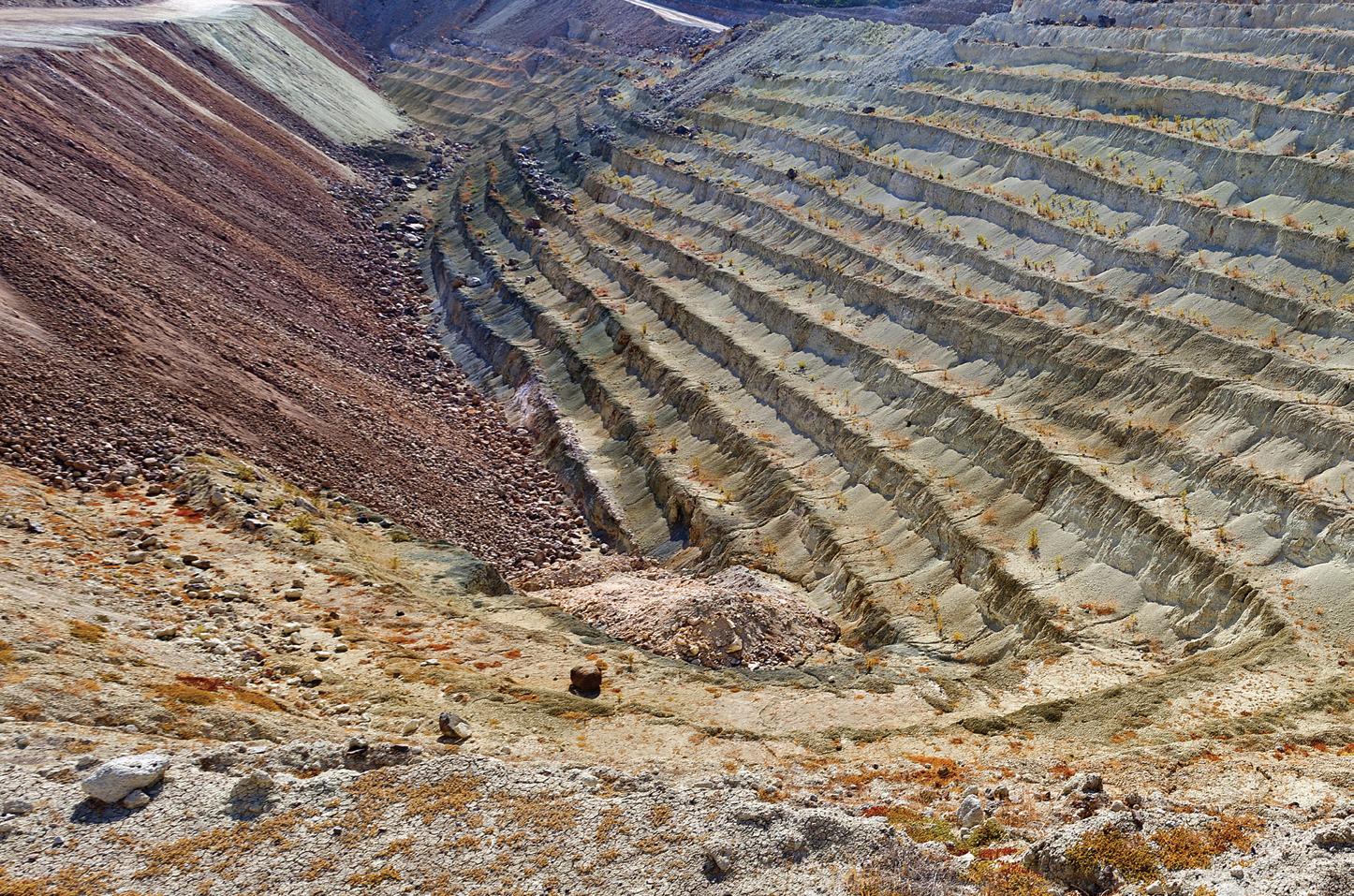
3 minute read
BLEACHING EARTHS
Processing of bleaching earths
Due to bleaching clays’ plentiful supplies around the world, bleaching earth producers often operate multiple mines in various regions. Clariant, for example, operates 60 bentonite mines.
“Prior to any mining activity, a core drilling campaign has to be performed on the mine deposit. This information will map out the usable layer configuration across the whole area and will facilitate selective mining activities. After the mineral is extracted, it is formed into big stockpiles to guarantee the homogeneity of the raw clay,” Bello says.
Once their quality is verified, the clays go to a processing facility. After reinspection, the bleaching clays become either natural or activated bleaching earth.
Natural bleaching earths, also called Fuller’s earth, undergo minimal processing after mining. Impurities such as stones are removed and the material is dried and milled to a specific particle size, depending on the product. Natural bleaching earth has been used for a long time and its production is a very low-cost process.
Activated bleaching earths, on the other hand, are subjected to an acid-activation process, also called acid-leaching or acid-washing. The process increases their acidity, as well as their absorptive capabilities. Acid activation can be carried out using either the slurry method or the granular method. Each method is suitable only for certain types of clays.
The slurry method involves submerging the raw, milled bleaching clay in water (called mother liquor), and the two are mixed into a slurry. Producers add sulphuric acid to the water and heat it to either up to
105°C for atmospheric digestion or up to 160°C for pressure digestion.
After the required period of activation, the slurry is quenched with water. The acid-activated clay is separated from the mother liquor and washed to remove excess acid and acidic salts by filtering it with plate-and-frame filter presses or by sedimentation, followed by filtration.
“The acid-activated filter cake is then sent to the drying and milling system to produce a free-flowing powder of the required moisture content – usually lower than 15%. The mother liquor may be sent to an effluent treatment plant or utilised to manufacture by-products,” Howes explains.
In the granular method, the natural bleaching clay is milled into small pellets, often around 6mm in diameter. These granules are placed in an open reactor with a porous lower membrane. This membrane allows the mother liquor to pass through while keeping the pellets in place. While submerged in the liquor, the producer adds acid into the reactor, which is recycled externally and heated to roughly 85°C. Howes notes that the granular process requires a longer activation period than the slurry method.
After activation is complete, the mother liquor is drained through the membrane and the clay undergoes washing, either with water or diluted acid.
The reactor is then drained for the final time and the clay granules are removed through a small hatch or door at the lower part of the reactor. Removing the clay from the reactor often requires additional labour as all the granules rarely flow out freely. After the clay has been removed, the holes of the bottom membrane require piercing to ensure they are not clogged for the next processing batch. As such, the granular method is more workintensive than the slurry process. Finally, the activated clay granules are dried and milled for distribution.
Natural vs activated
Natural and acid-activated bleaching earths not only differ in their production methods, but in their mode of action as well.
Natural bleaching earth removes impurities by absorbing them wholly physically, without altering the edible oil or other products, Howes says. The only exception to this is the natural bleaching earths’ greater ion exchange capacity, which allows them to remove iron and other undesirable metals.
Natural bleaching earths have a lower absorptive capacity than activated ones, although their lower acidity makes them more suitable for certain applications. All in all, however, natural bleaching earth makes up a single-digit percentage of global consumption, notes Bello.
Surface-modified acid-activated bleaching earth has a structure that is very similar to natural bleaching earth. However, the acid activation process increases their surface area, giving them higher absorptive ability. This is partially due to new silica surfaces that form during activation. At the same time, however, their ion exchange capacity falls as the sites causing the charge in the clay layer are removed during the bleaching process.
Additionally, the activation process turns the clays into solid acid catalysts, which enables them to crack and otherwise alter the structure of various pigments, making them invisible to the human eye.
“This bleaching earth will also easily convert primary oxidation products, such as hydroperoxides measured by peroxide value (PV), to secondary oxidation products, like aldehydes and ketones measured by anisidine value (AV),” explains Howes. “The PV will fall as far as zero, but the AV will increase. Consequently, the odour of the oil will become worse due to the formation of aldehydes and ketones. These odours need to be removed by deodorisation or steam refining under high vacuum.”
The activation process also causes other undesirable modifications. Activated bleaching earth can cause cis- to transisomerisation — in other words, the formation of trans acids. Not only are trans isomers harmful to health, they also make the oil look cloudy and less appealing.
Another catalytic reaction that activated