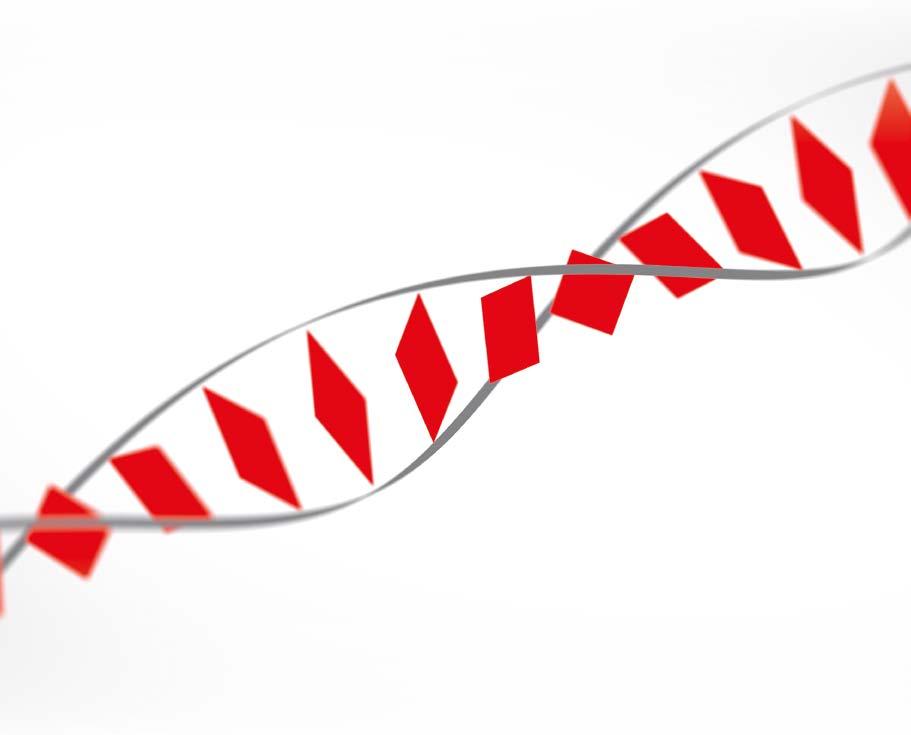
4 minute read
L’evoluzione del CNC
M8V: il CNC per lo Smart Manufacturing
M8V è il nuovo CNC interconnesso per lo Smart Manufacturing. Il livello evoluto, la praticità di utilizzo multitouch, le numerose nuove funzioni avanzate e la connettività wi-fi incorporata per la prima volta in un CNC, sono stati pensati per essere parte integrante del processo produttivo e per supportare ogni tipo di lavorazione con requisiti di precisione e velocità estreme. Il controllo numerico si evolve a supporto dello Smart Manufacturing e degli ambienti IIoT in fabbrica. M8V renderà possibile il futuro delle lavorazioni.
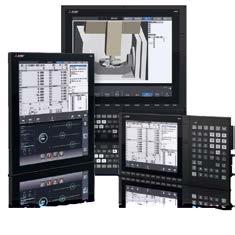
accettare una commessa con piccoli numeri o gestirne un’altra con grandi quantitativi di pezzi da produrre. Inoltre l’impiego di queste soluzioni intelligenti garantisce un elevato miglioramento della qualità del prodotto finale e una riduzione considerevole degli scarti e dei possibili errori.
A stretto contatto dell’automazione: digitalizzazione e integrazione IoT
Essendo inseriti in contesti di automazione sempre più sofisticati, per i fornitori di CNC, abilitare la gestione anche di altre parti dell’ecosistema di automazione è un plus ormai inevitabile. In tal senso, alcuni sistemi CNC sono progettati in modo da assolvere a tale esigenza in modo autonomo e indipendente dal controllore principale, sulla base delle stesse strutture hardware e software dei CNC dell’azienda produttrice. Altri, invece, sono in grado di dialogare sfruttando i protocolli di comunicazione più comuni con tutti i prodotti per automazione presenti, anche di differenti fornitori, dalla parte di elettromeccanica ai robot, gli inverter e il motion control. Interfacciandosi con tutti i device presenti, i CNC consentono la loro programmazione direttamente dal proprio pannello CNC di controllo, senza particolari difficoltà o competenze specialistiche. Proporre quindi soluzioni integrate per il controllo dei vari aspetti dell’automazione aziendale è diventato un requisito fondamentale ed essenziale. L’interfaccia verso i robot consente al controllo di gestire, ad esempio, le attività di handing per carico/scarico dei pezzi e nel machining. Tutto con un unico CNC, che grazie ad una flessibilità sempre più spinta consente sia la gestione di una pinza su robot che quella di una testa additive, laddove richiesto, nelle lavorazioni di difficile esecuzione con i metodi tradizionali. Prestazioni sempre maggiori necessitano tuttavia di una dotazione hardware sempre più potente in grado di sviluppare algoritmi sempre più dinamici e adattivi. Lo stesso vale anche per la possibilità, offerta dalle moderne macchine utensili, di combinare più lavorazioni sulla stessa macchina, sommando alle tradizionali lavorazioni di fresatura, cicli di tornitura e rettifica. Con l’incremento delle velocità, la riduzione dei tempi di attrezzaggio, fissaggio e manipolazione pezzi e la ricerca di soluzioni multitasking che integrino processi di foratura, fresatura e rettifica in un solo sistema, crescono anche le necessità di tempi e livelli di elaborazione più spinti, al pari del volume dei dati trasmessi. Ciò comporta che i CNC più evoluti offrano anche una maggiore versatilità e potenza.
Infine, un altro aspetto fondamentale nella scelta di un CNC risiede nella sua ergonomia e facilità d’uso. Questi due aspetti guidano i processi di innovazione dei CNC più evoluti e moderni. In particolar modo, la facilità di programmazione realizzata mediante testiere fisiche di elevata qualità e schermi touch sempre più user friendly con interfacce HMI personalizzabili sono le caratteristiche più richieste dal mercato. Al pari delle applicazioni di remote desktop manager grazie alle quali è possibile connettere tra loro i vari reparti aziendali coinvolti nella produzione e agevolare lo scambio dati. Le HMI completamente personalizzabili, permettono agli OEM di aggiungere valore alle loro macchine, grazie ad un’ergonomia migliorata.
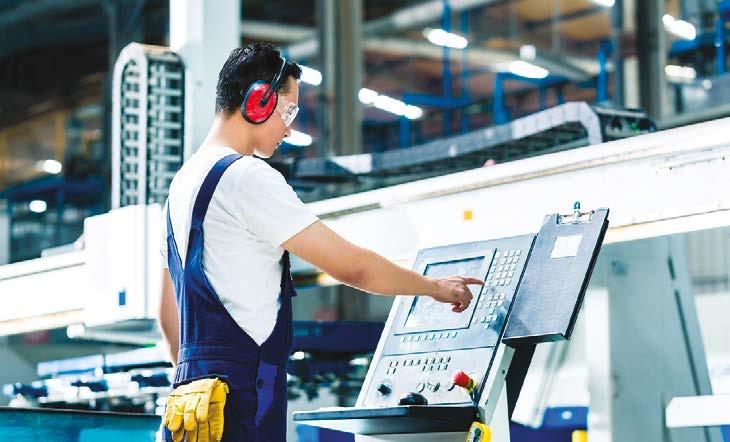
La manutenzione predittiva
Al giorno d’oggi non esiste macchina utensile che non sia connessa al mondo della fabbrica digitale. La totale apertura dei CNC di ultima generazione, in grado di dialogare con tutti i sistemi presenti sul mercato e di rilevare tutti i dati utili all’azienda per il controllo della produzione e dei consumi, consente alle aziende di realizzare un notevole risparmio in termini di energia e materie prime e di intraprendere produzioni sostenibili. Maggiore è la quantità di dati che il CNC sarà in grado di raccogliere e trasmettere, migliore e più corretta sarà l’interpretazione degli stessi, più efficiente e precisa la manutenzione e la previsione di possibili malfunzionamenti in un’ottica di manutenzione predittiva.
CNC 4.0 e digital twin
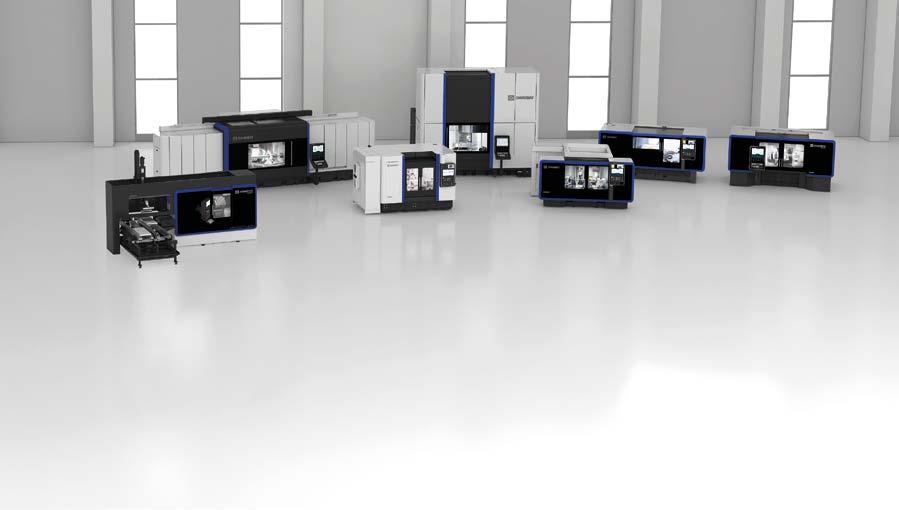
La tecnologia del gemello digitale si sta rapidamente affermando nel settore industriale come uno dei modi più convenienti per accelerare lo sviluppo di prodotti, processi e servizi. Nei prodotti di automazione quali le macchine utensili, il digital twin è un modello virtuale che utilizza la simulazione, l’acquisizione/analisi dei dati in tempo reale e le tecniche di apprendimento della macchina per fornire una valutazione completa delle prestazioni dinamiche della stessa prima di costruire un prototipo fisico. Un legame stretto caratterizza anche CNC e digital twin. I programmi parziali scritti manualmente o generati da CAM possono essere verificati e ottimizzati facilmente e velocemente, usando dei software di simulazione grafica, disponibili su un PC offline. Alternativamente, il software può girare direttamente sul pannello operatore e interagire con l’unità CNC della macchina per simulare parti del programma, sia prima del funzionamento o simultaneamente, con un’elaborazione parziale. In questo modo, gli utilizzatori possono visualizzare il percorso del punto centrale dell’utensile, simulare l’asportazione di materiale e verificare le possibilità di collisione. La possibilità di simulare tutte le lavorazioni che la macchina utensile sarà in grado di eseguire in modo sicuro, con una chiara stima dei tempi e dei costi, consentendo anche di prevenire collisioni accidentali, costituisce un reale vantaggio per i clienti che possono fare offerte più mirate per i pezzi finiti. Per ricavare il gemello digitale della macchina utensile, il CNC deve possedere dei requisiti specifici in termini di grafica 3D che rendano possibile la simulazione della macchina e delle sue lavorazioni. Infine grazie al digital twin di cui sono dotate le tecnologie CNC è possibile attuare un controllo immediato sul pezzo, sulle sue dimensioni e caratteristiche, e se necessario intervenire immediatamente sul processo di lavorazione simulato evitando di andare in produzione con un pezzo destinato allo scarto.