#6 settembre2024 mensile
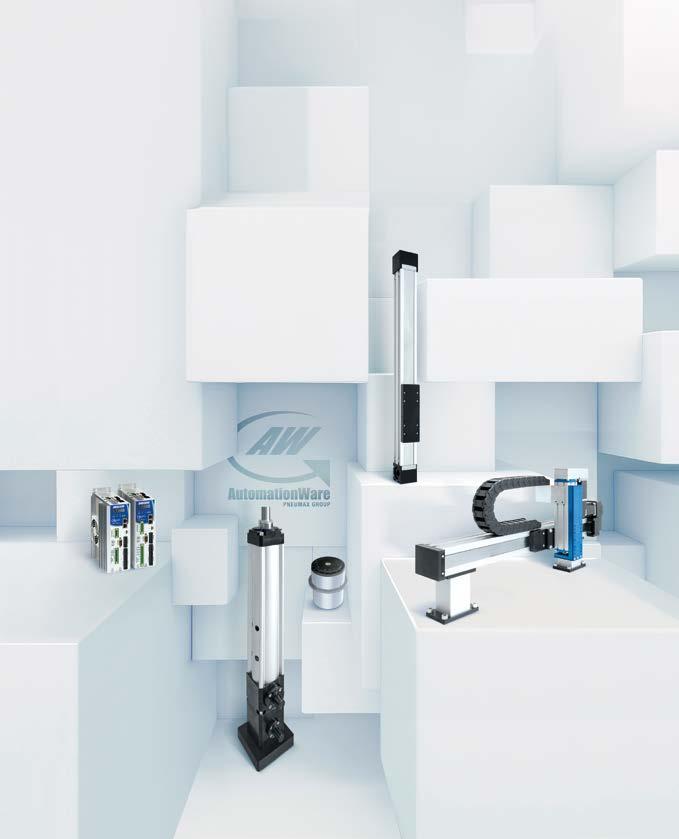
MACCHINE MULTITASKING
E RETTIFICATRICI
SPECIALE MANUTENZIONE PREDITTIVA
INNOVAZIONE TECNOLOGICA E SOLUZIONI INTEGRATE
www.meccanica-automazione.com
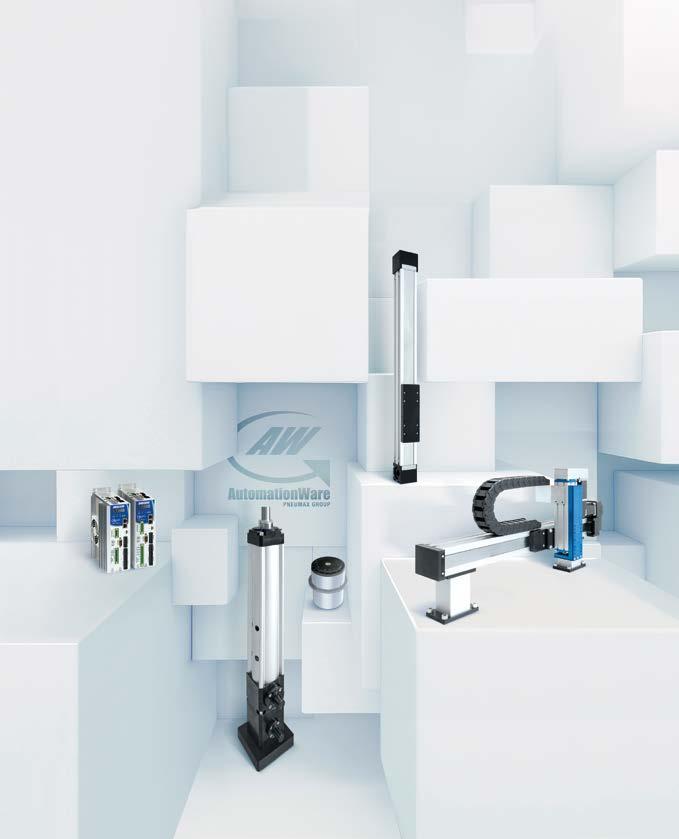
#6 settembre2024 mensile
MACCHINE MULTITASKING
E RETTIFICATRICI
SPECIALE MANUTENZIONE PREDITTIVA
INNOVAZIONE TECNOLOGICA E SOLUZIONI INTEGRATE
www.meccanica-automazione.com
Gli avviatori elettronici serie ME... sono ideali per applicazioni che necessitano di un numero molto elevato di avviamenti e risparmio di spazio all’interno del quadro. Sono realizzati con tecnologia ibrida, che combina il vantaggio della lunga vita di un dispositivo a semiconduttore esente da usura, all’elevata robustezza e bassi consumi di un relè meccanico.
Per comando motori fino a 2,4A o 7A (AC53a)
Versioni per avviamento diretto o teleinvertitore
Protezione termica motore integrata
Versioni con o senza arresto di emergenza STO (Safe Torque Off)
Contenitore compatto largo 22,5mm
Fissaggio su profilato omega da 35mm
BI-MU Milano 09.–12. ottobre
padiglione 11 stand D24
I nuovi convertitori di tensione e frequenza della Linea RamBatt, sono realizzati in Italia e perfetti per impieghi in laboratori di test e per alimentare macchinari industriali. Disponibili nelle versioni monofase e trifase, sono progettati e prodotti negli stabilimenti italiani del Gruppo DKC utilizzando componenti di alta qualità e tecnologie avanzate.
ELEVATA EFFICIENZA
Massimizza la produttività con prestazioni eccezionali FLESSIBILITÀ
Adattabili a diverse esigenze con un alto grado di personalizzazione
CONTROLLO REMOTO AVANZATO
Gestisce e monitora facilmente i convertitori da remoto AFFIDABILITÀ GARANTITA
Qualità italiana che dura nel tempo
di Chiara Tagliaferri
Il materiale è sicuramente il fattore abilitante da cui sono scaturite le più grandi conquiste ed evoluzioni storiche per l’essere umano. Nel corso dei secoli hanno reso possibili non solo miglioramenti incrementali rispetto le precedenti, ma hanno aperto la via a rivoluzioni industriali come sta succedendo per l’attuale. Basti pensare alle loro caratteristiche utilizzate per l’efficientamento energetico, sostenibilità, salute e cura della persona, mezzi di traporto, urbanistica e così fino a permeare tutto il costruito. Se consideriamo la definizione di materiale come “tutto ciò che è tangibile e fisico... il mondo concreto che possiamo vedere e toccare” il suo studio e sviluppo da sempre rappresenta il cuore pulsante, la miccia di innesco di innovazioni fondamentali. Per semplificare, si può pensare cosa ha comportato poter contare, oggi su materiali compositi come la fibra di carbonio e il kevlar, su polimeri ad alte prestazioni come il PEEK, il policarbonato e il nylon ad alta resistenza, come le leghe ad alta resistenza, i materiali intelligenti, riciclabili, biocompatibili o bio assorbibili. Certo, il costo di produzione e la scarsità delle materie prime di cui sono composti rappresentano spesso una discriminate importante per la scelta dell’uno o dell’altra ponendosi anche come barriera alle più promettenti ma, in combinazione con l’avanzamento delle tecnologie di produzione, oggi assistiamo ad una accelerazione anche in questa direzione. Ed è proprio perché i materiali avanzati sono alla base delle catene del valore di molteplici settori applicativi e sono sempre più riconosciuti come un fattore strategico per l’autonomia e la competitività delle impre-
se, la Commissione Europea il 27 febbraio 2024 ha pubblicato la sua comunicazione intitolata “Advanced Materials for Industrial Leadership”. La comunicazione vuole riconoscere con forza il loro ruolo quali abilitatori di tutte le sfide tecnologiche del futuro, ripuntando i fari dell’attenzione della comunità di riferimento (accademia, ricerca, industria) sulle ricerche che velocizzino le innovazioni verso il mercato, assicurando al contempo sostenibilità e protezione della salute umana e dell’ambiente. I primi settori target di questa iniziativa sono l’energia, la mobilità, l’edilizia e l’elettronica. A tal fine, e qui la buona notizia, “dovranno essere mobilitati più investimenti UE, nazionali, regionali e privati per affrontare questa sfida con un approccio coordinato”. Ma si dovranno (attenzione!) ricercare materiali sicuri e sostenibili, perché, come mi è capitato di sentire rimarcare nella lecture di apertura della 40 esima Conferenza Nazionale dell’Associazione Italiana di Metallurgia dove sono mentre scrivo, l’idrogeno, su cui così tanto si punta, non è poi così sicuro e sostenibile. Ma questa è un’altra storia.
Per ora mi piace lasciarvi con questa suggestione. Se con il termine materiale ci riferiamo a tutto ciò che è tangibile e fisico, e l’immaginario, riguarda le idee, i sogni e il regno della creatività da dove nascono le visioni del futuro e le innovazioni, il materiale e l’immaginario devono lavorare in sinergia per alimentare il progresso umano, trasformando le idee in innovazioni tangibili.
chiara.tagliaferri@cnr.it
EDITORIALE
5 Il materiale e l’immaginario
CALEIDOSCOPIO
8 News e novità
PANORAMA
12 Il digitale in Italia 2024
14 Nasce il salone dell’idrogeno
16 Bilancio di sostenibilità integrata
18 Assemblea UCIMU
22 All4pack Emballage 2024
24 Fiducia, innovazione e retaggio: faccia a faccia con i fondatori di WIBU-SYSTEMS
STORIA DI COPERTINA
28 Innovazione tecnologica e soluzioni integrate: i punti cardine dell’evoluzione
DOSSIER MACCHINE MULTITASKING E RETTIFICATRICI
34 Soluzioni e sistemi per lavorazioni complesse
36 Quando le lavorazioni complesse diventano semplici
40 La gamma MiKroturngrind di Hembrug
42 Centri di lavoro multitasking MCM, un’offerta integrata e affidabile
44 Lo stato dell’arte del controllo numerico
46 Encoder incapsulati e sonde per migliorare il controllo dei processi
50 Soluzioni di rettifica senza centri Ghiringhelli: un punto di riferimento nel mercato
54 Quando il silenzio è importante
58 Da 0 a 100% multitasking
62 Una storia di successo da Barcellona
SPECIALE MANUTENZIONE PREDITTIVA
66 Come rivoluzionare l’efficienza nell’industria manifatturiera
RICERCA E INNOVAZIONE
80 Ottimizzazione della Vita Utile Residua di componenti critici per la produzione
82 Roba-Drive-Checker il componente intelligente che misura e comunica
PRISMA
86 Prodotti
Dal 1943
investiamo nelle risorse e nella tecnologia per offrire ai nostri clienti le migliori soluzioni metrologiche
Dal 1943
guardiamo avanti grazie ad un solido passato
Fotogrammetria
Cambio al vertice di ANIE Sicurezza, parte di Federazione ANIE. In occasione della recente Assemblea dei Soci, lo scorso 30 Maggio, l’Associazione ha eletto alla Presidenza Andrea Monteleone, in carica per il biennio 2024-2026, attualmente Segment Develoment Manager EMEA per il mondo delle Infrastrutture Critiche di Axis Communications, Canon Group. Dal 2018, Monteleone ha ricoperto in ANIE Sicurezza, la carica di Vicepresidente e di membro del Board. In occasione dell’elezione, Monteleone ha presentato le Linee programmatiche che intende sviluppare nel suo mandato, incentrate sui seguenti obiettivi: promuovere un nuovo concetto di “base associativa”, favorendo il passaggio da una idea di “associarsi per consuetudine” all’associarsi “per contribuire alla crescita” dell’Associazione così da raggiungere obiettivi ancora più ambiziosi; rinforzare e sviluppare attività istituzionali, ancora più qualificanti e promotrici di una maggiore e migliore competitività delle Aziende associate. Ancora, influenzare ed educare il mercato verso la qualità e la professionalità stimolando il confronto e il dialogo aperto fra gli associati; implementare la consapevolezza che il contesto normativo europeo sta imponendo una forte accelerazione all’evoluzione del mercato. Regolamenti Europei come CRA (Cyber Resilience Act), NIS2 (Network and Information Security, v2) e Critical Entities Resilience Act, per citarne alcuni, hanno già cambiato e cambieranno ancora di più nel futuro prossimo il modo in cui tutta la filiera dovrà guardare al mondo della sicurezza nella sua accezione più ampia.
Tra i temi prioritari dell’agenda del neoeletto Presidente anche le iniziative per incentivare e strutturare nuove collaborazioni industriali, facendo sistema tra gli associati al fine di dare risposte proattive ed efficaci alle sfide che il mercato ed il contesto attuale impongono. Infine spingere all’internazionalizzazione, attraverso specifiche azioni che rendano ancora più visibile ed appetibile il valore espresso dalle Aziende associate in ambito internazionale. “È più che mai evidente - ha dichiarato il neoeletto Presidente – che nel contesto attuale le regole di mercato sono dettate, in buona parte, da regolamenti europei. Come Professionisti e Imprenditori non possiamo trascurare questo aspetto, verrebbe meno la nostra continuità aziendale e la possibilità di mantenere ed aumentare il nostro peso, sia in termini di influenza che di quote di mercato italiano ed estero. Se c’è un ruolo che ANIE Confindustria e, nello specifico, ANIE Sicurezza possono e devono continuare a ricoprire è quello di luogo di aggregazione e sviluppo del nostro comparto industriale. Obiettivi certamente ambiziosi che richiederanno il mio fermo impegno e un lavoro, importante, di squadra. In questi ultimi sei anni, come membro del Direttivo prima e come Vicepresidente poi, ho avuto il privilegio di sedere al fianco di Persone e Professionisti di altissimo spessore. Ho imparato da tutti, apprezzato il profondo rispetto – pur nelle diversità di opinioni – che ha sempre caratterizzato ogni confronto, riconoscendo le esperienze di ciascuno. È così che vorrei continuare ad operare: nel più puro spirito associazionistico”.
Si avvicina l’appuntamento con piùAdditive, il tema espositivo dedicato alle tecnologie additive di 34.BI-MU, in scena dal 9 al 12 ottobre 2024 a fieramilano Rho. Patrocinata da AITA, l’Associazione italiana tecnologie additive, l’iniziativa si conferma, anche per questa edizione, punto di incontro per tutti i player dell’addittivo e, avrà come protagonisti produttori, distributori, centri di servizio, utilizzatori, università, centri di ricerca e start-up. Ad oggi, tutti i principali player del comparto hanno confermato la loro presenza tra le fila degli espositori e la raccolta adesioni procede ancora con nuove richieste di partecipazione.
“Il grande interesse – ha dichiarato Luigi Galdabini, presidente di AITA – dei top player dell’additivo al partecipare, conferma la rilevanza di piùAdditive nel panorama fieristico del comparto. È importante evidenziare che, il settore dell’additive manufacturing sta vivendo un vero e proprio boom e l’Italia - tra
le Top 10 per il numero di depositi di brevetto di soluzioni additive e seconda in EU per installazioni industriali – si conferma un mercato ad altissimo potenziale per il suo sviluppo. Con queste premesse, piùAdditive non può che essere, sia nel panorama nazionale che internazionale, un appuntamento fondamentale, di grande valore e richiamo.”
L’offerta in mostra presenterà una ricca proposta di macchine, materiali, prodotti, soluzioni per il collaudo e il postprocessing, software e servizi correlati all’additive manufacturing, la cui presenza risulta sempre più diffusa in tutti i principali comparti del manifatturiero – tra cui aerospace, trasporti, biomedicale, oil&gas, pharma, food e molti altri.
Inoltre, presso lo stand AITA, fulcro dell’area espositiva, saranno predisposte vetrine con oggetti realizzati con tecnologie additive, esplicativi dei potenziali e dei progressi del settore, e saranno organizzati numerosi eventi,
tra cui speech, a cura di aziende, università, centri di ricerca, progetti europei, inerenti alle loro ultime soluzioni e convegni più istituzionali, focalizzati sulle future evoluzioni del comparto.
“Per offrire una completa esperienza di visita e per incentivare le occasioni di business tra i player presenti tra i padiglioni – ha affermato Alfredo Mariotti, direttore generale di UCIMU-SISTEMI PER PRODURRE –lo stand AITA, come ormai da tradizione, abbinerà alla dimensione espositiva quella di networking e approfondimento culturale attraverso l’organizzazione di un fitto calendario di incontri incentrati sulle tecnologie additive. Il programma è ancora in via di definizione ma, tra gli eventi già confermati vi sono il convegno dedicato ai 10 anni di attività di AITA, la tavola rotonda “Women in 3D printing” e un incontro dedicato al biomedicale.”
ITALIAN MACHINE VISION FORUM
Si terrà il 17 ottobre presso lo Spazio Fase di Alzano Lombardo (BG) la terza edizione di Italian Machine Vision Forum, mostra convegno itinerante promossa da ANIE Automazione e organizzata da Messe Frankfurt Italia. Il settore dei Sistemi di Visione rappresenta in Italia un bacino dalle ampie opportunità di sviluppo, soprattutto in ambito Industria 4.0. Mossi da questa consapevolezza, i principali fornitori di soluzioni tecnologiche per la Smart Vision, sotto la guida di ANIE Automazione, collaborano in modo sinergico alla realizzazione di attività volte allo sviluppo, promozione e diffusione della tecnologia dei SdV sul mercato nazionale. Nell’ambito di queste iniziative, nasce Italian Machine Vision Forum. Visione artificiale, competitività e
sostenibilità saranno i temi al centro dell’evento che offrirà una panoramica di un settore con ampio potenziale di sviluppo nell’ambito dell’industria green e digitale.
La sessione di apertura lavori sarà occasione di confronto su ruolo e opportunità di sviluppo delle soluzioni tecnologiche per la visione artificiale tra rappresentanti dell’industria del territorio che ospita la manifestazione. Le sessioni convegnistiche che si svilupperanno a seguire avranno come focus le “Tecnologie” e le “Applicazioni”. Qui i più importanti fornitori di componenti e soluzioni per la Smart Vision che operano sul mercato italiano presenteranno, anche attraverso casi applicativi, degli approfondimenti sulle tecnologie per la Visione Artificiale. Partendo dall’esistente verrà posta l’attenzione sul futuro del Machine Vision e sull’impatto in questo comparto tecnologico dell’Intelligenza Artificiale. Non si parlerà solo di manifatturiero, ma anche applicazioni in settori in cui il ruolo dei Sistemi di Visione è destinato a divenire sempre più strategico. Italian Machine Vision Forum rappresenta un appuntamento imperdibile per gli attori della filiera della Visione Artificiale: i fornitori di componenti e sistemi incontrano i costruttori di macchine e gli utilizzatori finali per presentare le soluzioni tecnologiche più innovative disponibili sul mercato e gli sviluppi tecnologici futuri che interesseranno l’industria e i servizi. L’ingresso è gratuito previa registrazioni su machinevisionforum.it
Scm Group, specializzata nelle tecnologie per la lavorazione di un’ampia gamma di materiali, ha siglato oggi l’accordo con Tecno Logica per l’acquisizione del controllo del suo capitale sociale.
Si tratta di un’operazione strategica che amplia l’offerta di prodotti e servizi del gruppo riminese con sistemi integrati, scalabili e modulari per le grandi industrie dell’automotive, dell’arredamento e della fabbricazione di porte.
Tecno Logica, con sede a Treviso, è uno dei maggiori produttori di impianti ad altissima produttività e flessibilità per un ampio spettro di processi industriali, con più di 200 installazioni in Europa, Medio Oriente, Messico e USA e un fatturato di oltre 30 milioni di euro.
“Questa acquisizione - sottolinea Marco Mancini, CEO di Scm Group - potenzia ulteriormente la nostra leadership nei settori della lavorazione di alluminio, materiali compositi e legno dove siamo già presenti con i nostri brand Cms e Scm. Si aprono inoltre opportunità nella fascia top del mercato con la possibilità di anticipare i nuovi trend e di innovare in modo ancora più strategico la nostra offerta”. “L’ingresso in una solida realtà multinazionale come Scm Group - aggiunge Mirko Piasentin, CEO di Tecno Logica - favorirà un più ampio accesso a clienti leader in tutto il mondo grazie alla presenza diretta e alla capillare organizzazione di vendita e service del gruppo”.
Progettato per la tua officina – con il 5° asse sull’utensile per lavorazioni simultanee su 5 lati ad alte prestazioni.
INFORMAZIONE DAL MONDO TECNOLOGICO
ANITEC-ASSINFORM, LA
PRINCIPALE ASSOCIAZIONE
DI SETTORE DELLE IMPRESE
CHE OPERANO IN ITALIA NELLA PRODUZIONE
DI SOFTWARE, SISTEMI
E APPARECCHIATURE
ELETTRONICHE E NELLA
FORNITURA DI SOLUZIONI
APPLICATIVE E DI RETI, DI
SERVIZI A VALORE AGGIUNTO E CONTENUTI CONNESSI
ALL’USO DELL’ICT E ALLO
SVILUPPO DELL’INNOVAZIONE
DIGITALE, HA PRESENTATO I DATI 2024
Di Cristina Gualdoni
Il settore digitale in Italia continua a rappresentare un pilastro fondamentale per la crescita economica del Paese. Il rapporto “Il Digitale in Italia 2024” evidenzia come il mercato digitale abbia raggiunto i 78,7 miliardi di euro nel 2023, con proiezioni che lo vedono salire a 91,6 miliardi di euro entro il 2027. Questo trend di crescita sottolinea l’importanza del digitale non solo come settore economico in sé, ma anche come abilitante per la trasformazione di altri settori industriali, della Pubblica Amministrazione (PA) e delle abitudini dei cittadini. Nonostante il quadro economico globale presenti segnali di rallentamento, con un PIL previsto in crescita dello 0,7% per l’Italia nel 2024, il digitale rimane un’area chiave di sviluppo. L’attuazione del Piano Nazionale di Ripresa e Resilienza (PNRR) gioca un ruolo cruciale in questo contesto, con risorse significative destinate alla
digitalizzazione della PA e delle imprese, nonché al miglioramento dell’infrastruttura energetica e dei servizi sanitari. Il PNRR ha visto un aumento delle risorse destinate alla Missione 1, “Digitalizzazione, innovazione, competitività, cultura e turismo”, che ora ammontano a 41,3 miliardi di euro.
Il mercato digitale: sfide e opportunità Nel 2023, il mercato digitale italiano ha continuato a crescere, nonostante la riduzione della spesa nel settore Consumer, compensata dall’incremento nel segmento Business. Le grandi imprese italiane mostrano un grado di digitalizzazione significativamente superiore rispetto alle PMI, con il 67% delle aziende che utilizza almeno una tecnologia digitale avanzata. Tuttavia, permangono sfide legate alla diffusione delle competenze digitali, soprattutto nelle PMI, che rischiano di essere escluse da questa trasformazione epocale. Le tecnologie digitali come l’Intelligenza
Artificiale (IA), la robotica e le piattafor me digitali sono sempre più adottate dalle imprese italiane. Tuttavia, esistono anco ra margini di miglioramento nell’utilizzo di tecnologie come la stampa 3D e i Big Data, dove l’Italia risulta leggermente indietro rispetto alla media europea e si gnificativamente rispetto agli Stati Uniti. In un contesto di crescente incertez za geopolitica ed economica, l’Italia deve continuare a investire nel digita le per mantenere la competitività glo bale. La sfida principale sarà quella di colmare il divario di competenze e ga rantire che anche le piccole e medie im prese possano beneficiare delle opportu nità offerte dalla trasformazione digitale. Questo articolo riassume i punti principali del rapporto, fornendo una visione d’insieme delle tendenze, delle sfide e delle opportunità nel settore digitale in Italia per il 2024. Il rapporto completo è consultabile sul sito dell’associazione.
Expertise – Passion – Automation
SMC, azienda leader nel settore dell’automazione industriale e dell’IIoT, risponde all’esigenza di ridurre le emissioni di CO2 ed i consumi energetici con il lancio della sua ultima innovazione, il sistema di gestione dell’aria compressa della serie AMS20/30/40/60. Grazie a questa nuova e rivoluzionaria unità, rivolta a tutti gli utilizzatori di aria compressa ed adatta a qualsiasi applicazione nei diversi settori produttivi, è facile compiere il primo passo verso la digitalizzazione dei processi, a vantaggio dell’ambiente e della vostra redditività. SMC, un fornitore unico per le vostre esigenze.
L’innovazione SMC Italia allo Stand 10 Rimini - Palacongressi, 16-18 settembre 2024
www.smcitalia.it
Questo impegno si concretizza in una strategia integrata che mira a generare impatti positivi sull’ambiente e sulla società, valorizzando un ecosistema di valori, relazioni e scelte sostenibili certificate.
La strategia di sostenibilità dell’azienda si articola in diverse aree chiave:
1. Prodotti e Tecnologie Ecologiche: SEW-EURODRIVE sviluppa prodotti e soluzioni che rispettano l’ambiente, inoltre l’uso di energia green, proveniente da fonti rinnovabili, è centrale nella strategia aziendale, così come la promozione di una cultura d’impresa più smart e inclusiva
2. Obiettivi Principali: Gli obiettivi di SEW-EURODRIVE si suddividono in tre ambiti principali:
o Ambientale: La riduzione e la compensazione delle emissioni di carbonio rappresentano un obiettivo cruciale, con l’intento di raggiungere la neutralità carbonica entro il 2026.
o Economico: L’azienda punta a sviluppare soluzioni e prodotti che non solo rispettino l’ambiente, ma che contribuiscano a rendere sostenibili le attività dei clienti.
o Sociale (Persone): SEW-EURODRIVE è fortemente impegnata nella promozione della Diversity & Inclusion, con iniziative volte ad aumentare la presenza di donne e giovani nell’organico aziendale, migliorare l’indicatore Trust Index, e ridurre il divario salariale tra i dipendenti di genere diverso.
o Iniziative e Risultati di Sostenibilità: Tra le iniziative più significative, l’azienda ha introdotto materiali a minor impatto ambientale nella produzione, ha implementato processi di riparazione
e ricondizionamento dei prodotti, e ha investito nel riciclo dei metalli. Queste azioni fanno parte di una più ampia strategia di economia circolare, che mira a ridurre gli sprechi e promuovere il riutilizzo dei materiali.
3. Collaborazione con gli Stakeholder: SEW-EURODRIVE riconosce l’importanza di ascoltare e coinvolgere i propri stakeholder, al fine di comprendere meglio le loro esigenze e creare valore per tutte le parti coinvolte.
3. Governance e Sostenibilità Economica: La sostenibilità è radicata a tutti i livelli dell’azienda, con un forte impegno verso l’etica e l’integrità. La governance aziendale è strutturata per garantire una gestione ottimale e responsabile, con attenzione particolare alla sostenibilità economica.
4. Innovazione nei Prodotti e Servizi: SEWEURODRIVE continua a innovare nel campo delle soluzioni di automazione
industriale, contribuendo alla sostenibilità propria e dei clienti finali. Con l’evoluzione rapida del contesto produttivo, l’azienda ha sviluppato nuovi prodotti come GearFluid, un olio ricavato da biomasse sostenibili che riduce le emissioni dell’85% rispetto agli oli minerali tradizionali, e ECO2, un prodotto in alluminio non verniciato che evita l’uso di materiali difficili da smaltire come vernici e solventi. Un’altra soluzione innovativa è Up-toNext, un processo di remanufacturing che estende il ciclo di vita dei motoriduttori, in linea con i principi dell’economia circolare.
5. Impegno Ambientale e Risultati Concreti: SEW-EURODRIVE misura annualmente la propria carbon footprint, adottando misure per ridurre le emissioni di gas a effetto serra. L’azienda ha già ottenuto risultati significativi, come la copertura del 100% del fabbisogno elettrico con energia da fonti rinnovabili e un tasso di recupero dei rifiuti del 99,2%. Grazie all’installazione di pannelli fotovoltaici e alla promozione della mobilità sostenibile (con politiche di carpooling e l’uso di auto ibride o elettriche), l’azienda ha ridotto del 8,2% i consumi energetici.
6. Riconoscimenti: L’impegno di SEWEURODRIVE è stato riconosciuto da EcoVadis. Inoltre ha ricevuto la medaglia di bronzo per la trasparenza nella catena di fornitura e per l’eccellenza nelle politiche e procedure di sostenibilità. Questo riconoscimento non solo celebra i risultati ottenuti, ma offre anche stimoli per ulteriori miglioramenti, attraverso un feedback dettagliato sui possibili ambiti di crescita. IL
ITALIAN EXHIBITION GROUP E HANNOVER FAIRS INTERNATIONAL GMBH (HFI), FILIALE
ITALIANA DI DEUTSCHE MESSE AG, HANNO SIGLATO UN ACCORDO DI COLLABORAZIONE PER L’ORGANIZZAZIONE CONGIUNTA DI UN NUOVO SALONE DELL’IDROGENO BY HYDROGEN & FUEL CELLS ALL’INTERNO DI KEY – THE ENERGY TRANSITION EXPO, IN PROGRAMMA A RIMINI DAL 5 AL 7 MARZO 2025 a cura della redazione
L’idrogeno, soprattutto quello verde derivante da elettrolisi alimentata da energia pulita, risulta fondamentale per il raggiungimento degli obiettivi di decarbonizzazione: l’Unione Europea prevede di arrivare a 20 milioni di tonnellate entro il 2030, di cui 10 milioni prodotte e l’altra metà importate. Nell’ottica di valorizzare il ruolo cruciale dell’idrogeno nella riduzione delle emissioni inquinanti e con il fine comune di contribuire ad accelerare lo sviluppo del settore, Italian Exhibition Group e Hannover Fairs International GmbH (HFI), filiale italiana di Deutsche Messe AG, hanno siglato un accordo di collaborazione per l’organizzazione congiunta di un nuovo Salone dell’Idrogeno supported by Hydrogen & Fuel Cells all’interno di KEY – The Energy Transition Expo, l’evento di IEG sulla transizione e l’efficienza energetica, punto di riferimento in Sud Europa, Africa e bacino del Mediterraneo, la cui prossima edizione è in programma alla Fiera di Rimini dal 5 al 7 marzo 2025.
Hydrogen & Fuel Cells
EUROPE è organizzata e gestita da Deutsche Messe AG (DMAG), la più grande società fieristica in Germania e una delle principali a livello mondiale.
Si svolge all’interno di Hannover Messe, la più importante manifestazione europea sull’industria e l’automazione, ed è dedicata all’intero ciclo di vita dell’idrogeno – in particolare di quello verde come sostituto dei combustibili fossili – nell’ambito della trasformazione industriale sostenibile.
Il Salone dell’Idrogeno
Hydrogen & Fuel Cells di diventare, a livello internazionale, il luogo di discussione privilegiato sui temi dell’idrogeno e sulla sua importanza per la transizione energetica, nonché momento di riferimento per i principali player coin volti, per incontrarsi, confrontarsi e soste nere la nascita di nuovi progetti. Il Salone costituisce la naturale evoluzione e il rafforzamento dell’area espositiva di KEY dedicata all’idrogeno, alle sue applicazioni e alla grande opportunità che questo vet tore può offrire per la decarbonizzazione
International GmbH, Sede Italiana.
turin.sepem-industries.com
La fiera delle soluzioni a tutte le tue necessità produttive: servizi, sicurezza, processi, manutenzione.
◦ Workshop, conferenze e tavole rotonde.
◦ Un’offerta dedicata al comparto manifatturiero.
◦ Rafforzare il rapporto professionale con il mercato locale.
Con il patrocinio di:
ora il tuo accredito gratuito:
2023 POSITIVO PER L’INDUSTRIA ITALIANA DELLA MACCHINA UTENSILE 2024 IN LEGGERO CALO. IN RALLENTAMENTO LA RACCOLTA
a cura della redazione
Il 2023 si è confermato anno favorevole per l’industria italiana costruttrice di macchine utensili, robot e automazione. Il nuovo record di produzione è stato però determinato esclusivamente dall’ottimo andamento delle esportazioni; in calo la domanda interna.
Con questi risultati, l’industria italiana di settore si è confermata, ancora una volta, tra i principali protagonisti dello scenario internazionale ove è risultata quinta nella classifica mondiale di produzione e quarta in quella di export e consumo.
Le previsioni per il 2024 sono di calo moderato della produzione: al trend positivo dell’export si contrappone la riduzione delle consegne sul mercato interno che risentono della debolezza della domanda domestica. D’altra parte, il rallentamen-
to della raccolta ordini nella prima parte dell’anno è frutto dell’incertezza del contesto sia in Italia che all’estero.
Questo, in sintesi, è il quadro illustrato dalla presidente di UCIMU-SISTEMI PER PRODURRE Barbara Colombo, questo pomeriggio, in occasione dell’Assemblea dei soci a cui è intervenuto il presidente di CONFINDUSTRIA, Emanuele Orsini, intervistato da Simone Spetia, Radio 24.
Secondo i dati di consuntivo elaborati dal Centro Studi & Cultura di Impresa di UCIMU, nel 2023, la produzione italiana di macchine utensili, robot e automazione ha segnato un nuovo record, attestandosi a 7.615 milioni di euro, per un incremento del 4,6% rispetto al 2022. Il risultato è stato determinato esclusivamente dall’ottimo
riscontro raccolto sul mercato estero: le esportazioni hanno raggiunto il valore record di 4.223 milioni di euro, pari al 21,8% in più rispetto al 2022.
Il consumo è calato, del 7,8%, a 5.816 milioni, penalizzando le consegne dei costruttori italiani scese, dell’11%, a 3.392 milioni di euro, e le importazioni, risultate in calo, del 3%, a 2.425 milioni di euro. Il rapporto export su produzione è tornato a crescere passando, dal 47,6% del 2022, al 55,5% del 2023.
Nel 2023, principali mercati di sbocco dell’offerta italiana sono risultati: Stati Uniti (567 milioni, +17,5%), Germania (359 milioni, +17,2%), Cina (286 milioni, +26,6%), Francia (247 milioni, +28,2%), Polonia (215 milioni, +14,5%), Turchia (211 milioni, +70,9%), Messico (195 milioni, +133,1%), Spagna (130 milioni,
+9,4%), India (117 milioni, +77%), Regno Unito (85 milioni, +44,1%).
Ancora elevato il livello di utilizzo della capacità produttiva, la cui media annua è di poco diminuita, passando dall’86,6% del 2022 all’86,2% del 2023. In lieve calo anche il carnet ordini, che si è attestato a 7,3 mesi di produzione assicurata, contro gli 8 dell’anno precedente.
Il fatturato di settore ha raggiunto la cifra di 11.012 milioni di euro.
Come emerge dalle previsioni elaborate dal Centro Studi & Cultura di Impresa di UCIMU, il 2024 segnerà un leggero arretramento dell’industria italiana costruttrice di macchine utensili, robot, e automazione il cui andamento si manterrà comunque su livelli mediamente alti. Al calo moderato registrato da tutti i principali indicatori economici si contrappone la crescita dell’export che segnerà un nuovo record.
La produzione si attesterà a 7.450 milioni di euro (-2,2%). Le esportazioni, attese ancora in crescita (+3%), raggiungeranno il nuovo record di 4.350 milioni di euro.
A soffrire di più saranno le consegne sul mercato interno (-8,6%) che si fermeranno a 3.100 milioni, penalizzate dalla riduzione del consumo domestico che scenderà (-7,1%) a 5.405 milioni. Anche le importazioni registreranno un calo, fermandosi a 2.305 milioni di euro (-4,9%).
La raccolta ordini dei costruttori italiani
nel primo semestre segna invece il passo. Nei primi sei mesi del 2024, l’indice UCIMU ha registrato un arretramento del 17,3% rispetto allo stesso periodo dell’anno precedente. -18,7% gli ordini interni; -16,2% gli ordini esteri. A determinare questo risultato poco brillante sono soprattutto le condizioni generali di instabilità in Italia e nel mondo.
Transizione 4.0 e 5.0
Barbara Colombo, presidente UCIMUSISTEMI PER PRODURRE, ha affermato: “Dopo un biennio davvero strepitoso, segnato da una crescita a doppia cifra per tutti i principali indicatori economici, il 2023 si è confermato anno favorevole per l’industria italiana di settore che ha messo a segno un nuovo record di produzione. Il risultato positivo è stato però determinato esclusivamente dall’ottimo andamento delle esportazioni che hanno registrato una vera e propria impennata”.
“Questo exploit dimostra, ancora una volta, la flessibilità delle imprese italiane capaci di riorientare rapidamente la propria attività verso i mercati più dinamici. Maha aggiunto la presidente - al tempo stesso, mette in evidenza la chiara debolezza del mercato italiano che, già a fine 2022, aveva cominciato a scricchiolare”.
“D’altra parte, l’andamento della raccolta ordini di questi primi sei mesi conferma la
debolezza della domanda che, sia in Italia che all’estero, subisce l’instabilità del contesto. Per il mercato interno, se questo rallentamento può essere considerato in parte fisiologico, vista l’eccezionale espansione del biennio appena passato, è altrettanto vero che, sul risultato, ha pesato l’incertezza intorno a Transizione 5.0”.
“L’attesa prolungata dell’operatività del provvedimento e la mancanza dei decreti attuativi hanno creato un doppio effetto negativo. Da un lato, hanno determinato la sospensione delle decisioni di acquisto da parte degli utilizzatori, in attesa che il provvedimento fosse chiaro. Dall’altro hanno, almeno in parte, oscurato la disponibilità del provvedimento 4.0 che è tuttora in vigore ma che, per molti operatori, è “finito nel dimenticatoio”.
“Con l’entrata in funzione di Transizione 5.0, che speriamo arrivi a giorni, le imprese manifatturiere italiane avranno l’opportunità di scegliere se operare con uno o con l’altro provvedimento, ben consapevoli che il 5.0 unisce digitale e risparmio energetico mentre il 4.0 continua a insistere esclusivamente sul digitale. E sarà a disposizione un bel plafond di risorse. Si tratta di circa 13 miliardi totali: 6,4 miliardi sono quelli stimati per il 4.0; mentre 6,3 miliardi sono le risorse certe per il 5.0 dal fondo Repower EU”. “Il punto è però che, se non sarà operativa nell’immediato, Transizione 5.0 rischia di veder svanita una parte consistente dei benefici che ha sulla carta. I tempi così compressi tra la disponibilità della misura e il termine di consegna e interconnessione del macchinario (fissato a dicembre 2025), mettono in difficoltà i costruttori italiani che, specializzati nel prodotto super personalizzato, hanno tempi di produzione di circa 6-8 mesi”.
“Anche in considerazione della promessa fatta dal governo di operare a supporto del Made in Italy, crediamo che queste lungaggini siano un vero autogol perché, di fatto, rischiano di favorire prima di tutto gli importatori che dispongono di ampi magazzini”.
“Per tale ragione ritengo che, una volta operativa Transizione 5.0, CONFINDUSTRIA debba intervenire immediatamente presso le autorità affinché si consideri l’allungamento al 2026 della possibilità di utilizzo dei fondi stanziati dall’Europa per tale misura”.
Disponibilità di personale preparato
Le macchine di ultima generazione hanno bisogno di persone capaci di gestirle, programmarle, utilizzarle. Ma imponendo anche una decisa riorganizzazione dell’attività aziendale richiedono approcci innovativi anche per le figure non direttamente legate alla produzione.
“UCIMU per questo ha potenziato, e lo farà ancora di più in futuro, il suo impegno in UCIMU Academy, progetto nel quale rientrano tutte le iniziative dedicate a ridurre il mismatch tra domanda e offerta di lavoro. Dai premi per le tesi, alla collaborazione con gli ITS, passando per tutto il lavoro che facciamo in occasione delle nostre manifestazioni espositive”.
“Tra queste vi è ROBOTGAMES, il nuovo contest di robotica e automazione, per giovani delle scuole secondarie di secondo grado, che presenteranno i loro prototipi di automazione robotica con applicazione al mondo dell’industria. ROBOTGAMES farà il suo debutto alla BI-MU, manifestazione di settore in programma il prossimo ottobre a fieramilano Rho. La giuria dovrà scegliere i 3 migliori tra i 10 team finalisti.
Sono ragazzi appassionati che arrivano da tutta Italia. Questo è un ottimo messaggio per tutti noi che operiamo nel mondo high-tech: le nuove generazioni sono pronte a seguirci, a impegnarsi, applicando la loro creatività all’industria. Noi imprenditori dobbiamo essere sempre più attenti a comprendere le loro aspirazioni, avvicinarli e coinvolgerli”.
Internazionalizzazione
“Stati Uniti, Cina, India, Vietnam e Messico oltre, ovviamente all’Unione Europea, questi sono paesi a cui guardiamo con maggiore attenzione. Esportare è il nostro primo modo di presidiarli ma non può e non deve essere l’unico. Su questo dobbiamo ancora migliorare. In risposta a questa esigenza, su spinta dell’associazione, sono nate le reti di impresa che aggregano diverse aziende del settore in mercati considerati particolarmente attrattivi. Ad oggi ne abbiamo due: ITC India, attiva da oltre 10 anni, a cui si è aggiunta l’anno scorso IMT Vietnam”.
“Strutturarci per essere realmente competitivi sul mercato globale è un processo
lungo. Per questo - ha affermato Barbara Colombo - è importante che le autorità potenzino le risorse destinate a supportare l’attività di internazionalizzazione delle aziende, dalle missioni di incoming di operatori esteri alle fiere internazionali che si tengono in Italia, ai tour di visita alle imprese italiane, ai forum all’estero di presentazione dei settori più attrattivi del made in Italy. Ma penso anche alle iniziative con SACE, per le coperture dell’attività di export, e con SIMEST, per i finanziamenti dei progetti di sviluppo estero così come per la partecipazione alle fiere internazionali che si tengono in giro per il mondo”. “E poi - ha concluso la presidente di UCIMU - osservando i colossi che ci circondano, dobbiamo essere consapevoli che la dimensione delle aziende e anche quella del paese non giocano a nostro favore. Per cui sempre più importante sarà la nostra appartenenza all’Unione Europea all’interno della quale potremo contribuire ad indirizzare programmi, direttive e piani economico-industriali nella misura in cui saremo capaci di presidiare, a tutti i livelli, i tavoli strategici”.
Scopri come i panni per la pulizia Tork exelCLEAN® possono aiutare la tua impresa a risparmiare tempo riducendo i tempi di lavoro del 35% rispetto agli stracci.*
Igiene migliore per una maggiore produttività www.tork.it/riduzionedeirifiuti
LA FIERA ALL4PACK EMBALLAGE RITORNA A PARIGI NEL 2024, CONFERMANDOSI COME UNO DEGLI EVENTI PIÙ IMPORTANTI E ATTESI NEL MONDO DEL PACKAGING E DELLA LOGISTICA di C.G.
Dal 4 al 7 novembre, presso il Paris Nord Villepinte Exhibition Centre, i professionisti del settore si riuniranno per esplorare le ultime innovazioni, tendenze e soluzioni che stanno plasmando il futuro dell’imballaggio, della movimentazione e della catena di approvvigionamento.
Un evento imperdibile per l’industria del packaging
ALL4PACK Emballage è riconosciuta a livello globale come una vetrina d’eccellenza per i leader del settore, fornendo una piattaforma ideale per fare network, la scoperta di nuove tecnologie e la creazione di partnership strategiche. L’edizione del 2024 promette di essere particolarmente innovativa, con un focus su sostenibilità, digitalizzazione e automazione, temi centrali
per affrontare le sfide del mercato globale in continua evoluzione.
Innovazione e sostenibilità al centro della scena
Con l’attenzione sempre maggiore alla sostenibilità, ALL4PACK Emballage 2024 si focalizzerà su soluzioni che riducono l’impatto ambientale, promuovendo l’economia circolare e l’uso di materiali riciclati e biodegradabili. I visitatori avranno l’opportunità di partecipare a conferenze e workshop dedicati a queste tematiche, con la partecipazione di esperti internazionali e case studies di aziende leader.
Quet’anno ci sarà uno spazio uno spazio dedicato alle aziende e alle start-up impegnate in iniziative di riduzione, riciclo e riuso (3R). ALL4PACK Circularity, infatti ospiterà un’agorà che permetterà di affrontare questi temi, nell’ambito di workshop e pitch che
metteranno in luce tutta la dinamicità del settore.
Molte start-up saranno presenti nell’area ALL4PACK CIRCULARITY. Offriranno soluzioni innovative e agili per l’imballaggio e la manutenzione: nuovi materiali, contenitori riutilizzabili e connessi, strumenti di programmazione robotizzata, ecc. Mettere in evidenza queste start-up ne promuoverà la visibilità e sarà per loro un’opportunità per incontrare investitori e industrie utilizzatrici che pongono la circolarità al centro della catena del valore.
Tra le start-up già iscritte:
• BAG’INNOV: Questa piccola azienda a conduzione familiare con sede a Narbonne è specializzata nelle buste flessibili autoportanti. Bag’Innov offre una busta riconosciuta come “Riciclabile”
da CITEO (Francia) o Fost+ (Belgio) da 1,5L a 5L con rubinetto, compatibile per il contatto alimentare e non. Le buste Bag’Innov sono adatte per il confezionamento a caldo (83°) o a freddo, per prodotti senza o con alcool (fino a 50°), per alimenti così come per detersivi o cosmetici. “Partecipare a ALL4PACK EMBALLAGE PARIS 2024 rappresenta una grande opportunità per promuovere la nostra soluzione, che soddisfa già i vincoli ambientali del 2030” Lionel Robert, CEO
• ECOCERT GREENLIFE: “Di fronte alle sfide ambientali, Ecocert ha scelto di rispondere alla crescente domanda di soluzioni sostenibili nel settore dei materiali offrendo certificazioni e garanzie che promuovono l’adozione di buone pratiche.La Business Unit di Ecocert Greenlife, dedicata ai materiali sostenibili, è principalmente interessata alle materie plastiche e offre la certificazione GRS, che garantisce la tracciabilità dei materiali riciclati lungo tutta la catena del valore, rispondendo al contempo alle impegnative sfide ambientali e sociali”. Sylvana Scampini - Responsabile della Business Unit Materiali Sostenibili
• TECNOLOGIA MAGMA:Un sistema di visibilità di nuova generazione per ottimizzare la gestione degli asset logistici. “L’azienda sta trasformando i container in “smart container” con la sua soluzione che combina tecnologie IoT e una piattaforma web. Consente l’accesso istantaneo agli inventari e ottimizza l’uso della base di utenti utilizzando i suoi algoritmi”. Etienne d’OLEON, Direttore Vendite - Gestione Patrimoniale
• OPACK: Il pacchetto del futuro! Riutilizzabile fino a 100 volte e Made in France, riduce i rifiuti di 25 kg e l’impronta di carbonio del 90%, pur essendo più economico del cartone monouso. Il suo punto di forza? Un cuscino gonfiabile brevettato che protegge tutte le spedizioni in 2 secondi. “La fiera ALL4PACK EMBALLAGE PARIS 2024 è l’occasione perfetta per OPACK di mostrare i suoi pacchi innovativi e di concludere partnership strategiche per la logistica circolare e solidale.
• Chrystelle Peltier, CEO di Opack
• PACK ME UP: Specializzata nella produzione di soluzioni di imballaggio sostenibili in Francia, l’azienda si impegna per
l’ambiente. “Durante ALL4PACK EMBALLAGE PARIS, presenteremo il nostro pluriball in carta riciclata e completamente riciclabile, offrendo un’alternativa ecologica ed efficace per proteggere tutti i tipi di prodotti durante la loro spedizione” Marjorie BARHAUD, responsabile vendite
ALL4PACK CIRCULATY andrà ad ampliare il ricco programma di eventi e opportunità di Networking. Oltre all’area espositiva, la fiera offrirà un programma ricco di eventi collaterali, tra cui:
conferenze e tavole rotonde, sessioni con esperti del settore su temi come l’innovazione tecnologica, la sostenibilità e le nuove regolamentazioni; Business Meetings: opportunità di incontri B2B per favorire la creazione di nuove collaborazioni e progetti.
Con oltre 1300 espositori provenienti da tutto il mondo ALL4PACK Emballage 2024 si conferma un appuntamento internazionale di primo piano per chi opera nel settore del packaging e della logistica. Un’occasione unica per scoprire le tendenze future, innovare e restare competitivi in un mercato in continua trasformazione.
MENTRE WIBU-SYSTEMS CELEBRA IL SUO 35° ANNIVERSARIO (1989-2024), I SUOI FONDATORI
OLIVER WINZENRIED, CEO DI WIBU-SYSTEMS AG IN GERMANIA, E MARCELLUS BUCHHEIT, CEO DI WIBU-SYSTEMS USA, HANNO CONDIVISO LE LORO RIFLESSIONI SUL PERCORSO, CHE LI HA PORTATI A DIVENTARE LEADER GLOBALI NELLA GESTIONE SICURA DELLE LICENZE
Daniela Previtali, Global Marketing Director
L’impegno per la continuità aziendale, il progresso tecnologico e la coesione del team ha guidato l’ecosistema aziendale. Guardando al futuro, restano impegnati per indipendenza finanziaria, espansione del mercato e innovazioni pionieristiche, che soddisfino le
esigenze dei clienti.
Riflettendo sui 35 anni di attività, qual è stato il momento in cui avete capito che la vostra visione per l’azienda stava diventando realtà?
Oliver Winzenried: Visti, sul mercato, i primi prodotti per proteggere il software dalla
copia illegale, Marcellus ed io abbiamo avuto l’idea che avremmo potuto fare di meglio e in modo più sicuro. Così, abbiamo iniziato a sviluppare la nostra soluzione. Il punto di svolta è arrivato quando abbiamo ottenuto il nostro primo cliente, che ha ordinato 500 pezzi di Wibu Boxes. Quello è stato il momento, in cui abbiamo capito di avere un
prodotto valido.
La nostra fiducia è cresciuta ancora di più alla prima fiera, cui abbiamo partecipato. Al CeBIT del 1990, abbiamo raccolto oltre 300 contatti in un solo evento. Questo successo locale si è rivelato essere una pietra miliare significativa, che ha aperto le porte a molti nuovi clienti. Abbiamo poi mosso i nostri primi passi in ambito internazionale. Nel 1993, abbiamo partecipato a Comdex Fall a Las Vegas, che ha attirato molti visitatori nordamericani e interesse internazionale. La domanda per il nostro prodotto era chiara, con richieste provenienti da distributori di tutto il mondo.
Siamo diventati fermamente convinti che ci fosse una necessità a lungo termine di una protezione robusta, per contrastare la pirateria del software su PC. Anche se non potevamo allora prevedere l’evoluzione del mercato verso IoT, mondo embedded e dispositivi intelligenti, sapevamo che il mercato era vasto e c’era spazio per più di un fornitore. Questa convinzione ci ha rassicurato che eravamo sulla strada giusta.
Come è cambiata la vostra visione iniziale negli ultimi 35 anni?
Marcellus Buchheit: La risposta breve è che siamo passati dalla protezione del software alla gestione delle licenze software e poi alla monetizzazione dello stesso. Inizialmente, il nostro focus era sulla protezione semplice basata su dongle: il software funzionava solo se la chiave hardware era presente. Tuttavia, i nostri clienti hanno presto richiesto funzionalità
più sofisticate, come date di scadenza per le licenze in abbonamento, contatori di unità per modelli a consumo e possibilità di aggiornare il dongle da remoto, presso il sito dell’utente finale. Questa necessità di maggiore flessibilità ci ha portati ad investire in una gestione dell’intero ciclo di vita delle licenze software.
Quando abbiamo sviluppato CodeMeter, abbiamo reso la licenza del software il nostro focus centrale, pur mantenendo robuste le caratteristiche di protezione. Questo ha portato al concetto di licenza software sicura, con le sue varie opzioni integrabili agilmente nei sistemi ERP. CodeMeter License Central è diventato il pilastro di questo nuovo approccio, in quanto permette ai nostri clienti di gestire modelli di licenza su misura per i vari mercati e clienti.
Questa evoluzione è culminata nella monetizzazione del software: una fase di maturità, in cui assistiamo i nostri clienti nel massimizzare le loro entrate, dando priorità alla gestione efficiente delle loro licenze. Oggi, permettiamo ai nostri clienti di ottimizzare le vendite dei loro prodotti, sfruttando strategie di licenza avanzate e assicurandoci che possano adattarsi alle diverse esigenze dei loro mercati e clienti.
Qual è la fonte delle nuove idee?
OW: Ci sono due fonti principali per le nuove idee: i nostri clienti e i nostri dipendenti. La combinazione delle loro intuizioni e feedback ci aiuta a sviluppare un’architettura di base, che soddisfi tutte le esigenze del mercato.
MB: Ad esempio, inizialmente, credevo che la protezione legata a soli contenitori software non fosse abbastanza sicura rispetto ai dongle. Tuttavia, i nostri clienti hanno espresso una forte necessità di questa alternativa all’interno della nostra architettura. Questo ha portato allo sviluppo di CodeMeter ActLicense e alla incorporazione di tecnologie avanzate come SmartBind, per soddisfare queste esigenze. In seguito, i clienti hanno richiesto l’alternativa CodeMeter Cloud e abbiamo risposto implementandola.
Queste innovazioni dimostrano l’importanza di ascoltare i nostri clienti. Se ci fossimo concentrati esclusivamente sui dongle, probabilmente avremmo perso rilevanza nel mercato. Invece, abbracciando nuove idee dai nostri clienti e dipendenti, seguitiamo a trasformarci e a soddisfare le esigenze in continua evoluzione del settore.
OW: Dimostrazioni della nostra innovazione sono il nostro CodeMeter License Central e License Portal. Queste piattaforme permettono agli ISV e ai produttori di dispositivi intelligenti di distribuire e gestire, in semplicità, le loro licenze all’interno dei loro processi aziendali, consentendo di autogestirle ugualmente anche agli utenti. Le idee iniziali per queste innovazioni sono venute dal nostro team di vendita e sono state perfezionate attraverso una stretta collaborazione con i nostri clienti. Questa combinazione di intuizioni interne e feedback dei clienti è la fonte chiave delle nostre nuove idee.
Quali sono state alcune sfide inaspettate e come le avete superate?
MB: Oliver ed io proveniamo entrambi da background ingegneristici e mancavamo di una formazione formale in ambito aziendale. Inizialmente, abbiamo sottovalutato l’importanza del marketing e delle vendite proattive. Credevamo che un prodotto superiore si sarebbe venduto da solo, ma la realtà ha dimostrato il contrario. Abbiamo dovuto adattarci rapidamente, per sviluppare le nostre strategie di marketing, perseguire attivamente le vendite e stabilire un robusto sistema di supporto, per mantenere soddisfatti i nostri clienti. Questi sforzi fondamentali sono stati cruciali durante i primi anni della nostra azienda.
Una sfida significativa si è verificata poco
dopo la nostra prima esposizione al CeBIT di Hannover. Siamo stati citati in giudizio da un’azienda, che sosteneva che stavamo violando il loro nome, Wibu, nonostante avessimo un marchio registrato per esso. Anche se, alla fine, abbiamo vinto la causa, è stata una distrazione lunga e frustrante dalle nostre attività aziendali principali.
Quando ci siamo espansi in Nord America, abbiamo affrontato un’altra battaglia legale per una presunta violazione di brevetto, che era infondata. Tuttavia, difenderci è stato difficile e, alla fine, ha comportato un costoso accordo, in un momento in cui la nostra azienda era ancora relativamente piccola.
L’espansione in Cina ha portato altre questioni. I concorrenti hanno sostenuto che il nostro dispositivo di sicurezza crittografica non poteva essere importato in Cina. Dopo una revisione approfondita, questa affermazione è stata respinta, permettendoci di continuare a vendere i nostri prodotti nel mercato cinese.
Queste esperienze ci hanno impartito preziose lezioni nel navigare le sfide legali e l’importanza di avere una solida strategia aziendale, oltre a sviluppare una grande tecnologia.
Potete condividere una decisione cruciale che ha significativamente plasmato il percorso dell’azienda?
OW: Tre decisioni cruciali hanno plasmato significativamente il percorso della nostra azienda:
1. Internazionalizzazione: Abbiamo iniziato la nostra espansione internazionale nel 2001 con WIBU-SYSTEMS USA, Inc. e abbiamo continuato nel 2003 con WIBUSYSTEMS (Shanghai) Co. Ltd. Questo passo è stato seguito da ulteriori espansioni in paesi europei, la fondazione di WIBUSYSTEMS K.K. in Giappone nel 2018, e, quest’anno, l’apertura di WIBUSYSTEMS Korea, Ltd. Questa presenza globale ci ha permesso di sfruttare nuovi mercati e ampliare la nostra portata.
2. Evoluzione della protezione dalla copia del software alla gestione flessibile delle licenze: Siamo passati dal concentrarci esclusivamente sulla protezione dalla copia del software per PC alla fornitura di soluzioni di gestione delle licenze altamente flessibili per dispositivi intelligenti e il cloud. Questo cambiamento ha riconosciuto che il software è ormai onnipresente e deve essere gestito in modo dinamico su varie piattaforme.
3. Collaborazioni: Cooperare con istituti di ricerca, fornitori e clienti è stato cruciale. Queste collaborazioni ci aiutano a comprendere le esigenze del mercato più rapidamente e ci permettono di sviluppare ed implementare le ultime tecnologie, combinando conoscenze uniche e specializzate di diversi attori. Questo approccio di reciproco scambio ci ha mantenuti all’avanguardia dell’innovazione.
Guardando indietro, c’è qualcosa che avreste fatto diversamente?
MB: Non proprio. Nel complesso, abbiamo espanso l’azienda con successo, anche se non eravamo sempre sicuri di cosa sarebbe accaduto. Abbiamo commesso errori, imparato dagli stessi ed, alla fine, migliorato grazie a quelle lezioni. Se dovessi cambiare qualcosa di importante dall’inizio, direi di no. Tuttavia, ci sono piccole cose che avremmo potuto fare più velocemente. Ad esempio, abbiamo aperto il primo ufficio di nostra proprietà solo 12 anni dopo la fondazione dell’azienda. Prima di allora, ci affidavamo ai distributori: alcuni erano di successo, altri meno. Abbiamo aspettato troppo a lungo nella transizione dai soli distributori alla loro combinazione con i nostri uffici regionali. Avere i nostri uffici prima ci avrebbe permesso di ottimizzare meglio la nostra strategia in determinati Paesi.
Cosa rende unici i prodotti WibuSystems?
OW: Wibu-Systems offre una soluzione completa, spesso descritta come il coltellino svizzero per la protezione del software, la gestione delle licenze e la sicurezza del software. Ci riferiamo a questo concetto come interoperabilità 4D, grazie al nostro supporto di varie piattaforme di processori come Intel, ARM, MIPS e PowerPC, oltre a numerosi sistemi operativi e piattaforme target. Offriamo diversi tipi di contenitori di licenze, inclusi dongle hardware, software e cloud. Inoltre, forniamo soluzioni che integrano la distribuzione delle licenze nei processi aziendali sia degli ISV che dei produttori di dispositivi.
Permettetemi di evidenziare due punti di vendita unici:
1. Disponibilità a lungo termine: Poiché forniamo i nostri prodotti agli integratori che incorporano le nostre soluzioni nelle loro offerte, la disponibilità a lungo termine è cruciale. Dimostriamo il nostro impegno verso questo obiettivo, offrendo ancora oggi supporto per le prime soluzioni rilasciate dal 1989 in avanti.
2. Alto livello di sicurezza: Le nostre soluzioni hanno ripetutamente dimostrato la loro sicurezza attraverso gare pubbliche riservate agli hacker e hanno ricevuto numerosi premi per la loro robustezza. Inoltre, assistiamo i nostri clienti, se incontrano qualsiasi violazione nel software protetto dalla nostra tecnologia,
assicurando una sicurezza e un supporto continui.
Come dovrebbero vedervi i vostri clienti?
MB: Vediamo il rapporto con i nostri clienti come una partnership a vita. Il nostro obiettivo è che i clienti, che utilizzano i nostri prodotti oggi, continuino a usarli indefinitamente. Questo impegno funziona solo se ascoltiamo attivamente le loro esigenze in evoluzione e le aspettative future, implementandole nei nostri prodotti e mantenendo i più alti livelli di sicurezza, flessibilità e compatibilità con le versioni precedenti.
Qual è una storia meno conosciuta sui primi giorni dell’azienda?
OW: Marcellus ed io ci siamo incontrati presso la stazione radio amatoriale dell’Università di Karlsruhe. Marcellus studiava informatica, mentre io studiavo ingegneria elettrica. È stato lì che abbiamo concepito l’idea di creare un sistema migliore di protezione del software dalla pirateria con un livello di sicurezza più elevato.
Un altro aspetto importante da menzionare è il supporto inestimabile delle nostre famiglie. La nostra prima fiera al CeBIT di Hannover nel 1990 non sarebbe stata possibile senza il loro coinvolgimento. Ci hanno assistito nell’allestimento dello stand, nella creazione del design dello stand e persino nella cura dei piccoli dettagli, come la realizzazione di vestiti di seta per il nostro
staff in fiera. Questo supporto familiare è stato cruciale, per far decollare la nostra azienda nei primi giorni.
Come immaginate il futuro dell’azienda e del settore?
MB: Miriamo a rimanere all’avanguardia della tecnologia e dell’innovazione, mantenendo la nostra flessibilità e compatibilità con le versioni precedenti. Le nostre strategie di successo del passato continueranno a guidarci. Tuttavia, dobbiamo anche riconoscere nuove opportunità di mercato. Molti dispositivi intelligenti vengono attualmente venduti come hardware senza software monetizzato. Questo aspetto presenta una significativa opportunità per noi. Crediamo che, diventando l’hardware gradualmente più standardizzato ed economico, il software risulterà il componente di valore, venduto attraverso abbonamenti, modelli a consumo ed altre opzioni, per le quali abbiamo già soluzioni pronte. Prevediamo anche che i dispositivi di consumo verranno venduti tramite modelli in abbonamento. Invece di un alto costo iniziale, la prima quota coprirà l’hardware, mentre il software sarà venduto, nel tempo, tramite abbonamenti. Da una prospettiva tecnologica, l’IA è un nuovo focus per noi. Pianifichiamo di proteggere il software IA e i modelli IA, dove appropriato, e vediamo l’IA come un’opportunità per migliorare i nostri prodotti, rendendoli più sicuri e flessibili. Inoltre, ci stiamo preparando per le sfide della crittografia post-quantistica. Il nostro
software si basa in modo significativo sulla crittografia asimmetrica; quindi, integreremo il prima possibile nuovi algoritmi, attualmente in fase di sviluppo, per rendere i nostri prodotti validi anche in futuro.
Come vedete il vostro ruolo nell’azienda cambiare nei prossimi dieci anni?
OW: Sono impegnato a garantire il potenziamento continuo e la crescita della nostra azienda, mantenendo l’indipendenza finanziaria e senza vendere l’azienda in futuro. La continuità è cruciale per i nostri clienti, dipendenti e partner. Creando un team di gestione giovane e dinamico, stiamo evolvendo l’azienda in linea con la visione mia e di Marcellus, assicurando innovazione sostenuta e stabilità per tutti gli stakeholder.
MB: Pensate all’azienda come a un corpo umano. Inizialmente, i fondatori sono il cuore: se smettessero di lavorare, l’azienda potrebbe cessare di esistere. Man mano che l’azienda cresce e aggrega più personale, i fondatori diventano il cervello, concentrandosi più su strategia e visione che sulle operazioni quotidiane. Avvicinandosi al pensionamento, o anche dopo, i fondatori rimangono l’anima dell’azienda, assicurando che continui ad operare secondo il loro ideale. Nei prossimi 10 anni, potrei non ritirarmi ancora, ma probabilmente passerò dall’essere il cervello a diventare l’anima, guidando lo spirito e la direzione a lungo termine dell’azienda.
Quale sperate sarà il vostro retaggio e quello dell’azienda?
OW: I miei principi ruotano attorno alla costruzione di partnership fidate con clienti, fornitori e dipendenti. Una cultura di fiducia all’interno dell’azienda consente al nostro staff di raggiungere i suoi obiettivi. L’indipendenza finanziaria è cruciale, poiché permette all’azienda di prendere decisioni liberamente. L’innovazione è essenziale, per affrontare le sfide future in modo efficace. Spero che Wibu-Systems sia sinonimo di protezione del software, gestione delle licenze e sicurezza del software. Il nostro obiettivo è fornire soluzioni, che non solo aggiungono valore aziendale, ma che rimangano anche etiche, eque e sostenibili. Questo retaggio di integrità, innovazione e fiducia è ciò che aspiro venga ricordato sia per me stesso che per l’azienda.
PER RISPONDERE ALLA CRESCENTE RICHIESTA DI SOLUZIONI APPLICATIVE, PNEUMAX POTENZIA LA PROPRIA CAPACITÀ DI OFFRIRE NON SOLO SINGOLI PRODOTTI, BENSÌ SOLUZIONI INTEGRATE
di Fabio Chiavieri
IIl piano di sviluppo in termini di innovazione tecnologica del Gruppo Pneumax prevede di operare su più fronti, da un lato garantire un accrescimento costante di competenze e tecnologie al proprio interno (in questa direzione va ad esempio la costituzione della Pneumax Academy), dall’altro guardando verso operazioni di M&A. Queste ultime realizzate con il duplice obiettivo di assicurare una presenza capillare incrementando il livello di servizio e di implementare rapidamente le competenze relative ad una
specifica tecnologia entrando in settori in espansione caratterizzati da peculiarità ben definite.
Alla base, comunque, c’è sempre la volontà di cogliere nuove tecnologie o processi innovativi che possono essere integrati nei propri prodotti o servizi. L’ultima operazione del Gruppo in ordine di tempo ha visto l’acquisizione del ramo d’azienda meccatronica di Automationware S.r.l., società veneziana di riferimento in Italia per la produzione di attuatori elettrici ad ele-
vate prestazioni, estremamente performanti e applicabili nelle situazioni più estreme, progettati per mantenere elevata efficienza eenergetica e configurabili per controllo cinematico multi asse, fondamentale a supporto delle attuali e future applicazioni industriali e robotiche, mantenendo la medesima denominazione.
La gamma di attuatori lineari e rotativi, si completa quindi con una vasta gamma di soluzioni applicative, inclusa la realizzazione di sistemi cinematici embedded, pneumatici
e meccatronici, applicabili negli impianti di produzione, accelerando il T2M (time to market) in sintonia con connettività e risparmio energetico.
Quali sono le motivazioni alla base di questo piano strategico lo spiega Rossella Bottacini, CEO del Gruppo Pneumax.
«Pneumax è ormai prossima ai cinquant’anni di attività, una storicità che ci ha permesso di essere presente in diversi ambiti e settori, con differenti tecnologie, con proprie business unit e una vasta offerta non solo di prodotti, ma anche di competenze per realizzare soluzioni specifiche e su misura per i clienti. Nella complessità attuale parlare di crescita aziendale è un esercizio assai complesso; i fattori endogeni e molto dinamici entrati in gioco stanno accompagnando un rapido e “ripido” cammino evolutivo della tecnologia, e taluni di questi non sono ancora ben noti. Questo tipo di evoluzione tecnologica interessa qualsiasi ambito dell’innovazione, che sia di prodotto, di processo, culturale, o relazionale. Se negli anni ‘70, le aziende potevano dedicare il giusto tempo per studiare con attenzione un determinato mercato e, conseguentemente, realizzare un prodotto idoneo, oggi a fare la differenza sono le nuove esigenze dei clienti, per soddisfare le quali servono competenze elevate ed integrate, che combinano prodotti, tecnologie e nozioni applicative. Portare la soluzione e il sistema al cliente è una delle strategie primarie che consente alle aziende di affrontare un futuro che non è più domani ma che è già ieri. Oggi i clienti non chiedono solo un prodotto, ma quello che possiamo realizzare per soddisfare le sue esigenze e come possiamo realizzarlo. Partendo da questi presupposti, la strategia di Pneumax è
stata improntata proprio a ricercare una realtà che condividesse, prima del prodotto, la nostra visione di proporsi al cliente con una capacità di analisi delle problematiche per risolverle insieme. E’ un approccio differente: studiare soluzioni custom per il cliente coinvolgendo le strutture tecniche e commerciali, forti di un know-how già riconosciuto a livello globale.»
Automationware è una realtà italiana che rappresenta un punto di riferimento nell’ambito delle tecnologie e delle soluzioni che propone, detenendo delle competenze applicative molto apprezzate dagli addetti ai lavori, proprio per questa ragione Pneumax ha deciso di acquisire il ramo meccatronico dell’azienda e di integrarla al proprio interno non solo per quanto riguarda gli aspetti commerciali e produttivi, ma anche a livello marketing,
mantenendo il riferimento ad un brand che è sinonimo di qualità e tecnologia. Questa acquisizione segna un passo significativo nella strategia di Pneumax, una operazione facilitata dalla profonda compatibilità industriale e dalla visione a lungo termine che caratterizza il Gruppo Pneumax, rendendolo il partner ideale per portare avanti questa parte dell’attività.
Un approccio applicativo differente
Automationware produce un’ampia gamma di prodotti che vengono integrati per offrire soluzioni meccatroniche applicative.
«Non partiamo dall’attuatore, ma dallo studio del problema – spiega Fabio Rossi, CEO di Automationware. - Questo significa che, se il cliente ha una problematica di attuazione complessa, noi abbiamo la capacità di mettere in gioco un’esperienza frutto di applicazioni in diversi ambiti, quindi con richieste di integrazione molto eterogenee, e di proporre soluzioni che uniscono, un po’ come in un lego, i nostri prodotti. Oggi, come parte del Gruppo Pneumax, possiamo integrare nell’offerta anche tutto il portafoglio di prodotti realizzati dal Gruppo, creando una proposta di valore multi-tecnologica offrendo soluzioni che integrano componenti elettrici e pneumatici. Esistono applicazioni estremamente complesse, la cui soluzione non può essere risolta banalmente attraverso l’attuazione elettrica, ma si deve trovare a livello ingegneristico.
I nostri attuatori elettrici sono perfettamente in linea con le tendenze tecnologiche del futuro che si basano su risparmio energetico e su sostenibilità ambientale, intesa come minore inquinamento e basso impatto degli impianti»
L-Actuators
Assi lineari con movimentazione a cinghia o a vite con ricircolo di sfere, combinabili tra loro o con altri prodotti AW per infinite possibilità di configurazione. Le configurazioni a catalogo hanno la possibilità di inserire il sistema di diagnostica proprietario AwareVu™ per una verifica in tempo reale del ciclo di lavoro e la prevenzione di blackout produttivi
E-Actuators
Attuatori elettrici AW ad elevate prestazioni, con viti a ricircolo di sfere. Una gamma di famiglie per applicabilità su spazi ridotti e/o su carichi elevati (si utilizzano viti con carichi dinamici fino a 750kN, su progettazione AutomationWare). Qualità di altissimo livello. Viti e chiocciole selezionate per risolvere le applicazioni più complesse e costruite dai leader di mercato.
SM-Soluzione modulare per sistemi di handling o Pick & Place
Sliders (slitte) lineari componibili e totalmente controllati nel movimento da motori Brushless ad elevate prestazioni. Le Slitte SM sono disponibili in 3 versioni per carichi, corse e velocità variabili, anche supportando Payload elevati. Il posizionamento e il movimento sono totalmente controllati elettronicamente garantendo precisioni fino a 0,01mm con totale controllo e modellazione del ciclo di moto.
Oggi il Gruppo può contare su una nuova filiale in grado di fornire competenza, servizio e tecnologia per incrementare la velocità di innovazione, talvolta più importante dell’innovazione stessa, ed entrare in nuovi settori con soluzioni e applicazioni dedicate, avvalendosi altresì del supporto di application engineer indispensabili per comprendere e soddisfare le esigenze dei clienti in tutto il mondo.
Digitali ed etici
All’interno del dinamismo con cui si muove il mercato, si susseguono nuovi paradigmi produttivi che lasciano poco tempo alle imprese di ragionare su come muoversi, ma semmai spingono verso una capacità di reazione pressoché “real time”.
L’innovazione tecnologica accelera a un ritmo esponenziale, creando un circolo vizioso in cui le nuove tecnologie sostituiscono rapidamente quelle vecchie, presenta una visione complessa e sfidante del futuro ed è necessario trovare un equilibrio tra noi e ciò che vogliamo dalla tecnologia. L’accelerazione dei cambiamenti ci richiede di adottare nuovi strumenti di lavoro che ci aiutino a comprendere in anticipo le sorprese positive o i problemi che dovremo affrontare, sia che si parli di Industria 5.0 o di Intelligenza artificiale.
«Si tratta di capire come verranno declinati tali concetti e con quali norme verranno disciplinati – dice Rossella Bottacini. Sicuramente ogni “rivoluzione” industriale ha delle proprie caratteristiche specifiche che se da un lato sicuramente possono contribuire a far crescere l’azienda, dall’altro richiedono delle regole “sburocratizzate” che supportino le aziende in un percorso di crescita sostenibile. Parliamo per esempio di intelligenza artificiale, di cui ci stiamo già avvalendo a supporto di specifici processi interni. È fuori di dubbio che il suo utilizzo nasconde potenzialmente enormi benefici, ma dobbiamo essere in grado di comprenderne le potenziali implicazioni e trovare la modalità di governarla in modo responsabile. La mole di informazioni di cui disponiamo oggi è inestimabile e questo ci porterebbe a sostenere che tutto è più semplice, ma viviamo nell’epoca dell’incertezza e proprio per questo dobbiamo sempre più allinearci a nuovi paradigmi, pensare e argomentare “fuori dagli schemi”, ponendo la massima attenzione al rispetto dell’etica, dei valori e al rispetto del prossimo»
Risparmia energia e riduci gli sprechi con soluzioni di automazione industriale progettate per rendere più efficiente la produzione.
MACCHINE MULTITASKING E RETTIFICATRICI
GRAZIE ALLE LORO CARATTERISTICHE DI PRECISIONE, VELOCITÀ, USABILITÀ E INTERCONNESSIONE IN OTTICA INDUSTRIA 4.0, LE MODERNE MACCHINE MULTITASKING E RETTIFICATRICI SONO IN GRADO DI RISPONDERE ALLE ATTUALI ESIGENZE DI LAVORAZIONE E COMPETITIVITÀ DEL MERCATO
IIn un settore industriale oggi sempre più competitivo, quale quello della moderna meccanica, le aziende hanno bisogno di lavorare rapidamente, riducendo i costi di manutenzione e attrezzaggio e incrementando le tipologie di operazioni effettuabili in un’unica macchina. L’utilizzo di macchine multitasking moderne e robuste, supportate da attrezzatura e utensileria di alta qualità, permette agli operatori del settore di lavorare componenti meccanici di valore garantendo precisione, efficienza, produttività, elevata vita utensile e sicurezza.
Come ben noto, la principale caratteristica di queste macchine è quella di offrire la possibilità di eseguire diverse operazioni
di lavorazione su un singolo pezzo senza necessità di spostarlo. Grazie ad esse, infatti, è possibile combinare tornitura, fresatura, foratura, maschiatura e altre lavorazioni, tutte all’interno della stessa macchina, riducendo il numero delle fasi di lavorazione ed il flusso di semilavorati in transito e consentendo, quindi, di usufruire di un processo completo, sempre più integrato e affidabile. Aspetti di fondamentale importanza per la riduzione del tempo ciclo e, parallelamente, dei costi di produzione.
I punti di forza delle macchine multitasking includono efficienza, precisione, flessibilità, riduzione dei costi e ottimizzazione dello spazio. Si tratta, infatti, di macchine che
consentono di completare più operazioni in un unico setup, riducendo le movimentazioni del pezzo e, quindi, i tempi di produzione, abbassando i costi di manodopera e di attrezzaggio e migliorando la produttività; di mantenere il pezzo nella stessa posizione durante le diverse operazioni, con una riduzione degli errori di allineamento e la garanzia di una maggiore precisione dimensionale; di lavorare una vasta gamma di materiali e realizzare componenti complessi con geometrie elaborate; di migliorare la qualità del pezzo grazie alla riduzione delle movimentazioni e al mantenimento della precisione durante tutte le fasi di lavorazione; ed infine, usufruendo di un’unica macchina, di occupare meno spazio rispetto a più macchine separate.
Queste macchine permettono quindi di svolgere lavorazioni molto precise che garantiscono ripetibilità. Al conseguimento di questo obiettivo, oggi, concorre anche un’utensileria di alta qualità che garantisce la realizzazione di ogni componente con tolleranze minime, riducendo gli scarti e migliorando la qualità del prodotto finale. L’utilizzo di utensili di qualità superiore assicura inoltre una maggiore durata della vita utensile, altro aspetto di fondamentale
importanza. Se utilizzati con ideali strategie di lavoro e corretti parametri di taglio, gli utensili di qualità superiore durano di più e mantengono le loro caratteristiche di taglio più a lungo, riducendo i tempi di fermo macchina per la sostituzione o riaffilatura degli utensili. Questo porta ad un aumento ulteriore dell’efficienza produttiva e una riduzione dei costi.
In alcuni casi, grazie allo sviluppo di tecnologie avanzate, il concetto di macchina multitasking, tradizionalmente associato all’integrazione in un’unica macchina di processi di tornitura e fresatura, permette di incorporare anche diversi processi di asportazione, e di rettifica, consentendo una soluzione “all in one”. L’operazione di rettifica, in particolare, rappresenta la fase che, nel processo di lavorazione, richiede maggior precisione e permette di concludere lavorazioni di pezzi industriali ad alto valore aggiunto.
Tuttavia, quando si vuole ottenere una superficie di alta qualità e precisione, con una tolleranza dimensionale e geometrica molto stretta, è opportuno avvalersi di una rettificatrice. Le rettificatrici, infatti, sono macchine specializzate nell’operazione di finitura che segue la sgrossatura, necessaria per portare il pezzo nello stato di forma o superficie ottimale di progetto, utilizzando una mola abrasiva come utensile. Queste macchine consentono di raggiungere uno speciale grado di finitura e misure e rugosità dell’ordine del millesimo di millimetro.
Si tratta di un processo complesso che richiede attenzione ed esperienza e che si differenzia in base al tipo di “rettifica”, al macchinario usato, alla morfologia del componente da lavorare e alla direzione di movimento della mola (rettifica in tondo/cilindrica, a tuffo, in piano, senza centri e verticale).
Nei settori in cui vengono richieste precisione, qualità e finitura superficiale, le rettificatrici sono ancora, oggi, macchine fondamentali.
La crescente richiesta di componenti rettificati con alta precisione e finiture estreme da parte di segmenti di mercato specifici, quali la mobilità ibrida ed elettrica, l’aerospace, l’orologeria, la micromeccanica, il medicale, l’elettronica e l’elettromeccanica, ad esempio, sta spingendo i produttori di macchine utensili verso la produzione di soluzioni di rettifica altamente produttive.
Se dunque le rettificatrici sono specializzate nella lavorazione di superfici con elevata precisione e finitura, le macchine multitask sono versatili nella lavorazione di pezzi complessi con diverse operazioni.
Inoltre, per soddisfare le crescenti richieste di mercato in tema di gestione macchina, le moderne macchine multitasking e rettificatrici sono dotate di soluzioni di controllo numerico avanzate e di tecnologie e funzionalità digitali per lo scambio dei dati e la manutenzione predittiva, nonchè di sistemi di ispezione e misura che rispondono alle esigenze di ogni tipologia di lavorazione, anche le più complesse. Questi sistemi, nel loro insieme, anche grazie alla simulazione digitale e all’intelligenza artificiale, consentono di disporre di piattaforme intuitive e integrate che permettono la visualizzazione e il monitoraggio dei processi, dando quindi l’opportunità in un’ottica di Industria 4.0 di prendere decisioni basate sui dati, sia per migliorare la produzione che per prevenire e agire preventivamente su eventuali criticità, rendendo possibile visibilità e accessibilità in tutta la fabbrica.
GRAZIE A KNOW-HOW E COMPETENZA, R.F. CELADA OFFRE AI PROPRI CLIENTI LE MIGLIORI SOLUZIONI TECNICHE POSSIBILI E SERVIZI DI QUALITÀ PER UNA MAGGIORE COMPETITIVITÀ SUL MERCATO
R.F. Celada è un attore chiave nel mercato italiano delle macchine utensili, specializzato nell’importazione e nell’ottimizzazione di macchine utensili di eccellenza. Tra i prodotti commercializzati da R.F. Celada, ci sono anche le macchine Multitasking, ad oggi tra le più evolute e ricercate del settore: nello specifico, le Okuma Multus per differenti modelli e taglie.
Le macchine utensili multitasking (o, come suggerisce il nome, “multi funzioni”) sono macchine CNC (Controllo Numerico Computerizzato) che possono eseguire diverse operazioni di lavorazione su un singolo pezzo senza necessità di spostarlo. Queste operazioni possono includere tornitura, fresatura, foratura, maschiatura e altre lavorazioni, tutte all’interno della stessa macchina.
I punti di forza delle macchine multitasking includono:
1. efficienza: consentono di completare più operazioni in un unico setup, riducendo i tempi di produzione e migliorando la produttività;
2. precisione: mantenendo il pezzo nella stessa posizione durante le diverse operazioni, si riducono gli errori di allineamento e si garantisce una maggiore precisione dimensionale;
3. flessibilità: possono lavorare una vasta gamma di materiali e realizzare componenti complessi con geometrie elaborate;
4. riduzione dei costi: riducendo il numero di setup e movimentazioni del pezzo, si abbassano i costi di manodopera e di attrezzaggio;
5. ottimizzazione dello spazio: un’unica macchina multitasking occupa meno spazio rispetto a più macchine separate necessarie
per le singole operazioni;
6. qualità del pezzo: miglior controllo della qualità del pezzo grazie alla riduzione delle movimentazioni e al mantenimento della precisione durante tutte le fasi di lavorazione.
In sintesi, le macchine utensili multitasking offrono vantaggi significativi in termini di efficienza, precisione, flessibilità e costi, rendendole una scelta ideale per molte applicazioni industriali.
Utilizzare attrezzatura e utensileria di qualità nell’asportazione truciolo su macchine a controllo numerico (CNC) multitasking, è di fondamentale importanza per diverse ragioni.
In primo luogo, queste macchine permettono di svolgere lavorazioni molto precise che assicurano ripetibilità. L’utensileria di alta qualità garantisce che ogni componente venga realizzato con tolleranze minime, riducendo gli scarti e migliorando la qualità del prodotto finale.
Possono inoltre eseguire più operazioni senza dover spostare o scaricare il pezzo, il che riduce i tempi di lavorazione e aumenta la produttività. Tuttavia, questo è possibile solo se si utilizzano attrezzature e utensili adatti, capaci di gestire diverse operazioni (come tornitura, fresatura, foratura, etc.) senza perdere precisione ed efficienza. Un altro aspetto importante è la durata della vita utensile.
Utensili di qualità superiore, se utilizzati con ideali strategie di lavoro e corretti parametri di taglio, durano più a lungo mantenendo le loro caratteristiche di taglio, riducendo i tempi di fermo macchina per la sostituzione o riaffilatura degli utensili. Questo porta ad un aumento dell’efficienza produttiva e una riduzione dei costi operativi.
Infine, l’uso di attrezzatura e utensileria adeguate su macchine
multitasking come le Okuma Multus, note per la loro robustezza, contribuisce a migliorare la sicurezza operativa.
Strumenti ben progettati e mantenuti riducono il rischio di guasti e malfunzionamenti, proteggendo gli operatori e prevenendo danni alle macchine stesse.
In conclusione, l’utilizzo di macchine multitasking moderne e robuste, supportate da attrezzatura e utensileria di alta qualità, permette di lavorare componenti meccanici di valore garantendo precisione, efficienza, produttività, elevata vita utensile e sicurezza in un settore industriale che è sempre più competitivo.
Sono diverse le possibilità offerte da R.F Celada a livello di asservimento per macchine multitasking e rettifiche, mediante le isole con processi complessi completamente customizzate per i clienti: vengono esaminati nel dettaglio tempi ciclo, di manipolazione pezzo e autonomia di lavoro non presidiato.
In questi anni, Celada ha maturato una grande esperienza a riguardo, riuscendo ad interfacciarsi con sistemi complessi, come visioni 3D per la presa e la messa in fase dei pezzi (orientamento), per la pallettizzazione su piani con interfalde, ma anche, a livello di correzioni offset utensili, grazie ai propri software, con diversi modelli di macchine di misura nelle quali la correzione avviene in modo incrementale in base all’usura dell’utensile stesso.
Lo studio e lo sviluppo del gestionale proprietario C-FAS permette ai clienti di visionare tutto il processo produttivo in tempo reale, così come lo stato macchina e il lavoro in atto e di mettere in sequenza, con differenti gradi di priorità, diverse mansioni, in modo da rendere l’asservimento della cella autonomo e smart.
Si passa quindi a sistemi più semplici, come le Smart Cell, in cui l’esigenza di continui cambi di produzione è reale, di conseguenza, la velocità e la facilità di riprogrammazione e riattrezzaggio sono essenziali. L’interfaccia per la programmazione è intuitiva in stile App, con cicli di lavoro già preimpostati tramite i quali il cliente sceglie, con delle semplici azioni per la manipolazione del pezzo, tra madrino, contromandrino e inversioni varie.
Anche in questo caso, si ha la possibilità di interfacciarsi con diversi dispositivi, come macchine di misura, nastri trasportatori o carichi/scarichi da pallet.
Inoltre, con le Smart Cell, si può spostare fisicamente l’automazione da un Multitasking ad un altro con un semplice transpallet, essendo settabili fino a quattro posizioni su quattro macchine diverse.
Digitalizzazione delle rettificatrici OKUMA per l’Industria 4.0
In ambito industria 4.0, R.F. Celada ha iniziato la propria trasformazione digitale assieme ai propri clienti, ponendo le fondamenta delle imprese del futuro e fornendo macchine in grado di soddisfare le esigenze di digitalizzazione. Attraverso l’integrazione di tecnologie digitali avanzate, l’azienda ha reso possibile l’automazione avanzata in linea con i requisiti di Industria 4.0, migliorando significativamente l’efficienza operativa e riducendo i tempi di fermo.
La sfida
Le rettificatrici OKUMA non sempre rappresentano una soluzione accessibile per le officine meccaniche. Tuttavia, la realizzazione di un sistema di automazione può costituire un aumento significativo nella produttività che giustifichi l’investimento in una macchina di eccellenza. La normativa italiana richiede che le celle robotizzate siano dotate di recinzioni e sensori di sicurezza per evitare l’accesso durante le operazioni, il che comporta inevitabili fermi impianto
per qualsiasi intervento manuale necessario. Questi fermi riducono notevolmente il beneficio dell’automazione rispetto all’utilizzo di una macchina singola.
La soluzione
R.F. Celada ha sviluppato un sistema di correzione utensili remoto, basato su una piattaforma software avanzata che consente la gestione e l’intervento sulle rettificatrici OKUMA e sui sistemi robotizzati senza interrompere il ciclo operativo. Questo sistema offre:
• monitoraggio in tempo reale: una dashboard intuitiva consente di visualizzare e analizzare i dati operativi delle macchine in tempo reale, facilitando il controllo e la supervisione continua;
• correzioni da remoto: grazie al software, gli operatori possono effettuare interventi di correzione utensili senza dover fermare la macchina o accedere fisicamente alla cella robotizzata, evitando così i tempi di fermo.
Il caso di successo
Un esempio di successo è rappresentato da un’importante officina meccanica italiana che ha implementato questa soluzione. Prima dell’adozione del sistema, l’azienda doveva fermare frequentemente le operazioni per effettuare correzioni manuali, con conseguenti perdite di produttività.
Dopo l’integrazione del sistema di correzione utensili remoto di R.F. Celada, l’officina ha riportato i seguenti miglioramenti:
• eliminazione dei tempi di fermo per correzioni: gli interventi di correzione sono stati completamente automatizzati e possono essere effettuati senza interrompere il ciclo operativo delle macchine, garantendo una continuità produttiva;
• miglioramento della produttività: la produttività è aumentata sensibilmente, grazie alla possibilità di operare senza interruzioni e alla maggiore efficienza delle macchine e dei robot.
SOLUZIONI IBRIDE
DI HARD TURNING
E RETTIFICA DI FINITURA PER MAGGIORE
PRODUTTIVITÀ, PRECISIONE E FLESSIBILITÀ
HHembrug Machine Tools, azienda del gruppo spagnolo Danobat, produttore di un’ampia gamma di rettificatrici di alta precisione, ha sviluppato 3 diverse soluzioni ibride di hard turning e rettifica di finitura. Integrando i due processi di finitura su un’unica macchina, già nota per le sue elevate prestazioni in termini di precisione, stabilità termica e affidabilità, si sono ottenuti considerevoli vantaggi in termini di produttività, precisione e flessibilità.
Esigenze specifiche
Come è noto, l’hard turning di alta precisione offre considerevoli vantaggi nella produzione di pezzi dalle forme complesse, dove è richiesta una combinazione di lavorazioni di diametri esterni e interni in un unico set-up o in presenza di lotti di piccole dimensioni. In altri casi, quali la lavorazione di particolari lunghi e a sezione sottile, grandi superfici interrotte, diametri interni di piccole dimensioni, applicazioni in grande serie, richiesta di finiture superficiali prive di micro-spirali o comunque non raggiungibili dagli utensili di tornitura, la rettifica resta la scelta migliore. La disponibilità di questi due processi in un’unica macchina, stabile e precisa, offre all’utilizzatore la possibilità di sfruttare
i punti di forza e le capacità di ciascuna tecnica di lavorazione. Le esigenze di ogni cliente e di ogni applicazione possono essere molto diverse, grazie alle MikroTurnGrind di Hembrug è possibile ridurre il numero di fasi di lavorazione, i tempi di set up, conseguentemente i costi di movimentazione, stoccaggio e produzione.
La gamma
Quando si parla di macchine ibride, Hembrug mette a disposizione una gamma completa composta da 3 modelli distinti, ognuno pronto a rispondere alle specifiche necessità del cliente.
MikroTurnGrind 1000
Il MikroTurnGrind 1000, il primo modello ad essere presentato al mercato, è una vera e propria macchina ibrida per hard turning e rettifica di finitura. La macchina è dotata di un asse B dove alloggiano la torretta porta utensili di tornitura ed i mandrini di rettifica per interni e per esterni. Essendo una macchina che privilegia la flessibilità, i mandrini di rettifica nascono per l’utilizzo di mole CBN ad alta velocità per lavorazioni di rettifica in contornatura. Resta comunque possibile utilizzare
mole convenzionali profilabili. Sono ovviamente integrabili tutti gli accessori e le opzioni necessarie per sfruttare pienamente i processi di rettifica (sistemi di diamantatura, lunette di supporto, misuratori, ecc.) e di tornitura (tool setter, tastatori di misura, ecc.). Essendo dotata di contropunta, MikroturnGrind consente lavorazioni a sbalzo e tra i centri, di pezzi con dimensioni massime: diametro 380mm, lunghezza 1.000mm, peso 100kg. MikroTurnGrind 1000 è la soluzione ottimale per una produzione flessibile e di alta precisione nel settore dei cuscinetti, mandrini e accessori per macchine utensili, stampi e matrici, componenti oleodinamici, motori elettrici e componenti meccanici della trasmissione, senza dimenticare i repartidi prototipazione.
MikroTurnGrind 100
La MikroTurnGrind 100 nasce dal Mikroturn 100, la macchina best seller di Hembrug, sul quale vengono installati la torretta di tornitura a 8 o 12 posizioni e un elettromandrino di rettifica.
La versione standard prevede un mandrino da 60.000 Rpm, ma è possibile scegliere all’interno di un’ampia gamma di mandrini ad alta frequenza. Il mandrino viene normalmente utilizzato per la lavorazione di fori di piccole dimensioni o fori e facce con superfici interrotte.
L’unità di rettifica ha un sistema di bloccaggio rapido e preciso per consentirne l’eventuale rimozione in caso di suo inutilizzo, di ingombri sul pezzo, di necessità di lavorazione con contropunta. A completamento dell’offerta di lavorazioni ibride disponibili sul modello MikroTurnGrind 100, nel caso di necessità di elevate finiture superficiali su pezzi montati tra i centri, è possibile integrare un’unità di finitura con pietra abrasiva. Si tratta di un processo stabile e perfettamente integrato nella macchina, completo di sensoristica e cicli di programmazione. MikroTurnGrind 100 è la scelta ottimale per una produzione flessibile e anche di serie nel settore degli ingranaggi, particolari oleodinamici, accessori per macchine utensili, stampi e matrici.
MikroTurnGrind Vertical
La MikroTurnGrind Vertical è la proposta Hembrug per la tornitura e la rettifica di finitura, adatta a pezzi più grandi, fino a 1.000 mm di diametro e 300 mm di altezza. Si tratta di un vero e proprio centro di finitura con un magazzino portautensili di tornitura e di rettifica a 46 posizioni. Un secondo magazzino consente il cambio automatizzato delle tre unità di lavorazione: unità di tornitura, mandrino di rettifica e/o mandrino di fresatura. L’attacco di serraggio dell’unità di tornitura o di rettifica sull’asse Z è costituito da un giunto Hirth di
comprovata precisione, affidabilità e robustezza a lungo termine. Il mandrino di rettifica ha una velocità fino a 12.000 giri/min. e dispone di un asse B con un intervallo di +/- 115°. Come per la versione orizzontale, sono integrabili tutti gli accessori e le opzioni necessarie per sfruttare pienamente sia i processi di rettifica che di tornitura. MikroTurnGrind Vertical risponde alle richieste di produzione flessibile nel settore dei cuscinetti, componenti e accessori per macchine utensili.
Fattori di successo per un processo ibrido
Precisione, stabilità termica e strutturale, smorzamento delle vibrazioni e affidabilità sono caratteristiche delle macchine Hembrug, che da decenni rendono questa azienda il punto di riferimento mondiale per le operazioni di Hard Turning e finitura in generale.
Ogni macchina viene assemblata sopra una rigida struttura monolitica di granito naturale. Per garantire un’elevata precisione ogni organo in movimento è montato su un sistema di sostentamento idrostatico sviluppato internamente da Hembrug. Questo sistema esente da usura, in cui le parti in movimento sono separate da una sottile pellicola di olio lubrificante, offre caratteristiche superiori di smorzamento delle vibrazioni. Inoltre, garantisce che ogni macchina continui a fornire la stessa precisione anche dopo 20 anni di utilizzo. Il mandrino principale idrostatico ha un’accuratezza di run-out di < 0,1 micron, assi X e Z idrostatici con una precisione di ripetizione di 0,2 micron e di posizionamento di < 1 micron.
Un processo ibrido offre davvero grande flessibilità, precisione e vantaggi economici, soprattutto per i produttori di piccole e medie serie e di un’ampia varietà di tipi di pezzi. Le macchine MikroTurnGrind di Hembrug hanno dimostrato di poter sostituire con un’unica macchina processi multipli che richiedono tempistiche e lavoro elevati. Non solo, ma ogni macchina offre una precisione insuperabile sia nell’hard turning che nella rettifica di finitura. Un elemento di forte differenziazione è che queste caratteristiche sono garantite nel tempo. Questo rende le macchine MikroTurnGrind un investimento in cui la precisione della macchina si mantiene anche dopo decenni di utilizzo.
La vendita e il servizio di assistenza in Italia delle macchine HEMBRUG sono curati dalla DANOBAT Srl danobatsrl@danobat.com www.hembrug.com www.danobat.com
La testa speciale progettata con asse controllato per l’alimentazione dell’olio da taglio, tramite uno specifico utensile-ugello, orbita intorno all’asse mandrino e attorno al proprio asse per garantire un flusso costante e tangenziale al punto di contatto molapezzo.
GRAZIE ALL’OFFERTA COMPLETA E ARTICOLATA, ALL’ESPERIENZA E ALLA
CAPACITÀ DI OPERARE CON APPROCCIO DI MULTIDISCIPLINARITÀ E FLESSIBILITÀ
PROGETTUALE, MCM CONSENTE AI PROPRI CLIENTI DI SODDISFARE LE ESIGENZE
CAVVALENDOSI DI UN UNICO PARTNER MACCHINE
Con l’ambiziosa prerogativa di poter rispondere ad ogni esigenza produttiva grazie a soluzioni flessibili e modulari, la gamma che MCM ha messo a punto nel corso degli anni è decisamente ampia e trova naturale applicazione là dove precisione, affidabilità e flessibilità sono requisiti fondamentali.
L’obiettivo è quello di proporre un processo completo, sempre più integrato ed affidabile.
La gamma dei centri di lavoro MCM, che comprende le famiglie Clock EVO, Tank EVO, Tank.G e Jet-Five, copre volumi di lavoro da 800 mm fino a 12.000 mm e oltre. Tutte le macchine sono concepite per dare ampie possibilità di configurazione, principalmente in termini di corse, lay-out e prestazioni. Sono disponibili a 4 e a 5 assi e tutte possono essere proposte in versione multitasking.
I centri di lavoro multitasking di MCM sono capaci di combinare
operazioni di tornitura, fresatura, rettifica e power skiving, oltre a consentire l’ottimizzazione del lay-out all’interno del sito produttivo, riducendo il numero delle fasi di lavorazione ed il flusso di semilavorati in transito. Aspetti, questi, che sono di fondamentale importanza per la riduzione del tempo ciclo e, parallelamente, dei costi di produzione. Di seguito, alcuni esempi di impianti multitasking realizzati su misura per specifiche esigenze.
CLOCK 1000 EVO Multitasking per operazioni di fresatura e rettifica
CLOCK 1000 EVO è un centro di lavoro ottimizzato per fresatura e rettifica progettato appositamente per ottimizzare le operazioni di rettifica e la distribuzione localizzata di lubrificante nell’area di asportazione materiale.
Una testa speciale progettata da MCM con asse controllato per l’alimentazione dell’olio da taglio, orbita intorno all’asse mandrino (con l’utensile di lavoro) quindi garantisce un flusso costante dell’olio orientato verso il punto di abrasione della mola. Gli ugelli possono ruotare anche su loro stessi, e questo doppio movimento rotatorio consente di orientare il getto di refrigerante nella direzione ottimale durante l’operazione di rettifica. I due assi rotanti appartenenti allo strumento ugello sono rigorosamente guidati dallo sviluppo CAD-CAM. Funzionano in coordinazione con tutti gli altri assi della macchina al fine di ottimizzare l’erogazione del refrigerante nella zona corretta. Lo scambiatore di utensili può gestire sia gli ugelli che gli utensili per rettifica o fresatura.
La macchina è inserita in un impianto FMS con manipolazione dei pezzi robotizzata. La linea include robot Fanuc su navetta, binario di scorrimento, posti di carico/scarico, posti di stoccaggio pallet (forniti da MCM) e macchine per elettroerosione (EDM), stazione di lavaggio, isola robotizzata di sbavatura (forniti da terzi).
Il sistema, che rappresenta un grande esempio di integrazione, è installato presso un’azienda spagnola leader nel settore aerospace, controllata da uno dei principali produttori di motori aeronautici a livello mondiale.
La collaborazione tra MCM e un’importante società spagnola nel settore delle trasmissioni risale al 2010, con la fornitura di un impianto di produzione flessibile (FMS) composto da quattro centri di lavoro Tank 1300 a 5 assi multitasking per la fresatura, foratura, tornitura, e rettifica di componenti di precisione. L’azienda cliente sviluppa soluzioni e componenti per la trasmissione di potenza per svariati settori industriali.
Prodotti come frizioni, freni, cambi, indicatori, camme, sistemi di rotazione etc., con alti livelli di complessità ed estrema precisione.
L’impianto è stato implementato in step successivi grazie alla modularità dell’automazione di MCM ed a speciali soluzioni studiate con il cliente per andare incontro alla necessità della produzione di pezzi di estrema precisione anche in modalità non presidiata.
L’esigenza iniziale del cliente consisteva nel lavorare diversi componenti effettuando operazioni di fresatura, foratura, tornitura e rettifica sulla stessa macchina. Nella linea attualmente installata, le prime due macchine sono interfacciate da un magazzino utensili “Mirror” condiviso con 740 utensili che consente ai due centri di lavoro di sfruttare le stesse risorse, ottimizzando così l’impiego degli utensili e saturando le ore di lavorazione disponibili. La terza e la quarta macchina, dispongono invece, di un proprio magazzino da 399.
Il progetto ha richiesto fin dall’inizio un grande lavoro di personalizzazione soprattutto a causa del poco spazio disponibile. Le macchine sono state quindi incassate, come pure le postazioni operatore, per risolvere un problema di altezze, mentre è stata utilizzata una nuova parte di capannone per contenere l’automazione relativa al deposito di 70 pallet diametro 1000 mm, ottimizzando gli spazi necessari per il transito dei pezzi grezzi, WIP e finiti.
Nelle ultime macchine installate il cliente ha, inoltre, richiesto di aggiungere anche la possibilità di eseguire lavorazioni di Power Skiving, una particolare operazione di dentatura che incrementa ulteriormente la versatilità della linea. L’esigenza di gestire precisioni estreme nelle lavorazioni in sincronismo a 5 assi ha portato MCM, in collaborazione con il cliente, a concepire e sviluppare particolari soluzioni. La difficoltà di esecuzione di pezzi complessi come, per esempio, le camme con un cinematismo a 5 assi implica, rispetto a una lavorazione lineare, maggiori possibilità di errore. Per questo sono stati sviluppati cicli particolari di ravvivatura mola e di tastatura delle superfici, con sonde che verificano la forma geometrica del pezzo durante le varie fasi di lavorazione della camma. È stato quindi integrato un calcolatore di profili che, laddove necessario, consente di rigenerare il percorso utensile per ripassare il pezzo a quote e forma variate. Questa soluzione consente alla macchina l’esecuzione di lavorazioni estremamente precise, garantendo l’automazione del processo ed elevando così al massimo la percentuale di utilizzo della macchina, anche senza il presidio dell’operatore.
MITSUBISHI
Come primo controller CNC collegabile direttamente alla rete WLAN, la serie M8V è un fattore abilitante chiave per ambienti Industrial Internet of Things mirati alla produzione ‘smart’ basata sui dati.
I CONTROLLI NUMERICI DELLA SERIE M8V DI MITSUBISHI ELECTRIC RISPONDONO ALLE ESIGENZE DI LAVORAZIONE DELLE MODERNE MACCHINE MULTITASKING E RETTIFICATRICI GRAZIE ALLE LORO CARATTERISTICHE DI PRECISIONE, VELOCITÀ, USABILITÀ E INTERCONNESSIONE IN OTTICA INDUSTRIA 4.0 MACCHINE
II controller per lavorazioni CNC della serie M8V di Mitsubishi Electric rappresentano lo stato dell’arte del controllo numerico rispondendo alle esigenze di ogni tipologia di lavorazione, anche le più complesse come quelle delle macchine multitasking e rettificatrici. Anzitutto, la serie M8V offre capacità impareggiabili in termini di precisione e velocità. La combinazione tra la CPU dedicata, l’innovativa tecnologia di controllo OMR-CC e il controllo automatico del carico di taglio aiuta le aziende a minimizzare i tempi di lavorazione beneficiando di una grande accuratezza. Infatti, queste caratteristiche consentono di creare prodotti di alta qualità riducendo i tempi di ciclo almeno dell’11% rispetto ai modelli precedenti, abbassando inoltre gli errori di percorso del 15%. Le applicazioni di lavorazione dei metalli possono inoltre beneficiare di un elevato numero di assi per i centri di lavorazione e i sistemi di tornitura, nonché di capacità di elaborazione dei segmenti fini raddoppiate, che possono arrivare a 540 chilo-blocchi al minuto.
Per offrire maggiore supporto agli operatori, la serie di controller
La testa mandrino speciale progettata con asse controllato per l’alimentazione dell’olio da taglio, orbita intorno all’asse mandrino e ruota attorno al proprio asse per garantire un flusso costante ed orientato.
CNC M8V è dotata di interfaccia con pannello interattivo che supporta i gesti multi-touch a 4 punti di contatto, offrendo così all’utente un’esperienza d’uso analoga all’utilizzo di uno smartphone. L’interfaccia user-friendly e il design intuitivo permettono agli utenti di controllare e monitorare facilmente i parametri chiave di processo. Anche la programmazione è semplificata e razionalizzata grazie al conversazionale Job Lathe, che guida gli utenti nella realizzazione del pezzo da produrre in modo veloce e intuitivo. L’interazione con il controller è quindi estremamente semplice, anche per il personale privo di competenze in G-code.
Connettività e integrazione
Oggi il controllo numerico deve essere interconnesso e capace di interfacciarsi coi sistemi complessi aziendali, per permettere alla macchina di essere parte integrante del processo produttivo. I controller per lavorazioni CNC M8V di Mitsubishi Electric rappresentano l’evoluzione della tecnologia CNC in ottica Industry 4.0, grazie al Wi-Fi
integrato e a tutte le possibilità di interconnessione sviluppate per supportare le strategie mirate alla trasformazione digitale e abilitare le applicazioni di smart manufacturing.
L’offerta di Mitsubishi Electric include anche due soluzioni software integrate, in ottica Industria 4.0, in grado di massimizzare le prestazioni delle macchine CNC. L’applicazione NC Machine Tool Connector costituisce uno dei capisaldi di una Smart Factory completamente interconnessa internamente ed esternamente, in grado di raccogliere dati da qualsiasi macchina CNC, a prescindere dalla marca; consente, quindi, di trasferire efficacemente le informazioni a sistemi di livello superiore, senza dover tenere conto dei diversi protocolli di comunicazione specifici dei produttori. A tale connettore si abbina il software NC Machine Tool Optimizer per migliorare l’efficienza delle strutture produttive, in grado di interpretare le informazioni ricevute da diverse macchine utensili, dotate di qualsiasi unità CNC, e dallo stesso NC Machine Tool Connector. In questo modo si ha a disposizione una piattaforma intuitiva e integrata che permette la visualizzazione e il monitoraggio dei processi, dando, quindi, l’opportunità, di prendere decisioni basate sui dati, sia per migliorare la produzione che per prevenire e agire preventivamente su eventuali criticità, rendendo possibile visibilità e accessibilità in tutta la fabbrica.
Simulazione digitale e intelligenza artificiale
In ambito software è stato recentemente introdotto NC Virtual Simulator, il tool sviluppato da Mitsubishi Electric per i propri controlli numerici che permette di avere direttamente sul PC una simulazione digitale della macchina utensile da diverse angolazioni, utilizzando le stesse condizioni di lavorazione della macchina reale. NC Virtual Simulator simula il movimento degli assi in modo realistico e preciso, compresi lo smussamento, l’accelerazione/decelerazione e il ritardo nella risposta del servo. Utilizzando le stesse condizioni di lavorazione di una macchina utensile reale, questa nuova funzione fornisce una simulazione
estremamente accurata. Consente di individuare i problemi prima della lavorazione effettiva, tra cui errori di lavorazione, impostazioni sbagliate e interferenze della macchina, che in precedenza non si riuscivano a rilevare fino alla lavorazione di prova. Si tratta, quindi, di una funzionalità particolarmente utile per l’utilizzatore, perché permette di aumentare l’efficienza e la produttività del lavoro.
Un altro nuovo software in programma è NC Machining AID che, grazie all’intelligenza artificiale, è in grado di prevedere l’usura e la possibile rottura dell’utensile, oltre a eventuali errori di lavorazione. Si tratta di un software installato direttamente su PC e connesso alla macchina utensile, senza necessità di hardware aggiuntivo.
In particolare, NC Machining AID recupera e analizza i dati di lavorazione dai CNC di Mitsubishi Electric ed esegue automaticamente la diagnostica. È in grado di riconoscere le buone condizioni di lavorazione e generare un allarme quando invece rileva una lavorazione difettosa. Infatti, apprende automaticamente il taglio conforme ed individua gli errori, come una velocità di scarico del refrigerante inadeguata, un bloccaggio improprio del pezzo e impostazioni errate di compensazione dell’utensile, oltre a errori di lavorazione causati da manovre sbagliate del robot. Inoltre, apprende automaticamente la durata dell’utensile e ne suggerisce il cambio, permettendo così di ridurre i costi degli utensili. Una volta addestrato, infatti, NC Machining AID è in grado di prevedere il deterioramento dell’utensile e, quando questo si avvicina alla fine della sua vita utile, indica un messaggio di allarme sul CNC per permettere all’operatore di provvedere al cambio.
Grazie alle caratteristiche di precisione, velocità e semplicità di utilizzo della serie M8V e all’offerta software completa che permette l’integrazione e l’interconnessione necessarie nella nuova fabbrica digitale basata sui dati, quindi, i controlli numerici di Mitsubishi Electric rispondono perfettamente alle esigenze di lavorazione delle moderne macchine multitasking e rettificatrici.
NELLE MACCHINE MULTITASKING E NELLE RETTIFICATRICI, LE RIGHE OTTICHE FORTIS DI NUOVA GENERAZIONE E LE SONDE CON TECNOLOGIA RENGAGE™ MIGLIORANO LA METROLOGIA E L’AFFIDABILITÀ, ASSICURANDO VANTAGGI IMPORTANTI RISPETTO AI MODELLI TRADIZIONALI MACCHINE MULTITASKING E RETTIFICATRICI DOSSIER RENISHAW
II sistemi Renishaw di ispezione e misura per macchine utensili aiutano le aziende manifatturiere a ridurre gli scarti e i tempi di inattività e a migliorare la qualità dei componenti, garantendo che le specifiche e le tolleranze desiderate di un pezzo di lavoro o di un utensile da taglio vengano rispettate prima e durante il processo di lavorazione. Il segreto per produrre componenti accurati, che rispettino le tolleranze, consiste nell’eliminare le fonti di variazione all’interno del processo di lavorazione. Un grado elevato di variazione all’interno dei processi produttivi, infatti, accresce il rischio di errori. Gli encoder Renishaw permettono di controllare i processi alla base e contribuiscono a eliminare tali rischi. Gli encoder lineari FORTiS-S™ e FORTiSN™ possono facilitare le misure che migliorano la metrologia della macchina utensile e accrescono l’affidabilità, portando importanti vantaggi a livello operativo e commerciale.
Gli encoder FORTiS
Gli encoder FORTiS mantengono inalterate le dimensioni e la disposizione dei fori delle righe ottiche incapsulate tradizionali, pensate per ambienti impegnativi, ma adottano un design meccanico senza contatto estremamente originale e innovativo. Il modello standard FORTiS-S va da 140 a 4.240 mm, mentre la versione sottile e compatta FORTiS-N™ va da 70 a 2.040 mm. Inoltre, gli encoder sono dotati dei protocolli di comunicazione più diffusi, con risoluzioni da 50 a 0,5 nm.
La struttura interna degli encoder FORTiS, tuttavia, include una serie di funzioni innovative e vantaggiose rispetto ai sistemi di stampo più convenzionale.
La riga in acciaio inox, e non in vetro, garantisce maggiore robustezza e presenta un coefficiente di espansione termica (CET) pari a 10,1 ±0,2 μm/m/°C, molto simile a quello dei materiali usati per le basi di buona parte delle macchine, contribuendo a ridurre gli errori causati dalle variazioni termiche e ad aumentare l’affidabilità delle misure. Il basso livello di rumore (jitter inferiore a 10 nm RMS) e un errore sottodivisionale (ovvero l’errore all’interno di un periodo della riga) di appena ±40 nm garantiscono un feedback estremamente affidabile che migliora il controllo di velocità e la stabilità. L’assenza di contatto tra riga e lettore porta una serie di vantaggi importanti rispetto ai modelli tradizionali, che incorporano delicati meccanismi di guida con molle e cuscinetti.
L’interno privo di parti mobili o scorrevoli elimina i problemi legati all’usura, riduce drasticamente i rischi di rottura e aumenta l’affidabilità e la durata del sistema. Inoltre, vengono ridotti gli errori di isteresi e gioco associati al contatto meccanico, migliorando la forma e la finitura dei pezzi lavorati.
Una vera rivoluzione nel design dei lettori
Uno degli elementi su cui i tecnici Reni-
shaw si sono concentrati è l’effetto delle vibrazioni su un encoder lineare incapsulato. I tradizionali encoder a contatto sono notoriamente sensibili alle vibrazioni, soprattutto in circostanze particolari, ad esempio lavorazione di materiali molto duri, tagli intermittenti e graduale usura della macchina. I lettori senza contatto dei sistemi FORTiS-S e FORTiS-N sfruttano una tecnologia di smorzamento a massa accordata (SMA) che offre la migliore resistenza alle vibrazioni tra i sistemi della sua classe. Lo SMA è un dispositivo meccanico che viene montato in una posizione specifica di una struttura, per assorbire le vibrazioni di risonanza. Negli encoder FORTiS vengono impiegati due SMA che contrastano le vibrazioni intorno all’asse verticale (asse Z) e orizzontale (asse Y) dei lettori. Il lavoro di sviluppo degli SMA di FORTiS permette di ottenere una riduzione di 5,3 volte dell’accelerazione di picco all’estremità del lettore (alloggiamento delle ottiche) più distante dai punti di montaggio.
Anche durante test prolungati a oltre 30 g e anche alla loro frequenza di risonanza, entrambi i modelli dell’encoder FORTiS mantengono il livello di prestazione e la resistenza alle condizioni ambientali difficili.
Le sonde Renishaw
All’interno dei processi produttivi, il fattore umano è la causa principale di errori. Le sonde di ispezione per macchine utensili contribuiscono in modo significativo all’aumento della precisione dell’intero processo produttivo in quanto permettono di automatizzare le attività di misura e quindi di eliminare tale rischio, fornendo un controllo in-process e funzionalità di verifica del pezzo.
Renishaw ha inventato la prima sonda a contatto per macchine utensili negli anni ‘70. Il successo di questo prodotto innovativo, basato su un principio a resistenza cinematica, ha contribuito a garantire all’azienda una posizione di leadership mondiale nella progettazione,
produzione e supporto di prodotti di misura dimensionale. Grazie ad una continua attività di ricerca e sviluppo, oggi, Renishaw è in grado di fornire prodotti di altissima qualità con prestazioni che non temono rivali sul mercato.
L’investimento in una sonda Renishaw consente di semplificare le attività di misura nelle fasi di preparazione, controllo e monitoraggio dei processi, migliorando la gestione delle attività produttive, con un conseguente aumento dei profitti.
Nello specifico, nella fase di preparazione eseguono misure automatiche in macchina della posizione e dell’allineamento del componente; nella fase di controllo in process effettuano la misura automatica del componente su rettificatrici, macchine elettroerosione a filo e a tuffo. Infine, nel monitoraggio post-processo, le sonde Renishaw permettono la verifica della conformità dei componenti prima della loro rimozione dalla macchina.
La tecnologia RENGAGE™
Frutto di oltre dieci anni di progettazione, le sonde con tecnologia RENGAGE™ sono brevettate da Renishaw e incorporano una tecnologia estensimetrica di provata affidabilità, con elettronica ultracompatta e un design meccanico di precisione per prestazioni e capacita che non temono rivali. Sono adatte per un’ampia gamma di applicazioni su macchine utensili e superano le limitazioni legate alle prestazioni 3D che affliggono molte altre sonde. I più recenti prodotti Renishaw che includono questo tipo di tecnologia sono MP250, OMP400, RMP400, OMP600 e RMP600.
I componenti estensimetrici sono posizionati su micro supporti
progettati con estrema attenzione per renderli parte della struttura della sonda, lasciandoli contemporaneamente separati dal meccanismo cinematico. Sono disposti in modo da rilevare le tensioni su tutti gli assi e i loro output vengono combinati elettronicamente tramite alcuni algoritmi brevettati.
Quando si raggiunge la soglia di resistenza in una direzione qualsiasi, viene generato un segnale di trigger con forze decisamente inferiori rispetto a quelle necessarie per le sonde convenzionali.
Dato che la rilevazione è completamente indipendente dal meccanismo della sonda, i dispositivi con tecnologia RENGAGE sono caratterizzati da bassa forza, elevata ripetibilità ed una caratteristica di comportamento costante, tutti fattori che non sono ottenibili con sonde dal design convenzionale.
La tecnologia RENGAGE permette di eliminare fino al 90% degli errori di lobing.
Nelle applicazioni a due assi, le sonde estensimetriche consentono di ridurre al minimo le operazioni di calibrazione. Tuttavia, è nelle applicazioni a tre assi e nelle misure di geometrie complesse che i vantaggi risultano particolarmente evidenti. In queste situazioni, infatti, le sonde dotate di tecnologia RENGAGE si rivelano assolutamente uniche.
Le sonde con tecnologia RENGAGE sfruttano il meccanismo cinematico sviluppato da Renishaw per riportare lo stilo nella posizione iniziale. Questo sistema vanta 30 anni di continui perfezionamenti e garantisce un ritorno ripetibile, elemento fondamentale per una metrologia accurata.
Per chi cerca prestazioni di eccellenza e velocità elevate in qualsiasi condizione di lavoro, durante la misura di elementi prismatici e a forma libera e con stili corti e lunghi, una sonda Renishaw con tecnologia RENGAGE è la scelta più logica e sicura.
MP250: design robusto per applicazioni in ambienti ostili
La sonda MP250 è stata studiata appositamente per applicazioni su rettificatrici. La guarnizione a doppio diaframma, infatti, ne consente l’utilizzo negli ambienti ricchi di particolati abrasivi, tipici delle rettificatrici. Anche in queste condizioni proibitive, la sonda conserva la sua accuratezza di misura per un lungo periodo di tempo. Le prestazioni rimangono elevate anche quando la sonda è sottoposta ad alti livelli di vibrazioni, come spesso accade durante i processi di tornitura e rettifica. Se le vibrazioni della macchina costituiscono un problema, è possibile impostare la sonda su un diverso equilibrio tra sensibilità e rischio di attivazioni indesiderate. Sono disponibili anche configurazioni a bassa latenza, utili quando si ha bisogno di tempi di risposta rapidi.
La MP250 permette l’uso di stili lunghi e pesanti, spesso necessari per le misure di utensili da taglio su affilatrici e rettificatrici. Grazie alla tecnologia RENGAGE™, la sonda può operare con la massima accuratezza, assicurando variazioni di precorsa minime anche quando si installano stili di grandi dimensioni.
Avendo un diametro di soli 25 mm, il suo design compatto ne consente l’uso anche in macchine in cui lo spazio è limitato. Inoltre, la connessione via cavo garantisce un’ottima resistenza alle interferenze, rendendo MP250 il sistema ideale per ambienti ostili.
Viteria, bulloneria e fissaggi industriali
Fissaggi per costruzioni
Sistemi di assemblaggio e installazione
Tecnologia per la produzione di viteria e bulloneria
Stoccaggio, distribuzione e attrezzature di fabbrica
Informazione, comunicazione e servizi
DDa oltre 100 anni, Rettificatrici Ghiringhelli S.p.a. è leader nella progettazione e costruzione di rettificatrici senza centri. L’azienda, fondata nel 1921 a Luino, è oggi conosciuta ed apprezzata in tutto il mondo perché capace di fornire soluzioni di alta precisione e qualità in grado di soddisfare ogni necessità, anche la più esigente. Le soluzioni Ghiringhelli si prestano a settori in cui vengono richieste alta produttività, elevata precisione e ripetibilità del processo. A differenza di altre tipologie di rettifica, la rettificatrice senza centri è una macchina poco flessibile, ma estremamente precisa e in grado di garantire il rispetto dei parametri nel tempo. Con tempi ciclo di qualche secondo, possono produrre ininterrottamente. Se opportunamente alimentate le rettificatrici senza centri Ghiringhelli spossono cioè lavorare 24H/gg per 365 gg/anno, senza interruzione se non per interventi di ordinaria manutenzione.
La filosofia
Rettificatrici Ghiringhelli S.p.a. ha sempre lavorato per interpretare al meglio l’evoluzione del settore della rettifica senza centri, sapendo ascoltare le specifiche esigenze dei suoi clienti. Nel corso degli anni, la filosofia problem solving è diventata il naturale completamento delle macchine Ghiringhelli. Qualità e affidabilità del prodotto, capacità di comprendere e risolvere ogni esigenza produttiva del cliente e del mercato, stretta collaborazione e vicinanza all’utilizzatore finale hanno permesso a Rettificatrici Ghiringhelli S.p.a. di essere riconosciuta da un pubblico sempre più ampio come fornitore e partner affidabile per soluzioni di rettificatura senza centri altamente tecnologiche.
Ogni fornitura si sviluppa, infatti, in co-engineering con il cliente al fine di fornirgli la soluzione più idonea alle sue esigenze produttive.
Sempre più, si tratta di impianti completi in termini di movimentazione e controllo dei pezzi, dove l’utilizzatore finale richiede una soluzione completa, oppure necessita di implementare alla rettificatrice soluzioni di carico/scarico, controllo e/o movimentazione a lui già note. Il successo dell’azienda di Luino si basa da sempre sulla propria capacità di trovare, in ogni caso, la soluzione più idonea per il cliente, tanto da evolvere, nel corso della sua lunga esperienza, da costruttori di rettificatrici senza centri a fornitori di soluzioni di rettifica customizzate e complesse, nonché implementatori di automazione.
Una strategia di innovazione continua
Il segreto del successo di Rettificatrici Ghiringhelli va ricercato non solo nell’ampia esperienza accumulata nei decenni, ma soprattutto in quella flessibilità che le ha permesso di adattare le sue proposte e soluzioni alle mutevoli esigenze di mercato. A partire dal 1935, anno in cui Giuseppe Ghiringhelli ha progettato e costruito la prima rettificatrice senza centri, la produzione aziendale si è continuamente specializzata, passando dalla fornitura di rettificatrici senza centri a comando idraulico a quelle a controllo numerico, fino ad arrivare, più recentemente, a vere proprie isole robotizzate in cui l’intero processo (alimentazione, carico, lavorazione, scarico, misurazione, manipolazione) avviene attraverso l’ausilio di caricatori automatici e robot antropomorfi.
Le soluzioni Ghiringhelli ben si adattano ai principali settori industriali, dall’automotive all’aerospace, dai motori elettrici agli utensili, dal settore del bianco a quello medicale, potendo soddisfare numerose richieste di mercato.
In funzione della tipologia di pezzo da realizzare, delle sue caratteristiche tecniche e dei volumi da produrre, la rettificatrice senza centri Ghiringhelli viene progettata e dotata degli accessori e delle periferiche necessari. “Dove vi sono uno o più diametri esterni di pezzi cilindrici da rettificare, Ghiringhelli è la soluzione ottimale!”, - dichiara Patrizia Ghiringhelli, Joint Managing Director di Rettificatrici Ghiringhelli. “Sono ormai numerose le soluzioni installate con successo presso utilizzatori finali in cui la nostra rettificatrice senza centri è dotata di due o più robot che gestiscono il prelievo e l’alimentazione dei pezzi grezzi, la manipolazione dei pezzi lavorati presso stazioni di soffiaggio, misura e controllo, nonché l’orientamento e il posizionamento presso magazzini pallettizzati di pezzi finiti. Tutte le fasi sono integrate nella HMI progettata dai nostri tecnici e gestite tramite CN per un uso semplice e intuitivo da parte dell’operatore finale”.
Soluzioni all’avanguardia per la diagnostica e la manutenzione ordinaria e predittiva
Per soddisfare le crescenti richieste di mercato in tema di gestione macchina, tutte le soluzioni realizzate da Rettificatrici Ghiringhelli S.p.a. possono lavorare senza presidio H24.
“Contrariamente a quanto accadeva fino a qualche anno fa, quando i clienti disponevano di un operatore per macchina, oggi sempre più spesso, la produzione di più linee se non di reparti interi è affidata ad un solo operatore. Le motivazioni sono diverse, non ultime il costo e la disponibilità di mano d’opera. Non sono pochi, quindi, i casi in cui l’utilizzatore finale deve ovviare alla carenza di tecnici con impianti che possano produrre turni interi senza presidio o con gestione da remoto”, - afferma Patrizia Ghiringhelli. “Di conseguenza, sempre più
spesso, ci viene richiesta la possibilità di gestire da remoto gli impianti e/o di connetterli alla rete aziendale”.
Per questo, alla telediagnostica presente da decenni sulle macchine Ghiringhelli, si sono aggiunte in questi ultimi anni tecnologie e funzionalità digitali per lo scambio dei dati e la manutenzione predittiva. Nonostante ciò, l’approccio all’impianto da parte dell’utilizzatore finale è rimasto molto semplice e intuitivo. “Fornire soluzioni sempre più complesse e performanti mantenendo la semplicità d’utilizzo è un aspetto che caratterizza le nostre rettificatrici senza centri ed è una sfida che i nostri tecnici hanno affrontato e superato da sempre”, spiega Ghiringhelli. Questo risultato è possibile grazie all’implementazione di soluzioni CN avanzate, quale ad esempio il SinumerikOne di Siemens, un CN nativo digitale che consente, in un unico ambiente, di programmare sia la macchina che tutte le periferiche e gli azionamenti di cui è dotata. L’utilizzatore, con semplici comandi guidati, è messo in condizione di poter gestire l’intero impianto senza avere necessariamente sviluppato competenze specifiche in programmazione elettronica e/o in automazione.
“Per attitudine siamo costantemente impegnati nella ricerca di soluzioni all’avanguardia che superino le aspettative dei clienti. Il nostro obiettivo è riuscire ad anticipare i bisogni emergenti del mercato, contribuendo così al progresso tecnologico e a diffondere il valore del made in Italy. Il nostro è un lavoro specialistico che perseguiamo instancabilmente, per garantire la massima soddisfazione dei nostri clienti e per rimanere un punto di riferimento nel mercato”, dichiara la Joint Managing Director di Rettificatrici Ghiringhelli.
Sicurezza e sostenibilità fondamentali nello sviluppo di nuove soluzioni
Grande attenzione nello sviluppo delle soluzioni di rettifica senza centri Ghiringhelli è da sempre dedicata anche all’aspetto sicurezza macchina e di tutti coloro che la dovranno gestire. Oltre alla dotazione di misure standard, quali le carenature e i blocchi elettronici che impediscono qualsiasi tipo di intervento a macchina in lavorazione, è stato introdotto un sistema di accesso a livelli tale per cui, in funzione delle proprie competenze, l’operatore può essere più o meno abilitato all’accesso di alcune funzionalità. “I livelli vengono precedentemente concordati con il cliente e salvati su chiavette elettroniche. Ogni operatore, attraverso una specifica chiavetta, potrà quindi accedere ad alcune funzioni e vedersi negato l’accesso ad altre. Così facendo la sicurezza macchina viene ulteriormente garantita escludendo un uso improprio da parte di operatori non autorizzati”, spiega Ghiringhelli. “Altro tema sviluppato negli ultimi anni per soddisfare una domanda crescente è la sostenibilità delle nostre rettificatrici senza centri. A questo proposito, mi preme citare alcune soluzioni adottate nel corso degli anni, quali il basamento in quarzo sintetico o in granito naturale, che ha sostituito la versione in ghisa più di 10 anni fa, l’impiego di accessori e dotazioni macchina di ultima generazione a consumo energetico ridotto oppure, ancora, alcune procedure automatiche di accensione/spegnimento o di stand-by che garantisco un ridotto consumo di energia. Chi sceglie una rettificatrice senza centri Ghiringhelli cerca qualità assoluta e affidabilità personalizzata. Ma non solo: la nostra tecnologia è sempre più conforme ai principi di eco-compatibilità e minor impatto energetico”, conclude Patrizia Ghiringhelli.
DOSSIER
MACCHINE MULTITASKING E RETTIFICATRICI
SANDVIK COROMANT
SILENT TOOLS™, LA SOLUZIONE DI SMORZAMENTO A MASSA ACCORDATA DI SANDVIK COROMANT, È IN GRADO DI SUPPORTARE UNA SERIE DI OPERAZIONI DI LAVORAZIONE PER LA TORNITURA, L’ALESATURA E LA FRESATURA MIGLIORANDO L’EFFICIENZA COMPLESSIVA NELLE OPERAZIONI DI TAGLIO DEI METALLI
CCosa potrebbero avere in comune una macchina utensile e l’edificio più alto di Taiwan? Situato a Taipei, l’edificio alto 508 m potrebbe restare vittima delle vibrazioni se non fosse per il suo intelligente sistema di smorzamento a massa. Nelle applicazioni di tornitura, fresatura, alesatura e foratura, i produttori potrebbero trovarsi di fronte allo stesso problema, se non fosse per Sandvik Coromant Silent Tools™. Situato a soli 200 m da un’importante linea di faglia, Taipei 101, uno dei grattacieli più alti al mondo, è in grado di resistere a terremoti e forti venti grazie ad uno smorzatore di 5,5 m di diametro, il più grande al mondo. Lo smorzatore a massa accordata può infatti ridurre fino al 40% dei movimenti della torre e ha salvato l’edificio dal disastro in diverse occasioni.
Sebbene la riduzione delle vibrazioni nelle macchine utensili non funzioni esattamente allo stesso modo, le due applicazioni condividono un obiettivo comune: offrire maggiore stabilità e combattere il rischio di errore. Silent Tools™ costituisce un elemento unico nel suo genere dell’offerta di prodotti di Sandvik Coromant da diversi decenni, ma cosa permette a questa soluzione di distinguersi dal resto? Ce lo spiega Anders Digernes, R&D Manager di Sandvik Coromant, esperto in utensili per il taglio dei metalli e in soluzioni di produzione, ripercorrendo la storia dell’innovazione nello smorzamento delle vibrazioni.
Una breve lezione di storia
Silent Tools™ è nato dalla ricerca di uno studente universitario, Hans Kristian Holmen, che nel 1964, mentre stava scrivendo la sua tesi sulle vibrazioni degli utensili, ha realizzato un prototipo di una barra di alesatura antivibrante. Il suo lavoro è rimasto solo un progetto universitario, finché il suo potenziale non è stato riconosciuto da un visitatore che vide il prototipo in un tornio nell’officina universitaria e capì che Holmen aveva scoperto qualcosa.
“Iniziarono così i piani per la produzione del prototipo, supportati all’epoca da una fabbrica di chiodi e punte situata a Trondheim (Norvegia), che iniziò a produrre gli utensili antivibranti. Più avanti, negli Anni Settanta, il produttore iniziò una collaborazione con Sandvik Coromant per supportare le vendite e la distribuzione al mercato globale. Da allora Silent Tools™ fa parte di Sandvik Coromant e l’area di prodotti continua a crescere ancora oggi”, racconta Anders Digernes.
Buone vibrazioni
Per capire il motivo per cui gli attacchi degli utensili antivibranti svolgono un ruolo importante nelle operazioni di lavorazione, è opportuno analizzare le vibrazioni. Sebbene le vibrazioni a volte possano essere utili, nelle lavorazioni non sono auspicabili.
“Le vibrazioni possono provocare imprecisioni in termini di dimensioni del pezzo lavorato. Se l’utensile da taglio vibra o batte contro il pezzo, può deviare dal suo percorso previsto, provocando imprecisioni dimensionali e una finitura superficiale insoddisfacente. Tali circostanze possono anche provocare irregolarità alla superficie del pezzo lavorato, il che rappresenta un problema soprattutto nelle applicazioni in cui è fondamentale una finitura superficiale liscia, come nella lavorazione di precisione o nei settori aerospaziale e mediale”, spiega l’esperto. Inoltre, quando l’utensile da taglio vibra in modo eccessivo, è più soggetto a stress e usura, il che può ridurre la sua durata e compromettere la qualità della lavorazione. Le vibrazioni possono necessi-
tare di velocità di taglio più basse e profondità di taglio inferiori per mantenere standard di qualità accettabili, aumentando in tal modo i tempi di lavorazione e riducendo la produttività complessiva.
“In breve, le operazioni con tendenza alle vibrazioni minacciano costantemente la produttività e la sicurezza della lavorazione, soprattutto in presenza di sporgenze lunghe o cavità profonde. La riduzione dei parametri di processo, come profondità di taglio, velocità o avanzamento, è una possibilità da considerare che rischia, tuttavia, di avere un impatto negativo sulla produttività”, afferma Digernes.
Gli smorzatori funzionano assorbendo, dissipando o reindirizzando l’energia generata dalle vibrazioni, minimizzando così i loro effetti sull’operazione di lavorazione.
Silent Tools™ utilizza una tecnica specialistica nota come smorzamento a massa accordata, proprio come il Taipei 101, dove un contrappeso all’interno dell’utensile assorbe l’energia cinetica delle vibrazioni e utilizza una frequenza di compensazione per eliminarle meccanicamente, invece di convertirle in rumore e calore. Con la più piccola configurazione dell’utensile di soli 10 mm di diametro e la più grande di 600 mm, valore da record, Silent Tools™ è in grado di supportare una serie di operazioni di lavorazione per la tornitura, l’alesatura e la fresatura.
“Per esempio – spiega Digernes - la lavorazione di fori profondi è un’operazione con particolare tendenza alle vibrazioni, soprattutto quando si lavora con lunghe sporgenze. Le barre di alesatura ammortizzate con sporgenze da 6 a 14 volte il diametro consentono volumi di truciolo asportato maggiori rispetto alle barre di alesatura non ammortizzate. Oltre a garantire una finitura superficiale di alta qualità e a soddisfare la tolleranza richiesta, i parametri di taglio più elevati consentiti da questa strategia di lavorazione creano trucioli più corti, migliorando allo stesso tempo l’evacuazione truciolo. Questo è fondamentale quando si lavora con lunghe sporgenze.
Poiché Silent Tools™ consente parametri di taglio più aggressivi mantenendo la qualità e la produttività, gli utenti sono in grado di ridurre i tempi ciclo della lavorazione e, di conseguenza, migliorare l’efficienza complessiva nelle operazioni di taglio dei metalli. Abbiamo appurato che, utilizzando Silent Tools™ insieme agli utensili e agli adattatori Sandvik Coromant per l’applicazione scelta, i clienti registrano miglioramenti di produttività di almeno il 50% quando vengono utilizzati adattatori di lunghezze inferiori, e fino al 300% per gli adattatori più lunghi”.
Per molti anni, Sandvik Coromant ha detenuto un brevetto per Silent Tools™ che ha reso la soluzione davvero unica nel suo genere. Oggi, sebbene i concetti di smorzatori a massa accordata siano meglio compresi dal mercato più ampio, sono molti i motivi per cui Silent Tools™ rimane unico.
“Innanzitutto, Silent Tools™ continua a evolversi. Questo comprende gli aggiornamenti lanciati nel 2024 progettati per offrire prestazioni più uniformi e una finitura superficiale ancora migliore. Il dispositivo antivibrante, che un tempo richiedeva una regolazione di precisione, ora viene assemblato automaticamente e ogni singolo smorzatore viene calibrato da una macchina. Questa automazione
consente una superficie di frequenza estremamente precisa e prevedibile, perfettamente adatta alla sporgenza e all’applicazione previste per ogni adattatore. Ciò significa che gli adattatori di tornitura Silent Tools™ sono più efficienti che mai nel contrastare le forze di vibrazione in presenza di lunghe sporgenze”, dichiara Digernes.
A ulteriore garanzia di precisione nei setup e di un’ottimale salute degli utensili, gli adattatori di tornitura aggiornati sono accompagnati dall’introduzione del dispositivo digitale Tool Status Checker. Tool Status Checker è progettato per aiutare gli operatori a controllare la salute degli utensili e a supportare il setup degli utensili prima che inizi la lavorazione. È compatibile con tutte le versioni degli adattatori di tornitura Sandvik Coromant. Gli utenti devono semplicemente agganciarlo all’interfaccia Serration Lock dell’adattatore grazie al magnete incorporato, scaricare il software ed è pronto a partire. Grazie alla funzione di regolazione del posizionamento in altezza di Tool Status Checker viene ogni volta garantita la precisione del setup, mentre con la funzionalità di monitoraggio della temperatura si avrà la certezza che l’adattatore stia sempre lavorando nel proprio intervallo di temperatura specificato.
“Questo ci porta a un altro vantaggio dell’utilizzo di Silent Tools™”, continua Digernes. “Pur essendo un’innovazione a tutti gli effetti, Silent Tools™ non ha bisogno di agire da solo: i clienti possono imparare di più sulle loro operazioni di lavorazione con Silent Tools™ Plus. Utilizzando un adattatore di tornitura connesso
e i sensori per monitorare carico, vibrazioni, flessioni, finitura superficiale, temperatura e rilevamento “in-cut” nelle applicazioni di tornitura, il prodotto è stato lanciato sul mercato per superare la sfida della mancanza di visibilità dell’operatore nella tornitura interna. Poiché l’operatore non ha immagini del processo interessato, era estremamente difficile individuare potenziali problemi fino al completamento della tornitura”. Trasmettendo i dati direttamente a un pannello di controllo, Silent Tools™ Plus fornisce agli operatori la visuale dell’area di taglio, consentendo loro di individuare eventuali problemi, come una flessione o una vibrazione eccessiva o problemi di setup, prima che si aggravino e i produttori siano costretti a scartare dei componenti costosi. Disponibile anche come versione integrata nella macchina, con CoroPlus® Connected, i dati generati nella zona di taglio possono essere trasformati automaticamente in azioni di taglio, eliminando il bisogno degli operatori di monitorare il pannello di controllo della macchina per l’intero processo.
“Taipei 101 e la lavorazione di lunghe sporgenze condividono una sfida comune, superata dallo smorzamento a massa accordata. La storia di Silent Tools™ può essere iniziata molti decenni fa, ma i continui sviluppi significano che la soluzione offre ai produttori qualcosa di più di un semplice sistema di eliminazione delle vibrazioni. Con Silent Tools™, i clienti possono avere una maggiore visibilità del processo di lavorazione e ottenere di conseguenza risultati migliori”, conclude Digernes.
Vi presentiamo la vostra nuova alleata: la gamma Swiss DT di ultima generazione. Superate le vostre stesse aspe ative, aumentate il vostro vantaggio competitivo e approfi ate di una soluzione che si evolve in base alla vostra strategia aziendale.
La gamma è composta da sei confi gurazioni di macchine S e HP che possono lavorare barre di 13, 26, 32 e 38 mm di diametro.
LE MACCHINE MULTITASKING SORALUCE SONO LA SOLUZIONE IDEALE PER OTTENERE I PIÙ ALTI PARAMETRI DI AFFIDABILITÀ NELLA LAVORAZIONE DI PEZZI DI GRANDI DIMENSIONI AD ELEVATA COMPLESSITÀ TECNICA MACCHINE MULTITASKING E RETTIFICATRICI
OOggi, più che mai, i clienti hanno la necessità di lavorare rapidamente, riducendo i costi di manutenzione e di attrezzaggio e incrementando le tipologie di operazioni effettuabili in un’unica macchina. Al fine di aumentare la produttività, nei diversi settori merceologici è stata quindi evidenziata la necessità di realizzare componenti in un unico piazzamento del pezzo. Grazie ad oltre 20 anni di esperienza nella fornitura di soluzioni multitasking, le macchine Soraluce consentono operazioni di fresatura, tornitura e rettifica in un unico set-up, permettendo così di effettuare differenti operazioni di lavorazione con un’unica macchina e di ridurre i tempi ciclo ed i costi, aumentando, allo stesso tempo, il livello di efficienza dei processi di lavorazione. Per rispondere alle attuali esigenze del mercato, infatti, le macchine utensili sviluppate da SORALUCE permettono di realizzare operazioni di fresatura/tornitura/alesatura/ rettifica e dentatura a clienti attivi in differenti settori: beni strumentali, meccanica generale, energia, stampi, ferroviario, aeronautico, ecc.
A fronte di una produzione di soluzioni multitasking che raggiunge il 30% delle macchine Soraluce, il concetto di multitasking sviluppato dall’azienda, può essere integrato in tutta la gamma di macchine sviluppate dalla stessa. Numerosi i vantaggi offerti: dalla riduzione dei tempi di carico, scarico e allineamento dei pezzi, a quella dei tempi di attrezzaggio macchina, dall’esecuzione delle differenti lavorazioni in un’unica macchina, al miglioramento della precisione e della qualità di lavorazione dei differenti pezzi e tanto altro ancora. “Soraluce ha riformulato il concetto di multitasking, tradizionalmente associato all’integrazione in un’unica macchina di processi di tornitura e fresatura, grazie allo sviluppo di tecnologie avanzate che permettono di incorporare anche i processi di rettifica in una soluzione “all in one”. Questa operazione costituisce la fase che richiede maggior precisione e permette di concludere lavorazioni di pezzi industriali ad alto valore aggiunto”, ha sottolineato Silvia Alducci, Vice Presidente di Soraluce Italia. La scelta di un sistema multitasking permette di ridurre l’investimento nel numero di attrezzature, riduce lo spazio necessario per l’impianto e il numero di operatori richiesti. Allo stesso tempo, i sistemi multitasking sono versatili, compatti, presentano una grande flessibilità, migliorano l’efficienza del processo e rendono possibile la produzione di piccoli lotti in modo efficiente.
Riducendo la quantità di fermi macchina e il tempo richiesto per la
preparazione dei pezzi e minimizzando i tempi ciclo e il rischio di errori, queste soluzioni rispondono appieno ai requisiti di versatilità, produttività ed efficienza propri del concetto “multitasking”.
La famiglia multitasking SORALUCE
Un’ampia gamma di prodotti e soluzioni permette a SORALUCE di fornire la soluzione ideale per ottenere i più alti parametri di affidabilità nella lavorazione di pezzi di grandi dimensioni ad elevata complessità tecnica. I centri multitasking SORALUCE includono i centri di lavoro SORALUCE della Performance Line, i montanti mobili della Productivity Line, fino alle macchine a portale gantry o con tavola mobile della Heavy Duty Line, dotate di traversa fissa o mobile.
Le soluzioni multitasking possono essere applicate all’intera gamma di macchine Soraluce. Le macchine Soraluce incorporano il mandrino multitasking ad alta coppia con una potenza fino a 43 kW e una coppia di 1220 Nm, con indexaggio ogni 2,5º o 0,001º. La testa multitasking integra un innovativo sistema di bloccaggio rotazionale, che include un blocco del mandrino per qualsiasi angolazione durante le operazioni di tornitura. Questo sistema di bloccaggio previene il danneggiamento dei cuscinetti. Con questo design unico, è possibile definire l’orientamento della testa e del mandrino con qualsiasi angolazione, evitando così le interferenze con il pezzo e ottimizzando la capacità di lavorazione.
Elevata versatilità e produttività per soddisfare le diverse esigenze di ogni cliente
Grazie al sistema di cambio utensili automatico, utensili e mole vengono caricati direttamente nel mandrino, senza la necessità di elementi intermedi. Per soddisfare le diverse esigenze di ogni cliente, SORALUCE offre una vasta gamma di teste, standard e speciali e stazioni di lavoro per una configurazione ottimale: oltre alla vasta gamma di teste di fresatura, Soraluce dispone anche di teste di tornitura specifiche con elevata capacità di taglio. Inoltre, tutte le teste possono essere cambiate in automatico, come gli stessi utensili sia di fresatura che di tornitura (orizzontale/verticale) con attacco C6, C8 e C10. Sono previsti supporti per barre di alesatura lunghe da Ø 100 a Ø 250 mm, con lunghezza fino a 2500 mm, inclusa la soluzione per il cambio testa
automatico. Tornitura esterna/interna sono possibili con una sola testa. Tutte le teste di fresatura, multitasking e tornitura possono essere cambiate in automatico consentendo così un cambio accurato delle teste tramite flange di accoppiamento. L’azienda dispone di un’ampia gamma di tavole girevoli e rototraslanti sia di fresatura che di tornitura. Tavole girevoli con portata da 2 a 200 ton, con diametri fino a 8 m. La tecnologia TBS (Table Balance System) viene utilizzata per bilanciare le tavole, per correggere la distribuzione dei carichi asimmetrici e garantire un’elevata precisione. La soluzione multitasking incorpora cicli specifici sviluppati da Soraluce presso la Soraluce Software Factory per facilitare le funzionalità di tornitura e rettifica: come la possibilità di gestire contemporaneamente sia i cicli di fresatura che di tornitura, il passaggio dalla modalità fresatura alla modalità tornitura o rettifica automaticamente o la facile programmazione della tornitura e cicli di molatura.
Tecnologia avanzata per una combinazione vincente
SORALUCE fornisce tecnologie intelligenti in continua evoluzione, rispondendo oggi alle domande di domani. Tutta la tecnologia sviluppata dall’azienda consente di migliorare l’efficienza, la produttività, la precisione e la capacità di adeguamento ai processi concreti di produzione del cliente, come i dispositivi: Chip Breaker, Adaptive Control, Accura Heads e il suo rivoluzionario sistema DAS+® (Dynamics Active Stabilizer), che include più funzioni per aumentare la capacità di lavorazione delle macchine. DAS+® comprende tutte le conoscenze e l’esperienza di SORALUCE nel campo delle dinamiche di lavorazione, a beneficio dei clienti. Include il monitoraggio del livello di vibrazione, il rilevamento delle vibrazioni in tempo reale e due diverse strategie extra per sopprimere le vibrazioni: le funzioni di sincronizzazione della velocità del mandrino e della variazione della velocità del mandrino. Il sistema
DAS+® rende la macchina più intelligente e aumenta la produttività e la robustezza del processo eliminando le vibrazioni e così facendo riducendo i tempi di ciclo, aumentando la durata dell’utensile, migliorando significativamente la qualità della superficie e riducendo l’usura della macchina.
Le soluzioni più rigide e dinamiche nel mercato
Realizzate con una struttura interamente in ghisa, le macchine adottano guide lineari a ricircolo di rulli combinate con pattini smorzatori, che garantiscono rigidità dinamica ed elevata precisione volumetrica. Una scelta, quella relativa ad una struttura totalmente in ghisa, legata al fatto che questa soluzione non risente di tensioni interne di saldatura che si generano invece nelle strutture elettrosaldate: fattore che su macchine di medio-grandi dimensioni può alterare considerevolmente la geometria dell’impianto, provocando errori geometrici sul componente da lavorare. Inoltre, l’elevato coefficiente di assorbimento delle vibrazioni presentato dalla ghisa consente all’utensile di lavorare nelle migliori condizioni, con un conseguente aumento della vita dell’utensile e della qualità della finitura del pezzo. Il sistema delle guide lineari a ricircolo di rulli combinate con pattini smorzatori è importante e garantisce elevata dinamica, rigidità e precisione nelle lavorazioni, ottenendo così un’eccellente produttività, riducendo i costi di manutenzione al minimo. Quindi, estrema rapidità nelle lavorazioni senza rinunciare alla precisione e alla produttività. Flessibilità, dunque è la parola d’ordine per le macchine multitasking SORALUCE le quali permettono di effettuare diverse lavorazioni, tra cui operazioni di fresatura, tornitura, alesatura, foratura, maschiatura e rettifica in un’unica macchina ed in un unico piazzamento. Ciò è oggi possibile con efficienza e precisione per pezzi di differenti dimensioni e forme.
DOSSIER
MACCHINE MULTITASKING E RETTIFICATRICI
STUDER
L’AZIENDA SPAGNOLA TEMSA METALLURGICAL GROUP È TRA LE AZIENDE LEADER A LIVELLO MONDIALE NELLA PRODUZIONE DI UTENSILI SPECIALI PER L’INCRUDIMENTO.
DA ANNI L’AZIENDA SI AFFIDA ALLE RETTIFICATRICI CILINDRICHE STUDER PER REALIZZARE I PROPRI PRODOTTI
TTEMSA Metallurgical Group è tra le aziende leader a livello mondiale per la produzione di utensili ad alta precisione per l’incrudimento ed è esperta di metallurgia delle polveri, sinterizzazione e orditura.
Nell’incrudimento il materiale prende una determinata forma per effetto di elevate forze di compressione e trazione a una temperatura inferiore a quella di ricristallizzazione. Rispetto alla lavorazione dei metalli ad asportazione di truciolo è possibile ottenere tempi di lavorazione minori per ogni pezzo riducendo così i costi della produzione in serie. Tra i vari vantaggi dell’incrudimento rientrano anche l’elevata resistenza, le geometrie complesse e le eccellenti proprietà superficiali. Con questa procedura vengono realizzati anche i componenti per settori altamente tecnologici come ad esempio quello aerospaziale o automobilistico. Tutto ciò è possibile solo grazie agli utensili speciali e a competenze specifiche, ed è qui che entra in gioco TEMSA.
“Il nostro team è in grado di realizzare utensili speciali con un range di tolleranza nell’ordine di un micrometro”, afferma Alfonso Vivar, responsabile di produzione di TEMSA. Nella sede di TEMSA vicino a Barcellona, in un complesso altamente tecnologico di 8.000 metri quadrati, lavorano un centinaio di dipendenti che realizzano componenti per soddisfare clienti esigenti in tutto il mondo. “Grazie al nostro know-how possiamo offrire anche tempi di consegna ridotti. Ciò è possibile però solo affidandosi alle migliori macchine”, dichiara Vivar.
Una tecnologia di cui fidarsi
TEMSA utilizza già da diversi anni i modelli del produttore svizzero. “Questa è la nostra nuova STUDER S100, ci è stata consegnata quest’anno assieme a una favoritCNC”, afferma Vivar indicando la rettificatrice in tondo per interni universale CNC con la caratteristica verniciatura in bianco con un tocco di blu, tipica combinazione di colori del marchio distintivo delle rettificatrici cilindriche STUDER. Infatti, sono molte le macchine STUDER che, nella sede di TEMSA situata ad ovest di Barcellona, si occupano degli interventi di rettifica. Oltre alla S131, anche una rettificatrice in tondo per interni universale CNC di nuovissima generazione. “Ci fidiamo di questa tecnologia e apprezziamo l’eccellente collaborazione con il produttore”: con queste parole Vivar motiva la decisione di investire su queste macchine. Inoltre l’elevata precisione, l’affidabilità e la semplicità di utilizzo delle macchine STUDER garantiscono la massima efficienza produttiva possibile.
Grazie alle molteplici possibilità di impiego, il modello S100 offre la massima precisione nella rettifica interna, in piano ed esterna. Con questa macchina è possibile realizzare un’ampia gamma di pezzi con lunghezza fino a 550 mm. La favoritCNC è una rettificatrice cilindrica universale a CNC per la produzione singola e in serie di pezzi di medie dimensioni con lunghezza fino a 680 mm. Per entrambe le macchine il rapporto qualità/prezzo è eccellente. Inoltre dispongono di una tecnologia avanzata, come ad esempio il basamento della macchina in ghisa minerale robusta Granitan, e dell’integrazione ottimale di hardware e software per la massima facilità d’uso. La rettificatrice in tondo per interni S131 con sistema di guide brevettato StuderGuide, testa porta mola a torretta con fino a quattro mandrini porta mola e asse C aggiuntivo, è ideale per la realizzazione
altamente precisa di pezzi a sbalzo e pezzi di dimensioni compatte di qualsiasi tipo.
Assistenza clienti con comunicazione diretta
Oltre alla qualità delle macchine, Vivar individua un ulteriore motivo importante per cui l’azienda ha scelto STUDER: “L’assistenza clienti è eccellente e ci interfacciamo con persone che parlano spagnolo”, afferma. La comunicazione è diretta e semplice. Anche l’offerta di STUDER per la “manutenzione preventiva” (preventive maintenance) è importante per il responsabile di produzione. L’offerta comprende un controllo regolare di routine delle macchine da parte degli esperti STUDER per minimizzare il rischio di interruzioni della produzione e aumentare la durata delle macchine.
“Il contatto personale è molto importante perché in questo modo so cosa funziona e cosa no e dove c’è bisogno di intervenire” spiega Riccardo Delai, responsabile vendite per l’Europa latina di STUDER. Di recente STUDER dispone di un tecnico dell’assistenza in loco in Spagna, per rispondere ancora più tempestivamente alle richieste dei clienti. Per Delai questo Paese dell’Europa meridionale è un mercato importante per il futuro, anche perché lo stato spagnolo e l’Unione europea supportano le aziende locali con investimenti mirati nelle tecnologie di alta gamma. “Siamo particolarmente felici del successo internazionale dell’azienda spagnola TEMSA, che mostra il potenziale delle nostre macchine”, sottolinea Delai.
Investire nel futuro è un successo assicurato
La storia di successo di TEMSA è iniziata oltre 30 anni fa quando agli albori era una piccola azienda per utensili di precisione in metallo duro e acciaio. Grazie però all’investimento continuo nel personale, nel know-how e in impianti moderni l’azienda spagnola è stata in grado di farsi rapidamente un nome a livello mondiale. Nel settore degli utensili speciali per i processi di incrudimento TEMSA fa parte delle aziende leader a livello mondiale.
L’attenzione alla tradizione va di pari passo con lo sguardo al
futuro. TEMSA ha puntato già dalle prime fasi sull’automazione per rendere la produzione ancora più efficiente. Un esempio su tutti. il braccio robotico completamente pivotante presente nello stabilimento, un gioiello tecnologico che classifica automaticamente numerosi utensili e, se necessario, li appronta a seconda delle esigenze e del ciclo di lavorazione. “In futuro vorremmo portare l’automazione a un livello ancora più alto, e questa è senza dubbio una sfida”, dichiara Vivar. Anche sotto questo punto di vista STUDER è un partner eccellente grazie all’ottima esperienza con le soluzioni di automazione standard e customizzate. La S100 ad esempio può essere dotata di interfaccia di caricamento e porta scorrevole automatica per l’integrazione in una linea di produzione automatizzata. Anche la S131 dispone di un’interfaccia standardizzata per caricatori e unità periferiche.
Nuovo sistema di carico universale insertLoad
Oggi, le rettificatrici STUDER offrono anche insertLoad, un nuovo sistema di carico universale che consente un’automazione standardizzata per caricare e scaricare le rettificatrici in tondo universali S33 e la S31. Entrambe le rettificatrici sono soluzioni ottimali per pezzi da piccoli a grandi per produzione singola e di piccole e grandi serie, che presentano distanze tra le punte da 400 a 1.600 millimetri e un’altezza delle punte di 175 millimetri. insertLoad è in grado di gestire distanze tra le punte fino a un massimo di 1.000 mm completando così i sistemi di automazione
standardizzati. I pezzi possono presentare una lunghezza massima di 100 mm e pesare 1,5 kg in caso di funzionamento alternato o 5 kg in caso di funzionamento singolo. Il sofisticato design e il semplice comando con la procedura di regolazione guidata digitale consentono di configurare applicazioni per punte e mandrini di serraggio senza disporre di conoscenze di programmazione. insertLoad è in grado di gestire pezzi sia verticali che orizzontali.
Il nuovo caricatore STUDER unisce i vantaggi di un sistema standardizzato con una grande flessibilità. Ciò gli consente di gestire i pezzi più disparati per quanto riguarda geometria, peso e dimensioni: gli addetti alla rettifica possono adattare la capacità dei cassetti e il grado di autonomia ai propri desideri e alle proprie esigenze. Il carico e lo scarico vengono eseguiti da un robot Fanuc, che si muove autonomamente su un asse lineare fra il caricatore e lo spazio di lavoro della macchina. Tipicamente il tempo senza intervento umano è compreso fra trenta e sessanta minuti.
Durante lo sviluppo STUDER ha dato particolare rilevanza alla sicurezza. Un portello separa quindi lo spazio di carico di insertLoad dallo spazio di lavoro della macchina per evitare la fuoriuscita di fiamme in caso di processi di lavorazione con olio di rettifica. Inoltre il software e un interruttore di sicurezza proteggono gli addetti alla rettifica in caso di deflagrazione.
Presentato nel 2023 in occasione della EMO di Hannover, insertLoad, al momento, è disponibile solo per le S33 e S31, ma presto saranno supportati anche altri modelli.
Il focus Industrial Automation è dedicato all’uso di sistemi di controllo e tecnologie digitali per gestire impianti e processi industriali. Non solo per migliorare produttività ed e cienza, ma per garantire equilibrio e sostenibilità rispondendo a esigenze sociali e ambientali.
La Power Distribution è alla base di tutti gli impianti: in ogni ambito è essenziale che l'elettricità sia disponibile in modo continuo e sicuro. Per questo sono necessari progettazione accurata e corretto dimensionamento, senza dimenticare le innovazioni che consentono una gestione più semplice ed e cace dei sistemi di distribuzione.
L’USO STRATEGICO DEI DATI E DELLE TECNOLOGIE DIGITALI PER TRASFORMARE LA GESTIONE DEGLI IMPIANTI E GARANTIRE
Di Patrizia Ricci
NNell’attuale panorama industriale, sempre più orientato verso la digitalizzazione e l’interconnessione, la manutenzione predittiva si rivela una scelta strategica per migliorare l’efficienza operativa e contenere i costi. Per mantenere l’efficienza e garantire la continuità operativa in un impianto manifatturiero, è infatti fondamentale implementare piani di manutenzione regolare. I guasti ai macchinari possono causare interruzioni dei servizi e, nei casi peggiori, arrestare la produzione, generando significative perdite economiche. Di conseguenza, le aziende del settore devono garantire un funzionamento ininterrotto per restare competitive sul mercato. Con l’introduzione delle tecnologie 4.0, la manutenzione predittiva sta progressivamente sostituendo le tradizionali tecniche di manutenzione correttiva o reattiva, che intervengono solo dopo un guasto, e quella preventiva o programmata, basata su intervalli di tempo prestabiliti o sull’intensità di utilizzo di un asset.
La manutenzione predittiva, resa possibile dall’Internet of Things (IoT), monitora costantemente lo stato di salute dei macchinari attraverso software avanzati e tecniche di condition monitoring, identificando eventuali anomalie prima che si trasformino in guasti, riducendo così il rischio di interruzioni e ottimizzando i processi produttivi. Questa tecnologia sta conoscendo una rapida crescita nel settore della manutenzione.
Un elemento chiave della manutenzione predittiva è la raccolta in tempo reale di dati operativi, inviati a una piattaforma IoT per il monitoraggio continuo delle condizioni dei macchinari. La crescente diffusione di dispositivi IoT, insieme a software analitici avanzati e all’evoluzione di intelligenza artificiale (AI) e machine learning (ML), permette l’integrazione di sensori intelligenti nei macchinari, connessi in rete per un controllo continuativo.
Grazie ai dati raccolti, è possibile analizzare in dettaglio le prestazioni degli impianti sia durante l’installazione, in fase di setup, sia durante l’esercizio. Questi dati permettono di sviluppare modelli predittivi che ottimizzano le strategie di manutenzione. Le analisi comparative, basate sui dati
in tempo reale e su serie storiche, permettono di rilevare disallineamenti rispetto al funzionamento previsto e di attivare tempestivamente allarmi per il cliente. Le soluzioni avanzate di AI e ML, con la loro capacità di auto-apprendimento, consentono alle piattaforme IoT di monitorare le prestazioni degli impianti, prevedere guasti e anomalie e supportare i processi decisionali in modo proattivo.Più dati vengono raccolti dai sensori, maggiore è la capacità degli algoritmi di ML di apprendere e prevedere le condizioni operative delle macchine, migliorando continuamente le metodologie di manutenzione.
Secondo Statista, il mercato globale della manutenzione predittiva crescerà significativamente nei prossimi anni, raggiungendo un valore di 64,3 miliardi di dollari entro il 2030. Questo aumento riflette la crescente adozione di questa pratica, considerata vantaggiosa dalle organizzazioni.
Uno dei principali obiettivi della smart factory moderna consiste proprio nella prevenzione dei guasti che, minimizzando i fermi macchina e garantendo la continuità operativa, è essenziale per mantenere la competitività sul mercato. Inoltre, gli strumenti e le tecniche di condition monitoring migliorano la disponibilità, l’affidabilità e la sicurezza delle operazioni.
I principali vantaggi della manutenzione predittiva e dell’IoT possono essere riassunti nei seguenti punti:
1. Riduzione dei costi e della complessità delle riparazioni: prevenendo guasti imprevisti, le aziende possono risparmiare tempo e denaro, migliorando la pianificazione della manutenzione con potenziali risparmi dal 10% al 40%.
2. Ottimizzazione della pianificazione manutentiva: rilevando difetti e guasti in anticipo, le squadre di manutenzione possono
pianificare gli interventi in modo più efficiente, stabilendo priorità e programmando sostituzioni preventive.
3. Estensione della vita utile degli asset: prevenendo i guasti, si limita l’impatto dei difetti sugli altri componenti, migliorando la longevità delle apparecchiature.
4. Pianificazione dei fermi macchina: la manutenzione predittiva permette di programmare gli interventi in momenti strategici, ottimizzando la gestione delle scorte e il rispetto delle normative vigenti.
5. Miglioramento della produttività: riducendo i tempi di inattività, le aziende possono aumentare la produttività e garantire la continuità operativa.
La manutenzione predittiva è spesso vista come l’applicazione di punta dell’Industria 4.0, poiché la sua implementazione richiede un percorso di digitalizzazione completo delle aziende, che va dalla raccolta dei dati sul campo all’adozione di sistemi ICT avanzati basati sul cloud e dotati di tecnologie di intelligenza artificiale. Questo perché non basta ricevere “dati” dalle macchine; è fondamentale trasformarli in informazioni utili per individuare l’origine dei malfunzionamenti e attuare le azioni necessarie per evitare che il problema si ripresenti, assicurando così la continuità operativa degli impianti.
La sfida nel campo della manutenzione è quella di promuovere un cambiamento di mentalità, passando da un approccio reattivo o preventivo a uno predittivo. La manutenzione non deve essere vista come un costo, ma come una risorsa essenziale per garantire la massima produttività degli impianti e la qualità ottimale dei prodotti. Vediamo alcune delle proposte e soluzioni presenti sul mercato per attuare strategie di manutenzione predittiva.
Centri di tornitura mono e bimandrino, plurimandrino e a fantina mobile
TRAUB TNL12, TNL20 e TNL32, i torni a fantina mobile convertibili velocemente a testa fissa.
La serie TNL è caratterizzata da elevate prestazioni in combinazione con una facilità di configurazione e programmazione. Disponibili in varie versioni, si caratterizzano per la struttura estremamente rigida e per l’ampia disponibilità di utensili consentita dall’utilizzo delle torrette che vi permettono di sfruttare al meglio la potenza e la flessibilità offerte da queste macchine.
Negli ultimi decenni, il settore industriale ha subito una radicale trasformazione per effetto della digitalizzazione, che permette di eseguire sui macchinari una manutenzione estremamente avanzata rispetto al passato. In particolare, il modello predittivo si delinea oggi come il più strategico per le aziende, poiché consente di ottimizzare la produttività, riducendo tempi e costi, e migliorando il rapporto con i propri clienti nelle attività post-vendita e di assistenza tecnica. In generale, da diversi anni ormai, il concetto di smart factory è realtà – e la manutenzione predittiva, che unisce la previsione dei guasti con l’analisi umana dei parametri legata agli obiettivi di business, è uno dei suoi pilastri. Questo modello supporta infatti le decisioni strategiche aziendali, suggerendo in anticipo gli interventi operativi necessari per migliorare il risultato finale.
“Le potenzialità dell’Intelligenza Artificiale, i sistemi di diagnostica evoluti e le interfacce utente sempre più interattive sono alla base dell’evoluzione della manutenzione nelle realtà industriali. La capacità di prevedere eventuali malfunzionamenti e rotture degli asset, ottenendo suggerimenti mirati sulla gestione di ogni singolo caso, rappresenta un elemento decisivo per il successo del business, consentendo di evitare perdite di tempo, fermi macchina indesiderati e conseguenti ripercussioni dal punto di vista economico”, afferma Christian Bonaldo, Product Manager, Medium and Low Voltage Products di Eaton Italia. “Nel 2024 e negli anni a venire, l’AI avrà impatti sempre più concreti anche sul settore industriale,
con i costruttori di macchine più strutturati e innovativi che acquisiranno maggiore consapevolezza delle sue potenzialità. Infatti, negli ultimi anni abbiamo assistito a una evoluzione, in quanto i benefici della manutenzione predittiva sono percepiti dalle aziende come valore strategico per il business e come leva per ottenere un vantaggio competitivo nel proprio mercato di riferimento”.
Tra le soluzioni Eaton che permettono di comunicare lo stato di usura e la vita rimasta del componente, rispondendo alle esigenze della smart factory, possiamo citare l’interruttore scatolato elettronico digitale NZM, che combina la protezione dei circuiti con la massima sicurezza e connettività, per una gestibilità della macchina migliorata in un unico dispositivo compatto. Ideali per l’utilizzo nell’Industria 4.0, gli interruttori digitali NZM sono progettati per applicazioni di potenza con elevata capacità di apertura a 690V CA. Inoltre, offrono compatibilità IoT con un sistema di comunicazione integrato e misurazione di energia in Classe 1. “Come componente di una combinazione partenza motore, la serie NZM non solo rende possibile un avviamento del motore sicuro ed affidabile, ma fornisce anche una vasta gamma di dati applicativi: informazioni sullo stato e sull’energia, oltre che relative allo status manutentivo dell’interruttore e alla durata del suo ciclo di vita. È quindi possibile controllare le configurazioni dei parametri di protezione, la vita residua del dispositivo o gli eventi occorsi con
relativi valori”, spiega Bonaldo. Grazie al software di interfacciamento gli operatori possono eseguire simulazioni realistiche e confrontare automaticamente i tempi di intervento in base alla curva di intervento selezionata, oltre a registrare tutti i risultati dei test e inserirli in una relazione stampabile con data e ora. Ogni interruttore NZM è dotato di un esteso registro eventi con capacità fino a 200 registrazioni. “Un ruolo importante nell’abilitazione della manutenzione predittiva è inoltre svolto dai pannelli operatore, come il XV300 di Eaton, il panel PLC dotato di tecnologia multitouch capacitiva, utilizzabile come HMI o HMI-PLC integrando un controllore programmabile attraverso il software CoDeSys”, aggiunge Bonaldo. Disponibile in diverse dimensioni e progettato per migliorare l’interazione uomo-macchina e semplificare la gestione del sistema, XV300 offre infatti un’interfaccia utente all’avanguardia e particolarmente sensibile, che permette l’integrazione di elementi multimediali (come video, PDF e contenuti web) e il controllo gestuale. “Inoltre, la CPU 800 MHz Arm Cortex-A9 con 512 MB di RAM abilita elevate prestazioni di sistema in termini di potenza e grafica. La conformità di XV300 al settore industriale, rafforzata dal sistema operativo real-time Windows Embedded Compact 7 Pro (a breve aggiornato a Linux), garantisce invece prestazioni affidabili. Infine, i panel PLC XV300 possono essere utilizzati sia in esecuzione orizzontale sia verticale, adattandosi al luogo di installazione e offrendo le visualizzazioni necessarie. Sono inoltre ideali per applicazioni industriali in ambienti difficili, grazie al design sottile e al pannello dotato di un vetro piatto anti riflesso e resistente”, conclude Bonaldo.
Nel paradigma Industry 4.0, il ricorso a protocolli di comunicazione digitale e dispositivi per l’IIoT è fondamentale per ottimizzare la gestione degli impianti. La rilevazione dei dati a livello di campo e la loro trasmissione, in tempo utile, all’intelligenza di fabbrica (edge) o remota (cloud), rende possibile intervenire tempestivamente con azioni di manutenzione predittiva, volte a ridurre al minimo il downtime e massimizzare l’efficienza operativa dei sistemi coinvolti.
Gefran soddisfa tali esigenze attraverso una ricca offerta di relè statici e Power Controller, dedicati al controllo dei carichi resistivi nel riscaldamento industriale, tra cui spiccano:
Relè monofase allo stato solido GRP-H con uscita IOLink
Caratterizzati da un design robusto e ultracompatto, gli statici monofase serie GRP-H sono disponibili in taglie di corrente che vanno da 15A fino a 120A, con protocollo digitale di comunicazione IO-Link.
Questo consente l’integrazione di questi SSR nelle architetture di automazione e permette lo scambio di molteplici dati, come le ore di funzionamento o i picchi di corrente e di temperatura, fondamentali in ottica di manutenzione predittiva.
Lato diagnostica, la gamma si distingue per l’estrema accuratezza nel rilevare la rottura parziale del carico, in grado di segnalare un’interruzione fino ad 1/8 del carico totale. Un requisito essenziale in alcuni ambiti applicativi, come il packaging, dove la temperatura rappresenta un parametro fondamentale.
Power Controller mono/trifase GRM-H con diagnostica integrata
I GRM-H sono power controller monofase, che in configurazione Master/Slave permettono anche il controllo di carichi trifase. Ideali per la gestione di carichi resistivi lineari e non lineari, questi dispositivi dispongono di tutte le principali tecnologie di firing mode, dallo Zero Crossing e Burst Firing, fino all’Half Single Cycle e al Phase Angle, utili per poter adeguare il controllo, in funzione delle diverse
caratteristiche degli elementi riscaldanti. In aggiunta, oltre alla funzione Soft Start, ideale per le Lampade IR, forniscono algoritmi di Feedback che rendono il regolatore una sorgente costante, con set point modificabile, di tensione, corrente o potenza. Un vantaggio importante quando si è in presenza di alcuni tipi di resistenze, come quelle al silicio-molibdeno, al carburo di silicio o grafite. Già disponibili con controllo digitale e analogico IO-Link, i GRM-H integrano ora anche il protocollo Modbus RTU, con interfaccia seriale RS485, garanzia di una diagnostica ancora più integrata ed efficiente. Oltre a informazioni di processo cicliche, infatti, i GRM-H sono in grado di registrare anche variabili acicliche come le ore di lavoro, i picchi di temperatura, l’energia e la temperatura interna, a favore di un’efficiente manutenzione predittiva della macchina. Compatti e facili da installare, i GRM-H integrano le caratteristiche tipiche di un power controller all’interno delle dimensioni di un relè allo stato solido. Disponibili in taglie di corrente da 10A a 120A, sono sinonimo di elevate prestazioni nel controllo della temperatura all’interno di un ampio ventaglio di applicazioni, quali trattamento termico dei metalli, produzione del vetro, lavorazione delle materie plastiche e semiconduttori, oltre che negli ambiti food e pharma. In più, per entrambe le serie, l’ulteriore plus è l’efficienza nel set-up dei parametri, garantita dall’esclusiva App Gefran NFC, disponibile per Android e iOS, che rende facilmente accessibili, anche da remoto, i dati diagnostici sul funzionamento dei carichi e dei dispositivi e consente di una configurazione dei parametri rapida e facilmente replicabile su più device. Infine, aprendo alle nuove prospettive offerte dall’impiego dell’Intelligenza Artificiale nel settore dell’automazione industriale, Gefran ha sviluppato un Digital Twin del GRP. Questa tecnologia consiste in una rappresentazione virtuale di un oggetto o sistema fisico per simulare, monitorare e analizzare le performance della controparte reale. In particolare, il gemello digitale del dispositivo confronta i dati ricevuti in tempo reale dal relè con un modello ideale, abilitando in tal modo funzionalità di diagnostica predittiva e controllo adattivo dei processi termici, per le quali è stato depositato un brevetto. Tali caratteristiche consentono di migliorare l’Overall Equipment Efficiency di macchine per settori quali plastica, packaging e semiconduttori.
HEIDENHAIN
Con il nuovo livello di controllo numerico TNC7 HEIDENHAIN, utilizzatori e costruttori di macchine utensili sperimentano possibilità completamente nuove per la programmazione e l’impiego delle loro macchine utensili. L’utilizzo è intuitivo, task-oriented e personalizzabile grazie a molte funzioni intelligenti che portano la produzione orientata all’officina in una nuova dimensione. TNC7 arricchisce la nota programmazione in Klartext con funzioni intelligenti e programmazione grafica di nuova concezione. L’utilizzatore disegna i profili direttamente sul touch screen. TNC7 converte e salva automaticamente il disegno in Klartext, il linguaggio di programmazione TNC a dialogo. È possibile continuare a utilizzare anche cicli e programmazione dei profili esistenti, così come ovviamente programmi NC già presenti. TNC7 affianca l’intero processo produttivo, dal progetto iniziale al pezzo finito con soluzioni avanzate. Ad esempio, con un pacchetto di cicli molto ampio, funzioni di tastatura intelligenti
e misurazione con guida grafica dell’attrezzatura di serraggio. Il nuovo editor ad alte prestazioni permette di gestire con rapidità e sicurezza anche programmi NC complessi. La perfetta visualizzazione di pezzo e area di lavoro facilita enormemente le attività quotidiane. E le simulazioni dei programmi possono essere eseguite in qualsiasi momento senza dover cambiare modalità. Tra le funzioni ne spiccano due decisamente interessanti: Process Monitoring e Component Monitoring. ll monitoraggio dei processi TNC integrato nel controllo numerico rileva con affidabilità anomalie di processo sulla base di scostamenti rispetto a una lavorazione di riferimento. L’utilizzatore controlla con semplicità il monitoraggio utilizzando la sintassi Klartext e l’intuitiva interfaccia utente. Il monitoraggio dei processi non utilizza sensori aggiuntivi e assicura una qualità di processo garantita. Questo consente un pratico controllo del risultato di processo e allo stesso tempo la garanzia della produttività mediante ampie possibilità
di reazione come la sostituzione di un utensile gemello. Il monitoraggio dei componenti TNC è la “cassetta degli attrezzi” che consente ai costruttori di macchine di realizzare estese funzioni di monitoraggio. Durante la lavorazione il monitoraggio dei componenti protegge, ad esempio, i cuscinetti del mandrino da sovraccarichi, o rileva l’usura crescente di componenti nella catena cinematica. Fornisce, inoltre, dati utili sulla sollecitazione effettiva della macchina per la pianificazione delle attività di manutenzione nell’ambito della Predictive Maintenance e per l’analisi della capacità di processo. Con il monitoraggio dei componenti TNC è possibile rilevare e visualizzare, ad esempio, l’usura dei cuscinetti mandrino o persino segnalare il sovraccarico del mandrino. È inoltre significativo ricordare che la Fabbrica Digitale HEIDENHAIN offre soluzioni pratiche e servizi competenti per la digitalizzazione standardizzata a 360° dell’officina, tra cui ad esempio il software StateMonitor per il rilevamento dei dati operativi. Questo, in primis, consente di monitorare in tempo reale lo stato di produzione delle macchine utensili CNC. Ma StateMonitor dispone di molte opzioni, come ad esempio MaintenanceManager che permette di definire le manutenzioni sulla base di diversi intervalli. Oltre all’organizzazione e alla documentazione delle manutenzioni, con MaintenanceManager è possibile rilevare anche guasti e fornire informazioni in modo mirato secondo una logica di Predictive Maintenance nell’officina. Definire una strategia di manutenzione in base all’elaborazione dei dati raccolti contribuisce a ottimizzare l’organizzazione e la flessibilità dell’officina, a incrementare la qualità delle lavorazioni e, in ultima analisi, la sostenibilità della produzione.
Il nuovo modulo di comunicazione igus collega i sensori i.Sense con il servizio superwise per monitorare in tempo reale le condizioni di impianti e macchinari in modo più conveniente, veloce e affidabile.
Fermare tempestivamente un macchinario prima che un difetto meccanico porti a costosi danni: è ciò che accade quando la tecnologia supporta l’occhio umano nelle attività di monitoraggio. Con questo obiettivo, igus offre da diversi anni i sensori intelligenti della serie i.Sense, che consentono di verificare in tempo reale le condizioni dei componenti igus in movimento come catene portacavi, cavi, guide lineari, cuscinetti a strisciamento, snodi sferici e ralle. In caso di anomalia, i sensori inviano immediatamente un messaggio o innescano l’arresto automatico del sistema per evitare costosi danni agli impianti. “Collegandoli direttamente al servizio superwise, iComm Box amplia ulteriormente le funzionalità dei sensori igus in modo semplice e conveniente, consentendo una trasmissione dei dati rapida e affidabile”, spiega Richard Habering, responsabile della Business Unit smart plastics in igus GmbH. Grazie al nuovo modulo di comunicazione, tutti i rapporti vengono salvati nel portale igus i.Cee e possono essere analizzati successivamente a scopi diagnostici. Inoltre, gli algoritmi intelligenti utilizzano questi dati per calcolare, ad esempio, il profilo di movimento delle catene portacavi, ottenendo previsioni dettagliate sulle loro condizioni. Grazie a questi dati, il pannello di controllo superwise consente di visualizzare in tempo reale informazioni sulla durata d’esercizio residua, raccomandazioni di manutenzione e indicazioni su eventuali anomalie. “Questo approccio garantisce l’utilizzo ottimale dei componenti fino alla potenziale durata d’esercizio, riducendo al minimo il rischio di guasti”, aggiunge Habering.
Veloce rientro sull’investimento
Tra i potenziali utilizzatori del modulo di comunicazione iComm Box igus vi sono aziende dell’industria di processo, come impianti di trattamento delle acque reflue e cementifici, gru portacontainer nei porti e l’industria manifatturiera in genere, compresa quella automobilistica. In questi settori, infatti, la nuova soluzione messa a punto da igus consente un rapido ritorno sull’investimento, ottimizzando la gestione della manutenzione in ottica di Industry 4.0 e prevenendo costosi tempi di inattività. “Nell’industria automotive, ad esempio, un solo minuto di fermo macchina può costare fino a 10.000 euro. Risparmiando anche solo pochi secondi grazie a iComm Box, l’investimento si ripaga rapidamente”, sottolinea Habering.
Con la nuova iComm Box, i sensori i.Sense possono essere perfettamente integrati nel servizio superwise. Il pannello di controllo superwise visualizza chiaramente in tempo reale le informazioni sulla durata d’esercizio dei componenti collegati, le raccomandazioni di manutenzione e le informazioni sulle anomalie. (Fonte: igus GmbH)
Come funziona iComm Box igus
L’esempio applicativo del sensore i.Sense EC.P, che misura le forze di trazione e di spinta nella catena portacavi, permette di capire meglio il funzionamento di iComm Box. Attualmente, i valori misurati da questo sensore vengono trasmessi tramite cavo al modulo di valutazione situato nell’armadio di controllo, che può essere collegato al PLC per innescare l’arresto automatico del sistema in caso di emergenza, come l’allentamento di un canale di guida. Tramite un cavo aggiuntivo è ora possibile collegare direttamente il modulo di valutazione all’iComm Box che, a sua volta, invia i dati al pannello di controllo superwise attraverso la rete mobile. La trasmissione avviene utilizzando un sistema di crittografia separato dalla rete TCP-IP del cliente per garantire la massima sicurezza. Inoltre, il trasferimento non comporta costi aggiuntivi, perché acquistando iComm Box, l’utente ottiene una tariffa flat per i dati per dieci anni.
igus si assume la responsabilità del monitoraggio Attraverso il proprio pannello di controllo personalizzato, il cliente può visualizzare in qualsiasi momento la durata d’esercizio residua dei componenti collegati e il momento ideale per la manutenzione. “Si tratta di uno strumento intuitivo ed estremamente facile da usare”, dice Habering. Tuttavia, qualora i clienti non avessero la possibilità di gestire autonomamente il monitoraggio dei propri impianti, igus può assumere questo incarico tramite il servizio superwise. In tal caso, il portale i.Cee è direttamente collegato al sistema CRM igus, informando il tecnico commerciale dedicato dei rapporti e delle azioni necessarie. Ad esempio, in caso di arresto dell’impianto, il tecnico igus può organizzare rapidamente l’invio dei componenti necessari per la sostituzione e contattare proattivamente il cliente per un intervento tempestivo. “Con questo servizio, solleviamo i nostri clienti da una serie di mansioni che possono gravare sulle loro risorse e quindi sulla produttività, soprattutto in questo periodo in cui è difficile trovare manodopera qualificata”, spiega Habering. “Con l’iComm Box offriamo un sistema all-in-one per affrontare al meglio le sfide dell’Industria 4.0”.
Nell’era dell’Industria 4.0, la manutenzione predittiva si impone come strategia vincente per ottimizzare le prestazioni, ridurre i costi e aumentare la sicurezza dei processi produttivi. LAPP - leader nello sviluppo e produzione di soluzioni integrate nella tecnologia di connessione e cablaggio - offre un sistema innovativo per la manutenzione predittiva dei cavi ethernet: ETHERLINE® GUARD. Anche i componenti passivi, infatti, devono essere al centro delle priorità manutentive, specialmente quando sono installati in ambienti gravosi: per questo LAPP ha introdotto ETHERLINE® GUARD uno strumento che permette di valutare lo “stato di salute” della componentistica passiva in tempo reale. Si tratta di un dispositivo IIoT che monitora le prestazioni dei cavi ethernet, durante il normale funzionamento della macchina.
Oltre la manutenzione tradizionale
La manutenzione tradizionale, basata su interventi programmati o riparazioni a guasto, non è più sufficiente per le complesse esigenze odierne. I fermi macchina imprevisti possono causare seri danni economici e produttivi, mentre la manutenzione programmata può risultare inefficiente e dispendiosa. La manutenzione predittiva, invece, sfrutta innovazioni tecnologiche per prevedere i guasti prima che si verifichino. L’evoluzione delle strategie di manutenzione nell’Industria 4.0 è resa possibile proprio grazie all’integrazione di tecnologie avanzate e, in primis, degli smart sensor. Si tratta di una tecnologia consolidata ma in continua evoluzione, sia perché applicata ad un numero sempre maggiore di componenti, sia perché oggi in grado di supportare nella
valutazione di un numero crescente di parametri. Per garantire il corretto funzionamento ed evitare il rischio di perdita di informazioni, è fondamentale disporre di dispositivi smart capaci anche di valutare lo stato di salute dei cavi. Questi dispositivi assicurano che le informazioni vitali siano trasmesse
correttamente sul cavo, migliorando ulteriormente la gestione della manutenzione.
Etherline Guard: il “guardiano intelligente” dei cavi Ethernet
ETHERLINE® Guard è un dispositivo smart in grado di analizzare le prestazioni dei cavi Ethernet e prevederne la fine del ciclo di vita, per una manutenzione predittiva dei cavi dati.
ETHERLINE® Guard è ideale per monitorare in tempo reale lo stato di cavi Ethernet installati in applicazioni sottoposte ad elevato stress meccanico, come nelle catene
portacavi, macchine utensili, nel settore food & beverage, nei robot o processi critici. Il dispositivo è studiato per cavi Ethernet conformi a 100BASE-TX secondo IEEE 802.3 (a 100 Mbit/s) ed è adatto per tutti i protocolli, tra i quali EtherCAT, EtherNET/IP e PROFINET. Inoltre, è disponibile in due versioni per la comunicazione verso il controllo principale: LAN cablata e wireless Wi-Fi.
Attraverso la lettura e l’analisi di parametri, confrontati con curve di riferimento, il sensore smart identifica lo stato di usura del cavo e invia un alert al sistema di supervisione mediante, ad esempio, il protocollo MQTT. La funzione di diagnostica è basata sull’algoritmo LAPP Predictive Indicator (LPI), in grado di calcolare la vita residua del cavo, attingendo ai valori di milioni di set di dati raccolti ed esaminati negli anni dal centro di test LAPP. Dal design compatto e con una messa in servizio rapida, grazie alla calibrazione automatica, ETHERLINE® Guard è dotato di due porte Ethernet e si collega al cavo da monitorare, adattandosi alle macchine esistenti senza ulteriori oneri di installazione. Infine, poiché i pacchetti dati vengono trasferiti da una porta Ethernet all’altra in modalità “cut through”, lo strumento risulta invisibile dal PLC collegato: non sono dunque richieste modifiche al software e non viene esercitata alcuna influenza sulla trasmissione dati della macchina. La manutenzione predittiva è il futuro dell’Industria 4.0 ed ETHERLINE® Guard è la soluzione ideale per implementare questa strategia in modo efficace e sicuro, evitando i fermi macchina imprevisti, a favore di una maggiore produttività, sicurezza e redditività.
Dai programmi di service definiti in base alle differenti esigenze dei clienti fino ad appositi software o funzioni che integrano l’intelligenza artificiale all’interno dei propri prodotti, Mitsubishi Electric propone una serie di soluzioni per la manutenzione preventiva e predittiva pensate per garantire il buon funzionamento di macchine e impianti.
La manutenzione è un’attività di primaria importanza per assicurare il corretto funzionamento degli impianti. Infatti, una corretta manutenzione permette di ridurre possibili fermi-macchina non programmati che hanno importanti ripercussioni sulla produzione. Grazie all’introduzione della digitalizzazione nelle fabbriche, oggi le aziende hanno a disposizione tecnologie sempre più efficienti e innovative per la manutenzione preventiva e predittiva. Una macchina che integra componenti in grado di fornire informazioni sull’usura di motori, robot, inverter o servoazionamenti permette all’utilizzatore finale di organizzare in anticipo gli interventi di manutenzione in base alle necessità di produzione, evitando di incappare in guasti o rotture imprevisti e nelle conseguenti perdite produttive ed economiche.
Programmi di manutenzione per robot e inverter Tecnologie come smart sensor, IIoT, Cloud Computing e Intelligenza Artificiale offrono un contributo importante per la manutenzione predittiva di macchine e impianti, in quanto permettono il monitoraggio in tempo reale dei diversi parametri per ottimizzare le prestazioni e la durata delle apparecchiature. Raccogliendo dati dai sensori e utilizzando strumenti avanzati come il Machine Learning, la manutenzione predittiva permette di identificare e risolvere eventuali problemi nel momento in cui questi si verificano, ma anche di prevedere il potenziale stato futuro delle apparecchiature riducendo i rischi. A seconda delle esigenze manutentive delle diverse realtà è possibile scegliere la tecnologia più adatta da utilizzare, grazie anche al supporto delle aziende di automazione. Mitsubishi Electric, oltre alle funzioni di manutenzione supportate da algoritmi di intelligenza artificiale all’interno dei propri prodotti, mette a disposizione il programma MELFA Care relativo alla manutenzione dei Robot e il programma FREQROL Care relativo alla manutenzione degli inverter, che includono vari pacchetti di service definiti in base alle differenti esigenze dei clienti. Come realtà globale, l’azienda dispone di centri di service dislocati in tutto il mondo, in grado di offrire anche ai clienti che vendono le proprie macchine al di fuori del territorio italiano un’assistenza
tecnica capillare e tempestiva. Anche i costruttori di macchine possono usufruire dei pacchetti MELFA CARE e FREQROL CARE, integrandoli nei loro servizi di assistenza post-vendita per garantire ai loro clienti finali un supporto completo a livello globale.
Funzioni integrate e soluzioni software
Mitsubishi Electric propone una serie di soluzioni per la manutenzione preventiva e predittiva, dagli HMI costeffective, che permettono di rilevare e visualizzare le variabili dell’impianto, alle soluzioni di manutenzione predittiva basate sull’intelligenza artificiale.
Gli inverter FR-E800 di Mitsubishi Electric dispongono di sistemi per identificare in anticipo eventuali guasti. Grazie all’utilizzo dell’intelligenza artificiale, le funzioni di manutenzione predittiva integrate nell’inverter permettono di analizzare i dati di funzionamento, identificando in anticipo un possibile guasto e individuando in real time le cause di eventuali allarmi. Anche i servosistemi MELSERVO MR-J5 integrano funzioni di manutenzione predittiva, che consentono di rilevare i consumi e le vibrazioni della meccanica collegata ai motori e di individuare anomalie meccaniche su componenti come cinghie o ingranaggi. L’opzione MELFA Smart Plus di Mitsubishi Electric, invece, permette di verificare l’assorbimento degli assi del robot e confrontarli con i modelli di degrado dei componenti soggetti ad usura, ricavando i programmi di manutenzione in base alle condizioni operative effettive. Mitsubishi Electric mette a disposizione anche appositi pacchetti software già pronti all’uso, come gli e-F@ctory Starter Package, che consentono di attivare funzionalità di analisi dell’efficienza della linea o della macchina e di verifica delle cause di guasti o fermi impianto, o gli iQ Monozukuri che ampliano ulteriormente le librerie di tool per la manutenzione. Inoltre, grazie alla soluzione SCADA Genesis 64 di Iconics, azienda statunitense che fa parte del Gruppo Mitsubishi Electric, la manutenzione può essere estesa a un intero impianto produttivo o a una serie di stabilimenti connessi tra loro. È inoltre disponibile l’innovativo tool di data science MELSOFT MaiLab che utilizza il Machine Learning, una branca dell’intelligenza artificiale, per automatizzare la raccolta di dati da diversi sistemi, la creazione di modelli predittivi e l’estrazione di grandi volumi di dati. Facile da implementare, la soluzione si basa sia su dati storici che rilevati in tempo reale, senza che gli utenti abbiano competenze specifiche o debbano sottoporsi ad una formazione dedicata.
Nel mondo della produzione industriale, la manutenzione predittiva si sta affermando come una componente essenziale per migliorare l’efficienza operativa e ridurre le emissioni di carbonio. Per contribuire a una manutenzione più efficiente e supportare l’obiettivo di una società a zero emissioni di carbonio, OMRON ha lanciato il sistema di monitoraggio delle condizioni K7TM, una soluzione innovativa progettata specificamente per gli elementi riscaldanti nei settori automobilistico e dei beni di largo consumo (FMCG).
K7TM: di cosa si tratta e che vantaggi offre Il K7TM rappresenta un salto tecnologico nella gestione degli elementi riscaldanti. Questo sistema è in grado di visualizzare le tendenze del deterioramento degli elementi riscaldanti, consentendo una manutenzione predittiva accurata. Il monitoraggio continuo dei valori di resistenza e temperatura permette di pianificare in anticipo le attività di
manutenzione, minimizzando i tempi di fermo non pianificati e mantenendo la produttività al massimo livello.
Le principali caratteristiche del K7TM includono la facilità di installazione su apparecchiature esistenti, la misurazione automatica della resistenza durante il funzionamento e la capacità di raccogliere dati di misurazione in remoto tramite connessioni di rete. Questi vantaggi riducono la dipendenza da personale di manutenzione esperto e garantiscono una qualità costante con un consumo energetico ridotto.
L’impatto ecologico del settore manifatturiero: il ruolo di K7TM L’industria manifatturiera è responsabile di circa un quarto delle emissioni globali di gas serra, e l’automazione intelligente può giocare un ruolo cruciale nella riduzione dell’impronta ecologica. Soluzioni come il K7TM aiutano ad ottimizzare il consumo energetico, ridurre gli sprechi e migliorare l’efficienza delle risorse, contribuendo a un futuro più sostenibile. L’integrazione dell’automazione e della
digitalizzazione permette alle aziende di migliorare significativamente l’efficienza energetica nei processi di produzione. Il K7TM, con la sua capacità di rilevare anomalie minime e monitorare l’energia consumata, contribuisce a mantenere condizioni ottimali per la qualità del prodotto e ridurre il consumo di energia in produzione. Ciò non solo diminuisce i costi operativi, ma supporta anche la riduzione delle emissioni di CO2. Le strategie di manutenzione predittiva, rese possibili dai sensori intelligenti e dall’analisi dei dati, aiutano i produttori a ridurre i tempi di inattività delle apparecchiature e prolungare la durata dei macchinari. Il K7TM consente di monitorare le prestazioni delle apparecchiature e di rilevare potenziali guasti in anticipo, pianificando così le attività di manutenzione in modo proattivo e riducendo al minimo il consumo di risorse. OMRON, con il suo impegno verso l’innovazione e la sostenibilità, è in grado di mostrare come l’automazione possa essere una forza trainante per il cambiamento nell’industria manifatturiera. Il sistema di monitoraggio K7TM è un esempio concreto di come le nuove tecnologie possano migliorare l’efficienza operativa e contribuire alla riduzione delle emissioni di carbonio.
Attraverso soluzioni come il K7TM, OMRON non solo migliora la produttività e l’efficienza energetica, ma si impegna anche a creare un mondo più sostenibile in linea con l’etica del suo fondatore Kazuma Tateishi. L’impegno di OMRON nella sostenibilità e nell’innovazione continua a guidare l’azienda nel suo percorso verso un futuro a zero emissioni di carbonio, mostrando come l’industria manifatturiera possa essere una fonte di soluzioni per le sfide climatiche globali.
Le nuove soluzioni centralizzate di controllo motore stanno rivoluzionando il panorama industriale, permettendo di ridurre significativamente i tempi di inattività. I centri controllo motore FLEXLINE 3500 di Rockwell Automation ne sono un esempio all’avanguardia, in grado di fornire dati in tempo reale e aiutare i produttori a risparmiare milioni di dollari. Nel contesto delle attività di produzione e processo, ogni minuto di operatività è cruciale. Nonostante la manutenzione predittiva sia riconosciuta dai produttori di tutto il mondo come una tecnologia strategica fondamentale per ridurre i fermi macchina, si stima che, a livello globale, il produttore medio affronti fino a 800 ore di downtime all’anno. I costi di questi fermi possono variare significativamente a seconda del settore, arrivando a cifre astronomiche di 100.000 dollari l’ora o più. Diego Wilches, global product manager di Rockwell Automation, sottolinea l’importanza delle soluzioni di “smart manufacturing” per il successo delle aziende, dichiarando che ogni anno, vengono intervistati migliaia di produttori e quasi il 75% ritiene che le soluzioni di smart manufacturing siano fondamentali per il successo della propria organizzazione. La tecnologia connessa di Rockwell Automation fornisce dati operativi in tempo reale, consentendo ai produttori di individuare e risolvere i problemi di fermo macchina prima che si verifichino. Alcuni investimenti tecnologici possono ripagarsi in soli sei mesi, e ciò spiega perché il 95% delle aziende industriali Fortune 100 scelga e utilizzi prodotti e soluzioni di Rockwell Automation e dei suoi partner. FLEXLINE 3500 MCC, il nuovo centro controllo motore a bassa tensione per i mercati IEC a livello globale, va ad aggiungersi a una gamma di prodotti intelligenti progettati per ottimizzare l’uso dei dati di produzione e aumentare il tempo di attività e la produttività. Integrato con dispositivi di controllo motore intelligenti, il FLEXLINE 3500 MCC fornisce dati di funzionamento e diagnostica in tempo reale per le apparecchiature critiche, contribuendo a ridurre i downtime. Il suo design modulare e personalizzabile permette di rispondere a diverse applicazioni di controllo motore a bassa tensione in vari settori industriali, adattandosi anche ai requisiti di ingombro delle fabbriche. Inoltre, quando integrati con inverter
intelligenti a frequenza variabile, i centri controllo motore FLEXLINE 3500 possono portare a significative riduzioni del consumo energetico.
Progettato per integrare il controllo motore e la distribuzione elettrica in un unico pacchetto centralizzato, il centro controllo motore è conforme alle norme IEC 61439-1 e 2, soddisfacendo le esigenze di clienti globali. I dispositivi intelligenti all’interno dei centri controllo motori FLEXLINE offrono vantaggi significativi: riducono i fermi macchina non pianificati grazie agli allarmi e alle funzioni di diagnostica avanzata, diminuiscono i costi energetici e di manutenzione, aumentano la produttività, migliorano la sicurezza dell’impianto e del personale, e riducono i costi di progettazione e messa in servizio.
Craig Resnick, vice president consulting presso ARC Advisory Group, evidenzia l’importanza di evolvere verso lo smart manufacturing affermando che “L’integrazione dell’intelligenza nella produzione che stiamo vedendo implementare in modo strategico all’interno delle realtà produttive, rappresenta un cambiamento importante. Con l’introduzione del proprio centro controllo motore FLEXLINE 3500, Rockwell Automation mette a disposizione degli operatori dell’impianto informazioni ancor più dettagliate, consentendo un processo decisionale più guidato dai dati, e ciò porta a migliorare la redditività, la produttività e l’efficienza operativa”.
La smart factory permette di ottimizzare e migliorare i processi produttivi e la catena di fornitura che negli ultimi anni sono diventati così complessi da non soddisfare la domanda di maggiore personalizzazione e di cicli di produzione più brevi. I produttori devono affrontare l’aumento dei costi della manodopera e dei materiali e trovare modi più efficienti per produrre beni di alta qualità, inoltre, la concorrenza a livello mondiale spinge i produttori verso l’innovazione per rimanere agili e rispondere rapidamente ai cambiamenti del mercato.
Le fabbriche intelligenti affrontano queste sfide integrando tecnologie avanzate per creare un ambiente di produzione più reattivo, efficiente e sostenibile. Adottando soluzioni basate su tecnologie come l’intelligenza artificiale (AI) o l’apprendimento automatico (ML) è possibile ottenere analisi predittive grazie alle quali i produttori possono ottimizzare i processi, gestire le scorte in tempo reale, ottimizzare la logistica e migliorare la gestione della fabbrica. Il monitoraggio della produzione in tempo reale e le ottimizzazioni a ciclo chiuso, insieme alla collaborazione tra robotica avanzata ed esseri umani, contribuiscono a creare queste trasformazioni. La capacità di raccogliere, gestire e analizzare i dati consente di ottimizzare la cosiddetta manutenzione predittiva. Grazie all’analisi predittiva, la produttività e l’efficienza migliorano attraverso l’ottimizzazione dei processi delle scorte just-in-time, riducendo i tempi di inattività e migliorando il flusso operativo. Ad esempio, le soluzioni di connettività remota forniscono una visione dettagliata di tutti gli asset hardware IT e OT supportando le varie fasi dei processi produttivi con la risoluzione da remoto dei problemi. Per il settore manufacturing le soluzioni basate sulla realtà aumentata (AR) migliorano l’attività dei lavoratori in prima linea fornendo istruzioni passo-
passo e assistenza remota aiutandoli a svolgere compiti complessi in modo più efficiente.
TeamViewer Tensor e TeamViewer Frontline sono soluzioni di accesso e di controllo remoto per la risoluzione dei problemi e la gestione degli ‘alert’ provenienti dai vari tipi di endpoint, consentono alle aziende di collegare in modo intelligente i vari dispositivi, registrare i dati e integrarli in rete per ottenere sistema di controllo avanzato. Se, ad esempio, la temperatura del chip di una telecamera aumenta e supera un determinato valore, questo può essere un indicatore di un guasto imminente. Il sistema lancia l’allarme e gli addetti dell’assistenza tecnica possono coordinarsi e intervenire introducendo misure adeguate. In qualsiasi processo produttivo, diventa sempre più importante identificare in anticipo guasti imminenti e di conseguenza i tempi di inattività. In media, le grandi aziende possono perdere fino all’11% del fatturato ogni anno a causa dei tempi di inattività con ricadute finanziarie immediate e gravi. La manutenzione predittiva offre un prezioso vantaggio, consentendo di intervenire prima che un problema provochi un’interruzione dannosa. La manutenzione predittiva diventa realtà solo quando è possibile collegare senza problemi tutti gli asset e garantire che i dati vengano analizzati e condivisi al momento giusto. In questo senso, le soluzioni TeamViewer offrono una piattaforma di connettività remota a 360° per tutti i tipi di dispositivi, compresi gli elementi IoT distribuiti nell’intera fabbrica/azienda. Grazie a funzionalità complete di monitoraggio remoto dei dispositivi, la piattaforma garantisce il riconoscimento tempestivo dei problemi
nell’intera infrastruttura tecnica e avvisa immediatamente quando si verifica un problema. Il risultato è una visibilità 24 ore su 24, 7 giorni su 7, di tutti gli asset e una maggiore capacità di prevedere le situazioni critiche prima che si trasformino in gravi problemi aziendali. La manutenzione predittiva è legata a doppio filo alla capacità di intervento a distanza dei problemi.
Le avanzate funzionalità delle soluzioni TeamViewer consentono ai team tecnici di accedere e controllare da remoto qualsiasi tipo di macchina o dispositivo connessi per eseguire la diagnostica, la risoluzione dei problemi e la riconfigurazione. TeamViewer non consente solo di ridurre gli interventi di manutenzione non pianificati, ma anche di ridurre la dipendenza dall’intervento fisico.
Non esistono due aziende uguali per quanto riguarda le esigenze di manutenzione predittiva. I requisiti esatti dipendono da una serie di fattori: tipologia di dispositivi, macchinari, requisiti di sicurezza, condizioni operative e obiettivi organizzativi. TeamViewer garantisce l’implementazione e la configurazione di una soluzione che corrisponda esattamente alle esigenze di manutenzione predittiva, tenendo conto delle variabili da monitorare, delle soglie di intervento, dei metodi di connettività e di trasmissione dei dati.
NEL PANORAMA INDUSTRIALE, DIVERSI MACCHINARI IMPEGNATI IN PROCESSI PRODUTTIVI COMPLESSI DIPENDONO DALLA PERFORMANCE DI COMPONENTI CRITICI. ESEMPI EMBLEMATICI INCLUDONO LE CAMERE D’ARIA NEL PROCESSO DI VULCANIZZAZIONE DELLA GOMMA, I CRIMPER NEI MACCHINARI DI PACKAGING E GLI UTENSILI NELLE MACCHINE CNC. QUESTI ELEMENTI, ESSENZIALI PER IL MANTENIMENTO DI STANDARD ELEVATI DI QUALITÀ, PRECISIONE ED AFFIDABILITÀ, RAPPRESENTANO UN COSTO DI PRODUZIONE SOSTANZIALE CAUSATO DALLA NECESSITÀ DI SOSTITUZIONI FREQUENTI
di Alessandra Pennuto – smartFAB; Samuel Nazzareno Monaco - AFIL
LLa stima della Vita Utile Residua (in Inglese, Remaining Useful Life, da cui deriva l’acronimo RUL) di tali componenti è quindi cruciale per massimizzare l’efficienza operativa e minimizzare i costi di manutenzione, nonché il costo annuale dei componenti critici nel settore manifatturiero. Tradizionalmente, per la gestione di questi componenti e per la stima della loro vita residua si fa affidamento sulle conoscenze di dominio degli operatori per determinare un valore unico per la RUL. Ciò comporta che le sostituzioni dei componenti avven-
gano al termine della loro vita utile stimata, indipendentemente dalla necessità reale. Questa pratica può portare a costi significativi non solo per la sostituzione anticipata di componenti ancora efficienti, ma anche per le conseguenze di guasti improvvisi, che possono includere scarti, perdite di produzione e tempi di fermo non pianificati per la manutenzione. La sfida, quindi, consiste nell’integrare metodi più sofisticati di previsione e diagnostica, al fine di ottimizzare sia la longevità sia l’efficienza dei componenti critici, garantendo così un
vantaggio competitivo sostenibile ed una riduzione dei costi operativi.
L’adozione di tecnologie avanzate come modelli di Intelligenza Artificiale (IA) e di analisi dei dati apre la strada ad un nuovo approccio, permettendo una predizione accurata della vita residua dei componenti critici e riducendo gli sprechi.
L’analisi dei dati può fornire un primo punto di partenza per stimare quando componenti specifici potrebbero guastarsi, in base alla lavorazione e alla tipologia di processo e di prodotto, aiutando le aziende
a calibrarne la durata e permettendo interventi di manutenzione preventiva. Integrando poi i dati di processo derivanti per esempio dai sensori, le soluzioni di analisi dei dati possono identificare potenziali usure o squilibri nel funzionamento dei componenti, in modo da individuare con anticipo la degradazione nella performance del componente e fornire così una stima più accurata della RUL per ciascuno di essi. I benefici derivanti da tale strategia sono molteplici. Infatti, odltre a ridurre i tempi di inattività ed i guasti delle attrezzature, l’adozione di tecniche predittive può ridurre i costi annuali per tali componenti aumentandone la longevità, ridurre gli scarti, nonché migliorare la prevedibilità e la gestione delle risorse. La manutenzione predittiva, che integra la RUL, consente alle aziende di pianificare interventi di manutenzione in modo più efficiente, prevenendo guasti costosi e migliorando la continuità operativa. Tale strategia ha inoltre un impatto positivo sulla sostenibilità ambientale. Sostituire i componenti solo quando è necessario, da un lato, riduce significativamente lo spreco di materiali e l’energia necessaria per produrre nuovi prodotti, dall’altro, aiuta le aziende a ridurre le emissioni ed a contribuire a pratiche industriali più sostenibili. L’analisi
predittiva permette di pianificare meglio l’approvvigionamento dei componenti di ricambio, evitando la sovrapproduzione e lo stoccaggio eccessivo, con un impatto positivo sui costi logistici e ambientali. Nonostante i vantaggi, ci sono delle sfide associate alla stima della RUL, legate principalmente alla qualità ed alla disponibilità dei dati, fattori che potrebbero influenzare i metodi di calcolo, nonché l’accuratezza dei risultati. In uno scenario ideale, i risultati migliori potrebbero essere raggiunti tramite l’adozione di soluzioni tecnologiche di data analytics che abbiano un approccio olistico e riescano a connettere diverse fonti di dati (storici ed in tempo reale) per creare un digital twin matematico del processo produttivo o del macchinario. Tra i dati utilizzabili per la creazione di questo gemello digitale, ve ne sono diversi: di processo, relativi ai prodotti ed alle materie prime, dei guasti, derivanti dai registri di manutenzione dei macchinari, di qualità, nonché inerenti alle risorse umane coinvolte nel funzionamento dei macchinari. In questo contesto, opera smartFAB, una start-up innovativa di Milano, associata ad AFIL - Associazione Fabbrica Intelligente Lombardia (Cluster Tecnologico per il Manifatturiero Avanzato della Lombardia). In particolare, l’azienda ha
sviluppato una piattaforma di AI industrial analytics in grado di supportare i produttori nello stimare la RUL dei propri componenti critici. La soluzione ideata da smartFAB sfrutta l’Intelligenza Artificiale per connettere i dati di produzione tra i diversi silos e creare un gemello digitale dei processi produttivi, con l’obiettivo di estrarre in modo automatico insights intuitivi. Le informazioni chiave vengono presentate tramite un mix di grafici, narrazioni contestualizzate e suggerimenti pratici, così che lavoratori in fabbrica possano prendere decisioni informate indipendentemente dal proprio livello di competenza e possano agire per ridurre gli sprechi sulle linee produttive, migliorare la qualità, aumentare la produttività e ottimizzare processi e prestazioni. La piattaforma sviluppata da smartFAB è dotata di funzionalità avanzate per la misurazione, il monitoraggio e l’ottimizzazione dei processi, il rilevamento delle anomalie, l’analisi delle cause radice, nonché analisi predittive, prescrittive e “what if”.
Tra le soluzioni implementabili per la stima e gestione della RUL, vi sono ad esempio:
• modelli di ottimizzazione che determinino la RUL data una qualsiasi combinazione di prodotti e processi;
• l’analisi predittiva per determinare il tempo di utilizzo residuo prima di un guasto;
• l’attivazione di alert in tempo reale, che avvisino gli operatori quando si manifestano dei cambiamenti nella performance;
• Human-in-the-loop AI per integrare le conoscenze degli operatori con l’Intelligenza Artificiale e validare le predizioni dei modelli.
Tramite questo tipo di analisi, smartFAB può aiutare le aziende ad ottimizzare la manutenzione, migliorare la gestione delle risorse e ridurre i costi operativi, garantendo al contempo un funzionamento continuo ed efficiente dei loro macchinari
AFIL – Associazione Fabbrica Intelligente Lombardia – è il Cluster Tecnologico per il Manifatturiero Avanzato ufficialmente riconosciuto da Regione Lombardia. Attraverso le Strategic Communities, ovvero gruppi di lavoro formati da grandi imprese, PMI, start-up, associazioni, università e centri di ricerca che lavorano su tematiche strategiche per il manifatturiero lombardo, AFIL accompagna i suoi associati in un percorso collaborativo di crescita attraverso incontri tematici, workshop, webinar, matchmaking, missioni internazionali, favorendo lo sviluppo di progettualità di filiera e promuovendo la R&I anche a livello interregionale. Le Strategic Communities di AFIL ad oggi sono 6: De- and Remanufacturing for Circular Economy, Digital Transformation, Advanced Polymers, Additive Manufacturing, Secure and Sustainable Food Manufacturing, Smart Components. Per maggiori informazioni sulle attività di AFIL e per le modalità di adesione al Cluster, si invita a visitare il sito www.afil.it oppure a scrivere all’indirizzo comunicazione@afil.it
MONITORARE LA CONDIZIONE DI UN MACCHINARIO UTILIZZANDO I COMPONENTI DEL SISTEMA DI TRASMISSIONE COME FONTE DELLE MISURE NECESSARIE È UNA NOTEVOLE COMODITÀ. NE ABBIAMO PARLATO CON RALF EPPLE, PRODUCT MANAGER DI MAYR, IL
PARTNER AFFIDABILE PER LE TECNOLOGIE DI AZIONAMENTO E LA TRASMISSIONE DI POTENZA
Di Eleonora Segafredo
IIl nuovo modulo ROBA-drive-checker
amplia le ben note qualità del robusto giunto lamellare senza gioco ROBA-DS con un sistema di controllo efficiente e compatto.
ROBA-drive-checker è in grado di misurare variabili rilevanti come la coppia, la velocità e la temperatura e di comunicarle in tempo reale ai sistemi di controllo della produzione per monitorare il funzionamento della catena cinematica e facilitare la manutenzione predittiva. Il tutto senza sensori esterni, ingombri aggiuntivi o costi rilevanti.
Come è nata l’idea di ROBA-drive-checker?
Quali esigenze, manifestate dai clienti o ancora inespresse, avete cercato di soddisfare
con questo prodotto?
Abbiamo iniziato a rendere “intelligenti” i nostri giunti per alberi più di 15 anni fa. L’idea all’epoca era che, essendo i giunti per alberi necessari in ogni trasmissione, vengono utilizzati proprio nel cuore dell’azione, per così dire. E se un giunto già presente potesse “parlare” e fornire informazioni sul suo stato? Invece di aggiungere alla trasmissione complesse flange di misurazione o dispositivi simili, abbiamo dotato i giunti di sensori integrati. In questo modo si risparmia spazio e si fa a meno dei componenti aggiuntivi. Questo approccio è particolarmente interessante nel campo del monitoraggio dei processi, dove sia la precisione, sia l’efficienza eco-
nomica giocano un ruolo importante. Ci siamo deliberatamente differenziati dalle più sofisticate tecnologie di misura e dai sistemi di controllo, che perseguono un obiettivo diverso.
La sensoristica dei giunti intelligenti aiuta a ridurre o a evitare completamente i guasti e i tempi di fermo. Il monitoraggio della trasmissione consente di individuare tempestivamente i malfunzionamenti e l’usura sin dalle prime manifestazioni, rendendo così possibile intervenire in anticipo. Pianificando i periodi di manutenzione, è inoltre possibile ordinare per tempo le parti di ricambio giuste. In questo modo si riduce il tempo necessario per la manutenzione e quindi il fermo macchina
complessivo del sistema. In particolare, il cambiamento dei modelli di vibrazione o delle coppie in sequenze di processo immutabili sono segnali o indicatori ideali. Le condizioni di carico registrate dai sensori (coppie/accelerazioni) nella trasmissione consentono inoltre all’operatore del sistema di anticipare o posticipare l’intervallo di manutenzione, se necessario, e di pianificare meglio. Oltre alla durata della macchina, è possibile aumentare la produzione e migliorare la qualità del prodotto.
Quali sono state le principali sfide che avete dovuto superare per arrivare alla soluzione che ora presentate al mercato? Ci sono aspetti che ritenete ancora migliorabili?
ROBA-drive checker si basa sull’idea del monitoraggio dei processi industriali. L’attenzione principale è rivolta al prezzo. In quanto prodotto industriale, ROBA-drive checker deve avere un prezzo accessibile per poter essere utilizzato nelle macchine di produzione in serie. Deve quindi essere redditizio per i clienti come pacchetto
completo. Allo stesso tempo, anche la sicurezza informatica gioca un ruolo importante e la trasmissione dei dati deve essere sicura. Stiamo lavorando a un pacchetto pratico all-in-one che sia sicuro, affidabile
e facile da integrare nel sistema di controllo della macchina (come soluzione plug-andplay).
ROBA-drive-checker in questo momento si presenta come un’integrazione del vostro collaudatissimo giunto ROBA-DS. C’è una ragione per la quale avete scelto questo giunto per presentare i sistemi di monitoraggio integrati? Prevedete di offrire a breve altri tipi di giunto integrabili con il modulo ROBA-drive-checker?
I giunti lamellari ROBA-DS si sono affermati in molte applicazioni industriali. Trasmettono la coppia senza gioco, sono estremamente rigidi dal punto di vista torsionale e compensano i disallineamenti radiali, assiali e angolari dell’albero. ROBAdrive-checker può essere considerato un nuovo componente del collaudato sistema modulare standard del giunto ROBA-DS, i cui elementi fondamentali sono la trasmissione dati multi-gateway e il manicotto di monitoraggio. Poiché sono disponibili tutte le opzioni di collegamento del giunto la-
mellare in acciaio ROBA-DS, questo sistema di monitoraggio del processo può essere facilmente integrato in molte applicazioni esistenti, anche nel campo della robotica. Inoltre, sono possibili combinazioni con giunti di sicurezza EAS.
In futuro si potrà anche pensare a un manicotto ROBA-drive-checker nel sistema modulare ROBA-ES. È peraltro consigliabile decidere la variante di accoppiamento più adatta a seconda dell’applicazione.
ROBA-drive-checker viene prodotto con le stesse linee di ROBA-DS? State valutando di creare una linea dedicata?
ROBA-drive-checker si adatta perfettamente alla serie standard di giunti lamellari senza gioco ROBA-DS; è quindi possibile produrre giunti intelligenti muniti di funzione di monitoraggio con la stessa linea attualmente in uso per il giunto standard, senza che sia necessario creare una linea dedicata. Con il configuratore di prodotto sul sito web, gli utenti possono configurare i giunti da soli, in modo rapido e semplice, partendo dal modello standard e includendo le funzioni di monitoraggio. Per questo motivo, chi utilizza già i giunti ROBA-DS può operare un retrofit e passare a ROBA-
drive-checker.
Come stanno reagendo i clienti a ROBAdrive-checker?
Oggi tutti gli utenti vogliono avere informazioni sulle coppie nella trasmissione. Tuttavia, queste informazioni si sono sempre potute ottenere solo in presenza di spazio sufficiente per implementare i sistemi di monitoraggio. Con gli strumenti tradizionali questo può portare ad un notevole incremento dei costi. Con le nostre soluzioni, è invece possibile ridurre i costi in modo significativo.
In passato, la manutenzione delle macchine veniva eseguita secondo un programma relativamente rigido. Poteva succedere che venissero effettuati anche interventi di manutenzione o di pulizia superflui, semplicemente perché erano stati calendarizzati. Oggi, le variazioni di coppia forniscono informazioni sul grado di deterioramento, ad esempio. La manutenzione è quindi mirata: avviene solo se necessaria, pianificata ed efficiente. I cicli di manutenzione diventano più lunghi o più personalizzati, i tempi di inattività più brevi.
I clienti lo apprezzano.
I vostri webinar sono apprezzati e seguiti
dai professionisti del settore: prevedete di organizzarne uno per illustrare funzionamento e vantaggi di ROBA-drive-checker o ritenete che siano intuitivi?
I nostri webinar sono seguiti da un numero crescente di persone: per questo motivo, anche se naturalmente ci siamo concentrati sull’intuitività e la praticità del funzionamento durante lo sviluppo, abbiamo comunque in programma di realizzarne uno sul ROBA-drive-checker per interagire con gli utenti e verificare che le sue potenzialità siano pienamente espresse e utilizzate. La visualizzazione dei dati registrabili (coppia, velocità e temperatura) e l’impostazione della frequenza di campionamento, della risoluzione e di altri parametri direttamente tramite un chiaro visualizzatore basato sul web sottolineano il funzionamento pratico del ROBA-drive-checker. L’implementazione è estremamente semplice, sia tramite un singolo canale sul multi-gateway sia tramite la configurazione guidata integrata. Inoltre, i segnali LED rapidamente riconoscibili consentono di verificare facilmente lo stato direttamente sul dispositivo. Anche i due diversi connettori M8 dimostrano la loro praticità, garantendo la protezione dall’inversione di polarità durante il collegamento, nonché la protezione da polvere e spruzzi.
In quali settori dell’industria meccanica sta avendo più successo ROBA-drive-checker? Trattandosi di una soluzione studiata per il monitoraggio dei processi, ROBA-drivechecker trova facilmente impiego in applicazioni come gli estrusori o le linee di alimentazione nel settore minerario, ma la gamma di potenziali applicazioni è molto ampia: prevediamo che i settori di utilizzo aumentino notevolmente nel prossimo futuro.
Quali sviluppi prevedete che avranno i giunti ROBA-drive-checker?
Continueremo a sviluppare ROBA-drivechecker: la gamma di coppie gestibili con questa soluzione è destinata ad aumentare. Inoltre, l’elettrificazione degli azionamenti (che sostituisce le soluzioni idrauliche), l’aumento della dinamica, l’automazione progressiva e l’elevata disponibilità della macchina sono fattori che determineranno un ulteriore sviluppo.
REVO® : velocita, precisione, innovazione.
Misurare 12 sedi valvole con un sistema standard a 3 assi richiede piu di 29 minuti. REVO completa l’operazione in 3 minuti e 42 secondi perche utilizza un scansione rapida a 5 assi che permette di rilevare migliaia di punti aumentando la precisione della misura con tempi decisamente ridotti.
Con l’hub per i cuscinetti iglidur, igus presenta il nuovo shop online caratterizzato da un’interfaccia utente moderna e intuitiva. Come negli e-commerce di utensili o di abbigliamento, oggi i clienti possono acquistare rapidamente online i cuscinetti adatti alle specifiche applicazioni. Oltre alla semplicità di utilizzo, il nuovo shop presenta anche funzioni completamente inedite. Da molti anni ormai igus mette a disposizione dei clienti numerosi strumenti online con funzioni che spaziano dal calcolo della durata d’esercizio dei cuscinetti alla scelta della tecnologia di produzione più vantaggiosa per i prodotti personalizzati, di cui è possibile visualizzare anche prezzi e tempi di consegna. Il nuovo hub per i cuscinetti iglidur combina in un’unica soluzione la consultazione dell’intero catalogo e il programma di calcolo. Ciò permette ai clienti di trovare molto velocemente il cuscinetto più idoneo alle singole esigenze, inserendo semplicemente nella piattaforma le dimensioni e le condizioni di funzionamento desiderate. In pochi secondi, vengono messi in evidenza tutti i prodotti adatti, specificando relativa durata d’esercizio, prezzo e tempi di consegna. Una selezione che diventa sempre più accurata se il cliente fornisce ulteriori informazioni sui requisiti che il cuscinetto deve soddisfare, come la conformità FDA, le temperature o i carichi. Se i parametri non corrispondono a un prodotto già esistente, la piattaforma propone in tempo reale prodotti che possono essere realizzati su misura da igus nel materiale richiesto dal cliente, con relativi prezzi e tempi di consegna. “Il
nuovo shop igus per i cuscinetti iglidur rappresenta un ulteriore passo in avanti nel processo di digitalizzazione dei nostri servizi”, afferma Lars Butenschön, Responsabile Marketing per i Cuscinetti iglidur in igus GmbH. “Un percorso che ha come obiettivo ultimo quello di rendere il processo di approvvigionamento il più semplice ed efficiente possibile per i nostri clienti”. Per quasi un anno, i tecnici del reparto IT igus hanno lavorato al progetto con il supporto di diversi collaboratori interdisciplinari. Nella fase di sviluppo del nuovo shop online sono stati coinvolti anche i clienti. “I workshop con i clienti hanno evidenziato l’importanza di poter offrire, oltre alle soluzioni a catalogo, anche prodotti speciali on demand che vengono realizzati su misura,” spiega Butenschön. E la possibilità di ordinare direttamente online anche geometrie speciali rappresenta certamente uno dei plus unici del nuovo shop online igus. A seconda dei requisiti richiesti, questi componenti custom possono essere prodotti con lo stampaggio a iniezione FastLine, da barra semilavorata o con stampanti 3D. Lo shop online, già attivo da qualche mese, viene utilizzato anche dai tecnici e commerciali igus sul campo. “I feedback raccolti tra clienti e colleghi confermano l’efficienza dell’interfaccia utente che velocizza il processo di selezione e ordine”. Tra le nuove funzionalità dello shop anche la possibilità di scaricare gratuitamente disegni tecnici e dati CAD per ogni cuscinetto iglidur. In questo modo, i tecnici possono scegliere più facilmente il cuscinetto perfetto per le esigenze individuali.
HOFFMANN GROUP
Incrementare la produttività in un mercato sempre più sfidante. È questa la priorità di industrie e piccole e medie officine meccaniche a cui Hoffmann Group risponde con il nuovo catalogo 20242025. Grazie agli oltre 3.400 nuovi articoli, l’offerta in catalogo di Hoffmann Group raggiunge ora quota 120.000 tra utensili, tecnologie di serraggio e strumenti di misurazione, postazioni di lavoro e stoccaggio, utensili manuali e protezioni antinfortunistiche. Le novità riguardano soprattutto gli utensili da taglio e le tecnologie di serraggio, categorie in cui è concentrata la maggior parte dei nuovi articoli (60%), seguita dai dispositivi di protezione individuale (20%) e dagli strumenti di misura (16%). Spiccano, in particolare, l’ampliamento della gamma di utensili GARANT Master per lavorazioni ad alte prestazioni, le nuove varianti di morse GARANT Xtric e Xpent, l’introduzione di nuovi detergenti industriali privi di obbligo di etichettatura di pericolo nella linea GARANT GreenPlus e la nuova burattatrice compatta GARANT GMT2 per la finitura automatizzata di lotti di piccole e medie dimensioni. All’interno del catalogo, oltre alle marche proprietarie GARANT e HOLEX, presenti con numerosi nuovi prodotti, sono presenti più di 500 marchi dei migliori produttori presenti sul mercato, tra cui anche ISCAR a cui sono dedicate oltre 60 pagine.
Hoffmann Group continua a investire anche in servizi e soluzioni coordinati, capaci di funzionare insieme come parti di un sistema e di garantire quindi una produzione snella e un livello superiore di efficienza e produttività ai propri clienti. In focus emergono, ad esempio, le innovative soluzioni di asservimento automatizzato GARANT Automation Basic e GARANT Turntable, il software per la digitalizzazione della produzione Connected Manufacturing e gli strumenti di misura e controllo Bluetooth Hoffmann Group Connected Tools (HCT). Nell’ottica di una maggiore sostenibilità ambientale, Hoffmann Group presenta il catalogo 2024-2025, disponibile in diciotto lingue, nella sola versione digitale, comodamente sfogliabile online, mantenendo l’impegno di pubblicarlo in versione cartacea ogni due anni. Grazie a questa misura, vengono drasticamente ridotti il consumo di carta e le emissioni di CO2 generate dal trasporto. Non solo, la versione digitale del catalogo offre numerosi vantaggi nella consultazione e nei processi d’ordine, grazie alla possibilità di aggiungere segnalibri ai contenuti di maggior interesse e di condividerli con i colleghi, di salvare singole pagine, navigare facilmente tra i nuovi prodotti e ordinare direttamente dal catalogo nell’eShop.
Dossier di approfondimento tematico
Tutorial di aggiornamento professionale
Case history selezionate dal comitato
Progettisti d’impianti,
* diffusione che verrà assoggettata a certificazione
Si amplia l’appuntamento con l’inserimento dei nuovi lemmi della meccatronica alla guida multilingue dei termini della meccanica che raggruppa circa 3.000 termini tecnici, già tradotti in ben 9 lingue. Un fascicolo personalizzabile nelle copertine, nella foliazione (con l’inserimento di quartino) e disponibile anche per piccole tirature.
Versione web
www.terminidellameccanica.com, guida online gratuita, consultata quotidianamente da tutti gli attori del mondo della meccanica, permette la sponsorizzazione di una serie di termini, collegando la selezione ai dati aziendali o di prodotto, immediatamente visibili durante la consultazione.
Distribuito agli studenti delle scuole professionali salesiane
NSK lancerà un cuscinetto ad alte prestazioni per servomotori che riduce le emissioni di particelle come grasso od olio. Questo sviluppo innovativo contribuirà al funzionamento stabile di macchinari industriali vitali come i robot. Per individuare una soluzione al problema delle particelle rilasciate dai cuscinetti, NSK ha studiato il meccanismo che si cela dietro questo annoso problema. Oltre a effettuare una valutazione più precisa e utilizzare una macchina di collaudo con una configurazione e un ambiente simile a un vero servomotore, l’azienda è riuscita a progettare una struttura di cuscinetto completamente nuovo con elementi progettuali avanzati. Sfruttando la sua ricca esperienza in tribologia (controllo dell’attrito e dell’usura attraverso lubrificanti e superfici dei materiali), NSK è riuscita a sviluppare un cuscinetto con nuove tecnologie di lubrificazione e tenuta che dimezza le emissioni di particelle rispetto ai prodotti convenzionali. Inoltre, il grasso ha una durata doppia rispetto alla norma, mentre la tenuta in gomma offre una coppia più bassa. Con molti Paesi afflitti da una progressiva carenza di manodopera, il mercato dei robot industriali continua a crescere. Tuttavia, le applicazioni robotizzate richiedono alti livelli di affidabilità per effettuare la transizione da attività manuali ad automatizzate. L’affidabilità dei robot è data dai loro componenti principali. Un tipico robot antropomorfo, ad esempio, può avere fino a sei servomotori per control-
lare il posizionamento e la velocità su diversi assi. Ogni servomotore ospita due cuscinetti: un cuscinetto sul lato di carico che sostiene appunto i carichi derivanti dall’applicazione; e un cuscinetto sul lato opposto posizionato fra il disco del freno e il disco dell’encoder. In ambienti con temperature elevate come i servomotori, i cuscinetti tendono a rilasciare minuscole particelle di grasso e olio durante la rotazione.
Queste particelle aderiscono ai dischi e causano problemi come errori di lettura degli encoder e slittamento dei freni.
La necessità di cuscinetti con basse emissioni di particelle è evidente in applicazioni di questo tipo. Per questo motivo NSK ha sviluppato lubrificante e tenute che non rilasciano particelle e offrono un’alta tenuta ermetica. Il nuovo grasso di NSK ha un’evaporazione molto contenuta in ambienti con temperature elevate come i servomotori e utilizza componenti termoresistenti superiori per garantire una bassa dispersione di particelle e una maggiore resistenza al grippaggio. La nuova tenuta in gomma di NSK presenta un labbro di forma ridisegnata che favorisce la riduzione delle emissioni, oltre a ridurre la coppia del 10%.
Oltre ai servomotori, il nuovo cuscinetto di NSK è adatto anche per altri prodotti che richiedono basse emissioni di particelle, contribuendo alla stabilità operativa di un’ampia gamma di macchinari industriali.
Cavi preassemblati dall’armadio elettrico alla macchina? Con le lunghezze corrette e con un percorso dei cavi ben progettato? A partire da settembre, questo sarà possibile utilizzando il software Eplan Cable proD, grazie al quale è possibile definire il percorso dei cavi all’interno del modello 3D. L’aspetto migliore è che i dati provenienti dai cad meccanici (MCAD) e le informazioni di Eplan Electric P8 e Eplan Pro Panel possono essere facilmente integrati, collegando i progetti di ingegneria elettrica con quelli meccanici. Come si possono sfruttare i vantaggi dei cavi preassemblati nell’ingegneria meccanica? Non tutti i costruttori di macchine si sono posti questa domanda, eppure è giunto il momento di iniziare a risparmiare denaro e risorse utilizzando metodi plug-and-play. Il fornitore di soluzioni Eplan i è focalizzato da tempo sul tema del cablaggio delle macchine e ha presentato in anteprima Eplan Cable proD alla Hannover Messe di quest’anno. Il prodotto, sviluppato appositamente per il cablaggio delle macchine, è destinato a colmare le lacune esistenti. Mentre gli armadi di comando possono essere già perfettamente progettati e i loro gemelli digitali utilizzati in produzione, c’è ancora molto potenziale inutilizzato da sfruttare nei processi di cablaggio. Ad oggi non erano disponibili informazioni sufficienti per garantire una pianificazione e un’installazione del cablaggio prive di problemi.
Eliminare gli errori fin dall’inizio
È quasi superfluo dire che gli attuali metodi di lavoro possono essere soggetti a errori e richiedere molto tempo. Le aziende hanno sempre più la necessità di intervenire in questo senso, poiché i cavi rappresentano un fattore di costo significativo. Se sono troppo corti, troppo lunghi o addirittura progettati in modo errato, i costi aumentano. Se un cavo viene progettato a occhio, le cose possono diventare complicate. I segnali
di interferenza possono portare a malfunzionamenti e a lunghi tempi di messa in servizio: non solo sono difficili da localizzare, ma possono anche rivelarsi estremamente dispendiosi in termini di tempo e denaro.
Focus sul gemello digitale
Non sarebbe meglio conoscere le esatte lunghezze dei cavi fin dall’inizio, soprattutto considerando l’uso di cavi preassemblati, ad oggi sempre più diffusi? Sebbene sia vero, ciò richiede gli strumenti e i dati corretti, idealmente basati su un gemello digitale. Eplan Cable proD è un software 3D che consente di creare esattamente questo gemello e funge da base per il cablaggio delle macchine. Il processo di pianificazione dei cavi è piuttosto semplice. I progettisti possono pianificare in Eplan Cable proD il percorso dei cavi appropriato, che altrimenti dovrebbero definire su un prototipo fisico. Questo permette di avere le esatte lunghezze dei cavi necessari in fase di progettazione, rendendo il lavoro molto più efficiente grazie alle progettazioni digitali. Le interfacce con tutti i più comuni strumenti CAD per l’ingegneria meccanica garantiscono la lettura dei dati in modo nativo e l’output in formato dati universale. Eplan punta molto sul cablaggio delle macchine, come dimostra l’imminente espansione della piattaforma Eplan 2025, grazie alla quale i cavi preassemblati potranno essere progettati e pianificati in Eplan Electric P8, ovviamente con trasferimento diretto dei dati a Eplan Cable proD.
I vantaggi sono evidenti:
- Progettazione precisa: il gemello digitale elimina la necessità di un prototipo fisico.
- Dati accurati: per la pianificazione, la preparazione del lavoro, la produzione, l’assemblaggio e l’assistenza.
- Maggiore produttività: è possibile utilizzare i cavi preassemblati.
- Riduzione dei costi: nessuno spreco di cavi/nessun magazzino di materiali.
- Affidabilità della pianificazione: i cavi si adattano all’assemblaggio e alla messa in servizio della macchina. Ciò che nel modo di lavorare tradizionale diventa chiaro solo attraverso un prototipo, con questo processo integrativo risulta subito evidente. Ad esempio, le modifiche che si rendono necessarie durante la costruzione di un prototipo possono essere effettuate con pochi clic del mouse. Non è più necessaria una controparte fisica in produzione o in officina.
SANDVIK COROMANT
Lo specialista di utensili da taglio Sandvik Coromant ha aggiornato il meccanismo di smorzamento per gli adattatori di tornitura Silent Tools™, per prestazioni ancora più costanti e una migliore finitura superficiale durante le operazioni di tornitura interna in presenza di lunghe sporgenze.
Con la forza di quasi 50 anni di esperienza nella prevenzione delle vibrazioni, il sistema di portautensili Silent Tools™ di Sandvik Coromant ha offerto il proprio contributo per la lavorazione in presenza di lunghe sporgenze smorzando in modo efficace le vibrazioni.
I 37 articoli cilindrici della gamma di adattatori di tornitura (diametri 32–100 mm e 1¼–4 poll.) sono ora stati migliorati e dotati del rinnovato e migliorato meccanismo antivibrante.
Così Åke Axner, Global Product Manager – Machine Integration presso Sandvik Coromant; “Il meccanismo di smorzamento è stato interessato da un notevole aggiornamento rispetto alla precedente generazione di adattatori di tornitura Silent Tools™”. “Il dispositivo antivibrante, che un tempo richiedeva una regolazione di precisione, ora viene calibrato e assemblato da una macchina.
Questa automazione consente una superficie di frequenza estremamente precisa e prevedibile, perfettamente adatta alla sporgenza e all’applicazione previste per ogni adattatore. Ciò significa che gli adattatori di tornitura Silent Tools™ sono più efficienti che mai nel contrastare le forze di vibrazione in presenza di lunghe sporgenze.”
Grazie all’aggiornamento, gli adattatori di tornitura Silent Tools™ garantiranno una maggiore uniformità e ripetibilità di lavorazione su tutti i rapporti di lunghezza e diametro disponibili, per un prodotto più affidabile e ad alte prestazioni.
A ulteriore garanzia di precisione nei setup e di un’ottimale salute degli utensili, gli adattatori di tornitura aggiornati sono accompagnati dall’introduzione del dispositivo digitale Tool Status Checker. Spiega Axner: “Tool Status Checker è progettato per monitorare gli adattatori di tornitura Silent Tools™ su un tablet o un computer Windows”. “È compatibile con tutte le versioni dei nostri adattatori di tornitura. È sufficiente agganciarlo all’interfaccia Serration Lock
dell’adattatore grazie al magnete incorporato, scaricare il software e si è pronti a partire.”
Grazie alla funzione di regolazione del posizionamento in altezza di Tool Status Checker viene ogni volta garantita la precisione del setup, mentre con la funzionalità di monitoraggio della temperatura si avrà la certezza che l’adattatore stia sempre lavorando nel proprio intervallo di temperatura specificato.
Axner sottolinea un’altra caratteristica di valore: “È ora possibile verificare il corretto funzionamento dell’adattatore ancora prima di iniziare la lavorazione.
Grazie alla funzione di prova di maschiatura di Tool Status Checker e al martelletto incluso sarà un gioco da ragazzi confrontare il setup corrente con uno precedente, e ottenere disco verde o disco rosso direttamente nel software. Si tratta di una funzionalità che i nostri clienti ci chiedono da tempo, e siamo molto contenti di metterla a loro disposizione.”
3D Systems lancia QuickCast Air™, uno strumento avanzato nel portafoglio di strumenti per microfusione, progettato per ottimizzare la rimozione del materiale all’interno dei modelli di fusione. QuickCast Air riduce il consumo di materiale e i costi del modello, offre tempi di costruzione più rapidi, processi di combustione più puliti e migliore efficienza del drenaggio. Di conseguenza, gli utenti finali in settori quali fonderie, aerospaziale, difesa ed energia possono fornire in modo affidabile modelli per microfusione di grandi dimensioni e ad alta precisione in minor tempo e a una frazione del costo rispetto agli stampi tradizionali e senza limitazioni di complessità geometrica. QuickCast Air sta già aiutando alcuni degli importanti clienti del settore aerospaziale a ridurre fino al 50% il consumo di materiale sui propri modelli. I clienti stanno inoltre riscontrando una riduzione di diverse ore nei tempi di costruzione.
QuickCast Air è disponibile per i clienti di 3D Systems attraverso il software 3D Sprint®, parte integrante delle piattaforme di stampa per polimeri dell’azienda. Questa funzionalità, disponibile tramite abbonamento annuale, consente ai clienti di progettare modelli di fusione con un minor numero di strutture all’interno delle pareti autosupportanti.
L’uso di una minore quantità di resina e la costruzione di strutture di supporto più raffinate si traduce in una minore quantità di materiale da bruciare, pertanto in minore quantità di cenere. Grazie alla struttura interna ridotta, è più facile drenare la resina, trattenendone così una quantità all’interno della vasca durante il processo di drenaggio che altrimenti andrebbe dispersa. All’interno di 3D Sprint, gli utenti possono facilmente regolare lo spessore del guscio della parte e aggiungere sfiati e drenaggi su qualsiasi superficie, semplificando la configurazione della parte indipendentemente dall’orientamento della costruzione. La microfusione è il processo di colata di metallo fuso in gusci in ceramica realizzati da modelli a perdere e ha una storia millenaria. L’utilizzo di metodi tradizionali, come la creazione di uno stampo per l’iniezione della cera richiede tempo e denaro, diverse settimane e decine di migliaia di dollari. A metà degli anni ’90, 3D Systems ha agito da pioniere nella creazione di modelli di fusione ad alta precisione con la stampa 3D, introducendo QuickCast® nell’industria manifatturiera. Questo processo di microfusione stampato in 3D consente ai produttori di creare parti leggere e cave con tecnologie per polimeri di 3D Systems, come la stereolitografia (SLA) o la stampa MultiJet (MJP),
che possono essere utilizzate sostanzialmente per produrre componenti metallici per uso finale. Gli stampi Quick Cast sono stati riconosciuti il principale tipo di modello di alta precisione realizzato mediante produzione additiva in tutto il settore, consentendo ai produttori di migliorare l’efficienza e ridurre i costi.
“Da quando 3D Systems ha introdotto QuickCast più di venti anni fa, abbiamo continuato a sviluppare questo strumento unico e le funzionalità che offre”, dichiara Patrick Dunne, VP, Advanced Applications di 3D Systems. “Il nostro approccio all’innovazione incentrato sul cliente alimenta questa trasformazione allineandosi minuziosamente alle loro sfide uniche. Come è successo a molti dei nostri prodotti, QuickCast Air è nato da esigenze applicative specifiche dei clienti. Sono molto contento che ora possiamo immettere sul mercato questo strumento avanzato, perfezionando così la progettazione e la produzione di modelli di microfusione. Non vedo l’ora di vedere come l’adozione di QuickCast Air continuerà a sbloccare la libertà di progettazione e ad accelerare le tempistiche di produzione”. Secondo Transparency Market Research , il mercato della microfusione è stato valutato in 16,9 miliardi di dollari nel 2023 e si prevede che raggiungerà i 33,9 miliardi di dollari entro la fine del 2034. La produzione additiva sta rivoluzionando questo settore consentendo un’alternativa più economica ed efficiente al tradizionale processo di creazione di
modelli che non richiede stampi. In qualità di pioniere di una metodologia standard del settore, 3D Systems ha dimostrato la sua vasta esperienza nel supportare i clienti nelle loro sfide applicative attraverso le sue soluzioni di produzione additiva che comprendono materiali, tecnologie di stampa 3D, software e servizi. Di conseguenza, molti settori sono in grado di fornire in modo affidabile modelli di fuAsione di grandi dimensioni e ad alta precisione in minor tempo e a costi molto inferiori rispetto ai metodi tradizionali con l’uso di stampi.
3D Systems presenterà QuickCast Air presso il suo stand (edificio ovest, stand 433129) all’International Manufacturing Technology Show (IMTS) di quest’anno che si terrà dal 9 al 14 settembre al McCormick Place di Chicago, Illinois. I partecipanti alla fiera sono invitati a fermarsi per comprendere come le soluzioni di stampa 3D di grandi dimensioni di 3D Systems accelerano la risoluzione dei problemi in fabbrica e consentono di ottimizzare i flussi di lavoro, aumentare i tempi di attività e prolungare la durata delle apparecchiature. Per ulteriori informazioni, visitare il sito web dell’azienda.
1 Transparency Market Research, “Investment Casting Market (Material Type: Ferrous Alloys and Non-ferrous Alloys) – Global Industry Analysis, Size, Share, Growth, Trends, and Forecast, 2024-2034” (maggio 2024).
Gli impianti automatizzati per i processi di produzione e imballaggio devono diventare sempre più flessibili, efficienti e intelligenti. Vi possiamo aiutare con applicazioni di sensori innovative. Dalla prima all‘ultima fase del processo di imballaggio.
www.leuze.com/packagingsensors
Per ottenere un futuro degno di essere vissuto è fondamentale ridurre rapidamente le emissioni di anidride carbonica (CO2) e di altri gas serra (GHG). SICK è leader mondiale nella fornitura di sistemi di monitoraggio continuo delle emissioni (CEMS), sistemi di misurazione dei gas grezzi e altre soluzioni di sensori per uno sviluppo sostenibile in vari settori industriali. Per sostenere gli sforzi del trattamento termico dei rifiuti come fornitore di soluzioni complete, SICK incorpora nel suo portafoglio la soluzione di campionamento della CO2 biogenica di Genius5-Instruments GmbH.
La combustione di combustibili fossili libera il carbonio che è rimasto bloccato nel terreno per milioni di anni, mentre la combustione di biomasse emette carbonio che fa parte del naturale ciclo rinnovabile del carbonio. I combustibili fossili vengono rilasciati da carbone, petrolio o gas naturale.
Gli impianti di termovalorizzazione dei rifiuti apportano un contributo nel ciclo biogenico del carbonio, emettendo di fatto una miscela di CO2 siadi natura organica che fossile. Il sistema PmCTrace misura esattamente la porzione di frazione biogenica, utilizzando un campionamento proporzionale continuo del flusso di gas di scarico, raccogliendolo in una cartuccia e analizzandolo poi in laboratorio sulla base dell’isotopo radioattivo del carbonio C14.
La CO2 fossile ha zero PmC (Part of modern Carbon) mentre quella biogenica ha 100 PmC.
Le principali ragioni della necessità di determinare la CO2 biogenica
Sono in funzione sistemi di scambio di emissioni (ETS), come la europea ETS, nel Regno Unito la Environment Agency’s Pollution Inventory Guidance, la BEHG tedesca e la cinese Certified Emission Reduction (CCER). Tutte le leggi discriminano tra carbonio fossile e rinnovabile. La carbon tax è relativa alla sola quota di carbonio fossile, così da incentivare l›uso delle rinnovabili. Il CEMS completo di SICK in accoppiata ad un sistema PmCTrace e ad il dispositivo di misurazione della portata a ultrasuoni FLOWSIC100 consentono di misurare in maniera precisa la quota della frazione fossile.
Il sistema ETS dell’UE mira a ridurre le emissioni di gas serra all’interno dell’UE. Stabilisce un tetto massimo alla quantità totale di gas serra che gli impianti sono autorizzati a rilasciare. Questo limite sarà gradualmente abbassato per ridurre a zero le emissioni totali consentite entro il 2050. Lo scambio di emissioni dell’UE copre attualmente circa il 40% delle emissioni di gas serra nell’UE e sarà gradualmente esteso per coprire tutte le emissioni.
Il software FLOW Core 4.0 aggiornato introduce una versione virtualizzata della soluzione leader di mercato di OMRON, Fleet Manager, per la gestione della flotta di robot mobili autonomi (AMR).
OMRON, leader nel settore della robotica industriale, ha annunciato il lancio del software Fleet Operations Workspace (FLOW) Core 4.0, una piattaforma di nuova generazione in grado di potenziare le funzionalità delle serie di robot mobili autonomi (AMR) LD, MD e HD, semplificando al contempo il processo di integrazione e migliorando la gestione della flotta. FLOW Core è un’unica software suite che consente il coordinamento di assegnazioni intelligenti dei lavori e programmi di ricarica, l’applicazione di funzioni avanzate di navigazione e controllo del traffico e la perfetta integrazione con sistemi IT e OT come MES, ERP e WMS.
Questa nuova versione aggiorna diverse aree chiave: Fleet Manager di OMRON, un’applicazione software utilizzata per la gestione di flotte di AMR, è stata riprogettata per l’implementazione su piattaforme hypervisor. Le piattaforme hypervisor sono software di virtualizzazione che consentono la creazione e la
gestione di macchine virtuali. Ciò garantisce un’infrastruttura IT sicura e flessibile. Le risorse della flotta possono essere scalate in base alle esigenze delle applicazioni con opzioni di tolleranza agli errori e di disponibilità elevata per un funzionamento ininterrotto. Il nuovo FLOW Core 4.0 include il supporto per 3D LiDAR per tutti i modelli AMR grazie alle avanzate opzioni di rilevamento OMRON. Sono stati aggiunti tool software per strategie di docking personalizzabili per adattare le routine di ricarica all’applicazione.
Il pacchetto di analisi dei dati di OMRON, FLOW iQ, consente agli utenti di visualizzare e monitorare il layout dell’infrastruttura wireless dal punto di vista del robot. L’introduzione della diagnostica di rete wireless dinamica consente la convergenza IT e OT accelerando l’implementazione della flotta di AMR e la risoluzione dei problemi wireless, con conseguente aumento del ritorno sull’investimento.
MobilePlanner 8, l’interfaccia utente per l’ingegneria delle applicazioni di OMRON, aumenta la produttività dei tecnici dell’automazione con il nuovo editor di forme 2D per la definizione nocode del bersaglio CAPS e per le forme robot.
n.6 Settembre 2024 www.meccanica-automazione.com
Redazione Direttore Responsabile
Giorgio Albonetti
Coordinamento Editoriale Area Industry
Marco Tenaglia –marco.tenaglia@quine.it – cel. 3298490024
Direttore tecnico
Chiara Tagliaferri
Segreteria di Redazione
Cristina Gualdoni cristina.gualdoni@quine.it – cel. 3477623887
Hanno collaborato a questo numero
Patrizia Ricci, Eleonora Segrafedo, Alessandro Pennuto, Samuel Nazzareno Monaco
Pubblicità
Costantino Cialfi | Direttore Commerciale c.cialfi@lswr.it - tel. +39 3466705086
Elena Genitoni | Ufficio Traffico e.genitoni@lswr.it – tel. 0289293962
Servizio abbonamenti abbonamenti.quine@lswr.it
Abbonamento annuale € 49,99
Costo copia singola € 7,07 (presso l’editore)
Produzione Antonio Iovene | Procurement Specialist a.iovene@lswr.it | Cell. 349.1811231
Grafica e Fotolito: Fabio Castiglioni
Stampa: New Press Edizioni srl Via Della Traversa 22 - 22074 Lomazzo (CO)
Registrazione del Tribunale di Milano n. 653 del 21.09.2005.
Iscrizione al R.O.C. n. 12191 del 29/10/2005 Tutti gli articoli pubblicati su m&a meccanica &automazione sono redatti sotto la responsabilità degli Autori. La pubblicazione o la ristampa degli articoli deve essere autorizzata per iscritto dall’Editore. Ai sensi dell’art. 13 del D.Lgs. 196/03, dati di tutti i lettori saranno trattati sia manualmente sia con strumenti informatici e saranno utilizzati per l’invio di questa e di altre pubblicazioni e di materiale informativo e promozionale. Le modalità di trattamento saranno conformi a quanto previsto dall’art. 11 D.Lgs. 196/03. I dati potrebbero essere comunicati a soggetti con i quali Quine S.r.l. intrattiene rapporti contrattuali necessari per l’invio delle copie della rivista. Il titolare del trattamento dei dati è Quine S.r.l. - via Spadolini, 7 - 20141 Milano Tel +39 02 864105 Fax +39 02 72016740, al quale il lettore si potrà rivolgere per chiedere l’aggiornamento, l’integrazione, la cancellazione e ogni altra operazione di cui all’art. 7 D.Lgs. 196/03.
Ai sensi dell’art. 13 Regolamento Europeo per la Protezione dei Dati Personali 679/2016 di seguito GDPR, i dati di tutti lettori saranno trattati sia manualmente, sia con strumenti informatici e saranno utilizzati per l’invio di questa e di altre pubblicazioni e di materiale informativo e promozionale. Le modalità di trattamento saranno conformi a quanto previsto dagli art. 5-6-7 del GDPR. I dati potranno essere comunicati a soggetti con i quali Edra S.p.A. intrattiene rapporti contrattuali necessari per l’invio delle copie della rivista. Il titolare del trattamento dei dati è Edra S.p.A., Via G. Spadolini 7 - 20141 Milano, al quale il lettore si potrà rivolgere per chiedere l’aggiornamento, l’integrazione, la cancellazione e ogni altra operazione di cui agli articoli 15-21 del GDPR.
Testata associata
Affidati ad un software potente che ti consente di lavorare l’intero ciclo del tuo prodotto in un unico ambiente
PROGETTAZIONE GESTIONE CNC
GESTIONE DATI REALTÀ VIRTUALE
È un principio che applichiamo in tutte le nostre creazioni da oltre 100 anni. Progettiamo soluzioni personalizzate di rettificatura senza centri che si distinguono per forte identità e grande attenzione ai dettagli. Garantiamo sempre processi di rettificatura perfetti “al micron”, e la perfezione non è un dettaglio.