
7 minute read
La stampa 3D di Formlabs per componenti e attrezzature per l’automotive
La stampa 3D di Formlabs per componenti e attrezzature per l’automotiveautomotiveMateriali e soluzioni per le auto del futuro
FFormlabs sta ampliando l’accesso alla fabbricazione digitale, per rendere la stampa 3D alla portata di tutti. Con sede a Somerville, Massachusetts, e uffici in Germania, Giappone, Cina, Singapore, Ungheria e Carolina del Nord, Francia e Ohio, Formlabs è il fornitore di stampanti 3D professionali scelto da ingegneri, designer, produttori e dirigenti di tutto il mondo. Grazie ai prodotti e alle soluzioni Formlabs, diverse aziende leader nello sviluppo di prodotti automobilistici leggeri in plastica e materiali compositi e famosi studi di design per auto, sviluppano prodotti per la realizzazione di prototipi funzionali, dalla fase di progettazione concettuale per la verifica delle geometrie, fino alla fase di progettazione dettagliata e creano le concept car di domani. Come nel caso di IGESTEK, un’azienda spagnola con sede a Bilbao, e di Vital Auto, uno studio di design industriale situato nel cuore del settore automobilistico del Regno Unito con una notevole esperienza nel design di auto che annovera fra i suoi clienti alcuni dei più importanti produttori di automobili, come Volvo, Nissan, Lotus, McLaren, Geely, TATA.
Iterazioni di un componente automobilistico progettato con il metodo generativo sulla Form 3L
Il team di IGESTEK sviluppa tecniche di lavorazione ibride e le integra tra loro per produrre componenti in materiali compositi, che vengono successivamente implementate da fornitori di primo livello del settore automobilistico e produttori di parti originali per realizzare parti per auto e moto di alta gamma. L’azienda utilizza la stampa 3D dall’inizio alla fine del processo di sviluppo dei prodotti, dalla fase di progettazione concettuale per la verifica delle geometrie, fino alla fase di progettazione dettagliata per la realizzazione di prototipi funzionali. Inoltre, la stampa 3D viene impiegata per la creazione rapida di attrezzature, come inserti per stampi a iniezione in plastica o attrezzature per la termoformatura di materiali compositi. Uno dei progetti più innovativi di IGESTEK è un supporto per ammortizzatori (Top Mount). Questi componenti fanno parte del sistema di sospensione di un’automobile e aiutano a ridurre le vibrazioni prodotte dal movimento del veicolo per migliorare il comfort dei passeggeri. Il supporto per ammortizzatori è stato sviluppato con il software di design generativo Fusion 360 di Autodesk, che ha fornito varie soluzioni in base a una serie limitata di requisiti. Successivamente, il team ha stampato in-house i design più promettenti usando la stampante 3D stereolitografica (SLA) Form 3L, convalidando così la geometria e sfruttando il grande volume di stampa per realizzare fino a tre diverse iterazioni contemporaneamente. La stampa 3D SLA ha permesso di realizzare le geometrie complesse ottenute attraverso il design generativo e di convalidare i processi cinematici e di assemblaggio utilizzando prototipi funzionali, senza dover investire in attrezzature costose. Il processo di ricerca e sviluppo ha portato all’elaborazione di un’architettura realizzata in diversi materiali, che combina la stampa 3D in metallo, basata su geometrie generative, con materiali compositi più leggeri, per offrire le migliori prestazioni possibili a fronte di una riduzione del peso pari al 40% rispetto alle soluzioni attualmente sul mercato.
Utilizzo di diversi materiali di stampa 3D SLA per creare uno strumento per la termoformatura
Oltre che per la prototipazione, il team di IGESTEK, utilizza la stampa 3D anche per la creazione rapida di attrezzature destinate alla produzione di parti in materiali compositi, come la termoformatura della fibra di carbonio attraverso laminatura pre-preg. Nerea Romero, responsabile dell’innovazione di IGESTEK ha dichiarato: “Le resine di Formlabs, come la Rigid 10K Resin e la High Temp Resin, sono davvero utili nel settore ingegneristico. Solitamente impieghiamo tecnologie che riguardano la termoformatura a compressione di materiali compositi. Gli strumenti che verranno inseriti nelle presse devono essere rigidi e resistenti al calore, perché saranno soggetti a pressione [per formare le parti in materiali compositi] e ad alte temperature, di solito intorno ai 180-200 gradi”. Un esempio recente è uno strumento sviluppato dal team per produrre tubi in materiale composito. La Rigid 10K Resin è stata impiegata per produrre i pilastri di supporto del componente, che richiedevano un’elevata rigidità, la High Temp Resin per produrre i morsetti, che richiedevano resistenza alle alte temperature e alla pressione dell’aria, e la Draft Resin per produrre in modo rapido i tappi terminali dello strumento. “[Senza la stampa 3D], avremmo dovuto utilizzare il metallo e avremmo impiegato molto più tempo e denaro per la produzione”, ha affermato Romero.
Produzione di design complessi con diversi materiali con la Form 3L
Lo studio Vital Auto crea prototipi estremamente fedeli e concept car, eseguendo rapidamente diverse iterazioni utilizzando una serie di strumenti avanzati, tra cui una vasta flotta di stampanti Formlabs Form 3L e Fuse 1. Il team Vital sviluppa le auto partendo da un foglio bianco, progetta il telaio, tutti gli elementi interni ed esterni, aperture e chiusure, e le parti interattive. Un progetto può durare da tre a dodici mesi, impegnando da cinque a trenta persone per un singolo concept. In questo lasso di tempo, un’auto da esposizione viene sottoposta a una dozzina di iterazioni del design di base e, all’interno di queste, si susseguono ulteriori iterazioni di
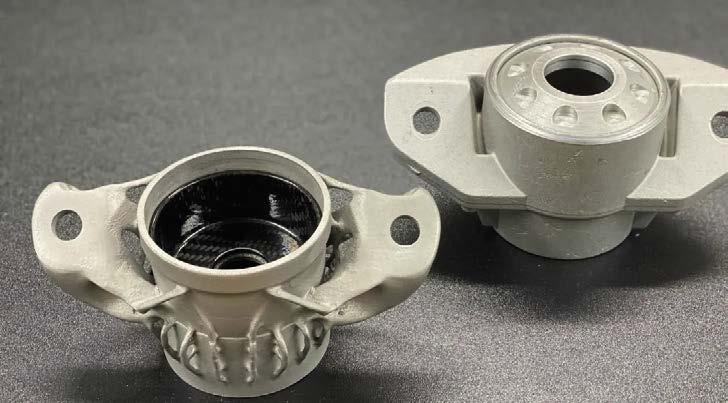
I prodotti Formlabs
I prodotti Formlabs includono le stampanti Form 3+, Form 3B+, Form 3L e Form 3BL, basate sulla stampa 3D Low Force Stereolithography (LFS)™, le soluzioni di post-elaborazione Form Wash, Form Cure, Form Wash le stampanti 3D SLS Fuse 1 e Fuse 1+ 30W e il sistema per il recupero della polvere Fuse Sift. Inoltre, Formlabs sviluppa una gamma di materiali ad alte prestazioni, che consentono di continuare a superare i limiti della stampa 3D, nonché software all’avanguardia per la stampa 3D, come il PreForm.
componenti più piccoli, fino a quando il design non soddisfa pienamente le aspettative del cliente. Per produrre parti personalizzate necessarie per concept una tantum, Vital Auto ha introdotto nel suo processo di produzione la stampa 3D, non solo per ridurne i costi, ma anche per offrire ai clienti maggiore diversità per i loro design e le loro idee. Col tempo hanno predisposto un intero reparto per la stampa 3D, che comprende dieci stampanti FDM di grande formato, tre stampanti SLA Form 3L di Formlabs, sempre di grande formato, e cinque stampanti SLS Fuse 1. Tutte le stampanti hanno funzionato al 100%, 24 ore su 24, 7 giorni su 7, praticamente dal primo giorno e vengono utilizzate per tutte le aree dei concept e design. In particolare, le Fuse 1 vengono generalmente usate per le parti che si basano sulla produzione e le Form 3L per le parti basate sul concept. “Utilizziamo le Form 3L per tutte le finiture superficiali di classe A, come ad esempio, in un contesto automobilistico, un interno in cui siano presenti parti che non vengono rifinite con pelle o Alcantara o, in generale, con un tessuto. I materiali di Formlabs producono una finitura bella e liscia con cui possono lavorare i verniciatori. In questo modo, possiamo usare le parti appena stampate direttamente su un veicolo”, ha detto Anthony Barnicott, ingegnere di progettazione, responsabile della produzione additiva, aggiungendo “Quello che mi interessa maggiormente degli apparecchi Form 3L è la loro versatilità, la capacità di fare un cambio di materiale in meno di cinque minuti. La variabilità dei materiali, da quelli morbidi e flessibili a quelli rigidi, per noi non ha prezzo”. Il team usa le Form 3L con molteplici materiali per una vasta gamma di applicazioni, come ad esempio, pacchetti di interruttori e guarnizioni per le portiere; mentre utilizza le Fuse 1 soprattutto per le parti meccaniche, come le cerniere, gli interni delle maniglie e gli interni delle portiere, e per le applicazioni strutturali. Le parti si possono utilizzare da subito, sin dopo la stampa, con rifiniture minime.
Concept interattivo per una supercar
La stampa 3D ha inoltre consentito al team Vital Auto di combinare i materiali SLA con quelli SLS per realizzare diverse iterazioni di design in un progetto specifico. Questo metodo consente di produrre rapidamente più iterazioni, associando entrambi i processi, utilizzandoli per le loro proprietà specifiche, per ottenere un design finale. Può trattarsi di qualsiasi cosa, dalle parti meccaniche a quelle trasparenti, per verificarne la qualità ottica e la resa. La stampa 3D non solo aiuta il team a creare prodotti migliori più velocemente, ma anche ad aumentare gli ordini. Molti dei clienti si rivolgono a loro perché vogliono avere accesso alle ultime tecnologie e vogliono che i loro componenti vengano realizzati con materiali all’avanguardia.