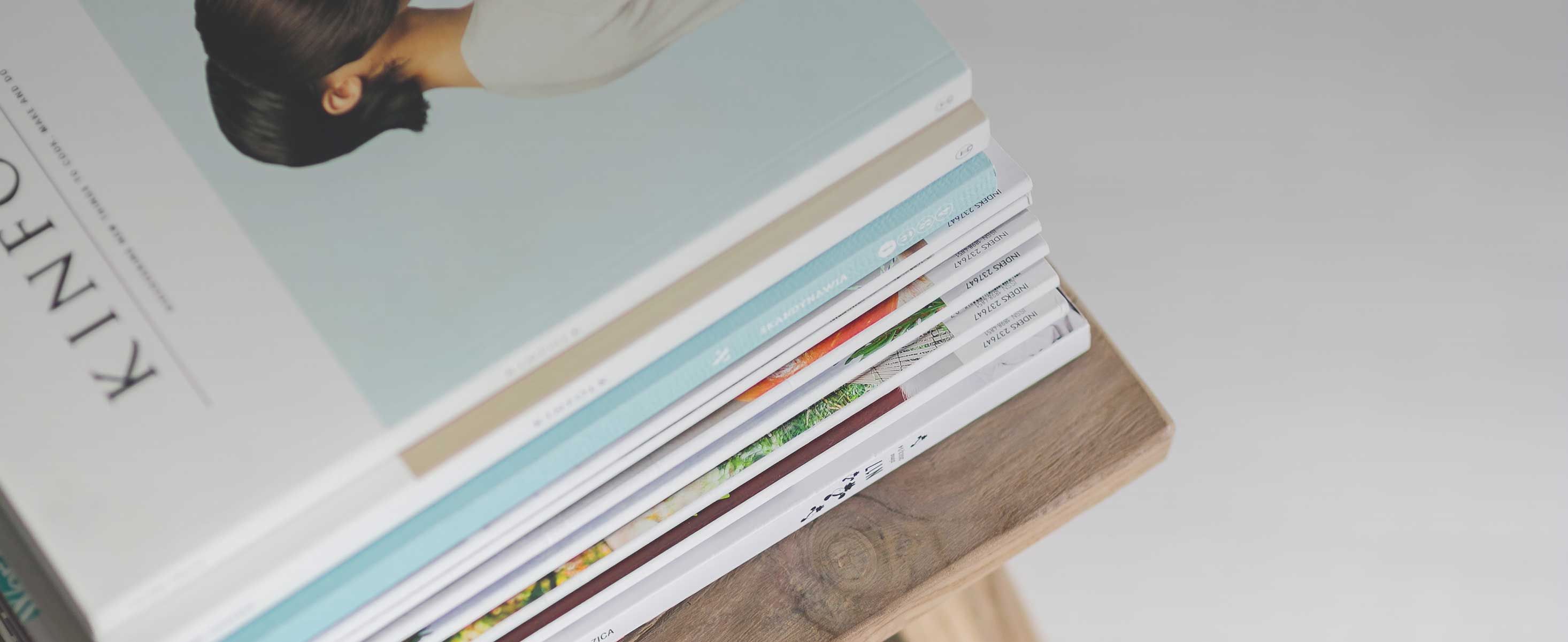
3 minute read
CNC Z32, IL CNC PRONTO PER L’INDUSTRIA 4.0
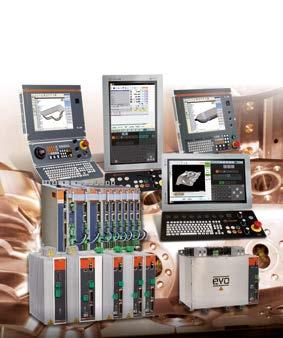
Oltre quarant’anni di vita votati all’innovazione nei controlli numerici e azionamenti sono il biglietto da visita di D.Electron, azienda fiorentina che è cresciuta divenendo un punto di riferimento nel settore della progettazione e costruzione di CN destinati ai centri di lavoro. Competenza, innovazione, collaborazione e servizio sono i quattro punti cardinali chiave per la storia di D.Electron. Una storia votata all’innovazione nel campo dei controlli numerici e degli azionamenti, ponendosi col CNC Z32 come partner per l’industria manifatturiera italiana e internazionale, forte del know-how maturato nel comparto della meccanica al servizio della clientela. Le configurazioni del sistema di controllo Z32 D.Electron ruotano attorno a una Unità Centrale che contiene il sistema operativo FlorenZ ed il software del controllo numerico. L’unità centrale è collegata ad una scheda che instrada i pacchetti d’informazioni dalle periferiche concentrate o distribuite e gli azionamenti digitali ZStar2 verso il controllo numerico e viceversa, il bus di comunicazione è in fibra ottica ed il protocollo è proprietario.
Il CNC Z32 D.Electron può gestire fino a 32 assi digitali e 16 tramite riferimento analogico oltre che 25 nodi distribuiti di periferiche I/O ognuno basato fino a 8 schede di acquisizione. Le schede possono essere da 16 o 32 IN oppure OUT digitali, riferimenti analogici, encoder, ecc. Il controllo può gestire fino a 6 canali di interpolazione. Svariate le possibilità di fornitura di soluzioni per l’interfaccia uomo macchina, dal compatto All-in-one Z32C15 al PC panel per soluzioni full-touch OST22.
Il contatto diretto con costruttori di macchine utensili ed integratori di sistemi ha favorito lo sviluppo di strumenti software tali da accompagnare il tecnico step by step verso la messa in servizio degli assi ed eventuali operazioni di service.
Nell’Unità Centrale è preinstallata la suite software “Z32 for windows” che contiene una ricca dotazione di applicazioni: ZETA, l’interfaccia operatore del CNC; ZFlash, il tool di programmazione a bordo macchina; Z32Info, che esegue il backup ed il ripristino dei dati del sistema ed il software per il teleservice.
Nella suite sono presenti anche gli strumenti per configurare il sistema e renderlo operativo: AXIS-Tune controlla il corretto cablaggio dell’hardware e dei servomotori asse della macchina. I parametri che definiscono elettricamente i servomotori e i trasduttori di posizione sono preinstallati nel configuratore Tarat e organizzati in liste. Alla prima messa in servizio si procede col check delle connessioni elettriche di potenza e di segnale tra il servomotore e sistema di controllo. Eseguite le verifiche di connessione, il tecnico inizia la messa a punto dell’asse. Il primo passo è definire i valori dei parametri della maglia di corrente e, per eseguire i calcoli necessari, in ingresso alla maglia AXIS-Tune applica un riferimento di corrente con forma d’onda a gradino ampia al 30% della corrente massima. Il servomotore esegue movimenti impercettibili sui quali si calcola la risposta migliore. I valori dei guadagni della maglia di corrente sono immediatamente visibili, attivi e acquisiti come taratura dell’asse, non occorre salvare dati ed elaborarli con altri strumenti o men che meno copiarli manualmente in altri campi o pagine. Successivamente il tecnico passa alla taratura della maglia di velocità. Anche in questo caso viene applicato un riferimento di velocità la cui forma d’onda è di tipo a gradino.
I movimenti del motore sono più ampi rispetto a quelli fatti per la maglia di corrente e AXIS-Tune se ne serve per rilevare l’inerzia meccanica dell’asse vista dal motore. La taratura G125 è una procedura automatica di tuning eseguita sfruttando uno degli strumenti per la gestione dell’alta velocità che sono a disposizione sia del tecnico installatore sia del programmatore dei cicli di lavoro. Il tecnico definisce velocità e corsa dell’asse mosso dalla G125 al fine di ridurre gli errori d’inseguimento della risposta e individuare le migliori condizioni di moto introducendo automaticamente le correzioni dei parametri necessarie all’ottimizzazione della dinamica del sistema.
La funzione G125 è potente, semplice da usare e permette anche all’utente finale della macchina di avere prestazioni ottimali nelle zone più critiche dell’area di lavoro specie se la macchina ha condizioni dinamiche che possono cambiare in virtù della configurazione oppure della posizione assunta dagli assi.
Il test finale è detto Maglia di Posizione ed è eseguito su tutta la corsa dell’asse che si sta mettendo in servizio. Analizzando i dati rilevati, questo test ha lo scopo di individuare possibili impuntamenti meccanici o non uniformità permettendo così ai tecnici di porvi rimedio. Infine, per individuare eventuali errori geometrici all’inversione dell’asse, si procede con un test del cerchio. Si tratta di uno degli strumenti della gestione dell’alta velocità chiamato Test G113X KA1 ed è assimilabile a una sorta di test di ballbar.