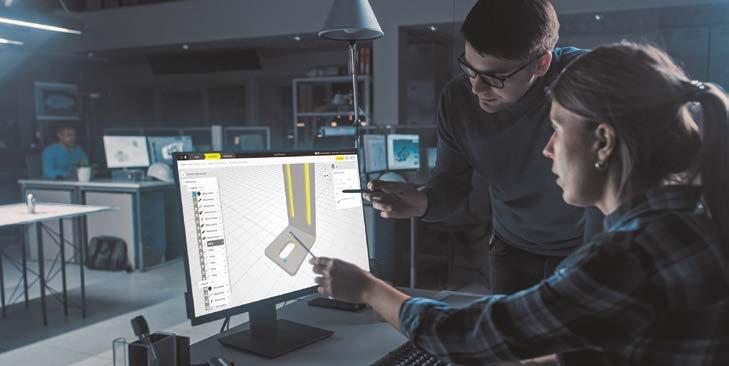
5 minute read
CORODRILL® 860 LA PUNTA IN METALLO DURO INTEGRALE PER L’INNOVAZIONE NELLA PRODUZIONE
CONCEPITA PER OPERAZIONI DI FORATURA RAPIDE E SENZA PROBLEMI, CORODRILL® 860
MASSIMIZZA LA PRODUTTIVITÀ GRAZIE ALL’ELEVATA EFFICIENZA DI TAGLIO DEL METALLO
LLa progettazione per la producibilità (DFM - Design For Manufacturability) è un processo che permette di progettare e sviluppare prodotti che possono essere realizzati in maniera più facile, efficiente ed economicamente conveniente. Per i clienti di Sandvik Coromant, questo significa ottenere un costo per componente favorevole nella lavorazione di componenti (o un buon costo per foro nelle applicazioni di foratura e maschiatura). Ognuno di questi obiettivi richiede utensili da taglio estremamente affidabili e ad elevata produttività.
Il maggior livello di globalizzazione delle catene di approvvigionamento, l’aumento della domanda di prodotti personalizzati e la mobilità elettrica, i cui componenti sono più vari e sempre più spesso realizzati in materiali tenaci come acciai debolmente legati, Inconel e alluminio, influiscono sull’evoluzione del concetto di progettazione per la producibilità.
Le soluzioni di attrezzamento avanzate possono fare la differenza nell’ambito della progettazione per la producibilità (DFM) nel passaggio dal modello CAD (Computer Aided Design) al componente, attraverso tre fasi di produzione: la fase CAD>mandrino, in cui si utilizzano modelli CAD e CAM (Computer Aided Manufacturing), compresa la simulazione di esatte repliche digitali, per preparare un’operazione di lavorazione e ottimizzare l’attrezzamento, il pezzo da lavorare e i parametri di lavorazione; la fase mandrino, ovvero l’operazione di lavorazione effettiva; la fase mandrino>componente, dove si valutano la qualità e la finitura del componente finale.
Indipendentemente dal settore, la finitura e altre caratteristiche, come l’integrità superficiale del foro, sono di primaria importanza. Una migliore qualità del foro può prevenire il guasto del componente — e dipende in larga misura dai processi di lavorazione adottati per la lavorazione o la finitura dei fori.
Il design della punta è particolarmente importante al fine di produrre fori di qualità migliore. Ecco perché le geometrie del tagliente sono in continua evoluzione: rispettare i più elevati standard di produzione e qualità del componente è fondamentale. Anche l’utilizzo di refrigerante è importante, per ridurre l’accumulo di calore nell’utensile. Ed è qui che gli specialisti di Sandvik Coromant possono rivestire un ruolo essenziale nel sostenere i clienti.
Facilità di produzione
Sandvik Coromant lavora al fianco dei clienti per raccogliere tutte le opportune informazioni sul loro progetto di lavorazione e stabilirne i requisiti.
Nella fase CAD>mandrino, gli specialisti di Sandvik Coromant possono esaminare e decodificare i processi del cliente, compresi i modelli CAD e CAM utilizzati e sviluppare un prototipo di utensile la mattina per averlo pronto al collaudo nell’area R&S nel pomeriggio. Prima dell’avvento del digitale, questo processo avrebbe richiesto lo scambio ripetuto di disegni e progetti, arrivando a durare fino a sei settimane. Oggi, avere la capacità di fornire prototipi nel giro di un giorno è rivoluzionario per Sandvik Coromant.
Maggiore durata utensile
Sandvik Coromant mette a disposizione una gamma di prodotti per sostenere i clienti nella produzione di componenti, anche quelli destinati alla mobilità elettrica. Questi includono CoroDrill® 860, una punta in metallo duro integrale concepita per operazioni di foratura rapide e prive di problemi che massimizza la produttività mediante un’elevata efficienza di taglio del metallo. L’utensile è disponibile in varie geometrie, tra cui la geometria 860-MM per materiali in acciaio inossidabile a truciolo lungo come quelli austenitici, superaustenitici, ferritici e duplex.
Poi c’è CoroDrill® 860GM, che si è dimostrata utile ai costruttori automotive nella foratura di blocchi motore, casse, flange e collettori. Oltre all’automotive e alla meccanica generale, questa punta è adatta anche a tutte le applicazioni in cui la qualità del foro è fondamentale — come spesso accade nel settore aerospaziale, Oil & Gas, nucleare e delle energie rinnovabili.
La punta 860-GM ha fornito risultati straordinari a numerosi clienti, tra cui un costruttore automotive in Corea. L’operazione del cliente di Sandvik Coromant prevedeva la realizzazione di fori passanti in un lotto di connettori per trasmissioni automotive. L’obiettivo era praticare otto fori passanti da 8.2 mm (0.32”) di diametro in ciascun componente, con una profondità di 10 mm (0.39”). In un confronto tra le due punte, la soluzione esistente è stata in grado di produrre 200 componenti, per un totale di 1600 fori, con una velocità di taglio (Vc) di 80 m/ min (3102 giri/min) e un avanzamento (Vf) di 381 mm/min. Con CoroDrill® 860-GM, invece, sono stati prodotti 2300 componenti (18400 fori) con un valore Vc di 100 m/min (3878 giri/min) e un valore Vf di 814 mm/min.
Complessivamente, CoroDrill® 860-GM ha offerto un aumento della durata utensile del 1150%, un traguardo straordinario. Questo risultato è stato accompagnato da un aumento della produttività che ha contribuito a ridurre notevolmente il costo per componente.
La maschiatura, ossia l’operazione che crea un filetto all’interno del foro, è importante almeno tanto quanto la realizzazione di fori lisci. Per questo Sandvik Coromant mette a disposizione le soluzioni CoroTap® 100, 200, 300 e 400, ognuna ottimizzata per applicazioni diverse. Per analizzare qualche esempio, CoroTap® 100 è una gamma di maschi con scanalatura diritta ottimizzata per i materiali ISO K, ISO N e ISO H a truciolo corto. CoroTap® 400, invece, è un maschio a rullare ad alta velocità che non prevede la formazione di trucioli ed è adatto alla lavorazione di fori passanti e ciechi su acciaio, acciaio inossidabile e alluminio. La scelta del cliente dipenderà dai requisiti della propria applicazione.
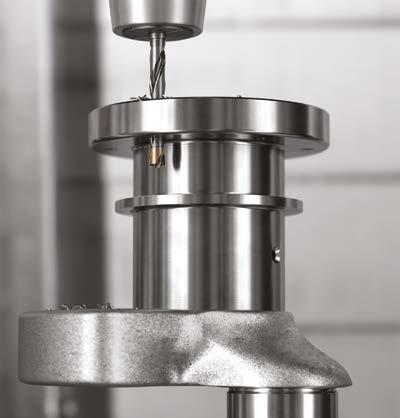
A marzo 2023, Sandvik Coromant ha presentato anche le soluzioni CoroTap® 100-N e CoroTap® 400-N, progettate per agevolare i clienti nella maschiatura dell’alluminio, un’operazione sempre più importante nei processi di produzione.
Per il momento, le prestazioni degli utensili Sandvik Coromant dimostrano che gli utensili studiati per agevolare le operazioni di foratura e filettatura su vari materiali saranno fondamentali per aiutare i costruttori a produrre componenti più leggeri, variegati e di minori dimensioni. Non solo le officine meccaniche possono progettare e sviluppare tali componenti in maniera più facile ed economicamente efficiente, ma possono garantire che la progettazione per la producibilità (DFM) continui a essere una priorità lungo l’intero processo di produzione — innovando così con efficienza.
AL CENTRO DEI NUOVI MODELLI ACCORD 500 E ACCORD 600 E DELL’UPGRADE DI MORBIDELLI M200, LA NECESSITÀ DEL CLIENTE DI RIAPPROPRIARSI DEL PROPRIO TEMPO, GUADAGNANDO IN PRODUTTIVITÀ, MANTENENDO ALTI LIVELLI DI QUALITÀ DI FINITURA
SCM cambia le “regole del gioco” nella lavorazione di porte, finestre, scale ed elementi in massello. According to wood (Secondo il legno), il claim scelto da SCM per il lancio della sua nuova gamma di centri di lavoro per il massello, esprime l’obiettivo di SCM di fornire un’ampia varietà di soluzioni tecnologiche ancora più efficienti e performanti, ma soprattutto “progettate dal legno” perché dotate di caratteristiche tecniche e prestazioni totalmente in linea con le sfide del mercato.
Al tempo stesso, According richiama ad accord: una lunga storia di successi e know-how come quella dell’omonima gamma di centri di lavoro per la fresatura e la foratura del massello di SCM, punto di riferimento per il settore da 15 anni. La stessa gamma da oggi si amplia e si rinnova in un’ottica del tutto nuova, strategica, per stare al passo con i tempi e dare giusto valore al tempo dei clienti, ottimizzando e velocizzando i loro processi produttivi, ma garantendo al contempo un’elevata qualità di finitura.
Proprio il tempo è il fattore-chiave che più ha guidato la rivoluzione dei centri di lavoro SCM. Ogni caratteristica tecnica è studiata per ridurre i tempi nelle fasi più cruciali per ogni produttore del settore: dalla programmazione al set-up della macchina, dal processo di lavorazione alla manutenzione. “Abbiamo voluto dare al cliente, che si trova ad affrontare problematiche sempre più complesse nella lavorazione del massello, una risposta da specialisti che individuasse la soluzione più puntuale per ogni specifica richiesta.
Queste nuove tecnologie semplificano notevolmente il lavoro quotidiano degli operatori, lo rendono più efficiente e consentono quindi un migliore ritorno dell’investimento”, sottolinea il Business Manager dei Centri di Lavoro di SCM Bruno Di Napoli.
Nuovi centri di lavoro accord 500/600