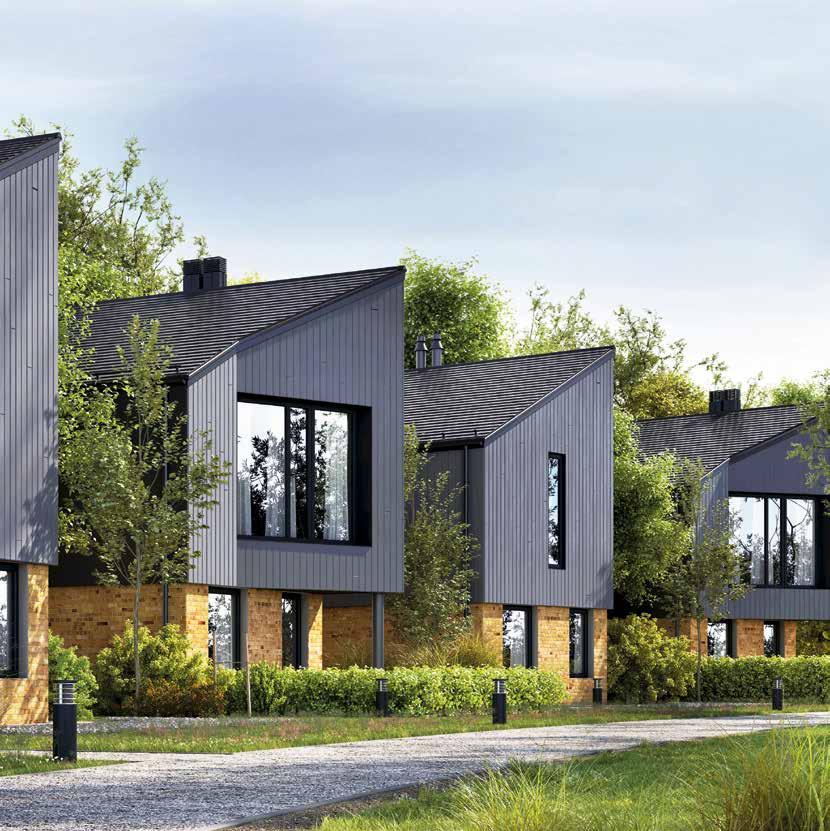
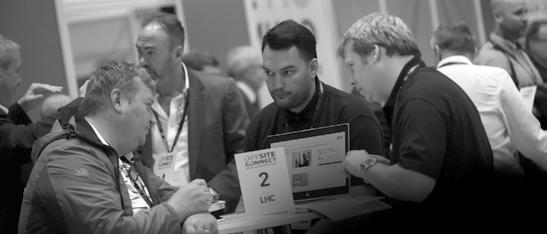
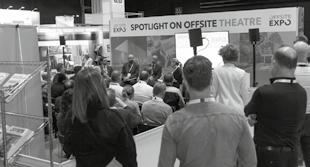
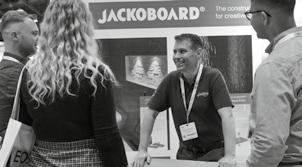
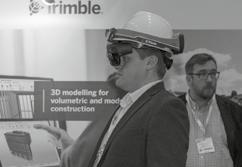
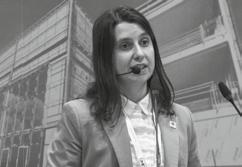
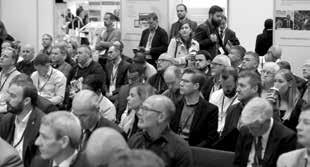
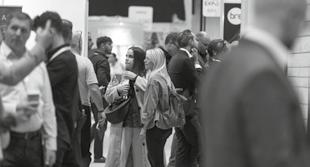
FRONT COVER OSHA
PRINTED ON: FSC Mix paper by Buxton Press
PUBLISHER:
Offsite Magazine is produced and published by Radar Communications: ©Radar Communications Ltd.
Radar Communications Ltd, 101 Longden Road, Shrewsbury, Shropshire, SY3 9PS
T: 01743 290001 www.radar-communications.co.uk
SUBSCRIBE TO RECEIVE OFFSITE:
This magazine is a bimonthly publication and the annual subscription fee for UK postage is £29.70 plus VAT for all six issues (£4.95 per copy). Visit www.offsitemagazine.co.uk
ADVERTISING ENQUIRIES PLEASE CONTACT: Julie Williams // T: 01743 290001
E: julie.williams@offsitemagazine.co.uk
SEND US YOUR NEWS: Gary Ramsay // T: 01743 290001
E: gary.ramsay@offsitemagazine.co.uk
BACK ISSUES VISIT: www.offsitemagazine.co.uk
FOR OFFSITE ENQUIRIES PLEASE CONTACT: E: info@offsitemagazine.co.uk
DISCLAIMER: The content of Offsite Magazine does not necessarily reflect the views of the editor or publishers and are the views of its contributors and advertisers. The digital edition may include hyperlinks to third-party content, advertising, or websites, provided for the sake of convenience and interest. The publishers accept no legal responsibility for loss arising from information in this publication and do not endorse any advertising or products available from external sources. The publisher does not accept any liability of any loss arising from the late appearance or non-publication of any advertisement. Content including images and illustrations supplied by third parties are accepted in good faith and the publishers expect third parties to have obtained appropriate permissions, consents, licences or otherwise. The publisher does not accept any liability or any loss arising in the absence of these permissions for material used in both physical and digital editions. No part of this publication may be reproduced or stored in a retrieval system without the written consent of the publishers. All rights reserved.
Welcome to the latest edition of Offsite Magazine. As 2022 ends after a chaotic political autumn, hopefully the new year will see the UK and wider global economic and financial outlook improve and provide muchneeded business stability.
Housing is never a subject far away from construction discussions. As we went to press the Conservative’s Levelling Up and Regeneration Bill pledge to build the oft-quoted target of 300,000 homes a year was effectively kicked into the long grass. The fear is that the reduction of this target – in yet more internecine pressure from within the Government’s own ranks – will lead to even less housing stock available for those wishing to step onto the housing ladder. All of this across the backdrop of the ongoing energy and cost of living crisis.
Certainly, the supply of affordable housing is not sufficient to meet the current housing demand – or even a reduced one – but as the Off-Site Homes Alliance (OSHA) outlines inside, offsite methods does solve many problems. OSHA currently consists of 23 registered housing providers, with strategic aims to grow its offsite housing portfolio using both panelised and volumetric modular technologies.
We spoke to Project Director, Mike Ormesher about progress on how this pioneering collaborative group is offering housing providers invaluable ways to deliver sustainable and vibrant new communities.
Away from housing there is plenty on offer across this last edition of the year, including several winners from the recent Offsite Awards 2022 plus Tony Jones, Technical Director at The Concrete Centre, points out some of the benefits of using precast concrete and explains how the material is working hard to be as carbon friendly and user-friendly as it can be. On top of that we report from one of our recent factory tour events, that saw visitors spend time at the Kingspan manufacturing facility on the outskirts of Leeds, to see what makes the TEK® Building System so successful. This advanced SIP system is central to Kingspan’s long-term ‘planet passionate’ 10-year plan, that will see them hopefully reach carbon zero by 2030.
A final thanks to all our contributors, advertisers and supporters for your help and support throughout 2022. Enjoy the festive break and see you in 2023.
Gary Ramsay Consultant EditorEmail: gary.ramsay@offsitemagazine.co.uk
The Brooklyn cubicle from Kinedo is the simple way to bring industrial chic into any bathroom.
Its striking looks, with black or grey finishes, combine with speed of installation to offer a high quality, self-contained solution that includes the cubicle, internal panels, tray, shower valve, head and handheld shower.
The Kinedo team works with you to make sure a Kinedo cubicle is the perfect choice for your project. From site visits, installation training and technical assistance, our first-class aftercare supports a first-class product.
The Off-Site Homes Alliance (OSHA) currently consists of 23 registered housing providers, pooling talent and working collaboratively to deliver a new generation of quality, energy efficient affordable homes. We spoke to Project Director, Mike Ormesher about progress so far.
We caught up with Tony Jones, Technical Director at The Concrete Centre, to find out more about the benefits of using precast concrete, its important role in the wider offsite construction sector and the road to decarbonisation and sustainable materials.
30
The MODULHAUS™ technology is continuing to bring fresh housing solutions and is evolving to be ever more innovative, sustainable and energy efficient.
38
Colin Dalton, Co-Founder and Director at architectural practice Gray Design explains how offsite technology holds many keys to unlocking low-carbon construction for the social housing sector.
42 | Think Offsite from the Start
Offsite manufacturing has jumped to the forefront of many debates within the construction industry in recent years, as Ross Baxter, Managing Director of Saint-Gobain Off-Site Solutions points out.
46 | View from a Hill
Clifford’s Tower in York shows what an immense transformation can take place when modern offsite timber design breathes new life into an ancient and under-valued visitor attraction.
50 | Why Offsite Delivers More For Less
With thermal efficiency and a range of advanced insulation products on show, Kingspan recently hosted a special factory tour allowing visitors to learn more about their TEK® Building System and view their manufacturing facility on the outskirts of Leeds.
08 | Industry News
News and developments from across the UK offsite industry and wider construction arena including: BE-ST unveil a new design guide to affordable housing, Bouygues UK completes a landmark modular project, the Construction Innovation Hub published its Product Platform Rulebook plus the Future Homes Hub appoints Barratt Chief Executive as its inaugural chair.
With a mission is to revolutionise construction and change the way houses are designed, manufactured, procured and built. COLAB and its DfMA Toolkit is providing several answers to the UK’s housing crisis to award-winning effect.
28 | Healthcare Priorities
Identifying a route to net zero emissions for the NHS is challenging. Richard Hipkiss, Development Director of the Modular and Portable Building Association, discusses how volumetric technology can help support the healthcare sector and produce energy efficient buildings.
52
James Withey, Managing Director at Algeco Offsite Solutions, examines the role offsite manufacturing could play in offsetting Governments investment cuts and keeping UK construction on track.
On behalf of Seismic Group, Richard Crosby explains how a platform approach and offsite technology can play a central part in disrupting construction industry practices and processes.
66
The award-winning MFS i-Form Solution™ is helping drive forward the concept of P-DfMA for offsite manufacture and building design.
68
As Alex Micallef, UK General Manager at Graitec explains, the take-up of digital technology must accelerate if offsite methods are to move mainstream.
The Off-Site Homes Alliance (OSHA) currently consists of 23 registered housing providers, pooling talent and working collaboratively to deliver a new generation of quality, energy efficient affordable homes. We spoke to Project Director, Mike Ormesher about progress so far.
and local authorities for its pioneering collaboration and the ways it is bringing together like-minded organisations to drive demand for offsite technology and factorymanufactured homes. “The efficiency of factory production lines in any manufacturing industry, relies heavily on a consistent flow of production throughput,” says Mike. “Preferably with the least number of disruptive changes to the product specification. Offsite manufacture requires a very well organised DfMA approach, and it is essential that demand throughput is maintained to keep the factory financially sustainable.
installation of quality homes rather than volume chasing, across many pilot schemes, with numerous clients offering differing (non-standardised) designs.”
At the start of the OSHA programme in October 2020, the ability to deliver an offsite procurement strategy, with as much control and level of expert support for each individual registered provider and local authority, was seen as highly unlikely. But as Mike points out, with a slogan and mantra of ‘better together than we can be alone’ this is changing mindsets.
OSHA and its supporting partners have a clear strategy to grow its offsite housing portfolio using both panelised and volumetric modular technologies. OSHA is made up of a steering committee and focused working groups seeking to engage with the Design for Manufacture and Assembly (DfMA) process – not only to aggregate demand – but to create supply chain efficiency, minimise risk and offer maximum opportunities for housing providers to deliver the lasting change affordable housing needs.
The organisation is attracting huge interest amongst housing associations
“This is a complex process, which requires great skill and robust management. The pressures that manufacturers have with design changes, varying site conditions, access to complex and tight building sites and a stop-start demand activity, are often a consequence of clients wanting to trial different technologies on pilot schemes. Although highly practical from a client perspective, pilot schemes significantly affect the efficiencies of offsite factories, especially in Category 1 volumetric module production.
“At OSHA, we have designed many processes and tools to improve this situation. With our growing client base, we have a pipeline of aggregated demand (from circa 10,000 homes per annum, which is the average number of homes built per annum by the existing 23 partners, ready to be converted into more advanced CAT 1 & CAT 2 MMC technologies) that will allow a consistent flow of production through many factories, allowing manufacturers and their management teams to fully focus on production and
“The speed of delivery, long term quality, and performance assurance for the current and future affordable homes for residents is a major driver for industry-wide collaboration,” says Mike. “Registered providers and local authorities require a sustainable and robust asset that stands the test of time and that can stand up to rigorous in-situ performance testing. This must ensure zero defects and a significant reduction in energy bills and carbon emissions. Zero energy bills and zero operational carbon are our immediate target with reducing embodied carbon to zero, also a longer-term aim.
OSHA has been developing a strategic toolbox of support via several offsite experts and a dedicated project director, to ensure the delivery of long term ‘best in class’ living conditions for residents. “Everything we do at OSHA is aimed at best-in-class delivery,” says Mike “This required a systematic approach to housing procurement from the offsite sector and not just the USP of aggregated demand. The now well-established toolbox and newly badged ‘OSHA eco-system’
will support the effective delivery of offsite homes. We have confirmed the launch of our national £2billion (four year) MMC framework for early January 2023, with a significant supply chain (CAT 1 and CAT 2) to deliver our needs, and to drive up performance, whilst driving down unnecessary costs, below that of traditional construction practices.”
Working with architects, MEP designers, structural engineers, offsite manufacturers and OSHA’s own in-house experts, it has created its own design pattern and zero carbon playbook, but what does this do and how is the overall DfMA approach helping deliver the much-needed new generation of energy efficient housing types?
“This significant and highly resourced asset provides a large range of house types with a controlled DfMA approach,” says Mike. “This allows a more efficient production process and a better-quality finish due to consistency of design and supervision in the factory environment. The zero-carbon strategy is fully aligned to those home designs (currently 13 options) which means we can monitor the performance of a controlled set of designs, rather than procuring from a vast range of suppliers with varying technologies and with multiple design strategies.
“While the pattern book fits very easily into a CAT 2 panelised approach, we are aware that for CAT 1 volumetric delivery, this will take a bit more time to deliver. With the aggregated demand from many client partners, and a controlled logistics process for varying sites (not affecting the supply partners), we aim to get to an OSHA branded volumetric home very quickly, giving assurance of delivery, with assurance of design and performance management through ongoing site testing, via our Building Performance Evaluation (BPE) partners.”
Collaboration and a New Way of Working With a co-ordinated supply chain key to any construction project, OSHA is maximising collaborative effort to giving housing providers the best value for money with another important part of its toolbox being the creation of a Project Management Office (PMO), to sit alongside the
“Site evaluation, suitability of technology, KPI dashboarding, PMV assessments, regional cost analysis and MMC support is a fundamental part of the service that the OSHA PMO will deliver,” says Mike. “There is a plethora of support services that the OSHA partners can choose from, as part of their extremely competitive framework fee, and this will be left to the partners to decide how they use the time available from the PMO. Some will require significant support, and some will only require specific technical or forensic support, depending on the size of their in-house teams and offsite experience. However, the framework, pattern book, and PMO are still only a selection of the support tools available to existing partners, and any new ones wishing to join OSHA.”
OSHA have now completed several research projects to underpin its strategy, all collectively developed into strong reports and business cases, and they have now completed the development phase of the programme. With the framework going
live in early January 2023, what are the next steps for OSHA in what will be an exciting and busy 2023? “We are fully focused on deploying the high-quality affordable homes we envisaged back in October 2020,” says Mike. “On top of that deployment focus, we have several initiatives currently under review including a strategic partner manufacturing hub and a performance centre for R&D, plus a range of other support services.
“The biggest driver for us is to ensure we keep the movement developing. Any new public sector partners, who are looking to start their offsite and zero carbon delivery programmes, should really consider joining our public sector colleagues that have pioneered and paved the way on this journey. Remember, ‘better together than we can be alone’ is central to the OSHA philosophy and the stronger we are, the more efficient and capable our partners become.”
For more information visit: www.offsiteha.org
Images: 01. OSHA is driving change through offsite manufacture and DfMA 02-03. Success for registered providers and local authorities is coming from expert support networks and collaborative working
make the transition as it builds zero carbon, nature positive homes and places. The benefits are not just environmental: energy efficient, nature friendly new homes are places where people aspire to live and will ultimately be more affordable to run over the long-term.
David Thomas (pictured) the Chief Executive at Barratt Developments PLC, has been appointed as the inaugural chair of the Future Homes Hub. The Future Homes Hub is a new and independent organisation bringing the homebuilding industry together, to accelerate and deliver an effective transition to building high-quality zero carbon and sustainable homes at scale.
On taking up the role as Chairman of the Future Homes Hub Board, David said: “The Hub has a pivotal role to play in building a sustainable future, and housing will be the one of the first sectors of the economy to
Work is well underway on-site at Little Ilford secondary school in Newham, London where offsite specialist contractor M-AR is currently working on one of its largest education projects to date.
The London Borough of Newham has experienced rapid population growth over the last ten years meaning that demand for secondary school places within Newham is forecasted to increase significantly over the next five years. Little Ilford School therefore needed to be able to accommodate a larger intake of students in the very near future, so a large new block with more facilities has been designed to sit adjacent to the existing school building within its grounds. It is being built using a hybrid offsite approach with M-AR playing a key role in its delivery.
The large new block, which will soon be complete and ready for teachers and students to move into, includes several new classrooms and connecting corridors, a SEND block, an activity studio and a new underground car park area complete with several electric car charging points and PV panels. There was no room to extend the footprint of the site itself meaning that the new block had to take up part of the school’s existing car park, and with parking at a premium in the area, this had to be maintained which meant sinking the carpark underground and building the new school block built directly above
“However, to succeed we need to fill the gaps in the roadmap, as well as developing the practical tools, skills and technological innovations. Crucially, we must also bring our customers with us on the journey. A smooth and effective transition to net zero cannot be achieved by individual organisations alone. The whole sector, from product manufacturers, utility companies, environmental bodies, housebuilders large and small and government, will have to work collectively. I am delighted to become the chair of the Future Homes Hub at this critical time, to help bring industry and government together as we work towards building a sustainable future.”
The Hub was set up in November 2021 by the housebuilding industry in collaboration with the Department for Levelling up, Housing and Communities, the Department for Environment Food and Rural Affairs, the Department for Businesses Enterprise and Industrial Strategy and Homes England to build the partnerships needed to meet environmental goals. The purpose of the Hub is to deliver the Future Homes Delivery Plan, first published in July 2021, which sets out the sector’s climate and environmental roadmap.
Ed Lockhart, CEO of the Hub, said: “There are over 2,000 homebuilders in this country that all face the same set of challenges to build zero carbon and sustainable homes fit for the 21st century. The Hub is the central place to bring together expertise and experience, working out the solutions once and sharing them across the sector. It is an enormous boost that David is giving his and Barratt’s backing alongside leaders from across the sector, to drive forward a new generation of high-quality sustainable homes. There is a spirit of collaboration across companies of all sizes that makes this a really exciting time to be working in the sector.
“Over forty homebuilders who deliver most of the country’s homes - ranging from major homebuilders to pioneering SMEs – have joined the Hub so far, with more quickly coming on board. Along with organisations representing partner sectors, they are committed to working together on the roadmap to achieve the change required as seamlessly as possible.”
The purpose of the Future Homes Hub is to facilitate collaboration across the new homes sector to meet climate and environmental goals, in line with the Future Homes Delivery Plan which was put together by the Future Homes Task Force.
Source: www.futurehomes.org.uk www.barrattdevelopments.co.uk
As this is an extension project, the school remained open throughout the project, so it was vital to keep disruption to a minimum and follow strict safeguarding regulations to keep everyone safe. Taking a proportion of the build offsite and into M-AR’s factory reduced both the time spent on site and the sheer number of tradespeople required on-site at any one time too.
Ryan Geldard, Director at M-AR said: “This is our largest education project to date and has not been without its challenges due to the constraints of the site and surrounding areas. But by taking a collaborative approach with everyone involved we’ve been able to meet the challenges safely and efficiently head on by developing each separate module for ease of manufacture, delivery and installation from the outset. It’s great to see the new school block taking shape
and we’re looking forward to seeing the staff and students making the most of their new space once the project completes.”
M-AR also recently completed the purchase of its existing manufacturing facility in Hull, further strengthening its position and ensuring it can keep pace with current demand as well as preparing for future growth in the offsite construction sector. The move from leased to purchased facilities, as well as bolstering its asset book, gives M-AR total control over its premises enabling the team to make any necessary adjustments to the layout to better suit its processes and marks M-AR’s commitment to its home city of Hull.
Source: www.m-ar.co.uk
A new catalogue of net zero carbon building designs could provide a significant boost to Scotland’s affordable housing sector, as part of a standardised approach for local authorities and housing associations to adopt across a range of future developments.
The energy-efficient design and performance standards have been created by the Edinburgh Home Demonstrator (EHD) programme. The catalogue covers different housing typologies, such as flats, houses and cottage flats, which combine fabricfirst energy efficient standards, renewable energy technology, and modern methods of construction –also known as offsite manufacturing.
The £1million EHD programme – involving partners from the City of Edinburgh Council, Offsite Solutions Scotland, Edinburgh Napier University, the University of Edinburgh, Built Environment – Smarter Transformation (BE-ST) and Scottish Futures Trust – is trialling the new approach for high-performing affordable homes.
The first pilot project of the EHD in Granton includes the creation of 75 net zero carbon ready one, two and three-bed flats being constructed by offsite construction specialists, CCG (Scotland), and is funded by the Scottish Government’s Affordable Housing Supply Programme and the City of Edinburgh Council. The first homes designed using the performance standard are expected to
be completed in the summer of 2023 and once occupied, will be monitored to test the approach in the guide.
With the new design and performance standards, the programme hopes to inform new build developments across the Edinburgh and South East Scotland City Region Deal, providing a route map to net zero carbon homes that utilise offsite manufacturing. While the guide recommends common parts, including floorplans and zero gas heating systems, elements such as the external materials and appearance of homes can be customised to ensure buildings remain in keeping with local surroundings.
Ainslie McLaughin, Chair of the Edinburgh Home Demonstrator Programme Project Board, said: “Our ambition is to reduce the carbon footprint of the housing sector by designing new homes that ultimately consume less energy. Affordable housing plays a significant role among many communities and we want to create homes that are better suited for future generations. The flats we are delivering in Granton will be highly energy efficient and will also encourage residents to make low carbon lifestyle choices in relation to services like transport and travel.
“A key output of the pilot project is the evidence we will collect on the performance of the homes. Not only will it inform the next stages of building work here in Edinburgh and the City Deal but it could also influence future designs and procurement practices across all of Scotland’s affordable housing.”
Sam Hart, Head of Modern Methods of Construction at BE-ST, said: “We are facing a climate emergency and need to rapidly transform all aspects of the built environment to reduce its carbon footprint. Compared to carrying out the majority of works on site, offsite manufacturing is proven to be more accurate and more efficient, while also reducing waste. This programme is helping to provide local authorities and developers with information about what zero carbon looks like in practice, as well as building evidence to support offsite specialists and other supply chain partners.”
Nicola Jackson, Chair of Offsite Solutions Scotland, added: “With advancing building performance requirements and increasing levels of technology required to be integrated in new homes to improve operational performance, we can better assure this is delivered through manufacturing homes in a controlled, dry factory environment to improve build quality. Offsite Solutions Scotland members have come together as a network of leading offsite timber manufacturing companies to deliver pilot projects as part of the Edinburgh Home Demonstrator programme. This will support the development of a new delivery model for net zero affordable homes using offsite manufacturing.”
Source: www.be-st.build
Our OJEU-compliant framework agreements provide public sector organisations with easy access to procure works, products and services for the construction, refurbishment and maintenance of social housing, schools and public buildings.
LHC strives for excellence in the services provided to their clients and aims to deliver the best solution to suit every project’s individual needs.
Our dedicated Client Support and Project Support teams are on-hand to assist throughout the life of the project. For more information on how our frameworks can work for you, get in touch.
The Construction Innovation Hub recently published the first edition Product Platform Rulebook. Following consultation with over 200 industry and government stakeholders, the Rulebook has been updated to deliver a clear path to deploying a platform approach to construction.
The Product Platform Rulebook is an open-access guide designed to support industry – clients, consultants, contractors, manufacturers and product suppliers – in building capability and capacity to develop and deploy product platforms to meet demand. It is an important tool that will drive greater productivity in construction, supporting the development of new skills, new ways of working and collaboration, both across and within organisations.
Following the release of the beta edition, the Hub conducted an extensive consultation with industry and government stakeholders. Taking this feedback, the authors made several important edits and additions. These include the addition of an eighth Rule for Circularity, additional guidance on intellectual property and liability in the context of the Demand, Develop, Deploy Product Platform Framework and enhancing the case studies to provide practical application of the defined product platform rules and models.
The Construction Innovation Hub’s continued focus will be on deployment – including embedding the Rulebook in platform construction and working with industry and government clients to move from concept to delivery.
Commenting on the publication, Hub Director Keith Waller said: “This is an important milestone for the Hub’s legacy to industry and government. The updated, improved Rulebook is a practical tool that will help deliver the schools, hospitals, homes and buildings of the future. It addresses the Government’s ambitions – set out in the Construction Playbook and TIP Roadmap – to accelerate the development and adoption of a platform approach – boosting productivity, innovation and quality and contributing
to economic growth. Our focus will now turn to deployment, taking the Rulebook and working with industry and government to embed it in projects.”
Construction Leadership Council co-chair Mark Reynolds added: “The publication of the Rulebook is another step forward in the work to transform our sector and ensure we are equipped to answer the increasingly complex challenges we face. The Rulebook will provide a vital route-map as we deploy and embed a platform approach for construction, ensuring clarity and a focus on real results for not just the construction sector, but society as a whole.”
Ben Carlisle, global practice leader for DfMA, Mott MacDonald said: “It is a pleasure to see today’s publication of the first edition of the Rulebook and to be part of the very welcome launch. The journey so far to create the Rulebook has been neither straight forward nor easy, but we have brought together individuals from across the sector, often from competing organisations, to collaborate on this vital work. This is a testament to our collective determination and commitment to addressing the challenges we face in our industry and indeed in society.
“Crucially, this is not the end of the journey. This Rulebook is an enabling and guiding tool for platform approaches but, to continue to drive transformation, we need to establish the commercial models, feedback mechanisms and increased application to allow product platform development and deployment to thrive. At Mott MacDonald, we have committed to this through the establishment of a dedicated practice team and a strategy to support our approach and meet the increasing demand we are seeing both in the UK and globally. I know we are joined by many of our clients, partners and competitors and I look forward to working with them towards delivering a better built environment for all.”
Source: www.constructioninnovationhub.org.uk
Turner & Townsend has appointed Dave Clowe as its new Head of Modern Methods of Construction (MMC), Real Estate. He will spearhead the development and expansion of Turner & Townsend’s MMC advisory service across cost management and project management, to provide clients with suitable MMC techniques that deliver higher quality projects more quickly, safely and cost-effectively than conventional, on-site construction.
A qualified architect with 35 years’ experience from project management through to development and construction, Dave’s background in MMC has included work across the educational, defence, residential and healthcare sectors. Previously, Dave designed the concept for the Department for Education Primary School Education Template Design and the pre-construction section of the Seismic platform. He joins the business from Blacc Ltd where he was Head of Design & Pre-construction and MMC/DfMA specialist.
Dave Clowe (pictured) said: “I am delighted to have joined Turner & Townsend’s Real Estate team, leading their work in MMC at a time when our industry is accelerating its move towards more sustainable and efficient methods of construction. This next chapter will build on 10 years of accumulated MMC expertise, combined with Turner & Townsend’s existing world-leading capabilities, to create an MMC advisory service that will help our clients make the best decisions for productive and sustainable development.”
Martin Sudweeks, Managing Director of Cost Management at Turner & Townsend, added: “Dave’s arrival to lead and build upon the MMC expertise within our advisory team marks the latest chapter for our business moving forward with construction techniques that boost sustainability and productivity. We have long been at the forefront of innovative, green, digitally enabled methods of delivering projects more efficiently. Adding further knowledge and experience to the team will only enhance this progress and help us to widen our MMC scope.” logies makes WGM an excellent fit for RSK family.”
Source: www.turnerandtownsend.com
Bouygues UK has completed its first ‘self-delivered’ modular project, successfully delivering 491 bedrooms of student accommodation at The Riverside, a mixeduse development in the historic City of Canterbury. Three of Bouygues Construction’s companies are part of the major urban regeneration project, Linkcity, the development partner of Canterbury City Council, Bouygues UK and Uliving – Linkcity’s dedicated student accommodation brand.
The 491-bedroom student accommodation scheme saw 430 modules built in a dedicated factory in Morocco and transported to the UK. A range of rooms have been delivered, from studios, ‘two-dios’, premium rooms and cluster rooms with an en-suite, while all rooms have access to the fitness studio, games area, roof terrace and courtyard as well as a study area and laundry.
Bouygues UK built a dedicated factory in Morocco to produce the student accommodation modules, which were then transported directly to the construction site in Canterbury for installation. This innovative process results in a shorter build time, less disturbance on-site, a reduction in risk and improved quality.
The Riverside sits at the centre of a new leisure quarter in Canterbury, with a new public square at its heart
and overlooking the River Stour that runs through the city centre. This leisure-led destination is anchored by a five-screen Curzon Cinema, as well as restaurants and bars wrapping around the new public square. In addition to the student accommodation, the wider development also delivers 189 new homes, all within a pedestrian friendly neighbourhood that knits into the existing community.
Rob Bradley, CEO of Bouygues UK, said: “As our first self-delivered modular project, completing the student accommodation at Canterbury Riverside is a really exciting milestone for us. The completed project is of the highest standard and showcases our ability to design, build and operate student accommodation. “Modern Methods of Construction (MMC) is a crucial part of the future for construction, and we have learned a tremendous amount from this scheme, which stands us in great stead for future modular projects. Its successful delivery is a result of great collaboration,
between Bouygues UK, Linkcity, Uliving, Canterbury City Council and our colleagues in Morocco, where we built a dedicated factory to manufacture the modules. We are looking forward to utilising these skills much more going forward.”
Canterbury City Council Cabinet Member for Place, Cllr Barbara Anne Flack, said: “For Canterbury, the epitome of a historic city, to become home to such modern buildings built in a cutting-edge and innovative way is something to be celebrated and sums up the kind of place this is. The fact this is part of a scheme that will revitalise a rundown but vitally important part of the city, provide the cinema and leisure facilities residents have been demanding for such a long time, create jobs and result in much-needed affordable housing is cause for a double celebration.”
Source: www.bouygues-uk.com
Global modular building specialist, Volumetric Building Companies (VBC), has announced ambitious plans to expand in the UK. VBC is on track to become a $1billion modular construction company over the next three years and is now targeting the UK build-to-rent, affordable housing, student accommodation, and hotel sectors. This follows VBC’s merger with Polish modular manufacturer Polcom earlier this year to extend its reach into Europe, and strategic acquisitions, which include the assets of the modular business Katerra, to facilitate efficient servicing of projects across the USA.
Led by Vaughan Buckley and headquartered in Philadelphia, VBC is one of the world’s largest modular businesses. It offers advanced steel-framed modular and innovative timber construction technologies. Both solutions are highly efficient, cost-effective and have significantly less environmental impact than in-situ construction.
With proven capabilities in the multi-occupancy residential and hotel sectors worldwide, VBC uses a technology-enabled design and engineering model and precision manufacturing to deliver higher quality, highly sustainable offsite building solutions which reduce build programmes by up to 50%. This approach is helping to address the chronic undersupply of housing globally.
Andy Smith, UK Director of VBC said: “Residential –both build-to-rent and affordable housing – is one of the fastest growing segments of the offsite sector, driven by the high cost of private rental, the lack of affordable housing, and changing demographics.
There is a critical need to increase the housing stock in high density urban areas and to radically improve the productivity of UK construction. We now have a dedicated management team in place in the UK and there are plans to have an offsite manufacturing facility for VBC here, in addition to our existing and extensive modular production resources in mainland Europe.
“Our aim in the next three years is to secure a strong order pipeline in our target sectors in the UK – student accommodation, build-to-rent, affordable housing, defence, custodial, and hotels – and to raise the profile of VBC here, ahead of our expansion into Western Europe. We are already in advanced discussions with a number of hotel groups, private developers, major contractors, and social housing providers.”
“VBC has the resource and proven expertise in the industrialisation of construction, using a Design for Manufacture and Assembly (DfMA) approach and data intelligence to drive continuous improvement.
We have dominated the hospitality and affordable housing spaces in other countries with our innovative timber volumetric and steel-framed offsite solutions. We also manufacture ‘components’ inhouse – such as bathrooms and cabinets for kitchens and bedrooms – giving us complete control and security of supply for fixtures, fittings and finishes from design to manufacture, installation and handover.”
Vaughan Buckley, CEO of VBC added: “VBC is set to become the leading provider of optimised, costeffective, sustainable solutions for modular buildings around the world. We have tremendous capabilities in the engineering and delivery of advanced modular solutions and buildings which are fully finished and even furnished offsite. Having technology-led production facilities on multiple continents, we are now well placed to drive change, transform construction, and address the housing crisis in the UK, Europe, US, and globally.”
Source: www.vbc.co
A brand new six-storey apartment block at the Abbey Wall development in Merton, South West London has been constructed over a third faster than traditional concrete methods, while mitigating on-site safety risks, thanks to a pre-manufactured steel framed system from Intrastack.
Constructed in just 25 weeks by RJB Interiors (RJB) for main developer, Indigo Scott, the mixed-use residential scheme comprises 66 apartments and a commercial unit to the ground floor. Due to the
six-storeys and composite concrete floor, a lighter, more versatile structure was required to support the construction. The developer opted for Intrastack’s light gauge steel system. Not only was it able to provide the right strength and weight-bearing capacity, but it also enabled the team to speed up the construction programme to deliver a quicker return-on-investment.
A typical concrete frame project of this size would likely run to a 30-week programme to install the frame, followed by a further 10 weeks of exterior
wall construction. In contrast, the Intrastack solution was installed fully in just 25 weeks. Critical to the project's success was the ability to manufacture the steel frame offsite, using a just-in-time approach to help improve build times and eliminate on-site fabrication. This process was carefully co-ordinated with planned delivery sequences to complement the build programme and ensure a seamless installation process.
Matthew Kirby, Commercial Director from RJB Interiors said: “We pride ourselves in delivering an efficient and cost-effective programme for our clients. The combination of the speed of construction on-site, alongside a high quality, durable end-product from Intrastack has enabled us to deliver an overall cost saving to our client. We spent approximately 15 weeks less on-site than would have been required with a concrete frame construction and this clearly translates into both labour and plant cost savings, estimated to be in the region of £60,000.
“Fabricating the panels offsite in a quality, processdriven manufacturing environment has helped to reduce health and safety concerns. With no cutting or fabrication required on-site, we were able to reduce site preliminaries and plant costs, with rapid construction of the primary structure, allowing us to commence on-site activities much earlier than with traditional construction. In particular, the offsite manufacturing techniques meant that waste was handled in a controlled environment, and we had confidence that any offcuts would be either reused or disposed of responsibly. This is a significant benefit on-site, and we estimate that waste was reduced by as much as 50%, plus the associated time of processing and managing waste disposals.
"Much of the build also took place during the winter months with exposure to the British weather. Concrete construction can be a lengthier process during the colder months, while we wait for the product to dry. The steel frame is less dependent on site and weather conditions during construction than traditional methods and has enabled a greater productivity rate on-site."
Intrastack has invested over a quarter of a million pounds on comprehensive system testing to ensure each suite of products meets all building performance requirements. By combining steel frame construction with a concrete floor, the buildings acoustic performance is enhanced, and the tested fire performance offers 120 minutes of protection.
Matthew Grant, Technical Product Manager from Intrastack added: “We offer a complete ‘through the wall’ offer, comprising the internal and external boards, composite concrete floors, and insulation. From the initial concept drawings, we have worked with RJB and Indigo Scott to construct a durable, high performance steel frame system that would meet their needs for speed of construction, improved on-site safety and a reduction in build costs."
Source: www.intrastack.co.uk
Accsys, the manufacturer of Accoya wood, has successfully expanded production capacity at its facilities in Arnhem, the Netherlands. The first commercial batch of Accoya wood has been produced from its new, fourth acetylation chamber.
Accsys has invested over €30million in expanding the Arnhem site, including improving the wood handling for the whole site. The new acetylation chamber, which weighs in at 65 tonnes and over 14m long, increases the production capacity at Arnhem by a third, up from 60,000m3 to 80,000m3 (25.4 to 34.0 million board feet) a year.
In addition to the new acetylation chamber, Accsys has also invested in developing the Arnhem plant’s facilities. The improvements include new capabilities to support safe and rapid handling and logistics of the increased volumes of wood and a new quality monitoring and assurance technology with cameras, infrared scattering and x-rays to examine every board to ensure customer satisfaction with the products. A new 20,000m2 (200,000sq ft) warehouse opened in October at Hoevers, which will provide 35,000m3 of raw material storage close to the Arnhem site.
Rob Harris, CEO Accsys commented: “The world urgently needs solutions for sustainable construction.
Durable, sustainable, and with incredibly high performance, Accoya is in high demand – and we’re working as hard as we can to produce much more of it. We have earned a loyal customer base and our priority is to deliver more of what they need.
Our expansion at Arnhem is a significant step in the right direction of getting more Accoya out to the market. It’s part of our ambitious growth plan to expand production and fulfil our purpose of changing wood to change the world.”
John Alexander, Group Sales Director, Accsys: “Reduced output from the Accoya facility in Arnhem
over the past 12 months due to the engineering work on site for the 33% capacity expansion has created some challenges for our customers. We now have the benefit from that work addressing the demand and significantly increasing supply to our distributors. As we look ahead to early 2024, having two world scale facilities for production of Accoya provides for continued market growth and increased resilience of supply.” Accoya wood has been on the market since 2007 and is now sold by stocking distributors in more than 35 countries.
Source: www.accsysplc.com
Across Europe and worldwide, BeA’s fastening technology, tools and consumables are the trusted choice for some of the biggest and best known names in timber frame and offsite construction.
• An unrivalled range of manual and semi-automatic fastening solutions combined with a fully automated range in Autotec.
• I ndustry leading quality controls, BeA meet or exceed standards such as Eurocode 5.
Reliable products, competitive prices and the kind of service and delivery you can depend on from BeA.
BeA manufacture an extensive range of market leading fasteners, nails, staples and tools. We offer customers: 01482 889 911 sales@uk.bea-group.com visit our website www.bea-group.uk
BeA your partner for timber frame and offsite construction manufacturing
Modular housebuilder ilke Homes was joined by Iceni Projects to host local councillors at the pioneering Hope Green development in Stanford-le-Hope where the company, in partnership with Gresham House and Octopus Energy, is delivering the world’s first-ever homes to guarantee zero energy bills.
Councillor Paul Arnold of the Ockendon ward, councillor Sue Shinnick of the South Chafford ward, and councillor Lynn Worrall of the Grays Thurrock ward, were all in attendance during the visit. Julie Rogers, Director of Public Realm at Thurrock Council and Leigh Nicholson, Assistant Director of Planning for Thurrock were also present, alongside Keith Andrews, Strategic Lead for Housing Development at Thurrock Council, and Bruce Chibesa, Senior Housing Development Project Manager at Thurrock Council.
Hope Green is a 15-acre site where ilke Homes, Gresham House and SO Resi are building the UK’s largest zero-carbon housing development. Branded Hope Green, the development will eventually comprise 153 homes once complete in Autumn 2023. 101 of these will be zero-carbon in operation - meaning they will generate their own source of energy, helping to drastically reduce emissions produced by utilities such as electricity and heating. All of the homes are being sold as a shared ownership, an affordable home ownership product that enables local people to get a foot on the property ladder.
Thanks to an innovative world-first partnership between renewable energy group Octopus Energy,
modular house builder ilke Homes and alternative asset manager Gresham House, the development will also comprise numerous factory-built, semi-detached homes that will guarantee residents zero energy bills. As part of their visit, councillors and members of Thurrock Council were taken on a tour of the site, during which ilke Homes representatives were on hand to demonstrate how, by integrating low-carbon technologies like air source heat pumps and solar panels, the company can deliver highly energy-efficient homes that keep bills to a minimum.
Matt Suggit, South East Development Director at ilke Homes, said: “Hope Green sets a new benchmark for housing development, so it’s great to show local councillors how we are delivering muchneeded, energy-efficient housing in the heart of their constituency. Thurrock has declared a climate emergency and therefore innovative solutions to house building are an absolute must if they are to tackle the climate emergency and housing crisis at the same time.
There is a pressing need for ilke’s sustainable homes in Thurrock and we would like to delivery more.”
Alistair Wardell, Investment Director at Gresham House, added: “We are delighted to have welcomed the councillors to the pioneering Hope Green development, which sees Gresham House and ilke Homes deliver an entirely affordable scheme of 153 shared ownership homes. Hope Green will deliver over 100 operational net zero carbon homes, as well as the UK’s first guaranteed Zero Bills houses in an effort to help limit residents’ annual housing related outgoings in a time of significant cost of living increases.”
ilke Homes hopes to deliver a similar development nearby, with an application for 230 homes in East Tilbury currently pending consent with Thurrock’s Local Planning Authority.
Source: www.ilkehomes.co.uk
NHBC, the UK’s leading independent provider of warranty and insurance for newbuild homes, has brought together some of the leaders of Build to Rent to share their thoughts on this burgeoning sector. Available to download and in print, NHBC’s ‘Build to Rent, Insights from Industry Leaders’ explores what today’s renters want from their homes, details the experiences of those at the forefront of the market and profiles some of the most exciting Build to Rent developments in the UK and the people behind them.
The collection also looks forward with its contributors considering the future of the market. From the rapid rise of working from home post-pandemic to a greater understanding of the value of community, this publication reflects how Build to Rent addresses changing societal and consumer needs. More than just examining how the sector operates, this collection delves into the mindset and motivations of its contributors from personal backgrounds and early careers, right through to professional successes and their emergence as market leaders, this publication portrays the people, as well as the projects.
NHBC Customer Relationship Manager for Build to Rent, Niki Kyriacou said: “Build to Rent is undoubtedly offering attractive opportunities for investors and it’s a fast-evolving market with a diversity of housing options across the affordability spectrum. Consumers are increasingly exacting, demanding better developments and the best amenities, pushing up standards across the board. ‘Build to Rent, Insights from Industry Leaders’ offers an in-depth window into this sector and draws experience from some of the brightest and best in the industry; it’s a must-read for all Build to Rent stakeholders.”
Drawing on the collected experience of developers, investors, lawyers, architects, agents and property pioneers, NHBC’s ‘Build to Rent, Insights from Industry Leaders’ publication can be downloaded at nhbc. co.uk/BTRInsights
By bringing critical processes off-site, project teams can eliminate risk and take total control over their final design solutions. This, alongside traditional on-site volume housebuilding methods, results in a hybrid solution that eases the pressure of delivering world-class architecture and design.
This results in development projects that benefit from:
• Acceleration of overall delivery/completion
• Reduced site waste
• A reduction in on-site inventory (i.e. less breakage/wastage)
• No more labour/skills shortages
• Better cash-flow management
• Improved health & safety issues
•
WISA-Spruce is manufactured using UPM’s proprietary BioBond technology and mirrors the qualities of plywood produced using the traditional higher-carbon bonding method. This means it offers a like-for-like greener alternative. As with all WISA’s plywood, WISA-Spruce with BioBond technology has undergone rigorous testing to guarantee its high-performance qualities, meeting superior standards of strength, resistance and sustainability.
standardisation across the brand’s high-performance spruce range is a game-changer, offering the best quality with a reduced carbon footprint. Not only is it helping us to promote more sustainable construction methods, but it’s also supporting a wider drive toward a net zero society.”
UPM’s ultra-sustainable new technology, WISA BioBond is now the standard bonding agent in all James Latham Ltd’s collection of UPM WISA-Spruce. WISA BioBond is the latest bonding innovation from UPM, a globally renowned manufacturer of sustainable architectural plywood, now used in the entire WISA-Spruce range.
A landmark development in plywood adhesive, BioBond replaces at least 50% of standard glue’s fossil-based phenol with lignin, timber’s inherent bonding agent. Obtained as a by-product of the Kraft Process, this partial-substitution reduces the carbon footprint of WISA-Spruce by approximately 10%, without compromising technical performance or visual appeal.
More than just a new form of glue, BioBond has reduced CO2 WISA’s plywood portfolio, already available for birch and now spruce, plywood, UPM plans to roll out BioBond across all its plywood mills, gradually covering its entire range. As one of the UK’s most sustainable materials distributors, Lathams is keen to introduce UK specifiers to the low-carbon advantages of WISA-Spruce with BioBond technology. By incorporating this innovation to its ever-expanding collection of green architectural materials, they are demonstrating their ongoing commitment to supporting sustainable design and build.
Commenting on the introduction of BioBond to the WISA-Spruce range, Nick Widlinski, Panels Director at Lathams said: “There’s no doubt timber and woodbased materials are helping architects and designers tackle global climate change through making loweremission material choices. However, a question around the carbon intensity of glues and adhesives used in the production of engineered wood persists, and WISA BioBond tackles it head on. Its introduction and
UPM’s VP of Strategy and Business Development, Susanna Rinne added: “Sustainability is at the heart of our ethos and guides our ongoing R&D. We are the first manufacturer in the world to use a ligninbased solution for spruce and birch plywood, offering a no-compromise sustainable material solution. It’s imperative we work with those who have similar values. Due to Lathams’ longstanding reputation for championing sustainable specification make them a great partner to help us introduce BioBond and its unique properties to the UK and Irish markets.”
Providing further confidence in WISA-Spruce’s green credentials and certification, the product category scored one of the best ratings on Lathams’ new Carbon Calculator tool. An academically developed formula which scores the embodied carbon of each Lathams’-stocked timber product from cradle-topurchase, BioBond WISA-Spruce achieved top ranking across the board, providing third party verifications for the material’s sustainability claims.
Source: www.lathamtimber.co.uk www.upm.com
Algeco parent company, Modulaire Group has published its Global Sustainability Report detailing how the global business has placed sustainability at the forefront of strategy and decision-making. ‘Sustainable Modular Solutions for a Fast-Moving World’ and prepared in accordance with UN SDGs (Sustainable Development Goals), TCFD (The Task Force on Climate Related Financial Disclosures) and UNGC (United Nations Global Compact) Standards, the report discusses Algeco’s roadmap to net zero, its wider ESG strategy and KPIs to measure progress.
Modulaire Group is a leading provider of modular services and infrastructure, offering flexible, costeffective, high-quality and timely solutions to help customers in a variety of end-markets efficiently meet their needs for space and remote accommodation. The document sets out the Group’s strategy’s three key pillars: environment, social and governance (ESG), with circularity, adaptability, and leasing at the core. Its ‘loops within loops’ model is at the heart of the strategy, which employs circular economy principles to minimise waste throughout its whole operations and activities.
Mark Higson, Group Chief Executive Officer of Modulaire Group, said: “I am convinced that by taking positive action and advancing the ESG Sustainability Strategy in 2022 and beyond we will achieve change at scale to benefit our stakeholders. We see sustainability both as a responsibility and an opportunity for our business. I firmly believe that we have an opportunity to help our customers reduce their GHG emissions through our sustainable products and services. Our portfolio of products and services are already becoming more strategically focused on serving high-growth, sustainable end markets.”
Inder Poonaji, Director of ESG and Sustainability added: “Sustainability is embedded in our purpose and is fundamental to everything we do at Algeco. Our approach is based on the principle that we must do social and environmental good, while providing a strong return for our shareholders and customers. This report helps our investors, partners, employees, and customers understand more about how we are growing our business and developing in an inclusive, environmentally conscious way.”
Source: www.algeco.co.uk/sustainability
A new report, published by the Supply Chain Sustainability School, Akerlof and the University of Salford, has been created to support clients and supply chain organisations on how to enhance the benefits of the social value created using offsite manufacture.
In the face of urgent challenges – including the need to rapidly decarbonise, combat growing poverty and inequality, and address the cost-of-living crisis – what and how the industry build is crucial. Offsite construction and the social value agenda are two responses, driven by both government and industry. This report aims to bring these two agendas together, addressing a gap in guidance for clients and the supply chain.
The report illustrates the benefits that can be felt at both development and manufacturing sites, focusing on five core themes: employment, skills, economy, social and environmental. Perspectives brought by participants indicate that social value is considered important by the sector, with compelling arguments put forward on the ability of the model to provide secure, long-term employment opportunities. The report also highlights recent case studies around embodied carbon which indicate saving of between 30-45% can result from adoption of offsite techniques.
It offers guidance to the offsite manufacturers by sharing clear examples of ‘good work’ including measuring reductions in embodied carbon, inclusion of local stakeholders in the design process using digital tools, creating training opportunities and routes to progression through direct employment. The findings indicate potential for offsite to deliver the same, if not more, value to society than traditional construction, providing early communication takes place among stakeholders to understand the possibilities and agree clear boundaries and methodologies.
Ian Heptonstall, Director of the Supply Chain Sustainability School, said: “I am delighted to share this guide providing practical recommendations within the offsite sector. I hope organisations will find it useful as a jumping off point to get to grips with their social value offering, measuring and communicating
impact for the benefit of all in the sector.”
Ellie Jenkins, Partner at Akerlof and co-author of the report, said: “Offsite construction can create significant social value. We hope this guide will shape understanding and encourage the offsite sector to embed social value, growing a community of great practice.”
Membership to the Supply Chain Sustainability School is free – simply register for an account to gain access to practical learning and support in the form of sustainability training, events and networking, e-learning modules, tailored assessment and a library of over 3,000 online resources. The report can be downloaded from the Supply Chain Sustainability School website.
Source: www.supplychainschool.co.uk
Britlift are a designer and manufacturer of lifting equipment, specialising in the lifting of modular homes, bathroom pods, commercial modules, containerised structures and pre-cast components.
With a wealth of experience in the design and manufacture of lifting frames and lifting systems to the Offsite Construction sector, Britlift are the Offsite sector partner of choice.
UK architects Studio Anyo has been commissioned to design and project manage a new multi-million-pound eco resort on a Caribbean island of Puerto Rico. The circa £10million project will see the creation of a family of 12 seven luxury eco-lodges featuring four one-bedroomed units, including a disability access unit, two two-bedroomed units, two VIP units and four one-bedroomed tree house units constructed offsite in the UK using the latest build techniques and MMC materials.
Tree house units in the activity section as individual rental units are also planned along with a luxury customised tree house retreat experience. These will then be shipped directly to Puerto Rico for erection on a seven-hectare site close to the El Hippie Waterfall on the edge of the El Yungue National Forest in the east of the country. Once built for developer Namu Investment Group, they will become the eye-catching centrepiece of an ambitious and ground-breaking sustainable eco-leisure destination that will also feature a fitness retreat, wild bathing, BBQs, tree top walkways and swings, cable cars, restaurants, a spa, and a coffee bean planting and tasting experience.
While still in the development stage, the eco-resort, which is scheduled to open for visitors in 2024, has been designed to incorporate a range of sustainable materials to create components assembled on-site to heighten enhanced levels of building fabric performance. Adopting the latest offsite techniques will reduce material delivery times and cut the construction site footprint while materials reclaimed from the demolition of existing buildings will be used in the construction process, delivering long term efficiencies.
Studio Anyo’s ‘carbon and energy positive, zero waste framework’ system will be utilised to create net biodiversity gains in the construction of its ‘Samlingen’ leisure accommodation, which has been designed to provide long term energy saving and sustainability benefits. Local skilled labour will also be employed to support the supply chain and deliver a higher quality product, with minimum impact on and disruption to the local community.
The ‘Samlingen’ incorporates leading edge design to deliver contemporary leading edge leisure accommodation. The interior features a large open
‘Samlingen’
CEO of Studio Anyo, James Walsh, who is overseeing the project design and development phases, said: “This is another ground-breaking, exciting project for Studio Anyo. We have incorporated design principles to deliver modular sustainability and a bespoke experience with tree-level living spaces within the sanctity of the local forest and wider natural environment. As architects, we have drawn on our extensive knowledge and expertise of bespoke solutions and contemporary design to create a stunning project that will undoubtedly make a huge contribution to Puerto Rico’s burgeoning, dynamic eco-travel market.”
Source: www.studioanyo.com
The Time for Timber team handed out trees at Manchester Piccadilly train station to raise awareness of its latest campaign to promote the use of timber as a low-carbon building material. The purpose of the tree giveaway was to increase awareness through the media and the public, that by planting and growing more trees, further carbon can be captured and stored.
The UK has set itself ambitious targets of reaching net zero by 2050, and if the carbon output of the construction industry is not addressed, this goal will not be met. As such, the use of structural timber represents a great opportunity for transitioning to a much more carbon efficient method of construction. The timing of the campaign coincided a week before the COP27 conference in Sharm el-Sheikh, where countries from around the world are coming together once again to try and form a plan to tackle climate change.
Andrew Orriss of the STA said: “It was genuinely refreshing to chat with members of the general public and to hear how many support methods that strive to reverse the negative impacts of carbon intensive methods of construction. Real action must be taken now if we are to stand any chance of combatting climate change.”
EOS Framing has been awarded an Environmental Product Declaration (EPD) in accordance with EN 15804+A2 and ISO 14025 / ISO 21930. The scope of the EPD is cradle-to-gate which provides information about the light steel framing systems impact upon the environment and includes a comprehensive lifecycle assessment.
This assessment considers the extraction of raw materials, the manufacturing process, distribution and also its end-of-life value, such as whether it can be recycled or reused. Steel is an example of a highly sustainable building material with qualities well-suited to circular economic use and capable of being reused and infinitely recycled without loss of quality.
This unique characteristic gives steel a high value at all stages of its lifecycle. The recovery infrastructure for steel recycling is highly developed and extremely efficient and has been in place for decades. Current recovery rates from demolition sites in the UK are 99% for structural steelwork and 96% for all steel construction products – figures that far exceed those for any other building material. An EPD is an important
Time for Timber’s overarching cause, which was explored through the tree giveaway, is to educate and promote the use of timber as a construction material as it presents itself as a truly vital solution to the ongoing climate crises. If the UK is to build more homes, schools and offices in a way that supports the UK’s commitment to net zero by 2050, timber must be utilised in an even greater capacity.
Andrew Orriss added: “The housebuilding industry has an enormous task to pick up the volume, and perhaps this is where the supply chain can help to
alleviate some of the pressure. Furthermore, MMC/ offsite allows us to pre-manufacture elements of the housebuilding process, contributing 55% to quality and speed, which was confirmed by Homes England. This represents a quick and efficient way of meeting these ambitious targets. There is a real risk that if immediate change isn’t implemented, the net zero goal for 2050 will not be met, and the adverse effects of climate change will continue to worsen.”
Source: www.timefortimber.org
validation tool for manufacturers such as EOS to provide transparent data about the environmental sustainability of its products and for specifiers to make informed purchasing decisions. Taking EPDs into consideration when selecting materials for construction projects can help specifiers meet client sustainability requirements.
EPDs can also be used by specifiers to help control building waste, a significant environmental and costly issue currently faced by the construction industry and encourage the re-use and recycling of building materials at the end of their life. Furthermore, making informed product choices at the specification stage
can contribute to the reduction of the developer’s carbon footprint over the lifecycle of the building helping reach net zero targets.
As part of Etex Group, sustainability is a key driving force in EOS Framing’s strategy and as innovators in light steel systems, the leading manufacturer wants to inspire construction professionals to develop buildings that are not only safe but more sustainable. EOS want to empower specifiers to be technical forerunners in the offsite sector and this EPD can help reduce the carbon footprint of new buildings across all construction sectors.
Source: www.eosframing.co.uk
We caught up with Tony Jones, Technical Director at The Concrete Centre, to find out more about the benefits of using precast concrete and its important role in the wider offsite construction sector.
Q: For those unfamiliar, can you give a bit of background to MPA The Concrete Centre and what it provides for those operating in the offsite sector?
Tony Jones (TJ): The Concrete Centre is part of the Mineral Products Association (MPA), that means that it is funded by the UK cement, concrete and aggregates sector. The sector invests in The Concrete Centre so that it can provide guidance and resources to enable specifiers and constructors to design and use concrete.
These resources include online webinars, design tools such as Concept, and RC Spreadsheets, together with a wealth of best practice guidance, all available online. The resources of The Concrete Centre are relevant to all types of concrete as well as all those using concrete – whether
the construction method uses cast in situ concrete, or offsite, factory produced solutions, or even hybrids of the two.
The Concrete Centre also champions innovation in concrete and the sustainable use of concrete, whether that is material efficient design, or using low carbon concrete. With the support our product expert colleagues across MPA we are also able to provide designers with updates on the decarbonisation of cement and highlight the excellent work and progress of our members, including those in MPA Precast.
Q: Where do precast concrete products provide specifiers with the most flexibility and range of options – structural products, cladding and facades or via volumetric modular units?
TJ: Whilst volumetric precast systems and volumetric systems that are partly concrete exist, the maximum flexibility comes from designs that combine precast elements, as that gives the designer more options to meet the design brief. Manufacturers can either provide the product elements, or guidance on a system approach for certain building types. They can also provide bespoke solutions that can be developed for just one project, or for a client’s whole project portfolio.
Often the most efficient solutions incorporate both standard and bespoke products. For example, standard precast floor planks are used with a variety of construction systems. They can be paired with precast concrete frame solutions or precast wall panels and bespoke precast concrete cladding to give the desired aesthetic. Precast solutions
are therefore able to accommodate virtually any practical structural layout and through the treatment of the façade provide limitless opportunities for the external aesthetic.
Q: What benefits does precast concrete have compared to competing materials such as light gauge steel frame or engineered timber?
TJ: Precast concrete is noncombustible and does not need fire protection. This means that in the event of a fire the structure does not contribute additional fuel to the fire and is not reliant on following trades to achieve either its fire resistance or its fire separation function. This means that fires in concrete buildings generally cause less damage.
Whilst the performance of concrete in fire is well documented in codes, standards and legislation, as an industry it is important to continue to review the state of the art. With this in mind, MPA Precast commissioned
a full-scale test on a precast concrete cladding panel system by the Fire Protection Association and has demonstrated the fire performance benefits of this form of cladding.
Concrete is also tolerant of water. Therefore, any water used to extinguish a fire, persistent leaks or accidental flooding in a precast concrete building is unlikely to cause any structural concerns. Precast concrete can also be used in combination with timber and steel, where there are advantages of using an optimised hybrid solution. Concrete ultimately provides superior structural and occupant safety, as well as providing a durable structure that can deliver the best whole life carbon outcome.
Q: Decarbonisation is hugely important across the construction industry generally – how is the precast concrete sector addressing the many issues surrounding the circular economy, embodied carbon and overall sustainability? Is net zero concrete possible?
TJ: The UK concrete industry was one of the first construction product sectors to introduce a sustainability strategy in 2008 and continues to report annually on a wide range of sustainability metrics.
Early action since 1990 has seen the absolute carbon emissions of the sector have reduced by 53% - meaning we have been decarbonising faster than the UK economy as a whole. The UK concrete and cement sector has a detailed and viable roadmap setting out how it will achieve net zero by 2050. The industry also has the potential to go beyond net zero to become net negative when factoring in elements including the effects of carbonation, where concrete absorbs carbon dioxide from the atmosphere.
MPA Precast also report on the precast and masonry sector’s performance annually and provide their members with annual sustainability audits. This ensures that all the sustainability principles identified in the strategy are sufficiently understood and
addressed. Since 2010, our members’ factory carbon emissions and waste to landfill have dropped by 50% and 66% respectively. The use of supplementary cementitious materials (SCMs) has risen by a third in just two years (from 2019 to 2021).
Many precast concrete manufacturers are introducing new low carbon mixes to their products and investing in renewable and low carbon energy solutions within their factories. We’re under no illusion about the scale of the net zero challenge for both our and the entire construction industry, but it is possible. It will require further investment and innovation, not only by precast manufacturers and their supply chains, but also by government through the introduction of the infrastructure to enable a net zero economy.
To demonstrate the sustainability of precast concrete and to promote best practice across the sector, The Concrete Centre and other MPA groups have worked with One Click LCA on customised templates, based on the One Click LCA tool, to generate Environmental Product Declarations (EPDs) for a number of precast concrete products. One Click LCA is one of the most widely used Life Cycle Assessment and carbon assessment tools by the construction industry in Europe and is already used
by many engineering consultants and architectural practices in the UK.
The templates developed are robust and comprehensive and were supported by an extensive list of hundreds of background datasets and EPDs, including MPA’s own latest cement EPDs. This would ensure that any concrete product EPDs generated by the new templates are as representative, accurate and comprehensive as possible. The tool has been externally verified by an Eco-Platform member EPD scheme, the International EPD® System, earlier this year.
Q: How do you see the offsite and precast concrete sector developing over the next 18 months? Any technical advances that will have an impact such as the revision to Eurocode 2?
TJ: The precast concrete sector continues to develop its concrete technology using the benefits of factory production and control to implement lower carbon and material efficient solutions. Currently the standard for the specification of concrete is being updated. This will give further options with regards to the use of lower carbon mixes including multi-component cements using limestone, GGBS and/or fly ash to increase the percentages of SCM
within a concrete mix. There is more research underway to demonstrate the performance of calcined clays as an SCM, and even recycled concrete fines. Cement technologies and concrete mix designs will continue to evolve to achieve lower carbon concretes, and to use available constituent materials.
Eurocode 2 is being revised, this will, for the first time allow durability performance to be demonstrated through testing. This approach is particularly attractive to precast concrete as the materials sources are well known and the factory control can ensure a high level of precision. The revision to the Eurocode will also cover the use of steel fibres, which should enable material savings in some applications.
For more information visit: www.concretecentre.com www.sustainableconcrete.org.uk
Images: 01. Tony Jones, Technical Director, The Concrete Centre 02. Brick faced concrete cladding panels at Cartwright Gardens by Maccreanor Lavington. Courtesy Thorp Precast 03. Bespoke architectural precast cladding combining polished and acid etched surfaces at Victoria Gate, Leeds. Courtesy Techrete 04-06. Precast panels used on a Marriott Hotel. Courtesy FP McCann
Boost your performance with a partner dedicated to optimising your productivity. At ITW Construction Products, our fully integrated approach to offsite fabrication has resulted in solutions that combine the power of automated prefabrication tools and fastening systems with the highest quality materials. So
Richard Hipkiss, Development Director of the Modular and Portable Building Association (MPBA), discusses how volumetric technology can support net zero targets for the healthcare sector and produce energy efficient buildings.
Identifying a route to net zero emissions for a complex system as large as the NHS is particularly challenging. On 1 July 2022, the NHS became the first health system to embed net zero into legislation, through the Health and Care Act 2022.
The Delivering a Net Zero National Health Service report is now issued as statutory guidance.
Recognising and finding ways to meet the requirements of changing regulations and policy demands is crucial in reshaping our approach to sustainability. The ecological clock is ticking, and we must take urgent action to mitigate the impact of global warming. The emphasis with net zero construction is quite rightly focused on the environment but through a more sustainable approach to designing and developing buildings, those operating
in the healthcare sector will reap the benefits for many generations to come.
Energy costs are now not only having a major impact on household budgets but also NHS estate resources. There is significant evidence that traditionally constructed buildings do not produce structures that perform as well as design expectations and there is a great void between anticipated and actual in-use performance. Findings from studies such as PROBE (Post Occupancy Review of Buildings and their Engineering) reveal that actual energy consumption in buildings is often as much as twice of that predicted at the design stage.
With great challenges come opportunities. We have a proud legacy of innovation and many of our members in the volumetric modular
and portable building sectors are setting out road maps to deliver structures that will be net zero in operation and highly energy efficient.
At the forefront of offsite approaches, it is now established that volumetric modular technology is a game changer for the construction industry – reducing build times by an impressive 50-60% whilst increasing quality, productivity and safety. Volumetric modular buildings however are less susceptible to poorly specified products as time can be taken upfront to validate the correct specification of materials.
Factory manufactured modular buildings are highly accurate, well insulated and airtight, with air permeability with 1.5-3 m3 @50PA being the norm. A key advantage of modular construction is the quality
benefits which come from working in a controlled environment. By producing buildings in a factory setting, the quality of elements such as insulation can be better assured. Predictability of in-use performance is a substantial benefit in not only achieving net zero goals but reducing primary energy requirements and in-use operational emissions during the lifetime of the building.
This manufacturing method also allows better control over optimising material use. The surplus materials are recycled or reused for future projects, reducing construction waste that ends up in landfill. Materials are protected from moisture and extreme weather conditions, reducing the risk of disposal through water ingress and damage. It is widely recognised that modular has the potential to reduce overall construction programmes,
but it is not often acknowledged this approach can reduce up to 90% of the waste generated when compared with traditional construction methods.
With volumetric manufactured buildings all construction data can be validated and co-ordinated as part of a structured process, which helps provide accurate and reliable information for clients at the point of handover. Volumetric construction helps ensure client satisfaction and product assurances through the certainty and quality embedded into the manufacturing process.
Many MPBA members are accredited under a number of modular building frameworks, including NHS Shared Business Services Framework, LHC, Crown Commercial Service and NHS Commercial Solutions. These frameworks help NHS trusts and
The MPBA plays a key role in the connecting of sectors in the modular and portable building industry. The association collaborates with specialist technical advisors to enhance innovation in the design and manufacture of volumetric modular buildings. These can be designed and manufactured from timber or steel in any size and shape to meet individual client needs while ensuring full compliance with Building Regulations. To discover how volumetric modular technology can benefit healthcare construction projects go to: www.mpba.biz
other public sector clients improve the speed and cost-efficiency of procurement to support world-class patient care.
The MPBA and many of our members understand the construction challenges facing healthcare providers – from highly constrained budgets, to increasing demands for carbon and waste reductions. The benefits of volumetric manufactured buildings begin in the factory, continue on to the construction site and last through the lifetime of the building.
Images: 01-03. Modular technology offers a route to net zero emissions for the complex NHS estate. Courtesy Wernick Group
The applications are vast and its range is rapidly expanding to meet demand. MODULHAUS™ technology is continuing to bring fresh housing solutions and is evolving to be ever more innovative, sustainable and energy efficient.
Back in 2019 as part of a landmark 20th anniversary celebration, Hill Group pledged to give something back to the communities in which they operate. The pledge – known as Foundation 200 – was set up to gift 200 modular homes to local authorities and charities to help alleviate the homeless crisis. This was the start of a successful partnership between Hill Group and VOLUMETRIC™ with innovation at its core.
SOLOHAUS™ was launched in April 2020, to great acclaim. The response was overwhelming with demand to purchase as well as interest in the Hill
Group charitable pledge. It was clear that there was high demand for a solution to the homeless crisis.
Designed, engineered and manufactured by the experts at VOLUMETRIC™, the system known as MODULHAUS™ is the technology behind these modular homes. The initial concept was for a single person interim home with 200 being gifted to charities, local authorities and third sector organisations through Foundation 200. But driven by commercial demand, VOLUMETRIC™ has expanded the range.
Delivered 100% complete ready for installation – all modules are futureproof for Building Regulation changes. LABC assured and BOPAS certified, homes are quality-accredited, fully tested, and commissioned predelivery with high-quality fixtures and fittings throughout. Designed to meet the need for rapid-build housing, the multi award-winning energyefficient modular accommodation, has been rigorously tested to ensure outstanding performance and quality.
Offsite Awards, the single-occupancy option – SOLOHAUS™ promotes independent living, offering a secure space with ultra-low running costs.
Picking up the Product Innovation trophy at the 2022 Offsite Awards, the double occupancy, DUOHAUS™ provides additional space whilst meeting high standards of efficiency and performance.
Launched at Offsite Expo 2022 –FAMILYHAUS™ maximises space and comfort, with two bedrooms for a safe, family-friendly home for two adults and two children offering an alternative solution to high-cost interim housing.
Designed to Perform Built to Last VOLUMETRIC™ modular homes provide a future-proof solution to the UK housing crisis, meeting the interim needs for homeless people, onsite keyworker and student accommodation. The MODULHAUS™ system is stackable, relocatable and carries a BOPAS certified 60-year design life. Modules are configurable to meet unique requirements with optional extras and modifications to enhance site functions and provide a long-term, cost-efficient solution to fit various sites and needs.
Right from the initial concept stage, the decision was reached to develop a modular solution that will exceed the Future Homes Standard to relieve the burden of ongoing expenses associated with traditional temporary accommodation and negate fuel poverty. SOLOHAUS™, DUOHAUS™ and FAMILYHAUS™ homes achieve lower whole-life carbon impact than equivalent timber frame dwellings of the same size. Design features include ergonomic internal fully fitted living space with furnishings, bedrooms, shower-rooms and kitchens complete with low energy white goods. Modules are provided on a turnkey basis, fully equipped for immediate occupation. Available in a range of claddings and colour combinations, the MODULHAUS™ system sits on six low-impact foundation pads to minimise groundworks and requires only electric, water and waste connections.
A revolutionary Energy Centre developed by VOLUMETRIC™, meets the energy requirements of up to six modules. This intelligent technology is digitally connected to each module – instantly responding to demands for hot water, heating and energy requirements. Although modules have mains connection, the Energy Centre can meet demands at most times of the year as energy generated during the day is stored in battery cells until required. Surplus energy goes back into the grid, carbon offsetting and creating net zero living.
Walls are double-lined with noncombustible (high impact) boards to provide fire and acoustic performance, whilst encapsulating insulation to meet energy efficiency requirements with exceptional U-values (as low as 0.09W/m²K) and airtightness to work
with the mechanical ventilation and heat recovery (MVHR) system.
The energy strategy is designed to exceed the Future Homes Standard with Environment B and A rating and emissions as low as 229.5Kg CO2/year. Significantly exceeding energy efficiency and sustainable requirements – modules are 100% factory fitted, delivered in one-load, virtually eliminating traffic to site. Modular interim homes can be purchased outright under the full turnkey package, or alternatively, they can be supplied under a leasepurchase agreement or leased under a long-term arrangement for a variety of packages to suit different sites and budgets.
VOLUMETRIC™ adopts a partnership approach and works in close collaboration to develop bespoke modular homes to meet individual site briefs and budgets.
You can read more about FAMILYHAUS™ in Volumetric Modular magazine included with this edition of Offsite Magazine.
For more information visit: www.volumetric.co.uk
Images: 01-03. The VOLUMETRIC™ portfolio provides many flexible housing options
The first large-scale affordable modular housing development in Scotland has been completed within budget and one month ahead of schedule showing the vast benefits offsite can bring.
The ground-breaking £9.8million project was successfully delivered by Riverside Scotland and Connect Modular, part of The Wee House Group, and will provide 63 highquality, low energy, affordable homes in Dundonald, South Ayrshire.
The gold accredited Secured by Design development has helped to sustain 60 local jobs with the energy efficient new homes built offsite at Connect Modular’s manufacturing facility in Cumnock, Ayrshire.
The homes have also helped to inspire the next generation of construction workers after four-year old Hector Hodge from Dundonald became fascinated by the scheme over the past year as he walked past the new housing development on his way to nursery.
The modular homes are 90% complete when they depart the factory with kitchens, bathrooms, plumbing and electrics installed, leading to a significantly shorter build
programme and earlier occupancy. In comparison to a traditional build project, fabrication under factory conditions improves quality, reduces waste, negates the impacts of adverse weather and allows for overlap of site preparation and build phases – a more efficient process all round.
The Dundonald development has given Hector a glimpse into the future of Scotland’s construction industry and led to him being made guest of honour at a ribbon cutting ceremony to mark the completion of this innovative housing development.
Aspiring builder, Hector was cheered on by his dad, David, Managing Director of Riverside Scotland, Diana MacLean and Jennifer Higgins, Managing Director of Connect Modular as he cut a ribbon to mark the completion of the innovative development ahead of schedule.
David said: “We live in the village and having a live building site on our doorstep has been a dream for Hector.
A real highlight for Hector was seeing the modules arrive on a convoy of lorries and be craned into position. He was fascinated with the process. He is mad about diggers and it’s been a real joy to visit the site with him and watch him bond with the workers.
“We were honoured to be asked to officially open the new homes. It’s a lovely memory for Hector to look back on when he’s older, and possibly working in construction, having been so inspired by this development. These homes were much needed in the village and its lovely to see new faces and welcome our new neighbours to the community.”
The Dundonald development is now home to ten military Veteran households – accounting for 16% of the affordable homes built in Dundonald after Riverside Scotland exceeded its targets. Riverside Scotland has made a strong commitment to providing homes for veterans at risk of homelessness at its two newest social housing developments by allocating more than 10% of new homes to support veteran households.
Jennifer Higgins, Managing Director at Connect Modular, said: “We are thrilled to hand over this awardwinning development ahead of schedule. Riverside Scotland’s willingness to embrace this evolution in construction on a large-scale project brings us a huge step closer to a housing stock that will achieve a net zero Scotland by 2045.
“It’s been an absolute pleasure to welcome Hector and David to the site throughout the project. It’s wonderful to see how inspired and interested Hector is in construction. He struck up a real friendship with our site manager, Archie Stobbs and his visits always brightened up our day. You never know, our youngest ever apprentice may join us for real some day!”
Riverside Scotland, part of The Riverside Group, manages 2,300 homes across Ayrshire with a programme to deliver 300 new homes over three years underway, increasing the size of its housing stock by 13%. Diana MacLean, Managing
Director of Riverside Scotland, said: “This nationally significant affordable housing scheme has raised the profile of offsite construction in Scotland and the rest of the UK. While we are a smaller housing association, we have big ambitions which we are able to achieve by being part of the wider Riverside Group.
“By providing high-quality, low energy homes at speed and scale we are helping to tackle climate change, prevent homelessness for our veteran community and help these residents to live in affordable, warm homes during the largest cost of living crisis our nation has faced for the past 40 years. We are delighted that Hector could help to cut the ribbon during the completion ceremony. He has become something of a site mascot, and it’s heartening to hear that local residents have embraced the development as an important project for Dundonald.”
The project was delivered with £4.65million of grant funding through the Scottish Government’s Affordable Housing Supply Programme. The development was highly commended in the Green Housing Category at The Herald Property Awards for Scotland 2022 and was shortlisted in both the Working in Partnership Category & Excellence in Affordable Housing Category at The Chartered Institute of Housing Scotland Awards 2022.
For more information visit: www.theweehousecompany.co.uk/ connect-modular-ltd
Images: 01-03. 63 high-quality, low energy, affordable homes have been created in a factory environment 04. L-R Diana MacLean, Managing Director, Riverside Scotland, Hector Hodge and Jennifer Higgins, Managing Director, Connect Modular
With a façade system for virtually every scenario and almost limitless choice of colours and finishes, we can help you create truly iconic buildings
With a façade system for virtually every scenario and almost limitlless choice of colours and finishes, we can help you create truly iconic buildings
With a façade system for virtually every scenario and almost limitlless choice of colours and finishes, we can help you create truly iconic buildings
A seamless rendered or brick slip rainscreen system on to LSF or timber framed structures. Increasing the speed of construction, it reduces the building modern methods of construction.
A seamless rendered or brick slip rainscreen system on to LSF or timber framed structures. Increasing the speed of construction, it reduces the building modern methods of construction.
A seamless rendered or brick slip rainscreen system on to LSF or timber framed structures. Increasing the speed of construction, it reduces the building modern methods of construction.
A fast track, mechanically- fixed clay brick slip system, designed for offsite, modular and site-based construction.
A fast track, mechanically- fixed clay brick slip system, designed for offsite, modular and site-based construction.
Highly versatile, lightweight yet strong, SLIPFAST® offers many cost and time-saving benefits as well as a 60 year design life.
A fast track, mechanically- fixed clay brick slip system, designed for offsite, modular and site-based construction. Highly versatile, lightweight yet strong, SLIPFAST® offers many cost and time-saving benefits as well as a 60 year design life.
Highly versatile, lightweight yet strong, SLIPFAST® offers many cost and time-saving benefits, as well as a 60 year design life.
The brick carrier system is supplied direct with pre-installed rails, ready to receive pre-formed clay brick-slips, which are then pointed and sealed on site (no adhesive needed).
The brick carrier system is supplied direct with pre-installed rails, ready to receive pre-formed clay brick-slips, which then pointed and sealed on site (no adhesive needed).
The brick carrier system is supplied direct with pre-installed rails, ready to receive pre-formed clay brick-slips, which are then pointed and sealed on site (no adhesive needed).
Highly-durable and weather-resistant insulated cladding systems, typically used on lightweight steel framed structures to create a void between the cladding and the sheathed framed structure. Available in a render or brick slip façade finish.
Highly-durable and weather-resistant insulated cladding systems, typically used on lightweight steel framed structures to create a void between the cladding and the sheathed framed structure. Available in a render or brick slip façade finish.
Highly-durable and weather-resistant insulated cladding systems, typically used on lightweight steel framed structures to create a void between the cladding and the sheathed framed structure. Available in a render or brick slip façade finish.
Swisspearl coloured fibre cement panels give façades individuality, character, texture, colour and, very importantly, a highly effective protective layer.
Swisspearl coloured fibre cement panels give façades individuality, character, texture, colour and, very importantly, a highly effective protective layer.
Our Swisspearl through-wall system offers numerous design options with an extensive selection of finishes, joints fastenings and panel formats.
Swisspearl coloured fibre cement panels give façades individuality, character, texture, colour and, very importantly, a highly effective protective layer.
Our Swisspearl through-wall system offers numerous design options with an extensive selection of finishes, joints fastenings and panel formats.
Our Swisspearl through-wall system offers numerous design options with an extensive selection of finishes, joints fastenings and panel formats.
T: 0845 519 8641 benx.co.uk
Manufactured using compressed natural basalt (a available volcanic rock) bonded together organic binder, Rockpanel façades are sustainable and environmentally friendly. The boards in the appearance and colour to provide a
Manufactured using compressed natural basalt (a readily available volcanic rock) bonded together with an organic binder, Rockpanel façades are sustainable and environmentally friendly. The boards
Manufactured using compressed natural basalt (a readily available volcanic rock) bonded together with an organic binder, Rockpanel façades are sustainable and environmentally friendly. The boards
to seal in the appearance and colour to provide a
to seal in the appearance and colour to provide a
Fully-ventilated rainscreen cladding system which has an appearance of traditional timber cladding but the durability and strength of cellulose fibre cement.
Fully-ventilated rainscreen cladding system which has an appearance of traditional timber cladding but the durability and strength of cellulose fibre cement.
Fully-ventilated rainscreen cladding system which has an appearance of traditional timber cladding but the durability and strength of cellulose fibre cement.
boards are coated at our inhouse automated facility, offering a wide range of
Supertech Weatherboards are coated at our inhouse automated facility, offering a wide range of colour options.
Supertech Weatherboards are coated at our inhouse automated facility, offering a wide range of colour options.
Through-wall system with coloured solid aluminium Its light weight and high strength-to-weight offer superior handling and resilience, while its reaction and insulating properties help provide and energy efficiency.
Through-wall system with coloured solid aluminium panels. Its light weight and high strength-to-weight ratio offer superior handling and resilience, while its fire reaction and insulating properties help provide safety and energy efficiency.
Through-wall system with coloured solid aluminium panels. Its light weight and high strength-to-weight ratio offer superior handling and resilience, while its fire reaction and insulating properties help provide safety and energy efficiency.
Insulated façade system that can be applied to SFS structures in an offsite or site-based environment.
Key benefits include superior thermal efficiency, speed of installation and design flexibility.
Insulated façade system that can be applied to SFS structures in an offsite or site-based environment. Key benefits include superior thermal efficiency, speed of installation and design flexibility.
Insulated façade system that can be applied to SFS structures in an offsite or site-based environment. Key benefits include superior thermal efficiency, speed of installation and design flexibility.
As Colin Dalton, Co-Founder and Director at architectural practice Gray Design explains, offsite technology holds many keys to unlocking low-carbon construction for the social housing sector.
In recent years European and UK governments have made commitments to reach net zero and reduce greenhouse gases by mid-century. In May 2019, the Committee on Climate Change (CCC) recommended that the UK should aim to be net zero on all greenhouse gases by 2050. This would keep the UK in line with the 2016 Paris Agreement. In the Paris Agreement, governments agreed to keep global warming below 2°C and to make efforts to keep it to 1.5°C.
Informed by the Paris Agreement, The UK Green Building Council (UKGBC) launched its ‘Net Zero Carbon Buildings: A Framework Definition’ document in 2019. The document defines what achieving net zero carbon emissions means, in terms of the construction of a building and its operation of it, and how to reduce embodied carbon levels. The framework sets out definitions around
two approaches to net zero carbon buildings.
Net Zero Carbon for Construction –when the amount of CO2 associated with a building’s product and construction stages up to practical completion is zero or negative, through the use of offsets or the net export of on-site renewable energy.
Net Zero Carbon for Operational Energy – when the amount of CO2 associated with the building’s operational energy on an annual basis is zero or negative.
If the methods of offsite construction are correctly used then the carbon emissions from the manufacturing, transportation and construction phases of a building can be reduced. Early engagement with offsite construction specialists is key to unlocking environmental transport benefits.
This means that solutions are optimised at the design stage of a concept and therefore reducing weight, materials, and volume.
With the increasing understanding of offsite construction, supports for M&E services are now becoming modular. These supports can be easily assembled with minimal tools removing waste as they are cut to size, and deliveries to and from the site are reduced because supports can be altered at the source.
Offsite construction is being seen as a way to meet some of the demand for new social housing. Prefabricated housing offers comfortable, well-insulated homes that can be constructed more quickly than traditional buildings. Offsite construction can deliver a modern apartment block in half the time that it would take to build using traditional methods.
Japan faced a housing crisis following WWII and the nation's construction industry couldn't keep up with the demand. Japan solved its crisis which led William Johnson to investigate how they did it in his report titled ‘Lessons from Japan: A comparative study of the market drivers for prefabrication in Japanese and UK private housing development’. The goal was to explore if the UK could learn anything from Japan. Johnson paid specific attention to the use of offsite construction which he claims is a major reason why Japan can build houses faster than the UK. In 2004, of the 1,160,083 houses built in Japan, 159,224 (13.7%) were prefabricated. This means the volume of offsite houses manufactured in Japan in 2004 exceeded that of total new build completions in England for that year.
A more recent example came from a project in Cambridge, where six modular homes were installed on a temporary site to house homeless people. A report by the Cambridge Centre for Housing & Planning Research noted that residents were impressed with the design, space, and quality of the modular units.
The Cambridge project is especially relevant to the UK’s large number of homeless people. In March 2020, more than 14,000 homeless people were housed in England as part of the ‘Everyone In’ initiative to take rough sleepers off the streets during the first wave of the COVID-19 pandemic. It is clear offsite construction can solve a housing crisis but it’s important to know which type of housing it is best suited for.
High-rise residential buildings seem to be the most popular. Following a thorough investigation outlined in a UK report titled ‘Application of Modular Construction in High-Rise Buildings,’ it was revealed that when modular construction was used for high-rise buildings it reduced overall construction time by 50%, waste by 70%, and led to an average cost savings of 30% compared to traditional techniques.
High-rise buildings are favoured due to its inherently topological modular form and the increased number of repeatable modules. Examples of this type of modular building in the UK include the 249-flat Creekside Wharf
development in Greenwich and the 700-bedroom Victoria Hall student accommodation in Wolverhampton. It was estimated that for the 25-storey modular building in Wolverhampton the total effort in constructing the building was approximately 16 manhours per square metre (1.5 man− hours per square foot) completed floor area, which represents an estimated productivity increase of approximately 80% relative to site-intensive construction.
Offsite construction for social housing has already proven it can be the solution to the current housing crisis however it requires further government policy development and carrying out multi-residential demonstration projects to further evidence its potential.
It is difficult to fully realise the potential of offsite construction for social housing as there is currently a skills shortage. However, there
are organisations that have already committed to solving this. For example, the CITB has invested £1.2million in educational resources for both classroom-based and handson training to upskill the workforce and improve the UK's capacity for offsite housing construction.
There are many different sectors crucial to the success of offsite construction. It is vital that the government and other major industry bodies continue to nurture this growing method of construction, demonstrating a longterm commitment to supporting innovative forms of construction and trying to combat the UK housing crisis.
For more information visit: www.graydesignltd.co.uk
Images: 01. Colin Dalton, Co-Founder and Director, Gray Design 02-03. Social housing is a sector that can benefit from the speed and quality of offsite technology. Courtesy CCG & rg+p
Kingspan – one of the most familiar names in advanced insulation and innovative building systems – recently hosted a special factory tour allowing visitors to learn more about their TEK® Building System and view their advanced manufacturing facility on the outskirts of Leeds.
A wide range of industry visitors gathered on-site to hear more from the Kingspan experts on the design benefits and technology behind their market leading TEK® structural insulated panel (SIP) system. The event saw professionals from across the construction industry attending, including those involved in building design, architecture, systems specification and the project management sectors. A well-organised presentation schedule balanced an informative overview of the TEK® system with case study examples, alongside the opportunity to quiz the Kingspan experts and view the technology at first hand.
Richard Surgey, Kingspan TEK® Product Manager, provided a detailed explanation of the TEK®
system and offered a comprehensive understanding of the technology and wider development of Kingspan products, explaining the system’s strengths, including its unlimited design options, precision engineering principles and exceptional structural performance.
As a ‘next generation’ system, TEK® SIPs provide a continuous line of insulation with panels offered at 142mm and 172mm thicknesses with varying U-values. The TEK® system consists of a high-performance fibre-free rigid urethane insulation core, sandwiched between two layers of oriented strand board type 3 (OSB/3). A closed cell structure means no movement or sagging, while Kingspan’s pre-calculated suite of values shows thermal bridging as low
as 4% is achievable. The TEK® system also offers exceptional airtightness, with air leakage levels of 1m3/hour/m2 at 50 Pa being achievable.
Richard Surgey also gave a comprehensive explanation of the unique panel jointing system and its many applications, both as the TEK® build system or inboard or outboard TEK® cladding system. As well as demonstrating to visitors the benefits of the available SIP product range, the presentation also highlighted how Kingspan is leading the way in creating a more environmentally and socially conscious construction sector. Kingspan has committed to long-term sustainability through their ‘planet passionate’ 10-year plan, allowing them to reach carbon zero by 2030. The company is already at net zero
energy and continues its mission to support the global shift to a fully decarbonised construction industry.
Following the presentation, attendees took part in the tour of the facility, with small groups led by the Kingspan team, who provided expert insight and information about the design and manufacture process. Marc Stoker, Kingspan Operations Manager explained each stage of the manufacturing process, starting with the creation of a motherboard using their state-of-the-art CNC cutting machine.
“Kingspan has a commitment to continuous improvement,” said Marc. “This includes the streamlining of our manufacturing productivity from five days to three, through the introduction of six SIGMA process improvement methodology, to the SIP manufacturing line. We have made a real effort to eliminate as much wastage as possible to achieve zero landfill and future plans include installing an on-site power plant to reduce our energy use.”
Visitors were also able to view materials, the production line in detail and ask questions as the tour progressed, culminating in a final stop at the Kingspan product display room, where the SIP panels were available to view as a completed system.
After the tour of the factory floor, a second presentation was given by Ian Still, National Sales Director at SIP Build UK (SBUK). As experts in the structural engineering, design, and installation of SIP panels, he gave attendees further insight and knowledge into the building process and how the TEK® system is playing a key role in developing a better built environment. He explained the whole process –from the importance of early-stage engagement and design approval to final delivery on-site. This included the importance of budgeting, programme time scales and how SIPS can deliver huge cost and time predictability. This was demonstrated through one of their award-winning projects – a sustainable, self-build dwelling in Hampshire, which was designed to meet exacting client specifications for low U-values and thermal efficiency and was installed in just four weeks.
For construction professionals interested in learning more about the benefits of adopting SIP technology, the tour of the Kingspan facility, offered an in-depth but concise introduction to their products and business. The feedback from attendees of the event was extremely positive, with all visitors able to take away a more comprehensive understanding – not only of the SIP panels and TEK® system – but also of the ways in which
Kingspan is constantly looking to the future and concentrating on investing in sustainability, productivity and technology.
For more information on Kingspan, its products and the TEK® SIP system visit: www.kingspantek.co.uk
Images: 01-03. The TEK® system is low carbon and created in an advanced manufacturing environment
04. Marc Stoker, Kingspan Operations Manager, explained to visitors all about the precision factory process
Offsite manufacturing has jumped to the forefront of many debates within the construction industry in recent years and as Ross Baxter, Managing Director of Saint-Gobain Off-Site Solutions points out, it's time to debunks several ‘myths’ to help developers choose offsite first.
Saint-Gobain Off-Site Solutions comprises several familiar names that will be familiar to those of you in the timber sector including Pasquill, International Timber, Roofspace Solutions, Intrastack and Scotframe. The construction industry is always evolving and developing. With new technologies, methods and practices being implemented regularly, companies within the sector are always looking for innovative ways to help them move forward.
One thing that many in the industry are looking at is offsite manufacturing (OSM). OSM sees the majority of manufacturing take place in a factory setting, rather than onsite at the development. This allows for a whole host of benefits for housebuilders, which many are taking advantage of. However, do people within the industry know the benefits of using OSM? And are they using it to its greatest potential? Pasquill, the UK’s largest supplier of trussed rafters, decided to conduct research into what the perceived ‘myths’ surrounding OSM were.
In a survey commissioned by Pasquill, over 100 housebuilders were asked what their perceived benefits of using OSM were. From the results, it was found that many benefits of OSM were not considered to be huge priorities as to why they decided to use OSM in their projects.
The survey, which looked at why businesses were turning to OSM products, asked “What are the biggest benefits to your organisation of using offsite manufacturing?”. In reply, 75% said that speed was the main benefit of OSM. This is because OSM construction takes place offsite by experts and is not affected by weather conditions on the day, something that can cause severe delays to a project. This also reduces the time spent building individual parts, as it all takes place in a factory, and reduces the need to have individual materials assembled on-site. With many in the industry under increased pressure complete projects on time, OSM has become a vital tool for managing these goals.
Cost was also deemed to be a big benefit by the survey respondents, with 44% believing it to be a huge positive point for OSM. This is due to the economies of scale, and the fact that costs can be predicted and forecast, which is never more important with an uncertain economic situation ahead. It can also give a clearer picture in terms of life costing, with OSM allowing savings during the lifetime of the build, as well as during construction.
However, there were other areas where survey respondents didn’t think that certain benefits of OSM were as important. Only 15% said that countering the skills gap was a big positive for housebuilders. This is surprising, as a skills shortage is one of the biggest issues facing the industry today. Using OSM to counter this is a great tool for those in the construction industry, with there being so much that OSM does to help fill onsite staff shortages and skills gaps. Alongside this, Pasquill is training up the next generation required for OSM via its junior designer programme, making sure they have the skills required to successfully implement OSM.
Other aspects that were not mentioned in the survey were product quality and embodied carbon. Through OSM a higher product quality is achieved in a factory-controlled environment compared to on-site. Additionally, we can qualify the embodied carbon through a known supply chain and product use. For example, SaintGobain Off-site Solution division has recently achieved an Environment Product Declaration (EPD) for one of its brands, Roofspace Solutions for its panelised roof solution, i-Roof.
However, through the survey, we also discovered that 21% don’t know or still don’t use OSM within their business. With OSM being one of the pillars of future construction, it will be an opportunity for those that have not used OSM to consider implementing it in future projects. Saint-Gobain’s offsite solutions brands are driving the use of OSM within construction and believe that in time, everyone will see a benefit through applying it to their businesses.
For more information visit: www.saint-gobain.co.uk/off-sitesolutions-division
Images: 01. Ross Baxter, Managing Director, Saint-Gobain Off-Site Solutions 02-03. Timber plays a central role in offsite manufacture and prefabricated roof trusses are a mainstay of housebuilding 04. eHome2 is a collaborative enterprise that will provide massive sustainable construction findings. Courtesy University of Salford
Construction and commissioning of Energy House 2.0 was completed in February 2022 and is the largest research facility of its type. It has two environmental chambers each able to accommodate two detached houses and under controlled conditions recreate a wide variety of weather conditions. The unique facility will play a key role in accelerating the progress towards low carbon and net zero housing design.
In June 2022, the next phase of work commenced and construction of the houses in chamber 1 of Energy House 2.0 is going according to schedule. Bellway Homes are building ‘The Future Home’ and the property being built by Saint-Gobain and Barratt Developments is known as eHome2. These are both modular build construction with the main structures now complete and both houses weathertight. Work continues at a pace with the next phases, internal partitioning, external cladding, and M&E work, now well underway. Testing and research programmes are expected to continue until spring 2023.
You can keep up to date with developments at: https://energyhouse2.salford.ac.uk/
When we talk about the supply chain, we often think in terms of individual disciplines and building components, each with its own objective and purpose. Great results rely on collaboration – not only between the client and contractor, or specifier and manufacturer, but amongst all parties at every stage of the project delivery process.
Project success lies not only in what has gone well, but in identifying and mitigating risks along the way. Right now, the construction industry is facing more challenges than ever before. Labour shortages, rising energy costs, and instability within the supply chain are causing many to reconsider the best routes for avoiding risk and costly programme delays or wildly escalating costs.
Our ethos at Fusion has always been one of collaboration, this starts at project conception. As leaders in light steel framing solutions, we put more than twenty years of knowledge and experience into creating our fivestep construction process. Synergy between our team and the people we work with is key to yielding the best results –focusing on the concept that the combined value and performance of several companies will be greater than the sum of the separate individual parts.
Right from the start, we enable a culture of support and guidance that allows us to maximise the project's
potential. We offer advice during tendering which, once the project is won, leads to estimating and preconstruction support. So, we know even before Stage One, what the goals are and can help find the best and most cost-effective solution. When construction professionals work with us, they have the reassurance of experienced hands to take them from design and planning all the way to manufacture and installation.
In times of economic instability, we cannot underestimate the value of providing predictability and certainty – whether in material costs, product performance, or delivery times. A broken link in the chain can cause a pile-up of obstacles that can devastate a project’s chance of on-time and onbudget completion. We understand the importance of ownership and establishing open communication channels. Our success is the success of our supply partners and vice versa.
While the supply chain involves many elements, synergy lies in bringing the sum of the parts together to achieve construction objectives. I think people often make the mistake of thinking that streamlining is about cutting back. Rather, it’s about having that singular driving force to bring all those components into one place – this is Fusion FOCUS™. By being involved collaboratively throughout the supply chain process, visibility and traceability improve dramatically, enabling us to identify opportunities for optimisation
and improvement at the right time and avoid complications further down the line. When you build robust relationships throughout the supply chain, utilising the benefits of each party’s knowledge, the potential value of the total project is increased. That is what we bring to the table through our five-step Fusion FOCUS™ process.
Through taking ownership of every building component, we have created an industry-leading solution in our through-wall FusionX™ system which, when combined with the Fusion Xterion™ cladding range, offers a complete integrated system with precise value-engineering and tried and tested performance.
We aim to be the supply chain partner of choice for light steel frame buildings, engaging early with projects to achieve client goals through a fabric-first approach, partnerships with our experienced specialists, and expert technical support. Over the years, we have established a demonstrable track record of delivering high-performance steel frame solutions across the UK. Ensuring a well-established end-to-end supply chain process plays a big part in that success.
For more information visit: www.fusionsteelframing.co.uk
Images: 01. The five-step Fusion FOCUS process provides a streamlined project approach
Mike Fairey, Managing Director of FusionSteel Framing, highlights
the value of developing a more synergetic approach to the supply chain in a bid to optimise delivery performance.
The multi-award winning Clifford’s Tower in York shows what an immense transformation can take place when modern offsite timber design breathes new life into an ancient and under-valued visitor attraction.
Clifford’s Tower is the largest surviving structure from the medieval royal castle of York, built in the mid-13th century but has stood as a roofless ruin since 1684. The tower offers superb views over the city and following a £5million project to conserve and improve the interior of the 800-yearold landmark for English Heritage, it now incorporates a free-standing timber solution that protects the ruin, carries a timber viewing deck, and sees new walkways and stairs give public access to features unseen for over 350 years.
Timber was ideally suited for the new structure, with its low carbon impact and lightweight nature. The glulam timber structure was designed so that all connections were concealed, and a neat appearance achieved.
The main structure comprises primary beams supported on four columns, carrying a timber viewing deck and central atrium. The columns have recesses concealing drainage and services routes. New services were ducted through the new raft foundation and concealed within the glulam columns, allowing the deck to be used for functions and night-time events with LED lighting concealed in structure, finishes and handrails.
The design is ‘circular’ with the timber frame demountable and reusable, if needed at any point in the future. This gives further sustainability benefits where the carbon captured within the timber can stay locked into the material for a significantly longer period of time.
Using timber supplied by leading French softwood supplier Piveteaubois, Buckland Timber installed the engineered timber elements alongside Douglas fir decking. Buckland chose to work with Piveteaubois as they could supply the sapwood-free Douglas fir that was used to make the glulam for the larger elements. They were looking to cut down on in-house manufacturing work and Piveteaubois could supply the floor joists thanks to their cutting-edge CNC machining capabilities. Piveteaubois provides a consistent grade of sapwood-free Douglas fir. Being dried to 12% moisture content it is perfect for glulam manufacture, so it worked well for Buckland to call on them for any large volumes that are needed quickly. For the Clifford’s Tower project, having
some of the beams delivered already machined was useful as it allowed a reduction in manufacture time.
Piveteaubois supplied 36m3 of 140mm x 350mm GL24h sapwoodfree Douglas fir glulam, comprising of 55 beams, with 38 of them further processed by Piveteaubois’ state-ofthe art SMC OIKOS 5-axis machining centre. This delivered precision cutting to any required length plus a wide range of machining capabilities. The 38 beams were cut into 129 pieces of various lengths and machined with mitre and bevel cut, as well as drillings and counterbores for easier installation.
Piveteaubois produces 50,000m3 of glulam and finger-jointed Douglas fir, Spruce and Pine glulam annually. With a permanent stock of around 3,000m3 in its 5,000m2 warehouse, they are ready to supply customers with standard 13m lengths or bespoke orders. This also includes a range of glulam treatment options including pressure treatment of Douglas Fir to Use Class 3.2 or pre-pressure treated UC4 Pine glulam for higher risk environments.
Douglas fir combines remarkable mechanical properties with excellent natural durability as its duramen is naturally Use Class 3.2 without treatment. Sapwood-free Douglas fir glulam, cladding and decking are excellent for use outdoors and age gracefully just like Larch and at a lower cost. Piveteaubois also offers Douglas fir C24, finger-jointed timber as well as CLT, making it a hugely versatile building material. All Piveteaubois Douglas fir comes from sustainable forestry and is PEFC-certified.
The non-slip timber deck was constructed using PEFC-certified Marley CitiDeck®, which is manufactured from premium grade European Redwood and was specified by Hugh Broughton Architects Ltd. The decking was installed, and carefully cut to a smooth curve following the line of the new metalwork guarding at the edge. There is also a large opening in the middle that allows visitors to look down to the floor of the keep. The boards were also used to create seating areas and the guard structure around the central opening. CitiDeck® is an attractive and robust anti-slip timber decking solution ideal for use
in public areas, the non-slip surface ensures the deck is safe to use all year round.
Working with Hugh Broughton Architects and conservation architect, Martin Ashley Architects on the detailed design, Ramboll provided the engineering design solution for this sustainable timber structure. This unique project introduced an architecturally stunning, structural timber intervention within the tower, to allow the public to fully access and appreciate the monument whilst demonstrating exemplary conservation practice by respecting the significance of the monument and site. Clifford’s Tower re-opened in April 2022 and
has been shortlisted and won several design and construction awards including Best Retail & Leisure Project and Winner of Winners Award at the Structural Timber Awards 2022.
For more information visit: www.uk.ramboll.com www.piveteaubois.com/en/ www.bucklandtimber.co.uk
Images: 01-04. A hugely successful revamp using engineered timber has transformed one of York’s most iconic sites. Courtesy Dirk Lindner/Hugh Broughton Architects English Heritage/Ramboll
A new senior school building for Crosfields School, a coeducational independent day school in Reading makes the most of the site’s hilltop position and boasts a superb timber approach to living and learning.
Designed to protect the landscape and provide a rich range of spaces for learning and socialising, this new senior school building combines offsite construction and cross laminated timber (CLT) with a collaborative digital approach. This significantly reduced construction time and disruption to the ongoing life of the school, whilst being exceptionally sustainable and creating bright open spaces and a warm, welcoming feel.
Over and above delivering on budget and programme, the client’s brief included the requirement to create a welcoming, sustainable and exceptionally inclusive building – in keeping with the school’s ethos. They wanted to create a building that would represent that new, more mature community, and once that was
able to grow and adapt. By taking a collaborative approach and combining digital design with structural timber and offsite construction, the design team has achieved an exemplar project that achieves each of the school’s goals, whilst also being elegant, functional, affordable and exceptionally sustainable.
Built using CLT and glulam, the distinctive S-shaped building weaves around the existing site – protecting the trees and forming an open courtyard. It provides a new entrance, nine classrooms, staff area, library, wellbeing hub, and a double height, flexible performance space and café that links to the courtyard with a covered walkway that creates a modern cloister. CLT expertise and the relationship between Engenuiti and KLH developed an offsite, prefabricated composite glulam beam and CLT slab ‘ribdeck,’ to provide an elegant and aesthetic solution to the first-floor walkway around the double-height atrium –removing 8,600 kg of painted steel from the reference scheme and using much less timber than a simple CLT slab.
The first of two phases, the design allows for future additions, planned for when the senior school expands. Customisation of standard CLT elements achieved a beautiful bespoke environment, tailored to the school’s needs and the site. The design celebrates the techniques used to build it: the exposed timber structure knits the building into the mature landscape and internally and brings proven wellbeing benefits. The school’s need to remain operational throughout led to early selection of CLT, combined with digital design techniques and BIM Level 2 protocols. This decision was to become pivotal in mitigating a three-month delay in starting on-site due to the first COVID-19 lockdown.
1The project is an exemplar in sustainability with an A-rated EPC. CLT’s thermal qualities add to the overall performance of the building and its natural air permeability give it an almost Passivhaus level of performance, significantly reducing the operational cost/carbon of heating the school. Caroline Purdom, Bursar, Crosfields School said: “The design that we have developed together has created an amazing space for teaching and learning. Our teachers, support staff, parents and students have simply been ‘wowed’ by the open, light, modern building that is now the heart of our new senior school.”
For more information visit: www.engenuiti.com
Images: 01-02. Crosfields Senior School has been transformed using CLT and offsite digital design. Courtesy Engenuiti
Our products and people continue to serve the housebuilding and construction industry with a wide range of wood panel products.
West Fraser trading as Norbord Europe Ltd.
uk.westfraser.com
James Withey, Managing
Directorat Algeco Offsite Solutions, examines the role offsite manufacturing could play in offsetting the Governments investment cuts, keeping UK construction on track to deliver on its targets.
In its autumn budget, the UK Government announced cuts to public funding affecting many parts of the economy. Although most big-ticket infrastructure projects escaped the chop, and health, education, defence and justice all kept or increased their budgets, the construction industry is still operating in a challenging economic climate. As the sector attempts to negotiate these difficult headwinds, there are questions over whether the tough targets set out in its Construction 2025 strategy are still achievable.
The global construction market is forecast to grow by over 70% by 2025, and with that growth will come new opportunities for the UK sector. In its strategy document, Construction 2025,
the UK government set out a blueprint for developing the industry, with an emphasis on reducing costs, increasing efficiencies and cutting greenhouse gas emissions. The strategy, when it was announced, set out the following ambitious targets for the sector to achieve by 2025:
• 33% reduction in the initial cost of construction and the whole life cost of assets
• 50% reduction in the time from inception to completion for newbuild and refurbished assets
• 50% reduction in greenhouse gas emissions in the built environment
• 50% reduction in the gap between exports and imports of construction products and materials.
The latest round of funding cuts and price inflation, combined with these challenging targets, will make for a difficult operating environment for businesses in the construction sector. However, new challenges give rise to new ways of thinking, and front-runners in the industry will seek innovative new ways to increase efficiencies and reduce emissions, without compromising on quality.
Leading the way will be proponents of offsite manufacturing, which is cited in the Construction 2025 report itself: “As demand for low carbon and sustainable construction continues to increase, the potential of offsite construction to deliver assets with half the waste and 25% less energy in use will make it an ever more attractive option.”
There’s a broad consensus across the industry that modular and offsite construction, or Modern Construction Methods (MMC), has numerous benefits over traditional methods, offering a faster way to deliver high quality new buildings, by maximising efficiencies at every level. What’s more, compliance with building regulations is easier to manage and waste is minimised, making modular building a more environmentally friendly option.
In terms of public sector priorities, we believe that the urgent and impending needs of education, health, justice and defence can often be satisfied directly via MMC or indeed as a hybrid solution.
What’s more, with its lower costs and reduced emissions, offsite construction may well be the only way for some projects to meet budget, which has been made more difficult by recent material price rises as well as the targets set out in Construction 2025.
But is it possible to take offsite a stage further, in order to deliver even more efficiencies across the board? Our multi-award-winning Seismic platform, uses the principles of MMC and DfMA to unlock the benefits of standardisation and efficiency, driving a major shift towards a more productive, better quality and lower carbon construction industry. Ultimately, its purpose is to deliver quality buildings that can be delivered within shorter timescales.
The new Cockburn Laurence Calvert Academy school in Leeds, which is currently under construction, is a live example of how the Seismic platform works in practice, and how it aligns with the government’s push for more efficient solutions. Acting as principal contractor, we are providing a full turnkey solution at the school, involving construction of a three-storey whole school block and associated external works. Work began on site in June 2022, with a planned completion date of August 2023.
We are using the Seismic platform on this project, which means that the new school will be completed sooner than a conventional modular build, whilst offering significantly lower carbon impact and much better value than traditional construction. Analysis
shows that a standard Seismic module comprises 581.3 kgCO2e per m2, well below the Construction 2025 target of 1,300 kg CO2e per m2. In addition, because Seismic can be reused, either by relocating modules to other sites or by refurbishing individual components and cassettes, it adds a 234 kgCO2e per m2 clawback. This brings Seismic well beyond even the lowest stretch targets being discussed in construction today.
In summary, standardised, offsite construction platforms offer publicly funded projects a way of delivering high quality buildings in less time, at lower cost, with reduced waste and
fewer emissions. The current economic climate requires us all to achieve more with less, whilst still reducing emissions. Offsite construction platforms, combined with DfMA and lean manufacturing are clearly sensible approaches which could form a significant part of the solution.
For more information visit: www.algeco.co.uk/permanent
Images: 01. Cockburn Laurence Calvert Academy School, Leeds 02-03. Hatchlands Primary School
Never in our history has the construction industry been so ripe for disruption to its practices and processes. On behalf of Seismic Group, Richard Crosby explains how a platform approach and offsite technology can play a central part in that change.
Although the automotive industry is often cited as an example of how construction should become more efficient, the financial model is simply not comparable. Construction companies and their suppliers cannot afford to spend billions on the development of individual platforms before producing a single product, but it can get there through a collaborative and iterative process. To help facilitate this we have developed the Seismic platform which is the primary case study within the Platform Rulebook and qualifies on all eight requirements to be officially termed as a platform.
The availability of technology combined with rising prices and skills shortages create a culture for change. The need to meet net zero carbon targets together with worldwide economic uncertainty could be a driving force to transform outmoded construction methods. The faster pace of change means we not only need to view our built environment in a different way, but we also need to deliver it differently, more efficiently, to better value, and higher sustainability standards.
The Construction Playbook sets the guidelines to facilitate change in one of the UKs largest industries. The guidelines present an opportunity to change mindsets and cultures in how to procure, design, and deliver our
social infrastructure for the betterment of all. Construction is an industry not known for its appetite for change. Business models have developed around processes and practices that have been around for centuries. It is a huge task but if we all embrace these guidelines change is certainly possible.
The construction industry must be the only major industry that has not embraced platforms in some way shape or form. Almost everything we use today is based on a platform, our phones, our cars, our clothes, even our kitchens, so why not our buildings?
The Platform Rule Book together with the Construction Playbook is a real eye opener for what is not just possible, but what is actually starting to happen.
1Originally developed by a collaboration of industry partners; McAvoy Group, Algeco and Tata Steel together with academic associates, The Manufacturing Technology Center (MTC), Specific (Swansea University and The National Composites Centre) and funded by UK Research and Innovation (UKRI) – the Seismic Group has been established to make the patented technology widely available and to encourage participation to help facilitate a platform approach across the industry.
Critical in doing so is engagement of the light gauge steel industry which is driving the adoption of modern methods of construction (MMC) across all sectors. The latest revision to the Playbook – ‘Embracing the Circular Economy’ certainly plays to the advantage of steel.
The use of a patented connector block supplied by Seismic Group via a network of approved suppliers negates the need for hot rolled steel sections other than the vertical posts and significantly reduces the volume of steel and labour required.
It enables cross-market and crosssector connectivity. The Seismic Group offers management consultancy services to assist in its adoption. Benefits of the platform include the standardisation of dimensions that de-risk projects for clients who would prefer not to commit to a contractor until the design is fully developed and costs are known, thus taking a greater share of the traditional market.
The Seismic Group are now working with the light steel frame industry to provide the floor cassettes to both tier 1 and tier 2 MMC contractors with particular interest from volumetric modular providers. The cold formed sections creating 2D floor cassettes can be provided fully accessible or in a kit of parts ready for assembly.
The Seismic Group launched to the market in line with the introduction of the Platform Rulebook and has already seen huge interest particularly from client organisations and advisors with large scale projects that are too big for any one provider or those who do not want to be contracted to one specialist before prices are agreed.
For more information or to get involved in the Seismic Platform, contact: richard.crosby@sesimicgroup.co or visit www.sesimicgroup.co
Images: 01. The Construction Playbook and the Platform Rule Book together set the guidelines to facilitate change across the construction sector 02-03. Technological innovation is at the heart of the Seismic approach
There is a strong demand for brick cladding from offsite suppliers due to its suitability alongside modular construction methods.
At Aquarian we have three solutions, each with their own unique benefits for modular construction, including speed of build, product consistency and unlimited design capabilities. If you want an authentic clay brick façade on your modular project, we can provide it.
The Housing Forum has published a new supplementary guide that offers advice on how to procure in a ‘hyperinflationary’ environment and will be of interest to all home developers.
start on-site by appointing contractors from frameworks.
With inflation now at a 40 year high of 11.1%, fuelled by rising energy costs and global supply chain difficulties, it has created an extremely tough landscape for procuring construction work, threatening the prospects for new housing development. The Autumn statement offered little by way of help for the housing sector facing rising costs and an uncertain market.
Last year The Housing Forum published the Better Procurement for Better Homes Guide. They have now published ‘Better Procurement for Better Homes Supplementary Guidance’ to help the sector to cope with these new inflationary challenges
The key audience for the new supplementary guidance is local authorities and housing associations who are seeking to procure new homes in the current economic climate. The guide may also be of interest to developers, contractors and consultants looking to work in partnership to develop housing or tendering for work, and to policy makers and regulators who need to understand the challenges facing social housing developers bidding for funding.
Key messages from the guidance include the importance to build trust and work with contractors who share
values of commitment to quality, are willing to work in an open book environment and demonstrate a collaborative approach reduces risk. It is also critical to closely involve the finance and procurement teams –whole-team decision making needs to be a dynamic process, with budget holders updated and alerted as soon as inflation looks to be adding cost pressures that threaten to breach contingencies. Managing risks equitably between commissioner and contractor and acknowledging that some sort of price fluctuation (both up and down) will have to be accommodated over long contracts is recommended alongside the age old need to engage early with the contractor’s supply chain and enabling quicker on decision making.
When appointing the contractor/ supply chain, the supplementary guidance points out: “The main principles set out in Better Procurement for Better Homes of appointing main contractors and the supply chain early are even more critical in a hyperinflationary market. Appointing the contractor at the earliest opportunity (potentially at the pre-planning stage) under a flexible partnering contract, or using a PCSA, is vital to manage design and risk and optimise use of Modern Methods of Construction (MMC). Clients can aim to reduce the time from appointment to
“Firms on these frameworks will have already been cleared against certain criteria – and clients can take comfort that these firms will have had to have demonstrated, amongst other things, financial probity and a good health and safety record. As in our original guide, bringing the supply chain in early also remains a high aspiration, but this is likely to prove difficult in the current landscape, and the process of bringing on board suppliers is likely to be spread out for a much longer period.”
Matthew Goulcher, Managing Director of Levitt Bernstein and Chair of the Housing Forum Working Group which produced Better Procurement for Better Homes as well as the new supplementary guidance said: “The 40-year-high inflation rate, fuelled by rising energy costs and global supply chain difficulties, has resulted in an extremely tough landscape for procuring construction work, as contractors and their specialists become reluctant to commit to fixed prices too far in advance of work starting. This has profound implications for clients trying to plan and budget for work. Our new guidance will help steer through these obstacles.”
Shelagh Grant Chief Executive of The Housing Forum added: “Our new supplementary guide, which is based on the vast practical knowledge and experience of The Housing Forum’s extensive membership, will prove a tremendous boon to housing associations, councils and commissioners who may be considering pausing developments in these very challenging times.”
The publication: ‘Better Procurement for Better Homes Supplementary Guidance’ is available at www.housingforum.org.uk
a mission is to revolutionise construction and change the way houses are designed, manufactured, procured and built. COLAB and its DfMA Toolkit is providing several answers to the UK’s housing crisis.
COLAB is an interdisciplinary consortium of forward-thinking organisations at the cutting edge of innovation in the construction industry.
Led by L&Q, alongside partners Virtual Viewing, HTA Design, and Hawkins\ Brown, the consortium was awarded funding by Government's Innovate UK under the ‘Transforming UK construction round 2: MMC, digital and whole-life performance’ competition to develop a digital solution addressing the key issues facing the construction industry.
The DfMA Toolkit is a digital application enabling housebuilders and their design teams to store portfolios of offsite manufactured products – from bathroom pods to house types – to source materials, capture in use data and inform decision making for future projects. Key to this is moving away from traditional project specific solutions to building homes, and towards a portfolio and product-based approach – adopting a manufacturing mentality.
As construction increasingly looks to technology for solutions that create efficiencies, the DfMA Toolkit can give stakeholders in our sector a betterinformed understanding of MMC and DfMA to enable them to take the right strategic decisions enabling change, transformation and innovation.
DfMA and MMC approaches can help speed up construction times whilst enabling the delivery of consistently high-quality homes.
The DfMA Toolkit demonstrates how these methods can be used in practice to achieve tangible results. Features include a DfMA design guide to upskill the industry, an MMC product portfolio to store and manage offsite products, a mapping tool to identify and locate MMC suppliers and a business intelligence platform for metrics and analytics that advance DfMA and offsite adoption.
Launched in December 2021, the Toolkit has been a key step towards developing and adopting a standardised house type portfolio within L&Q. The team have been able to interrogate highly detailed 3D models by selecting desired configurations and features on individual house types. This has increased the team’s understanding of the house type and the variations available on key elements of the house, which demonstrates the improvements being seen as a direct result of the Toolkit.
It is estimated that wide adoption of the Toolkit could speed up design and construction programmes by 30%, providing total savings of around 25% to housebuilders. Toolkit stakeholders are working towards adopting it within their organisations, recognising the potential impact it can have on future projects, consolidating their own product portfolios and better understanding BIM data, golden thread potential and ways of displaying complex information digitally.
L&Q is one of the top three largest Housing Associations in the UK. With an existing stock of over 120,000 homes, with 100,000 in the pipeline, the business has identified MMC, offsite and DfMA as key components of its delivery strategy.
Virtual Viewing is an award-winning studio specialising in software solutions and applications in the construction sector. Their innovative portfolio of solutions builds on the use of BIM, VR and AR.
HTA Design are housing design specialists at the leading edge of offsite construction in the UK.
Having completed several volumetric modular buildings in London their interdisciplinary collaborative approach and DfMA expertise are key in advancing innovation in UK construction.
Hawkins\Brown is an internationally renowned, award-winning architectural practice, with a wealth of experience in designing and delivering innovative and socially sustainable buildings. They have a fresh collaborative approach to every design challenge, developing workflows to take designs straight into manufacture.
For more information visit: www.thedfmatoolkit.com
Images: 01-02. The DfMA Toolkit is a digital application enabling housebuilders and their design teams to store portfolios of offsite manufactured products
With
A light gauge steel frame from Sigmat is at the centre of a new flagship development near the centre of Norwich that is breathing new life into riverside living.
Canary Quay is a four-phased, light gauge steel-framed development of 323 high specification riverside apartments on the River Wensum. Phases 1-3 comprise 222 one and two-bedroom apartments in three separate developments which were completed in May 2021. The remaining 101 apartments of Phase 4 are planned to complete in December 2022. The development will contribute significantly to easing the pressure on housing waiting lists and will help those needing housing.
The development has been built for Broadland Housing Association who have over 5,000 social and sharedownership homes under management throughout Norfolk. Phases 1 and 3 are being offered as social housing and Phases 2 and 4 will be a combination of Broadland Housing tenants and private owners.
RG Carter were chosen as the contractor for this project because of their experience of and expertise in high-rise developments and twostage tenders and an exemplary
record of client collaboration, project deliverables and reliability. A Sigmat steel frame was selected due to its environmental, programme, logistical and commercial benefits. Challenges included dramatic changes to labour logistics with the start of COVID-19 in early 2020, M&E clashes, steel supply issues and residents onsite as the phases progressed. These were overcome with resequencing and regular, close liaison with the design team, M&E contractors, suppliers, residents and the client with each phase being completed on time and on budget.
The use of the light gauged steel frame Sigmat system eliminated the requirement for secondary infill steel to the external wall. The system has the external wall pre-panelised offsite and includes the formation of all structural openings in the façade. A key benefit of a project built with the Sigmat system is the ability for it to be re-used and repurposed at its end of life. After demolition many elements of the building are usually sent to landfill. With a Sigmat frame however, all the steel components can be reused and recycled, even the concrete in the floor slabs can be crushed and used again as an aggregate in lean mix concrete.
Most of the project team have been together from the start of the build and have used their skills, ingenuity
and teamwork to overcome a number of challenges and keep the project on budget and on time. In recognition of the skill and experience applied to this project, Canary Quay was visited in March 2022 by Caroline Gumble CEO of the CIOB who wanted to see an example of an exemplary project using a light gauge steel frame system. They were interested to understand more about the speed and efficiencies it has brought to the scheme.
Canary Quay was one of the first uses of light gauge steel frame in Norwich. The spacious apartments all have balconies, river or garden views and are fitted with hi-spec bathrooms and kitchens. There is a critical need for housing in Norwich and Canary Quay will help to address the problem by
providing high quality dwellings in an attractive and convenient location for those who need it most. The development is regenerating and opening up a previously run-down area of Norwich that now has a thriving community on the River Wensum with communal spaces and river views for many residents providing a pleasing and positive environment for residents.
For more information visit: www.rgcarter.co.uk www.sigmat.co.uk
Images: 01-04. Canary Quay is bringing four phases of offsite construction and light steel frame technology to a new thriving community.
Courtesy RG Carter
SES Engineering Services (SES), has completed £25million worth of engineering services at The JJ Mack Building, commercial developer Helical’s flagship scheme for sustainability.
Working closely and collaboratively with principal contractor Mace, SES has delivered full mechanical, electrical and plumbing (MEP) services for the 200,450sq ft, ten-storey block in the heart of Farringdon, London – originally referred to as 33 Charterhouse Street. This includes a Category A office fit-out with the latest in integrated building services to make the building ‘smart’ and ultimately, more energy efficient.
Smart technology includes making variables like heating, lighting and security accessible on one network, giving the end user real-time updates of usage and allows them to control the entire building using just one platform.
This innovation has meant that the JJ Mack Building is on track to achieve a BREEAM rating of ‘Outstanding’ –Helical’s first commercial offering to do so – as well as a NABERS five-star rating. It has been designed with sustainability as a priority from its conception, to support the developer’s ambitions of having all newbuilds net zero carbon in operation by 2025.
The scheme prioritises end-user operation. SES worked closely with all delivery partners and stakeholders – including facilities management company, Ashdown Philipps – to ensure all services were integrated correctly, while an extensive digital twin model was used to ensure seamless assimilation.
Offsite construction was vital to construction with the company’s bespoke offsite manufacturing facility, PRISM being utilised to help design, build and deliver pumps skids, floor service modules, duct work riser modules and the largest and most complex mechanical risers that the facility has built to date.
Steve Joyce, Managing Director at SES Engineering Services, said: “Smart buildings are revolutionising the commercial sector as the potential to reduce energy costs and personally manage usage becomes an incredibly attractive option to end tenants. Providing this service seamlessly is a true test of engineering ingenuity and
we pride ourselves in being able to deliver this capability to clients to such a high standard.
“As well as our technical expertise, our prior working relationship with both Helical and Mace has been invaluable. Integrating complex building systems relies on early stakeholder collaboration. Already being onboarded with their teams, fully aligned with their goals and ways of working helped streamline delivery and, alongside our offsite capability, has played a large part in successfully handing over this scheme ahead of schedule.”
1SES MEP Installation commenced in July 2021, with handover achieved on 30 September 2022 – finishing on programme.
Frank Connolly, Operations Director at Mace, said: “The success of this project is directly attributed to the teamwork and understanding of both Mace and SES project teams. The positive attitude set by senior SES management has influenced the SES site team and their supply chain, setting a constructive and supportive attitude on site. It has been a pleasure to work and deliver this fantastic project with SES and Prism.”
Pavlos Clifton at Helical, added: “Working with trusted companies like SES has allowed us to explore our aspirations to challenge construction methodologies to find better solutions to deliverability. The team understood what we were trying to achieve and had the in-house support and capability to deliver what we wanted. In that way it was mutually beneficial to both our businesses, which is the best working relationship.”
The JJ Mack Building is the latest build to demonstrate SES’ capabilities in delivering smart buildings, with the company currently delivering other smart projects including 4 Angel Square, at the NOMA development in Manchester.
For more information visit: www.ses-ltd.co.uk
Images: 01-02. Offsite MEP services have helped deliver a smart and sustainable building
Construction of a new Urgent and Emergency Care Centre at Walsall Manor Hospital has adopted an offsite approach to MEP provision to award-winning effect.
The new Urgent and Emergency Care Centre at Walsall Manor Hospital is to replace the current building whose physical environment struggles to meet increasing patient flow demands. The new development, which has maximised MEP offsite engineering, incorporates a new emergency department with ‘front door’ access to a new Urgent Treatment Centre and Paediatric Assessment Unit with the first floor accommodating a new Acute Medical Unit.
The new multi-million-pound facility has significantly embraced offsite engineering strategies for the MEP services resulting in enhanced programme delivery, improved health and safety, increased supply chain collaboration and efficient sustainable delivery. With offsite manufacturing and lean construction rooted within main contractor Tilbury Douglas Engineering’s culture, offsite solutions were embedded in the delivery strategy for safely, efficiently, and sustainably delivering key MEP elements of the project.
Taking advantage of pre-manufactured solutions to provide the Trust with low-risk, repeatable results in controlled environments, the project was also an early adopter of the NHS MMC Business Case compliance requirements acting as another driver for maximising MEP MMC offsite opportunities.
The offsite strategy was reviewed during the preconstruction phase undertaking specific MMC/offsite workshops and opportunity and risk analysis to identify areas where offsite solutions would add value to the MEP installation resulting in the delivery of 120 horizontal floor modules, packaged plantroom skids for LTHW plant/pipework, pumpsets, boosted cold water, medical gas plant skids, 50 prefabricated distribution boards
and 110 prewired and pre-plumbed bedhead trunking units.
Moving into the construction phase, collaboration was required between the offsite partners, plant suppliers and key sub-contractors including ductwork and thermal insulation, and controls. Plant skid and module manufacturing programmes were collaboratively developed with all stakeholders in line with the overall construction programme. Collaboration of suppliers and subcontractors was undertaken at the offsite manufacturing facility for production of the corridor modules and plant skids which required subcontractors to integrate into partners manufacturing, H&S, and delivery processes.
The offsite approach has promoted collaboration across the supply chain for integrated delivery of the offsite elements. Specific examples include integration of key supply chain members into an online BIM collaboration environment for module co-ordination as well as collaborative factory manufacturing programmes and factory installation processes. The offsite approach has enhanced sustainability through reduced carbon impact from site deliveries and site trades travelling to site totalling a saving of 7.73 tonnes of CO2
The factory fabrication has reduced on-site risk of injury by removing 7,000 hours offsite of which 5,355 were working at height which we always look to minimise where possible due to the increased risk. The offsite MEP solutions enabled programme acceleration of the MEP services whilst the build elements were simultaneously being constructed without MEP trade impediment/ co-ordination. Overall, this saved 7,000 hours on-site equating to a programme efficiency of 18 weeks.
The new facility will enhance clinical staff efficiency, provide improved quality of care, improved patient experience, and a much-improved working environment for staff. The overall project and offsite solutions are being delivered within budget and the project is on target for successful timely completion.
For more information visit: www.tilburydouglas.co.uk
Images: 01-03. The MEP installation resulted in the delivery of 120 horizontal floor modules.
The award-winning MFS i-Form Solution™ is helping drive forward the concept of P-DfMA for offsite manufacture and building design.
The Masonry Frame Systems (MFS) team have formulated an offsite construction rationale, which has been trademarked as the MFS i-Form Solution™. This combines large scale calcium silicate elements and precast concrete components with an offsite methodology to drive forward a suite of 'platforms', or standardised and repeatable offsite components. This enables the delivery of a bespoke solution to the client's needs, in terms of building function and site demands.
The MFS i-Form Solution™ was trademarked in 2020 and is a highly engineered construction process, best described as a platform for design, manufacture and assembly (P-DfMA) approach.
Platforms – this is a tried and tested suite of construction components – or standardised and repeatable platforms
Design – digitally designed in BIM to enable highly efficient construction and high-performance buildings for end users – without any compromise to the architect’s vision
Manufacture – over 90% of all components are manufactured offsite, using methods that minimise the reliance on cement in the precast concrete components
Assembly – delivered as a complete kit of parts for easy, swift and costeffective onsite assembly, with 80% less labour and up to 200% faster than traditional build.
Masonry Frame Systems are a specialist frame contractor with the i-Form Solution™ applied to everything that they design, manufacture and assemble and see the construction industry as a “low volume, high variety” industry with pretty much every project unique or bespoke to its environment or surroundings. One of the big advantages of the system is that it can be tailored to each project, specifically. The i-Form Solution™ is a masonry and precast concrete solution, combining the benefits of a suite of standardised calcium silicate or concrete components that can flex to bespoke designs, with all the cost, time and sustainability benefits of a volumetric or modular construction.
The MFS i-Form the combines Xella elements with precast concrete, such as floor planks, staircases and balconies, where we pre-stressed Hollowcore technology is used, which maximises strength, but minimises the need for cement. So, the system makes the most of concrete technology to achieve the highest technical achievements but with sustainability and the environment as primary drivers.
Core to the i-Form Solution™ is offsite manufacture and sustainability. By constructing the whole structural envelope of a building, from ‘oversight to weathertight’, using offsite methodology savings of time and money can be delivered (typically 20% saving on the overall build programme) for clients and provide a high-performance solution.
For more information visit: www.masonryframesystems.co.uk
Images: 01-03. The MFS i-Form Solution™ is bringing a new dimension to offsite concrete technology
Anne Daw, Associate and Head of MMC Delivery at HLM Architects on a few reasons why the Platform approach to Design for Manufacture and Assembly (P-DfMA) can deliver ambitious construction targets.
“Platforms can accelerate industry transformation by boosting quality, speed, outcomes and performance. The Product Platform Rulebook is a very positive step forward. It outlines a set of open-access rules and principles to create a common set of standards and processes for the industry to collectively develop product platforms and drive efficiencies, as well as societal and environmental benefits. It mandates that platforms must be deployable, configurable, and open – comprising repeatable, standardised assets with interoperable components.
“By harmonising repeatable features into a ‘kit of parts’ accessible to all, organisations can share knowledge, components and processes across a wide range of solutions and sectors, bringing economies of scale. This approach replicates what we’ve seen in other industries, such as aerospace and manufacturing, and can work to overcome challenges in the fragmented construction industry including lack of standardisation, productivity, quality and predictability. The platform approach will not only optimise the fabrication and installation elements of construction but will also free up architects to be creative and focus on designing high-quality projects tailored to specific needs while automatically meeting all technical, sector-specific requirements.
What the Product Platform Rulebook delivers is a set of common guidelines to bring clarity on how platforms can be successfully adopted at scale. Platforms can bring significant advantages, such as improved cost efficiencies through standardisation of solutions, faster delivery of projects, and safer conditions for workers on-site. They can also reduce the huge waste seen in the construction industry, which contributes 11% of all carbon emissions globally. We have no choice but to look at new options and accelerate innovation – it’s the only way for the built environment to reach net zero. Without embracing new models such as the platform approach, we will miss crucial environmental targets.
An industry-wide platform approach significantly streamlines and simplifies the process, with key connections and details decided upfront. The platform approach allows the advantages of MMC, which have been spoken about for years – such as using 67% less energy than traditional construction and being significantly faster – to fully materialise within the wider construction industry.
www.hlmarchitects.com
As Alex Micallef, UK General Manager at Graitec explains, the take-up of digital technology must accelerate if offsite methods are to move mainstream.
While progress has been made in recent years, driven largely by the swathe of emerging and existing issues exerting pressure on outputincluding the COVID-19 pandemic, skills and materials shortages and looming net zero carbon targets - the pace must quicken if Modern Methods of Construction (MMC) are to become mainstream.
MMC is playing a growing role in new buildings coming forward - not just homes, of which 20% are expected to be built using MMC by 2030, but across both commercial and residential developments, from hospitals and schools through to offices. Digital technology is central to the delivery of these new, next generation MMC schemes, from design and costing through to day-to-day delivery
and development, with Building Informational Modelling (BIM) software like Revit utilised throughout the entire lifecycle of a project.
While our team has seen growth in the uptake of software within the construction industry - from developers and architects through to engineers and project managers - there remains a general lack of awareness within the industry around the benefits technology can provide (including speeding up delivery, preventing mistakes, improving accuracy and reducing margins for error) as well as capabilities of new and emerging digital platforms and software. We spend a lot of time working with teams to embed new technology and educate on its scope and the capabilities it brings to the table.
As a construction software expert, our goal is to help digitise construction, manufacturing and fabrication, streamlining processes and improving performance. The conversations we are having demonstrate that the appetite is there to deliver genuine digital transformation - along with the understanding that it is no longer a choice, but an inevitability.
To put things into perspective, a recent report from GlobalData revealed that 36% of companies lack the financial budget for technological innovation, while 28% blame a lack of awareness of new technology. In addition, 34% feel that they lack sufficiently skilled labour to adopt technology. There remains a great deal of work to be done in encouraging the industry to not only adopt new digital technology,
but to ensure that software is being optimised and used to the best effect.
Digital technology is a welcome new addition to the Construction Playbook
The government recently included digital technology as a key component of its updated Construction Playbook while continuing to spearhead the adoption of MMC. The drive for MMC in government projects was reiterated in the latest Playbook, backed up with the introduction of new targets for the adoption of new building techniques alongside a presumption in favour of offsite construction. It’s positive to see the inclusion of digital technology within the guidelines, with the government continuing to lead from the front - particularly in highlighting the importance of ‘data interoperability’, ensuring that project partners can work more collaboratively and effectively with each other.
Ending the reliance on outdated tools Unfortunately, there are still many businesses working from excel spreadsheets - either unaware of the capabilities that digital technology offers or due to a reluctance make the shift to new processes and workflow management. Yet much of the software that would make a real difference to big picture challenges is very simple to install and adopt - such as cloud production applications, for example.
Cloud technology helps to improve productivity and streamline interaction between project teams, helping to prevent errors and ultimately accelerating the delivery of development. It’s a simple piece of kit that delivers enormous benefit. Similarly, BIM tools are an essential component of any new scheme coming forward, yet the technology is still, in many cases, not being used properly or to best effect. Through this lens, it is easy to see why more advanced tools, such as automation, robotics and mobility, are still not properly understood.
Adoption of digital technology must be a key focus for 2023
The adoption of digital technology is an essential component of the wider shift to MMC in the UK - both MMC and technology are key to tackling the many challenges facing the construction industry, from the ongoing skills shortage and reducing carbon output as well as business
Recognising the industry’s need for improvement in accuracy, efficiency and data co-ordination, Trimble has revealed a range of new features and enhancements for its 2022 Tekla PowerFab steel production management tool.
The updated 2022 version of Tekla PowerFab includes an array of new features, one of which is the ability to change the status of elements that are currently within the production process. If the status of a drawing changes or if something is flagged, fabricators can now put elements ‘on hold’ and halt the production process. The ability to temporarily pause production of a particular component then allows both the drawing office and those on the shop floor to implement an effective change management process and decide whether the item needs to remain ‘on hold’ or if fabrication can resume. This new functionality helps contribute to a reduction in waste and rework - critical given the emphasis on sustainability and reducing carbon emissions.
Speaking about the software update, Chris Gatehouse, Account Manager Detailing & Manufacturing at Trimble, said: “It’s a tool that really does align the entire workforce efforts, helping to automate those time-consuming tasks (critical during a time with skilled labour shortages), giving fabricators access to the project data they need when they need it, enabling them to monitor and report on production, and deliver a more productive, streamlined and sustainable process.”
For more information visit: www.tekla.com/uk
critical short-term challenges such as the impact of inflation on margins, the subsequent value engineering in the design and delivery of projects and ensuring that new schemes remain viable.
Moving into 2023, leaders must champion the adoption of technology in construction, forming teams with the skills and knowledge to ensure that software is being operated efficiently and to its maximum potential. Embedding technology throughout the construction process will encourage new innovation, expand development capabilities and move
the MMC agenda forward in a more meaningful way.
For more information visit: www.graitec.com
Images:
01. Alex Micallef, UK General Manager, Graitec
02. Digital tools are making offsite methods even more efficient
03. The updated 2022 version of Tekla PowerFab includes an array of new features, including the ability to change the status of elements that are currently within the production process
Sophie Weston at Geberit, explores how wall-hung sanitaryware can open up a world of design possibilities for pod and modular manufacturers, while driving efficiencies and cost savings across bathroom projects.
With customers increasingly looking for cost-effective and complete bathroom packages that boast both quality and design excellence, Geberit’s range of space-saving ceramics and bathroom furniture offer a range of different styles and options for any budget or project.
Wall-mounted furniture and ceramics, which create the illusion of ‘floating’ above the floor, can offer a spacesaving solution that opens up the space and creates a streamlined design.
The premise is simple. Wall-hung toilets are made possible in bathrooms thanks to the inclusion of quick and affordable pre-wall frame systems, such as Geberit Duofix. By concealing the cistern behind a stud wall, a wall-hung toilet reduces the outward projection of the ceramic.
In smaller pods, opting for wall-hung ceramics can make a real differencethe ability to conceal the cistern and lift the toilet’s footprint off the floor can make even the smallest of bathroom spaces instantly appear bigger.
Servicing and access to the cistern is also made easy via the flush plate.
Opting for wall-hung sanitaryware can also offer operational benefits across commercial projects. Lifting the toilet from the floor makes maintenance and cleaning much easier, helping reduce dirt and dust accumulation – in turn, this can help commercial customers reduce any associated staffing and maintenance costs.
With more than 10 models available, Geberit’s Duofix wall-hung frame system, together with the wide range of wall-hung ceramic furniture, pod and bathroom manufacturers will find a wall-hung solution for any project.
Back-to-wall toilets offer another space saving option for modular and bathroom pod manufacturers. Instead of installing a wall-hung frame, the WC stands on the floor with the cistern is concealed inside the wall or furniture. These designs, just like wall-hung, are space-efficient by reducing the outward projection of the ceramic and offering a streamlined design.
Both Geberit’s wall-hung and backto-wall ceramic ranges boast features such as soft closing seats, water saving flush options and Rimfree pans for easy cleaning.
Slimline ceramics
Opting for simple, slim design solutions can create valuable space on a bathroom project and unlock value. Geberit’s Selnova Compact and Renova Plan series, for instance, offer a suite of compact and slimline furniture options, including short projection WCs and smaller-depth basins. Both ranges also incorporate a number of smart storage solutions like vanity units, tall shelving and mirror cabinets, helping add value and design appeal to the project.
Putting our customers first, Geberit’s dedicated OEM team work closely with manufacturers, applying their product know-how and technical expertise every step of the way. For more information visit: www.geberit.co.uk/prefab-washrooms
Images: 01-03. Geberit provide a wide range of sanitaryware that can be optimised for pod and modular systems
‘Hybrid’ precast concrete is the term used to refer to concrete products that are partially precast offsite in a factory and then completed with ‘in-situ’ concrete on-site.
For leading supplier Kerkstoel, the two most widely used products are Twin Walls and Wide Slabs – also known as lattice or filigree slabs. Whilst they have been widely used in mainland Europe for many years, these products remain relatively unknown and under-used in the UK.
1Consisting of a thin shell –normally 60mm of factory-cast concrete containing the lower layer of reinforcement plus lattice reinforcement – which gives the element rigidity during lifting and on-site casting and acts as support for the top layer of reinforcement which is placed on-site before the upper layer of concrete is poured. Wide slabs can also incorporate pipework to create ‘activated’ flooring, allowing warming or cooling of the building taking advantage of the thermal mass of the concrete. This is one of the most energy efficient methods of doing this.
Twin Walls
Essentially, two wide slabs connected by the lattice reinforcement with a gap of 60mm or more between the skins, which is filled with concrete on-site. The precast skins contain all the reinforcement. The twin walls can also incorporate an insulation layer if required. All the products are custom
made to the customer's requirements and can incorporate openings for doors, windows and electrical boxes, ducting etc.
Structurally they are practically the same as cast in-situ concrete with extremely rapid on-site construction where a team of three can typically install 200sq m of walls or 400sq m of slabs per day. With high quality and accuracy due to factory production plus little waste, they are lighter than solid precast panels for craneage and transport and with just in time delivery – little or no on-site storage space required.
For more information visit: www.kerkstoel.be/en/home
Images: 01. NO6 East Village, London, where 7,000sq m of walls were delivered for MACE (PCE), as part of their unique modular hybrid building method
If you are interested in learning more about offsite construction and the associated manufacturing processes then the following industry events may be of interest:
2023
07 & 08 February Modular Matters
NCC, Birmingham
www.modularmatters.co.uk
Modular technology is ever evolving and to help keep pace with this fast-moving sector, Modular Matters demonstrates how to tackle industry challenges through a range of project case studies, innovative architecture and building design together with net zero. Presenting an insight into the future of construction, this event represents a great opportunity to gain industry intelligence and network with those who are at the forefront of the volumetric modular sector.
07 - 09 March
Futurebuild
ExCeL, London
www.futurebuild.co.uk
Futurebuild provides the stage for inspiring ideas, innovative solutions and knowledge sharing to drive sustainable construction and help us reach our goal of net zero. Your free ticket will give you access to over 400 brands, never seen before innovations, the world-class conference programme and inspirational seminar content curated by over 90 industry partners.
More information coming soon!
The groundswell of interest in engineered timber is driven by both technological advances and concern for the environment and sustainable construction practices. It is undergoing a ‘revival’ where it is used in widespread applications delivering high-quality architecture to the realisation of cutting-edge structural engineering. Experts from the structural timber sector will come together to address timber’s use in the construction industry as a versatile and natural material undergoing a contemporary design resurgence.
www.focusonframing.co.uk
The only specialist event of its kind, Focus on Framing provides a solution for construction professionals looking to gain a greater understanding of the latest advances and best practise principles from sector experts. Through informative speakers and case study presentations the seminar will focus on the fast-track non-combustible solutions that are having a significant impact delivering outstanding buildings across all construction sectors.
www.offsiteawards.co.uk
Returning for it’s nineth year, there will be 25 categories that cover every aspect of the industry from hybrid and modular technology to engineering and installation, ensuring that all aspects of the offsite building process is celebrated - recognising the design and technology that makes these inspiring projects possible.
13 June Tall Buildings Conference Birmingham www.tallbuildingsconference.co.uk
Tall Buildings Conference brings together industry leaders and pioneers, offering a wealth of knowledge and learning opportunities. Providing insight into revolutionary engineering principles, the Tall Buildings Conference gives delegates the chance to engage in invaluable networking and intelligence sharing with those at the forefront of technological building advances.
23 June Structural Timber Awards Entry Deadline Online www.structuraltimberawards.co.uk
Featuring compelling examples of what can be achieved using the most natural and sustainable of materials, the 2023 Structural Timber Awards will be a celebration of not only outstanding projects and inspiring individuals, but the coming together of an industry. 19 & 20 September Offsite Expo 2023 Coventry Building Society Arena www.offsite-expo.co.uk
Offsite Expo brings together those who are driving change in the construction sector. The event will play host to the
Futurebuild provides the stage for inspiring ideas, innovative solutions & knowledge sharing to drive sustainable construction and help us reach our goal of net zero. The exhibition brings together the entire supply chain to showcase, debate and understand the advancements in sustainable construction and the emerging technologies that will make net zero possible.
Futurebuild is taking a stand for a better built environment and is urging companies and professionals throughout the construction supply chain to make a similar commitment by ‘taking a stand’ on an issue they passionately believe will help propel the industry towards a more sustainable future. Join us in taking a stand.
www.futurebuild.co.uk
In partnership with Volumetric Modular Magazine and The Modular and Portable Building Association, this TWO-DAY CONFERENCE and EXHIBITION presents a prime business opportunity to gain insight and network with those who are shaping the future of the volumetric modular industry as it focuses on the latest developments, innovations, and investments in the volumetric modular offsite sector.
2021 Offsite Awards Winner for ‘International Project of the Year’ Image courtesy of FortaPRO