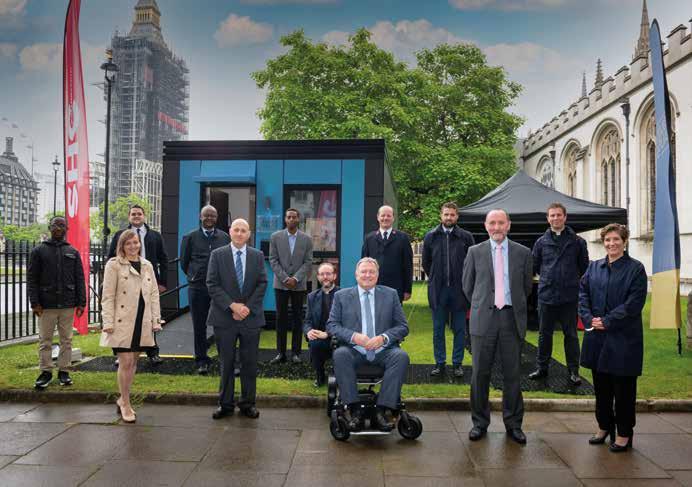
57 minute read
Industry News
MODULHAUS™ Takes Centre Stage at Westminster
Volumetric modular technology has been making national news headlines and receiving universal acclaim for bringing much needed facilities onstream in record time to support efforts to mitigate the impact of the pandemic, but 28 June marked a first for the industry.
MODULHAUS™– a one-person volumetric modular home took centre stage in the grounds of Westminster Abbey opposite the Palace of Westminster to raise awareness of the plight of rough sleepers and demonstrate how modular technology can provide a high quality, cost-effective solution with all the benefits of a permanent dwelling but equally designed for relocation as required.
Through Foundation200, prominent housing developer Hill Group has pledged £12million to help end rough sleeping. VOLUMETRIC™ – a specialist manufacturer of custom-built homeless solutions has worked in close collaboration to design and manufacture bespoke MODULHAUS™ single person homes with 200 being gifted via Foundation200 to charities and councils across the country.
Under the new SHC Partnership, the Salvation Army, Hill Group and Citizens UK hosted the Westminster event for MPs, prominent charities, and council leaders to launch a new initiative to provide homes and support packages which promote independence, a sense of place and belonging. Invited guests had the opportunity to meet experts from the SHC Partnership and VOLUMETRIC™ to find out more details of the scheme.
Offering a safe, independent and innovative interim housing solution, MODULHAUS™ allows individuals to find the stability they need to secure a reliable income before making the transition to a permanent home. Delivered 100% complete, ready for simple site connection and commissioning, MODULHAUS™ proves that temporary accommodation does not have to be low quality and can be delivered to exceptional standards. The super energy efficient homes reduce ongoing energy costs to less than £5 per week – negating fuel poverty.
The energy strategy for MODULHAUS™ is designed to surpass the Future Homes Standards. Every module includes low energy lighting, white goods, controlled flow showers and dual flush cisterns to minimise energy and water consumption. Renewable energy technology is built into every home including air source heat pumps and mechanical ventilation and heat recovery (MVHR) systems. Through lean world class manufacturing principles combined with Design for Manufacture and Assembly (DfMA) protocols, a balance of mass standardisation with elements of interior customisation and colour combinations is attained.
VOLUMETRIC™ have a close partnership with Foundation200 but modules can also be procured directly outside of the charitable scheme and can be delivered as a basic module or on a full turnkey basis. Fully integrated maintenance packages are available if the turnkey option is used.
MODULHAUS™ can also provide keyworker accommodation at time of peak demand or a longterm adaptable asset investment for NHS Trusts. A community module is also available for shared dining and meeting facilities which can be customised to form office or learning spaces as required.
The BOPAS certified 60-year MODULHAUS™ design life opens up several funding options over longer periods of time which have the potential to reduce the impact on capital budgets. Futureproof and future ready – each MODULHAUS™ is a long-term asset delivered to a better performance specification than traditionally constructed accommodation.
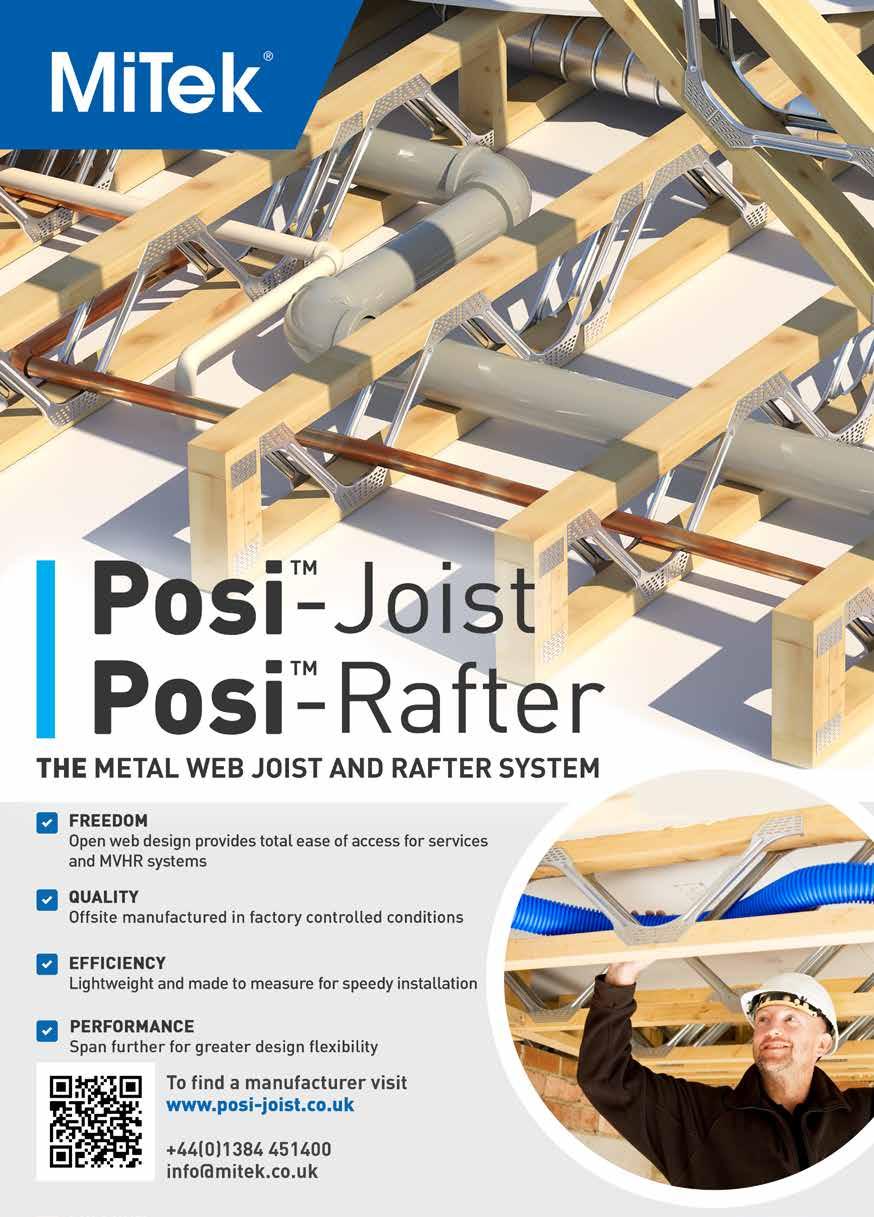
NHBC Accepts for Rollalong’s Modular Homes Offsite Suppliers Appointed to £330m Framework

Rollalong has been approved by NHBC Accepts, the industry standard accreditation scheme for the residential housing sector provided by NHBC. Rollalong is the largest permanent offsite manufacturer in the south of England and is now one of only two modular manufacturers in the UK using light gauge steel to have achieved this accreditation.
The accreditation allows Rollalong to register the modular homes manufactured offsite at its factory in Dorset with NHBC for a full 10-year warranty. NHBC Accepts is NHBC’s comprehensive review service for innovative products and systems. It is the fast-track route for acceptance for building products and systems used in homes covered by all NHBC warranty products. “This is a tremendous achievement by our team and I’m so proud and delighted by the news,” said Steve Chivers, Managing Director of Rollalong. “System approval by NHBC Accepts gives us an advantage and will help to cement our position as a significant player in the residential housing market.”
The Rollalong HDA System is an offsite, volumetric method of building houses based on light gauge steel structures. Floor, ceiling and wall elements are assembled together in the factory to create modules which are fully fitted out with fire linings, thermal insulation, breather membrane, windows and doors. The modules are then installed on-site on a prepared foundation, the roof is added and connections are made to the previously installed drainage and utilities services in the ground. Rollalong also recently completed its latest turnkey residential project, delivering 13 new modular council-owned homes in Barking, East London. The new homes installed on Sugden Way are part of a development managed by Be First for Barking and Dagenham Council.
“We’re extremely pleased to have completed this residential scheme which now provides a range of high-quality, affordable homes for people in Barking and Dagenham,” said Clive Harris, Construction Manager at Rollalong. “Like many parts of the UK, Barking and Dagenham suffers from a shortage of housing, and our modular approach offers local authorities a chance to address this shortfall in around half the time of a traditional build.”
Be First Construction Manager Sam Parry added: “We’re really pleased to say that in spite of coronavirus we’ve delivered 13 new affordable homes for the council in a fraction of the time a traditional build would take. More importantly, the standard is excellent, which means top-quality new homes for local people that will stand the test of time.” The new homes include a one-bedroom flat, eight two-bedroom flats and four three-bedroom flats.
The modules were transported to site and lifted into position and connected together over a five-day period, after which the internal and external finishing process commenced. Seventeen offsite manufacturers have won places on a new £330million public sector framework. The Modular Buildings (MB2) framework from LHC allows local authorities, social landlords and other public bodies to source preapproved specialist suppliers who can design, supply and install permanent, temporary, and refurbished modular buildings.
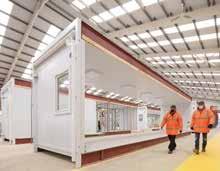
The framework is worth up to £250million in England, £60million in Scotland and £20million in Wales. It primarily covers education, healthcare, emergency services, offices and community related amenities such as sport facilities and theatres, but it can also be used for residential projects that are part of a mixed-use development or for student accommodation.
Dean Fazackerley, Head of Technical Procurement, said: “This framework provides contracting authorities with a pool of pre-approved suppliers who have won their place on the MB2 framework based primarily on the high quality of their work, but also the long-term value they can deliver. The consistent quality that modular building offers can help to not only provide more efficient projects that have lower lifetime costs, but can also help local authorities, NHS trusts and other public bodies work towards their net zero targets by providing better fabric performance.
Commenting on its framework appointment, David Harris, Managing Director of Premier Modular, added: “The framework allows public sector construction clients to radically reduce the time and cost of procurement, with the additional benefits of instant access to project data, guaranteed service levels, best value pricing, and faster project commencement. Our success in so many lots and geographical regions on this prestigious and long-established framework highlights the scope, quality and diversity of our hire buildings and offsite construction solutions for public sector clients across the UK.”
LHC are looking forward to working with the Appointed Companies to deliver outcome-based solutions which deliver social value and community benefit for our clients in line with LHC’s Lifetime Values.”
The MB2 framework will run until May 2025. For more information on the framework visit the LHC website: www.lhc.gov.uk
ADVERTORIALADVERTORIALADVERTORIALADVERTORIAL
STRATEGIC APPOINTMENTS ESS MODULAR GROUP STRATEGIC APPOINTMENTS ESS MODULAR GROUP STRATEGIC APPOINTMENTS ESS MODULAR GROUP STRATEGIC APPOINTMENTS ESS MODULAR GROUP ATATAT AT
Bill
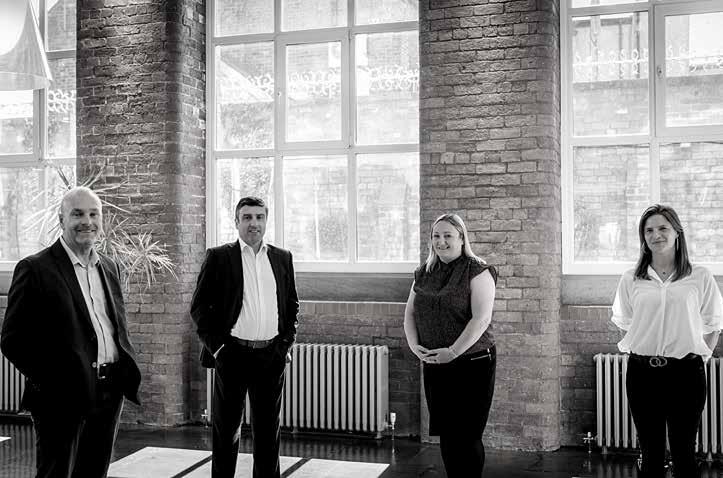
Bill
BillBill Marsh,
Marsh,
Marsh,Marsh, Jonathan
Jonathan
JonathanJonathan Airey, Airey, Airey,Airey, Karen
Karen
KarenKaren Morley
Morley MorleyMorley and
and
andand Emily Emily EmilyEmily King
King KingKing
Andy
Andy AndyAndy Shaw
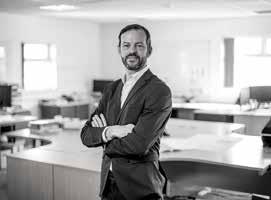
Shaw
ShawShaw Warren
Warren
WarrenWarren Donnelly
Donnelly DonnellyDonnelly Faisul
Faisul
FaisulFaisul Naqui
Naqui NaquiNaqui
ESS Modular has announced
ESS Modular has announcedseven new strategic hires toESS Modular has announcedseven new strategic hires toESS Modular has announcedsupport the continued growth seven new strategic hires tosupport the continued growthseven new strategic hires tothe Group across the UK and support the continued growththe Group across the UK andsupport the continued growthIreland.the Group across the UK andIreland.the Group across the UK and Ireland.Ireland.The senior appointments will of
of
of of
The senior appointments willbolster the existing managementThe senior appointments willbolster the existing managementThe senior appointments willteam in its drive towardsbolster the existing managementteam in its drive towardsbolster the existing managementcontinued product innovationteam in its drive towardscontinued product innovationteam in its drive towardsand sustainable construction. continued product innovationand sustainable construction.continued product innovation and sustainable construction.and sustainable construction.The company is also opening a
The company is also opening anew UK Headquarters in TraffordThe company is also opening anew UK Headquarters in TraffordThe company is also opening aPark, Manchester to support its new UK Headquarters in TraffordPark, Manchester to support itsnew UK Headquarters in Traffordcontinued growth.Park, Manchester to support itscontinued growth.Park, Manchester to support its continued growth.continued growth.The appointments include a
The appointments include anumber of seasoned and highlyThe appointments include anumber of seasoned and highlyThe appointments include aexperienced construction number of seasoned and highlyexperienced constructionnumber of seasoned and highly experienced construction experienced construction professionals who will take
professionals who will takethe following roles: professionals who will takethe following roles:professionals who will take the following roles:the following roles:Andy Shaw, Operations up
up
upup
Andy Shaw, OperationsDirector, ESS Modular GroupAndy Shaw, OperationsDirector, ESS Modular GroupAndy Shaw, OperationsEmily King, DivisionalDirector, ESS Modular GroupEmily King, DivisionalDirector, ESS Modular Group
Director, Spatial InitiativeBill Marsh, Head of
Director, Spatial Initiative
Production, ESS ModularBill Marsh, Head of
Production, ESS ModularBill Marsh, Head ofGroup
Production, ESS ModularGroup
Production, ESS ModularKaren Morley, Director of HR,GroupKaren Morley, Director of HR,GroupESS Modular GroupKaren Morley, Director of HR,ESS Modular GroupKaren Morley, Director of HR,Warren Donnelly, Director ofESS Modular GroupWarren Donnelly, Director ofESS Modular GroupCompliance, ESS ModularWarren Donnelly, Director ofCompliance, ESS ModularWarren Donnelly, Director ofGroupCompliance, ESS ModularGroupCompliance, ESS ModularJonathan Airey, Head ofGroupJonathan Airey, Head ofGroupProduct Development, ESSJonathan Airey, Head ofProduct Development, ESSJonathan Airey, Head ofModular GroupProduct Development, ESSModular GroupProduct Development, ESSFaisul Naqui, Head of IT, ESSModular GroupFaisul Naqui, Head of IT, ESSModular GroupModular GroupFaisul Naqui, Head of IT, ESSModular GroupFaisul Naqui, Head of IT, ESS Modular GroupModular Group Paul Tierney, CEO said "Our
Paul Tierney, CEO said "Ourbusiness has experienced aPaul Tierney, CEO said "Ourbusiness has experienced aPaul Tierney, CEO said "Ourperiod of rapid growth driven inbusiness has experienced aperiod of rapid growth driven inbusiness has experienced apart by the increased awareness period of rapid growth driven inpart by the increased awarenessperiod of rapid growth driven inof MMC and the significant part by the increased awarenessof MMC and the significantpart by the increased awarenessbenefits it can deliver, and in part of MMC and the significantbenefits it can deliver, and in partof MMC and the significantdue to the public sector demandbenefits it can deliver, and in partdue to the public sector demandbenefits it can deliver, and in partfor more healthcare, residentialdue to the public sector demandfor more healthcare, residentialdue to the public sector demandand education facilities.for more healthcare, residentialand education facilities.for more healthcare, residential
and andWe education facilities.education facilities.have strategically reviewed
We have strategically reviewedour organisation and, combinedWe have strategically reviewedour organisation and, combinedWe have strategically reviewedwith adding 80 new staff over our organisation and, combinedwith adding 80 new staff overour organisation and, combinedthe last 12 months, these keywith adding 80 new staff overthe last 12 months, these keywith adding 80 new staff overappointments will further supportthe last 12 months, these keyappointments will further supportthe last 12 months, these keyour vision for operational appointments will further supportour vision for operationalappointments will further supportexcellence and product our vision for operationalexcellence and productour vision for operationalinnovation. Their combined excellence and productinnovation. Their combinedexcellence and productexpertise will greatly support theinnovation. Their combinedexpertise will greatly support theinnovation. Their combined expertise will greatly supportnext phase of our growth. ” thenext phase of our growth. ” expertise will greatly support the next next phase phase of of our our growth. ” growth. ”
www.essmodular.com | @essmodular
www.essmodular.com | @essmodularMANCHESTER | LONDON | DUBLIN | BELFAST | CORK MANCHESTER | LONDON | DUBLIN | BELFAST | CORKwww.essmodular.com | @essmodular MANCHESTER | LONDON | DUBLIN | BELFAST | CORK www.essmodular.com | @essmodular MANCHESTER | LONDON | DUBLIN | BELFAST | CORK
NBS BIM Survey Wants Your Views
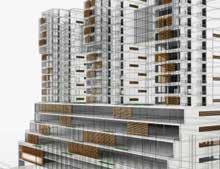
NBS the platform for connected construction information, has launched its annual survey with a new direction this year. For over ten years, NBS has been tracking the adoption of Building Information Modelling (BIM) via its National BIM Survey. The survey, previously known as NBS BIM Survey, will become the Digital Construction Survey from this year onwards. The survey, which is the most comprehensive in the sector, allows those working in construction, architecture and engineering among others, to better understand the status quo and developments to make informed decisions, leading to a safer industry. The construction sector has been implementing BIM widely over the last few years, with adoption standing at 73% in 2020. NBS wants to capture exciting new developments through the new iteration of the BIM survey with the aim of gaining a more comprehensive understanding of the current picture of digital transformation and day-to-day usage of technology.
The 2020 BIM report represented the views of over 1,000 industry professionals showcasing the adoption of BIM has grown substantially across the industry – in comparison, a decade ago, 43% of respondents had not even heard of BIM. BIM adoption by many in construction has helped transform how people work. While recognising that there are different views about the process of embedding BIM, NBS also sees other new ways of working and new technologies. NBS Research Manager David Bain said: “We have been monitoring BIM adoption at NBS for over a decade. Digital transformation is changing the industry, and it will continue to do so. We know an increasing number of construction professionals are beginning to adopt virtual reality and other technologies like modern methods of construction, and the effects of the pandemic have undoubtedly accelerated this. These new digital tools are transforming the construction sector and will likely lead to a better built environment. In this year’s survey, we are taking a step further and plan to look beyond BIM to some of the new technologies being used in the built environment. We look forward to seeing what progress we have made as an industry and what changes we anticipate in the next year.” The Digital Construction Survey is for designers, specifiers, manufacturers, contractors and others working in the built environment. The survey will monitor offsite construction, collaboration in the cloud and the impact of COVID-19 on the sector’s digitalisation.
For every completed response, NBS will donate £1 to the charity Crash. The survey should only take 10-15 minutes to complete. A pre-release report is sent to all participants, so those taking part will be among the first to access the findings.
You can complete this year's NBS Digital Construction Survey at: www.thenbs.com/digitalsurvey1
Premier Modular Delivers Offsite SEN Facility
Premier Modular has delivered a new £2million special educational needs (SEN) facility at Nethergate Academy in Nottingham – an Ofsted Outstanding special school for children with autism, learning difficulties and disabilities. The school is sponsored by Greenwood Academies Trust.
The main driver for Nottingham City Council’s decision to use offsite was the essential need to reduce noise and disruption to the children by moving construction work into a factory. The building also had to be delivered to a short programme ready for occupation for the start of the new academic year. To achieve this, Premier continued work on the project through the COVID-19 pandemic and lockdown.
Designed and built by Premier with delivery architects Lungfish, the scheme had to be installed on a constrained site within the fully operational school. Careful logistics planning and traffic management ensured access to the school was maintained throughout the construction programme. Cranage of the modules was also timed for the school holidays to further minimise disruption.
Commenting on the project, Sam Simons, Team Leader at Nottingham City Council said: “The children at the school have complex needs and site-based construction was not the best way to proceed because of the noise and vibration levels that would then be generated. Moving work offsite and into a factory was therefore a huge advantage. The manufacturing processes of modular construction also allowed the building work to continue safely during the COVID-19 lockdown. It is definitely easier to manage and maintain social distancing requirements in a factory environment than on-site.”
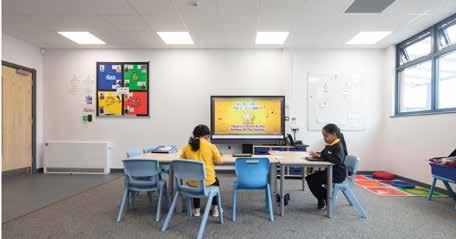
Tracey Ydlibi, Executive Principal at Nethergate Academy added: “Premier Modular was sensitive to the need for us to continue the day-to-day operation of the Academy and was able to complete the build with minimum disruption. Their team has produced a wonderful, purpose-built facility which will enable us to continue to provide the best possible educational experience and further meet the needs of autistic children with complex needs.”
Craig Taylor, Associate Director at Lungfish Architects, said: “The demand for offsite construction continues to grow and this project proves why. The Premier building system gives us a high level of design flexibility which ultimately improves the finished building in both aesthetics and functionality, and particularly when creating a learning environment to support SEN. We collaborated on the design with Premier to help deliver a new facility that will undoubtedly prove to be an invaluable addition to the academy and the community.”
The 710sq m building was fitted out offsite and has high quality pre-installed concrete floors for a robust finish. Facilities include classrooms for key stages 1 to 4, group therapy rooms with specialist multi-coloured lighting, food technology room, occupational therapy, staff room, and a double-height multi-purpose hall for dining, assemblies and indoor sports – all built using offsite construction. The design of the facility was developed to meet SEND principles.
Source: www.premiermodular.co.uk
Modulous Gets £5m Venture Capital Boost
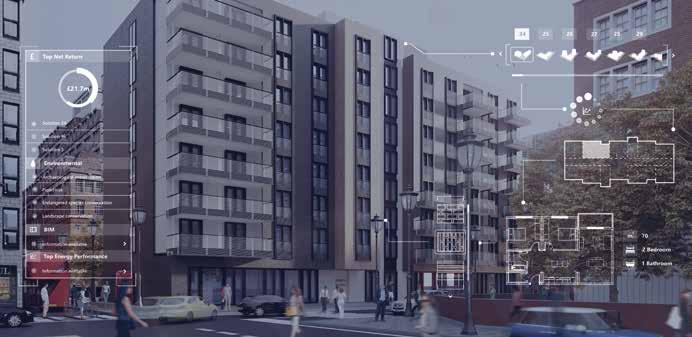
Three global venture capital firms have invested £5million into Modulous, to develop digital solutions to modernise the design and construction of affordable and sustainable housing. Modulous is an asset-light business with no factories. Instead, the company’s global supply chain and its investment in logistics will enable it to become more scalable and more responsive to the cyclical nature of housebuilding.
Blackhorn Ventures, CEMEX Ventures and GroundBreak Ventures have backed London-based Modulous which has created a software platform to streamline design and overhaul the inefficient logistics that weigh down the sector. Alongside its software platform, Modulous has developed a precision-engineered apartment product that enables high-quality, affordable, sustainable homes to be computer designed and delivered to a specific cost.
The new funding will expand the company's building design team and grow its technology group in order to speed up the evolution of its software platform being developed to exploit digital technology in a bid to make delivering homes better in every way.
The game-changer is that the Modulous design software platform combines with its own modular building system – its kit of parts. This enables developers and housing associations to specify the sort of building they want, harvest local planning regulations to determine what is permitted and then quickly generate designs that accurately detail the precise cost. Because every building component is mapped within the system - like a wardrobe from IKEA - it is possible to monitor and measure the carbon footprint of every single building on a mass scale. Sections of the building are supplied by a selection of high-quality supply chain partners, including Knauf, CEMEX, Ideal Standard and Ibstock. The software platform orchestrates the logistics to ensure that components arrive just in time and sequence - which can play a critical role in helping inflate construction companies’ margins.
Chris Bone, Modulous CEO says: “Our digitally-led approach to project management and innovative ‘kit of parts’ platform delivers sustainable, high quality housing at a fraction of the time of traditional construction. As the costs of materials rise and profit margins are continually squeezed, Modulous provides partners with the end-to-end tools necessary to accurately estimate project costs, compress programme timescales and mitigate against the risks inherent in planning, design and implementation. It’s a system that solves multiple problems plaguing the industry for decades, while engaging flexible, net zero-ready technologies that allow our partners to realise high-speed assembly and installation.”
Phillip O’Connor, Managing Partner and Co-Founder at Blackhorn Ventures, said: “This is about far more than modular housing. The opportunity here with the suite of products Modulous is developing is to create a standard akin to Pro Tools which can orchestrate and produce all elements of the housing process. Technology will not replace the many talented architects, engineers and construction workers – but simply enable them to focus on what they do best, making their jobs more profitable and enjoyable. And their capital-efficient, outsourced manufacturing business model allows Modulous to weather fluctuations in demand that characterize construction in contrast to capital-heavy, vertically integrated modular housing developers.” Mateo Zimmerman, Investment Manager at CEMEX Ventures, said: “We have to put industrialized construction and MMC at the heart of design, manufacturing, logistics and assembly. The change to a ‘product mindset’ (instead of project mindset) will open up many opportunities and benefits for our industry, such as efficiency, climate action and sustainable profitability.”
Scott Kaplanis, Partner at GroundBreak Ventures, added: “The scalability of the Modulous suite of products is vast and its ability to work with governments around the world to help solve global challenges of creating and delivering sustainable and affordable housing means we see a huge opportunity to grow the firm and support local construction firms and supply chains.”
By leveraging artificial intelligence and generative design alongside 5D Building Information Modelling (BIM), developers, contractors and housing associations can drastically reduce the time and cost overruns that have crippled the industry in recent years. Combining technology with a forward-thinking logistics platform will help accelerate the delivery of much-needed housing across the UK and respond to the government’s own review of construction from 2016 by Mark Farmer which said the industry needed to ‘modernise or die’. New building regulations have been introduced by the UK Government to ensure homes are ‘net-zero ready’ from 2025, but that means that homes being built between today and 2025 will require retrofitting to meet soon-to-be-introduced standards. Modulous’ BOPAS-accredited method of delivery is directly helping to combat these challenges by offering a quick and low-energy solution to housing delivery.
Atkins Appoints New Offsite Specialists
Atkins has appointed Rami Mansour as Head of Design for Manufacture and Assembly (DfMA) and Eugene Smethurst as Head of Lean to lead the company’s drive to help increase the efficiency of design and construction across the infrastructure sector.
Rami will help clients understand the suitability of different modern methods of construction (MMC) systems to their projects, whilst looking at a sliding scale of standardisation within their designs. Eugene’s role will focus on applying lean techniques from manufacturing and other industries into the infrastructure sector, ensuring lean processes are embedded in the way Atkins delivers its services.
Rami joins Atkins from Capita where he led the civil and structural engineering team and the multidisciplinary consultancy on a number of volumetric MMC residential schemes. Eugene joins Atkins from Arcadis where he led the company’s process and automation business. Eugene brings to Atkins cross-sector experience in the application of lean techniques, training in Japan before working in manufacturing for Honda and on major rail projects in the UK and abroad. On his appointment Rami said: “Thanks to government backing and incentivisation, there’s never been as much interest or investment in DfMA and MMC which – while positive – has led to a very crowded marketplace that can appear confusing and impenetrable to clients. My aim is to help our clients understand the suitability of all the MMC typologies available to them and to guide the decision making process to help them decide whether MMC is right for their project and if it is, to select the system or systems, that will provide them the best outcomes.”
Eugene said: “Lean has a crucial role to play in the transformation of the infrastructure sector, but it must be put front and centre of our thinking. Before looking to use digital tools, for example, we must remove waste by implementing lean processes which can result in time and cost savings of up to 60%.”
Mike McNicholas, Managing Director – Infrastructure at Atkins, added: “These appointments are an important step as we continue our transition to a more digitally-enabled, efficient future. By focusing on DfMA and lean, we will help our clients deliver more efficiently, increasing overall productivity for the infrastructure sector and UK PLC.”
Pictured: Eugene Smethurst (left) Rami Mansour (right)

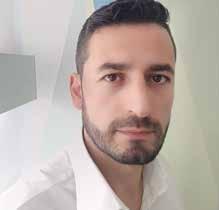
Source: www.atkinsglobal.com
Etopia Homes Makes Zero Carbon Housing Commitment
Etopia Homes has become the UK’s first developer to commit to achieving an EDGE Zero Carbon certification. Launched under the UN Secretary General’s Zero Carbon for All Initiative and backed by the UK Government, the certification recognises homes that achieve a 100% reduction in operational emissions using low carbon technologies.
The EDGE Zero Carbon certification has only been awarded to three other developments in the world, all of which were office buildings overseas. The news follows last year’s announcement that Etopia Group, Etopia Homes’ parent company, had become the first housebuilder in the world to achieve the Carbon Neutral International Standard and to join the United National Climate Neutral Now Initiative. The EDGE certification process is taking place at Etopia Homes’ development in Wilburton, Cambridgeshire. Branded Juniper Place, the scheme is delivering 30 zerocarbon homes.
By using low-carbon technologies, sustainable building methods and materials, and smart devices that can model a home’s energy performance, all the homes are expected to achieve an energy performance certificate rating (EPC) of over 100, ranking them well-above the highest category of ‘A’. In the UK, only one percent of newbuilds are ‘A’ rated, while the average rating is ‘D’.
The announcement follows the introduction of new building regulations that require new homes constructed from this year onwards to produce 31% lower carbon emissions compared to previous standards.
Joseph Daniels, CEO and Founder of Etopia Group, says: “The UK is in the midst of a dual crisis: climate change and a shortage of homes. If Government and industry are to tackle these head on, then there’s an urgent need for the built environment to be dragged into the 21st Century by bringing forward innovative technologies in both the methods of construction and the homes themselves. Our data-led, technologydriven approach will ensure that we’re able to meet the certification’s stringent criteria, optimise our methods of delivering zero-carbon homes, and actively offer a ready-to-go solution to the UK’s climate change and housing crises.”
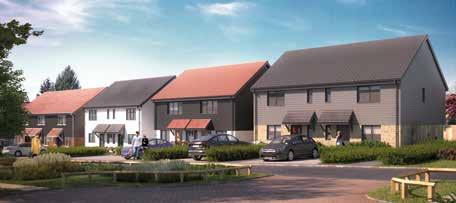
Eleni Polychroniadou, Commercial Director at Sintali, the body responsible for certifying buildings to the EDGE Zero Carbon standard, added: “Project Etopia has taken a position of leadership in the UK market as the first residential developer to commit to EDGE Zero Carbon certification. There is an urgent need for green housing in the UK, and the world as a whole. By committing to certifying homes through an internationally-recognised green building standard, Project Etopia are encapsulating the vision that every home on this planet can be green and delivering it in a quantifiable and verifiable way.”
Source: www.projectetopia.com
TTF Signs ‘Building a Safer Future’ Charter
The UK Timber Trade Federation (TTF) has joined major contractors, housing providers, local authorities and trade bodies in helping to change the culture around building safety. The TTF has taken the positive step of becoming a Registered Signatory to the Building a Safer Future (BSF) Charter.
The BSF Charter is a proactive response to Dame Judith Hackitt’s Building a Safer Future Review in the wake of the Grenfell Tower tragedy. The Charter is administered by a not-for-profit independent organisation, set up to encourage collaboration, drive change, and ultimately to transform the culture around building safety.
The community of Charter signatories is committed to putting people’s safety first through a series of five Charter Commitments. David Hopkins, CEO of the Timber Trade Federation said: “The TTF is pleased to become a Registered Signatory of the Building a Safer Future Charter. We recognise that becoming a Registered Signatory is an important first step towards achieving the culture and behavioural change required in relation to the Charter's objectives around building safety. In confirming our support as a Registered Signatory, we will now be working to ensure that we embed the principles of the Charter into our organisation’s and our sector’s activities.
“As the TTF and TRADA move further towards integration under the banner of Timber Development UK, which will bring suppliers and specifiers under the same body, we will be in an authoritative position to enact our Commitments under the Charter, particularly in collaborating to spearhead culture change and become the voice of building safety across our sector. We will also be able to play a central role in providing the key information and resources need to achieve and maintain building safety.”
Becoming a signatory to the BSF Charter underlines the TTF’s commitment to product safety, accurate product information (through its active engagement with the Code for Construction Product Information), and standards of Competence, (through its involvement the post-Grenfell Working Group 12, Construction Products Competence).
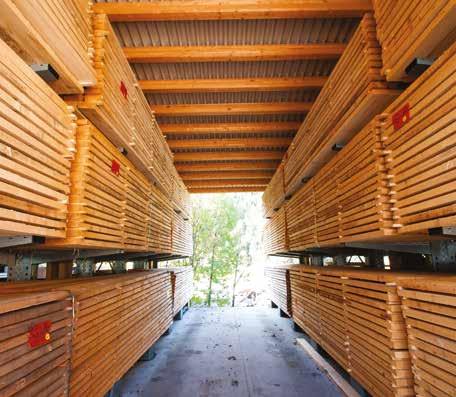
Find out more about the Building a Safer Future Charter at: www.buildingasaferfuture.org.uk
New Integrated Wates Business to Drive Offsite Manufacturing
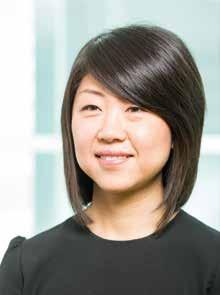
Wates Construction Group has appointed a new Strategy and Integration Director for its recently formed Group of businesses Wates Integrated Construction Services (WICS). This sees the engineering and specialist businesses including SES Engineering Services, Wates Building Services and Prism offsite manufacturing coming together under the WICS group.
Inna Lim (pictured) joins from Skanska UK, where she was Head of Strategic Markets, and will work closely with Wates’ Rob Clifford, who was announced last year as the Managing Director for the newly established WICS. She will be based at the firm’s London office and her role will be fundamental in helping to establish and bring to market a brand new integrated offer from Wates which will champion emerging technologies, innovation and offsite construction.
“What a great time to be not only joining Wates, but specifically Wates Integrated Construction Services, in such a unique period of change for our industry and economy,” said Inna. “Having spent the last 10 years in this industry, I believe we are about to enter into a period where our sector will experience the fastest technological progress to date. I am extremely pleased to see that WICS has already achieved such a solid foundation ready to build on. With enthusiastic support from a great team and ambitious drive from all who have been involved in its creation so far, I believe WICS has all the necessary attributes to become a market-leading construction solutions provider in the UK. I am really excited and privileged to play my role in helping it happen.”
Rob Clifford, Managing Director for WICS, said that Inna’s appointment marked an important milestone in the development of the WICS offer: “We believe that Inna, with her proven track record, will be a superb addition to the WICS team. Her extensive experience in leadership, business strategy and planning make her ideal for this important role which will prove crucial in how WICS evolves and supports our customers in the future. At Wates we are committed to continuously evolving our business and offering. The newly formed WICS will be a catalyst for enhancing and connecting up our capability, enabling us to become more sustainable, more profitable and more progressive as we modernise our group and make it fit for the future.”
TopHat to Launch New Apartment Product Range
TopHat has submitted a planning application to deliver the company’s first factory-built apartments at its flagship Kitchener Barracks site in Chatham, Kent. The planning application, submitted to Medway Council, includes proposals for the construction of three four-storey factory-built blocks of apartments, which will comprise 96 one and two-bedroom homes. All of the 96 apartments will be precision-engineered along production lines at TopHat’s factory in South Derbyshire.
TopHat is delivering a total of 302 homes at the 4.8-acre Kitchener Barracks site. The new homes are being delivered across three phases, with over 100 already delivered by the modular housing company. The new apartments will be the first TopHat has ever delivered and signals the company’s move to delivering alternative residential assets for investors, such as build-to-rent and co-living schemes. The application submitted by TopHat includes plans to deliver a further 183 homes at Kitchener Barracks, as part of the scheme’s third phase, including a proposal to repurpose an early 20th century barracks to deliver 68 apartments and 19 two and four-bedroom houses.
Dating from 1757 and named after Earl Kitchener in 1928, the Kitchen Barracks site is an important local landmark, most recently used as accommodation for the Royal School of Military Engineering. The news of TopHat’s latest planning application at Kitchener Barracks comes just a month after the company announced the appointment of Matthew Evans, a former Airbus vice president, as its new Chief Technology Officer – which will see him lead on the TopHat’s ambition to revolutionise housing delivery across the UK.
Krishan Pattni, Chief Design Officer and Founding Director at TopHat, says: “By diversifying our product range, we are now able to deliver a higher volume of homes to a wider range of partners. For investors investing in long-term income-producing assets like affordable housing, build-to-rent and co-living, it is crucial to have certainty that a project will be delivered on time so revenue streams can be accessed as early as possible and that the homes are cost and maintenance efficient throughout their use. Demographic trends and spurring on the growth of alternative residential asset classes we, as a company, want to make sure we have products capable of catering to this increasing investor appetite.”
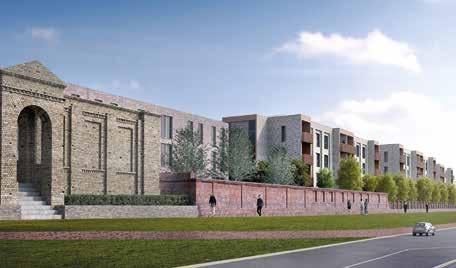
Source: www.tophat.io
INNOVATION IN LIFTING
Britlift are a designer and manufacturer of lifting equipment, specialising in the lifting of modular homes, bathroom pods, commercial modules, containerised structures and pre-cast components.
With a wealth of experience in the design and manufacture of lifting frames and lifting systems to the Offsite Construction sector, Britlift are the Offsite sector partner of choice.
BATHROOM POD LIFTING PRECAST LIFTING
Awards 2019 WINNER
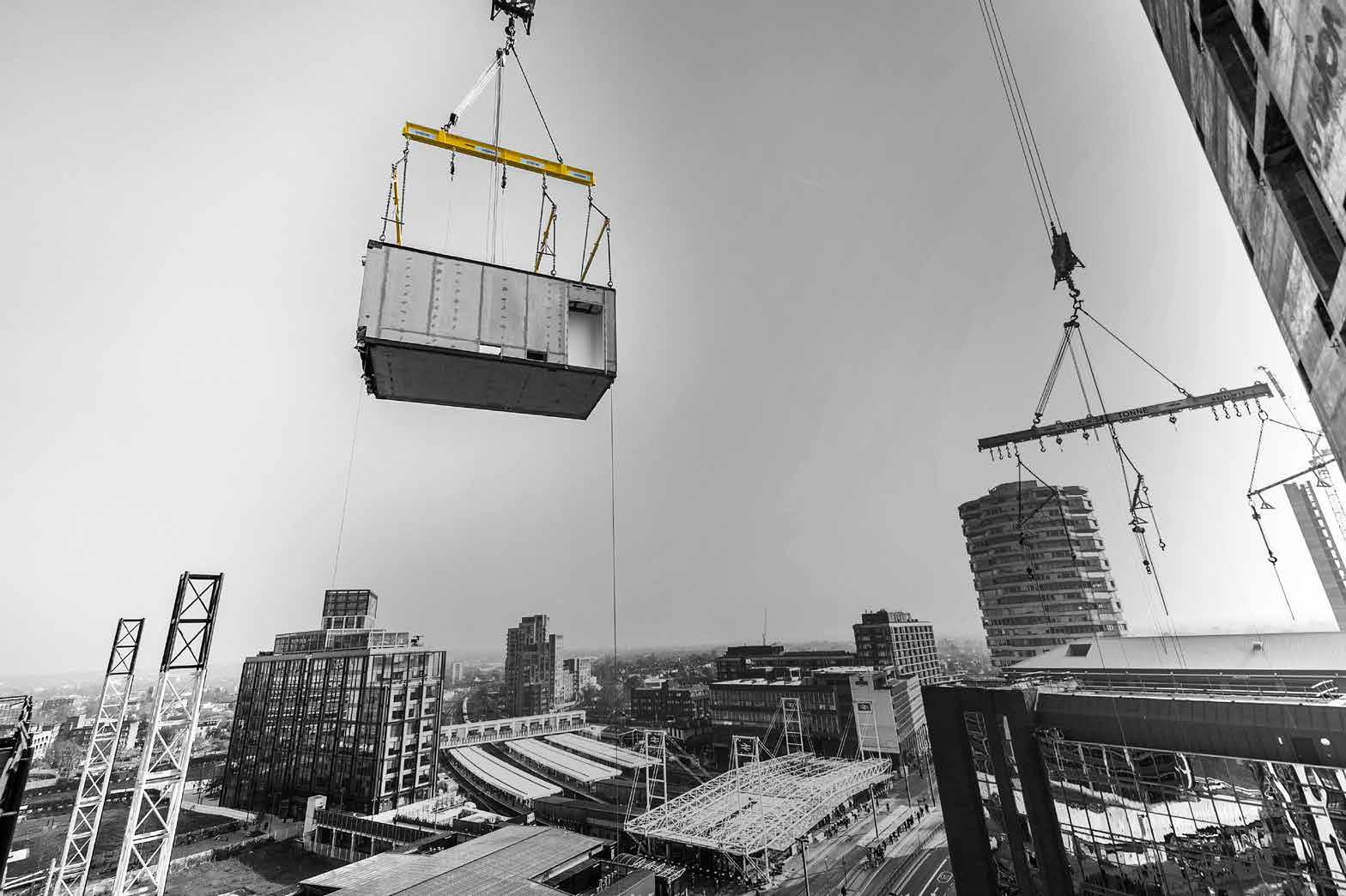
CTI Announces New Chair
Essex Receives Modular Classrooms
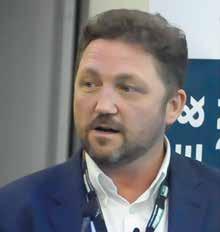
After serving four years as Chair of the Confederation of Timber Industries (CTI), Roy Wakeman OBE, has decided to leave his post with fellow sector expert, Alex Goodfellow (pictured) taking over. As a result of Roy’s stewardship, the influence of the CTI as an advocacy group for timber has increased significantly, with the All-Party Parliamentary Group (APPG) for the Timber Industries, reports including ‘How the timber industries can help solve the housing crisis’, and events bringing industry and politicians together strongly highlighting the status of timber as the material of the future. This means the CTI is poised to help the UK Government make construction more sustainable and move towards a zero-carbon economy. Roy said: “I wish the organisation and colleagues every success in their quest for an even wider awareness of the unique advantages and selling points of the material in the construction, building, home improvement and consumer markets.”
Stepping into the role is Alex Goodfellow, Group Managing Director, Strategic Development, of Stewart Milne Group. Alex has over 35-years’ experience of working within the housebuilding and offsite timber frame sector bringing vast and varied experience to the Chair role of the CTI. Alex is a board member of the Structural Timber Association (STA), having previously served as Chair, and Director of Offsite Solutions Scotland, an organisation established to grow offsite manufacture across the UK and internationally. His industry influence allows him to build innovative and collaborative relationships with many UK housebuilders and other industry influencers in the drive to ensure offsite timber manufacturing continues to provide an effective MMC solution to the housing crisis.
Alex said: “I look forward to driving forward the mission of the CTI and placing timber at the centre of a sustainable, vibrant and prosperous modern UK economy. It is more important than ever we work collaboratively to promote and protect the markets for, and interests of, timber and timber products and systems. Building in timber is a form of carbon capture and storage and is essential to decarbonising construction. To make this happen we have a full calendar of engagements, political advocacy, market research, policy reports, and other events in the year ahead. Our many thanks to Roy for his hard work over the last four years to advance the interest of timber, and helping to secure a better, stronger future for our industry.”
Source: www.cti-timber.org

Construction has started to create a number of new classroom blocks at three secondary schools across Essex – adding 750 much-needed school places for pupils in the county. The modular units will be installed at Clacton County High School, The Colne Community School and College and Sweyne Park School, as part of the Essex County Council-led scheme.
The designs for all three schools have been tailored to be as flexible and efficient as possible to maximise the benefits of a modular solution, while simultaneously meeting both the client’s educational needs and environmental requirements. Leading independent property, construction and infrastructure consultancy Pick Everard has been appointed to deliver architecture, civil, structural and MEP engineering, and principal design services.
Keith Prendergast, Director at Pick Everard, said: “We have worked closely with the client and had close collaboration with a modular supplier to ensure the brief was achieved and the design was conducive with an offsite modular solution. This will provide the high-quality education facilities the next generation of students deserve. The implementation of modular for these projects has also allowed the overall programme time to be greatly reduced, meaning that schools will be able to make the most of their new classrooms much sooner than if the traditional construction route were taken. We look forward to seeing all three schools open their new modular buildings, and to seeing students enjoying and making the most of their new environments.”
Tom Wint, Quantity Surveying Associate at Pick Everard, added: “When compared to traditional on-site methods, Essex County Council has reduced the overall project time by six months by opting for modular builds, which are a great way to save time and money on a scheme due to providing an efficient solution – allowing Sweyne Park School to open its new building at the start of the new academic year in September 2021.”
Source: www.pickeverard.co.uk
Build UK Common Standard to Speed-up Tendering Process Norbord Europe Now Part of West Fraser
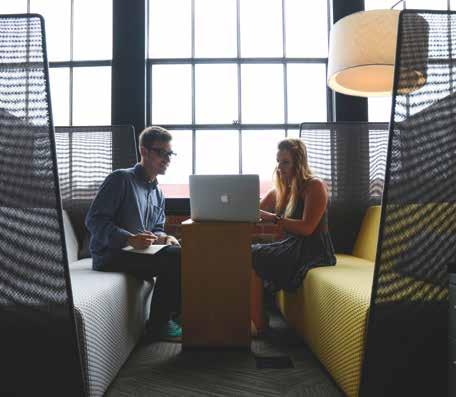
Build UK has announced that the new industry-wide pre-qualification (PQ) system will simplify a complex system for the benefit of everyone in the construction sector. The rollout of the Common Assessment Standard will significantly reduce the duplication of time, effort and resources that are costing the sector up to £1billion a year.
Major contractors and clients – including Balfour Beatty, Costain, HS2, Mace, Multiplex and Skanska – have all adopted the Common Assessment Standard meaning that members of their supply chains will need to obtain just one certification to tender for work with them. This follows the recent implementation of a new data sharing solution, which enables contractors and clients to obtain key PQ data from any one of three recognised assessment bodies: Achilles, CHAS or Constructionline.
The Common Assessment Standard is an industryagreed question set with two levels of certification – desktop and site-based – and companies can apply to any Recognised Assessment Body to get the appropriate level dependent upon their trade, size and requirements of their clients. Created by Build UK with the support of CECA, the Common Assessment Standard is endorsed by the Construction Leadership Council (CLC), which is actively seeking its adoption throughout Government construction procurement, including the Construction Playbook.
Jo Fautley, Deputy Chief Executive of Build UK, said: “We’re delighted that the new system is now fully up and running and already being used by major contractors and clients. It’s been a collaborative effort, involving companies across the whole sector, and the new system is a huge step towards more efficient working, which is more important than ever in the current challenging economic climate.”
Neil Mant, Chair of the Interim Cross Industry Body, which has overseen the development of the new system, said: “The new PQ system is a huge step forward for construction. With a single Common Assessment Standard and data sharing now in place, we have not only eliminated a huge amount of costly duplication of effort but also raised the bar in assessing the competence of the supply chain. Supply chain companies will need certification from only one of the three Recognised Assessment Bodies, and contractors can continue to deal with the body they have an existing relationship with.”
Andy Mitchell, Chair of the CLC, said: “The CLC is delighted to endorse the Common Assessment Standard which is set to transform the construction PQ process. It is a real and practical way of reducing bureaucracy and improving quality in the industry and it comes at just the right time. Companies will be able to demonstrate that they meet an agreed industry standard, and clients and contractors will be able to rely on the certification. The CLC will be encouraging the adoption of the Common Assessment Standard throughout public and private sector procurement.”
Source: www.builduk.org
Norbord Europe Ltd has joined the West Fraser organisation. As the UK’s number one engineered wood panel manufacturer and serving the housebuilding and construction industry with a vast array of board products for flooring, panelling and roofing, Norbord was the go-to name behind the company's popular brands SterlingOSBZero, CaberFloor and CaberWood MDF.
David Connacher, Marketing Manager, said: “We are delighted to be working within the West Fraser family. It gives us the opportunity to continue growing, developing and maximising our European business as we have been doing for many years. It is very much business as usual and our customer-facing teams are communicating this positive message to our key partners.” It is business as usual at the three UK plants – in Cowie and Inverness, Scotland and South Molton, Devon – with no change in personnel.
West Fraser is a diversified wood products company with more than 60 facilities in Canada, the United States and Europe. From responsibly-sourced and sustainably- managed forest resources, West Fraser produces lumber, engineered wood (OSB, LVL, MDF, plywood, particleboard), and other products including pulp, newsprint, wood chips and renewable energy.
David Connacher, added: “The two companies are much aligned and share many common values, including a commitment to safety, efficient manufacturing facilities, a focus on continuous improvement and teamwork, as well as manufacturing sustainable products that are essential for a low-carbon economy. Product development and efficient supply chains will also be at the crux of the new organisation due to the merging of experienced teams. Absolutely nothing has changed for our customers. The people are the same, the products are the same, the plants are the same – Norbord Europe now becomes the European arm of West Fraser following the acquisition.”
Simon Woods, European Sales, Marketing & Logistics Director, West Fraser added: “The joining of our two companies is a very exciting move for us in Europe. To list West Fraser’s long standing core beliefs – efficiency, modern mills, responsibility and leadership in environmental performance, the active involvement of employees in the business, a commitment to safety and a relentless pursuit of excellence in everything we do – is to echo Norbord’s. There is a huge opportunity for us to grow and develop in Europe together.”
All previous Norbord contact details are the same but the website is now: https://uk.westfraser.com
Ilke Homes Secures Significant Exeter Development Site Work Begins on Abbey Farm Primary School
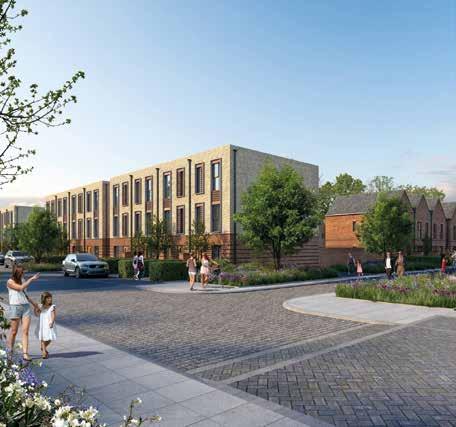
Leading modular housing company ilke Homes has secured a development site for 165 new homes on Phase 2, Exmouth Junction, Exeter from Eutopia Homes. The scheme, which will be delivered on a brownfield site that has laid vacant for many years, will comprise 165 new homes, comprising a mix of one and two-bed apartments and two, three and four-bed homes – subject to receiving final planning consent. The site, currently owned by Eutopia Homes, was most recently used as a self-storage yard and historic uses include former railway sidings, a concrete depot, and a coal distribution centre.
In March 2021, Exeter City Council (ECC) resolved to grant outline planning permission for the site for a total of 400 new homes and 65 retirement units. The application submitted by Eutopia Homes reflects a high quality designed scheme and promotes a lesser reliance on cars for other modes of travel, coupled with ECC’s condition that buildings must achieve at least a 19% reduction in carbon emissions compared to 2013 building regulations, truly sets the scheme apart from other traditional schemes within the city.
Thanks to precision-engineering techniques, the homes being delivered at Exmouth Junction will be some of the UK’s most energy-efficient. By achieving at least a ‘B’ EPC rating, the homes will be more energy-efficient than 92% of the UK’s housing stock. The energy performance of each home also translates into huge cost savings for residents, who could save hundreds of pounds on energy bills each year, as it is far cheaper to heat and power one of ilke’s homes compared to a traditionally built home due to increased levels of airtightness.
Eutopia Homes are responsible for the master plan of the whole site and the delivery of the build to rent phase. Eutopia Homes will also provide the infrastructure for ilke Homes to access and develop phase two. Tom Heathcote, Executive Director of Development at ilke Homes, comments: “This scheme marks our first major development in the South West and signifies to the market that ilke Homes is well-positioned to deliver as part of wider multi-phased developments. We’re particularly delighted to be working with Eutopia Homes on this fantastic design led scheme, and we are very much looking forward to playing our part to help transform and regenerate this redundant brownfield site for the benefit of the wider community.
Scott Hammond, CEO at Eutopia Homes, added: “One of the main reasons we selected ilke Homes was the benefits that modular construction can bring to speed of delivery across a large site. Our commitment to Modern Methods of Construction made a partnership with ilke Homes the natural fit and we look forward to working with them on this exciting project.”
Source: www.ilkehomes.co.uk
Work has begun on the new Abbey Farm Educate Together Primary School in North Swindon, designed by HLM Architects working with Reds10. The primary school is for the Department for Education (DfE) and will be operated by the Educate Together Academy Trust, who provide an ethical and values curriculum suited to a rapidly changing world at four primary schools in the South West.
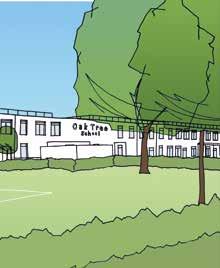
The school, which is aiming to achieve net zero operation carbon, is the first in the Department for Education’s (DfE) £3billion ‘Off-site Schools Framework’. The programme runs for four years and will deliver the next generation of off-site schools in England, supporting a wider government move towards offsite construction. The new school, which is set to open in September 2022, is located on a 4.6-acre (1.9-hectare) site. It will accommodate 460 pupils from the local community and is part of a wider residential-led mixed-use development by Redrow.
Paul Ruddick, Chairman of Reds10, said: “We are particularly proud to see this project come to fruition under the banner of the government’s ambitious new strategy for offsite schools. The building is a future-proofed, sustainable facility equipped with SMART building technology, enabling it to achieve the highest principles in energy efficiency and management. This sets a high benchmark for all future schools under this programme.”
Claire Wakelin, London Studio Director, HLM Architects, added: “We are pleased to see this project advance to the next stage of development. Our strategic design approach has been centred on the creation of a high-quality, safe and secure environment for pupils that maximises the opportunity for learning and socialising. Biodiversity was also a major inspiration, resulting in an environment that seamlessly integrates into the surrounding landscape.”
Source: www.reds10.com
New Trimble Publication Demystifies DfMA
#RSUDC21 Stuns Organisers
Recognising the industry shift towards offsite construction, Trimble (UK) has released an e-book that aims to raise awareness of Design for Manufacture and Assembly (DfMA), the benefits such an approach can offer and how DfMA and digital processes can work together to provide additional value.
The UK Government is delivering a clear push on modern construction methods, with offsite, standardisation and a ‘kit of parts’ approach all featuring in the recently published Construction Playbook and National Infrastructure Strategy. Despite this renewed emphasis, there is still work to be done. As part of the push, Trimble (UK) has released an e-book, ‘How to win at digital construction using a Design for Manufacture and Assembly (DfMA) approach’, which explores the theme of offsite in more detail. Specifically: exploring DfMA, what it means in a practical sense, the value it can bring to both a project and a business and how digital construction tools can help to deliver DfMA.
Built environment students have stunned organisers of the Riverside Sunderland University Design Challenge (#RSUDC21) with 16 entries from multidisciplinary teams showcasing low-carbon homes and a neighbourhood of the future.
Sunderland City Council, the Ministry of Building Innovation and Education (MOBIE), and the Timber Development UK University Engagement Programme launched the competition in February. Since then, more than 200 students from 35+ UK universities have been competing within teams composed of architects, engineers, quantity surveyors, landscape architects, project managers and urban designers – reflecting the multidisciplinary nature of sustainable construction and place making.
#RSUDC21 has become a powerful channel for built environment students to collaborate and share their vision for the future of urban living. Each team has designed a one three-bed family home in detail, and an indicative masterplan for 100 homes, which includes landscapes and streetscapes with green and open spaces against the backdrop of Riverside Sunderland.
The entries are now being shortlisted, and eight will be chosen to be judged by industry leaders, including Andy von Bradsky, MHCLG’s head of architecture, Mark Farmer, the Government’s Independent MMC Champion and a partner at Cast consultancy, Kelly Harrison, Associate Director of Whitby Wood and The e-book also includes case study examples of how Building Information Modelling (BIM) has been used at the Design, Manufacture and Assembly project stages to help bring structures to life, as well as discussing the future of the industry and how BIM fits into the concept of standardised design. Speaking about the e-book, Steve Insley, National Sales Manager at Trimble, said: “Despite offsite construction, in all its various forms and terms, being a common topic within the construction industry, there still remains some confusion around what it all
TDUK Board Member, and Dr Gemma Jerome, Director, Building with Nature, and Neil Guthrie, who as Development Director of Sunderland City Council represents the client perspective.
In response to the entries, George Clarke, founder of MOBIE said: “Students never fail to amaze me with their imagination, talent and passion, and this competition is providing a critical avenue to inspire young people to help define sustainable homes, and the future of where and how we live. Taking on the climate and housing crises is so incredibly important, and our built environment is key to creating a more sustainable future.”
TDUK University Engagement Programme manager, Tabitha Binding said: “What these student teams have created in little more than a few months is incredible and provides so much hope for the future of UK means and the value that it can deliver to businesses on the ground. Given this, we hope that our e-book will help to demystify the topic of DfMA, highlighting the perfect working relationship between DfMA and digital processes and proving how digital construction software can support businesses through this next journey.”
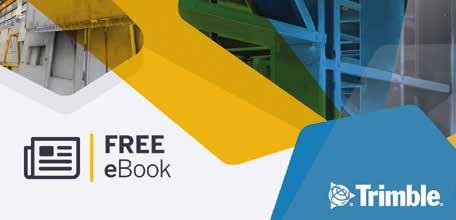
For more information and to download the E-Book visit: www.tekla.com/uk

construction. These students have taken forward the lessons from the webinars to create low-carbon, homes and neighbourhoods of the future, and built skills which they can undoubtedly take forward well into the future.
“Our built environment is responsible for around 40% of the UK’s greenhouse gas emissions. Through the skillsets these students have developed, they can help decarbonise building by employing lowcarbon, sustainable building materials like timber and using modern methods of construction. These 16 entries show the benefits of working together in interdisciplinary teams as we take on the climate challenge.”
Source: www.mobie.org.uk www.ttf.co.uk
CHALLENGING THE CONSTRUCTION STATUS QUO
HLM Architects recently appointed Dan Brown as Head of Modern Methods of Construction (MMC) Delivery, where he will provide advice and support to existing and new clients on the delivery of offsite projects. We caught up with him to know more about the role and his thoughts on the offsite sector.
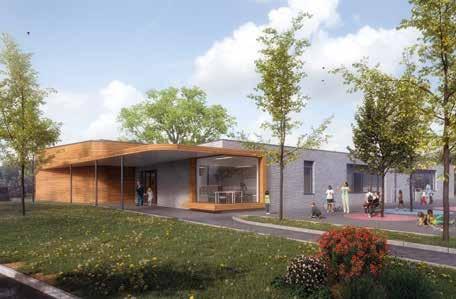
1
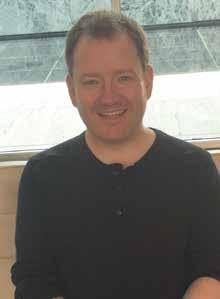
Q: As new Head of MMC Delivery at HLM Architects, can you say more about what the role will entail and what you will be wanting to achieve with it?
Dan Brown (DB): My role is to drive HLM’s ongoing integration and implementation of MMC and digital delivery across all studios and sectors and hone our strategic approach to delivery of offsite and MMC. Through collaboration with internal and external partners, I plan to develop and implement R&D initiatives that will innovate in this arena. Some of this activity is likely to be particularly relevant in addressing emerging updates to legislative frameworks such as the building regulations, and to the development of a circular economy. I fully expect the outcomes of R&D to be incorporated into project work across the practice so anticipate involvement in the production of digital tools and the delivery of training.
Q: The practice has committed itself to a ‘Think: Off-site First’ approach – what does that mean and how will you and the HLM team implement it?
DB: We are one of the first architectural practices that has committed so openly to embedding MMC at the heart of its work. Through ‘Think: Offsite First’, HLM hopes to implement across all sectors the many benefits that MMC can bring to projects in terms of quality, time, budget, environmental sustainability and health and safety. The wider team already question whether offsite construction can be implemented on projects and for me, this will include ‘hands-on’ involvement in current live projects as well as strategic input to guide what MMC categories might suit the specific needs of a programme, sector, site or scheme.
Q: The offsite construction sector has boomed over the last 2-3 years with many new entrants to the market with lots of talk of ‘disruptive design’ – from an architect’s perspective where is this disruptive design happening?
2
DB: Around the world, use of ‘modular’ and other types of MMC varies significantly, but its potential to improve the impact and efficiency of the built environment is clear. The adoption and acceptance of MMC in the UK is positively evolving and accelerating, thanks in part to investment and commitment from government and businesses across most construction sectors.
Through continued learning from manufacturing industries and by targeted research and development, especially in relation to societal impacts, digital tools and the platform approach to MMC which is being advocated for Government’s cross-departmental procurement, I believe that closer collaboration in the construction industry can help
drive success in the delivery of offsite projects.

This evolution includes disruptive design methodologies: data capture and analysis using sophisticated digital tools to test and evolve solutions which challenge the status quo are being developed. Alongside this, design programmes are being ‘turned on their head’, requiring new digital processes and a much earlier detailed involvement of specialist designers to work closely alongside the more ‘traditional’ design team to achieve a successful outcome.
Q: There is a real focus on the economic, environmental and smart technology aspects of the built environment now – where does aesthetics and visual appeal figure in improving where we live and work?
DB: Architecture has always been about more than simply the aesthetic. Visual appeal works alongside other sustainability measures to create successful places to live, work and play. Importantly, creative use of offsite manufacture should not impinge on aesthetic appeal. While the appearance of the built environment remains a key, but subjective, element in design, software solutions that objectively test iterative parametric changes to evolve a design solution that is technically successful and visually appealing are now becoming a crucial tool which architects adopt as part of their design methodology.
Q: The type of skillsets required in the modern construction industry is changing rapidly – not least in the offsite sector with the growth in digital tools (AI/VR) more important than ever. How central is technology to future offsite delivery and more efficient construction?
DB: The technological evolution is critical to MMC, not only for offsite manufacturing and assembly but also in relation to those elements of construction which remain site based. Numerous manual construction trades have for some time been subject to a fluctuating or diminishing skills-base. The offsite approach to construction aims to address these shortfalls but it is correct that different skills are required for successful delivery of MMC.
Alongside ‘production line’ skills, the use of drones, robots, AI/VR, these will automate elements of the delivery but of course, humans will be required to some degree to produce and control these tools. The education system needs to evolve to provide people with the right skills and the industry needs to work with schools, universities and other training providers to ensure a sustainable pipeline of digital and other relevant skills are maintained.
3
Q: The construction industry is under huge pressure to reduce energy consumption and change material use across the built environment to meet the UK’s net zero targets. How will HLM deliver energy efficiency in its approach to building design?
DB: As a practice, we’re keen to ensure we are taking responsibility to create places that have minimal negative impact on the world. HLM have committed to meeting the RIBA 2030 targets by 2025 and has developed strategies and design principles for each of these themes aligned to the RIBA Plan of Work that are embedded into our thinking. We have a suite of tools to ensure we define, develop and assess clients’ building projects in an evidenced-based way, such as our Thoughtful Design Toolkit.
We have established HLMGreenbuild, an association consultancy with the renowned environmental design consultant GreenBuild. This combines our expertise and offers specific services including: sustainability and energy design and reporting – BREEAM, LEED, and WELL certification
– as well as environmental modelling. We are also corporate members of the Passivhaus Trust, an independent, non-profit organisation that provides leadership in the UK for the adoption of the Passivhaus standard and methodology, and we have several qualified Passivhaus designers.

Q: Building regulations, the planning process and warranty issues are often held up as stymieing some of the benefits of offsite – e.g. its speed. What can be done to improve this situation and widen its client appeal?
DB: The planning process is not just an issue for offsite but for all construction projects. However, the recent moves to reform the planning system and take it to a new level with digital technology will hopefully address concerns so that teams can further streamline projects with reduced risk.
Building regulations are in the midst of significant review which will impact all construction. The offsite industry will need to work with these evolving legislative frameworks in future. The adoption of more standardisation, ‘type testing’ and certification, such as BOPAS, will provide clients and funders with more confidence in offsite solutions, and more innovative warranty schemes are likely to emerge. With all these areas, careful programming, standardisation and creative design will help balance the conflicting demands of control, speed and quality.
Q: The use of technology and digital tools within factory environments is now central to offsite technology plus the adoption of ‘repeatable components’ and ‘harmonised’ design – is this the future of offsite’s successful adoption?
DB: New digital tools, ‘platforms’ and integrated BIM are definitely an integral part of the future success for offsite. Changes in the perception that some stakeholders have in relation to offsite also needs to evolve. I’m particularly interested to see how the industry might change so that design teams integrate specific manufacturer’s requirements much earlier in a project – perhaps with a partnering approach where design, manufacturing and other team members come together for programmes of work to build efficiency and speed into projects? This will require design, procurement and funding philosophies to adapt so that risks are fairly managed, and creativity is maintained.
Q: In a post-pandemic world – where do you see the UK offsite sector developing and thriving over the next 18 months?
DB: There is strong potential for offsite to be applied more across all sectors. HLM has long been an advocate of this and our recent work in education is an example of where MMC has lots of potential and is helping clients, such as Wokingham Borough Council, reach sustainability and net-zero carbon targets. The recently completed expansion at Addington School showcases this point. BIM Level 2 and data-led technology enabled the team to work closely together, creatively putting user needs and carbon reduction at the forefront. Efficient use of time and digital tools at the front end of the process enabled manufacturing to begin more quickly and gave scope for more stakeholder engagement in the early design decision making process to help establish a holistic digital and offsite strategy.
4
Although 3D volumetric modular offsite construction offers many benefits, it isn’t a solution for all cases and other MMC categories will develop across all sectors. As materials shortages continue, there is probably going to be some fluctuation in which offsite solutions appear most beneficial. However, this will be cyclical, and, on balance, there will remain strong opportunities for the industry, particularly as central government has offsite high on the construction agenda.
For more information visit:
www.hlmarchitects.com
Images:
01. Dan Brown, Head of Modern Methods of Construction Delivery, HLM Architects 02. Addington School is a new sustainable, offsite manufactured facility in Wokingham 03-04. Technology is revolutionising the way the built environment is perceived. Courtesy Manufacturing Technology Centre/FIT Homes
RAISING THE SUSTAINABILITY STAKES
Environmental discussions used to focus on lifecycle analysis including recycling at the end of a building’s practical life and embodied carbon calculations. But as Steve Thompson, Managing Director of EOS explains, this is only part of the sustainability equation.
Light steel frame construction is used extensively in the UK in a wide range of building applications. The precise nature of the advantages will depend on the application and project specifics. However, there are generally five overriding value benefits – safety, quality, speed, strength and the lightweight yet robust nature of light steel frame construction. These lead to additional advantages, such as reducing concrete foundations, early completion, fewer snags, elimination of shrinkage and minimal re-work.
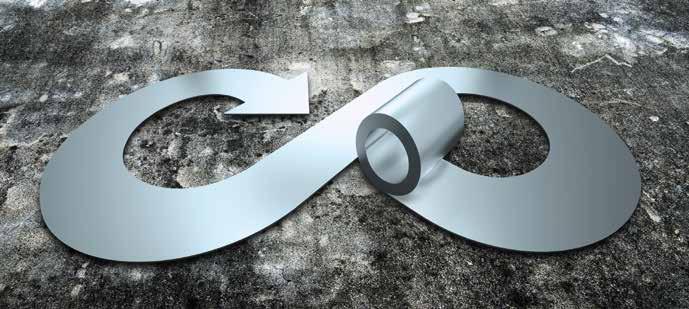
But the sustainability benefits are often overlooked. In the UK, the Steel Construction Institute (SCI) has produced evidence that we are largely self-sufficient in steel, meaning we can pretty well produce all the steel we need through recycling our latent stock to satisfy market demand.
Manufactured from the most abundant component on earth, steel can be recycled or reused endlessly without detriment to its properties. This unique characteristic gives steel a high value at all stages of its lifecycle. The recovery infrastructure for steel recycling is highly developed and extremely efficient and has been in place for decades. Current recovery rates from demolition sites in the UK are 99% for structural steelwork and 96% for all steel construction products – figures that far exceed those for any other construction material.
Light steel frame is predominantly used for complex buildings where additional structural integrity is necessary and provides the answer to complex questions where a lightweight response is required. Offering the best strength-to-weight ratio improves efficiencies – you get a lot of structure for relatively little weight which reduces embodied carbon. This is where steel cannot be beaten. Lighter structures not only reduce material consumption but also concrete in the ground. This means that foundation loads and sizes are reduced by over 70% relative to concrete and block-work construction.
Site waste is virtually eliminated by the use of prefabricated light steel components compared to the industry average wastage of 10% in construction materials. With cold rolled steel, components are manufactured to length the only waste is the swarf and offcuts produced which are minimal and can be recycled. One thing that is not considered as part of the sustainability equation is the utilisation percentage of steel – all offcuts are recycled and there is no waste at all during the manufacturing process, therefore no production waste.
High levels of thermal insulation and airtightness are achieved in light steel framing. EOS has developed
1
2

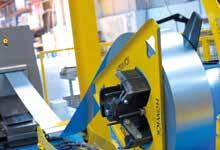
3
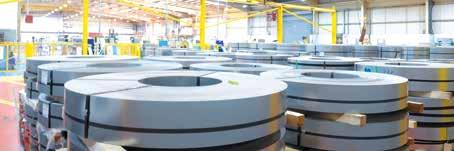
in collaboration with our Etex group partners, Siniat, a leading expert in plasterboard and drylining systems, together with fire protection specialists Promat and FSi – our Thrubuild® complete load-bearing walling and flooring systems. Our components and products are rigorously tested together to ensure compatibility and system performance, enabling us to warrant the technical performance of our Thrubuild® range of solutions and offer a 30-year warranty.
Carbon Calculations
In my opinion we cannot take a shortterm embodied carbon ‘construction’ approach – it is far greater than that. We have to think long-term to mitigate the devastation of climate change and consider the health of our planet for generations to come. But to do this we need to turn to technology to provide full lifecycle carbon analysis from manufacture and construction to inuse together with recycling and reuse at the end of a building’s life. Digital value toolkits are required to provide much needed evidence to change the debate and to offer in-depth accurate analysis of whole life carbon calculations.
This whole life approach will be a ‘game changer’ for light steel framing systems in the sustainability stakes and long-term analysis will show that steel is intrinsically more sustainable than other construction materials. Light steel frame is most definitely part of a carbon neutral solution and communicating this is crucial. Its assets make it the ultimate sustainable construction solution in terms of its longevity, material and recycling properties and importantly, enhancing the safety credentials of steel-framed buildings.
4
Images:
01-04. Steel can be recycled or reused endlessly without detriment to its properties with prefabricated light steel components providing wider sustainability benefits
EOS is a leading innovator in the design and manufacture of light gauge steel systems. The EOS product and service range is underpinned by investment in state-of-the-art design and manufacturing technology, coming together to deliver award-winning sustainable steel framing systems across a wide range of construction sectors.