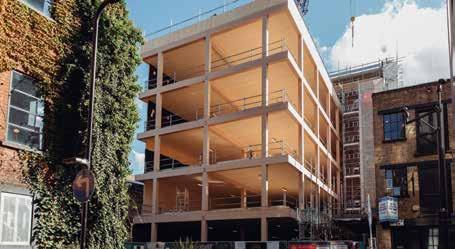
10 minute read
Next Stage in the New Timber Age
THE NEXT STAGE IN THE NEW TIMBER AGE
Laminated veneer lumber (LVL) is becoming a more familiar feature of timber-based construction. Peter Wilson, architect and founding director of the Mass Timber Academy explains more.
Like glulam, LVL is formed from layers of wood in which the grain in every layer runs in the same di-rection. Unlike glulam, however, LVL’s layers are only 3mm thick and are produced by putting a long blade against a rotating log to peel a continuous veneer that is subsequently glued and pressed into boards or beams. There are two advantages to this over CLT or glulam – the resulting LVL products have significantly greater strength than their two mass timber siblings, plus they make far more effi-cient use of the raw timber.
Over the next few years, LVL demand in Europe is forecast to have a projected average annual growth rate of 6+%. This substantial LVL consumption increase will likely be driven in the main by several key factors, including growing LVL usage rates and volumes in domestic house construction both as beams and headers as well as I-Joist flanges – builders’ needs to shorten building erection times, to avoid expensive on-site equipment and to reduce the cost of on-site labour. This base level demand will undoubtedly benefit from greater awareness amongst architects and engineers of LVL’s properties and benefits and its consequent use in larger commercial and public projects.
1
Amongst these benefits are the continuing advances being made in peeling and lamination technology that allow manufacturers to produce lighter and smaller LVL sections with a greater strength and longer span than sawn timber. As wood defects have been removed and randomised within thin lay-ers, LVL is stronger, straighter, and more uniform than traditional sawn timber. The phenomenon of shrinkage and swelling is hugely reduced, making for more dimensionally stable and accurate con-struction. Due to its composite nature and pre-graded veneers for stiffness, LVL is also much less likely to warp, twist or bow than tradition timber.
But why the emphasis on the use of hardwood as opposed to softwood LVL? Essentially this product has massive structural strength benefits compared to softwood glulam and delivers a more highly effi-cient yield from the log its veneers are sourced from than is possible in the manufacture of CLT and glulam. Because it can be produced in long sheets as well as beam and column form, its potential to be curved and twisted in two directions at once offers considerable design potential to conceive and construct building forms never previously possible with wood.
Some readers may not be aware of LVL projects in the UK, but there are some remarkable examples, not least the five-storey Black & White Building currently being completed in London’s Shoreditch area that is attracting considerable attention from commercial developers. Its prefabricated beech hardwood LVL post and beam structure supports a CLT core and slabs, but the apparent simplicity of this fully-engineered, precision-built timber construction belies its groundbreaking innovation. Sitting on a very tight site and erected at remarkable speed with no major plant and with practically no noise and no waste, its optimisation of material delivers a powerful sustainable agenda with only 410 kgCO2e/m2 embodied carbon (A1-A5).
The opportunities available with LVL lie not only in the creation of new building forms, but in LVL’s potential to for designers to rethink and reshape the way in which we build out towns and cities. Two of the world’s leading LVL manufacturers are busily exploring these possibilities: Metsä Wood and Stora Enso are not only talking the talk, but they are also walking the walk, the latter constructing its 'Wood City’ in Helsinki, the largest sustainable urban wooded district in Finland and a demonstration to the wider world of the efficiency and high quality that can be achieved with LVL.
For more information visit:
www.masstimberacademy.com
Images:
01. The Black & White Building has a prefabricated beech hardwood LVL post and beam structure supporting a CLT core. Courtesy Waugh
Thistleton
CASE STUDY LUXURY LIVING WITH STEEL FRAME
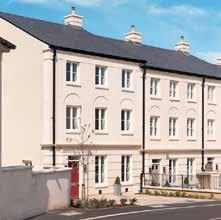
Located in Bath, Holburne Park is an ambitious £26million high-end development where Fusion Steel Framing was proud to contribute to the successful delivery of with 198 residences.
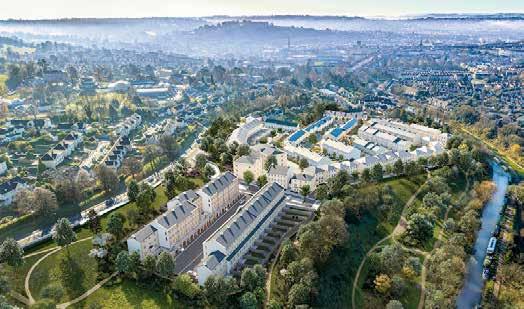
The project was rolled out over a three-phase construction period, with Fusion Steel Framing delivering the cold-rolled light steel framing system for the site. The Fusion team worked collaboratively with project leads and site teams to ensure they met specific requirements for each phase for each unit. The Fusion light steel systems offered the benefit of complete control over design, allowing the provision of accurate cost, time and delivery calculations from start to finish.
Construction offsite allowed faster production and reduced turnaround times while BOPAS-accredited steel framing systems developed based on the principles of adding value by embracing a Design for Manufacture and Assembly (DfMA) approach. Manufacturing components offsite reduced overall project costs and offered faster production times, reducing time spent on-site.
Fusion Steel Framing BIM processes, alongside activity models, were able to accurately predict, assess, and negate potential risks, ensuring buildings remained in keeping with the classical architecture of the area and providing high standards of structural integrity and performance. By utilising offsite factory facilities, Fusion manufactured all individual components to the exact quantities required; meaning the amount of waste generated in the production and onsite was extremely low.
1
Utilising the Fusion steel frame system in the superstructure for the Holburne Park buildings allows the site to benefit from reduced embodied carbon in building fabric. Not only this, but this system offers enhanced occupant safety. Fusion systems, when combined with ancillary light gauge steel products, result in exceptional fire safety performance which, depending on the components used with the steel frame, can provide fire resistance at 60, 90, and 120 minutes. The project, which includes a mix of three and four-bedroom houses and five-bedroom luxury villas, utilised precision engineering, delivered through a five-step digitally enabled process, with all elements tried, tested, and approved before use. The delivery system was planned to minimise the number of vehicles required, with storage for optimising human resources, and transport organised to mirror the build process for more efficient just-in-time installation. All of which contributed significantly to improving health and safety onsite.
2
Holburne Park offers a notable showcase of collaborative construction practises, with the Fusion team working alongside lead developers and lead construction contractor Bect, to ensure each stage of planning and delivery worked to promote site safety, best practice, and material optimisation. The project was approached with high respect for the integrity of the surrounding natural area.
Steel offers up to a 70% reduction in weight load comparatively to concrete and block work, resulting in reducing the environmental impact on the ground, and embodied carbon in building fabric can be reduced by as much as 20%. In-house design and engineering teams were able to work collaboratively with project partners and the client to ensure the project was delivered on time and to budget by adopting a just-in-time delivery protocol and using a BIM-based common data environment.
Holburne Park is the result of exceptional communication and planning across all stages of development, with the Fusion team offering full support and adaptability during planning, design, delivery, and installation to ensure bespoke requirements were successfully met.
For more information visit: www.fusionsteelframing.co.uk
Images:
01-02. The Fusion light steel systems offered the benefit of complete control over design, allowing the provision of accurate cost, time and delivery calculations from start to finish
ALWAYS KEEPING QUALITY HIGH
Developers are under increased pressure to construct safer buildings on fast-track schedules whilst still achieving outstanding building performance. Here Steve Thompson, Managing Director of EOS Framing, stresses the importance of delivering complete and compliant systems.
We take our responsibilities as a manufacturer extremely seriously. Our light steel frame systems are rigorously tested, manufactured under ISO 9001:2015 quality management standards and are now backed by Buildoffsite Property Assurance Scheme (BOPAS) Accreditation. Our aim is to deliver confidence and certainty in the construction process and empower specifiers to be technical forerunners in the offsite sector.
Against a backdrop of government targets to build 300,000 homes a year combined with increasing construction costs and poor quality conventionally constructed houses as well as a huge shortfall in traditional skills – the demand for innovative offsite construction methods has never been greater.
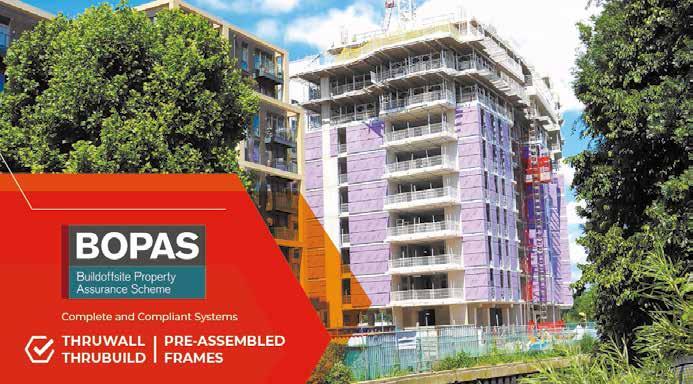
BOPAS Accreditation is recognised by principal lenders as providing the necessary assurance underpinned by a warranty provision that residential properties will be readily mortgageable for at least 60 years.
Pioneering a Certified Systems Approach
For funders and lenders BOPAS provides assurances that our light steel systems are fit for purpose and eliminates the uncertainty surrounding the construction for valuation purposes. It also removes the risk for developers of mortgages being declined on construction grounds. BOPAS demonstrates to funders,
1
lenders, valuers and purchasers that homes built from non-traditional methods will be durable, delivered to high quality standards and stand the test of time.
Specialising in advanced light steel framing technologies, the team at EOS are taking the construction industry forward by pioneering a new certified systems approach, helping specifiers to comply and compete in challenging markets. We are committed to technical competence and as part of Etex, have some of the best building performance experts in the UK on our team. They work closely with certification bodies to jointly design and develop advanced technical solutions.
We are continually looking at ways to make the building process not only inherently safer but also to offer performance assurances to residential developers to ensure they can provide sufficient levels of protection to residents. Improving levels of occupants’ safety, and increasing the quality of the build, is our primary objective. Our research and perspective interviews with sector experts have equipped us with a deep understanding of the challenges faced by housing specifiers. Lack of performance testing is a major concern.
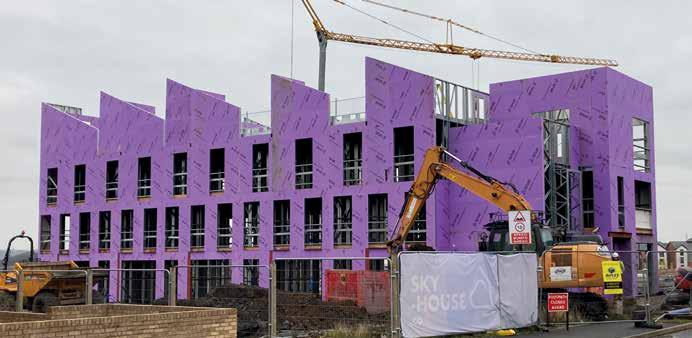
Fire protection for light steel framing is typically provided by the use of non-combustible boards for internal linings and fire protection systems such as those manufactured by our Etex group partners – passive fire protection specialists, Promat and FSi who develop and manufacture a full range of built-in fire protection systems to protect infrastructure and assets.
Backed by Robust Testing and BOPAS Accreditation
We have invested in research and testing to bring a new safety-first systems approach to the offsite sector. EOS can now help specifiers reduce risk and operate with more certainty by verifying and certifying our systems performance.
Through the collaborative expertise of Etex brands EOS Framing, Siniat, Promat and FSi, our light steel non-combustible systems are helping construction clients comply and compete in challenging markets. Our full-scale testing regimes study the performance of products working together to establish how they interact in ‘real’ circumstances, such as fire conditions or when exposed to wind and rain.
Our range of Thrubuild®, Thruwall® and Pre-Assembled Frames (PAF) have been developed to eliminate uncertainty surrounding the design and specification of the external envelope. All components and products in the systems have been rigorously tested together for fire, acoustic, weathering, airtightness, durability and mechanical performance. Fire resistance periods of 60, 90 and 120 minutes are achievable.
2
Our Thrubuild® loadbearing and Thruwall® non-loadbearing range is supplied as a tried and tested customdesigned kit of parts integrating steel framing, external Siniat Weather Defence sheathing, Siniat internal drylining, ancillary parts, fixtures and fittings. Providing crucial safety, time and cost benefits, Thrubuild® has multiple loadbearing applications and can be used for external or internal walls together with internal and separating floors. Thruwall® is a fully engineered custom-designed nonloadbearing infill system manufactured offsite and supplied as a complete certified kit of parts that can be used with concrete and steel main frames. Following the success of Thruwall® – EOS has taken factory manufacturing to another level. Our Pre-Assembled Frames (PAF) are prefabricated and preassembled offsite, these nonloadbearing infill systems are delivered to site as an assembled panelised unit. Backed by rigorous testing and now BOPAS Accreditation, our Thrubuild®, Thruwall® and PAF systems get the safety and building performance balance right through the combination of light steel framing, external sheathing, internal wall linings and glass mineral wool insulation – only tested configurations are available.
By working closely with specifiers EOS is now able to deliver precisionengineered solutions with assured performance which can be produced at scale better than, faster than and more cost-efficiently than other market offerings. When Thrubuild®, Thruwall® and PAF systems are built with Etex Group components and materials, following a validation process — Etex award a 30-year warranty.
For more information visit:
www.eosframing.co.uk
Images:
01. The final phase of Riverside Quarter is the first development in the UK to specify
Pre-Assembled Frames (PAF) 02. Sky House integrates Thrubuild® walling and flooring solutions providing performance guarantees and fire resistance of 60 – 120 minutes