
15 minute read
Searching for Maximum Efficiency
Seismic’s platform approach offers a new way for construction, with Sam Stacey, Challenge Director for Transforming Construction at UKRI, saying that it offered: “tangible evidence of what the future of construction looks like.”
Delivered by a consortium of seven companies, including offsite experts, manufacturers, and consultants, the results for Seismic are impressive – projects can be delivered up to 75% faster, 70% lower in carbon and 47% better value, when compared with traditional construction. The standardisation even allows it to compete with other modular solutions, with an improvement of around 30% on speed. It makes for a compelling offer, according to the project team. “The direction from UK government is that we need platform-based construction solutions for the industry to achieve the targets outlined in Construction 2025, hit net zero and meet projected demand,” explains Richard Crosby, director at consortium lead blacc. “Seismic is a huge step towards achieving this. The consortium has demonstrated that a platform-based approach is faster, better quality and better for the environment. Crucially, this is not theoretical – we have a market ready solution that clients can use now.”
A two-part journey
Seismic is the culmination of a fouryear project, delivered in two phases. Alongside blacc, the consortium included offsite manufacturers Algeco (formerly known as the Elliott Group) and McAvoy, Tata Steel, the Manufacturing Technology Centre (MTC), the National Composite Centre (NCC) and Specific (part of Swansea University). Phase one focused on the design of a standardised, lightweight steel frame and connector block. Completed in 2020, the natural next step was to look at the design and construction of core components that would work with the frame, starting with wall, floor, ceiling and roof cassettes.
1
The ambition was an ‘all-in-one’ solution for clients that would be suitable for a range of sectors. In practice, this would allow clients to commission a project that uses the Seismic platform, working directly with the relevant manufacturer to specify the building that they wanted. Modules would be configured to achieve the desired floor space and then, depending on the performance levels desired, the client would select the appropriate floor, ceiling, roof and wall cassettes.
For example, the client could choose a thicker wall option to up the thermal mass or want to use more sustainable components within the build, such as the Vitromite floor option which is made from recycled glass. There are a range of aesthetic options too, with multiple cladding alternatives, internal fit out choices, and both flat and pitched roof solutions.
Martin Harvey, Head of Design and Technical Services at McAvoy, said: “The advantages of a platformbased approach are huge, with reduced delivery programmes, consistent quality, and more cost certainty for clients. And, whatever their requirements, the relevant components can be ordered and installed to the frame.” For the manufacturer, working to a consistent platform also reduces design time, helps speed up procurement as key materials can be held in stock, and results in a shorter build programme.
Manufacturing processes add value
Seismic has been designed on an efficient grid, optimised to reflect sizes of existing materials and logistics capabilities. Work led by the MTC focused on the factory set up to determine the most efficient layouts and equipment for delivering modules at a higher volume, alongside analysis in areas such as quality assurance, future workforce requirements and opportunities for continuous improvement.
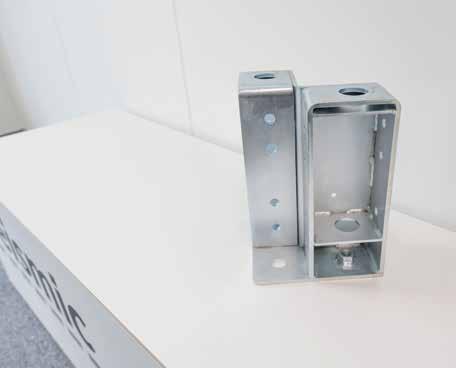
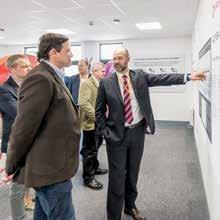
This process, focusing on the design of the modules and the factory capability, has resulted in a new standard for a smoother manufacturing process, with the Seismic team removing as much waste and unnecessary work as possible. This approach improves quality, with repeatable, standard components manufactured consistently in a controlled, safe environment.

It is something that makes Seismic unique in the market according to Algeco’s UK Technical Director, Jim Cowell. “You could argue that every building is a prototype, designed and built once. Seismic takes that away. Everything is comprehensively tested together, it is produced in factory conditions and what arrives on site is exactly what was asked for, at a higher quality standard and with a much faster and smoother handover process.”
Reducing risk for clients
A further advantage of a standardised system is that it is compatible across a range of manufacturers. This removes significant risk for clients as they are not “locked in” to one solution. For example, if the building needs to be extended in the future or adapted for a different use, the client can go to any manufacturer that works to the same
3
platform. And, if new and improved components become available, there is nothing to stop clients switching them in at some point in the future as part of their normal maintenance activity.
“What we are describing is a new way to think of buildings,” says Alex Small, BIM and Digital Platforms Manager - Construction and Infrastructure, at Tata Steel. “A platform-based approach makes it easier to disassemble and reassemble buildings, whether moving them to a new location, changing their purpose or making improvements. We can’t keep taking the traditional view that a building lasts for 60 years and just demolish it and move on – we need to consider the full lifecycle of every element.” To show people what has been achieved, the consortium has built
2
4
a demonstrator building at the BRE Innovation Park in Watford. The building combines components from the three manufacturers in one, and merges two systems. While a normal project would not usually be delivered in this way, it proves that the concept works – everything was produced in different locations before being seamlessly combined on-site.
To find out more visit: www.seismicgroup.co or email: info@seismic.co to register your interest in visiting the demonstrator.
Images:
01. Seismic Demonstrator Building 02. Phase one connector block 03-04. Over 100 people attended the launch of the demonstrator building at the BRE Innovation Park
MAKING FIRE SAFETY A PRIORITY
Since the Dame Judith Hackitt Report on building safety in 2018, the construction industry is changing its perception of how fire safety should be undertaken. The golden thread initiative now means that fire safety will be designed by architects and specifiers at project design stage, to safeguard our future city environments.
1
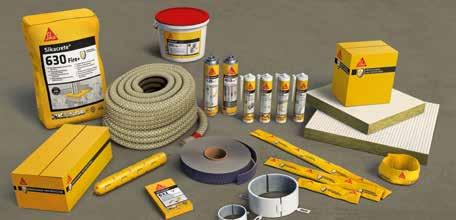
Passive fire protection solutions have become vital elements within modern offsite construction and as with all fire safety systems and products, they need to be rigorously tested to ensure that they meet the appropriate regulations. Global building solutions provider, Sika, has developed a range of passive fire protection systems that can now be incorporated into offsite solutions. With modern buildings populated by a plethora of multi-configurated utility and network services such as cables, pipes and ventilation, the opportunity for fire-spread through linear joints and penetrations in walls, floors and ceilings is abundant. Fire isn’t the only threat, however. Gaps and joints between building elements also provide a passage for heat and toxic smoke to wreak havoc with potentially fatal consequences.
Providing crucial safety time
Although unable to extinguish a blaze, passive fire protection measures are nonetheless effective in retarding the spread of fire and heat by sealing gaps through construction joints and where services run. Fire spreads quickly so containment in the form of passive fire protection provides vital extra time for occupants to evacuate buildings unharmed and for firefighters to safely carry out their duties. Passive fire protection systems save lives and should be considered at the earliest stages of a building’s design. Passive fire protection applications for building compartments can be divided into three main categories: linear joint seals, penetration seals and cavity barriers. Each solution should be thirdparty tested and certified according to relevant international standards. For the UK and Europe, these standards are EN 13501-2, EN 1366-3/4, BS 476-20, UL EU, UL 2079, Sika products solutions are fully compliant with the relevant standard to each product. For testing the fire resistance of its linear and penetration sealants, Sika creates real world scenarios in which the products are assessed as part of entire wall and flooring systems. With regards to modular construction panels, this involves testing sealants with surrounding pipes, cable work and insulation. The elements constructed together are then placed before a furnace to assess their resistance the extreme heat and fire.
Simplifying the fire-resistant sealant specification process
Sika has recently developed an online programme that’s designed to support the product selection process in relation to fire-resistant penetration sealants. Its Fire Stopping Solution Finder simplifies the search for the appropriate fire sealant through taking the prospective customer/specifier through a series of questions that are based on where and how the sealant is to be used and what type of type of fire resistance it needs to display. Unlike other programmes of this ilk, if the customer is unable to provide all of the required information the search process can still be completed. This may mean that a number of products are offered rather than one definitive solution but, in lieu of the missing data coming to light, this still provides the customer with a clearer idea of the fireresistant sealant required. If using an external contractor, this document can be logged by the architect and applicator to form part of the ‘golden thread’ of information that Dame Judith Hackitt called for in her post-Grenfell ‘Building a Safety Future’ report. This thread of data is seen as crucial to improving fire safety in buildings, as it will contain information that proves a building complies with all applicable building regulations during its construction. It will also provide evidence that it meets the requirements of the new building control route.
For more information visit:
www.sika.co.uk
Images:
01. Sika has a range of fire stopping and fire protection products
CHAMPIONS OF OFFSITE
Following the unprecedented success of the 2021 event, the Offsite Construction Awards returns later this year and will take place at Offsite Expo – the UK’s largest offsite technology event in the construction calendar.
Winner of International Offsite Project - Forta Pro
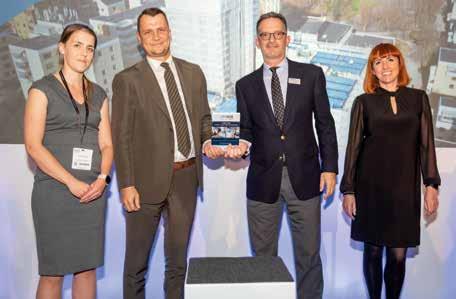
The entry deadline for the 2022 Offsite Awards has been extended to 5pm on 10 June 2022.
In order to claim the extension, you must provide the below information to the organisers no later than Wednesday 08 June: I am submitting my intent to enter the Offsite Awards in the following category/ies: Category/ies: Project/s: Company Name:
Please send this information to Rhian Morris at: rhian.morris@radar-communications.co.uk
FULL LIST OF OFFSITE CONSTRUCTION AWARDS CATEGORIES FOR 2022 INCLUDE:
Taking centre stage at Offsite Expo on the evening of 20 September 2022, the Offsite Awards will be a major gathering of the industry where over 500 guests will come together to celebrate ground-breaking achievements and the pioneers who are developing radical new offsite technologies, innovative product developments and landmark projects using factory-based methods. Entries in to the 2021 Offsite Awards were record breaking with over 200 entries and the profile and coverage gained by all the finalists and winners has helped to propel the sector to another level.
This event is the ideal opportunity for construction professionals to maximise industry exposure by demonstrating what separates them from their competitors. So, if you are proud of your exceptional team, project development or product innovation, there are just five questions to answer to grasp the opportunity to take centre stage at the 2022 Offsite Construction Awards.
Being shortlisted for the Awards will earn the recognition within the offsite community and the wider construction industry – opening doors to securing new business development opportunities.
BEST USE OF BEST USE OF TIMBER TECHNOLOGYSTEEL TECHNOLOGY
BEST USE OFBEST USE OF VOLUMETRIC HYBRID TECHNOLOGYTECHNOLOGY
BEST USE OF CONCRETE TECHNOLOGY BEST USE OF MEP & POD TECHNOLOGY
EDUCATION PROJECT OF THE YEAR
PRODUCT HEALTHCARE PROJECT INNOVATION AWARD OF THE YEAR
BEST USE OF COMMERCIAL PROJECTRETAIL/LEISURE PROJECT INFRASTRUCTURE
CONCRETE OF THE YEAR OF THE YEAR PROJECT OF THE YEAR
TECHNOLOGY BEST USE OF TIMBER TECHNOLOGY BEST USE OF STEEL TECHNOLOGY BEST USE OF HYBRID TECHNOLOGY BEST USE OF VOLUMETRIC TECHNOLOGY BEST USE OF MEP & POD TECHNOLOGY PRODUCT INNOVATION OF THE YEAR COMMERCIAL PROJECT OF THE YEAR RETAIL/LEISURE PROJECT OF THE YEAR EDUCATION PROJECT OF THE YEAR HEALTHCARE PROJECT OF THE YEAR INFRASTRUCTURE PROJECT OF THE YEAR
2022 2022
20.09.22 CBS ARENA - COVENTRY
Co-located with FFSITE EXP
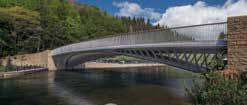
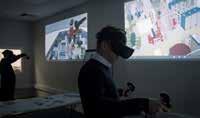
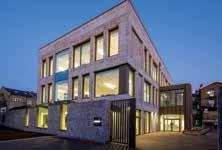
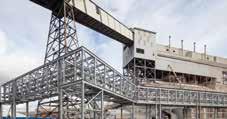
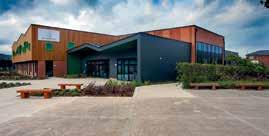
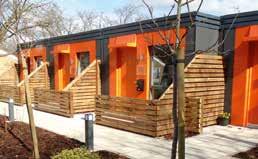
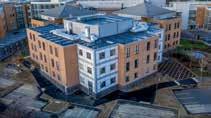
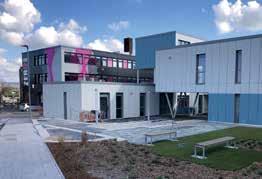


The winners of the 2022 Offsite Awards will be announced on 20 September 2022 at Offsite Expo. Many of the sponsorship packages have already been snapped up by savvy companies wanting to take advantage of the opportunity to promote their company and maximise industry exposure.
For more information on how to get involved in the Offsite Construction Awards, please contact Rhian Morris at: rhian.morris@radar-communications.co.uk
All 25 categories are free to enter, and the submission deadline is 10.06.2022 – simply visit www.offsiteawards.co.uk to start your submission today.
SOCIAL HOUSING OFFSITE PIONEER PROJECT OF THE YEAROF THE YEAR PRIVATE HOUSING PROJECT OF THE YEAR PRIVATE HOUSING INSTALLER OF THE YEAR INTERNATIONAL OFFSITE PROJECT OF THE YEAR PROJECT/CONSTRUCTION MANAGER OF THE YEAR
PROJECT
OF THE YEAR SOCIAL HOUSING PROJECT OF THE YEAR OFFSITE PIONEER OF THE YEAR INTERNATIONAL PROJECT OF THE YEAR PROJECT OR CONSTRUCTION MANAGER OF THE YEAR INSTALLER OF THE YEAR
ENGINEER ENGINEER OF THE YEAR OF THE YEAR ARCHITECT ARCHITECT OF THE YEAR OF THE YEAR CONTRACTOR CONTRACTOR OF THE YEAR OF THE YEAR BIM/DIGITAL CONSTRUCTION AWARD
CLIENT HEALTH & OF THE YEAR SAFETY AWARD
BIM/DIGITAL BUILDING PERFORMANCE PIONEER AWARD
CONSTRUCTION
AWARD
CLIENT OF HEALTH & THE YEAR SAFETY AWARD
BUILDING PERFORMANCE PIONEER
DELIVERING ON SPACE AND AESTHETICS
Gartree High School appointed modular provider Wernick to supply a standalone building to accommodate an increase in students. Gartree’s Deputy Head Ben Rackley and Assistant Head Edward Wilson, describe the project and their experience of working with Wernick.

Requiring a seamless transition with minimal intervention from teaching staff and timely student occupation, the building also had to look the part and mimic the school’s existing building. With decades of experience within the UK education sector, Wernick specialise in the design and build of modern school buildings, with each project managed by Wernick’s dedicated construction division to ensure a thorough service and the utmost levels of health and safety. “Before obtaining our new building, all Gartree’s classes took place within one large building,” says Ben Rackley. “Student numbers have increased, and it was time to increase capacity by adding at least four new classrooms. A modular classroom block made sense to us due to the timescales involved. We were aware of neighbouring schools who have chosen this route, and they helped to demonstrate the speed and aesthetics achievable with this building method. “It was vital to us that the new addition matched the look and feel of the existing building, with green, metal window surrounds and brick cladding. Inside the new building would be two science classrooms and two ‘allpurpose’ rooms. “During the procurement process, Wernick’s designs were the closest match to the school’s brief – ‘they looked like Gartree’. Wernick Buildings quoted for a two-storey, 414sq m block and it was well within our budget – in fact, the quote gave us some room to specify additional features, such as reinforced flooring, triple glazing and PIR lighting. “Wernick really paid attention to every detail on the project. For example, I was pleasantly surprised to see that Wernick had included elements of the existing building in the new block without being asked. Feedback from users of the building has been hugely positive. “I’m lucky enough to teach in the new building and a few things are really clear,” says Edward Wilson. “First of all, we’ve noticed no difference in the behaviour of the children and students who are working in the building, which is exactly what we want.

1 2
“Teachers find the new building very comfortable – air conditioning throughout ensures a consistent temperature year-round, which is something they are not used to. Rooms are also more spacious, the whole building has an open feel to it. Triple glazing creates a peaceful environment which is ideal for pupils sitting exams. The quality of the finish is really excellent, it’s a lovely place to work in and we’re finding that teaching here is a real pleasure.”
“I wanted people to see this as a permanent building,” adds Ben. “That is exactly what we have achieved. The modular building fits in perfectly and the finish gives it that ‘wow factor’ when you walk in.”
Wernick provided a bespoke, onplan building that followed the school’s wish for the new building very closely and they have been genuinely impressed with what they have supplied. “I had absolutely no time or inclination to manage a traditional building project,” says Ben. “But Wernick’s dedicated Construction Division managed the project from start to finish. A Project Manager attended site every day – this was a major selling point for me. The team on-site were brilliant and having the same point of contact throughout was invaluable.”
For more information visit:
www.wernick.co.uk
Images:
01-02. Gartree High School has exceeded client expectations and proves what a modular approach can provide for the education sector