
4 minute read
Building in a Meaningful Way
Naomi Pratt, Consultant at the Supply Chain Sustainability School (SCSS), discusses its upcoming report which will help organisations across the value chain maximise social value outcomes through offsite construction.
Social value has become a mainstream concept across the built environment sector. Having entered the policy landscape in 2012, it’s now mandated with a minimum 10% weighting as a consideration in central government contracts under procurement notice PPN 06/20 and is commonly included as a requirement in tenders in the private sphere. Despite this, there remains a lack of practical guidance around how to understand and communicate the additional social value benefits of the offsite construction process. Within the Offsite Leadership Group of the School, which includes 30 industry partners working in the sector, there was a strong desire for social value to be a key topic of focus this year. With the support of consultants Akerlof and researchers at the University of Salford, we felt well placed to pull together perspectives and best practice.
So over the past few months, we’ve been carrying out desk-based research, gathering experiences through workshops and conducting interviews with organisations ranging from designers to manufacturers and contractors. This work has brought to light some fantastic projects demonstrating evidence of social value benefits and highlighted common challenges for the sector.
The report, due to be published in September, will highlight the opportunities offsite construction can bring across the suite of social value themes, as well as identifying perceived tensions, primarily the focus on social value near to site rather than elsewhere in the value chain. It is important to remember that most construction projects have an inherent level of social value whatever the building process used. For example, building a hospital brings inherent social value to the local community regardless of its build type. Therefore, our report focuses on the additionality of social value that the offsite process brings. We hope the guidance will give clients more confidence offsite can meet their ambitions and inspire supply chain organisations to achieve better outcomes for people and planet.
Providing new jobs local to site, especially apprenticeships, was cited as a common client request and a challenge for offsite providers to achieve in comparison to traditional models. But this is a narrow view which can miss genuine social benefits of a contract – including the site of manufacture is necessary to understand the full social value impact and helpfully is not precluded by legislation. This isn’t just a workaround – our research reveals that offsite manufacturers can provide a safer and less transient working life for people in the sector, as well as creating a lower barrier to entry in the assembly phase of the project, which can give greater agency and involvement to local
1
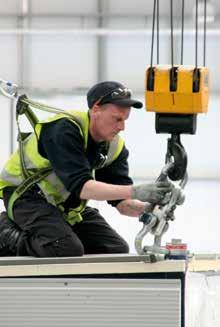
2
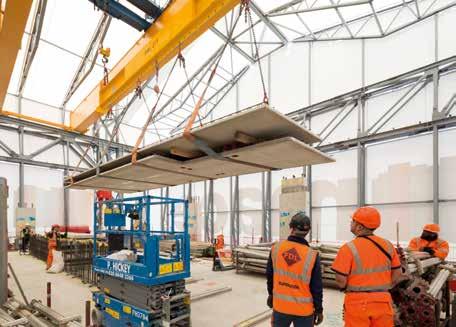
communities and occupants of the building and smooth the journey into the sector for new starters.
The environmental case for offsite is also growing, with a number of studies demonstrating reduced greenhouse gas emissions and greater resource efficiency compared to traditional construction. This is the case across the construction lifecycle, resulting from shorter times onsite, fewer vehicle movements, lower-carbon materials, and improved in-use performance.
For more information visit:
www.supplychainschool.co.uk
Images:
01. Naomi Pratt, Consultant, Supply Chain Sustainability School 02-03. Social value is a key aspect of offsite construction and a better placemaking approach
3
More highlights and findings from the report will be presented at OFFSITE EXPO from 16.00-16.45 on 20 September in the Spotlight on Offsite Theatre, so make sure you register for your free place. The
Supply Chain Sustainability School
will also be exhibiting at Stand G15 throughout the Expo.
DIVERSITY & THE SUSTAINABILITY TOOL
The Sustainability Tool – a software application designed to help organisations and their supply chains measure and monitor their sustainability performance – has launched the 2022 employee diversity benchmarking survey. The annual employee diversity benchmarking exercise, carried out within the Sustainability Tool, is a collaborative effort to better understand and improve the diversity of the built environment industry.
Between July and September 2022, organisations are invited to anonymously report their diversity data within the Tool, with categories including Gender, Age, Religion & Belief, Ethnicity, Sexual Orientation, Disability, Voluntary Leavers, Part-Time Status, and Attraction & Recruitment. Each category informs subsequent indicators that align with the ONS’ standard of diversity data collection.
Suppliers with over 250 employees will be automatically directed to complete a more detailed submission, while those with less than 250 employees can complete a ‘Lite’ version – encouraging smaller SME and Tier 2 business engagement. Respondents will gain free access to in-depth and interactive dashboards that they can use to benchmark their diversity data against their sector, industry and the ONS data set.
Client and contractor organisations can also use the exercise to collect and benchmark diversity data from their supply chains. While the exercise is live, the Supply Chain Sustainability School will be running free online webinars to support organisations with completing the survey. Last year’s survey collected data from over 250,000 employees across 88 supply chains, making it the largestever UK data survey on employee diversity.
Ian Heptonstall, Director of Supply Chain Sustainability School (and owner of the Sustainability Tool), said: “Last year’s survey was the largest and most comprehensive to date with over 250,000 people included. It provided us with important insights into ‘what good looks like’ and where we can take action to make improvements. I’m delighted therefore that this year we’ll be expanding to other sectors and organisations, as the more information we have, the better our decision-making can be.”