
17 minute read
Build Homes, Build Jobs, Build Innovation
BUILD HOMES, BUILD JOBS,
BUILD INNOVATION
Published in September to seemingly little fanfare, Cast CEO, Mark Farmer and HTA Architects partner, Mike De’Ath’s report offering up a ‘blueprint for a housing led industrial strategy’ explained how modular construction could deliver upto 75,000 homes a year across the UK. What were some of the key themes to emerge?
This report sets out a bold ambition to seize on the opportunities presented by COVID-19 recovery planning to accelerate the role modular homebuilding plays in the future as part of a much more strategic approach to nurturing and mainstreaming the manufactured housing market. The vision in the report sets out the potential to create a sector capable of delivering 75,000 new build homes every year within a decade through a series of interlinked, long term interventions by Government and its agencies co-ordinating demand stimulation alongside responsible capacity building. At its heart is the call for more tenure diversity to allow deeper market absorption combined with a new modular homebuilding
1
national integration platform capable of aggregating and co-ordinating the market at scale such that clients and manufacturers can combine and collaborate in one place in a move towards more unified design and technical standards, quicker and larger data and evidence collection and the building of confidence in underwriting markets.
“We are seeking to create a platform for significant additional housing delivery and market diversification that also places modern methods of construction (MMC) and, particularly, modular manufactured housing at the heart of making quality homes. In doing so we envisage a major industrial strategy boost that moves us towards a greener future with resulting jobs and opportunities.”
2

The three linked objectives proposed in the report are:
• More Homes – a programme to build 75,000 additional, high-quality, manufactured homes a year by 2030. • More Jobs – the potential for 50,000 high productivity and quality jobs, ranging from SME level to larger innovators, all helping to level up regional economies. • More Innovation – beautiful new homes and skilled jobs that are underpinned by fresh design and manufacturing thinking, low and zero carbon performance, cutting edge embedded technology and connectivity and much more innovative thinking in tenure products to maximise and stabilise end market demand.
A wide range of consultees were spoken to from all four corners of the offsite sector – a ‘coalition of the willing’ – that represented the leading authorities and organisations in each sector referred to in the report. And on whose achievements and commitment form the bedrock of future housing delivery. “We have deliberately brought together consultees who represent an unprecedented and broad cross sector network. Leading residential investors, developers, modular manufacturers as well as local and regional government representatives with different political leadership, all with a shared interest in increasing housing delivery through factory production.” “We calculate that there is potential capacity at the moment in the volumetric modular sector to deliver 10,000 - 15,000 technically accredited, mortgageable homes in the UK with only 7-8 businesses able to deliver over 1,000 homes per annum as of today. Of that capacity only 30-40% is currently being used so the starting point for any strategy must be to fully utilise existing untapped production capacity including bringing in the untapped technically accredited SME capacity that exists. “From discussions with consultees in the sector, each factory operating at a capacity of 2,000 homes per annum would create on average 600 jobs, or 12,000 new jobs based on the 20 factories envisaged. Based on econometric principles, this is likely to also support a further 15,000 jobs in the related supply chains, including in manufacturing equipment supply. Extrapolating this to a 2030 target of 75,000 modular homes per annum would create and sustain a total of 50,000 additional jobs. “The most important step to underpin demand side stimulation and to achieve the growth in modular manufactured homes and the jobs envisaged is to create a smooth, sustained, long-term pipeline of demand that is visible and appropriate for modular delivery. Design quality and lasting performance should be an absolute for residential development in the UK, the fact that it is modular should be secondary to making a beautiful home, designed first and foremost to create the best possible living environment and one that responds well to the local context.
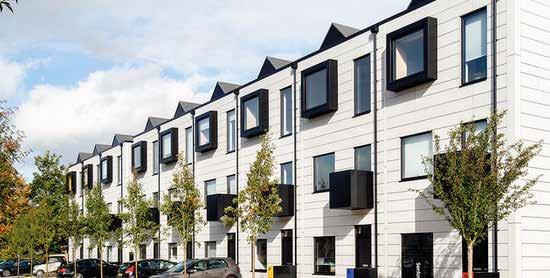
“This report is about creating a more sustainable and resilient housing market that works immediately for a post COVID-19 world and which is enabled by a modern and innovative industrial strategy. All of this can be aligned to existing policy initiatives or already proposed regulatory changes including planning and Building Regulation reforms. It can also accord with The Future Homes Standard, The Fire Safety Bill, The Building Safety Bill as well as the New Homes Ombudsman or the wider desired outcomes from the Construction Sector Deal and Transforming Construction programme. We purely suggest a housing policy that is better synchronised at scale with industrial strategy objectives and the co-ordination of support between BEIS, Her Majesty’s Treasury, MHCLG and Homes England. Also, it promotes the enthusiasm and commitment of organisations and authorities already working hard to promote innovative partnerships and utilising modular manufacture.
3
“The report is rooted in the experience of not just the authors but our consultees. They deserve recognition and encouragement as well as the wider policy support to grow and scale up. The biggest challenge is in moving quickly to the aggregation and integration platform needed to re-shape the modular market and in the tenure innovation and associated funding models that will underpin more sustainable and stable demand. Everything depends on building that resilient and demand led market that immediately absorbs the new homes that our economy needs to be urgently delivering now as part of its post pandemic stimulus. Creating an additional 75,000 new homes a year by 2030 could add 0.75% to our GDP annually. “Ultimately modular manufacturing and offsite systems must enable high-quality residential design. For the homeowner, the fact that a house is modular is secondary to the fact that it’s beautiful and practical and affordable. “Our ask of government is simple: help us stimulate and then galvanise the demand for modular homebuilding. With this help, a sustained long-term pipeline can underpin investment in manufacturing to deliver the quality homes we need, creating the jobs we want.”
For more information and to download a copy of the report ‘Build Homes, Build Jobs, Build Innovation’ visit the Cast Consultancy website: https://bit.ly/3iY0iVo
Images:
01-03. A target of 75,000 modular homes per annum could create and sustain a total of 50,000 additional jobs. Courtesy HTA Architects/Vision Modular/ Tide Construction/Urban Splash
SECURED BY
OFFSITE DESIGN
Picking up multiple awards at the Offsite Awards 2020 and the coveted Winner of Winners honour, the newbuild resettlement prison in Wellingborough is an exemplar for integration, collaborative working and a successful offsite methodology.
Wellingborough’s primary purpose is to create spaces that encourage rehabilitation and support a reduction in reoffending. It is the first in a series of schemes to be undertaken as part of the Ministry of Justice (MoJ) wider challenge to reform and modernise the prison estate to make it more efficient, safer and focused on rehabilitation. Situated on a 36-acre site in Northampton, this vast £253million project will deliver 1,680 prison places. Led by the MoJ, each partner has worked single-mindedly from day one to create a highperforming, collaborative team with shared objectives and values. The scale of the build has facilitated investment within Kier’s supply chain and the MoJ has been keen that Kier takes every opportunity to use Wellingborough as a platform to educate, train and inspire new and existing industry professionals to fully appreciate all aspects of digital and offsite construction. This provided Kier and their supply chain with a perfect storm as a platform for digital platforms and design for manufacture and assembly (DfMA) advancement. The results have been considerable and diverse – providing direct project benefits, wider economic gains, as well as programme-wide improvements through standardisation, digital integration and offsite construction. In procuring the Prison Estate Transformation Programme – which resulted in the newbuild prison at Wellingborough – MoJ knew that in order to meet the demand for 10,000 new prison places, a new approach
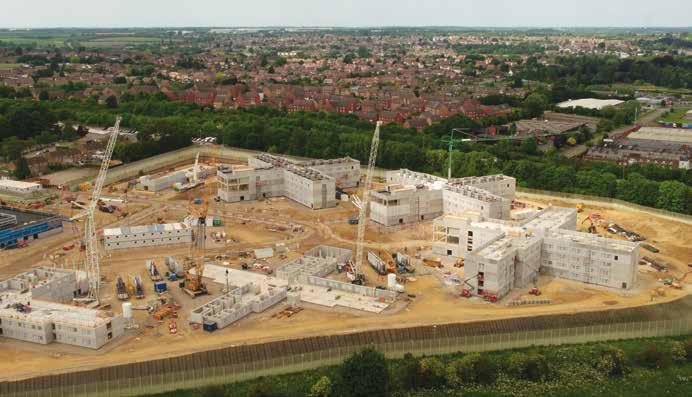
1
was required. This included setting ‘golden principles’ that apply beyond Wellingborough and establishing a platform-based design that can be utilised across its wider 10,000 prison places programme, thereby creating economies of scale and driving an offsite approach. A core feature of the programme is to optimise how the MoJ’s assets are designed, procured, delivered and operated, through a DfMA or ‘platform’ approach. Compared with traditional construction, this involved forming an integrated, cohesive team much earlier in the process, bringing in specialist input to maximise value. The result is updated technical standards, that reflect a new category of prison and an enhanced rehabilitative environment delivered
2

through a rapid repeatable build process. A platform for delivering future prisons more quickly and efficiently. The standardised design that can be rolled-out across the additional 10,000 prison places programme quickly and efficiently. Increased stakeholder engagement was required to agree on a new design that could create smaller cohorts of prisoners and be procured through supply chain partners that would share the MoJ’s drive for digital, offsite construction and a partnering ethos. Challenges included agreeing common specifications details, along with maximising the attractiveness to the precast concrete market to leverage economies of scale. Against a backdrop of political change, increased public scrutiny on prison sentences and reoffending rates, the MoJ sought to develop a new style of prison that would develop a design that is more conducive with rehabilitation, supported the wider smart construction agenda and created increased social value during construction and in operation. The MoJ also knew their bold aspiration required a new approach, optimising how assets were designed, procured, delivered and operated, through a DfMA or ‘kit-of-parts’ approach. The component assemblies designed for Wellingborough will form the blueprint for further prisons. It was therefore crucial to work together to create a repeatable design that could be replicated and progressed across the next wave of projects and that could be produced at scale by multiple manufacturers and main contractors. The result is an optimised prison design that is repeatable but also fast and safe to construct. Wellingborough will be built 22% faster than using traditional methods with on-site labour reduced by a third, preventing almost 20 accidents (based on HSE’s statistics).
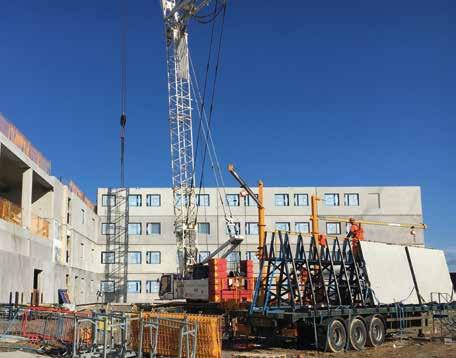
Wellingborough also saw the firstever use of a PPC2000 contract across multiple Tier 1 contractors as part of the wider prison transformation programme. MoJ has been a collaborative and open client from tender stage through to delivery. Developing a fresh approach to tendering that sought to procure supply chain partners that shared the MoJ’s vision, drive for digital and offsite and a partnering ethos. The collaboration was demonstrated by the groundbreaking ceremony, which was attended by over 70 people, including government ministers, and the MoJ’s most senior civil servant. During COVID-19, MoJ have been a supportive and encouraging client, playing their part in helping to ensure the project was able to maintain progress. Maximising the benefits of early, transparent and collaborative supply chain engagement, Kier led a
3
collaborative procurement strategy in partnership with the MoJ's consultants, WT Partnership and Mace, to collectively agree how the programme would be delivered in a safe, efficient way that met the aspirations of the contract and vision statement.
The results at Wellingborough have been considerable and diverse: from direct project benefits to wider economic gains and programme-wide improvements via standardisation, digital integration and offsite construction. The platform-based design for Wellingborough is already being replicated at another new 1,680-place prison development in Glen Parva. A clear sign of the MoJ’s confidence in their offsite approach is the leadership they have demonstrated among their peers. They regularly offer Wellingborough as a case study and opportunity for site visits to share best practice with fellow government departments progressing a ‘presumption in favour of offsite’.
For more information visit:
www.kier.co.uk
Images:
01-03. Precast concrete was at the heart of the prison design alongside expert use of digital design, prefabricated components and a mature collaborative offsite approach. Courtesy Kier Construction
WORKING TOGETHER TO CREATE
VOLUME & DEMAND
Steve Chivers, Managing Director at modular manufacturer Rollalong and Paul Read, Head of Development and Sales at Magna Housing, discuss how their partnership is encouraging more clients to see the benefits of offsite construction.
1
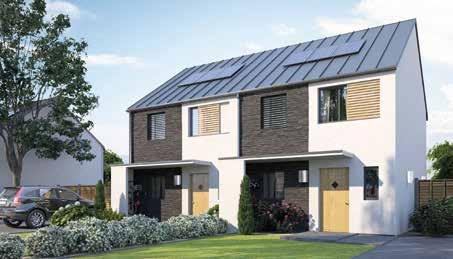
The two Dorset-based companies have been working together to develop a cluster of clients in the south of England to create a strong enough pipeline of demand for modular housing to make the offsite approach cost-effective for the manufacturer.
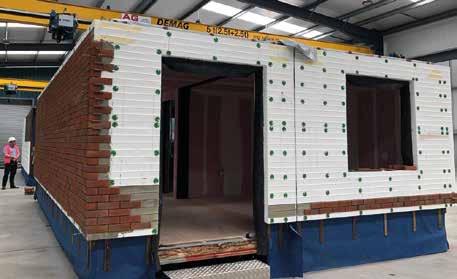
“Our main issue at present is that clients aren’t prepared to commit to the volumes that make MMC work,”
2
says Steve Chivers. “It’s a chicken and egg situation: clients want our higher quality product but at the price of a traditional build home. If factories had the same volumes, clients would soon be getting the quality and the price point they naturally demand. Clusters of clients who are prepared to embrace modular construction as the way forward would bring that into reality.” Rollalong and Magna Housing have been working together for about 18 months and to date have manufactured 45 houses which are identified for seven different schemes at various stages of planning approval. “Data we hold as a social landlord backs up the narrative of the well-publicised performance gap issue which was highlighted by the Committee on Climate Change and Future Homes Standards,” says Paul Read. “Our data demonstrates that the people who are really taking a leap of faith are those who procure homes on a site-by-site basis at the lowest initial cost: sometimes you get lucky on quality and price and sometimes you don’t.
“We spent a year looking into the business case for MMC as a social landlord and working with Complex Asset Management Solutions (CAMS) to understand in detail the whole life value of the buildings, and after we’d done all that due diligence we decided that this was the best way to proceed. We then went out to procurement, weighting heavily on quality rather than lowest price to find a manufacturer we could partner with. Rollalong in fact won on both quality and price, and 18 months into our relationship we are now on our second design iteration.” “For clients to switch their approach from building onsite to offsite manufacture turns things completely on their head – it’s a fundamental shift in thinking. A manufacturing environment has fixed costs and employs its workforce directly. The quality control, environmental, health and safety and staff welfare advantages are well known, and as a client we appreciate the use of local labour, reduced waste, time certainty, considerate construction and speed of
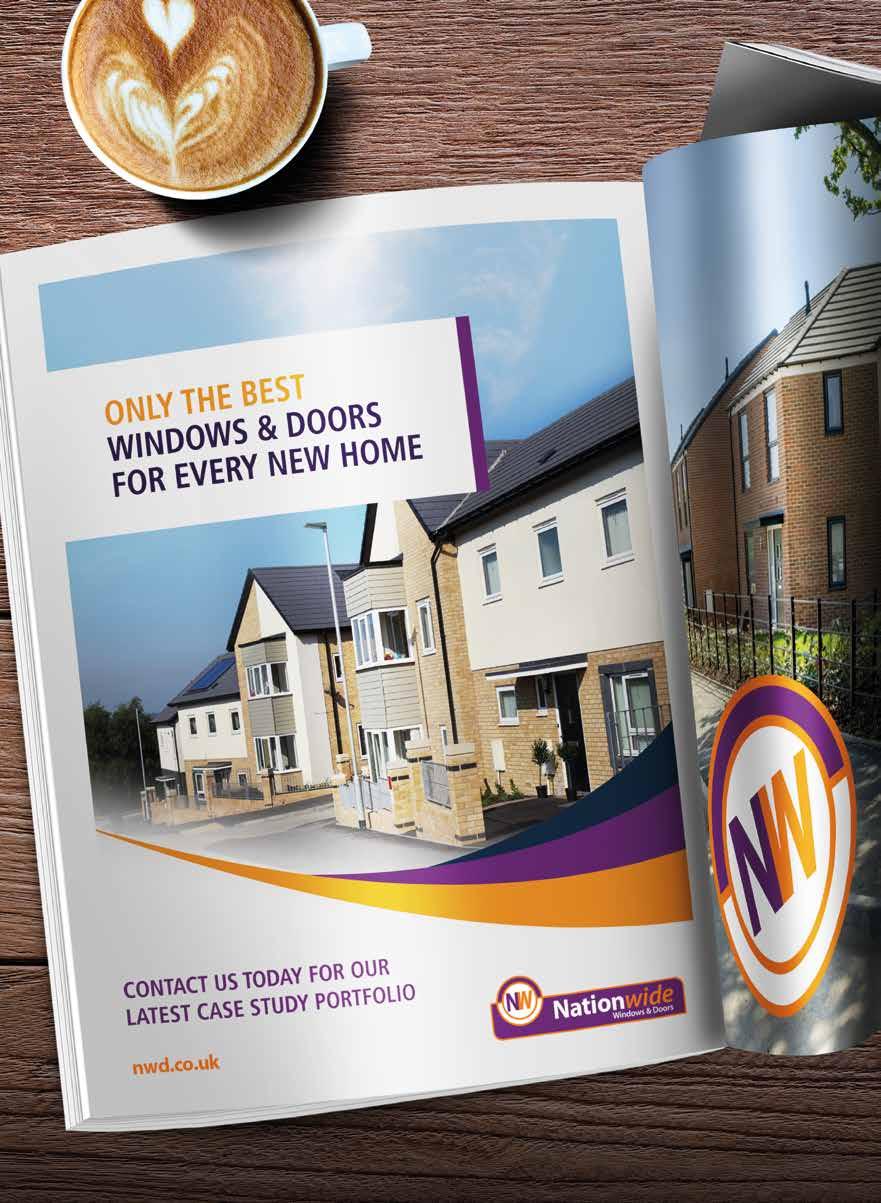
3

delivery. It’s the fixed cost that enables these other things to happen and the only way to spread and reduce that cost is to increase productivity through repetition and volume of orders. “Every client who’s yet to be convinced has a different reason for not embracing MMC. If the reason is quality, and you employ a clerk of works or enhanced employer agent services to solve that, then presumably that’s because your data is telling you that the performance gap is real. If that’s the case, what is the rationale for not looking at both MMC and traditional options to start to explore the business case for change? “What Magna Housing and Rollalong are doing is trying to get these clients to come together, share data and experience and embrace MMC based on a clear business case, and we are working with Homes England to support this switch. They commissioned a research study into MMC this summer to drive innovation in the construction industry, which is welcome news.”
One principle that is important to Steve Chivers is that the manufacturer is guided by the housing association when it comes to design. “What we haven’t done is design our own suite of homes to take to market,” he explains. “We don’t know what the optimum house layout looks like for a particular client, but Magna Housing have a portfolio of homes that have been tried and tested and consistently reviewed using 10 years of residents’ feedback from social landlords across the South West. So Magna Housing have designed the layouts for their residents and Rollalong have designed the portfolio for manufacture. “By manufacturing homes offsite and building up stock we can work flexibly with Magna Housing and other clients. Under the old system a developer identifies and secures land, then gets planning consent and then builds. But that system doesn’t work for a manufacturer. We just want to keep building up our stock. In an ideal world, if I’ve got 400 modular homes stored in our yard but no planning approval on site, I can use the houses on another site where there is approval or sell them to another client. “Similarly, Magna Housing can call off 50 new homes from our core stock and order the other homes they need later on. If there’s a delay in getting planning consent the houses can be used on a development somewhere else, so the system remains flexible and the clients get all the benefits of speed of delivery.” While Rollalong offers speed and flexibility, Magna Housing takes great pride in the design and build quality of their homes. “We know people so we’ve designed houses that we know people will love living in,” says Paul. “Rollalong have brought all their engineering knowhow and knowledge from years of manufacturing and applied it to a housing product. We’ve taken things that we know people like and Rollalong have looked at the area we’re operating in and come up with a solution that meets the requirement. “With MMC we can design homes that can flex and adapt to people’s lives. Our lives may never return to normal after the pandemic – lifestyles will change and people’s needs may alter. Perhaps more people will work from home in future and will be looking for extra space, and our products can flex

4
and adapt to that. Or a customer might be looking to buy an electric car, or fit solar panels, and these homes of the future can be adapted to that. Magna Housing is a build and stay developer, not a build and leave developer. We’re looking for a lifetime relationship with the owner or renter and we want to give them more flexibility to enable them to stay in their new home for longer. It’s an old idea that I’ve always seen the value of, but it seems that only now is the market beginning to be ready for it.” Steve Chivers adds: “There are lots of headlines at the moment about poor quality and low standards in traditional construction. Modern methods of construction resolve that issue because the manufacture is of a very high quality and it takes place in a controlled factory environment. There are also benefits to having fewer workers on-site and fewer journeys to and from site – especially in the context of a global pandemic and social distancing in the workplace. As a manufacturer we want to work collaboratively with clients who totally understand the benefits of MMC in terms of safety, quality, speed and flexibility.”
For more information visit:
www.rollalong.co.uk www.magna.org.uk
Images:
01-04. Partnerships between modular manufacturers and housing associations could be a successful future procurement model.