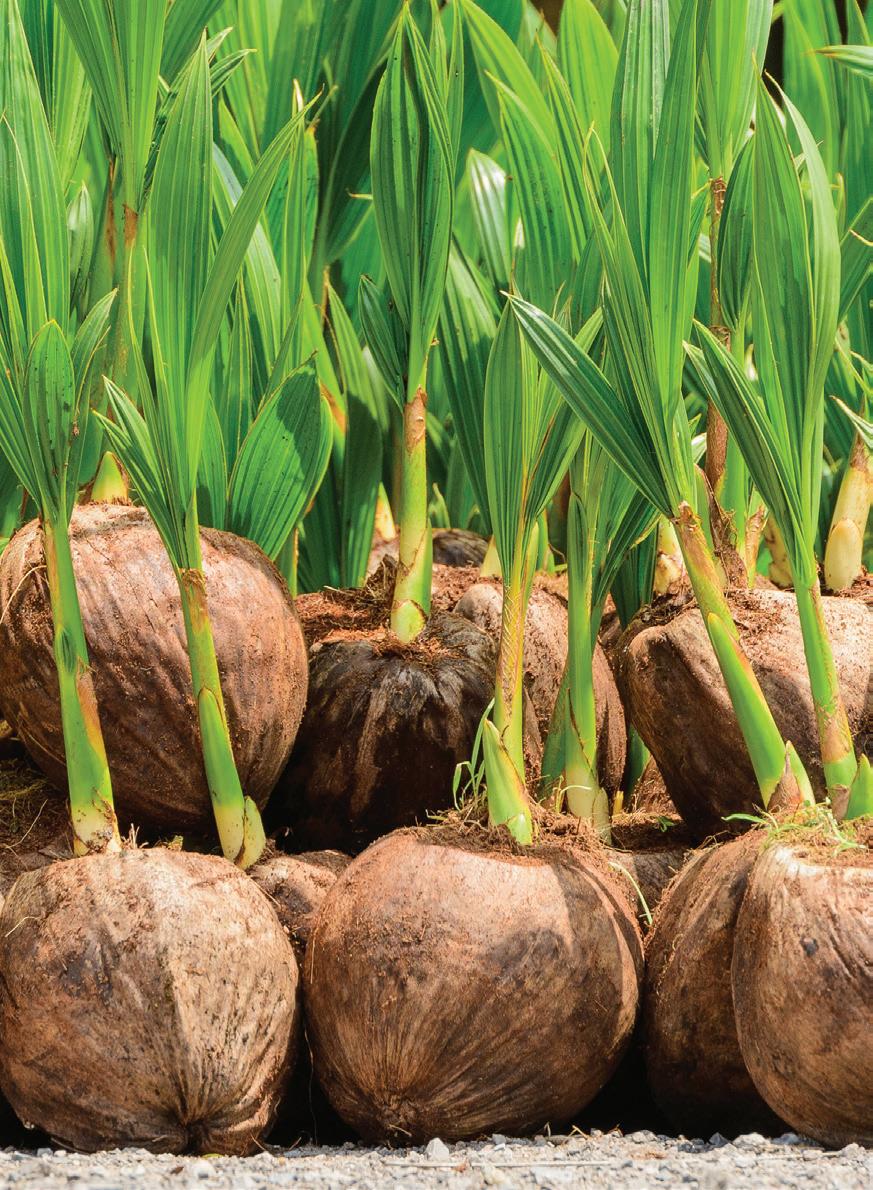
However, refining coconut oil can be challenging and is greatly influenced by how the crude oil is sourced.
To fulfil all safety and specification requirements for refined coconut oil, high- quality bleaching agents are needed for an effective and efficient bleaching process. The most common bleaching agents used to refine coconut oil are bleaching earth and activated carbon.
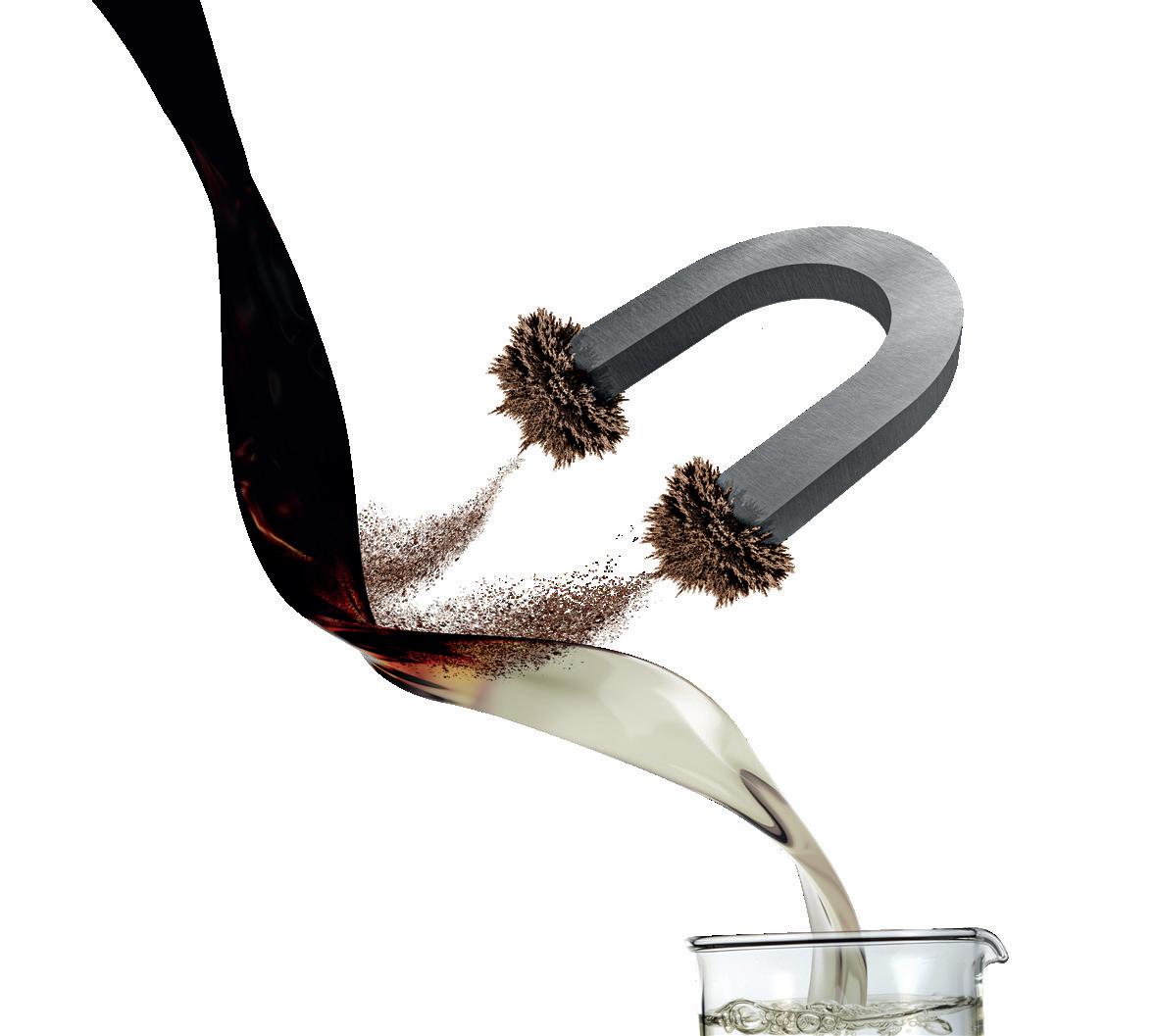
High-quality activated carbon is critical for removing PAH impurities, while oil colour can be significantly enhanced and lightened using the right bleaching earth and process. Furthermore, the bleaching agents should be combined in an optimum ratio in order to achieve the desired oil profile. ●