
47 minute read
Industry News
Construction firm Beard has entered into a strategic partnership with Green Unit Limited, in order to help boost production of modular low-carbon buildings. The move is part of Beard’s ambition to be more sustainable and to actively drive sustainable alternatives in the construction industry.
Beard had been studying opportunities to join forces with a sustainable and eco-friendly business, focused on offsite construction. The partnership enhances Green Unit’s ability to provide its customers with premium quality, modular, eco-buildings for commercial, community and residential use. It will enable Green Unit to expand demand across a variety of sectors, such as healthcare, education and leisure.
As the UK heads into a winter set to be dominated by the coronavirus pandemic, Green Unit will continue to provide its distinctive modular units to the NHS for various uses such as staff respite and patient care areas. Green Unit was co-founded in 2012 by Jonathan Finnerty, to develop distinctive eco-buildings, which are design-focused and based on Passivhaus principles to create a sense of peace and relaxation for users.
As well as being environmentally-friendly they are built with low embodied carbon and high operational performance due to their levels of insulation and airtightness. The buildings are manufactured offsite in sections, transported by road and delivered to site virtually complete. The investment from Beard will enable Green Unit to relocate its operations to a 21,000m² factory at Lockwood Farm, near Abingdon, Oxfordshire, which will significantly increase its production capacity.
While Green Unit Limited remains an independent company, Beard’s Chad Murrin will sit on the board of Green Unit as part of this partnership. Beard chairman Mark Beard said: “Methods of construction are changing and as a business we want to move further towards sustainability. Offsite and modular construction methods are being increasingly used in our industry and there are some key learnings we can take from this for the wider construction sector. These techniques can significantly improve quality, reduce construction time and lessen dependence on site works.
“We have been looking for some time for a long-term partner with this expertise and in Green Unit we feel that we have found a perfect match. We can support its ongoing growth and development while at the same time we can further increase our own ilke Homes is set to deliver up to 140 homes in Nottinghamshire after being selected by Nottinghamshire County Council to regenerate a brownfield site. The deal, which followed a competitive tender process, will see the redevelopment of the nine-acre site in Rolleston Drive in Arnold. The former depot was derelict for six years before being destroyed by fire in 2017. Innes England advised Nottinghamshire County Council acting as its agent. The scheme is ilke Homes’ third in Nottinghamshire. In July, ilke Homes signed a deal with Network Rail to build 40 homes in Beeston. In February, ilke Homes delivered nine zero-carbon homes in Newark for SME developer, Positive Homes. The homes will be manufactured at ilke Homes’ factory in Knaresborough, North Yorkshire, before being delivered to Rolleston Drive. This marks the first time that Nottinghamshire County Council has released land for a factory-built housing development. The local authority announced last year it was supporting major infrastructure and capital projects costing over £200million to help boost prosperity for its residents and the local economy. It has secured an £11million grant from Homes knowledge of sustainable methods of construction. It is important for Beard to transfer knowledge about modular construction methods into our core business and in due course have a modular offering for our customers.”
Green Unit Managing Director Jonathan Finnerty added: “The development of this new partnership is a key moment for Green Unit as a business, as it enables us to significantly expand our production capability. Beard has an excellent quality, environmental and ethical reputation and a large customer base, notably in the education sector. Beard has grown significantly in recent years and is well-placed to assist and support our young company as we grow. We look forward to working together to develop a new, unique, modular building product which can be offered to Beard’s customers.”
Source: www.greenunit.co.uk
Modular for Nottinghamshire Brownfield Site
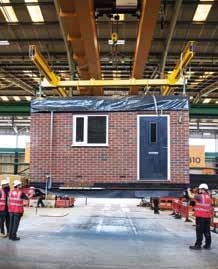
www.beardconstruction.co.uk
England to prepare eight redundant sites that it owns for housing development to meet the growing demand in the county.
Tom Heathcote, Executive Director of development at ilke Homes, said: “We’re delighted to have been selected by Nottingham County Council to unlock this important brownfield site. Our housing technology means we can quickly deliver a high-quality scheme that brings this derelict site back into productive use and deliver much needed, sustainable family homes for the local community.”
Councillor Kay Cutts, Leader of Nottingham County Council, said: “We selected Ilke Homes as the purchaser for this site after receiving many bids from different housebuilders and developers during the tender process. The re-use of this site for housing will be a huge benefit to the community and ilke Homes already appear to be making progress with their planning application. The sale will realise a notable capital receipt for Nottinghamshire County Council.”
Source: www.ilkehomes.co.uk
New Home Registrations Gain Momentum After Lockdown Slump
NG Bailey has completed a fast-paced installation of mechanical and electrical services installation at the UK’s prestigious and pioneering new battery development facility, the £130million UK Battery Industrialisation Centre (UKBIC). Acting as principal contractor, NG Bailey completed the £14.6million installation in just eight months. With commissioning and handover of the Coventrybased facility now complete, NG Bailey has been retained as principal contractor to support UKBIC during the ongoing installation phase of the facility’s specialist equipment. The publicly-funded facility, which combines manufacturing, experimentation and innovation, covers the whole production process from electrodes to cell, module and pack assembly. Its clients span a wide range of sectors, including electric vehicles, rail, aerospace, industrial and domestic equipment and static energy storage. The majority of mechanical and electrical equipment – including more than 6km of pipework and 140 heavy duty service modules – was manufactured at NG Bailey’s specialist offsite manufacture facility in Bradford. Other solutions delivered using offsite construction techniques include production of horizontal multi-service modules which enabled rapid installation and innovative space-saving solutions including a multi-service bridge structure which reduced the amount of space needed to house essential services and maximised useful production areas. The number of new homes registered to be built by the UK’s housebuilders in the first three quarters of 2020 is down by 30% on the same period last year, according to figures released by NHBC. In the year to date (January to September 2020), 83,359 homes were registered to be built compared to 119,476 in the same period last year.
The biggest impact was seen in the second quarter of 2020 which saw registration levels halve compared to the second quarter of 2019, decreasing from 42,580 to 20,102, as housebuilders felt the full force of lockdown restrictions in the spring. There were encouraging signs in the third quarter, as builders returned to site and quite quickly got used to COVID-secure working practices. New home completions recovered significantly with 33,440 in the third quarter, just 4% below the same period last year, with this reflecting the strong sales demand that has persisted for newbuild homes.
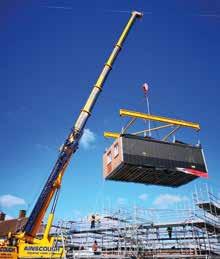
There were encouraging signs on new home registrations too, notably in September, but at 29,587 they were down by 25% compared to third quarter 2019. While the third quarter saw falls in registration numbers across several of the UK regions, the North Duncan Smith, NG Bailey’s Operations Director, Midlands explained: “By being involved in the early stages of the project we were able to develop bespoke solutions for rapid delivery. It only took six weeks from developing the initial concept to delivering the first module to site. By using our offsite manufacture and building information modelling (BIM) expertise, we were also able to deliver other tangible benefits for our clients, in particularly positioning our services to sit above the facility’s own plant and equipment. This approach also dramatically reduced the time needed to deliver the project by shifting more than 17,500 hours of work away from site – it also creates safer working environments and reduces on-site congestion.” West & Merseyside experienced a 15% increase and London was level with the same period last year with 5,111 registrations in the quarter.
Commenting on the latest statistics, NHBC Chief Executive Steve Wood said: “The COVID-19 pandemic delivered a sharp shock to the housing market in the second quarter of 2020, when work on site was halted and new home registrations fell to historically low levels. It is encouraging that by early summer housebuilders established COVID-secure operating practices and had moved closer to prelockdown productivity levels by the third quarter.
Housebuilders are facing an unprecedented set of challenges and whilst sales demand has been strong in recent months, there is significant economic uncertainty going into 2021, as the full impact of the pandemic plays out and the UK exits the European Union. Despite these headwinds, the housebuilding industry is adaptable and resilient and the fundamental factors affecting supply and demand point to gradual recovery over the medium term.”
NG Bailey Completes M&E Installation At UK’s First Battery Industrialisation Centre
Source: www.nhbc.co.uk
The £130million UK Battery Industrialisation Centre (UKBIC) is a pioneering concept in the race to develop battery technology for the transition to a greener future. The unique facility based in Coventry, provides the missing link between battery technology, which has proved promising at laboratory or prototype scale, and successful mass production. Jeff Pratt, Managing Director of UKBIC, added: “We’re delighted with the progress made on the facility, and look forward to UKBIC being operational, a milestone we’re all looking forward to achieving. Once complete, our facility will be accessed by any organisation with existing or new battery technology – if that technology will bring green jobs and prosperity to the UK.”
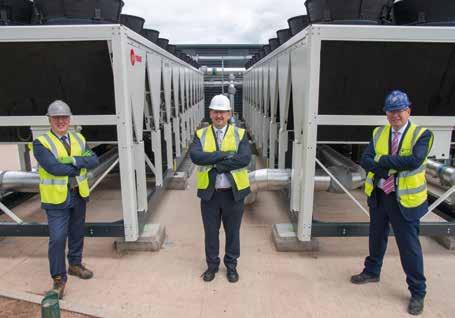
Roofspace Solutions’ i-House Helps Lovell Build Better New Modular Homes for Barking & Dagenham
Roofspace Solutions’ innovative offsite manufacturing product i-HouseTM – which guarantees a waterproof dwelling in five days – is being implemented in a Lovell Homes site in Norwich. The result is a 35% timesaving compared to traditional building methods.
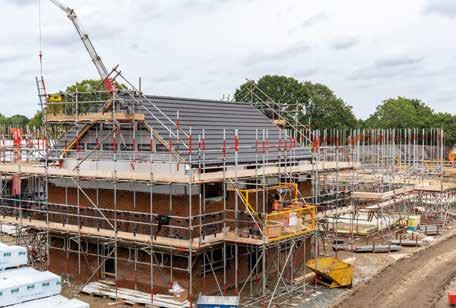
Leading partnerships housing expert, Lovell Homes, prides itself on transforming communities across the UK. As part of its commitment to innovative residential construction and regeneration projects, it chose to embrace i-HouseTM technology during the building of its latest development.
Crown Meadows in Norwich comprises two, three- and four-bedroom homes. Construction began in June 2020 and is planned to complete in two years – or possibly sooner as Roofspace Solutions’ i-House can create a watertight standard house shell in under a week, while combining quality, speed and safety. In addition to speed, Lovell Homes specified i-House in 15 of the 69 Crown Meadows plots as part of its aim to reduce waste and dust, while also minimising the risk of accidents.
The i-House uses a bigger and lighter variant of the aircrete block, which are lifted by crane and assembled in a similar sequence to a timber frame build. This results in a much faster construction process than a traditional build. Intended for domestic property construction of up to three storeys, i-House consists of inner leaves of external cavity walls, separating walls, floors, lintels, cavity closures, insulation and roof trusses, with the inclusion of soffit and fascia for the internal skin of the property.
Roofspace Solutions is working alongside supplier H+H to design and produce the large-scale Celcon Elements, which are manufactured from the same material as the aircrete blocks. This gives them the same advantages, such as outstanding thermal performance and reduced heat loss at thermal bridges.
Crucially, as the homes are watertight in under a week, it has increased Lovell Homes’ construction programme, allowing internal trades to begin their work sooner than with a traditional build. With the additional consideration of building during the time of COVID-19, the offsite solution enhance Lovell Homes’ stringent social distancing protocols. At the Crown Meadows site, approximately four builders will be able to build six houses in four weeks, with i-House increasing the output per person.
Paul Terry, Managing Director of Roofspace Solutions, said: “The construction industry is facing many challenges. The only way we will be able to ‘build back better’ and meet government and industry targets for housebuilding is by working together and embracing new technologies. The Crown Meadows development is coming along well, and we’re glad that Lovell Homes is already experiencing the time-saving benefits from i-House and Celcon Elements. We’re enjoying working on this project with a developer who has such high standards and look forward to seeing the site completed.”
Chris Gray, Senior Construction Site Manager at Lovell Homes, said: “I believe Crown Meadows will be a much quicker build, from start to finish. Of course, it’s difficult to compare like-for-like, but recently a plot went from being a concrete pad to us laying the roof tiles within two weeks – everything fits like a Lego set. Based on the success so far, it’s now our ambition to bring in the development a few months ahead of schedule. For the construction industry, it’s another tool to help us get the job done well and meet the demand for housing.” New factory-made homes have been delivered to Barking and Dagenham as part of a project to house local homeless people. The 20 two-bedroom modular homes will be finished off by Jerram Falkus, at a former garage site in Wivenhoe Road, Barking and are set to be completed in 30 weeks.
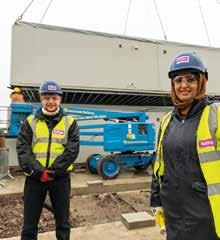
Cllr Saima Ashraf, Deputy Leader and Cabinet Member for Community Leadership and Engagement (pictured), who visited the site said: “These new homes will be for local families who are on our council waiting list and are yet to be given a permanent home, so they can still remain in the borough and close to family and friends. By using the latest modular technology we can build at pace so we can put a roof over their heads more quickly.”
Cllr Cameron Geddes, Cabinet Member for Regeneration and Social Housing added: “The housing situation is not getting any easier in these current times and now more than ever it’s so important we deliver quality housing more quickly to house local families.” Martin Andvik, Construction Manager at Be First, said: “The use of modern modular construction has allowed for these new homes to be built and delivered in record time, matching the council’s ambition to provide homes for people in need.”
Peter Bowtell, Jerram Falkus’ Construction Director also said: “It is great to see the delivery of the first units at Wivenhoe Road, our second modular housing project for Be First and Barking and Dagenham. By using offsite construction we are able to deliver these new homes faster and more efficiently to the client, on what would be a challenging site to develop using standard construction methods.” The development is due to be completed in February 2021.
Source: www.befirst.london
New Appointment at Reds10 to Drive Growth
Leading Passivhaus design and construction company Beattie Passive has successfully expanded into a significantly larger facility to ramp up production of their signature Passivhaus standard modular homes for clients across the UK, creating 80+ new jobs in the process. Established in 2010, Beattie Passive was the first company in the UK to be awarded Passivhaus certification for a complete build system. To support this expansion, 50 new jobs have so far been created at a variety of levels, from apprentices to skilled carpenters and factory management and support roles. Work began immediately on the first wave of 150+ modular pods for multiple clients throughout the UK with many of these going to clients in Wales. The company will be looking to hire another 30-50 people throughout the remainder of 2020 as they increase production. Beattie Passive are passionate about skills development and training: therefore all employees undergo a rigorous training programme to build the necessary skills to deliver Passivhaus standard housing. Beattie Passive are not only providing a positive impact on the local community through significant employment but are also sourcing materials and sub-contract suppliers for the modular homes from local supply chains wherever possible. This combined is leading to positive economic and social benefits for the local community. Reds10 has appointed Phillip Cartwright as a Non-Executive Director of Reds10 (UK) Limited and Reds10 Space as a Service Limited to support growth across both businesses. Reds10 provides clients with a full turnkey service for modular buildings.
The newly launched space-as-a-service offer will provide customers with high performance, low carbon, SMART buildings on flexible ownership terms. Using offsite construction, cradle-to-cradle design and the latest technology, it will design, finance, build and fit-out healthcare, education, workplace and accommodation spaces. It will also use building and organisational performance data to optimise customer experience, building use, operation, energy consumption and maintenance.
Phillip Cartwright (pictured) will help drive growth for Reds10. He was previously Director of Engineering Excellence Group at Laing O’Rourke and Global Head of Electrical Power and Control Systems at Rolls-Royce. Most recently, he was Executive Chairman for The Centre for Modelling and Simulation, the successful digital technology joint venture company between Airbus and Rolls-Royce. He is currently a board adviser for innovation at MACE and developed, designed and delivered significant energy and transport related safety critical systems with ABB, ALSTOM, AREVA, GE and Rolls-Royce across the globe. The factory will manufacture Beattie Passive’s Haus4 range from Haus4Studio’s, Haus4one and Haus4two through to one, two and three-bedroom volumetric apartments. The Haus4 range offers modular, relocatable homes that can meet the clients immediate housing requirements, whilst delivering both the exceptional performance of Passivhaus and the higher quality of a Beattie Passive build. Beattie Passive have seen a considerable increase in demand for their Haus4 range since the outbreak of COVID-19, due to the increasing pressure on Housing Association and councils to find housing solutions for the growing homelessness population. Managing Director, Ron Beattie said: “Following considerable time and investment in R&D we are delighted to have moved to a larger facility to start delivering our modular solution at scale. This is the first Phillip said: “The built environment, during its lifecycle, currently impacts the UK economy to the tune of approximately £808billion, around 43% of GDP. Despite these huge numbers and huge advances in the application of information and technology, the way existing infrastructure is operated and exploited has changed very little over the past decades. I am honoured and delighted to be joining a company that wants to change all that. Reds10 is an inspirational team, delivering innovative financing, excellent designs, high performing buildings and low carbon services in a truly unique approach.”
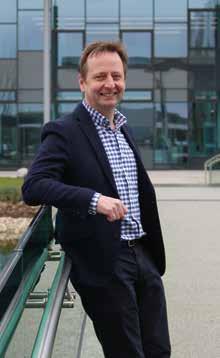
Paul Ruddick, CEO of Reds10, added: “Technology and data are key enablers in the space-as-a-service model, which is why we have appointed Phill to our board. With over 35-years of experience in engineering, which has led to innovation in both the construction and automotive industries, there is much to learn. He shares our passion to drive the industry forward and equip society to live, learn and thrive in amazing and highly efficient spaces. We welcome his no-nonsense and personal approach to the investment in and use of technology to help drive our growth.”
Beattie Passive Expands Facility
Source: www.reds10.com
of a number of large scale Beattie Passive factories across the UK and we are excited for the opportunity to not only deliver high quality Passivhaus standard housing at scale but also for the employment, training and positive economic and social benefits this will bring to the local areas.”
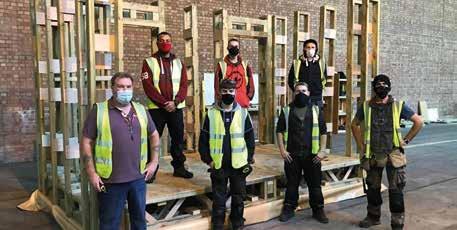
Cardiff Council Cabinet Member for Housing and Communities, Cllr Lynda Thorne, added: “Beattie Passive’s modular solutions provide a fast and effective response for our plans, including provision for a potential increase in family homelessness. The flexibility of this fully demountable system means they can be moved elsewhere in the future if required, enabling us to respond to changing housing need over time.”
Source: www.beattiepassive.com
Modern Prefabricated Extension for Iconic Home
64 Old Church Street is a Grade II* listed residence, designed by Erich Mendelsohn and Serge Chermayeff in 1936. It has been a home and focus for the family of its current owner for more than 40 years. During this time, the building has demonstrated its flexibility, adapting to accommodate the changing circumstances and needs of its occupants through a series of sensitive adjustments to the internal configuration of space that retain the essential spirit and character of the building. In 1992, Sir Norman Foster and Partners were commissioned to design a new conservatory at the south end of the building, sympathetic in nature but clearly defined as a contemporary addition.
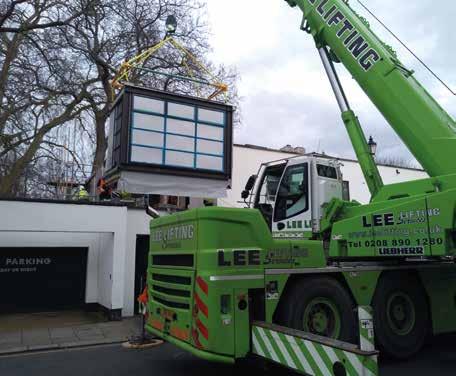
A new prefabricated extension at the north end of the building on the first floor provides self-contained living accommodation, with the conception of offsite fabrication designed to minimise disruption to the existing house and its occupants. It also enables the existing house to be reinstated to its original state in the future if desired.
The new intervention complements the existing building by following the tripartite vertical division and proportions of the glazing, whilst carefully maintaining the building’s asymmetry and clear segregation between old and new. Internally, careful research into the materials used and the replication of key details ensures that the space is a seamless continuation of the original house.
Working with structural engineers Expedition Engineering and fabricators Weber Industries, Apt designed the open plan space to have three distinct zones: kitchen, dining, and living, under a series of vaulted ceilings. This led to the design of three structural steel frames and in turn, three individual modular pods which were manufactured offsite, and then assembled on-site to form a singular extension. “A modular system might not be the first solution that comes to mind for an extension to a listed property,” said Alessandro Maccioni from Expedition Engineering. “However, the bespoke system that we developed with Weber Industries and the rest of the design team ensured the highest quality of finish and limited significant site works to a single day.”
The evolution of the design enabled the pods to be constructed offsite and arrive largely complete, with insulation, cladding, roofing, dry lining, building services and fixed joinery assembled within the workshop. The remote development of the modules provided opportunity for regular inspection and sign-off of details, both in terms of aesthetics and construction methodology, reducing the need for onsite adjustment.
The installation of the pods was meticulously planned over several months, including the commissioning of a point cloud survey which would serve to assist the extension’s integration with the listed building fabric. An independent structural frame spanning between the garage wall and the existing house provides the platform upon which the pods sit, meaning all preparatory work could be completed in advance without major disruption.
The three units were delivered to site and lifted by crane over an eight-hour period, before being bolted into position and sealed to each other and the existing house, creating a watertight perimeter. James Ewen from Apt said: “64 Old Church Street is a wonderful example of how offsite construction techniques can be utilised to create a sensitive addition to a muchadmired heritage building, retaining the building’s character whilst also ensuring that it is suitable for modern day living.”
Source: www.apt.london
Tired of explaining your OFFSITE TECHNOLOGY and business goals to agencies who don’t quite hit the mark?
www.radar-communications.co.uk
TECHNICAL KNOWHOW
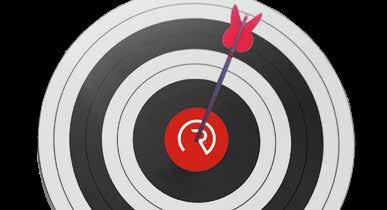
Swan/NU living Acquires Second Factory
Swan/NU living has announced the acquisition of a 15-year lease of Basildon 117, a newly built 116,841sq ft industrial unit, opposite their existing modular housing factory in Basildon, Essex. Unit 117, which was developed by Panattoni, will be used by Swan, through its NU living development subsidiary, to manufacture light gauge steel modular housing and will operate alongside Swan's existing cross laminated timber (CLT) volumetric system delivered in its current factory.
This expanded capacity will not only allow Swan to build high quality modular homes for its own secured development pipeline but also will position NU living, in time, to provide additional capacity to support Swan's partners and other stakeholders in meeting the growing expectation from Government for a proportion of modular housing to be incorporated in their own programmes. With both factories in full operation, NU living will eventually be capable of delivering over 1,000 modular homes each year.
Geoff Pearce, Swan's Deputy Chief Executive commented: “The acquisition of our second factory is a key strategic move, which will give us
Merit Launches Health Division
Merit has launched Merit Health, a new healthcare division focused on building hospitals faster, more cost-effectively and sustainably while also deploying enhanced infection control which can make wards COVID-19 safe. Merit Health will use the company’s unique offsite manufacturing technology to significantly reduce long-established building construction timelines, without compromising quality. This approach will be critical in supporting the Government’s pledge to build 40 new hospitals. The North East-based company has already completed a number of projects within the health and life sciences sector, including expansion of the Cell and Gene Therapy Catapult manufacturing centre in Stevenage. In addition, it is currently working on the ongoing construction of a state-of-the art healthcare sterilisation facility for Northumbria Healthcare NHS Foundation Trust. Merit Health will focus on accelerating projects of this kind to meet the demand for flexible, safe, and sustainable healthcare sites. A typical acute facility takes 3-4 years to build, from inception to handover, whilst Merit’s offsite approach can deliver projects in half the time. With 75-90% of the building manufactured at the 270,000sq ft Merit factory near Newcastle, a combination of Merit standard designs, offsite the additional capacity to build at height using a steel framed approach and to increase the use of pre-manufacturing and componentisation which will deliver more high quality homes, more quickly.
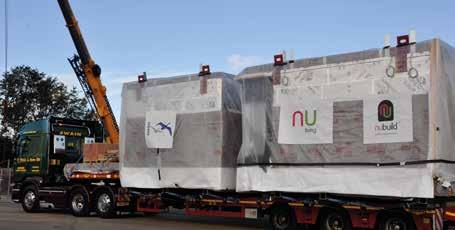
“We were early adopters of this way of working and we have worked hard since 2017 to realise the opportunities and benefits that modular construction can bring. We are confident that, in line with our corporate strategy aims, this expansion will help us deliver the majority of our future developments using precision engineered, low carbon homes. Factory 2 makes us well placed to support the Government's growing focus on MMC – including the recent announcement that development programmes funded technologies and shorter supply chains, significantly accelerates the construction process. Merit’s breadth of technological expertise in cleanroom and high containment laboratory construction has also been applied to address issues with circulation of infections in hospitals. This is even more important given the COVID-19 pandemic and the expected emergence of other communicable diseases in the future. Tony Wells, Managing Director at Merit, said: “The NHS will undergo a major upgrade of its estates, including the 40 hospitals programme and it is great the Government has recognised the benefits of standardisation and the need to utilise modern methods of construction. With the innovative methods Merit employs, this can be done quicker, at lower cost, and with higher standards of infection control and zero carbon emissions.” through the Affordable Homes Programme 2021-26 include at least 25% offsite manufacture and, in time, will enable us to support our partners to meet their modular delivery targets also.”
The second NU living factory is expected, by the time it is in full production, to create over 120 additional jobs in Essex and will see further significant investment by Swan in training and skills at a time when local investment in retraining and new local opportunities is critical to the businesses wider response to COVID-19. It is expected that Swan's second factory will commence production in Spring 2021.

Source: www.swan.org.uk
“The government is only going to deliver its ambitious building programme if companies like Merit enter the fold and show how it can be done. This will also be a critical element towards achieving the NHS’ net Zero Carbon commitment which was announced last week. Our individual hospital bay ventilation and extraction technology also means no cross contamination, which is critical as the NHS continues to deal with COVID-19 as well as future potential pandemics,”
Building on the company’s long-standing expertise, Merit Health’s offering also ideally suits the needs of facilities requiring superior infection control and containment, such as vaccine manufacture and advanced therapy units.
Source: www.merit.co.uk
Taylor Lane Completes Landmark Somerset Development
Taylor Lane Timber Frame has supplied and erected its 140mm pre-insulated timber frame kits for the first phase of Acorn Property Group’s landmark development – Cubis Bruton in Somerset – comprising three and four-bedroom houses and two-storey apartment blocks. Devised by land artist Mark Merer, Cubis Bruton is striking and architecturally innovative. Combining sustainability and environmentally aware technology with compelling design, the properties offer flexible, future-proof living. Robin Squire, Regional Managing Director of Acorn’s Bristol Region said: “Where possible, Acorn strive to use timber frame across all our developments. We are aware of the environmental impact our industry has and try to design and build our schemes with sustainability very much at the forefront of our minds in order to limit this impact. We take a fabric-first approach to our developments meaning we look to ensure the envelope of the building is as energy efficient as possible by opting for methods like timber frame construction.”
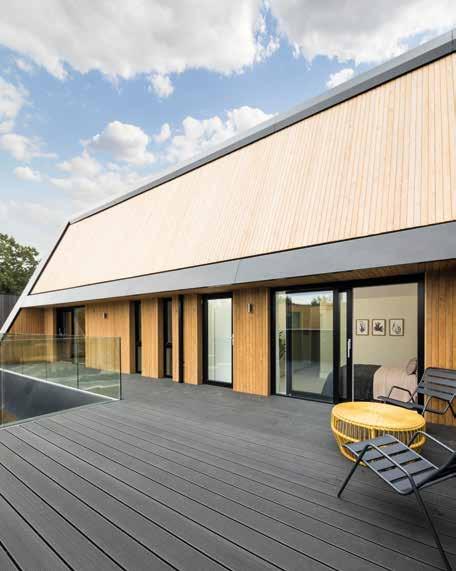
Due to the demands and design complexity of Cubis Bruton, it is highly unlikely that this scheme could be achieved using traditional masonry construction. The Hereford-based timber frame specialist also supplied and installed Posi-Joists, roof trusses, and structural and architectural steel. The complete package was designed and manufactured in-house. The Taylor Lane 140mm pre-insulated timber frame plus a continuous layer of 50mm insulation on the inside face achieves an exceptional U-value of 0.15W/m2K. The added continuous layer prevents cold bridging and improves the U-value enormously. This level of thermal performance could not be achieved with masonry construction without a negative impact on room size and build costs.
Cubis Bruton is unique, requiring complex design and product engineering. Large, open plan internal spaces with modern lines combine with a distinctive roofscape of geometric shapes, cantilevers and green roofs. The number of variations (up to three) per house type (x 11), added to the timber frame design challenge. While 80% of the properties featured flat roofs, several had sedum roofs. The weight of these affected the centre and size of the joists required. Taylor Lane utilised Posi-Joists as the engineered metal web joists can span further and bear additional load over standard timber joists whilst accommodating services. Cubis Bruton is shortlisted in the Private Housing Project of the Year at the Structural Timber Awards 2020.
Source: www.taylor-lane.co.uk
WELL CONNECTED
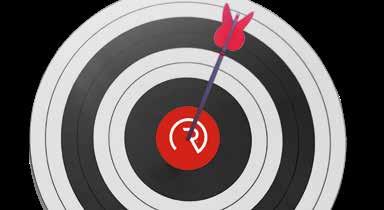
Looking for a MARKETING AGENCY with the right credentials? We’re not a jack of all trades agency we are masters of one – OFFSITE.
www.radar-communications.co.uk
The Supply Chain Sustainability School has launched Offsite for Everyone, a comprehensive new suite of learning materials to guide the construction industry in its adoption of offsite construction. Offsite for Everyone is targeted at both organisations and individuals,
“We hear so much about the need to change the way we build, but very little about what have to do differently in our day-to-day jobs,” says Ian Heptonstall, Director of the Supply Chain Sustainability School. “Our new free to access, CPD-accredited, learning materials take six key job functions: design, project management, procurement, logistics, quantity surveying and site management, and for the first time outline what we must do differently if we are to reap the many benefits of offsite.”
The learning materials in Offsite for Everyone range from full-day courses, virtual courses and e-learning modules, to videos – all of which are free for anyone to use. With funding from the Construction Industry Training Board (CITB), the materials have been developed by the School in partnership with the Manufacturing Technology Centre (MTC) and National Open Colleges Network (NOCN).
For architects and designers, it is critical to the successful implementation of offsite that they follow a Design for Manufacture and Assembly (DfMA) process and consider offsite at an early
CITB Chief Executive to Leave in 2021
Sarah Beale, Chief Executive of CITB, has given notice of her resignation which will come into effect from September 2021. She has served as CEO since January 2017, having previously held a range of senior leadership positions at the organisation over the past 16 years. stage – so, embedding knowledge of MMC within design professions is essential to increasing premanufactured value in the UK construction industry.
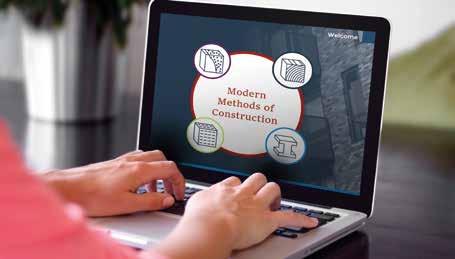
“Each sector has its own specific requirements,” says Nigel Ostime, Project Delivery Director at Hawkins\ Brown. “So it is important to understand which MMC categories are best suited to each building type. The free-to-use School learning resources provide clear advice on this and have proved an invaluable resource for our designers, as well as forming networking and knowledge-sharing opportunities with likeminded professionals, constructors and manufacturers.”
Construction recruitment business Build Space supported the School to develop the training modules, Sarah, CITB’s first female CEO, led the training body through a major, successful transformation programme, Vision 2020. It saw CITB shift from direct provision of a range of commercial services towards delivering strategic outcomes for the whole construction industry. This was achieved through improving influence at government level, introducing a new governance structure and increasing the return and impact from the Levy. Sarah played a pivotal role in protecting hundreds of apprentices who had lost their jobs due to the collapse of Carillion in January 2018. This year she led a rapid response to the COVID-19 pandemic, making a series of difficult decisions which have been welcomed by industry – protecting apprenticeships and prioritising direct funding for employers, while helping businesses’ cash flow by agreeing an unprecedented ‘Levy holiday’. During her tenure she has promoted the value and importance of diversity and inclusivity. In order to ensure delivery of CITB’s current plans, provide leadership and stability through these challenging times and make sure that the organisation is in the strongest possible position to move forward, Sarah will be staying on until September 2021. introducing key contacts to the course development team to bring relevant case studies and expert insight. The firm now requires that all candidates placed into offsite construction complete the relevant Offsite for Everyone training modules. Dominic Coyne, Director at Build Space explains: “We have been helping offsite construction contractors build their teams for over 10 years and during this time we have seen some massive advances in the market. Quality, sustainability, design and cost have all improved immeasurably and constant advances being made need strong training to support them. The School training is a gamechanger, in a market with a major skills shortage, it is a great way of bridging the knowledge gap.”
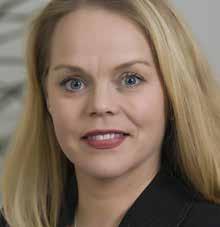
Source: www.supplychainschool.co.uk
Peter Lauener, Chair of CITB, said: “Sarah has been a superb Chief Executive for CITB, serving industry’s skills needs with dedication, and making us a stronger and more effective organisation in the process. Thanks to Sarah’s work, and that of her senior team, the Board and I can remain confident in CITB’s commitment and ability to deliver the new strategic plan and to achieve industry endorsement of our approach in the consensus process we expect to run next year. We wish Sarah well for the future – whatever she does, we know she will bring the unique mix of energy, enthusiasm and expertise to bear which makes her such an effective leader.”
On announcing her departure, Sarah Beale added: “It’s been an honour to lead CITB. A part of me will always stay in this great organisation, which is full of brilliant people making a real difference to people’s lives and careers, as well as supporting construction employers across Great Britain. I’m proud of the work we have done together, and our record of delivery. It will be tough to leave after 16 fantastic years, but right now I’m focused on delivering our Skills Stability Plan, including seeing through internal changes and setting up CITB to deliver beyond that, before taking a breather and identifying a new career challenge.”
Source: www.citb.co.uk
Palmerston House Called a ‘Game Changer’
A new modular council development in Newhaven, East Sussex, is being hailed as a ‘game changer’ for social housing and a window on the future of residential schemes. The entire development consists of 36 modules constructed within the Boutique Modern factory in Newhaven and craned into place.
The 13 one and two-bed apartments are equipped to the highest specification, in terms of standard and desirable features, sustainability credentials and fire safety standards that effectively future proof the development against all anticipated toughening of regulations post-Grenfell enquiry. Every apartment has its own 2.1kWh solar PV installation and 2.7Kw battery to store electricity generated during the day for use at peak times. Power usage monitoring displays are also installed in each home and all residents will receive advice and guidance on how to interpret and use the information to further reduce energy use.
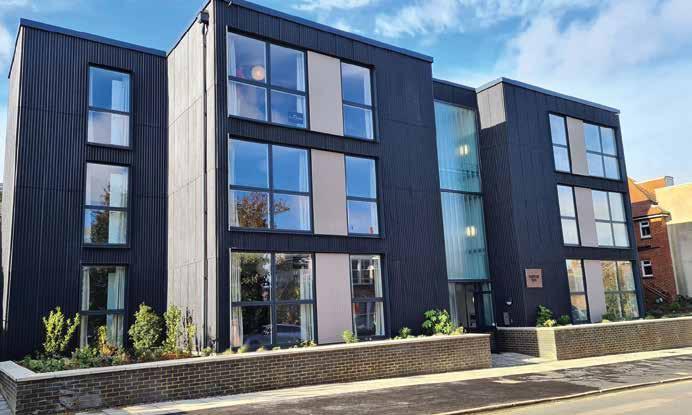
It is anticipated the mains energy use will be reduced by 70%, taking the properties ‘off-grid’ for up to three or four months of the year. The modules are super insulated, meaning they are 40% more energy efficient than traditional homes. Mechanical ventilation and heat recovery systems are installed in each apartment. They filter and exchange the air to keep the environment low in humidity, saving on maintenance issues/costs and maintaining a healthy fresh air supply within each home. Councillor William Meyer, Cabinet Member for Housing at Lewes District Council, said: “Palmerston House represents a complete and hugely exciting departure in 21st century housing construction. These wonderful new homes provide a design template that I am certain will be replicated all over the UK as decision makers discover what we have achieved in Newhaven. There is no doubt that this is a game changer, not just in terms of raising the bar for sustainability and fire safety, but also in build quality and finish. The apartments are stunning examples of what social housing professionals should be striving for.”
Source: www.boutiquemodern.co.uk
As the LEADING OFFSITE COMMUNICATION SPECIALISTS, Radar’s results driven approach delivers fast, targeted, and cost-effective engagement.
www.radar-communications.co.uk
BUSINESS OBJECTIVES
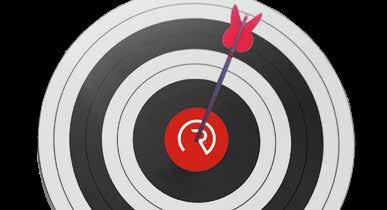
Premier’s Multi-Million COVID-19 Testing Contract Doubled
The multi-million pound contract awarded to Premier Modular to provide bespoke modular buildings for COVID-19 testing has been doubled to 50 sites across the UK. In the last three months, Premier has invested £7million in its hire fleet to meet the increasing demand for its modular buildings in the healthcare, infrastructure, education and construction sectors.
The extension of the modular building contract for COVID-19 testing follows the success of the first phase awarded to Premier by the Department of Health and Social Care for an initial 25 sites from Inverness to Portsmouth. This major national project is supporting the Government in increasing testing capacity in the current pandemic and was procured through the Crown Commercial Service.
Since the first project was delivered in Bolton, Premier has now set up standalone community testing sites in towns and cities across the country including Inverness, Leamington Spa, Dudley, Nottingham, Aylesbury, Buxton and Liverpool. The next batch of sites will be in Leeds, Redcar, Durham and Oadby in Leicestershire.
David Harris, Managing Director of Premier Modular, said “The work our teams have carried out
Latest Phase Complete on King Edward VI School Renovation
Midlands contractor G F Tomlinson has completed the latest phase of works on the expansion and renovation of King Edward VI School in Lichfield, Staffordshire. Comprising two phases of works for Staffordshire County Council under the Staffordshire Construction framework, the project involves the delivery of a new extension to an existing building, as well as the construction of a new modular building to provide essential replacement teaching spaces at the co-educational comprehensive for pupils aged 11 to 18. Phase one is expected to be complete in spring 2021 and involves the construction of a new three-storey extension on the site of a former swimming pool, which has been closed for over ten years. The extension will provide the school with enhanced teaching and auxiliary spaces, as well as an administration area on the lower ground floor, which will be the location of the school’s new student services area. Phase two started in spring this year and is now complete – works involved the demolition of the existing accommodation buildings, replacing them with a brand new standalone modern modular across the country and round the clock has been phenomenal and has been very well received in those communities. Our colleagues continue to pull out all the stops in the factory and on site to set up the testing sites in just two to three days which really is an outstanding achievement given the bespoke nature of the buildings and the complexity of the site requirements. We are delighted this work has been recognised with the doubling of our contract to 50 sites.”
“Our teams remain totally committed to playing their part in the national effort to support the Government in rapidly increasing COVID-19 testing capabilities. This is a vital initiative to help safeguard public health. This contract also demonstrates just how responsive structure to provide enhanced science laboratory teaching facilities. This is the second contract secured by G F Tomlinson through the Staffordshire Construction framework for Staffordshire County Council, led by Entrust Property Services, and follows the successful delivery of the £5.2million Poppyfields Primary School in Cannock last summer, as part of a major housing development in the area. Building on a winning collaboration following Poppyfields Primary School, G F Tomlinson once again appointed Arc Partnership to provide architectural and engineering services for works at King Edward VI School. Ideal Modular, part of G F Tomlinson’s existing supply chain, was also appointed to deliver the modular element of this project. modular construction can be when combined with strong project management and logistical operations to help the NHS respond to urgent local needs.”

Each standalone test site has a 110sq m purposedesigned testing building pre-fitted with eight patient cubicles, hygienic walls, separate staff entrance and exit, test collection and drop off zones and a family testing room. Premier’s contract also includes the supply of welfare facilities in three buildings to accommodate a PPE room, stores, test preparation, staff rest room, kitchenette and toilets, as well as essential services – water supply, effluent collection and electricity generators.
Source: www.premiermodular.co.uk
Chris Flint, Director of G F Tomlinson, said: “We are pleased to have completed the latest phase of this project for our client Staffordshire County Council. The works are providing the school with a much-needed renovation, by removing older buildings and replacing them with brand new, optimised teaching spaces and facilities. These important changes to the school will maximise the space and have a positive impact on the overall experience of both the pupils and the staff.”

Staffordshire County Council is leading this project, with project management from ENTRUST, G F Tomlinson acting as main contractors and Arc partnership acting as architect and structural engineer.
NATIONWIDE ‘RAISING THE BAR EVEN HIGHER’
Clear communication has been key to companies making a safe return from lockdown restrictions enforced by COVID-19. Acting with ‘integrity and professionalism’, the measures taken by Nationwide Windows have been described as ‘clear and concise’ and praised for raising ‘the bar even higher’.
“Nationwide were very proactive in sending us information early on from the onset of the coronavirus outbreak and throughout lockdown concerning the COVID-19 measures that they were adopting,” says Katie Waller, Programme Manager at Saxon Weald. “They managed to reassure us, as a client, that they were following government guidelines, had put specific contingency plans in place and gave us further information and links to their website. The videos that they produced were both straightforward and informative and offered comfort in their processes at this worrying and unusual time. We have always been impressed with the way that Nationwide acts with integrity and professionalism. However, their recent communications have raised the bar even higher.” Mark Lewis, Senior Commercial Manager at Sovereign, commented: “Nationwide has tackled this very difficult period with their usual excellent levels of communication and prompt responses. The decision to use videos as an aid for both staff and households was an innovative action that has been received really well. All requests by Sovereign have been dealt with in a ‘can do’ attitude by Nationwide. Nationwide are one of the leading contractors when dealing with change and new challenges with clear and concise guidance, method statements, risk assessments and preconstruction phase plans.” Dante La Bella, Customer Services Manager at Abbey Developments Ltd, added: “Nationwide’s service is very efficient indeed even through these difficult times and communication is always excellent.” “It was obvious to us from a very early stage that we needed to keep in regular contact with our customers and keep them informed of all the steps we were taking to make a safe return to operations,” says John Whalley, Nationwide Managing Director. “It’s great to receive feedback like this as it shows that we’ve tackled this difficult situation in the best way possible in order to safely service our customers’ needs.”

For more information visit:
www.nwd.co.uk
TM
So call the OFFSITE MARKETING EXPERTS and embark on a campaign in 2021 that hits the target!
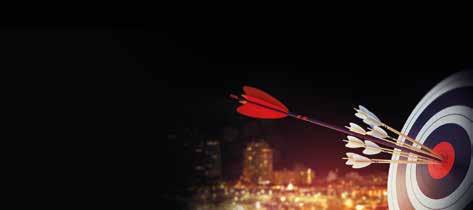
Phone 01743 290 001 or email
PLACE Units Delivered to Test Site
The first batch of modular homes designed as accommodation for homeless Londoners has been assembled on a test site in Tower Hamlets. The prototype units belong to PLACE (the Pan-London Accommodation Collaborative Enterprise), a notfor-profit company established by London boroughs with a mission to provide high-quality temporary accommodation for homeless families.
The initiative is supported by £11million of funding from the Mayor of London and represents the first collaboration between UK local authorities purchasing modular housing for this purpose.
Designed with council housing and homelessness experts according to PLACE’s specifications, the units are manufactured by ESS Modular. PLACE accommodation meets all London design requirements and building control regulations and has the quality of permanent housing but has the added advantage that the units can be relocated to a different site when required. The modular homes will be placed on vacant ‘meanwhile’ sites – land earmarked for development in the long term, which would otherwise remain underused for at least the next seven years.
Following the successful assembly of the prototypes on the Tower Hamlets test site, PLACE is working with participating boroughs to confirm sites and accommodate homeless households within the next year. Tower Hamlets and several other boroughs are looking into suitable locations and PLACE aims to supply 200 homes across the capital by February 2022.
TTF Issues New Brexit Guide

Sir Steve Bullock, Chair of PLACE, said: “This is an exciting step forward in our mission to boost the supply of high-quality temporary accommodation for homeless Londoners. Designed and manufactured to strict standards and with the needs of homeless families at the forefront of our minds, PLACE’s modular housing is attractive, comfortable, and spacious. This is accommodation that families will enjoy living in and we can’t wait to see boroughs start to use our units over the coming year.”

John Biggs, Mayor of Tower Hamlets added: “I am glad we’ve been able to host these test units in Tower Hamlets. We’ve already identified a site for the first modular homes and in the coming weeks we hope
The Timber Trade Federation (TTF) has updated and republished advice to help firms prepare for the end of the transition period when the UK leaves the EU Customs Union on 1 January 2021. The ‘TTF Brexit Guide: preparing for 1 January 2021’ aims to support the UK timber supply chain to prepare for new processes and challenges.
These are significant changes, as the EU is the primary source of timber imports into the UK, and the introduction of new requirements such as Custom Checks will mean greater administrative burden for firms when importing from the EU. While most timber products will remain duty free under the UK Global Tariff, firms should still check and familiarise themselves with the Commodity Codes relevant to their products.
UK importers of EU timber will also be considered ‘Operators’ and will be obliged to exercise due diligence to ensure negligible risk of illegally harvested timber entering their supply chain. The UK TTF recently launched a free Due Diligence Toolkit to support firms to meet their obligations.
UK CA marking commences from 1 January 2021, and while manufacturers can continue to supply CE to secure planning permission. It’s important that we think outside the box to tackle these complex challenges and this programme is doing just that.”
Paul Tierney, CEO of ESS Modular, said: “It is an honour for ESS Modular to work with PLACE on this important project which will provide highquality, local accommodation for people needing a home. Using modern methods of construction, our precision-manufactured homes deliver the quality of a permanent home but offer a huge additional benefit as they can be relocated to another site needing urgent accommodation at a later date.”
Source: www.londoncouncils.gov.uk
marked goods to the UK during 2021, where they are using an EU Notified Body they must prepare for the UK CA mark to become the sole UK requirement from January 2022. European harmonised standards and UK designated standards will be identical to begin with, however firms should also plan for a future where these may diverge over time.
David Hopkins, Chief Executive of the TTF, said: “Regardless of whether a deal is signed, the UK will see a fundamental shift in the relationship with our biggest trading partner. When the UK exits the EU single market and customs union, it is essential every business in the UK timber supply chain is prepared. Using this guidance, which is tailored to meet the needs of the timber supply chain, firms will be able to build a working knowledge of these changes, as well as be directed to where they can find detailed information.” The guidance is focused on providing information on Contract Documents, Logistics, Customs Entry, Finance, CE Marking, Plant Health, EUTR vs UKTR, Duty Rates, Commodity Codes, Trade Preferences, and linking to where firms can find more.
Source: www.ttf.co.uk/brexit-and-thetimber-industry
New Faces at TopHat
TopHat has announced the appointment of Carl Leaver as Chairman and James Matthews and Kate Davies as Non-Executive Directors. Founded in early 2016, TopHat commenced production in early 2018 at its state-of-the-art manufacturing facility in South Derbyshire and has been a pioneer in developing industry-leading technology and manufacturing processes that will shape the UK’s digital construction sector. Earlier this year, TopHat announced a five-year contract that will see TopHat work with BoKlok UK to manufacture two and three-bedroom houses.
Carl Leaver has a strong track record of value creation as both CEO and Chairman, gained across industry sectors ranging from leisure to telecommunications. Most recently, Carl was Chairman of eir (formerly Eircom Ireland) and Executive Deputy Chairman of Ladbrokes Coral Group plc. Carl is also Chairman of Lebara. Carl Leaver said: “I am very excited to have joined TopHat as Chairman to help the business achieve its mission of transforming housebuilding in the UK through the application of technology and leading-edge production capability. TopHat’s platform underpins the quality of its product while at the same time reducing production costs to among the lowest in the industry.”
Taking a Safety-First Approach to Product Development
EOS are supporting prominent rainscreen and facade manufacturer, BTS Facades and Fabrications to bring an innovative and high-performance complete walling solution to market. Taking a safety-first approach, the is a complete through-wall system incorporating an external rainscreen facade, protected using EOS’s newbuilds and refurbishment projects. Developed by BTS in partnership with EOS, Etex, Siderise, DuPont, Knauf Insulation and SFS and Nvelope - the system is believed to be the first in the UK to have successfully completed two large scale tests in accordance with the most recent BS8414-2:2020 standard. The Vantage® Secret Fix-Full System was recently tested in Belfast for fire performance by UKAS-accredited test laboratory Efectis UK and Ireland, and successfully conformed to all the stringent criteria for both internal and external spread of flame, as well as mechanical failure. Steve Thompson, Managing Director of EOS said: “Bringing our expertise in developing advanced steel framing solutions to the project team, the new James Matthews has been at the heart of the scaling of Ocado’s technology platform over the past fifteen years. As CEO of Ocado Technology he leads a team of 2,000 technologists across four countries, building Ocado Smart Platform for international clients and providing technology services to the rest of Ocado Group. James Matthews, said: “In TopHat I see a great opportunity to drive the adoption of technology and automated manufacturing in an industry that has historically lagged others in this regard”
Kate Davies has been the Chief Executive of Britain’s fourth largest housing association, Notting Hill Genesis (and previously Notting Hill Housing Trust) since 2004, growing it from a 16,000 unit organisation to one with over 64,000 homes in London and the southeast. partnership with EOS and Etex.” Compliance with BS8414-2:2020 provides not only technical credibility but importantly for designers and specifiers – certified assurance is now a prerequisite for many tender opportunities, giving the advantage. Mark Wiper, BTS’ Technical Manager said: “Working collaboratively enables us to harness the collective intellect of industry-leading experts as well as deliver proven performance. This has given us the ability to develop a wall system that is fully compliant with the latest building regulations. Through the dedication and commitment of our supply chain partners, the system has been delivered to market in She has also worked in the private sector, local government and the NHS. Kate Davies said: “Modular house-building will be central to addressing the UK’s housing crisis by providing modern, desirable and connected housing far more quickly than traditional methods. TopHat is in a strong position to lead the sector. Not only does its technology and manufacturing platform enable TopHat to produce homes of outstanding quality at low cost, but also its approach to design reshapes perceptions of what modular homes look like and feel like to live in.”
Pictured (L-R): Carl Leaver, James Matthews and Kate Davies
pioneering Vantage® Secret Fix-Full System (SF-FS) innovative Thruwall® system, that can be used in both
Vantage® Secret Fix-Full System is protected by our ground-breaking Thruwall® system – developed in
new Vantage® Secret Fix-Full System a commercial
Source: www.tophat.io
record time, allowing us to meet the latest safety test standard. This level of testing and collaboration gives clients the confidence in our system knowledge and in our ability to bring projects to market.”

A robust testing protocol was seen as an essential part of the product development strategy to not only gain a specification advantage in the open market but also to demonstrate technical prowess to a wider construction audience at a time when a building’s safety performance is under rigorous interrogation. Demonstrating commitment to regulatory compliance by bringing a fully tested and certified system to market with proven performance was deemed vital by the development team to offer confidence to the construction sector.