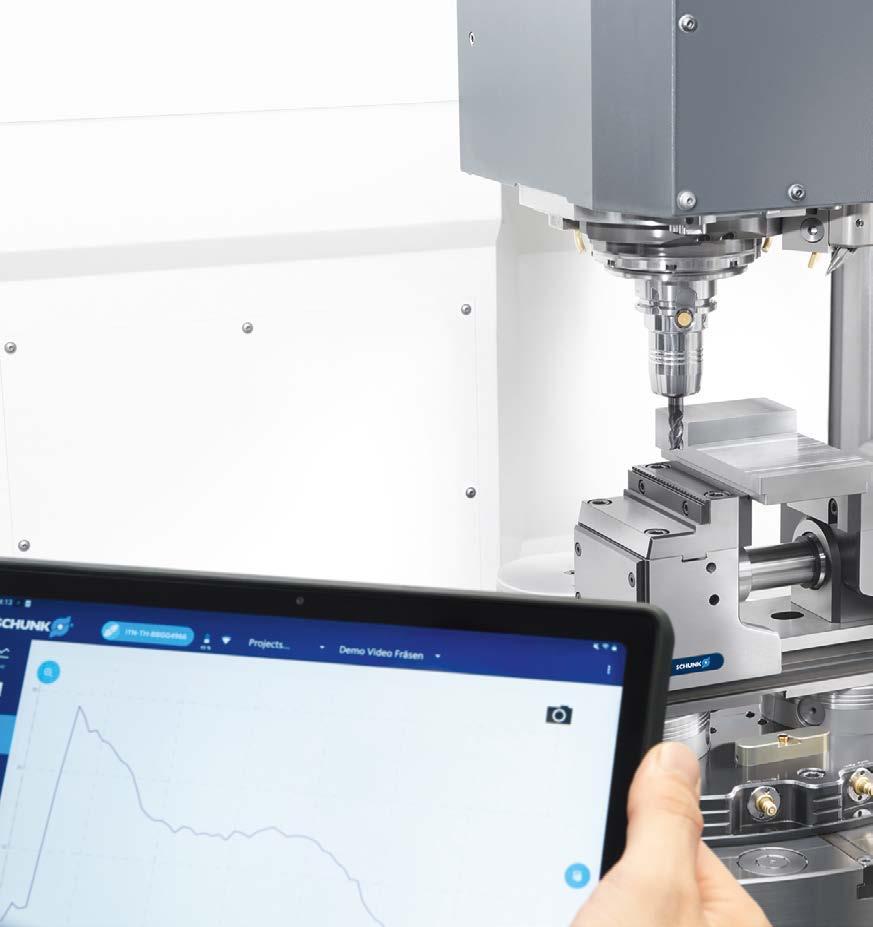
4 minute read
L’EVOLUZIONE E IL VALORE AGGIUNTO DEI CNC
CAPACITÀ DI RACCOLTA E TRASMISSIONE DATI DI MACCHINA E DI PROCESSO, DIGITALIZZAZIONE E INTEGRAZIONE IOT SONO I REQUISITI ESSENZIALI DEI CNC 4.0 di Patrizia Ricci
NNel corso degli ultimi anni, i mercati hanno richiesto al settore delle macchine utensili di eseguire lavorazioni meccaniche con prestazioni sempre più spinte, maggiore velocità e produttività, qualità e precisioni sempre più elevate, con livelli di sicurezza e flessibilità sempre crescenti. Queste richieste hanno determinato una parallela e naturale evoluzione delle tecnologie di controllo del CNC, deputato all’esecuzione delle lavorazioni meccaniche, verso una progressiva digitalizzazione. Nelle smart factory, grazie al loro impiego, ogni azione delle macchine viene decisa e controllata tramite un software integrato, da cui deriva l’acronimo CNC, ovvero “controllo numerico computerizzato”. Oggi, i CNC rappresentano il cuore di quella che è la fabbrica guidata dal flusso trasparente dei dati, la soluzione e lo strumento ideali per far fronte alle difficoltà delle aziende determinate dall’approvvigionamento delle materie prime e di tutte quelle criticità che caratterizzano lo scenario dei mercati globali.
I moderni controlli numerici si contraddistinguono per l’approccio votato alla versatilità: si tratta di piattaforme hardware dalle alte prestazioni sulle quali è installato un software completo, per coprire i più disparati settori, e al tempo stesso totalmente adattabile. Questa flessibilità costituisce il valore aggiunto riconosciuto dal mercato, perché permette di trovare una risposta per ogni genere di macchina (per metallo, vetro, marmo o legno) e tipo di operazione (rettifica, tornitura, fresatura, alesatura, taglio laser o plasma...). Le soluzioni disponibili si differenziano proprio per la loro capacità di soddisfare più ambiti applicativi e per il loro essere modulari e ampiamente configurabili e scalabili per un controllo sicuro delle macchine utensili. Queste caratteristiche permettono agli OEM di standardizzare una singola architettura CNC, ottimizzata per costi e prestazioni, per una vasta tipologia di macchine: da quelle piccole, con pochi assi, ai grandi centri di produzione multi celle, anche con centinaia di assi e mandrini. In tal modo, l’architettura aperta della piattaforma può ridurre sensibilmente i costi di sviluppo e di supporto e velocizzare il tempo di introduzione dei prodotti sul mercato. Per garantire una ancor maggiore versatilità, prestazioni dinamiche e precisione, queste piattaforme sono dotate di hardware che comprendono azionamenti digitali con sicurezza integrata, moduli PLC di sicurezza, moduli di ingresso e uscita sicuri e pannelli operatore multi processore con touch screen. I software di supporto dovrebbero includere sistemi operativi di precisione e PLC di automation, interfaccia uomo-macchina completamente personalizzabile (HMI), architetture di sicurezza integrate e complete di funzioni di lavorazione opzionali e simulatore 3D per la verifica di parti del programma e per la visualizzazione dei processi di lavorazione.
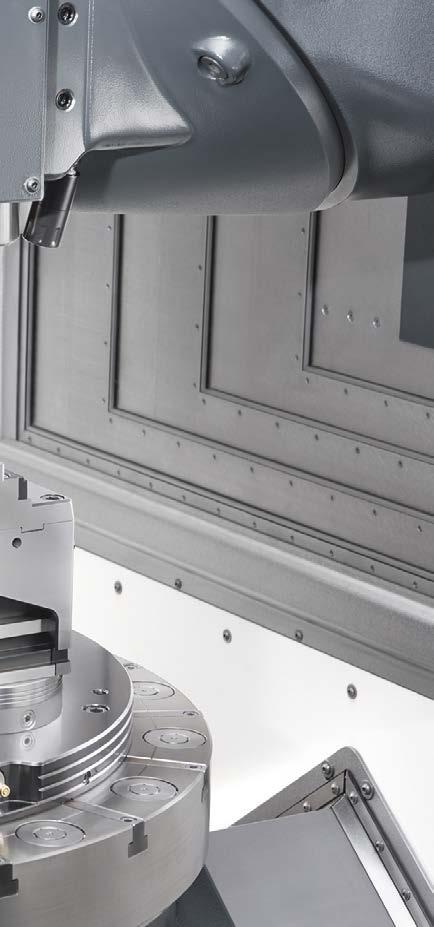
Ma cosa si intende con tecnologia CNC?
CNC è l’acronimo di Computer Numerical Control ed è un tipo di tecnologia che, inserita all’interno della macchina, le permette di muoversi seguendo un preimpostato programma di lavoro. Grazie al dispositivo digitale interno, è possibile conservare in memoria le funzioni eseguite durante la lavorazione. Tenere traccia delle operazioni, permette di adattare la macchina in base alle esigenze produttive. A differenza dei robot, non essendo in grado di adattarsi a mutamenti dell’ambiente e di reagire ad eventuali imprevisti, ostacoli improvvisi e collisioni, le macchine a tecnologia CNC necessitano del controllo di un operatore, che pur non essendo indispensabile per il suo corretto funzionamento, può esercitare una supervisione utile per impostare il programma di lavorazione, preparare i materiali da manipolare e intervenire in caso di malfunzionamenti.
La tecnologia CNC, attraverso l’impostazione di software CAM (Computer-Aided Manufacturing), CAD (Computer-Aided Design) e CNC, viene impiegata nelle lavorazioni ad alta precisione, in quelle che necessitano di tempi lunghi e in quelle che richiedono velocità, flessibilità, adattabilità, ripetizione, coadiuvando l’operatore ed evitando errori di distrazione derivanti da processi lunghi e ripetitivi.
I passaggi salienti dell’evoluzione del CNC
In effetti, l’evoluzione del CNC muove i primi passi con l’introduzione del PLC, il Controllore Logico Programmabile integrato. All’inizio, infatti, i CNC, ovvero quelle che altro non erano se non macchine calcolatori nate per la gestione dei movimenti degli assi, non erano dotate di PLC. Questi controller possono automatizzare un processo specifico, una funzione della macchina o persino un’intera linea di produzione e, quindi, consentono al CNC di gestire in modo più completo le macchine utensili, incrementandone la funzionalità e flessibilità. La possibilità di assolvere a lavorazioni sempre più complesse, invece, è stata garantita dallo sviluppo delle cinematiche a 5 assi; un passaggio, quello dai 3 ai 5 assi con algoritmi dedicati, significativo perché consente di lavorare profili pezzo tra i più complessi, particolarmente utilizzati nei settori aerospaziale, dell’automotive, in particolare quello sportivo, degli stampi e medicale, aumentando la produttività grazie a tempi di elaborazione e di ciclo ridotti. L’ultimo step del processo evolutivo, in ottica 4.0, ci porta da un controllo numerico di tipo stand-alone ad un CNC interconnesso responsabile della centralità della macchina utensile all’interno del processo produttivo e protagonista dello scambio di dati e informazioni con il mondo interno ed esterno all’ambiente di fabbrica, sulla base del quale vengono prese le decisioni sui processi produttivi. Oggi, i moderni CNC sono sempre più user-friendly e interattivi, capaci di gestire la macchina e di integrarsi nei sistemi IoT che proliferano in ambienti di fabbrica data-driven sempre più digitali e connessi, sempre più aperti, dove, grazie all’Intelligenza Artificiale, è possibile avere maggiore produttività e flessibilità, un costante monitoraggio di sistemi e consumi che garantiscono un uso più responsabile e sostenibile delle risorse.
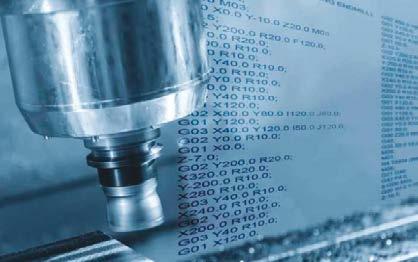
A garantire che il CNC possa assolvere a queste funzioni, oltre all’aumento delle prestazioni hardware, c’è la parte software, determinante nel processo di evoluzione del controllo CNC.
È infatti il software, sempre più intelligente, che raccoglie i dati dai numerosi sensori installati sulle macchine e trasmette al CNC le informazioni sulla base delle quali cambiare in automatico i parametri delle lavorazioni per ottimizzare i processi e assicurare una maggiore flessibilità. Spetta, infatti, alle piattaforme software dotate di intelligenza artificiale e algoritmi di machine learning il compito di aggregare dati in modo strutturale e di analizzarli per restituire in real time informazioni legate a produttività, qualità superficiale del pezzo e manutenzione predittiva di processi e macchinari, facendo comunicare reparti IT e OT all’interno dell’azienda e mettendo a disposizione dei team manager i dati del controllo numerico, dei drive e dei PLC.
I vantaggi del CNC
L’impiego del CNC consente di aumentare o ottimizzare la produzione in funzione delle richieste del mercato, ridurre i tempi passivi, anche quelli di montaggio e smontaggio, e adattare velocemente la produzione a molte variabili, grazie alla possibilità di programmare le lavorazioni e la gestione dei costi in funzione delle specifiche esigenze e dei lotti da realizzare. Diventa quindi più facile per un’azienda