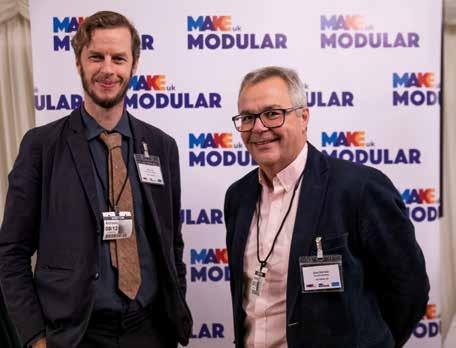
12 minute read
Rebuilding the Construction Landscape
Steve Cole, Head of Make Modular, outlines why the new organisation is required and where it sits in a constantly evolving construction and homebuilding world.
For as long as I’ve worked in housing, modular has been the coming thing, the innovation which will save the housing industry from low productivity, an ageing workforce, massive carbon footprint and poor build quality. But somehow, it has never quite happened, even though everyone in the industry knows that: • The UK needs more homes, and fast • It needs homes which are green to build • It needs homes which use less energy • It needs homes to be great quality and good value • And it needs new people to build them.
It needs homes: greener, better, faster and this is where Make Modular comes in. The modular sector is at a tipping point as it moves from an innovator to early adopter market. If we’re going to finally move UK housing out of perpetual crisis mode, our sector has
1
the key role to play. Make Modular, the new trade body, has been formed to support the sector in making that transition. Everyone in the sector knows modular means greener, better, faster housing delivery. The tricky bit is ensuring those outside the sector ‘get it’.
Launched in parliament in December 2021, Make Modular was founded by Ilke Homes, TopHat, Urban Splash, Laing O’Rourke, L&G Modular, Vision Modular Systems, and the trade body for the manufacturing sector Make UK. Most trade bodies, very reasonably, are focused on stability and incremental growth. With ‘what we have we hold’ being, very reasonably, the dominant mentality. Make Modular was set up for exactly the opposite reason. The intent is for the new trade body to act as the voice for the volumetric modular housing sector ensuring that Government and stakeholders understand what the sector has to offer the country and the support it needs to transform our housing market. Make UK, under whose umbrella Make UK Modular, sits has an excellent reputation for producing evidencebased policy work which means it regularly engages with the most senior levels of government and business. We intend to take the same approach, and indeed make use of the expert economists and public affairs specialists within the wider organisation.
Over the last five months we’ve focused on building our relationship with Department for Levelling Up, Housing and Communities (DLUHC), Homes England and wider political stakeholders. We want to be the first port of call for Government on all things modular and with regular meetings with civil servants, MPs, and think tanks are making great progress on that front. Our recent joint workshops with DLUHC on warranties, standardisation and data are just one example of this.
Unlike the social housing or housebuilding sectors there is currently only limited data available on the volumetric modular sector. This means we are an industry with a limited overview of ourselves. We don’t really know how many modular homes are being built, what standard they are being built to, and what is being invested in the sector. This is a gap we aim to fill. Our recent work on the sector’s capacity gap is one example of this. We now know that the UK has seen nearly £1b of investment in modular factories, prototyping and systems in the last five years. We also know that there is sufficient capacity in place today to deliver more than 20,000 modular homes a year by 2024. The sector is at a crucial point in its development.
Government must capitalise on this investment and capacity, it won’t have this opportunity again.
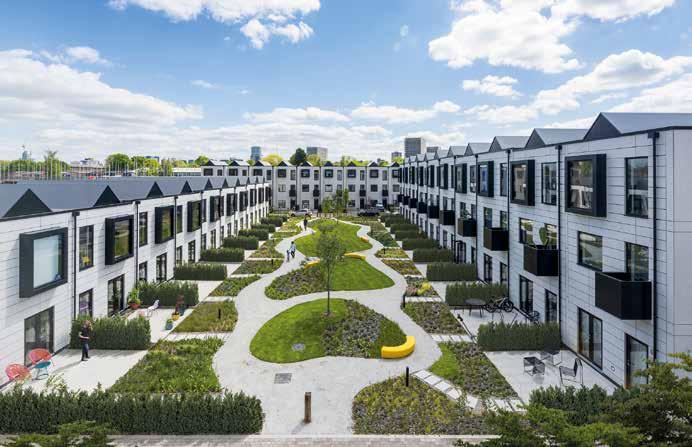

We need government to accelerate delivery ensuring the viability of the investment made and the jobs created by removing the remaining barriers holding the industry back. These are moves which can only be delivered by government, and do not require new money.
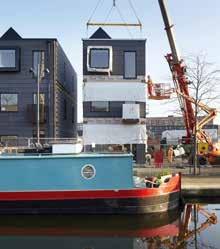
These include: • Sustainability: enhance housebuilding sustainability by introducing more a robust commitment to and targets for netzero • Scale: dedicate 40% of the
Affordable Homes Programme to
MMC, and 50% of this to volumetric modular • Planning: create a fast-track planning route for net-zero homes • Land: government to require a minimum percentage of its land bank to be allocated for modular homes • Levelling Up: create a modular capacity strategy linking new factory location, high housing demand areas, and levelling up priority regions
2
3
However, Make Modular can’t deliver this on its own. That’s why working in partnership with our members and growing our membership is so important. Our membership already covers around 70% of the modular homes delivered in this country but we want to ensure we can speak confidently and accurately to Government on behalf of the entire sector.
I’m confident that with the right evidence base, strategy, and the modular sector pulling together we can ensure the Government delivers
4
the best possible environment for modular industry to deliver the transformation the nation’s housing so badly needs.
For more information visit:
www.makeuk.org
Images:
01. Steve Cole and ilke Homes’ Dave Sheridan at Make Modular Launch 02-04. Modular manufacture has the means to transform UK housebuilding
PREMIER GUARANTEE TURNS 25
Manchester United won the league title, Tony Blair was Prime Minister and Harry Potter became a literary phenomenon. Yet 1997 was a landmark year for another reason – Premier Guarantee was launched. Now 25 and the second largest provider of structural warranty in the UK, Premier Guarantee has become a major player in offsite construction.
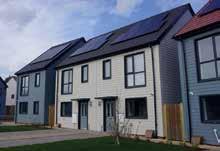
1
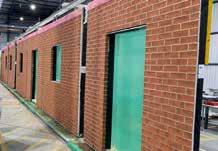
Premier Guarantee’s first recorded use of modern methods of construction (MMC) was for a custom build home at the self-build development in Graven Hill, Oxfordshire, in 2003. Since then, the UK’s second largest provider of structural warranties has worked on hundreds of developments using MMC elements, from complex skyscrapers to closed panel timber frame low-rise homes.
Offsite elements and MMC make up a growing proportion of many UK construction projects. In working on such developments, Premier Guarantee has created a system acceptance process to ensure specified systems meet our warranty performance standards.
Manufacturers can take advantage of our four-step acceptance process, beginning with initial triage, detailed review, factory inspection and trial site assessment. Once a site has shown that a system can meet our warranty requirements, the product or system will be granted Premier Guarantee system acceptance for one year. At that stage renewal will be required, to ensure changing technical requirements and the current legislation can be met.
2
In addition to factory visits, site inspections start at foundation stage and combine typical build-stage visits with risk management inspections, based on an initial assessment and according to the risk factors of the development.
It’s important to note that Premier Guarantee warranty system acceptance does not constitute a third-party product approval from a UKAS-accredited testing body and is designed to recognise that a product or system used can meet our warranty requirements.
LoCaL Homes closed panel timber frame
Using timber frames, specialist insulation, pre-installed claddings and a range of innovative techniques, LoCaL Homes manufacture a sustainable, environmentally conscious, low carbon alternative to more traditional brick-built structures. Run on social enterprise principles through social housing provider GreenSquareAccord, LoCaL Homes is committed to communities as well as the environment.
Clifford Davis, Technical Innovations Surveyor at Premier Guarantee, said the warranty provider’s acceptance of LoCaL’s closed panel system offered an exemplar of how MMC system manufacturers should engage with the supply chain.
He said: “LoCaL is just the kind of company we want to work with, as they strive to produce a high-quality product and are happy to work with us to improve their own standards, which in some instances already exceed current building regulations. “They have invested heavily in a new factory and machinery to improve and protect their product. All timber elements are cut and nailed by automated machines to ensure a high level of accuracy.
Coupled with this they have good QA processes, multiple checks and supervision through-out the construction process, ensuring a consistent level of quality".
Premier Guarantee’s range of structural warranties provide cover for 10 or 12 years and can include mechanical and engineering defects for plant installations as well as structural defects. Also typically included is cover for contaminated land, alternative accommodation and professional fees.
For more information visit: www.premierguarantee.com/ our-services/system-acceptance email: systemacceptance@ premierguarantee.co.uk or call: 0800 107 8446
Images:
01-02. Premier Guarantee has worked on hundreds of developments using MMC elements over the last 25 years
INTELLIGENT CONSTRUCTION
Sam Hart, Head of Modern Methods of Construction (MMC) programmes, Built Environment – Smarter Transformation (BE-ST) sees the public sector playing a huge role in boosting the adoption of MMC technology.
While robotic excavators and autonomous vehicles might be some of the first things that spring to mind when people think of automated construction, these are somewhat futuristic illustrations of the types of advanced technologies most likely to be used on construction sites. Digital transformation is well underway, however, with artificial intelligence (AI) becoming an increasingly important tool for enhancing efficiency, improving safety and eliminating human error.

A number of companies have brought robots to construction sites, for instance, with robot ‘dogs’ or remotely operated vehicles (ROVs) similar to those used by the subsea and oil and gas sectors supporting tasks like data gathering, measurements, remote monitoring and 3D mapping. Initial studies have shown that these robots can easily navigate potentially hazardous conditions to collect different types of information through sensors, cameras and scanners.
Last year, we also saw the first automated bricklaying robot secure accreditation from NHBC, giving formal recognition that the robot could deliver work to the same standard as a human. A recent study suggested that the number of robots used on construction sites could rise to around 7,000 over the next five years, but as most construction sites begin to embrace enhanced digital technologies, one area where the adoption rate is already standard is in offsite manufacturing.
In fact, intelligent, automated technology is already playing an important role in offsite and modern
1
methods of construction (MMC) with some of the UK’s major housebuilders investing heavily in new equipment and digital infrastructure to support the increasing demand for more advanced industrialised build systems. There is one client in a unique position to drive change: the public sector is one of the industry’s largest ‘customers’ so to speak, responsible for around £26b of new projects in 2020, including schools, hospitals, infrastructure and other types of construction activity. Rising public sector demand for offsite projects and the introduction of frameworks and policies that promote the use of advanced offsite manufacturing methods are acting as a catalyst for investment and development – particularly among the major contractors in England.
For example, the recently launched Offsite Construction Solutions framework being delivered through The Crown Commercial Service (CCS), is a £10b framework to be used by all UK public sector bodies providing access to manufacturers of offsite solutions. The proposed seven-year agreement is planned to supersede the existing £500m CCS framework launched in 2019 for offsite construction. The intention is that it is used by central government departments, their arm’s length bodies and the wider public sector including local government, health, education, police, fire and rescue, housing associations and third sector.
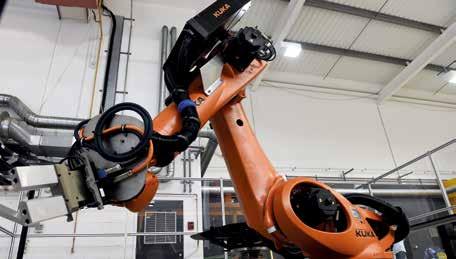
With a greater focus on MMC in public procurement practices, we will see more contracts being awarded to offsite specialists who can invest further time and resources in innovation and new technology. These larger public sector contracts are likely to be awarded to some of the bigger contractors, but if robotics and automated technology become the norm for them, it will ultimately filter down to smaller companies and the wider supply chain too. Of course, change won’t happen overnight and, particularly for the public sector, it requires an evidencebased approach. For those of us already working closely in offsite and MMC, we have seen the benefits first-hand – and we need to be able to effectively communicate these to decision-makers.
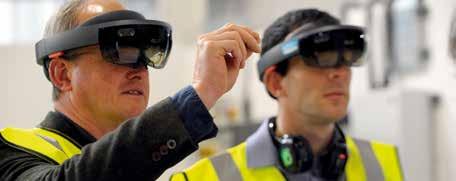
Initiatives such as the Advanced Industrialised Methods for the Construction of Homes (AIMCH), Edinburgh Home Demonstrator, and Transforming Timber – all supported by Built Environment – Smarter Transformation (BE-ST) – are intending to do just that, building an evidence base that can be used across the built environment. Perhaps most importantly, each of these projects also take account of the carbon savings and environmental benefits that come from offsite manufacturing combined with the use of natural alternative materials such as engineered timber. With data and scientific evidence in place, public procurement practices could be updated further in favour of MMC across other parts of the UK, leading to more work for offsite manufacturers. In turn, this will enable them to invest and develop their offering even further to include robotics and AI.
CSIC = BE-ST
Built Environment – Smarter Transformation (BE-ST), formerly Construction Scotland Innovation Centre (CSIC), has a new strategic focus prioritising the built environment’s transition to zero carbon and improving the sector’s contribution to the fight against climate change. The new brand and mission for the innovation centre underlines its core purpose: to accelerate the move to a more sustainable, energyefficient and more circular built environment. The refreshed ambition also reflects its growing partner base beyond the construction sector, including organisations right across the wider built environment ecosystem, and its expanding geographical reach beyond Scotland.
2
3
Digital transformation is a process that we have to approach stage by stage and it will take time. We can’t jump straight from building houses by hand to having robots and automated technology on every project – and that might never happen – but we have an opportunity to maximise the role of digital transformation in offsite manufacturing. We already know that waste is minimised, productivity improved and accuracy enhanced through the use of MMC, so we can make some assumptions as to how the greater use of robotic technology could influence these elements too.
As with any kind of innovation, we need to evidence scalability and surety of pipeline demand to drive widespread investment. In the case of offsite manufacturing, it could quite feasibly be the public sector that holds the sustainable fuel to supercharge change at scale.
For more information visit:
www.cs-ic.org
Images:
01-03. Digital technology underpins the offsite sector and will play a huge part in future construction projects