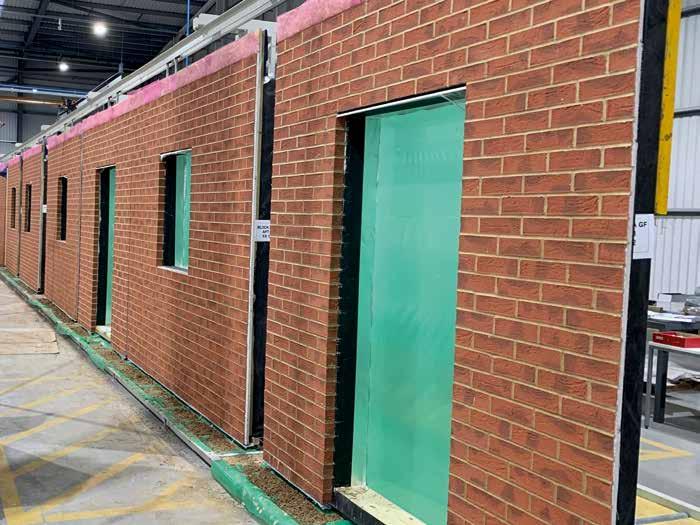
48 minute read
Industry News
First Firms Selected for £600M Social Housing System
Building Better, an alliance of 29 housing associations and councils, supported by the National Housing Federation, has appointed an initial six manufacturers to its new dynamic purchasing system (DPS) for MMC category 2 construction systems. Future Built, LoCal Homes, Project Etopia, Roe Timberframe, Sigmat and Starship Homes are the first firms selected by Procurement for Housing and Building Better to provide 2D panelised systems, assembled on-site.
The DPS is worth £600m over four years and will run in parallel with Building Better’s first MMC framework which launched in July 2021 and covers category 1 volumetric 3D systems. The alliance aims to give members access to a range of different MMC solutions so they can find the right one for their site.
Building Better took the decision to create a DPS, not a fixed framework, so panelised manufacturers can join at any point during the term of the DPS. The category 2 segment of the offsite market is evolving rapidly with new products and manufacturers emerging all the time. By setting up a DPS, social housing providers can access the latest solutions and suppliers as they come to market. Over 215,000 homes are managed by the 29 housing associations and local authorities that make up Building Better. Since the launch of its volumetric framework in 2021, alliance members have put nearly 40 schemes through it, getting costs on over 900 MMC homes. With the launch of its DPS, Building Better will help the social housing sector to produce around 5,000 MMC properties by 2026.
Manufacturers wanting to join Building Better’s DPS must first be certified by the Buildoffsite Property Assurance Scheme (BOPAS) or assessed by building warranty provider National House Building Council (NHBC) and their products must aim to meet the Future Homes Standard. Once they have passed an additional selection procedure, looking at their commercial, social and sustainability credentials, manufacturers can bid for opportunities via a tender call-off. This process has been streamlined for social housing providers too, with members receiving a tender template pack and hands-on support from Procurement for Housing.
Trina Chakravarti, Project Director of Building Better said: “The emerging nature of this part of the MMC marketplace means that social housing organisations have, to date, been wary of category 2. Some told us they were anxious about committing to a panelised manufacturer – not knowing if the company or even this form of MMC would be around in four years. Because of this, we knew a different procurement approach was needed, one that would still provide high standards and ease of access like our category 1 framework, but a solution that didn’t ‘clip the wings’ of manufacturers operating in such a fluid environment.”
John Bellamy, Category Manager for Construction & Sustainability at Procurement for Housing added: “A major benefit of setting up a DPS is the learning. As an alliance, we’ll be able to grow our understanding of what housing organisations actually require with category 2 and the technical solutions they gravitate to. Creating a framework now would have meant guessing the answers. But a DPS allows us to gather data and feedback on products and manufacturers, educating ourselves and helping us to normalise offsite and use it at scale across the sector.”
Source: www.buildingbetter.org.uk www.procurementforhousing.co.uk
MTX Announce Latest Healthcare Win
Innovative New Platform for Roof Truss Delivery
Modular healthcare specialist, MTX, has announced its latest project win, with the multi-million-pound Dame Clare Marx Building at Colchester Hospital. Dame Clare Marx picked up the first spade-full of earth and dug in on Wednesday 11 May 2022 as work began on the multi-million pound centre for planned orthopaedic care which will open in 2024.
With long patient wait times, which were apparent even before the COVID-19 pandemic, and growing demands and pressures placed on the NHS, there was a need for further operating facilities at the hospital. The threestorey modular building will house the new orthopaedic centre for the East Suffolk and North Essex area. Once complete, the brand-new facility will include six theatres, space for up to 72 beds and all the necessary ancillary spaces, including a main reception and waiting area.
David Hartley, Managing Director at MTX, said: “As all the recent news has suggested, waiting times are a real pressure point for the NHS. This has only been exacerbated with the pandemic, and more than ever, it’s shone a light on the benefits of modular solutions – particularly the quicker speed of delivery. We’re excited to be working with the team on this new project and can’t wait to see it come to life and provide the end users with a real tangible benefit.”
The Donaldson Group, is branching out with the launch of online roof truss ordering service, Donaldson Direct. The new platform provides a simple and fast way to order roof trusses, which will be delivered to site in just five working days.
Available to access online for delivery direct to customers within a 100-mile radius from a dedicated site in Welwyn Garden City, Hertfordshire (AL7 1AD). This service is ideal for self-builders, small developers, independent builders, and architects in need of highquality, carefully crafted trusses. It is also valuable for timber merchants to source a range of trusses quickly and easily for their customers.
Users input their truss requirements via an instant quote function on the website. The Donaldson Direct team then confirms requirements via telephone within 24 hours and issues drawings for the truss designs. Following approval, confirmation of dimensions and agreement of payment terms, trusses are delivered direct to site within five working days.
Commenting on the launch of Donaldson Direct, Managing Director, Luke Roberts said: “We’re excited This follows on from MTX collaborating with one of the UK’s leading providers of healthcare solutions, B. Braun Medical Ltd. B. Braun Aseptic Consulting Services (BBACS). The co-operation of the two brands is the first of its kind, combining more than 190 years of experience, bringing together the expert user knowledge in Aseptic Operations of B. Braun, and the high-specification construction expertise of MTX.
David Hartley said: “We’re immensely proud to be collaborating with B.Braun and together we’ll be able to deliver world-class Aseptic solutions for our healthcare clients. Leveraging their real-world insight into cleanroom layout and operational excellence for users, we can deliver state-of-the-art facilities that carefully
to bring this new online concept to the market. Timber roof trusses are the most widely used roofing solution – they are sustainable, simple to erect and offer a flexible solution to a wide range of roofing projects such as new builds, extensions, and residential developments. With this new service you can get an instant online quote any time, day or night. We also understand that you don’t always have the luxury of being able to access lots of storage space so you can’t order materials too far in advance. Equally, you don’t want to put your project on hold waiting for key items to arrive on site. We deliver directly to you within five working days, so there are no delays and no uncertainty.” consider equipment design, validation, servicing, robotics, and even automation.”
Paul Bradley, General Manager, BBACS added: “We’re excited to be co-operating with MTX to deliver modern cleanroom solutions for the NHS and healthcare clients. As a supplier of compounding solutions and consumables, we have a real-world perspective of the requirements of aseptic compounding operations, and by linking with MTX and providing our Aseptic transformation knowledge, we’re confident we’ll be able to deliver an exceptional service and unmatched expertise.”
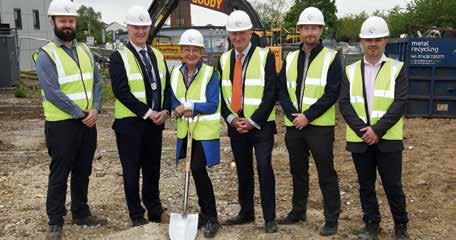
Source: www.mtx.co.uk
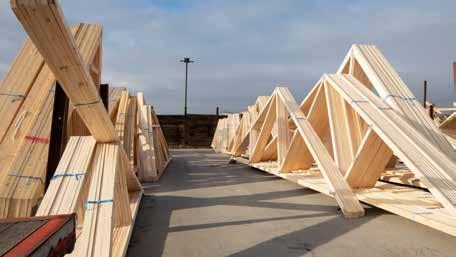
Andrew Donaldson, CEO of the Donaldson Group, added: “Donaldson Direct sums up the Donaldson ethos perfectly – an innovative approach to meeting the needs of our customers; with the promise to deliver a high quality, sustainable product. We’ve been experts in manufacturing roof trusses for volume builders for over 30 years, so it’s great to see this expertise now tailored through Donaldson Direct with a dedicated focus on lower-volume builders and self-builders. This is an exciting new addition to the Group, and we look forward to seeing it develop.”
Source: www.donaldson-direct.com
M-AR Delivers Lean Green Leeds Transport Hub
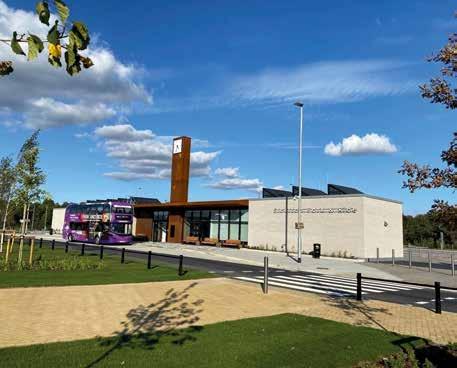
Specialist offsite contractor M-AR has created an environmentally friendly terminus building for the first fully solar-powered park and ride facility in the UK. The Stourton Park and Ride site, situated to the south of Leeds, is the third Park and Ride facility to open in the city and forms a major part of its sustainable transport strategy to reduce traffic, congestion and pollution.
A key aspect of this project, which was delivered by BAM Nuttall for Leeds City Council, was the need to minimise its overall environmental impact in terms of construction, lifespan and ongoing operations. BAM Nuttall and M-AR worked together to create an efficient offsite hybrid build solution to meet the exacting brief, while minimising the impact of the build itself. Having previously constructed the terminus buildings for both existing Park and Ride facilities in Leeds at Elland Road and Temple Green.
The completed project comprises eight modules which were manufactured offsite before being installed and finished on site. Together the modules create a fully heated, safe and secure terminus hub building with seating and ticket machines, WCs, changing place room, a staff office, retail area and a secure ticket window. The modules were designed to complement the other elements of the project, which were built on-site using a traditional steel frame construction to securely house the high-tech electrical equipment including the Tesla batteries needed to support the solar panels.
Another key part of the build was the green roof which was designed to increase biodiversity by creating a habitat for wildlife to thrive. M-AR worked with a specialist roofing contractor to determine the design details to make sure the factory-assembled modules could accommodate the green roof. More than 11,000 trees and 9,000 shrubs were also planted around the site to create an attractive environment for people using the facilities and help minimise the overall impact of the project on the environment.
Sabby Khaira, Programme Executive, Leeds City Council commented: “Sustainability was a key driving force behind this project, so as well as the ultimate goal of improving the air quality in Leeds, we wanted to make sure that the project was undertaken as sustainably as possible. It was a pleasure to deal with the M-AR team who worked collaboratively with our partners to deliver this exciting, innovative project using offsite technology to meet the sustainability criteria. In particular, we were impressed with M-AR’s delivery of the complex nature of the building with the modern passenger facilities, the solar power related infrastructure and battery housing areas.”
Ryan Geldard, Operations Director at M-AR added: “The main driving force was sustainability, so our aim was to reduce the environmental impact of the modules we provided, looking at the way they’re constructed, delivered and installed as well as how they perform over time and at the end of their lifecycle. The Stourton Park and Ride is a key part of Leeds’ sustainable transport network and we’re proud to have played our part in making Leeds a greener city.”
Source: www.m-ar.co.uk
MEDITE SMARTPLY OSB Facility Completes Upgrade
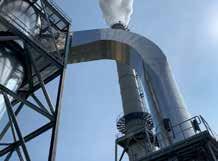
The upgrade of MEDITE SMARTPLY’s OSB factory in County Waterford has been completed. This new world class drying, energy and screening system will enhance resource efficiency and asset reliability for SMARTPLY OSB.
From 2016 MEDITE SMARTPLY has been focusing on investment and product innovation. An initial investment of €59m was made to the SMARTPLY facility which saw the creation of a new forming and finishing lines with a new state-of the art continuous press. €44m was invested for this latest significant upgrade to the drying, energy and screening facility. The completion of the upgrade is a very exciting stage of development for SMARTPLY OSB. The construction of the biomass energy plant ensures that SMARTPLY will operate on 100% renewable biomass material for process drying and heating.
The crucial upgrade means that SMARTPLY OSB will have an improved output, at a time when demand is high, and is predicted to grow further throughout 2022. The UK’s built environment is responsible for almost half of the UK’s carbon emissions, with the initial embodied carbon accounting for approximately 30% of this. This is a challenge as the industry is aiming to reach Net Zero. However, using renewable timber products is a solution.
“We are extremely delighted with the completion of this project,” commented Chris King, Managing Director – Commercial at MEDITE SMARTPLY. “Not only will this upgrade allow us to deliver more sustainable best in class timber panel products, but the increased output of SMARTPLY OSB will enable us to support existing customer positions and develop new market sectors and opportunities as part of our strategy and growth plan.”
The completed upgrade follows the successful launch of SMARTPLY SURE STEP, a T&G structural OSB/3 panel with improved slip resistance and durability. This joins a range of sustainably produced speciality and technical products, from moisture resistance to flame retardance, demonstrating MEDITE SMARTPLY’s consistent innovation and contribution to the future of sustainable building.
Source: www.mdfosb.com
Rollalong Partnership Boosts Energy Efficient Homes
People across Dorset, Wiltshire and Somerset will benefit from a new partnership to build more energy-efficient homes for rent and ownership. Magna Housing and Wiltshire Council have joined forces to address the housing crisis, appointing offsite manufacturing company Rollalong via the South West Procurement Alliance (SWPA) Offsite Construction of New Homes framework to build nearly 1000 new homes over the next three years.
At the forefront of this work in the local area, the partners are committed to accelerating the delivery of modular homes in the UK, using offsite manufactured, precision-engineered techniques to deliver much needed homes in the local area, as well as modernising and speeding up the overall process. The latest range of homes are net zero carbon ready and net zero carbon living, supporting the Government’s objective of delivering net zero carbon homes by 2050.
Paul Read, Magna’s Executive Director for Sustainability and New Supply, said: “We have been on an exciting journey leading this approach to modular homes. I am delighted that we are now seeing our hard work turn into reality with new homes now on-site and people being ready to move in. Our priority, in addition to creating homes designed for living, is to reduce the amount of carbon in delivery and occupation of homes. In addition to creating great places to live, and beautiful homes, they are also more sustainable and cheaper to run, providing huge benefits for our customers. This partnership will not only make more homes available for local people but will lead the way in how we can transform the delivery of these.”
Steve Chivers, Managing Director of Rollalong, said: “We are building the homes of the future designed for living today. It’s another great opportunity to demystify modular housing and champion the benefits that this style of housing can provide in the face of a nationwide housing crisis. This unique partnership delivers the volumes that we require using a market tested portfolio of standard designs – we are aggregating demand through client cluster relationships and rolling out through a regional delivery model.”
Mary Bennell, Director of SWPA, added: “We have worked closely for a long time with Magna Housing, and more recently with Wiltshire Council, to provide the innovative procurement solutions required to meet their housing aspirations. The demand aggregation approach used here will provide a stable pipeline of homes, via a manufacturing process, and demonstrates benefits in terms of value for money. We hope that this becomes the preferred route for all social housing clients to deliver affordable, highquality and energy-efficient homes.”
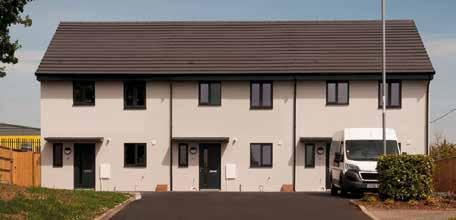
Source: www.rollalong.co.uk www.magna.org.uk
INNOVATION IN LIFTING
Britlift are a designer and manufacturer of lifting equipment, specialising in the lifting of modular homes, bathroom pods, commercial modules, containerised structures and pre-cast components.
With a wealth of experience in the design and manufacture of lifting frames and lifting systems to the Offsite Construction sector, Britlift are the Offsite sector partner of choice.
BATHROOM POD LIFTING PRECAST LIFTING
Awards 2019 WINNER
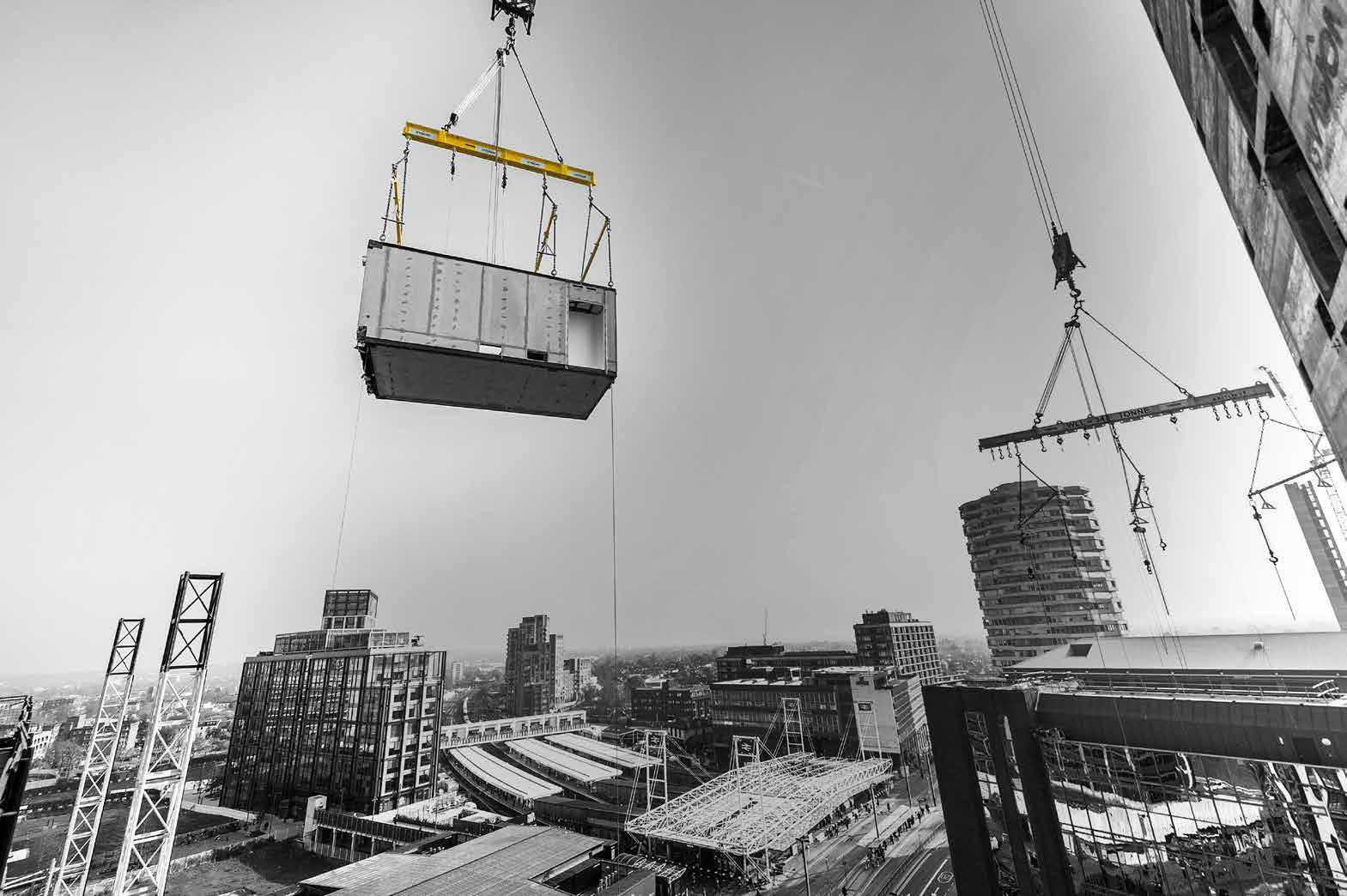
Vision Modular Systems Wins Global Award Bryden Wood Heads to USA
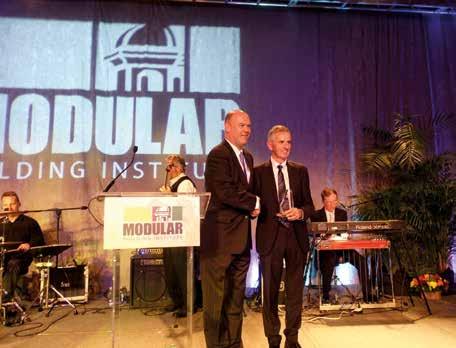
Vision Modular Systems has won the prestigious ‘Excellence in Innovation’ award at this year’s Awards of Distinction at the World of Modular Conference in San Antonio, Texas. The company, which has seen sustained year-on-year growth and is responsible for some of the world’s most ground-breaking modular buildings, was represented by its founder and chairman John Fleming, who received the award in front of over 1,000 attendees from across the globe, following an earlier presentation by the Chairman to the audience.
In its 39th year, the World of Modular Convention and Awards is organised by the Modular Building Institute (MBI), the USA’s largest trade association serving the modular construction industry. The body has been instrumental in removing legislative barriers for the sector while also working with universities and research institutions across the world to advance offsite construction.
Vision Modular Systems with its development and contracting company – Tide Construction – specialises in delivering volumetric, modular schemes, such as the George Street skyscraper for Greystar in Croydon, London that is currently the world’s tallest modular building. The approaches deployed by the company make it possible to achieve quantifiable savings on energy and waste, helping Vision Modular Systems adhere to its own stringent ESG criteria. Buildings are currently responsible for 39% of global carbon emissions, but Vision Modular Systems’ volumetric-led approach reduces a project’s embodied carbon levels by up to 45%.
John Fleming, Founder and Chairman of Vision Modular Systems, said: “This award recognises Vision Modular’s sector-leading position in the UK, where we have a strong track record of revolutionising the way in which housing is delivered. Years of significant growth, in terms of our pipeline and financial strength, is demonstrated through our long-standing partnerships with some of the world’s biggest institutional purchasers and has established modular as a mainstream method of delivery.
“It is an honour to receive such a high-profile accolade from the Modular Building Institute; an organisation that has been actively shaping the future for modular construction across the globe, and I would like to thank all those involved.”
Michael Hough, Director and Founder, MJH Structural Engineers, said: “The Modular Building Institute has recognised the achievement of Vision Modular Systems and MJH Structural Engineers by inviting us to receive the inaugural Excellence in Innovation Award at the World of Modular conference. The MBI has recognised Vision Modular Systems as world leaders and for bringing modular construction into the realm of skyscrapers.”
John McMullen, Director of the Modular Building Institute, added: “MBI introduced its Excellence in Innovation Award this year and I can’t think of a better inaugural project than 101 George Street. Michael and John did great work here that truly shows the potential of modular construction. On behalf of the industry, thank you and congratulations.”
Source: www.visionmodular.com www.tideconstruction.co.uk
Offsite technology specialists Bryden Wood is opening a new USA headquarters in Boston, MA. Board Director Jaimie Johnston MBE (pictured), together with Phil Langley, Board Director and Head of the creative technologies division, will lead on the US expansion.
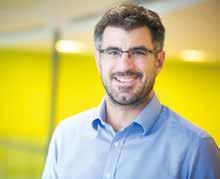
The new US HQ will allow more US clients to benefit from its market-leading offsite and DfMA approach. “This move puts us at the centre of an industry that embraces change – with large, tech-led clients working in innovative ways and moving quickly,” says Jaimie Johnston. “Being a US-registered company, with global teams, will enable us to take a leadership position for our US clients.
“We’re consistently being asked the same questions by our US clients and general contractors – can you develop a kit of parts approach, and drive it using configurators? How will this approach reduce the time and costs to deliver my assets?” continues Johnston. “Clients are seeking the same benefits of continual improvement that have allowed other industries to flourish. By developing solutions that allow appropriate levels of repeatability, without sacrificing design quality, we are helping them transform their businesses.”
Bryden Wood are working with: The Boldt Company, a leading contractor and lean construction expert on a major manufacturing facility in the US, major Canadian constructor Chandos and supply chain innovator and digital platform creator, KatalystDI.
Using standardised sets of manufactured components will create a new, open marketplace and new supply chain possibilities. These are already being explored by forward-thinking consultants in the US who are linking their clients directly to the supply chain to map out the industrialised construction process. Phil Langley says: “Clients want more control in the way they make key decisions about their future assets. They want to get to market faster, be more productive, and achieve their climate goals. This means developing new, ownable, creative technologies to enable automated design.”
Source: www.brydenwood.com
Premier Modular Awarded Europe’s First ESG Certification
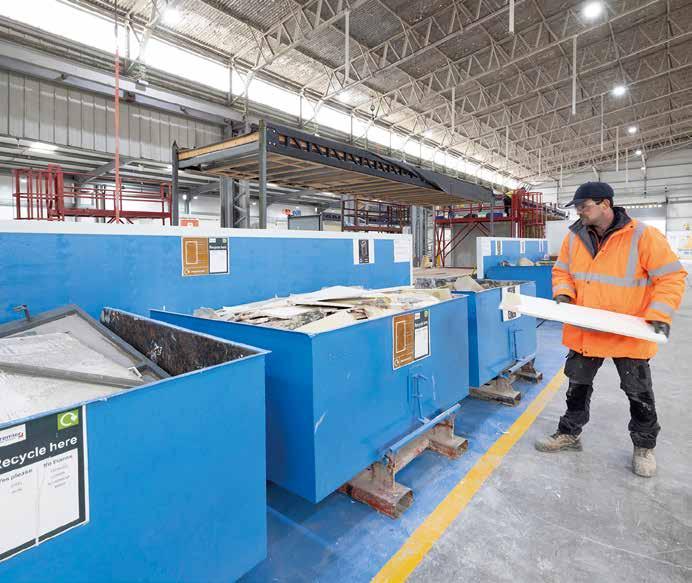
Following a rigorous independent audit conducted by global testing, inspection and certification specialists SGS, Premier has been assessed and certified for its management and performance in Environmental, Social and Governance (ESG).
According to David Harris, Managing Director of Premier Modular: “Our aim is to radically improve the sustainability of the built environment with our approach to construction, and to generate social value across all our building projects and operations. We are therefore delighted to be the very first company in Europe to receive the new certification developed by SGS. This is the next step in our ESG journey, and it demonstrates our serious commitment to corporate social responsibility and sustainability.”
“This independent endorsement gives all our stakeholders – staff, customers, supply chain, and investors – complete assurance that we are evaluating our ESG performance in line with the latest best practice, and that our ESG data and analysis are both accurate and transparent. This has been an important initiative in helping us to advance our commitment to reducing carbon emissions within Premier and in the long-term operation of our modular buildings for both rental and permanent space. And by prioritising social value in everything we do, we have the potential to unlock a range of social, economic, and environmental benefits for the communities we work in.”
Jonathan Hall, Global Head for Certification Services at SGS added: “The ESG standard developed by SGS focuses on the most important environmental, social and governance risks to a company. This enables Premier to better assess, monitor and evaluate ESG at different stages, allowing it to further reduce energy consumption across its operations, optimise material efficiencies in manufacturing, manage risk more effectively, demonstrate strong leadership in ESG, and enhance employee engagement. The Premier team has worked really hard to attain this European first and we would like to congratulate them on this significant achievement.”
A key aspect of Premier’s ESG commitment is reducing carbon footprint and several new initiatives are underway. An R&D project is in progress looking at alternative materials for modular building manufacture, which have lower embodied carbon, and Premier will be launching a new range of sustainability and fabric first options for its building rental fleet this year. Premier has a zero waste to landfill policy in the manufacture of its buildings. Its modular buildings are fully re-useable, reconfigurable, relocatable, and the steel-framed structures are infinitely recyclable, meeting decarbonisation goals. Low and zero carbon technologies can also be specified to incorporate renewable energy into its buildings for both rental and permanent space.
Source: www.premiermodular.co.uk
Supply Chain Sustainability School Awarded Queen’s Award for Enterprise
Launched in 2012, the School is an industry-wide collaboration of major companies to enable a sustainable built environment through knowledge and collaboration. The School is unique – it enables collaboration between competitor companies who share a common supply chain, and a realisation that the industry cannot develop the sustainable buildings and infrastructure society it needs without more sustainable suppliers. Its free online learning platform gives 50,000 registered users access to 3,000 learning resources, 400 virtual training sessions each year, and a range of diagnostic and benchmarking tools to support companies on focusing their sustainability strategies.
The School has been awarded the Queen’s Award for Enterprise in Sustainable Development because its approach has delivered significant environmental, social and economic benefits to its Members and Partners. The School has led pioneering work to set new standards in climate change, modern slavery, social value, sustainable supply chain management and more.
Ian Heptonstall, Director of Supply Chain Sustainability School said: “When we first floated the idea of an online sustainability learning platform for the built environment industry, we were told it was unlikely that competing companies would collaborate, nor would people use an online training platform. But most of all, that the supply chain was simply not interested in sustainability.
“A decade on and 50,000 people have trained through the School – last year alone we had over 100,000 e-learning downloads. We’re thrilled to receive a Queen’s Award for Enterprise in Sustainable Development. I see it as thank you to all those people who have joined us to collaborate and drive real sustainable change across our industry.”
Co-funded by over 180 collaborating companies (Partners), the School is delivered by an independent third-party consultancy, Action Sustainability. Leadership is provided by a School Board comprising elected representatives of Partners, responsible for fiscal governance and strategic direction. A Code of Ethics is signed by all Partners as part of the School Constitution and Partners lead the direction of the School content and activities through leadership groups.
Now in its 56th year, the Queen’s Awards for Enterprise are the most prestigious business awards in the country, only awarded for outstanding achievements, entitling winning businesses to use the esteemed Queen’s Awards Emblem for the next five years. The School’s 10-year anniversary will take place on 21 June 2022. Its vision is of a built environment industry where everyone has the skills and knowledge to deliver a sustainable future.
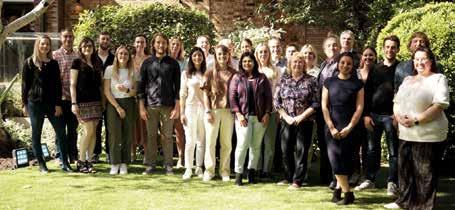
Source: www.supplychainschool.co.uk
Aptus Fastener Systems have developed the most comprehensive range of certified fastening solutions for the modular housing market.
STOCKED & SUPPORTED IN THE UK

Power Clamp – lifting device for transportation of solid panels and beams.
HECO-Topix Countersunk & Flange Head – German innovated CE compliant structural screws through ETA.
Pitzl Connectors – certified wood connection systems manufactured according to the highest quality “Made in Germany”
CALL NOW
FOR OUR LATEST BROCHURE
Building to Net Zero Report Points to Part Z
The UK Government’s Environmental Audit Select Committee (EAC) report, ‘Building to net zero: costing carbon in construction’ was published in May. The report finds that current policy inadequately addresses the need to reduce embodied carbon, develop lowcarbon materials, or prioritise reuse and retrofit.
The report makes several recommendations to resolve these issues stating: “The single most significant policy the Government could introduce is a mandatory requirement to undertake whole-life carbon assessments for buildings. This requirement should be set within building regulations and the planning system. Following introduction of whole-life carbon assessments, the Government should develop progressively ratcheting carbon targets for buildings, to match the pathway to net zero.”
Environmental Audit Committee Chairman, Rt Hon Philip Dunne MP, said: “From homes to offices, retail units to hospitality venues, our buildings have a significant amount of locked-in carbon, which is wasted each time they get knocked down to be rebuilt, a process which produces yet more emissions.
“Mandatory whole-life carbon assessments, and targets to crack down on embodied carbon, provide part of the answer. Constructors and developers can then determine which low-carbon materials, such as timber and recycled steel, they can use. As in many other areas in the drive to net zero, the UK must have the green skills to make its low carbon future a reality. Before the summer recess in July, I urge the Government to publish a retrofit strategy and upskilling programme that can ensure the UK economy will have the green jobs necessary to deliver a low carbon built environment.”
The industry-proposed Part Z amendment to the Building Regulations, outlines a method by which the Government could implement the policy suggested by the Select Committee.
Will Arnold, Head of Climate Action at the Institution of Structural Engineers (ICE) said: “We welcome the Environmental Audit Committee’s report, and it’s fantastic to see the Government recognising the need for whole life carbon regulation in the UK. The Institution of Structural Engineers supports the call for the introduction of a Part Z of the Building Regulations, which would implement the regulation called for by the Committee.”
The report also identifies that the UK has a chronic skills gap in energy efficiency and retrofit. Without these vital green skills in the UK economy, net zero ambitions will fall flat. EAC is therefore reiterating its previous recommendation that a retrofit strategy and upskilling programme be developed and published. In addition, EAC recommends that training in undertaking whole-life carbon assessments is made accessible through the education system.
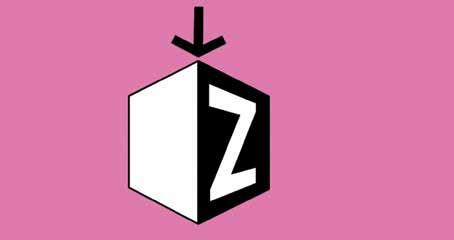
Source: www.istructe.org www.part-z.uk
CSIC Rebrands as BE-ST
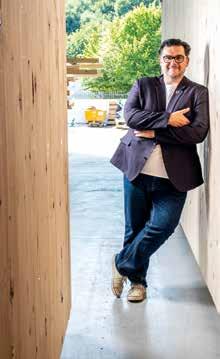
The Construction Scotland Innovation Centre (CSIC), has announced a new strategic focus prioritising the built environment’s transition to zero carbon and improving the sector’s contribution to the fight against climate change and has rebranded as Built Environment – Smarter Transformation (BE-ST). Stephen Good, (pictured), CEO of BE-ST revealed the centre’s new direction at an event hosted at the innovation factory in April that marked the midway point between COP26 and COP27.
The new brand and mission for the innovation centre underlines its core purpose: to accelerate the move to a more sustainable, energy-efficient and more circular built environment. The refreshed ambition also reflects its growing partner base beyond the construction sector, including organisations right across the wider built environment ecosystem, and its expanding geographical reach beyond Scotland.
Estimates suggest that the built environment accounts for around 47% of all UK carbon emissions, highlighting the sheer scale of the decarbonisation challenge facing the sector. BE-ST will play an important role in driving change to achieve that ambition, with a range of programmes aligned with industry, national and policy objectives. Included among them is a roadmap for the sector to reach zero carbon, with activities focussed on modern methods of construction, retrofit, sustainability and digital transformation. Since CSIC was launched in 2014, it has supported the commercialisation of more than 400 new products, processes and services, many of which focus on low and zero carbon outcomes that will help to future-proof the sector. The innovation centre has been involved in more than 350 collaborative innovation projects valued at over £34m, engaging with a range of academic, public sector and industry partners, generating over £1.3b of additional value to the sector.
Stephen Good said: “We have set out a new direction for the innovation centre, focused on delivering maximum impact and rapid transformation across the built environment ecosystem in its widest possible sense – not just the construction sector. We’ve always helped organisations explore how to do things in a more sustainable way but, from now on, this has to be our top priority. Building on that, we needed a new mission, brand and name that better reflects who we are today and, most importantly, where we’re going tomorrow. The acronym is of course BE-ST, but it’s not about us thinking we’re the best. It’s about us all working together to do our best, to find the best ideas and the best approaches.”
For more on the work of BE-ST and understanding offsite technology see page 54.
Algeco New Website Live
Net Zero Buildings Reports 300% Pipeline Increase
Algeco (formerly known as Elliott) and a longestablished brand in the European modular services and infrastructure industry, has unveiled its new website. It is the first time that the Elliott Group, Procomm Site Services and Carter Accommodation suite of portable and modular building solutions have been showcased on a single, combined brand and website platform.
The new website is the latest customer facing initiative of Elliott, Procomm and Carter’s unification under a single brand, which took place at the end of March 2022.
Algeco.co.uk has been designed to offer the ultimate user-friendly experience, employing the latest techniques for navigation and improving functionality, allowing customers to easily view the full suite of products and services on offer. Favourites such as an internal search engine and online chat have been retained. Featuring the iconic Algeco logo and font, common across the wider Algeco European business, the website brings a fresh perspective to the UK portable and modular building sector. Created with the user experience in mind, the website incorporates more motion content to enhance user interest and engagement. Look Ahead Navigation reduces the
Net Zero Buildings Ltd (NZB) has secured a new contract to deliver a £1.6m net zero in operation building at Hart School, while reporting a 300% increase in its pipeline during Q1 2022.
The business was acquired by Premier Modular in summer 2021. After a period of consolidation, it has relaunched with a new management team, ambitious growth strategy and new brand identity that better reflects its ethos. Divisional Director Dan Allison is working alongside Managing Director David Harris and the wider team to drive forward its ambitious new growth strategy as it targets projects within the healthcare, education, commercial and retail sectors.
Dan Allison, Divisional Director at NZB said: “We are extremely encouraged by the business’ performance as we approach our financial year end – we have a strong, strategically focused pipeline in place which reflects our focus on both zero carbon in operation buildings alongside our panel manufacturing division.
David Harris, Managing Director of Premier Modular Group added: “NZB has undergone a complete transformation since the acquisition last year, which has refocused its priorities to ensure that it is in the number of clicks which visitors have to make to navigate the site. Product Filters then allow users to easily hone down the Algeco product or service they require.
Chris Coxon, Head of Marketing at Algeco, said: “The design of our new website reflects the latest updated branding of the Algeco business globally. At the same time, it brings together three UK businesses under a single, consistent brand, allowing customers to quickly browse a much wider product range on a single platform, to give us a stronger online presence.
best possible shape. Sustainability has been a major factor in the design and delivery of new buildings for many years, but, with net zero targets creeping closer, innovation is accelerating rapidly. It’s vital that new projects coming forward really ‘push the envelope’ to achieve net zero carbon in operation in order to meet current and future expectations; particularly where ESG is a factor.” “The new website has been accompanied by a merging of our social media channels, simplifying and creating larger networks for us to continue to develop. We now have over 13,000 LinkedIn followers – and growing rapidly. With the online strategy we have in place, we’re in a strong position to help the business fulfil its ambitions.” The new brand represents Algeco UK’s collaborative approach to finding solutions for customers, developing both its products and people to deliver leading quality service and ensuring the futures of customers, their end users and our organisation are sustainable.
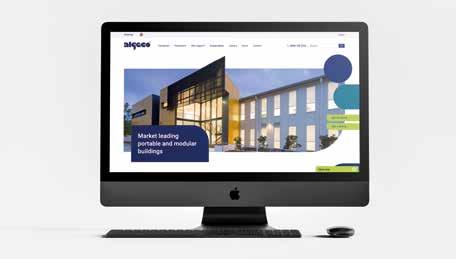
Source: www.algeco.co.uk
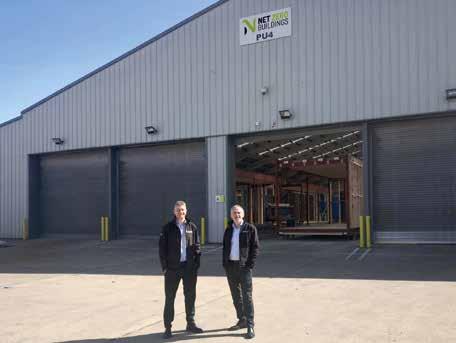
NZB specialises in the delivery of intelligent buildings that achieve carbon zero in operation across the education, healthcare and commercial sectors. Working alongside AESG consultants, its carbon experts guide customers through their journey in achieving net zero energy buildings.
Source: www.netzerobuildings.co.uk
Kier Introduces Smart Solution for Site Accommodation
Kier Construction Western & Wales, working with Elliott (now Algeco), has unveiled a revolutionary pilot project that uses smart technology solutions to cut carbon emissions by up to 25% on its site accommodation at the Winterstoke Hundred Academy Expansion.
432m2 of Moduflex® buildings were specified by Kier for use as welfare, offices and meeting rooms on its net zero, 900-school place Winterstoke Hundred Academy School Expansion Build in Weston-superMare. Kier’s innovative approach to cutting carbon and energy use on this project sets new standards for site accommodation. It is being hailed as a blueprint for how future construction projects will achieve endto-end carbon reduction that start from day one.
Energy saving features and smart technology is being used in the Moduflex® modules to monitor, manage and reduce carbon and electricity use. This will contribute to significant carbon savings during the 80-week construction schedule. The Moduflex® modules fully furnished and ready for the smart technology. The technology will monitor energy within zones, taking readings across a wide range of parameters every few seconds to optimise energy use and identify any interventions required. Moduflex® is made using responsibly sourced recycled PVC-U and recyclable timber from certified/ managed forests. Even the temporary foundations are made using sustainable, reusable materials that haves significantly less embodied energy compared to traditional concrete foundations.
Jon Woodman, Bristol Area Manager at Kier Construction, said: “This project sets new standards for site accommodation, and it is fitting that they are deployed on a zero-carbon build. The cabins are already installed on-site and early indications are that they are achieving impressive carbon reductions. We will gain a better understanding of savings over the next few months. The site accommodation at Winterstoke Hundred Academy School will be in place for 80 weeks and so the savings in energy and carbon will make a significant difference over the duration of the development.”

Source: www.kier.co.uk
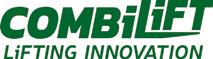
Safety Storage Efficiency
Meet the needs of your customers more safely, using less space and with greater efficiency when you invest in Combilift materials handling solutions
• • • • Safer product handling Optimised production space Improved storage capacity Increased productivity & • output Enhanced profits
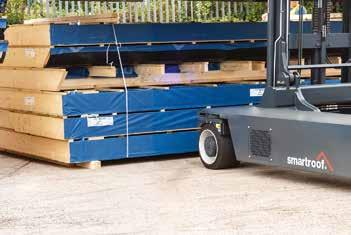
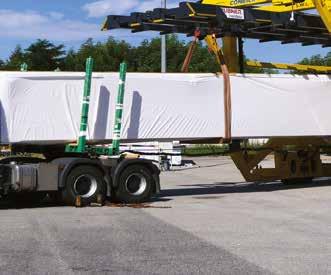
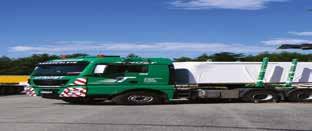
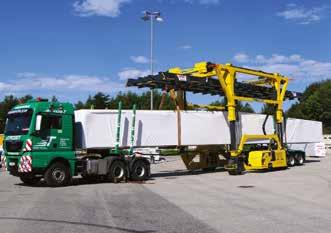
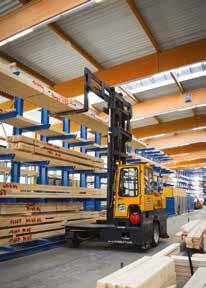
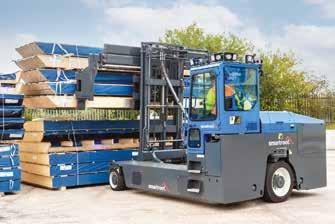
Gramophone Works Reaches Completion Euramax Solutions Gearing up for Growth
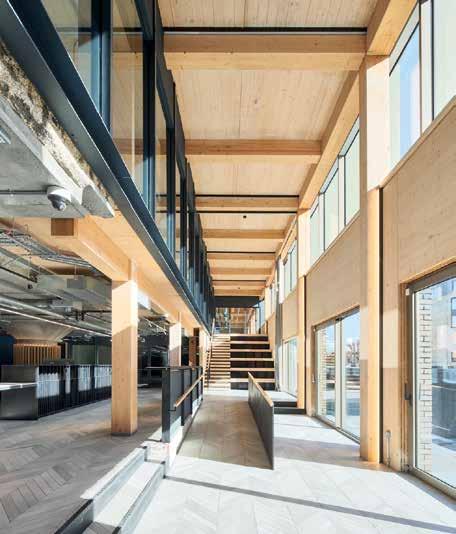
GRAHAM has completed the design and build of The Gramophone Works, a new landmark development offering premium workspace in Notting Hill, London.
Over the course of the construction programme, GRAHAM refurbished and extended the former home of Saga Records to provide 65,000sq ft of new and refurbished commercial space for small and medium businesses. This includes communal amenities, cycle storage, a café, large open plan working areas and green areas at ground and roof levels.
The addition of a lightweight glass and cross laminated timber (CLT) and glulam structure, constructed using the latest in timber technology, emphasises the development’s commitment to reducing its environmental impact, establishing it as an exemplar of low carbon development as well as one of the largest CLT and glulam office building in Europe.
Located next to the Grand Union Canal in west London, the building’s architecture seamlessly integrates into the historic and social fabric of the external environment through new brick and glazed façades added to all elevations, referencing both the building’s rich, industrial heritage and cultural significance. The scheme’s sustainable approach is further emphasised through the adoption of existing structural elements, reducing waste and construction activity, as well as the implementation of photovoltaic solar panels, reducing energy consumption. As a result of these efforts, the scheme was awarded the Environmental Prize Winner at the New London Awards in 2021.
Rob Joyce, Graham’s London Office Director, said: “It’s great to see this state-of-the-art commercial campus come to life and officially launch to the business community. We’re proud to have played a central role in the delivery of this transformative development that we feel has set a high standard for sustainability and architecturally led design.”
Source: www.graham.co.uk
A leading manufacturer of uPVC windows and doors for the modular and offsite construction sectors is gearing up for 12 months of ambitious growth. Euramax Solutions, a Modular Group Investments (MGI) company that also supplies to national builders’ merchants and newbuild and holiday home markets, is growing rapidly thanks to high demand. A plan to grow by more than 35% in the next 12 months is in place, with everything from supporting and extending its existing customer base, investment, recruitment and net zero a focus to help achieve it.
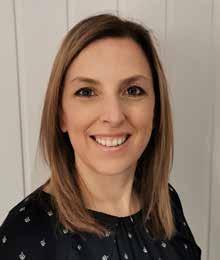
Emma Chapman, Euramax Solutions’ new Business Unit Director, said: “After a successful first quarter of 2022 we are in a position to push forward with our growth plans for the next 12 months. We have rapidly grown into the modular sector and are currently targeting more partnerships in the modular and merchant world while continuing to strengthen our support for our customers. We are also looking to invest in new machinery so we can not only continue to make our high-volume products but bespoke ones as well.
“Due to the growth we intend to make, we need to make sure that we have got the personnel in place to help us succeed, so we will be looking at doing another recruitment drive. We are also focused on our net zero journey and our plans to reduce carbon, which will reduce costs. We’re in a growth period and we’re in a great position - and it’s only going one way and that’s upwards.”
MGI CEO Nick Cowley added: “One of the reasons we acquired Euramax Solutions at the beginning of last year was because we recognised its potential and its ambitious growth plans are hugely exciting for the future. The UK offsite and modular sector is only going to get bigger and both Euramax Solutions and MGI will be at the forefront.”
Source: www.euromaxuk.com
Construction Minister Visits Landmark Timber Building
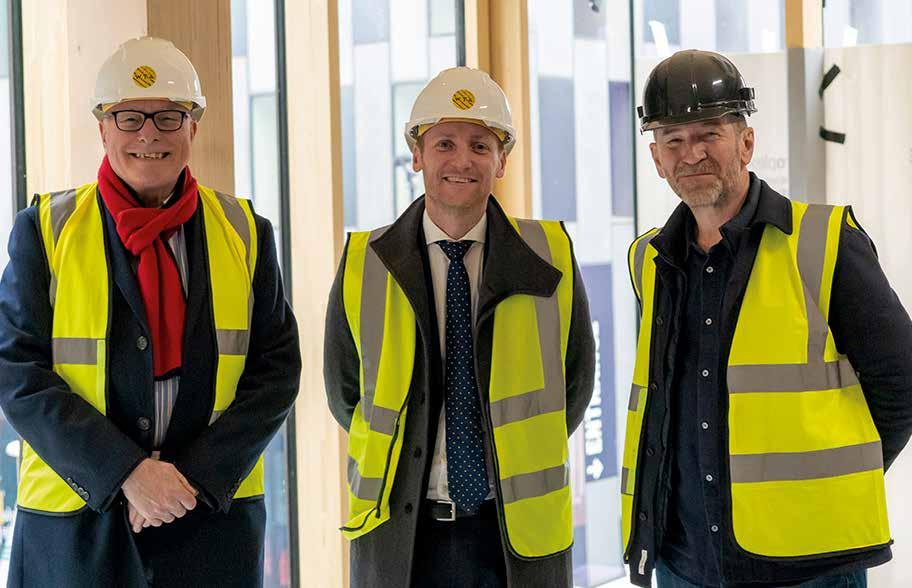
As the Government works to ‘build back greener’, the Confederation of Timber Industries (CTI) in partnership with Waugh Thistleton Architects recently hosted the UK Construction Minister Lee Rowley, on a site visit to the Black and White building.
The Minister was taken for a tour of the engineered timber building, which is owned by The Office Group (TOG), the premium flexible workspace provider with a platform of more than 50 buildings across the UK and Germany and will be the tallest timber office structure in London when complete later this year.
Boasting a powerful sustainable agenda, the hybrid structure comprising beech laminated veneer lumber (LVL) frame with cross laminated timber (CLT) has resulted in 37% less embodied carbon than an equivalent structure built using steel or concrete, demonstrating how a shift towards the use of biogenic materials in construction could help the industry to significantly reduce its impact on the environment.
Following its release of the Build Back Greener Strategy Document, the Government has signalled a clear intent to increase the use of sustainable materials, such as timber, within construction as it seeks to meet its net zero obligations. Key to the success of this endeavour, is increasing the awareness and knowledge of structural timber. As such, the CTI is actively engaging with the Government and other stakeholders via the Timber in Construction working group, set up to develop a policy roadmap to help the Government deliver on its environmental ambitions.
Speaking on the visit Andrew Carpenter, Director at the CTI said: “Independent bodies such as the Climate Change Committee have already said that increasing the use of timber within construction is crucial to achieving net zero status by 2050, because of the low-carbon benefits of these forms of construction. The sustainable benefits of timber as a form of carbon capture and storage are widely known, and today has been about illustrating how these benefits are already being delivered safely across the UK, as well as globally, to create a new wave of low-carbon construction. In partnership with the UK Government via the Timber in Construction Working Group, and together with members of Parliament through our APPG for the Timber Industries, we are helping bring forwards the benefits of greater use of structural timber.”
Construction Minister Lee Rowley commented: “It was fantastic to visit the Black and White building to see how this innovative approach to building, harnessing engineered timber, is helping to drive sustainability in the construction sector. The site’s construction is an excellent example of the benefits timber buildings can bring and I look forward to seeing it when it is complete and in operation.” Andrew Waugh, Founder and Director at Waugh Thistleton Architects, commented: “It’s great to see the Government taking an interest in engineered timber construction. We need Government leadership and systemic support for the use of regenerative, low carbon construction materials if we are to have any chance of reducing the impact of our industry on the planet.”
Charlie Green, co-Founder and co-CEO of TOG commented: “The Black and White Building is set to be Central London’s tallest mass timber office building. Alongside Waugh Thistleton, we have worked to reduce embodied carbon as much as possible, delivering a building that represents what future workspaces should be. It has never been more important to develop techniques and approaches that deliver buildings for a better world. Innovative construction processes and sustainable materials, like those employed here, will form a central part of the sector’s journey to net zero over the coming years. We’re really pleased that Lee Rowley, MP, visited the site today to see this evolution in practice and look forward to further engagement.”
Pictured (L-R) Andrew Carpenter, CTI, Lee Rowley, Construction Minister, Andrew Waugh. Waugh Thistleton Architects
Source: www.cti-timber.org
SHIFTING BUILDING MINDSETS
Legal & General Modular Homes (L&GMH) are one of the major names transforming housebuilding in the UK with sustainability and precision quality at the core of its offsite manufacture approach. Chief Executive, Rosie Toogood spoke to us about how they are helping deliver next generation living.
Q: Most industry observers would agree that L&GMH got off to a misfiring start but seems to be operating more smoothly now – what’s changed and how have you realigned the way things work?
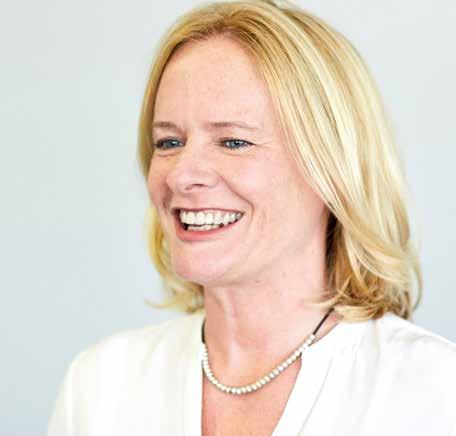
Rosie Toogood (RT): Transformation does not happen overnight. True innovation takes time. We have been creating a system to ensure that we can build the best quality homes in the most efficient way possible. We have had to get this right to start to deliver at scale. As a result, our innovative approach to housing delivery, has gained significant momentum within
1
the marketplace with the business commencing construction on sites at Selby, Bristol and Broadstairs last year for the delivery of 450 homes. Having also acquired land at Littlestone, Kent, North Horsham and Warminster the business is currently seeking planning permission for the delivery of over 450 homes across these three sites where construction is expected to commence this year. The factory in Yorkshire is the largest in the UK. With capacity to produce 3000 homes annually, we employ 600 people and provide the skills and training our staff need through our Modular Academy.
Q: You took over as Chief Executive mid-2017, bringing design-led manufacturing and factory experience from Rolls-Royce – how has this mindset and approach transferred to creating volumetric modular homes?
RT: So many industries, automotive, aerospace, electronics to name but a few, have proven that modern manufacturing techniques significantly improve quality and speed of delivery whilst reducing cost and improving the product. Volumetric modular manufacturing has the potential to do the same for housebuilding but it is not easy. Typically, it takes many years of significant investment in people and culture as well as equipment and engineering to do it well and build to scale. The automotive industry for example has taken 100 years to get where it is now. Few businesses have the investment capacity, capability and skills needed to do this, many like to stick to the status quo. However, I’m pleased to see the volumetric modular industry in the UK maturing. We are committed to investing into this industry which will transform the housing industry. As we increase our output over the next few years we will create thousands of jobs, employing people directly in our factory and on construction sites as well as in the UK supply chain creating a new industry with meaningful jobs.
Q: The UK housing market has faced a shortfall in new homes for decades with an increasing number of ‘market disrupters’ offering various answers – how does L&GMH fit in to this dynamic?
RT: Society currently faces a dilemma. On the one hand, we have a decade to prevent catastrophic climate change.
On the other, there is a chronic housing shortage that requires the provision of new homes – but building with conventional methods would only increase carbon emissions. It is possible that by transforming the way we build homes in this country we can also reduce emissions. There has been much talk of the benefits of volumetric modular technologies, but it has yet to really capture the public imagination. Beyond the pandemic, though, modern methods of construction can enable the construction of beautiful, high-quality homes at speed and – importantly – with lower carbon emissions than traditional methods.
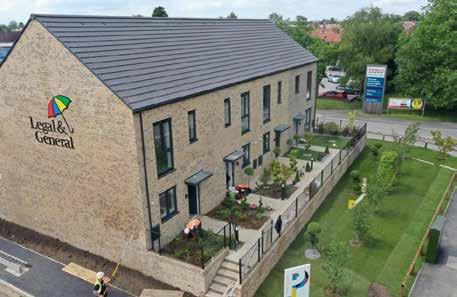
Q: The ‘traditional’ way of housebuilding construction – masonry and site-based operations – is increasingly seen as outdated. Can offsite delivery, DfMA and factorybased methods really deliver lasting industry change?
RT: Absolutely. We believe that there will be many ways in which we build that would significantly benefit traditional housebuilders. Like how we have taken learning from industries such as the automotive industry, there are so many ways that we can be more efficient and innovate when it comes to housebuilding. For example, our way of building, by using a precision engineered system, ensures minimal snagging and results in a higher quality product. We can produce homes quicker by using offsite construction. We have a chronic housing shortage so one thing that is clear is that we can’t stick to the status quo.

Q: How integral to the future of homebuilding is the understanding and use of digital tools and technology to develop energy efficient new homes and increase quality and productivity levels?
RT: The use of digital design tools is fundamental to our approach, and we have and will continue to invest heavily in their development, enabling us to broaden our product range and increase the efficiency of operations within our business and the supply chain. Our objective is to fully integrate our key business systems enabling a flow of information from design, through the procurement process, into production, construction and ultimately to customer support. This approach has transformed operations in other industries, and we are well on the way to doing so in our business with many of the resultant improvements in productivity and quality already being seen.
Q: In general, carbon reduction is central to everything we do in society, but there is an additional construction focus on understanding embodied energy more. How is L&GMH delivering its homes with sustainability issues and net zero targets in mind?
RT: At Legal & General, we have pledged to make all our new housing stock net zero in terms of operational carbon by 2030. Legal & General Group is therefore working to improve the thermal performance of
2
3
homes and incorporate low-carbon technologies that will reduce the amount of energy used. This will be implemented in a phased approach across all homes in which the groups invests or that it builds. As we move towards net zero, modular housing provides us with an immediate advantage. L&GMH is already net zero regulated carbon capable and we will deliver our first ‘net zero’ homes at our site at Bonnington Walk Bristol later this year.
The combination of thermally efficient materials, air source heat pumps and solar panels, results in homes that are highly energy efficient with a greatly reduced carbon footprint both during construction and across the lifetime of each home. It also means significantly reduced heating bills for residents.
To put this into perspective our modular homes are 60% more efficient to run for the homeowner than a Building Regulations compliant newbuild home and our apartments are up to 30% cheaper to heat and run than the average apartment. If you also look at the cost in use and the amount of carbon used over the lifetime of the property, the results are impressive. Using one of our homes over a 100year period would result in about 85 tonnes of carbon over that period. A similar newbuild home would emit about 213 tonnes. That’s 40% less carbon than a Building Regulations compliant newbuild home. This is important as we need to be building homes that will last and keep up their quality and sustainability credentials throughout their lifetime.
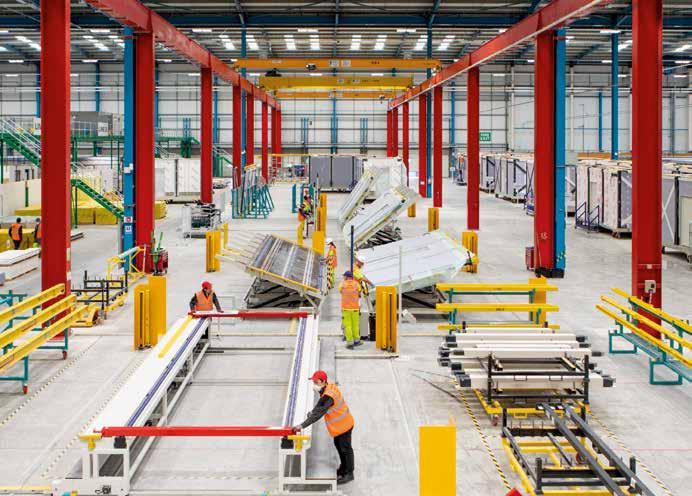
Q: Can you say a little about the materials used for the volumetric modules – timber/light gauge steel/ hybrid – what does each house comprise of and what stage of completion do the units exit the Sherburn-in-Elmet facility?
RT: Our houses are made primarily from cross laminated timber (CLT) with a steel floor on the ground floor sitting on the foundations. Our apartments are constructed of concrete and steel. The modules leave the factory fullyfitted, with bathrooms and kitchens fitted and walls painted. If you stood inside a module shortly after it landed at site, apart from some minor plastering required at the points where the modules joined, you would feel like you were in a completed new home.
Q: You have several projects at various stages of completion, including a new neighbourhood at Bore Hill Farm in Warminster. What feedback are you getting from developers and clients on the volumetric modular process?
RT: The feedback has been really positive with regards to the placemaking, quality of build, and space and light provided. Our site at Bonnington Walk, Bristol won a design award and our site at Selby was the regional finalist in the prestigious NHBC Pride in the Job awards.
4
Q: How do you see the offsite and volumetric modular sector developing over the next 18 months and what ideally do you want to see change from a L&GMH perspective?
RT: Our pipeline is growing rapidly and fundamentally the market’s acceptance and perception of modular homes is definitely changing. Customers are excited to buy, rent and live in a home which embraces the best sustainability technologies available in the housing market, provides a real community feel with great placemaking and accessible open space for them to enjoy within the developments and saves on fuel bills as a result of the energy efficiency of the homes.
For more information visit:
www.legalandgeneral.com/modular-homes/
Images:
01. Rosie Toogood, Chief Executive, L&G Modular Homes 02-03. The newbuild modular homes are high quality energy efficient homes 04. The factory environment provides precision DfMA results
STEEL HORIZONS: A UNIQUE INDUSTRY EVENT EXPLORING THE FUTURE FOR MODERN CONSTRUCTION
Continuing Howick’s focus on advocating for better ways of building, the company is bringing a unique event to London for June 2022.
Howick CEO Nick Coubray says the venue is iconic, offering spectacular panoramic views of the London skyline. It is the ideal setting for guests to ponder how technology may be shaping similar vistas in years to come, he says, as the STEEL HORIZONS event will explore the future of modern construction.
This exclusive event will feature guest speakers representing a range of leading-edge construction disciplines offering international as well as UK perspectives on the industry and its future.
Joining Nick as speakers are
• Nicola Moriarty, Director of
Structural & Civil at Bryden Wood
- The Forge – an inside look on the platform approach of DfMA – the successes and lessons learnt
• Matthew Teague, Senior Architect
& Project Manager at Tata Steel –
Design led, manufacturer enabled, how DfMA can make better buildings
• Dave Cooper, Co-founder &
Host of Dave Cooper Live - Out from behind the mic: A global view on innovation in the built environment
• Chun Qing Li (Lee), Founder and
CVO of KREOD – Digital Master
Builders, using design, innovation technology and Intelligent
Automation (IA) to create changes in the AEC space
• Scott Mitchell, Founder of
STUD-IO - Computational
Construction and pushing the boundaries of light steel fabrication to unlock capabilities and explore innovative uses in complex construction projects A full overview of the presentations and programme for the event can be found on the event website at steelhorizons.com
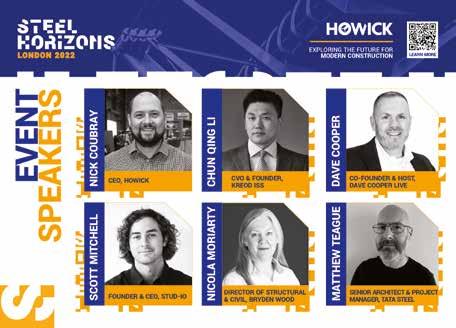
Attendees will have the opportunity to put questions to the experts following each session, and the event will wrap up with drinks and hors d’oeuvres so guests can mingle with industry peers and speak to our presenters.
REGISTER YOUR INTEREST STEEL HORIZONS | London 2022 New Zealand High Commission’s New Zealand House, Penthouse Suite, 80 Haymarket, London SW1Y 4TE Thursday, 23rd June from 2 to 6pm
To join Howick and guests for this unique event, register your interest on steelhorizons.com. Numbers are strictly limited, so attendance is by invitation only. Everyone who registers will receive access to videos and materials of the presentations following the event.
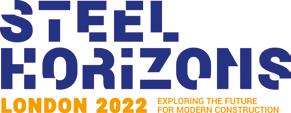