Helping housebuilders comply and compete in challenging markets, our precision-engineered light steel frame systems deliver assured performance better than, faster than and more cost-efficiently than other market
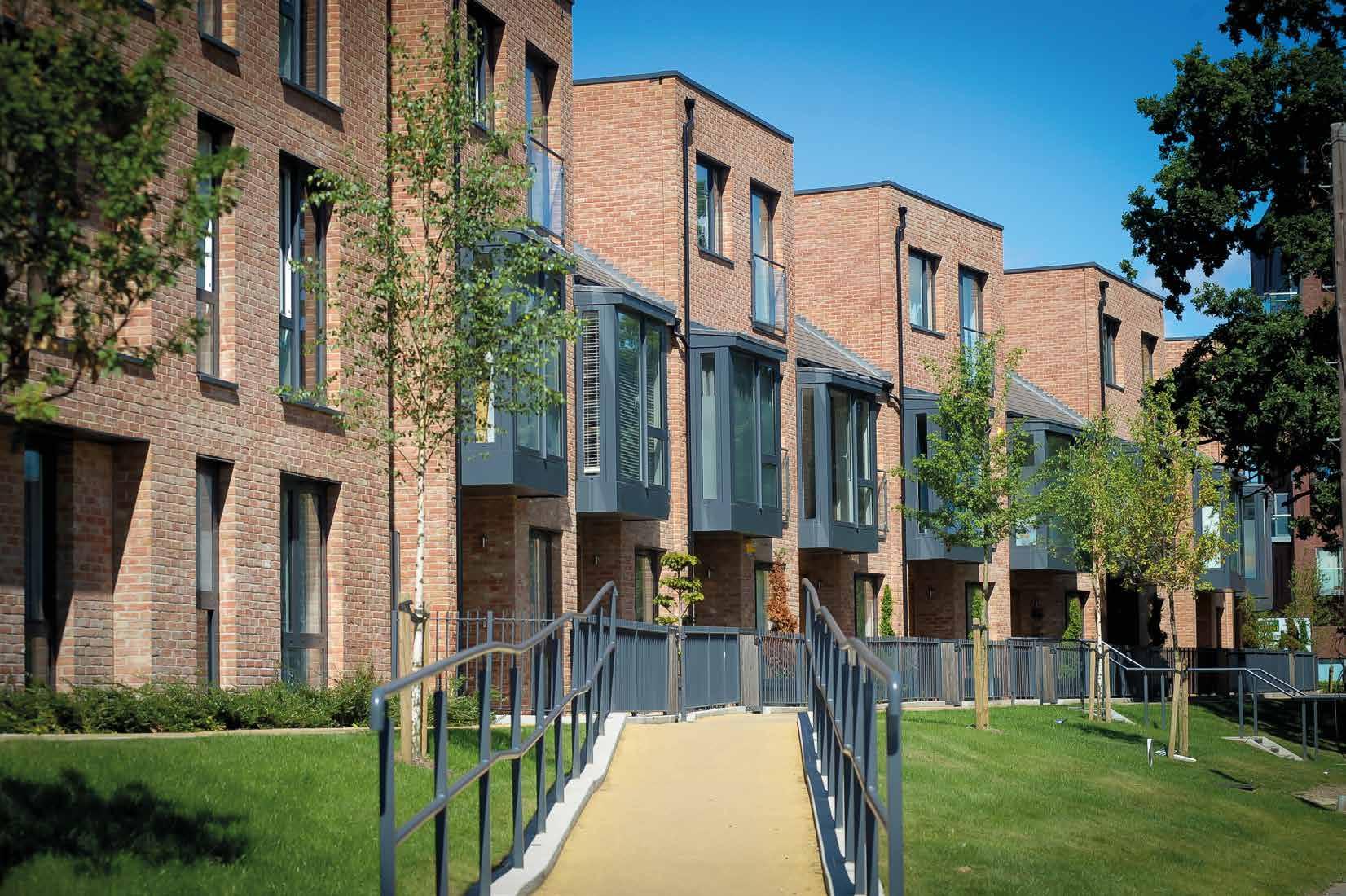
Helping housebuilders comply and compete in challenging markets, our precision-engineered light steel frame systems deliver assured performance better than, faster than and more cost-efficiently than other market
EOS is taking the construction industry forward by pioneering a certified light steel frame systems approach. Through the collaborative expertise of Etex brands – EOS Framing, Siniat, Promat and FSi – our 2D panelised solutions eliminate the uncertainty surrounding specification decisions.
Unitised loadbearing systems
• Winner Best External Product Housebuilder Awards 2021
• Custom-designed systems for external/internal walls and internal/separating floors
• 60, 90 and 120 minutes fire resistance options THRUWALL ®
Non-loadbearing infill systems
• Supplied as custom-designed certified kit of parts
• Can be applied to concrete or steel main frames
• 60, 90 and 120 minutes fire resistance options
Panelised non-loadbearing infill systems
• Custom-designed infill systems achieving 60 minutes fire resistance
• Prefabricated offsite and delivered to site as an assembled panelised unit
• Reduces construction programmes by up to 30%
Meeting requirements of External Wall Fire Review - EWS1, our unitised systems get the safety and building performance balance right through the combination of light steel framing, external sheathing, internal wall linings and glass mineral wool insulation. Only tested configurations are available for specification.
When Thrubuild®, Thruwall® and PAF systems are built with Etex Group components and materials, following a validation process - Etex award a 30-year product and performance warranty.
*
We take our responsibilities as a manufacturer extremely seriously.
Our light steel frame systems are meticulously tested, manufactured under ISO 9001:2015 quality management standards and are backed by Buildoffsite Property Assurance Scheme (BOPAS) Accreditation.
A warranty provision which demonstrates to lenders, valuers and purchasers that homes built from non-traditional methods of construction will be delivered to high quality standards and will be mortgageable for at least 60 years.
Annually we conduct over 500 tests in Europe alone. Etex Group have three Innovation and Technology Centres where we have our own fire, acoustic, mechanical, structural and thermal testing facilities, equipment and laboratories. We work closely with certification bodies to jointly develop and design technical solutions. Our full-scale testing regimes study the performance of products working together to see how they interact in ‘real’ circumstances, such as under fire conditions or when exposed to wind and rain.
DEVELOPER: Sky House Construction
ARCHITECTS: CODA
STRUCTURAL SYSTEM: Thrubuild®
LOCATION: Waverley Phase 02, Sheffield/Rotherham
Based on the ‘back-to-back’ concept –the Sky House design with saw-toothed roofs references the areas industrial heritage. Featuring 40 of the next generation three-bedroom flex Sky Houses and four-bedroom end townhouses –all homes are tailored for the design conscious buyer.
Delivering structures faster backed by the latest testing and engineered to the latest Eurocodes, Thrubuild® was selected as it integrates complete walling and flooring solutions which offer performance guarantees and fire resistance of 60 – 120 minute options.
Engineers from EOS worked with the architectural team to rationalise the design by adjusting walls and loading path lines through the building, optimising the cold rolled steel Thrubuild® solution and value engineering out various hot rolled steel elements. Reducing costs and construction carbon emissions.
Using an offsite system approach achieved predictability of costs and enhanced the construction programme – shaving months from the build schedule. Sky House Construction were therefore able to reduce financing costs and shorten the period of construction liability for Waverley Phase 02.
Contemporary thinking runs right throughout this project – with increasing build quality, the safety and wellbeing of occupants being central to every design and specification decision. Creating bright, airy and spacious accommodation, Sky Houses set the standard for 21st Century living.
e-house showcases our new service offering which will be available in 2023. Constructed from our awardwinning Thrubuild® system, e-house is the ultimate in advanced offsite construction delivering outstanding pre-manufactured added value with various factory fitted cladding, window and door options.
Our demonstration e-house presents the ideal opportunity for housing developers, architects, engineers and specifiers to get down to the detail and discover how this advanced systems approach can deliver residential projects in record time whilst enhancing build quality and performance values.
Designed to inspire and inform, the EOS technical team host CPD events, factory visits and site study tours for architects, contractors, engineers and clients. These sessions offer the opportunity to find out more about the technology and discover what makes EOS market leaders in light steel frame solutions.
TO REQUEST A CPD OR REGISTER YOUR INTEREST FOR A FACTORY OR SITE STUDY TOUR, PLEASE GO TO : www.eosframing.co.uk/contact-eos-framing/eos-cpd-events
A key advantage of light steel frame is its fire performance and protection from weather during the construction process. The amount of combustible materials in a light steel framed building is much lower, therefore the fire risk during construction and when in use is vastly reduced. Steel is non-combustible and does not add to the fire load of a building – reducing the fuel for a potential fire limits risk of damage and injury.
Developed in collaboration with our Etex group partners, Siniat a leading expert in plasterboard and drylining systems and fire protection specialists Promat and FSi – our Thrubuild® loadbearing, Thruwall® and PAF non-loadbearing systems range combines our technical and manufacturing expertise to deliver tested and certified solutions for light steel frame construction –all from one supplier.
This approach mitigates risk for housing developers because all components in our unitised walling and flooring systems are rigorously tested together to verify compatibility and certify technical performance. Our systems range provides total confidence and peace of mind for residential specifiers.
The overriding benefits of safety, quality, speed, strength and value are widely acknowledged but the sustainability benefits of light steel frame are often overlooked. Steel can be recycled or reused endlessly without detriment to its properties. This unique characteristic gives steel a high value at all stages of its lifecycle.
Steel recycling is highly developed and extremely efficient. Recovery rates in the UK are 99% for structural steelwork and 96% for all steel construction products – figures that far exceed those for any other construction material.
Light steel frame is often used for residential buildings where additional structural integrity is necessary and where a lightweight response is required. Offering the best strengthto-weight ratio improves efficiencies. This is where steel cannot be beaten. Lighter structures not only reduce material consumption but also concrete in the ground. Foundation loads and sizes are reduced by over 70% relative to concrete and block-work construction. Site waste is virtually eliminated by the use of prefabricated light steel components compared to the industry average wastage of 10%.
Our steel carries an Environmental Product Declaration (EPD) in accordance with EN 15804+A2 and ISO 14025 / ISO 21930. Made from 59% recycled content, our steel is 100% recyclable.
OSCO Homes custom design and build new homes predominately for the social housing sector.
Gwen Beeken talks about how EOS has become an integral part of the team.
We do not think our clients should ever settle for anything less than the best. Everything we do is bespoke and to the highest quality, we therefore required a light steel frame partner that was not only able to manufacture custom-made solutions to exacting standards but could offer continuous support and sound technical advice.
As a business we always strive to do more with the resources we have and part of our journey has been building our own skilled workforce. We wanted to build a culture that was supportive, created opportunity, drove continuous improvement and valued everyone. So supported by EOS we established a training facility in HMP Hindley where we prepared prisoners for employment on release. Highly successful it has reduced re-offending within the group to below 10% against a national average of 60% but even better, it has contributed to building our own skilled workforce many of whom continue to progress in the company today.
We refer to EOS as our ‘intelligent supply chain partner’ and when things do not go to plan – regardless of whether it is related to their elements or not – support and technical advice is always available.
With the backing of the EOS team, we have come a long way and we are now looking to break into the private housing and build-to-rent sectors.
Gwen Beeken Director, OSCO Homes
www.eosframing.co.uk/information-centre/#video-library
• A £250 million development located on the south bank of the River Thames.
• Delivered in four phases, comprising six buildings ranging from 11 to 15 storeys.
• The project created over 750 new apartments, including 197 affordable homes.
• The final phase was the first development in the UK to specify our Pre-Assembled Frames.
ENDERBY WHARF GREENWICH• A joint venture between Barratt Homes and Morgan Stanley Real Estate comprising 700 homes and leisure facilities. Offsite manufactured was crucial in achieving speed and quality of build.
• EOS engineered and manufactured bespoke light steel frame infill systems for the high-rise residential apartments.
• Transforming the former Young’s Brewery, Ram Quarter sensitively integrates historic Grade II buildings into a contemporary scheme.
• EOS designed, engineered and manufactured a range of around 15,000m2 of infill walling and 280m2 loadbearing steel systems for the project including preassembled window components together with non-standard use of our loadbearing Thrubuild® frames.
RIVERSIDE QUARTER WANDSWORTH RAM QUARTER WANDSWORTHOur unitised systems can form external and internal walls together with roofs and floors. From full loadbearing structures and modular applications to panelised non-loadbearing infill systems. Steel is non-combustible and does not add to the fire load of a building.
• EOS custom designed and manufactured a range of light steel framing systems for a new community of 412 homes by Barratt London.
• Providing a variety of apartments together with three and four bedroom houses, all homes have outdoor space – many with views across the Green Belt.
• Attractive mixed tenure development with more than 1,225 high quality private, shared equity and affordable rental homes.
• Working with Ardmore, EOS designed, engineered and manufactured light steel infill systems for phases three, four, five and six. This was a massive undertaking throughout a period of seven years –delivering a total 42,837m2 of light steel framing systems across four phases of the scheme.
• Barratt Homes development comprising 189 homes in linear blocks and also the refurbishment of listed B1 buildings, formally the Colart factory and offices.
• EOS designed, engineered and manufactured a loadbearing structure for the scheme including a modular system to extend the listed office buildings.
is part of a global group of companies –ETEX New Ways which brings together the products and solutions of major construction material providers. In partnership with housing developers, we deliver high-performance buildings that are safe, robust, sustainable and energy efficient.