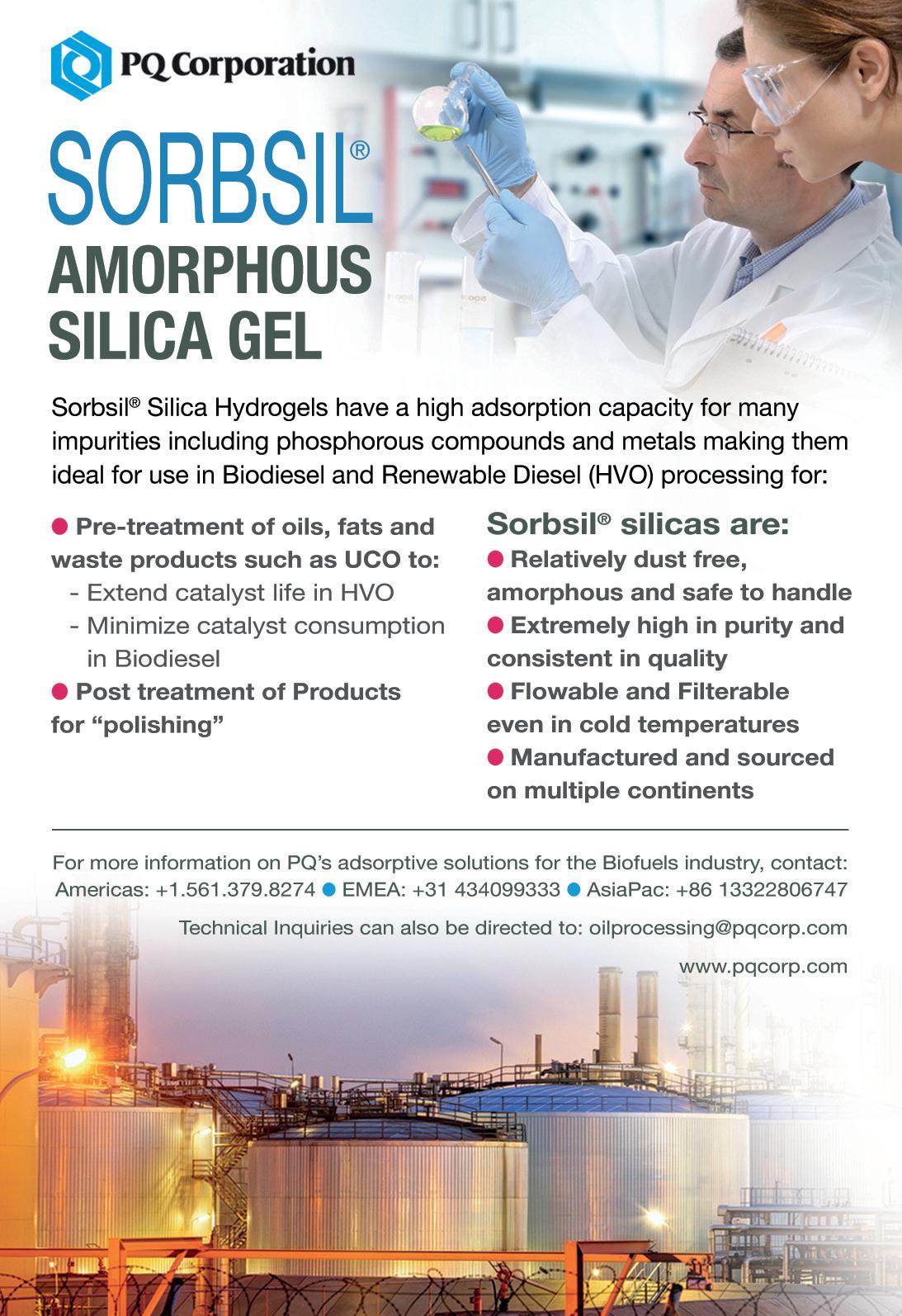
8 minute read
BLEACHING EARTHS
bleaching earths may cause is the double bond shift. This reaction may, for example, turn anti-inflammatory omega-3 oil into pro-inflammatory omega-6 oil.
“In nature, an oil that has three double bonds will have them separated by two single bonds. But when placed over a solid acid catalyst – such as acidactivated bleaching earth – the bonds will conjugate so that there is only one single bond between each double bond. This conjugation adversely affects the stability of the oil. An oil that would naturally take 25 days to go rancid could turn rancid in only one day,” says Howes.
So, although activated bleaching earths have a generally higher ability to absorb impurities, they are not a silver bullet for the edible oil industry. Due to their capacity to cause negative changes in oils, natural bleaching earths still have their place.
Uses of bleaching clays
In edible oil refining, bleaching earth can be used in two ways.
In the dry bleaching process – more common in Europe and Asia – the oil is heated by injecting steam into it and mixed with a bleaching clay under a vacuum to prevent oxidation. Following bleaching, the clay is removed from the oil with pressure leaf filters and gathered for post-processing.
In the wet bleaching method, water (in the form of a citric acid solution) is added to the oil after heating and before adding the bleaching earth. The added water makes it easier for the minerals to absorb metals and remove residual soaps, reducing bleaching earth consumption and oil loss. Despite its increased efficiency, wet bleaching has much higher initial costs, which limits its applicability.
In addition to vegetable oils and animal fats, bleaching earth is used to purify a wide range of other oil and fuel products.
Biodiesel and green diesel production is the second largest consumer of bleaching earths, and Bello sees this segment continuing to grow in the next five years. Biodiesel producers use bleaching earth to purify their feedstocks, which often contain phosphorous and metal contaminants.
“Bleaching earths are used to purify used cooking oil (UCO), sludge oils, acid oils and other waste oils that are utilised in the manufacture of biodiesel and renewable diesel. Thus, bleaching earth plays a part in the control of greenhouse gases,” says Howes.
Bleaching clays are also used in the final purification steps of petroleum oil refining, for products such as kerosene and jet fuel. Howes notes that they can also help recycle petroleum products. “Bleaching earths are used to recycle synthetic and mineral oils, such as engine oil. After bleaching earth treatment, the recycled oil can have a better quality than the original base oil. Many leading brands such as Mercedes and Aston Martin have approved the utilisation of recycled engine oils.” Bleaching earths are also used in many other industries including as:
• An animal feed additive to reduce the amount of fungal mycotoxins
• A moulding sand additive to increase the accuracy of metal casting in foundries
• A drilling additive in civil engineering projects
• A formation additive in paper production
• Stabilisers and aromatic removers in plastics production
• Purifiers for wastewater treatment
• Surfactants in detergent and soap production
Spent bleaching earth
Once bleach clays have been used in edible oil bleaching, they are known as spent bleaching earths (SBEs).
The global edible oil industry produces around 2.5M tonnes/year of SBE, according to the report ‘Effect of activating solution modulus on the synthesis of sustainable geopolymer binders using spent oil bleaching earths as precursor’. SBE poses various problems for industry.
According to the American Oil Chemists’ Society (AOCS), SBE can contain 30-50% of entrained oil by weight. Due to the high oil content, SBE is susceptible to spontaneous combustion as the thin film of oil spread across the clay’s high surface area oxidises rapidly, generating heat. This makes handling, transporting and reusing them a significant challenge.
The oil trapped in SBE is also a source of environmental regulatory concerns. SBE decomposes slowly, so it cannot be disposed of in landfill. Due to the risk of combustion and environmental issues, SBE is classified as hazardous waste in the EU. Yet, there is a strong incentive for oil producers to do something with SBE to mitigate some of the oil loss associated with bleaching earth use.
Sabah M. Abdelbasir et al describe some uses for SBE in their 2023 review, ‘Spent bleaching earth; recycling and utilization techniques’. SBE can be recovered and recycled by removing the entrapped oil through various methods, including pyrolysis, chemical treatments (particularly acid), solvent extraction, or a combination method. However, many of these methods are labour-intensive and not economically viable. To date, solvent extraction with methanol, acetone and hexane is the most commercially sensible method.
After SBE recovery, there are various uses for both the separated oil and bleaching clay. Neste, for example, uses oils recovered from SBE as a raw material for its NEXBTL renewable diesel. SBE can be composted with palm oil milling and other agricultural residues to create a fertiliser that can positively impact soil quality. The de-oiled SBE may also be suitable for re-use in processes such as wastewater purification.
AOCS has experimented with a process to add salt to SBE to eliminate the risk of spontaneous combustion. A salt content as low as 35% can reduce the risk, but for optimal results, a salt content of 45% is recommended. The salt/SBE mixture can then be compressed into a salt-lick brick for cattle and other livestock.
Other experimental uses for SBE include compressing it into bricks for construction utilising polymerisation under high heat. The polymerised oil remnants form bonds that hold the bricks together. It should be noted, however, that many such theoretical SBE applications have not been applied commercially and may not be economically viable.
Relationship to other adsorbents
Bleaching earths are popular adsorbents in edible oil refining and other industries, but they are not the only options refiners have available to them. Many alternatives exist, although Bello highlights that these products are not rivals.
“Porous materials like synthetic hydrogels, activated carbon, activated cellulose and other products do not compete against bleaching earths but they complement their application. These mesoporous and microporous materials are effective on certain types of impurities but, in the end, bleaching earths are the adsorbents to remove 90% of the contaminants,” he says.
Silica, or silicon dioxide, is one product that works in conjunction with bleaching clays. In fact, acid-activated bleaching earths form silica structures on their surfaces. “Acid-activation of bentonites removes a part of the octahedral alumina layer, leaving the two silica layers in place.
This enriches the silica species that are beneficial to the absorption of certain impurities,” Howes explains.
In addition to naturally-occurring silicas, there are synthetic silicas, such as silica hydrogel mentioned by Bello. This material is produced by allowing a sodium silicate solution – also called water glass – to react with an acid, according to the AOCS Lipid Library.
The acid destabilises the water glass and forces the silicate polymers to form colloidal silica particles known as silica hydrosol. The product is then washed to remove excess acid and salt by-products and left to age so it develops the required pore structure.
After milling, the silica hydrogel is ready for use in edible oil or chemical refining, biodiesel production and the oleochemical industry. Silica hydrogel can have triple the surface area and pore volume of bleaching clays, which can make it an extremely efficient adsorbent.
Activated carbon (or activated charcoal) is produced from carbonaceous sources like coal, coconuts, peat or wood. The carbonaceous raw materials are activated using chemical or physical processes to remove internal carbon atoms and create a porous microstructure that can absorb impurities.
In the single-step chemical process, an activating agent such as an alkali is used to dehydrate the carbon and cause pyrolytic decomposition, which enhances the porous structure.
In the two-step physical process, the raw material is first carbonised in an inert atmosphere and then activated with a gas like CO2, steam, or air. Chemically-activated carbon must be washed before use, so it produces wastewater, but it is also faster and produces a higher yield of carbon.
By mixing bleaching clays, silicas and activated carbon, adsorbent producers can create products that are ideally suitable for their intended applications. Each material has its own function, benefits, and cost-effectiveness, which means combining them can help increase the adsorbent product’s effectiveness and value. For example, roughly 70% of Natural Bleach’s bleaching earth products contain activated carbons, says Howes.
Challenges
Although bleaching earths are a vital part of many industries and their supplies are not projected to run out any time soon, bleaching earth producers nonetheless face challenges in their operations. The largest on the horizon is developing new products to address constantly increasing regulatory and oil quality demands.
Legislative controls on the levels of various impurities in refined edible oils have tightened. As most of the issues surrounding these impurities must be resolved at the bleaching stage, it has largely fallen on bleaching earth producers to address them. For example, producers have had to formulate their bleaching earths to reduce and/ or remove polyaromatic hydrocarbons (PAHs), dioxin, pesticides, polychlorinated biphenyls (PCBs), 3-monochloropropane diol (3-MCPD) and glycidyl esters (GEs).
This is where the mixing of bleaching clays and other adsorbents comes in. For instance, Natural Bleach was the first to introduce bleaching earths blended with activated carbon for everyday use in edible oil refining.
“Currently, the major challenge is to mitigate mineral oil saturated hydrocarbons (MOSH) and mineral oil aromatic hydrocarbons (MOAH),” says Howes. Producers, including Natural Bleach, are working on this. “We are in the process of developing a special bleaching earth that could remove 40% of the MOSH and MOAH present in edible oils going into the bleacher.”
Bello adds that while developing new solutions for new needs, bleaching earth producers must continuously maintain a consistently high product quality and competitive cost. “All premium companies have to deal with maintaining good quality. Part of that is helping customers and end users select the right product for their process and optimise usage. We invest a lot of resources in educating them on how to minimise usage, cost and environmental impacts,” he says.
The environmental question
The environmental impacts Bello mentions are another challenge facing bleaching earth producers. The public is increasingly aware of environmental issues and the demand for eco-friendly products is constantly growing. Bleaching clays must be mined from the earth, and mining has not generally been viewed favourably in environmental terms. Additionally, SBE poses its own environmental concerns in terms of recycling and reuse.
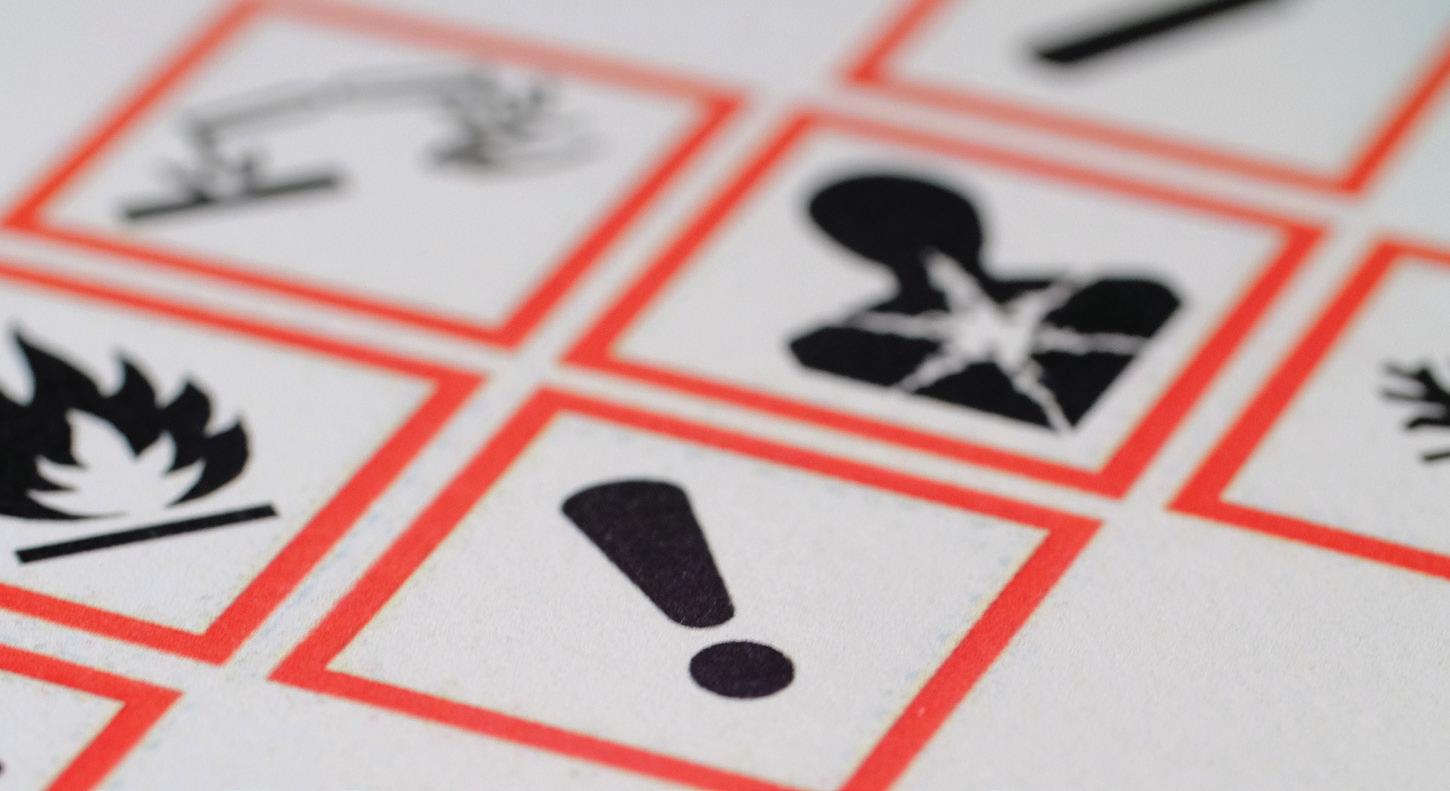
As an example of challenges posed by environmental issues, the Wyoming Division of Environmental Quality is currently investigating and conducting public hearings on a proposed Black Hills Bentonite mine in the state.
The investigation aims to confirm whether the mine, set to produce 25,000 tonnes/year of bentonite, will be able to comply with Wyoming’s air quality and pollution standards and regulations. Feeding into the concerns are whistleblower reports from 2019 that accused Black Hills Bentonite of various environmental violations, such as failing to protect wildlife and improperly handling extracted topsoil.
Yet, properly-handled topsoil removal and the bleaching clay mining process can actually benefit the environment. The key here is re-cultivation and reclamation.
The process includes removing the topsoil and separating a portion called the overburden, explains Howes. Sand and rock overburden can be used for projects such as road construction. After clay mining, the remaining hole could be lined with a geotextile membrane and used to dump approved domestic and industrial waste. Afterward, the fertile topsoil can be restored.
Clariant notes that the re-cultivated land can even be used as farmland. If, for some reason, the area cannot be re-cultivated, it could be flooded and used for water storage or recreational watersports.
To mitigate negative environmental effects and maintain regulatory compliance, leading producers are constantly evolving and developing environmentally-responsible mining practices.
However, Bello notes that bleaching earth producers cannot complete the task alone. “Addressing environmental concerns associated with bleaching clay mining – or any other ore deposit –requires a collaborative effort between mining companies, government agencies, and local stakeholders to promote responsible and sustainable mining practices,” he states.