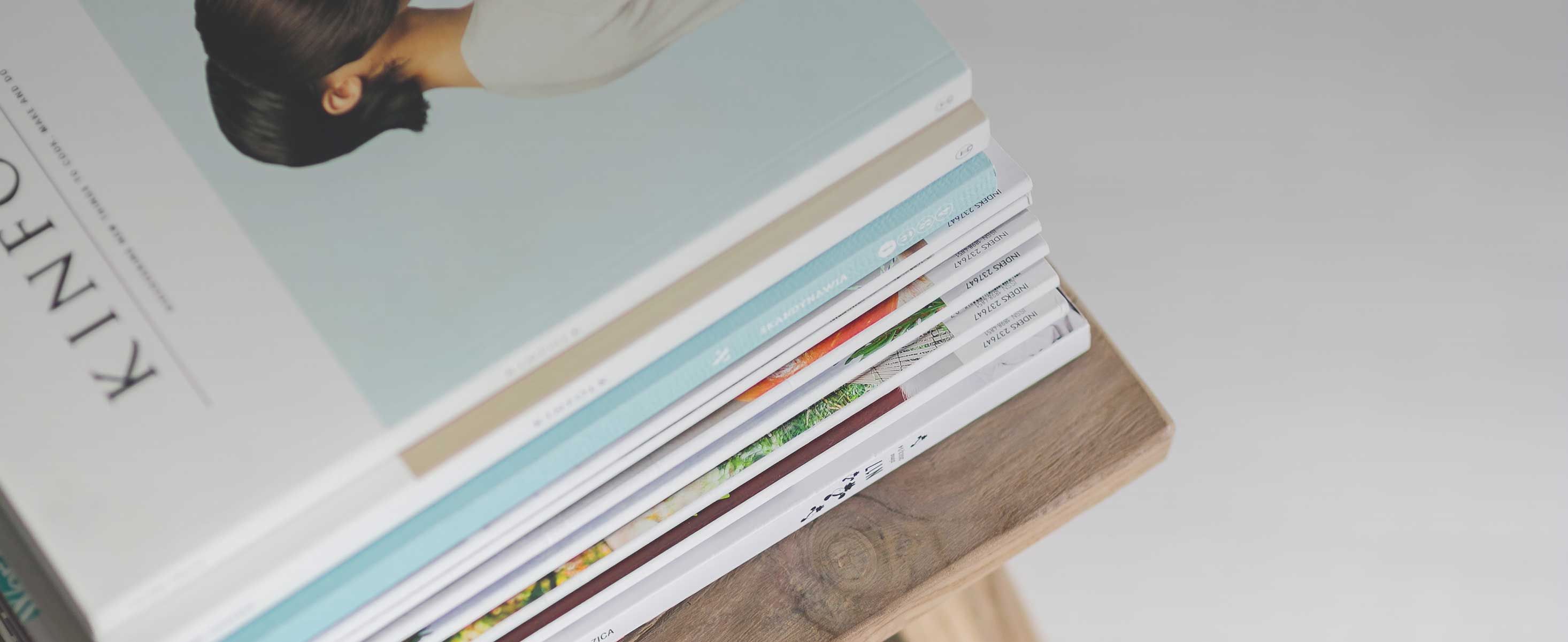
3 minute read
MATERIALI, TRATTAMENTI E FINITURE PER LA STAMPA 3D
risulti identico, ogni volta, eliminano i “rallentamenti” del postprinting manuale, combinando combustibili eco-sostenibili con l’uso di software e hardware proprietari, per portare a termine una rimozione dei supporti automatizzata e intelligente.
La rimozione dei supporti non è l’unica esigenza alla quale provvedere. Infatti, per alcuni settori particolarmente esigenti in termini di qualità dei componenti, sicurezza e prestazioni, come ad esempio quello sanitario, più tipicamente quelli medico e dentale, il problema maggiore risiede nella difficoltà di ottenere finiture lisce nei canali interni del pezzo, che rimangono quindi esposti alla possibilità di intrappolare potenzialmente batteri e contaminare il processo produttivo. Lo stesso dicasi per il settore automobilistico che richiede il raggiungimento di standard molto elevati per le parti stampate in 3D.
Come già detto, quindi, le caratteristiche delle superfici prodotte, in determinate condizioni, possono influenzare le proprietà finali dei manufatti. Questo vale anche nel settore degli stampi, per i quali le opportunità di creare canali di raffreddamento con geometria complessa (conformal cooling) fornita dalla stampa 3D rappresenta un valore molto importante e innovativo per un miglioramento delle loro performance, e le finiture sono determinanti. Le ricerche attualmente in corso hanno come scopo proprio il conseguimento di una soluzione al problema del trattamento superficiale di configurazioni complesse e il condizionamento delle superfici interne di tali canali. La libertà nel design del pezzo ed in particolare la facilità di creare camere, cavità e canali interni non altrimenti ottenibili, resa possibile dalle tecnologie additive, rappresenta indubbiamente uno degli aspetti più interessanti ed apporta numerosi vantaggi alla produzione, ma l’elevata rugosità dei componenti prodotti, che per alcuni di essi costituisce di per sé un requisito voluto, rimane, nella maggior parte dei casi, ancora uno dei limiti principali e un elemento penalizzante, specialmente all’interno dei canali e delle camere. L’industria della manifattura additiva è quindi alla ricerca di tecniche e processi di levigatura delle superfici che permettano di raggiungere livelli di rugosità ottimali.
Una possibile soluzione viene fornita dal sistema di postproduzione automatizzato di AMT chiamato Vapor Smoothing, che fornisce una finitura superficiale liscia e sigillata per le parti stampate in 3D. Questo metodo di post-produzione, di cui si fa cenno in una delle soluzioni di seguito presentate, permette alle parti di superare diversi test che dimostrano che esse soddisfano gli standard e le normative per le applicazioni industriali in numerosi campi. Il metodo di Vapor Smoothing consiste nell’introduzione in sospensione di una serie di lotti di parti in una camera di lavorazione sigillata, e nella successiva immissione sotto forma di vapore in un sistema a circuito chiuso di una miscela di solventi proprietaria. Il vapore, entrando in contatto con le parti, le sigilla eliminandone le irregolarità superficiali. Sigillando completamente la superficie ed eliminando le possibili crepe, il processo di Vapor Smoothing comporta un aumento dell’allungamento a rottura del pezzo senza perdita di resistenza nella trazione finale.
Questo processo può essere utilizzato per ottenere la rugosità superficiale desiderata nelle parti create utilizzando tecnologie di produzione additiva come SLS, Multi Jet Fusion (MJF), Selective Absorption Fusion (SAF) e Fused Deposition Modeling (FDM). In termini di materiali, le soluzioni di AMT sono compatibili con un’ampia gamma di polimeri, tra cui poliammidi (PA12, PA11 e PA6), materiali flessibili come TPU e materiali più standard come l’ABS, tra gli altri.
La peculiarità di questo processo consiste nella possibilità di levigare geometrie complesse senza influire sulle proprietà meccaniche del pezzo e nella controllabilità e ripetibilità. Nel settore del medicale, i vantaggi del Vapor Smoothing risiedono soprattutto nell’impedimento dell’accumulo di batteri e nella maggiore sterilizzazione del pezzo oltre che nell’importanza che la levigatura della superficie assume per le parti soggette a contatto con la pelle, come protesi, tamponi nasali, applicazioni dentali, ecc. il metodo consente anche di sigillare le superfici contro l’ingresso di liquidi e gas.
Tornando tecniche di post-processing, quindi, per finitura superficiale si intende un processo che assicura che ogni parte soddisfi le sue specifiche, come la rugosità media desiderata e la coerenza dimensionale, mantenendo intatti i dettagli fini della parte stampata in 3D, mentre con la colorazione, detta anche tintura, si fa riferimento al terzo passo della post-elaborazione delle parti stampate. Le parti bianche sono quelle più adatte alla colorazione.
Per molti versi, il post-trattamento rappresenta ancora una sfida. La finitura di componenti ottenuti da Additive Manufacturing richiede tuttavia un’analisi dell’intero flusso di processo per poter garantire la qualità superficiale desiderata, sia che avvenga tramite operazioni di rimozione delle strutture di supporto, che di rottura degli spigoli, di lucidatura ad alto gloss, di levigatura, raggiatura o di preparazione alla verniciatura. Già da diversi anni, alcune aziende del settore hanno messo a punto numerosi processi di levigatura, lucidatura e granigliatura sviluppati specificatamente per questo scopo: in questo modo, è possibile trattare praticamente qualunque materiale, dalla plastica al metallo, e pezzi ottenuti con le più svariate tecnologie. Il ventaglio delle opzioni disponibili spazia dall’omogeneizzazione delle superfici alla lucidatura con bassi valori di rugosità e persino ad alto gloss. I fattori da prendere in considerazione sono la tecnologia di produzione additiva impiegata, la granulometria, le tolleranze degli strati di materiale applicati e la posizione del pezzo nella camera di produzione. La finitura di massa, ad esempio, è la tecnologia di riferimento per i pezzi in plastica o metallo. A seconda della forma e dimensione dei componenti e delle loro specifiche tecniche, è possibile ottenere le finiture desiderate con un trattamento in batch o individuale. Anche se, in ogni caso, sarebbe importante prendere in considerazione il grado di finitura richiesto già a partire dalla fase di progettazione.