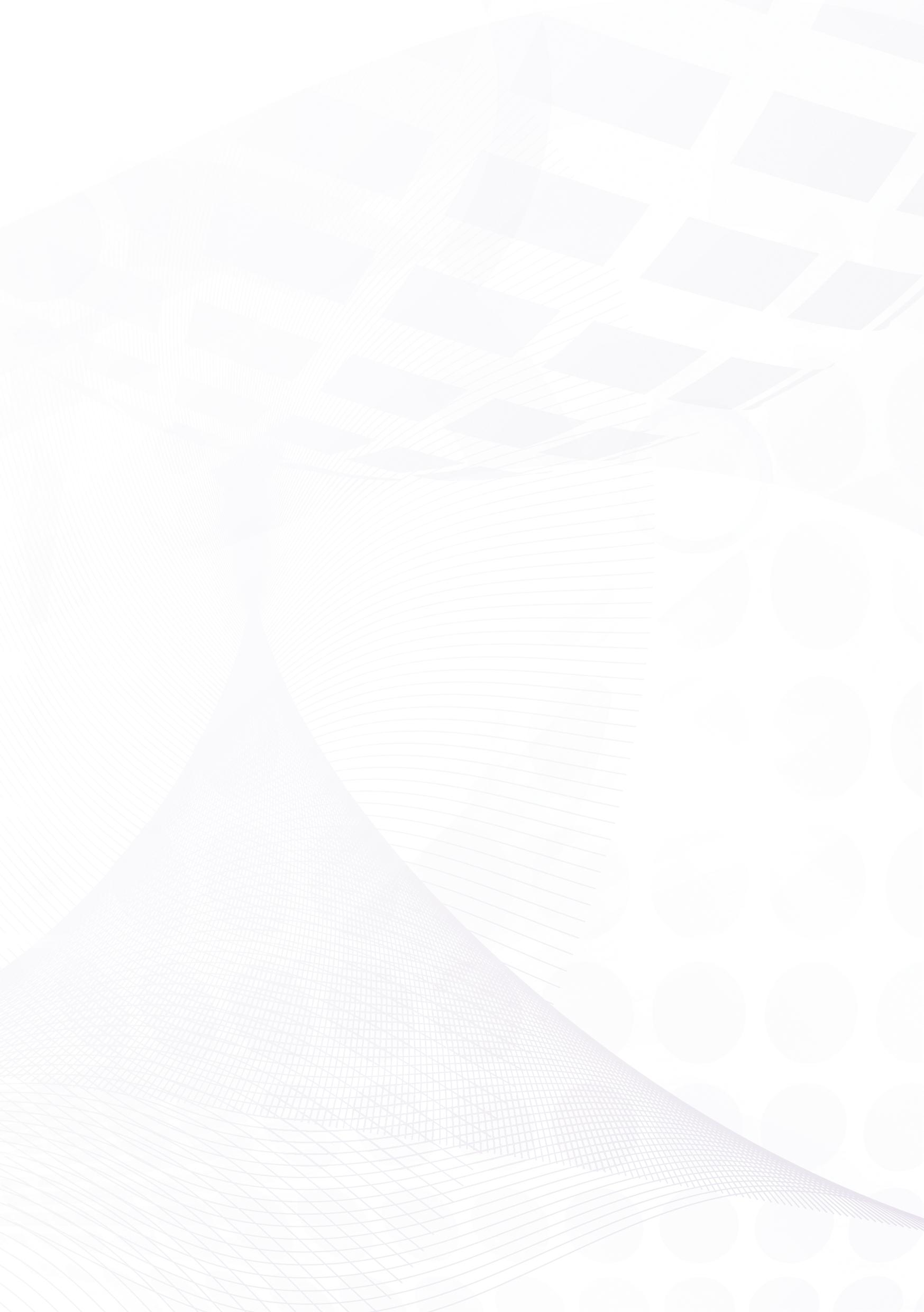
4 minute read
Australian Brewers Association
from Drinks Guide 2019
by Racs Salcedo
BRETT HEFFERNAN, CHIEF EXECUTIVE OFFICER
Austrailia’s major brewers – Carlton & United Breweries, Coopers Brewery and Lion Beer Australia – are committed to ambitious targets to help create a more sustainable world and help ensure certainty of supply and pricing.
Advertisement
CUB has committed to source 100% of purchased electricity from renewable sources by 2025.
In February this year, a major step towards made through the opening of the Karadoc Solar Farm outside Mildura in northern Victoria.
CUB is the farm’s biggest customer, due to source 74,000 MWh a year of power, which is enough to power 7,500 homes.
The iconic brewer is installing solar panels on the roofs of all its breweries this year to supply its remaining electricity needs.
Another sustainability target is a commitment to go either 100% plasticfree or using recycled plastic by 2025.
This marked their last ever use by CUB and will save more than 25 million of them from entering the environment each year. The plastic six-pack rings will be replaced by environmentally-friendly cardboard packaging.
CUB also recently stopped using plain shrink on slabs of cans brewed at Abbotsford. These will be replaced by cardboard packaging too, meaning 137 tonnes less of plastic will leave the brewery each year.
The new packaging is in market now but it may be a few more weeks before old stock disappears entirely across the country.
At Coopers Brewery in Adelaide a 4.4 megawatt natural gas powered cogeneration plant located supplies the maltings and brewery with its power needs, and the excess power is then fed back into the South Australian power grid.
The plant generates 50,000 tonnes of steam each year, which is used in the brewing and packaging processes eliminating the need for stand-alone gas-fired boilers, thereby, increasing the brewery’s energy efficiency.
The hot water produced in the brewery is used to kiln the malt, reducing gas usage by up to 40%.
Aquifers beneath the brewery allow groundwater in the onsite reverse osmosis plant, reducing the reliance on SA’s reticulated water resource. With 70% of the water from the aquifers used in the brewing process, the remaining 30% is then pumped through a 7km dedicated pipeline into the Baker Inlet Wetlands.
The plant has been upgraded several times to accommodate the changing needs of the brewery and now has a total treatment capacity of 4.5 Ml per day. The advanced technology of Coopers’ highly efficient mash filter means that less water is used in the brewhouse to produce the beer and extracts.
Establishing a Maltings onsite has eliminated malt transportation entirely.
The small grain from the malting, as well as the spent grains and protein waste from the brewing process, is harvested as a highly-prised bulk animal feed as it is high in fibre and protein. The sales proceeds are given to the philanthropic arm of the brewery, the Coopers Brewery Foundation.
Coopers, Australia’s largest family owned brewer, endeavours to have as high a recyclable content as possible in all packaging material. All glass, corrugated cardboard and stretch wrap used in packaging is 100% recyclable.
Diversions from landfill is a key priority. Coopers partners with government and industry through the Australian Packaging Covenant Organisation to actively reduce any harmful impacts of packaging on the environment.
Since 2005, Coopers has reduced the amount of waste going to landfill by 40%, through segregating all recyclables and non-recyclable waste and staff education.
Lion Beer Australia is investing in numerous renewable energy projects across its sites, including over $2 million in a solar power system at XXXX in Queensland, cutting its annual carbon emissions by approximate 1,260 tonnes – 7% of CO2 emissions from electricity.
The target overall is for Lion to reduce carbon emissions by 30% from FY15 levels by 2026.
Water is the most important ingredient in beer. To improve resilience, Lion is exploring innovative ways to improve water management within the communities it operates. In 2009 Lion commissioned a water recycling plant for its Castlemaine Perkins brewery (Queensland) to halve water-use.
A decade on, the brewery is approaching world-class standards in water management and is continually pushing the boundaries of conservation.
In 2009, Lion partnered with the Queensland Government to install a reverse osmosis plant, to recover waste water and minimise our reliance on mains-fed town water.
All waste water from the site, whether it is waste from brewing, packaging or cleaning, is captured in a collection pit. Much of this water includes useful organic compounds, like yeasts, beer and other brewing products, which when mixed in a large balance tank are digested by bacteria in a tank, creating biogas.
The biogas is used as a fuel to offset some of the natural gas usage in the steam boilers. Steam generated by the boilers is supplied across the site as an energy source for heating, cleaning equipment, pasteurisers and boiling the wort kettle.
Following reverse osmosis, the waste water is now cleaner than rainwater. It then goes through further sterilisation (including using UV light and chlorine treatment), before it’s ready to store in a two million litre tank. None of the recycled water is used in beer, but it is reused in cooling towers, boilers and for cleaning.
In 2018, the plant generated more than 220 million litres, that’s the equivalent of 88 Olympic-sized swimming pools saved.
Importantly, the plant enables XXXX Gold to be produced at a ratio of 2.8 litres of water for every litre of beer produced – which is approaching worldleading levels of water efficiency.
A decade ago, Lion began the process of phasing out plastic rings in its beer packaging, with the last removed three years ago.
Lion is committed to ensuring 100% of its consumer packaging is recyclable by 2025, and that packaging is made from at least 50% recycled contents in the same time frame.