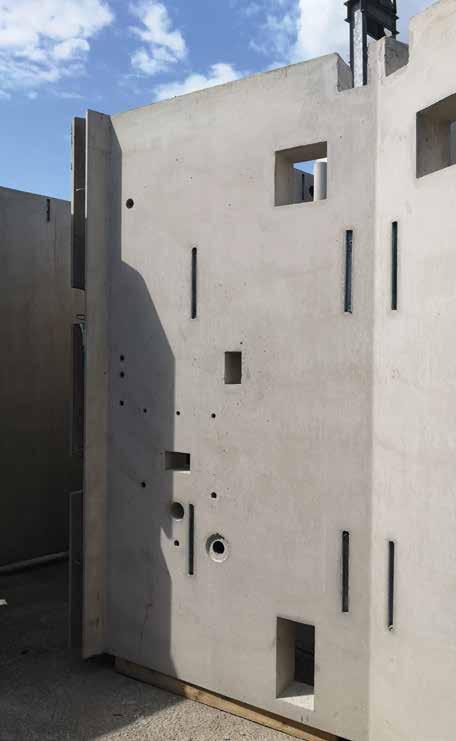
23 minute read
Decarbonising Precast Concrete
A new Innovate UK-funded pilot to decarbonise precast concrete in construction is looking to change perceptions about the material, help reduce carbon emissions and identify opportunities for sustainability improvements.
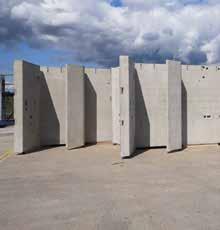
1 2
The UK’s built environment sector is turning its attention to the embodied carbon in buildings, which – according to the World Green Building Council – accounts for 11% of our national total emissions. Concrete, whilst a default choice for many structures, is acknowledged as a carbon-intensive material and a focus for an industry challenged to develop a roadmap to net zero. AMA Research has forecast that the precast concrete sector will grow by 18% to £2.3billion by 2024.
A collaborative team, led by design for manufacture experts Akerlof, alongside leading UK materials manufacturer Forterra and superstructure and façade construction specialist PCE, supported by engineers Curtins and sustainability consultants Accelar, has collaborated to research and develop processes that significantly reduce the emissions of precast concrete methodology and materials. Funded by Innovate UK and supported by the Ministry of Justice (MoJ) as part of its future capital programmes, this pilot project is aligned to the UK Government’s strategic commitment to develop low carbon infrastructure, decarbonise the economy and secure better outcomes for the environment.
3
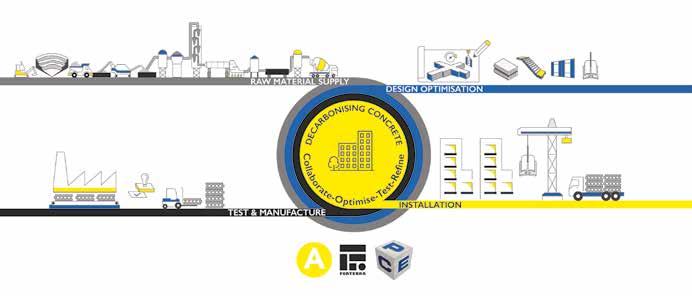
Gareth Jones, Head of MMC & Technical Services, Ministry of Justice, said: “This study demonstrates how collaboration through the supply chain can bring subject matter experts together to develop innovative solutions for decarbonising. We look forward to utilising and embedding such solutions in the MoJ’s New Prison Programme.’’
The Decarbonising Precast Concrete (DPC) project builds on the learning from recent research-based studies on ways to both reduce concrete used and apply lower-carbon concrete mix types, crucially applied against a real-life project. Through collaboration the integrated team have addressed gaps along a typically fragmented value chain, to enable iterative testing, robust data capture and detailed analysis at each stage in engineering an optimised system. Benchmarked against the performance of the MoJ’s existing delivery methods, the project outcomes are intended to be transferable to other sectors and development types, including student and rental housing, and major health and education infrastructure.
“We urgently need to find ways to decarbonise the delivery of the UK’s future infrastructure and buildings with solutions that are commercially competitive,” says John Handscomb, Founding Partner, Akerlof. “This pilot brings together innovators from each stage of the process to tackle this challenge directly through a real-life project. We are extremely hopeful that in demonstrating significant carbon reductions we will be able to formalise a project model that can enable others across the industry to apply to their development pipelines, to deliver better outcomes.”
Traditional concrete manufacture is a fuel-intensive, electro-intensive and therefore carbon intensive process, using cement, said to be responsible for as much as 8% of the world’s carbon dioxide emmisions. While addressing its material makeup to lower manufacturing and embodied emissions is critical to decarbonising, the pathway to net zero relies upon a holistic view: with intelligent design that minimises material use without affecting a structure’s integrity, as well as an understanding of a product’s transport and installation emissions. The DPC project is made up of three stages:
• Design Solution Optimisation – minimising material use at the source • Material Development and Testing – incorporating use of novel cement and/or clinker substitution technologies and admixtures • Production and Logistics Review – identifying opportunities for improvement in carbon emissions.
“This is a UK team, backed by UK innovation money,” said Stephen Harrison, CEO at Forterra. “Trialling a way to help UK construction lower its carbon emissions – a vital focus to keep our climate goals within reach as recovery measures stimulate the sector to increase building.”
Jonny Voon, Head of the Sustainable Innovation Fund at Innovate UK, added, “Decarbonisation of concrete manufacturing is fundamental to helping the UK government achieve its net zero ambition of slashing emissions by 78% by 2035. Innovate UK is proud to support the project and an exciting consortium with their world-leading efforts.”
The pilot’s findings and recommended future methodology, expected to be released in June, will be shared with the sector to enable it to consider a more holistically-sustainable approach as it ramps up delivery of new buildings and infrastructure postpandemic.
Simon Harold, Business Development Director, PCE, says: “By looking in the round at one important aspect of delivering today’s buildings, we are confident we’ll find a relatively simple, cost-effective and eminently scalable way to reduce carbon emissions, benefitting our clients’ communities as well as contributing to the UK’s efforts to hit its net zero carbon target.”
For more information visit:
www.akerlof.co.uk www.forterra.co.uk www.pceltd.co.uk
Images:
01-02. The award-winning Wellingborough Prison 03. The route to decarbonising precast concrete. Courtesy Akerlof, Forterra, PCE
USING CONCRETE TO REDUCE WAVE ENERGY COSTS
Wave energy has the potential to contribute to the UK’s race to reach net zero carbon by 2050 with precast concrete a major factor in making this happen. Karoline Lende, Engineer, Advanced Digital Engineering for Arup explains more.
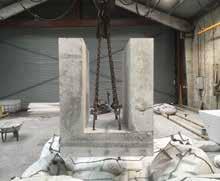
1
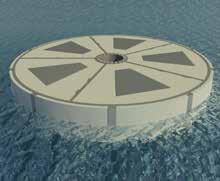
The current cost of wave energy converters (WECs) means large scale deployment is not yet commercially viable. Funded by Wave Energy Scotland (WES), a team of structural engineers from Arup has been looking at ways in which concrete can help reduce the cost of WECs, and ultimately ensure that the wider wave energy sector can adopt these innovations.
The Arup team has been seeking to unlock the opportunities for innovative concrete construction techniques to drive down the cost of WECs, which are typically constructed from steel. Following a sector-wide review of WEC types, floating devices were found to have the most potential for innovation and cost reduction. For these devices, structural concrete offers a more efficient solution by using the weight of the structure directly, rather than requiring additional ballast.
After a series of research, design, modelling and physical testing stages, Arup’s specialist material and structural experts concluded that the use of concrete for WECs could reduce the through-life cost of floating wave energy devices by up to 20%.
Whilst concrete is a widely used and well understood material in the built environment, its use in lightweight floating structures is less well established. To demonstrate the technical feasibility of using concrete for floating WECs, Arup developed two concrete designs to Front End Engineering Design level, working closely with contractor BAM to develop innovative manufacturing solutions and drive down cost. This included designing a load-bearing precast concrete connection detail, which underwent full-scale physical testing to demonstrate watertightness. The interleaved T-headed bar connection detail achieves full load transfer at the joint whilst using hydrophilic strips to prevent water ingress.
Arup also explored the wider benefits from using concrete beyond cost reduction. The material can take advantage of a mature supply chain and increased local construction content. Concrete has superior durability compared to steel in the offshore environment and can typically offer a 50-year design life, further reducing through-life cost. Arup also assessed the embodied carbon of different designs, concluding that concrete devices would be more favourable than steel devices in terms of environmental impact and global warming potential. To enable WEC developers to understand and realise the potential for concrete, Arup has placed great emphasis on disseminating the findings of the project. They have created a digital decision-making tool – Convex – helping WEC developers exploit the knowledge gained throughout the project by assessing the feasibility of incorporating concrete in their designs.
The Arup team have demonstrated the commercial opportunity associated with concrete WECs. With further work by WEC developers and the concrete supply chain to maximise the chance of successful exploitation, wave energy could play an important role in the UK’s renewable energy mix. Arup are continuing to work with developers in this innovative sector and has transferred the findings of the study to floating offshore wind substructures where concrete could also have a significant impact.
2 3
For more information on Convex visit:
http://convex.ade.arup.com/
Images:
01. Arup’s concrete design of the
Carnegie CETO 6 1MW WEC device 02. Full-scale physical testing of precast connection detail 03. Precast components of Arup’s concrete design of the CETO 6 device
THE CHALLENGES OF A ‘NEW NORMAL’
Earlier this year, Ultrapanel Building Technologies launched its next generation of ‘room in the roof’ systems, combining offsite techniques and advanced manufacturing technology to help the housebuilding sector deal with a ‘new normal’.
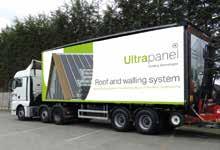
1
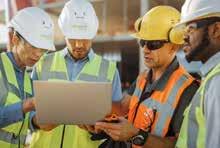
The pressure of operating COVIDsecure construction sites, combined with tough schedules, supply chain issues and difficult specification decisions, are all taking a toll on housebuilders. There is also a widespread agreement that in order to operate effectively and safely, developers need to reduce their reliance on labour-intensive traditional construction methods and look to new advanced offsite approaches.
A Brexit-driven fear of a skills exodus, compounded by chaos in construction supply chains and materials shortages, are also creating a climate for rapid change. Many are now realising that taking the construction process into well-managed factory environments where social distancing measures are easier to implement, is just one of many benefits.
It is not only construction methods that are going through a period of unprecedented transformation – working remotely has altered not only the way we use our homes but is also creating a change in consumer demand and maximising available space is now a priority.
Tried and tested by one of the UK’s largest housebuilders, the new Ultrapanel system provides invaluable benefits for volume housebuilders not only looking to create space and increase revenue, but also to
2
overcome supply chain concerns and eliminate complex performance and safety specification issues from the critical construction timeline.
The Ultrapanel ‘room in the roof’ system is both lightweight and easy to manoeuvre, reducing the cost and complexity of expensive lifting equipment and on-site cranage. The Ultrapanel system can be installed by a team of three with a telehandler in just one day to achieve a rapid weathertight building envelope. The adaptable system creates 50-60% more usable space than traditional attic trusses.
Importantly, windows and dormers can be placed anywhere in the roof with no ‘dead zones’. This means that the layout of the top floor room can be maximised as windows can be placed exactly where they are needed, even above staircases to bring natural light into the floors below. As Ultrapanel has no traditional roof trusses or purlins, the ceiling can be vaulted, allowing space for mezzanine floors in some roof designs.
“The complete Ultrapanel system is the only ‘room in the roof’ solution with BBA certification and NHBC Accepts,” says Andrew Thomson, Ultrapanel’s Design and Development Director. “This provides assurance to housebuilders that the structural, thermal, condensation and fire risk have all been independently verified. The design has a structural eaves section which distributes the load into the supporting walls, so the support traditionally required either side of a roof opening does not need aligning with the wall below. The absence of internal structure means maximum flexibility to utilise the space.”
Precision engineered in one ‘unitised hybrid panelised solution’ the Ultrapanel system maximises the material properties of the structural steel and timber elements, integrated with a high-performance insulated core. Mass customisation techniques at high capacity ensure simultaneous volume production of various roof types with vaulted ceilings, mezzanine floor options, and the ability to accommodate dormer or inline windows.
“We have been developing the system over the past four years alongside major housebuilders to ensure we get off to a quick start,” says Andrew. “We have developed a version of the panel utilising non-combustible materials which we use for the party wall structure and we will continue to extend applications of this new material.”
With a two-week flexible lead time and an established supply chain, the Ultrapanel system can help volume housebuilders overcome the challenges of the ‘new normal’ and deliver critical time and space gains.
For more information visit:
www.ultrapanel.co.uk
Images:
01-02. On-site work can be minimised easily using factory-manufactured elements.
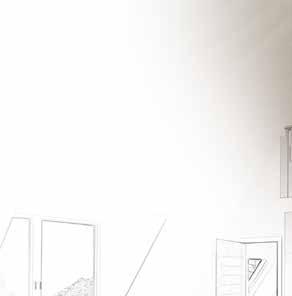
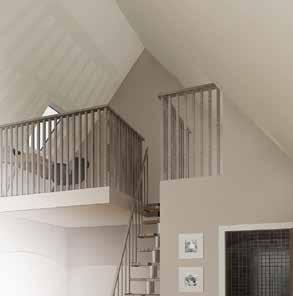
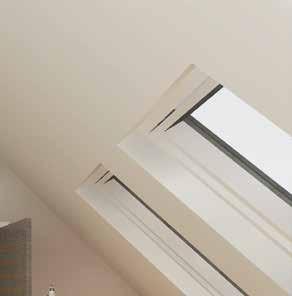
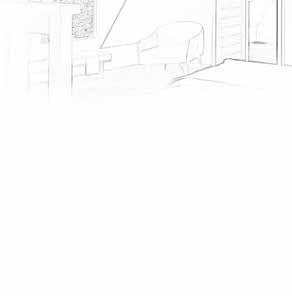
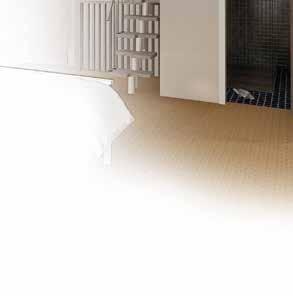
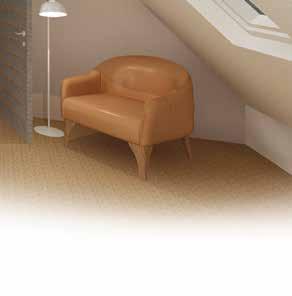
MODULAR ON TREND FOR CREATIVE HUB
Finalist in the Offsite Awards in two categories, Boho 8 is the latest phase of Middlesbrough’s commercial campus for the town’s digital media, technology and creative sectors.
Supported by the Local Growth Fund from the Tees Valley Mayor and Combined Authority, the £2.5million project, provides additional growth space for local companies and is also intended to attract a new cohort of creative businesses to the area.
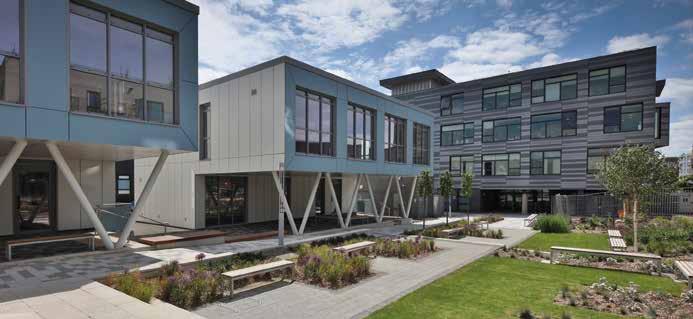
Middlesbrough Council carried out a ‘demand survey’ with digital and creative companies based in and around Middlesbrough, this demonstrated that there were high levels of growth but no suitable quality office accommodation. The timescales these companies identified meant the Council had to consider alternative methods of construction to traditional build. The additional offices were required as a matter of urgency to ensure expanding companies remained in Middlesbrough and continued to provide local employment opportunities.
Modular construction was identified as a means to deliver high-quality, environmentally friendly units that could be in situ in six months to meet this demand. The production methods involved ensured that materials were used more efficiently and accurately, eliminating onsite waste. On average 67% less energy is required to produce a modular building and up to 50% less time is spent onsite when compared to traditional methods, resulting in up to 90% fewer vehicle movements which in turn, reduces carbon emissions.
Consortium Procurement Construction (CPC) worked closely with Middlesbrough Council and Faithful+Gould (F&G) through the MB1 Modular Buildings Framework – resulting in the appointment of modular specialists M-AR to deliver the complete project, from groundworks to final commissioning. The award-winning concept by Seymour Architecture creates highquality facilities encompassing four, one to three-storey modular cantilevered buildings ranging from 1,000 to 3,000sq ft delivered by main contractor M-AR who designed, engineered, manufactured and installed the volumetric modular solution.
Predictability of Price, Programme and Performance
From the outset, the Council worked with consultants F&G to benchmark costs, timescales, quality standards and energy efficiency of modular technology against traditional construction methods. Through this work the Council agreed there would be little cost difference between modular and traditional approaches and placed the emphasis on the speed, safety and quality standards of the development.
The supply chain simplicity offered via M-AR’s complete turnkey modular approach, removed many complexities from the critical construction timeline. The pandemic had the potential to create serious challenges for this build, but the modular approach delivered predictability of price, programme and building performance. M-AR are at the forefront of advanced building technologies, ensuring projects are digitally constructed and virtually tested before they enter the company’s controlled manufacturing environment.
1
This technology-led approach consistently reduces defects and increases quality and accuracy.
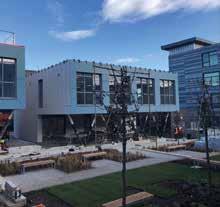
The project began in August 2020, with the modules being manufactured at M-AR’s offsite factory facility where quality controls are embedded into the manufacturing processes. Modular builds are not susceptible to poorly specified products as time is taken upfront to validate the correct specification of materials. With a powerful combination of controlled deliverables and customisable outputs, modular construction provides repeatable quality and enhanced building performance. Simultaneously M-AR’s groundwork team carried out all elements of ground remediation, drainage, strip foundations and RC piers, cross-site services, retaining walls, steps, podia seating together with hard and soft landscaping.
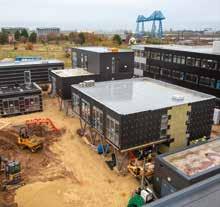
Just eight weeks later, four office blocks consisting of 18 individual 49sq m modules were completed and quality checked and were installed over a five-day period. Middlesbrough Mayor Andy Preston said: “Great buildings attract jobs and investment. They can also help create better working environments which stimulate good mental health and productivity – Boho 8 definitely does that.”

Full Turnkey Package
The modular units are steel frame with a Class B HPL Formica cladding system on 110mm rockwool slab insulated rail system. Total fit out was included in M-AR’s full turnkey package which consisted of open planned office space, toilet and kitchen facilities, all finished with suspended ceilings, carpeting and tiled floors to wet areas. The majority of M&E was factory-installed with final connections between modules and floors and roof mounted equipment taking place on-site followed by testing and commissioning. The innovatively designed and constructed light, bright and inspiring offices provide ideal spaces for ambitious and contemporary businesses. Achieving excellent EPC Rating of A and air permeability of 4.69 m2/(h.m2) @50 Pa – this will reduce heating requirements and carbon emissions for the lifetime of the buildings.
“The quality of the development and the fit out of the office units is equal
3
to, if not higher quality than traditional build methods,” said Michael Canavan, Project Manager for Middlesbrough Council. “All parties involved in the Boho 8 project have been extremely impressed. The speed of delivery and certainty around offsite construction provides more reassurance that projects will be delivered on time and within budget. Boho 8 is a perfect example of this, having been delivered on time and within budget whilst navigating the implications from Brexit and freedom of trade as well as two lockdowns as a result from the COVID-19 pandemic.
“There have been a number of traditional construction projects that were adjacent to Boho 8 on-site before and were due to complete before Boho 8 that have still not completed. The Council will definitely use offsite technology as part of its future development projects and is currently looking at potential sites where the construction method would be better suited to deliver the Council’s ambitions.”
2
4
For more information visit:
www.m-ar.co.uk
M-AR have been nominated for Best Commercial Project and Client of the Year 2021 for their work on BoHo 8.
Images:
01-04. The work on Boho 8 has seen modular offsite techniques deliver on Middlesbrough Council’s creative ambitions. Courtesy Seymour Architecture, KMC Photography and M-AR
CASE STUDY OFFSITE CROSSING SUCCESS

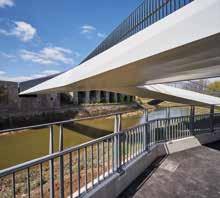
The St. Philips pedestrian and cycle bridge in Bristol spans the River Avon. It’s offsite design and installation contributed much needed accessibility to an isolated area.
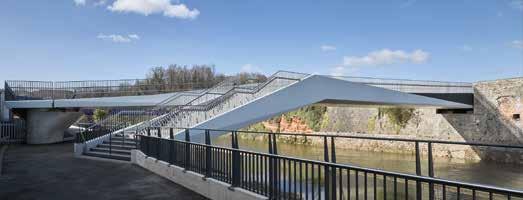
The new St. Philips pedestrian and cycle bridge is one of two pieces of infrastructure recently built in Bristol to increase the city’s sustainable transport network and to improve accessibility to Temple Island, a centrally-located area behind Temple Meads railway station restricted to rail-related uses for more than 150 years.
The new crossing spans the watercourse, connecting the area with a riverside pedestrian and cycle path. The footbridge connects two banks with a significant difference in elevation (approximately 5m), appearance (historic stone wall with relieving arches and green slope), ground conditions and accessibility. The footbridge – a 50m-span and 4m-wide steel beam with a forked geometry – seamlessly hosts a ramp for disabled users and cyclists and a staircase to maximise functionality in a very limited space.
The challenge for the location of the bridge over a river with a 5m tidal range and especially soft ground and limited access in one of the banks, were significant constraints for the design, the material choice, and the decision to maximise offsite construction in the project. Bridge supports within the river and the tidal zone were rejected early in the design process to minimise the impact in an environmentally sensitive area. Offsite steel fabrication was the perfect approach to precisely realise the large, complex and sculptural multifaceted geometry, combined with enough lightness for installation in a single piece using a crane on just one of the banks. The bridge was fabricated in sections in the workshop, transported to site by road, and then assembled on Temple Island before being lifted into place with lattice boom mobile crane with a maximum capacity of 750t.
The bridge was designed as a sculpted shape to compactly respond to such a constrained crossing. The innovative steel beam with a forked geometry maximises functionality in a very limited space. It naturally guides people along the desire lines and does not restrict potential future connections when the current industrial area will be redeveloped. Offsite construction was crucial for the delivery of such a large and wide object. The inherent cost benefits of offsite construction enabled high-quality architectural design that may not otherwise have been deliverable on budget in that site, by making possible the exacting fabrication of a complex steelwork and its installation in a single crane lift.
The use of offsite technology was a key factor in delivering the project, by significantly reducing the programme, financial and safety risks whilst ensuring a high-quality finish was achieved. The fabrication and assembly of such an atypical steel box girder was extraordinarily challenging due to the number and variability in geometry of the internal longitudinal ribs and diaphragms. To avoid compromising the legibility of the object, external welds and local deformation caused by internal welds should not compete with the edges of the origami shape. The hugely successful result was thanks to the offsite fabrication – which allowed for precise work within tight tolerances – as well as the skills and experience of the steel fabricator and contractor.
The installation of the structure itself, after assembly, was undertaken in a single day, reducing disruption to the construction site and minimising environmental impact. Offsite technology gave greater cost predictability for the contractor, meaning there was less risk in the pricing, giving both client and contractor greater cost certainty. Traditional onsite construction would have been barely feasible, within a reasonable budget, at this location due to limitation in site access and the characteristics of the ground and tidal river. Offsite technology provided extraordinary benefits compared with traditional onsite construction, in terms of programme reduction, financial and safety risk management and quality of the final product.
1 2
3
For more information visit: www.knightarchitects.co.uk
Images:
01-03. Bridge installation was undertaken in a single day and has transformed the area. Courtesy Knight Architects
OTL CELEBRATE 21 YEAR LANDMARK
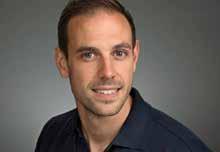
The original wet room former company, On The Level (OTL) is going from strength to strength and is celebrating 21 years in business.
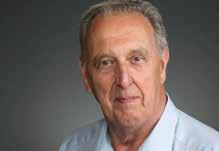
The company’s founder, Phil Clark, invented the patented OTL wet room former after seeing the need for a radically more effective kind of flooring. Thirty years as a builder spent installing shower areas for local authorities gave him the insight and experience to develop the revolutionary OTL shower floor tray, or ‘former’, out of a piece of timber which once installed could be covered with a non-slip vinyl sheet flooring – known today as OTL’s Level Access formers.
Back at the company’s beginnings, Phil started to manufacturer the formers by hand from a shed at the end of his garden in Watford. Today, each product is still hand finished by skilled craftsman, however they have since moved with the times using state-of-
Phil Clark
the-art machinery to create the perfect gradient for the quick flow of water.
Today the company is proud of the partnerships and strong relationships it has formed with a variety of builders, architects, interior designers, contractors, end users and showroom clients and has had its products specified and installed countless times across various sectors.
James Clark, OTL Managing Director, says: “Wet rooms continue to grow in popularity year-on-year, as their contemporary stylish designs suit the tastes of consumers, whilst also providing an inclusive bathroom space suitable for all. Our company has always been at the forefront of innovation in the marketplace, from being the first to create a former, introducing the most minimalist product on the market, to adapting and growing our capabilities to suit modern methods of construction. It’s a company I am proud to develop and see go from strength to strength as we continue to build our fantastic team and relationships with our clients.”
James Clark
For more information visit: www.onthelevel.co.uk or email: info@onthelevel.co.uk
CELEBRATING 21 YEARS
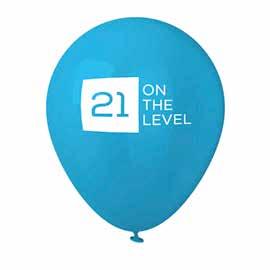
FIND OUT MORE
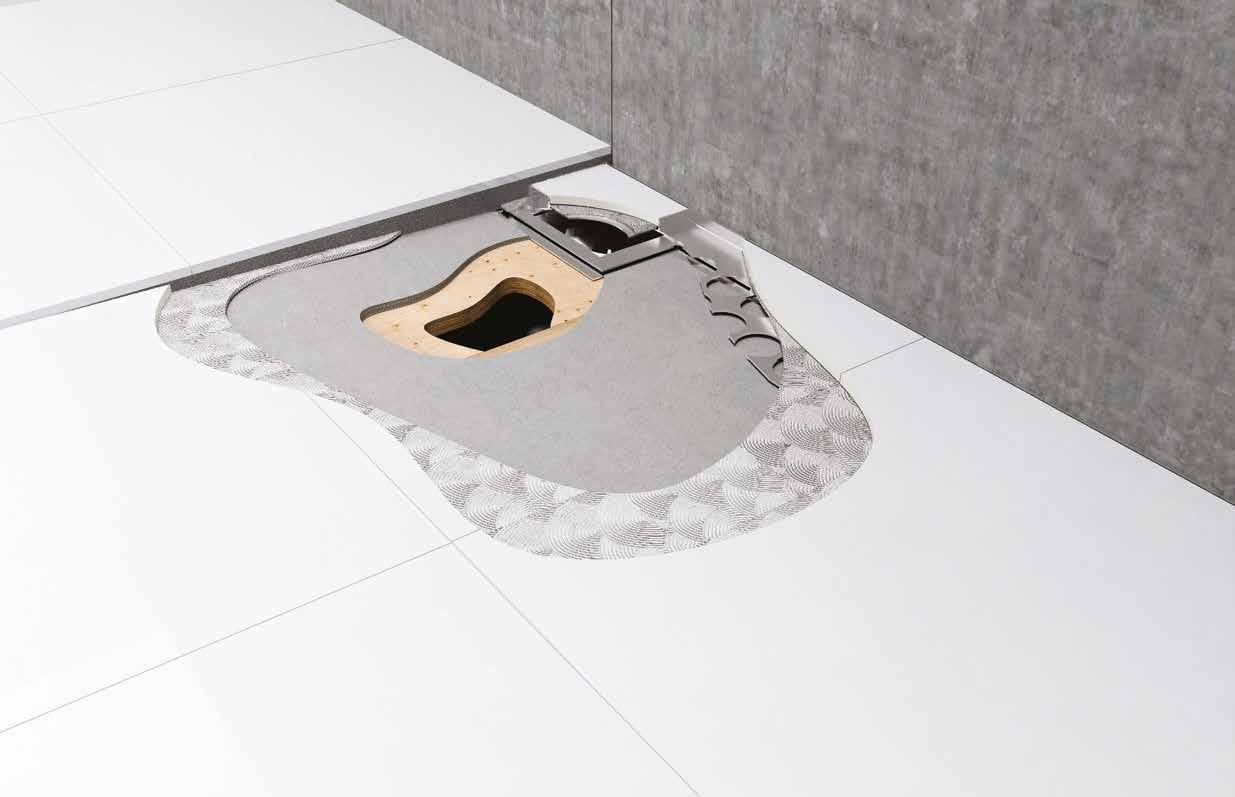
THE UK’S SPECIALIST WET ROOM FLOOR MANUFACTURER
Bespoke has been our specialty for 21 years, so nothing comes close to our UK made water control systems.
A MODERN TOUCH FOR LONDON TOWNHOUSES
FLEXIBLE, MODULAR AND SUSTAINABLE
Specialist external brick and terracotta cladding systems supplier Aquarian Cladding Systems has provided a perfect modern construction solution at the historic Dulwich Estate in south London.
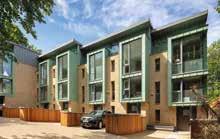
Designed by Syte Architects and built by Aspect Construction for specialist developer Lightbox, Edward Milner Terrace is a collection of five-storey townhouses. With strong emphasis on the Georgian and mid-century aesthetic of the area, the contemporary townhouses were clad with the Gebrik Brick Cladding System, courtesy of Aquarian, combined with copper, zinc and large feature windows.
“CoreHaus utilises a hybrid of modern methods of construction (MMC) categories 2 and 5 – a pod and panelised approach to provide high levels of flexibility whilst solving a wide range of construction challenges,” explains Scott Bibby, CoreHaus, Managing Director. “This allows the full implementation of Matthew Horn of Lightbox explained: “We wanted a product that reflected our modern approach to construction and Aquarian offered the perfect solution of Gebrik, a modern building solution that suited the constraints of our steeply sloping, wooded site. We required an externally insulated cladding system that ensured we had maximum internal room sizes on our concrete structure, was quick to install and easy to use. The lightweight and compact nature of the product was also an important feature.”
The Gebrik solution has robust and extensive fire test data, including five successful BR135 Classification Reports – it could also be fixed directly into the concrete of the end units, which had exposed textured walls. With a U-value of 0.19W/m2K on a 328mm total wall thickness, SAP issues were also greatly reduced. Aquarian’s Sales Director Jazz Rigden, says Edward Milner Terrace is yet another success story for Aquarian and Gebrik. “The development is hugely impressive, and we’re delighted Lightbox found Gebrik to be the perfect solution at Edward Milner Terrace. Our systems are tried and tested, and they guarantee simpler, faster builds that require little or no maintenance, performing precisely as they should.”
For more information visit:
www.aquariancladding.co.uk
Images:
01. The contemporary townhouses clad with Gebrik
CoreHaus Ltd, launched in 2018, applies tried and tested construction technology in an innovative way to meet the growing demand for offsite solutions in the housing sector.
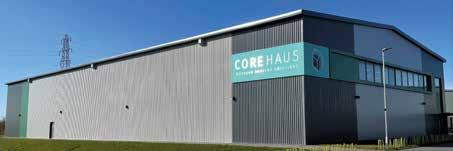
offsite manufacturing benefits into the process whilst maintaining customer choice in our solutions.
With principles based on ground and first floor standardised ‘modular cores’, CoreHaus provides a prefinished kitchen, staircase, WC, central heating, electrical control systems and bathroom. A customisable external finish allows CoreHaus homes to be built in any location regardless of surroundings.
Backed in part by social enterprise Fusion 21, CoreHaus have the unique focus on not just supporting the housing market but making a genuinely noticeable impact socially and towards building a sustainable future for all. “Everything we do is underpinned by sustainability,” adds Scott. “From the flexibility of the design to the use of innovative materials and our commitment to delivering social and economic value.”
For more information visit:
www.CoreHaus.co.uk