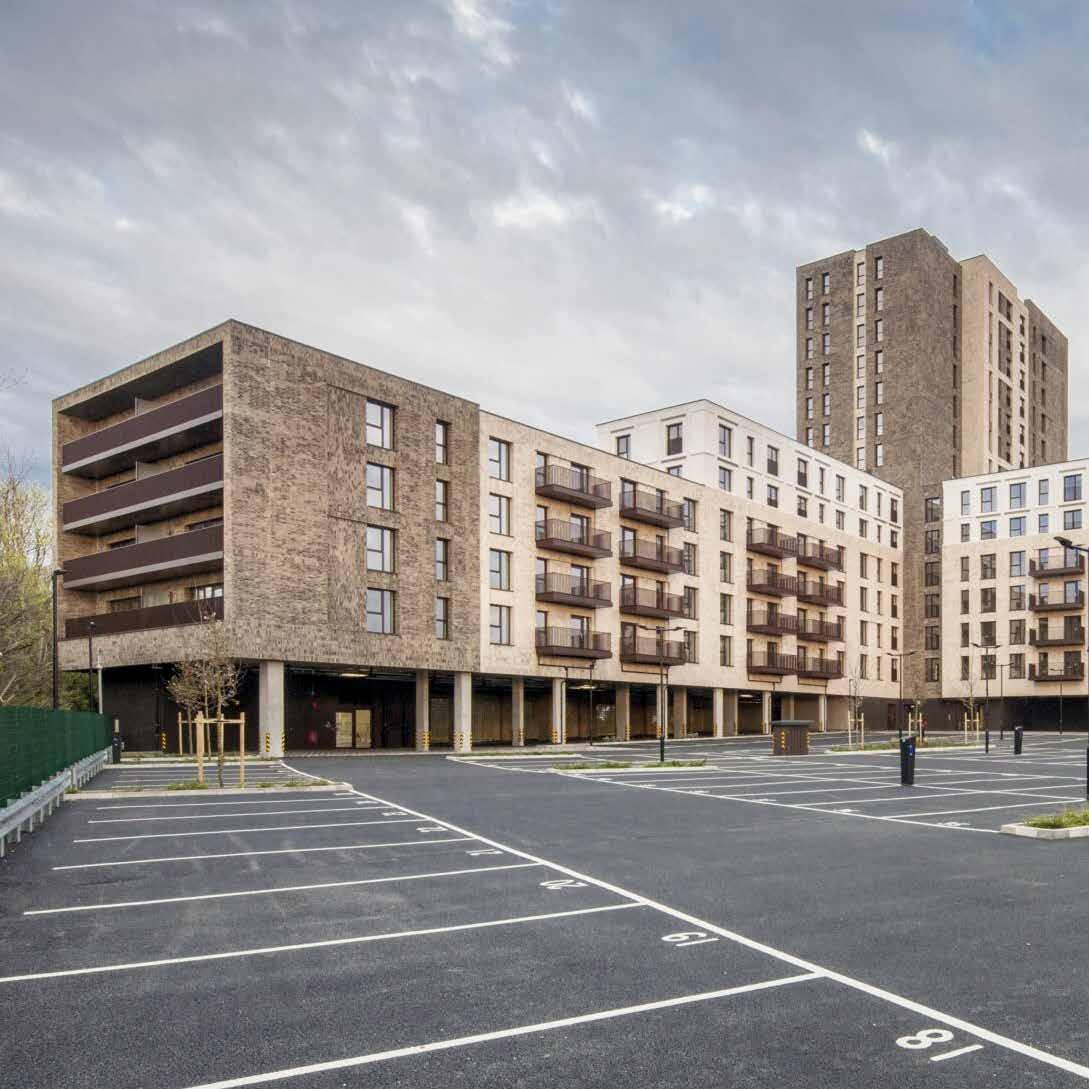


FRONT COVER FP McCann
PRINTED ON: FSC Mix paper by Buxton Press
PUBLISHER:
Offsite Magazine is produced and published by Offsite Media Ltd
101 Longden Road, Shrewsbury, Shropshire, SY3 9PS T: 01743 290001 www.offsitemagazine.co.uk ©Offsite Media Ltd.
SUBSCRIBE TO RECEIVE OFFSITE:
This magazine is a bimonthly publication and the annual subscription fee for UK postage is £29.70 plus VAT for all six issues (£4.95 per copy). Visit www.offsitemagazine.co.uk
ADVERTISING ENQUIRIES PLEASE CONTACT: Julie Williams // T: 01743 290001 E: julie.williams@offsitemagazine.co.uk
SEND US YOUR NEWS: Gary Ramsay // T: 01743 290001 E: gary.ramsay@offsitemagazine.co.uk
BACK ISSUES VISIT: www.offsitemagazine.co.uk
FOR OFFSITE ENQUIRIES PLEASE CONTACT: E: info@offsitemagazine.co.uk
DISCLAIMER: The content of Offsite Magazine does not necessarily reflect the views of the editor or publishers and are the views of its contributors and advertisers. The digital edition may include hyperlinks to third-party content, advertising, or websites, provided for the sake of convenience and interest. The publishers accept no legal responsibility for loss arising from information in this publication and do not endorse any advertising or products available from external sources. The publisher does not accept any liability of any loss arising from the late appearance or non-publication of any advertisement. Content including images and illustrations supplied by third parties are accepted in good faith and the publishers expect third parties to have obtained appropriate permissions, consents, licences or otherwise. The publisher does not accept any liability or any loss arising in the absence of these permissions for material used in both physical and digital editions. No part of this publication may be reproduced or stored in a retrieval system without the written consent of the publishers. All rights reserved.
KEEP IN TOUCH:
@ExploreOffsite linkedin.com/groups/7456674
offsitehub
offsitehub.co.uk/blog
Welcome to the latest edition of Offsite Magazine. This issue covers a lot of ground with a focus on precast concrete and its role in the offsite world plus we have news on the upcoming MMC Ireland event that throws light on what is a clearly vibrant Irish market.
Speaking of events, the recent Modular Matters in Coventry saw two days of discussion on offsite generally but with an obvious focus on the modular aspects. Sadly, the event was bookended by the announcement of Lighthouse and Beattie Passive entering administration. Beattie Passive in particular came as a surprise to many. You don’t need me to tell you that the construction sector is in the doldrums. The result of the building slowdown – forever at the mercy of the residential sector it seems – trickles down to the offsite sector and it is here where the struggle is.
If you are in the education, healthcare or build to rent (BTR) space then the climate is very different. As evidenced at Modular Matters by many speakers, there are all sorts of opportunities in the marketplace where the tried and trusted benefits of offsite design are working wonders. Can the government and public sector do more to help
– well, can’t they always? But the chances of anything happening under the current Conservative political malaise is unlikely. Homes England have come under fire recently for it's perceived wavering support for offsite providers, but its ultimate duty to us – the UK taxpayer – means they need to watch where the money is being invested.
John Fleming’s ongoing high-rise modular success story with Tide and Vision (neatly ‘rebranded’ to Vision Volumetric recently) has a long list of landmark projects including one currently in North Acton, where they are once again working with HTA Design on ‘The Castle’. These landmark buildings need to be spoken of more and how offsite methods – of any type – are driving the UK built environment to better quality buildings. For high profile, you’ll find two fine examples inside sporting ‘hybrid’ approaches – the Salvation Army’s UK and Ireland HQ and within the precast concrete section – Google’s ‘landscaper’ UK home.
Repeated thanks to all our contributors, advertisers, and supporters for their help this issue. We can’t do it without you all.
Gary Ramsay Consultant Editor
Email: gary.ramsay@offsitemagazine.co.uk
• Digital Offsite Magazines
• Online Newsroom
• Monthly Newsletters & Eshots
• Podcasts & Webinars
• Suppliers Directory
• Awards & Events
• Project Profiles
• Offsite Blog
When it comes to maximising thermal performance, look no further. Don & Low’s reflective membranes are the ultimate solution. Reflectashield®, a reflective breather membrane for the cold side, and VapourTX® Thermo, a reflective vapour control layer for the warm side of the insulation, work together to enhance energy efficiency and ensure lasting durability in timber frame, steel frame and modular build-ups.
The housing market is in a period of accelerating change and the need to modernise the way we build to provide affordable and sustainable living has never been stronger. Precast concrete specialist FP McCann is at the centre of addressing these huge demands
With an exciting and developing market, what can you expect to see and hear at the MMC Ireland National Conference 22-23 May 2024? We also posed a few questions to MMC Ireland CEO Paul Tierney about the present state of play in the Irish offsite market.
Questions surrounding the levels of embodied carbon in construction are not easily answered, but new data from Timber Development UK provides new levels of understanding on specifying a wide range of timber products to help hit 2050 net zero targets P79 |
08 | Industry News
News and developments from across the UK offsite industry and wider construction arena including: two more volumetric modular providers exit the market, Tide and Vision continue work at The Castle, David Hurcomb retires as NG Bailey Group’s CEO and Intrastack launch a new low-rise housing solution.
A special section covering one of the offsite sector’s central materials including news, in-depth case study on Google’s ‘landscaper’ HQ, Carlow Concrete, progress at Everton FC’s new stadium and Seamus McKeague, Creagh’s CEO and Joint Chairman talks about its 50 years in business.
26 | BOS: a journey through innovation
Embracing 20 years of evolution, Buildoffsite (BOS) has refreshed its brand identity in preparation for its anniversary in 2024. The transformation reinforces its commitment to innovation, collaboration and leadership within the offsite construction arena.
52 | Blending Heritage with Modernity
Architects and urbanist studio TateHindle has completed work on the new six-storey Salvation Army UK and Ireland HQ in Denmark Hill, London using concrete, mass timber and panelised brick.
56 | Tale of the Task Ahead
19-20 March saw the sixth Modular Matters event take place at its new venue at the Coventry Building Society Arena and saw two days of serious discussion surrounding a sector in flux.
60 | Feeling the Offsite Benefits
The £12.5million endoscopy unit at the Queen Elizabeth Hospital, King’s Lynn NHS Foundation Trust is being recognised as an outstanding example of combining offsite design with collaborative working.
62 | Offsite Construction Week
Taking place from 16-20 September 2024, Offsite Construction Week will revolve around three major industry events – Offsite Expo, the Offsite Summit and Offsite Awards, offering unparalleled opportunities for industry collaboration.
64 | Statistics Paint a Positive Picture
You could be forgiven for thinking the offsite industry is not in good shape but as Jackie Maginnis, Chief Executive of the MPBA tells us, there are some phenomenal success stories to be told.
72 | Offsite & Low Carbon Housebuilding
Rebecca Goldsmith, Product Manager at MEDITE SMARTPLY, explains why OSB offers many advantages for offsite built homes as part of timber frame systems.
76 | Navigating the Competency Landscape
Andrew Way, Associate Director at the Steel Construction Institute (SCI) explores how design competency within the offsite sector is being confirmed and supported.
78 | Automating Brick Slip Systems
Ibstock Plc is embarking on the next stage of its major investment programme at its Nostell factory that will include the UK’s first fully automated brick slip manufacturing centre.
The housing market is in a period of accelerating change and the need to modernise the way we build to provide affordable and sustainable living has never been stronger. Precast specialist FP McCann is at the centre of addressing these huge demands.
The continuing shortfall in meeting the ever-growing requirement for housing is running head-on into other major challenges such as carbon targets and net zero policies. What’s more, the skills drain within the industry continues at pace, with few new entrants coming in to replace the generation of proficient tradespeople. The simple answer is that the housing sector has to quickly adapt and accommodate new and modern methods of construction (MMC) to deliver the built living environment.
The UK’s housing sector therefore requires a multi-pronged approach, with both new and traditional methods of build working side by side to alleviate the crisis in supply that exists. There is a recognition that the government’s target of 300,000 new homes a year isn’t being met and cannot be met by traditional build alone. The growing capabilities of offsite manufactured solutions alongside MMC is clearly the way forward.
Offsite manufactured solutions and MMC are very much at the forefront of the UK’s largest precast concrete supply and installation company, FP McCann. The family run business which now employs 1,700 with an annual turnover of £415million operates out of 13 strategically located precast concrete manufacturing facilities, allowing for UK wide coverage. From its roots in Northern Ireland, the company rapidly extended its operations from 2005 onwards via several key precast business acquisitions. Fundamental to this growth, has been the measured recruitment of the necessary engineering and technical skills and knowledge to enable FP McCann to not only react quickly to the changing construction landscape, but also to influence change through its numerous partnering agreements. This is no more evident than within urban settings, where FP McCann is engaging with some of the UK’s major residential developers to build quality, affordable living space on brownfield sites across
towns and cities. The beneficial effects of offsite precast concrete in MMC continues to grow in recognition, with developers and contractors alike turning to this tried and tested structural system.
Hollybrook Harlow
As part of a £50million regeneration scheme in Harlow, Essex, FP McCann has recently completed a supply and install project for Hollybrook. The development consists of 172 new homes on a key gateway site in and out of the town. The 15-storey building on Fifth Avenue near Burnt Mill roundabout contains 139 twobedroom properties and 33 single bedroom apartments, all housed above 12,500sq ft of commercial space. The NHBC multi award-winning development is an in-situ reinforced concrete frame to first floor, with a structural precast concrete frame and precast concrete architectural cladding to the 14 upper floors.
The full precast concrete frame solution has been designed, manufactured and installed by FP McCann – a Tier 2, BIM Level 2 certified supplier. As a Tier 2 Supplier, FP McCann has recognised the drivers and its responsibilities for meeting and exceeding BIM Level 2 criteria. The established digital engineering protocols in place not only satisfy the company’s BIM modelling business agenda, but also the expectations from its clients. As is the case on all such contracts, BIM Execution Plans (BEP) were prepared for the Hollybrook development, demonstrating FP McCann’s proposed approach, capabilities, capacity and competence to meet stringent Employer’s Information Requirements (EIR). FP McCann recognises that predictability of the building’s delivery is very important for the financial calculation of the business in terms of cost and revenue and therefore a key factor in helping the client gain an early return on its investment.
The FP McCann precast structural frame comprises precast concrete core and party walls, prestressed hollowcore flooring planks and precast stair cores and stair landings. Integral to the structural frame itself, are the architectural brick-faced insulated sandwich panels and coloured concrete feature panels, both offering the attractive external finish to the building from the first floor up. Transfer slab cladding, and ground floor cladding are other key precast concrete elements of the build. Many other MMC features included the supply and fix of galvanised conduits and the fair face finish to internal walls, allowing for follow-on trades to complete their works in a timely and efficient manner. Co-ordinated works in conjunction with other contractors incorporated the bolt-on stair and balcony fixings and the placing of bathroom, ensuite and utility pods.
Notwithstanding the quality controlled manufactured precast concrete products installed, there are many other benefits and advantages of offsite/MMC construction as clearly illustrated on the project itself. Significantly less waste is evident onsite as precise material usage comes as a result of the accurate BIM modelling process: controlled emissions are driven down by the reduction in ‘wet trade’ activity and associated vehicle
3
movements on-site, uninterrupted working programme due to weather conditions (construction can continue in temperatures as low as –20°C). The accelerated construction time typically seen in such offsite precast concrete structural frame builds, saw the Harlow project completed in just 50 weeks. Speedier delivery to the client of the finished building is a major advantage. Reducing construction times by 40%-60% compared to traditional build methods has to be factored into addressing the housing shortfall in urban locations. Traditional construction methods, while tried and tested, are increasingly inadequate to meet the soaring demand for quality, affordable housing.
Structural precast concrete frame buildings are now also being recognised for their inherent fire resisting qualities. In a real-life fire scenario in conjunction with Ulster University, FP McCann has undertaken intensive fire safety tests on its precast concrete insulated sandwich panels. Panels were exposed to three fire conditions with temperatures in excess of 1000 degrees celsius recorded. In all cases, the insulated core of the panels remained intact, the outer layers of concrete with their low thermal conductivity protecting
2
4
the interior insulation from exposure to heat and flames. Precast concrete architectural external finishes to sandwich panels eliminates the requirement for independent decorative cladding of the building with a proprietary material, an area undergoing investigation and in a number of cases in the UK, currently being addressed as a matter of urgency.
The UK’s housing crisis is a multifaceted challenge that requires an equally multi-faceted response. The future depends on the industry’s ability to adapt and innovate. The Harlow Hollybrook housing project is a clear demonstration that offsite construction and MMC in urban locations not only helps address the current housing challenge but lays the groundwork for a more efficient and sustainable home building industry. By embracing these methods, we can build faster, reduce our environmental impact and provide safe, affordable living space.
For more information visit: www.fpmccann.co.uk
Images: 01-04. Hollybrook, Millbrook Studios, Harlow
Chartered Institution of Building Services Engineers (CIBSE) has been appointed as the new NABERS UK scheme administrator. CIBSE is one of the most prominent professional bodies in the UK building sector, with a history of leadership in energy efficiency
The Hill Group has handed over six new modular homes to Torridge District Council to address homelessness in Devon. The purpose-built DuoHaus® and SoloHaus® homes are intended to provide follow-on temporary accommodation for people, including couples, who may be experiencing homelessness.
Last year, the charity Shelter disclosed findings from a Freedom of Information request spanning Devon and Cornwall, which highlighted that the Torridge district has the highest rate of homelessness in the region, with one in every 279 people affected. The modular homes were launched through Hill’s philanthropic initiative, Foundation 200, a £15million pledge to design, manufacture, and donate 200 modular, single-person homes (SoloHaus®) to homeless charities and local authorities by 2025. DuoHaus®, a larger model of the successful SoloHaus® has been designed with couples in mind and features additional bedroom space and a double bed.
Created in collaboration with leading homelessness charities, both models are manufactured offsite and arrive fully furnished, ready for residents to move into straight away. The homes are also easy to install and secure, with a high-quality finish throughout and relocatable. Built to last for at least 60 years, the homes are highly energy-efficient to keep costs low, and are designed to Future Homes Standards, exceeding building regulations for energy efficiency and sound insulation.
and decarbonisation. The organisation brings with experience in certification, professional training, standards development and industry engagement, providing a strong foundation for the role of NABERS UK scheme administrator.
NABERS UK is a leading building energy efficiency and decarbonisation initiative that was launched in the UK in 2020 following an international partnership between major UK industry organisations, led by the Better Buildings Partnership in the UK, and NABERS in Australia. The initiative drives improvements in energy efficiency in commercial buildings through the measurement and verification of actual in-use energy performance, which also provides critical assurance and integrity for building owners and their stakeholders.
The UK scheme has had strong industry backing since its launch and has gained significant momentum, with nearly 150 new and refurbished office buildings setting NABERS UK Design for Performance targets, representing a significant portion of UK office developments. As one of the founding members of the NABERS UK Steering Committee, the CIBSE has supported the scheme throughout its
development. The organisation will now be taking over the scheme administration from BRE with both organisations working closely together to enable a smooth transition and support the next phase of growth for the Scheme.
CIBSE Chief Executive, Ruth Carter, said: “We are delighted that CIBSE is now overseeing the administration of NABERS UK. This strategic move aligns with our commitment to advancing energy efficiency in the built environment. NABERS UK plays a crucial role in bridging the performance gap and enhancing transparency. We are excited to contribute to the continued success and impact of NABERS UK.” NABERS Director, Carlos Flores, added: “We are thrilled to announce CIBSE as the new NABERS UK Scheme Administrator. CIBSE has an illustrious history of leadership in building sustainability and decarbonisation, and an unmatched track record in certification and the development of technical standards. Buildings in the UK can and should lead the world in tackling the climate crisis, and we are excited about the role NABERS UK can play with an organisation of CIBSE’s calibre at the helm.”
Source: www.cibse.org
The three SoloHaus® and three DuoHaus® homes have been installed to offer emergency housing support to households who have lost their homes due to a severe shortage of private rental properties in Devon as well as the ongoing pressures from the cost-of-living crisis. The council is now supporting a large number of households through this difficult time using a range of innovative facilities, like modular homes.
Andy Hill OBE, Group Chief Executive at The Hill Group said: “We are pleased to hand over three SoloHaus® homes for single people, and for the first time, three DuoHaus® for couples who are affected by a lack of housing supply, to Torridge District Council, bolstering its efforts to tackle homelessness. This is the first time we have delivered modular homes in Devon, and we are confident they will make a tangible difference to residents’ lives by providing secure, modern, and comfortable accommodation to enable them to get back on their feet and regain the dignity they deserve."
Hamish Cameron, Project Manager, Torridge District Council added: “We are delighted to have acquired these six homes which are already helping alleviate the housing challenges within the district and we are primarily using them to home people that are experiencing homelessness, and this remains an important aspect of our strategy to support these needs in the local community. Notably, their highquality design and energy efficiency, will ensure they offer a comfortable and affordable place to live.”
The multi-award winning SoloHaus® and DuoHaus® homes are manufactured by Volumetric Modular from its factory in the West Midlands. Fabrication takes just 10 days, and on-site installation can be even quicker, making the homes an ideal solution for addressing accommodation shortages swiftly.
Source: www.volumetric.co.uk www.hill.co.uk
BUILDING SAFETY ACT
GATEWAYS 1, 2 & 3
BUILDING REGULATIONS
CDM 2015
BUILDING SAFETY REGULATOR
REACTION TO FIRE
Now you can get everything you need for compliant rainscreen cavities from Knauf Insulation - including sheathing insulation, cavity barriers and fixings - in a single, tested system.
With solutions available for both ventilated and closed state cavities, you can meet the requirements of building regulations and the Building Safety Act.
GATEWAYS 1, 2 & 3 SECTION 38
BUILDING REGULATIONS
CDM 2015
BUILDING SAFETY REGULATOR REACTION TO FIRE U-VALUES
For every rainscreen. For the real world.
Simplify specification with the new Rocksilk® RainScreen Cavity Systems. knaufinsulation.co.uk
Timber import volumes started 2024 around 6% lower than in January 2023, down by around 45,000sq m, according to the latest figures from Timber Development UK (TDUK). This reduction was made up of very different levels of performance in the first month of the year.
Softwood, hardwood and plywood imports were all lower than in January 2023, but particleboard, engineered wood, OSB and MDF products all saw imports increase slightly at the start of this year. For softwoods, a 9% reduction in volumes from Sweden was the largest contributor to the 9.6% drop, with import values also 15% lower in January 2024 than they were in January 2023. This fall was caused by the volume decline, coupled with a 5.6% fall in the average price of a basket of softwood products, down from £256sq m to £241sq m.
Hardwood imports experienced a 13.8% fall, largely due to tropical hardwood imports being down by around 3,000sq m. In contrast, volumes of temperate hardwoods increased by 2%, with imports from the USA, Croatia and Romania accounting for most of this growth. Overall plywood imports were also down 6%, though hardwood plywood volumes rose 36%, mostly because of a near 18,000sq m increase from China.
Substantial increases in particleboard imports from Belgium, Portugal and Spain helped account for the
sector’s 3.4% growth, while OSB and MDF imports were up 6% and 4.1% respectively. Finally, a 12.8% growth in engineered wood product import volumes rounds out the varied January 2024 results. TDUK statistics also examined the impact of Brexit on timber supplies.
Although timber volumes have experienced steep rises and falls since Brexit, as well as being adversely affected by a pandemic, wars and a sluggish economy, a simple examination of import volumes both before and after the 31 January 2020 exit date, reveals that little has changed in terms of timber import figures.
For softwoods, the proportion of timber arriving from Europe stands at 99% of the pre-Brexit figures, while for hardwoods, the percentage of trade with Europe has marginally increased from 66% in 2020 to 67% in 2023. For panel products, volumes imported from Europe have also changed by just 1%.
The only sector that has seen a noticeable reduction in European imports is MDF, which has fallen from 97% to 86%.
TDUK Head of Technical and Trade, Nick Boulton, said: “It’s always very difficult to accurately assess import and export trends at the start of a year, because with just one month’s data available, small changes from last year can result in significant shifts in performance. A truer reflection of the sector’s
product performance will be visible towards the end of Q1, but the 6% reduction we’ve seen in January’s figures does confirm the greater stability in the market when compared to the high increases and decreases experienced from 2020 to the end of 2022.
“We also need to bear in mind the latest housing start data, which indicates that while housing starts and completions held up well in 2021 and 2022, data for the full 2023 year is likely to be substantially lower once it is made available. Housing starts in England during Q4 2023, for example, were 51% Q4 2022, on the back of a similar 52% reduction in Q3 2023 over Q3 2022. Given the importance of the newbuild housing sector to the timber industry, this is likely to indicate we can expect continuing challenges in the short term, and likely until after the coming General Election.
“However, despite the volatility of recent years and the subdued start to 2024, the longer-term trend of UK timber and panel product imports remains upward, and the government’s renewed focus on timber as a core construction material suggests that the future continues to look brighter.”
Source: www.timberdevelopment.uk
Connect Modular has announced the successful delivery of the first six houses to a new 14 home affordable housing development programme for North Ayrshire Council.
Twelve modules landed across two sites in Laburnum Avenue, Beith and Newhouse Drive, Kilbirnie. Works commenced on-site and in the Connect Modular factory in February and the modules were delivered to site with 90% of works already complete, demonstrating the exceptional efficiency and speed in providing this offsite, affordable housing solution.
This marks the third affordable housing project Connect Modular has delivered for North Ayrshire Council in recent years. The module delivery at Newhouse Drive, Kilbirnie was warmly welcomed by pupils of nearby Primary School, St Bridget’s who watched on in amazement from their playground as the modules arrived on lorries and were craned into position. Connect Modular has been working closely with pupils of St Bridget’s since the project began. Colleagues from Connect Modular’s marketing team delivered a presentation for pupils at their school assembly covering topics including modular construction, health and safety and careers in construction.
Intrastack, part of the Saint-Gobain Off-Site Solutions division and leader in Light-Gauge Steel Frame (LGSF) solutions, has launched its new Low-Rise Housing solution tailored to meet the needs of the construction industry. Utilising offsite construction methods, the Intrastack Low-Rise Housing solution (ILRH) will provide a quick, durable, and cost-effective option for low-rise residential developments.
Utilising LGSF technology, the ILRH system is an ideal solution for the market – offering a multitude of benefits. Manufactured in a controlled factory environment, the load-bearing wall and floor cassette panels are fabricated from cold-rolled steel. This system also provides options to add either a timber trussed roof or room-in-roof cassette solution, adding to its versatility.
The steel frame solution provides a non-combustible alternative to timber frame construction while also expediting the building process. Intrastack continually undertakes extensive fire testing across all systems, ensuring its solutions meet, and exceed, all legislative requirements. Recognising that fire safety is a critical consideration for all sectors, Intrastack has ensured
“We are thrilled to reach this important milestone in our latest housing project for North Ayrshire Council,” said Richard Reid, Acting CEO at Connect Modular. “The successful delivery of the first houses to the development sites in Beith and Kilbirnie, exemplifies the speed, efficiency, and quality that modular construction offers. We take great pride in contributing to the provision of affordable housing solutions for the local community, and this accomplishment further solidifies our commitment to sustainable and forwardthinking construction practices.”
Connect also announced the return of founder and CEO Jennifer Higgins, who is officially back in action after enjoying a year’s maternity leave. “It feels like a
great time to be coming back,” said Jennifer. “2024 has already been a record year for Connect Modular, having been appointed to deliver two brand new affordable housing developments and with several more pipeline projects soon to be announced. Our live developments at Kilmarnock and in Beith and Kilbirnie are thriving and it’s all thanks to the hard work and dedication of our teams. I would like to thank my staff for their ongoing commitment. I was able to enjoy my maternity leave knowing the company was in safe hands.”
Source: www.connect-modular.co.uk
that the ILRH solution has a range of tested build-ups that can be used to address fire safety needs. There are many ways in which the Intrastack Low-Rise Housing solution aims to aid the housing sector through its key benefits, which include: offering diverse external façade options to suit aesthetic preferences and local planning needs, open panel LGSF internal walls for easy installation of plumbing and electricals on internal walls, robust floor cassettes with P5 chipboard or OSB3 structural decking securely fastened to loadbearing walls to increase durability and customisation for each ILRH system to meet specifications for seamless integration and superior performance.
Andy Higson, Business Director at Intrastack, said: “We’re delighted to be able to provide the Intrastack Low-Rise Housing solution to the market. We believe it will address the needs of the Low-Rise Housing sector, meeting each customer’s specific project requirements. Our knowledge and expertise in steel frame construction, together with our understanding of market demands, has enabled us to develop a solution which meets the evolving needs of the housing sector.” Intrastack’s Low-Rise Housing solution is now available across the UK.
Source: www.intrastack.co.uk/solutions/ilrh
In response to growing demand across the healthcare, pharma, education and commercial sectors, Northern Ireland-based offsite manufacturer McAvoy has continued investment of its SmartSpace temporary building fleet.
Having recently launched additional new innovative space solutions via its QSpace and ESpace single modular buildings, the business continues to experience high demand for rental projects in both the healthcare and education sectors, including a second, significant 10-year rental contract for University Hospitals Birmingham NHS Foundation Trust.
Investment in manufacturing capability has continued with the acquisition of a custom-built mobile gantry, increasing efficiency, and improving workplace safety. This commitment to investment in the business also includes ESG, digital technologies, recruitment, and people development.
CEO of McAvoy, Ron Clarke, said: “The group continues to see strong interest in its proposition, and with the continued support of our shareholders the company is in an excellent position to deliver its strategic growth plan. We are confident that our high performing temporary and permanent buildings will continue to deliver modern, flexible, and sustainable
the Helm
After 14 years of leadership, innovation and strategic vision, David Hurcomb will retire from his role as Chief Executive Officer of NG Bailey Group in May 2024.
Under David’s leadership, NG Bailey, the UK’s largest independent engineering and services business, has experienced extensive growth, diversification and success. From cultivating a balanced business in the engineering and building infrastructure services sectors, to delivering groundbreaking projects, David has been instrumental in positioning the company as a formidable force in the built environment sector.
space solutions to our customers. Looking ahead we are on track to deliver a significant increase in performance in 2024.”
During the 12 months the business has delivered several key projects across the country, including a new Collaborative Research & Innovation Centre in Wiltshire, the pioneering Low Carbon Pathfinder, 900 pupil school at Redhill in Surrey for the Department for Education, and two 24-bed ward buildings at Antrim Area Hospital. The company has also been chosen by the Department for Education to design and build a £37.5million, 1,200-place academy in Essex.
Several of the company’s projects and innovations have been recognised by independent peer group awards, including Healthcare Project of the Year at the 2023 Offsite Awards.
Jonathan Stockton will replace David in the role of Chief Executive Officer. Jonathan joined NG Bailey in 2016 and has held several senior roles within the business, including Chief Financial Officer and Chief Operating Officer. He was appointed to the Group Board in 2021, since when he has worked closely with David at a strategic Group level as part of this planned transition. Following his retirement in May, David will continue to work closely with the business for a short period to support the transition of responsibility and overall leadership to Jonathan.
David said: “It has been a huge honour to have played my part during my time as Chief Executive in the ongoing success of what is a truly fantastic familyowned business. I am immensely proud of the many remarkable highlights and achievements there have been over the years, and it has been a pleasure to have worked with so many talented colleagues.
“While we have faced undoubted challenges along the way, including Covid-19 and challenging wider market conditions in more recent times, I am delighted that the business is well on its way to pre-pandemic levels of performance. Indeed, early indications show an increase in turnover and expected double-digit profit figure for the 2023/4 financial year. Alongside this, our well diversified portfolio means we have a healthy £1.4billion forward
For the period ending May 31, 2023, McAvoy reported a strong performance within its rental division with revenues of £12million and EBITDA growing to £3.8million primarily due to rental fleet expansion in the health and education sectors in the UK. The business also reported a steady performance in its permanent offsite division. In its latest set of consolidated accounts McAvoy’s revenues were c.£60million and generating c.£5million EBITDA. For the period ending FY24 the business reports that it is on track to achieve revenues in excess of £70million, primarily driven by investment in the fleet and further success in the temporary segment.
Source: www.mcavoygroup.com
order book, with strong growth in sustainable markets. “Looking ahead, I am certain we will further develop and innovate across our engineering and services divisions, ensuring we continue to make a positive impact in the key sectors we operate in and through the vital UK infrastructure projects we deliver.
“Finally, being able to fill my role by promoting from within is testament to the great people we have and significant investment we make as a business to develop our skills and talent. I would like to take this opportunity to wish Jonathan every success in his new role as he leads the Group on the next phase of its exciting journey.”
Jonathan added: “I am very much looking forward to my new appointment and taking on the position of Chief Executive Officer, working with the Board, shareholders and senior leadership teams to lead the business through its next chapter. I would like to thank David for his ongoing support, and I wish him a much deserved, long and happy retirement.”
Images: (L-R) David Hurcomb and Jonathan Stockton
Source: www.ngbailey.com
Timber frame specialist Scandia-Hus is to showcase the energy efficiency of its Actis-insulated properties when it opens its newest show home later this year. The company, which has used the Actis Hybrid range on all show properties at its Sussex HQ, is currently fitting its latest show home with H Control Hybrid, 105 mm Hybris and insulating breather membrane Boost R Hybrid in the walls to achieve a U-value of 0.14W/m2K. It is using H Control Hybrid in the flat roof.
The garage will be used to house a display giving information on the U-values, EPCs and air testing results achieved by using Actis Hybrid products, to trumpet the energy efficiency of the buildings to potential customers and self-builders. The Lodge, a single storey 1,915sq ft property, will have three bedrooms all with en-suites, a large kitchen/ dining/ living room, snug and utility room as well as a full heat recovery system. Previous Scandia-Hus show homes have been insulated with a combination of insulating vapour control layer Actis H Control Hybrid and 155mm honeycomb design Actis Hybris in the pitched roof and H Control Hybrid and 105mm Hybris in the walls to achieve a U-value of 0.14 in the roof and 0.16 in the walls.
The Scandia-Hus team again plans to carry out a thermal imaging survey once it's completed to
demonstrate the effectiveness of the products. A similar exercise carried out a few years ago on its first Actis Hybrid-insulated show home showed an impressive lack of thermal bridging, confirming that Hybrid was the right choice for the bulk of its ongoing projects.
Scandia-Hus MD Derek Dawson said: “As with the three other properties at our show centre, along with countless customer self-build projects, we have chosen to use Actis Insulation's Hybrid range to insulate The Lodge. The thermal efficiency performance achieved with this innovative system, which can be combined or used separately in walls, roofs, ceilings and timber floors, as well as the speed and ease of installation, makes it the ideal product for our timber frame homes.
“All products have been designed to eliminate thermal bridging by helping to ensure an airtight envelope. The range can achieve the highest U-value requirements with a minimal thickness. High performance Hybrid panels also offer the benefit of being simple and quick to cut accurately, minimising wastage and reducing installation time, which can be up to 30% quicker than using alternative methods.”
An open day being held at the Scandia-Hus Show Centre in East Grinstead on May 18, which also marks the company's 50th anniversary, will see Actis regional sales manager join other suppliers to talk about Actis products and answer technical questions.
Source: www.insulation-actis.com www.scandia-hus.co.uk
Outpost Management has announced the forwardfunding acquisition of a 462-unit development in North Acton, London, through its joint venture with BlackRock Private Markets from developer and contractor Tide. The scheme is due to open in summer 2025.
The North Acton site, currently called The Castle, will be operated by Outpost Management under its Enclave brand and is the third asset to be acquired by the firm’s joint venture with BlackRock Private Markets, through its real estate business. Having already invested £500million, the joint venture plans to commit an additional £500million, totalling £1billion of investment in UK residential assets.
Tide is delivering the project using its offsite manufacturing arm, Vision. The North Acton development is a 32-storey, 220,000sq ft residential-led, mixed-use scheme, designed by HTA. It will feature 462 co-living apartments, with 18,000sq ft of amenity space across five floors, including a spa, lounge areas, private dining and coworking spaces, a library, bespoke gym, cinema and
games rooms. Residents will also be able to enjoy a 2,000sq ft landscaped roof terrace on the 32nd floor, giving extensive views across London.
In addition, the scheme will feature a new 3,500sq ft public house, replacing the previous pub, The Castle, which dates to the 1930s but has remained vacant since 2020. The Castle demonstrates the design flexibility of the Vision volumetric system with a unique triangular floor plan arrangement for the studio apartments, along with amenity spaces.
Innovative sustainability technology will feature across the development, targeting WiredScore Platinum and BREEAM Excellent ratings. High speed internet will be available in all areas, and residents will be able to control their unit's lighting and heating through a dedicated app. Utopi multi sensors will provide residents with real-time data on their energy and utilities consumption.
Troy Tomasik, Outpost Management Founder and CEO, said: “We are thrilled to have acquired this fantastic development, and proud to continue our
partnership with BlackRock and deliver another market-leading scheme with Tide. Enclave is helping to transform the UK rental market by creating pragmatic lifestyle-enabling homes that empower our residents to live their own way. We’re excited that bringing Enclave to Acton will not only provide new homes and extensive amenities for future residents but will also become a hub for the local community.”
John Fleming, Chairman of Tide and Vision, added: “The Castle is the second co-living scheme developed by Tide and purchased by Outpost Management, showing how volumetric construction is driving innovation in this asset class. We look forward to supporting our longstanding partner Outpost Management on its joint venture with BlackRock by delivering The Castle. This deal demonstrates the confidence in our volumetric product to deliver highquality homes and cultivate new communities.”
Source: www.tideconstruction.co.uk www.visionvolumetric.co.uk
Transform
Discover
Collaborate
Thorngate Churcher Trust, a charitable registered social landlord, has selected Vale Southern Construction to build 30 new homes for the over 50s in Gosport, Hampshire. The £6.7million contract will provide warden-assisted flats as part of the charity’s long-term commitment to providing affordable housing in Gosport.
Vale Southern will transform a derelict corner plot into a development spanning two and three storeys offering contemporary homes, communal facilities, car parking and landscaped grounds. Modern methods of construction will be used by the contractor, including a lightweight steel frame, which will be assembled offsite to achieve higher programme productivity.
Oliver West, Managing Director of Vale Southern, said: “We’re looking forward to working with Thorngate Churcher Trust for the first time and bringing much needed housing to the area. Although the site itself is vacant, we’re mindful of the surrounding residents and will be liaising closely with them to try and minimise any potential disruption. Our priority is to deliver this vital development within 56 weeks enabling the first residents to move in by late spring 2025.”
Thorngate Chief Executive, Anne Taylor, said: “Finding the right contractor to work with us is hugely important and it was vital that we appointed
March saw two familiar names from the volumetric modular sector entered administration to continue the negative arc the sector has been following over the last 18 months. Based in Sheffield, timberframe volumetric specialists Lighthouse – formerly known as Ideal Modular Homes (IDMH) – entered administration after a bid to sell the business failed after struggles with cashflow. Lighthouse was initially formed to take over the assets of IDMH which collapsed during the pandemic. Richard Goodall and Martyn Rickels of FRP Advisory have been appointed
a company which understands the intricacies of creating our homes and can work with us on tight timescales and budgets while causing as little disruption as possible to nearby residents. We look forward to seeing the new homes take shape over the coming months.”
The project has been kickstarted thanks to a grant from Homes England and will meet a growing
as joint administrators and said the company: “Has suffered cashflow pressures in recent months and efforts to secure a sale of the business and assets has unfortunately been unsuccessful. FRP will now aim to maximise’ returns for creditors.”
A message sent by Lighthouse on the eve of the announcement, CEO Tom White said: “As you all know, our leadership team has been working tirelessly to secure the ongoing future of our business. Despite exploring all available options, it has now become clear that there is no near-term solution to secure our company’s future. Time has been against us and, as of this evening, all options have expired.
“I am devastated to say that as a result of this we must now take the necessary next steps. We will host an online meeting and will send details of how to join ahead of this. We understand that some of you may wish to visit the factory in due course to collect any personal items or drop things off, and we will make arrangements to enable this, looking to have teams come in together where possible. Please know that we are fully committed to providing you with the support and information you need throughout this process. Your well-being remains our utmost priority, and we are here to assist you during this challenging time.”
demand for housing in the borough with more than 100 people on Thorngate’s waiting list for an assisted living home. The charity already operates 124 flats for assisted living in Gosport as well as a 44-bed care home offering residential care for older people, including those living with dementia.
Source: www.valesouthern.co.uk
The second business entering administration was Beattie Passive – a seminal name in the sector that created the UK’s first Passivhaus-certified build system. Work has stopped at the company’s 10,800sq m Norwich factory after parent company Beattie Passive Group Ltd and four related companies filed notices of intention to appoint an administrator.
Despite boasting a strong order book worth £4.5million and achieving year-on-year revenue growth, the company had encountered a cash flow gap, which it blamed on delays to major projects.
Ron Beattie, Founder and Managing Director (pictured), commented: “Having explored all strategic options, it is with deep regret that we have filed a Notice of Intention to appoint administrators and paused operations. My family and I founded this business 15 years ago to deliver the types of high-quality, energy-efficient homes our country so desperately needs, while creating highly-skilled, green jobs within the local communities we operate. I want to express my sincere thanks to all of those who have helped Beattie Passive become the pioneering company it is today, and we will continue to explore all possible options as part of our strategic review.”
Source: www.frpadvisory.com www.beattiepassive.com
Modular building manufacturer Phoenix Building Systems has launched a new product range to make it easier for schools and businesses to find a suitable building. With Phoenix Building Systems’ new Breeze 1 range, schools across the UK can conveniently purchase or hire top-quality modular classrooms directly from a reputable manufacturer.
The new modular classrooms make sourcing quality learning spaces a ‘Breeze’. The buildings in this range have been optimised to guarantee that they will fit education needs. They can be scaled to a larger format or be made multi-storey, completely hassle-free. There is also a wide range of bespoke customisation options to ensure the appearance of your modular classroom seamlessly integrates with the rest of your premises.
Phoenix Building Systems also has a Breeze 2 range, which offers the same level of service and ease as Breeze 1 but provides motivating office spaces instead. Breeze 2 modular offices are convenient and customisable to fit a number of business requirements. “Our modular classrooms have been tried and tested. The pre-designed, environmentally friendly, ready-to-order classroom buildings are fit for any school. This makes the buying process a BREEZE,” said Managing Director, Michael Taylor.
Phoenix Building Systems also launched a new website to simplify finding the right modular building. Straightforward navigation, more images and case studies mean customers can make sure they find a building that suits their needs.
To help customers visualise their buildings, Phoenix Building Systems has also invested in an interactive augmented reality Breeze 1 classroom. Scan the QR code on the website’s home page to really get a feel for the space. “Scanning the QR code gives you a real opportunity to immerse yourself in your new modular building and get a real feeling for it before you buy,” added Michael Taylor. “Modular buildings are a huge asset to schools and businesses alike, so the ease that the Breeze range brings to customers
Using Totalkare’s mobile column lifts with infill plates when loading modular buildings for dispatch can save significant time and money.
Ask us about our flexible finance options - including hire - today!
is hugely important. These buildings offer quick and cost-effective spacing solutions. Modular classrooms and offices are also significantly more sustainable than traditional buildings, which can improve your image, carbon footprint and energy usage.”
Phoenix Building Systems is a Hull-based modular building specialist working nationwide with public and private organisations. It was founded in 2003 by Martyn Taylor, Martyn retired in February 2023 and the business was taken over by his son’s Michael Tayor and Steven Taylor as the Managing Directors and Jayne Wilson as the Commercial Director.
Source: www.phoenixbuildingsystems.com
New research by NBS has found finds half of industry professionals still unclear on duty holder responsibilities for higher-risk buildings. As the six-month transition period for Higher Risk Buildings (HRBs) comes to a close, new research from NBS shows the industry is still struggling to achieve a consensus on the scope and requirements of the Building Safety Act 2022.
The report reveals half of industry professionals remain unclear on the responsibilities of duty holders for the gateways defined for higher-risk buildings. Additionally, only 20% of respondents feel confident they are ‘very clear’ on the differences in responsibilities if the project is defined as a higher-risk building.
Thanks for this data, the NBS believe a greater effort is urgently required to ensure a universal understanding of the Building Society Association’s (BSA) role – particularly, clarifying the lines of responsibility and duties, while improving the consistency and quality of documentation and record keeping on construction projects.
Commenting on the findings, Russell Haworth, CEO UK & Ireland at Byggfakta Group, NBS’ parent company, said: “At our Construction Leaders’ Summit last October, Dame Judith Hackitt told the audience, in no uncertain terms, that regulatory change is coming, and it’s unstoppable, so the construction industry needs to be fully prepared.
The Institution of Structural Engineers (IStructE) has written to the Secretary of State for Levelling Up, Housing and Communities (DLUHC) to express its concern that the regulation of embodied carbon has been omitted from the Future Homes Standard and Future Buildings Standard consultation.
“Fast-forward to April 2024, and our research shows many specifiers are struggling to get to grips with the requirements, and this needs to be resolved. All designers must have the correct approach to specifications if the industry is to raise the bar on building safety. This includes getting to grips with the ‘nitty gritty’ of the BSA if they want to operate in the new regulatory landscape.”
Worrying still are attitudes towards the Golden Thread and the critical role it plays for HRBs. For example, just under half of those surveyed (45%) are clear as to how they will manage building information to realise the Golden Thread and just one in ten have a solid plan in place.
Dr Stephen Hamil, Innovation Director at NBS, added: “The level of understanding around the golden thread of information is worrying. As well as providing a continuous flow of information throughout the entire lifecycle of a building, it is necessary to
The Institution sees this as a missed opportunity to regulate embodied carbon to meet the UK’s net zero legal commitments. IStructE explains that previous commitments from the Department to consult on embodied carbon regulation would have made this consultation the perfect occasion to gain feedback from industry. IStructE believes that such regulation is already welcomed, with wide support for the net zero carbon building standard as evidenced by the 200+ statements of support for Part Z, including from household names such as Barratt Homes, British Land and NatWest.
The letter also highlights their concerns to the Secretary of State about the phrase ‘net zero ready’ being used in the consultation to only refer to operational carbon emissions. This is despite that half the lifetime emissions of a new home being due to embodied carbon, which accounts for 10% of UK emissions and is a figure that continues to rise as the national grid decarbonises. IStructE suggests that this could leave the UK open to legal challenge on whether the legislation meets net zero commitments.
Will Arnold, Head of Climate Action, comments: “It's disappointing that embodied carbon was excluded
ensure all relevant safety-related information is readily accessible and up to date.”
He stressed the need for robust specifications that will act as a point of reference to demonstrate that designs meet the Building Regulations as part of the submitted plans at the gateways. “However, the Building Safety Act presents a great opportunity for the industry to take back control of both the design process and through proper change control processes ensure that sub-standard construction does not happen. Safety starts with the specification and a well-managed approach to spec writing must form part of the standard design process.” The full report, which provides insight into industry views on the Building Safety Act and its implementation, launches in April 2024.
Source: www.thenbs.com
from the consultation. Our letter urges DLUHC to consider consistent regulation, aligning the UK with global standards. Our view is that a building is only net zero if its whole life carbon emissions are considered.”
Patrick Hayes, Technical Director at IStructE added: “Introducing embodied carbon regulation provides certainty, consistency and efficiency for all parties on how to meet our legal obligations. It ultimately reduces the burden on business and reduces costs of transitioning to net zero by introducing a level playing field.” The letter includes a recent policy paper from IStructE along with ten other major institutions and organisations in the built environment sector which asks in this 2024 election year for political leaders to commit to reducing embodied carbon emissions in construction within two years of starting government. Such a move is needed urgently because the materials used in buildings and construction are responsible for 10% of UK carbon emissions, a main driver of climate change.
Source: www.istructe.org
A family-run Black Country manufacturer has moved and doubled the size of its factory, following a £7.59million investment from the West Midlands Combined Authority (WMCA). Drywall Steel Sections, which has invested alongside the WMCA into the wider £13million scheme, has moved to a new 39,850 sq ft factory built on four-and-a-half acres of brownfield land in Ettingshall, Wolverhampton. The firm was previously based in Cradley Heath, Dudley, for more than ten years but had outgrown the facility, which was also no longer fit for purpose for its modern production methods.
The factory manufactures light gauge steel framing for the construction industry (including modular housing), as well as steel products for wall partitions and ceilings. It also has an engineering department, DrySpec, which specialises in designing and detailing steel framing for a vast range of buildings across the country.
Andy Street, Mayor for the West Midlands, and Chair of the WMCA, said: “I was here 12 months ago to watch work start on Drywall’s new factory so it’s exciting to be back and see them up and running in their new home.
“Manufacturers like Drywall are incredibly important to our regional economy which is why we use the money we secure from government to support those businesses who want to grow and generate new jobs for local people.
“We are also continuing to protect our green belt by prioritising investment on the regeneration of brownfield sites like this one. It’s important we clean up these sites to provide high quality affordable housing for local people and modern commercial premises for our businesses, helping to attract further investment into our region.
“Now Drywall are in their new factory I can’t wait to see them continue to grow and prosper in the years ahead.”
Drywall Steel Sections Ltd is part of a familyowned group of companies set up by Rajinder and Sunita Gupta more than 20 years ago. Since joining the business six years ago, their son Mayank has taken over as the Managing Director, and the firm is seeing new growth through fresh vigour. Mayank said: “We are proud to bring Drywall Steel Sections Ltd’s headquarters back to our home city of Wolverhampton.
“Our new headquarters is equipped to handle significantly more manufacturing capacity with a much more efficient production process, allowing us to remain competitive in the market. Alongside our family investment, we are most grateful to the WMCA for its support in unlocking this brownfield site.
“The new Drywall HQ and commercial starter units on G5 Industrial Park will help safeguard current jobs and provide a much improved facility for the existing team. It will also create new jobs, help smaller businesses to grow in brand new premises, and boost the region's economy. Drywall Steel Sections Ltd. has further expansion and growth plans, and this new facility will help us bring those plans to life.”
Image: Andy Street, Mayor of the West Midlands and Chairman of the WMCA; Mayank Gupta, director of DryWall, and Stephen Simkins, Leader of Wolverhampton City Council. Courtesy West Midlands Combined Authority
Source: www.drywallsteelsections.co.uk www.wmca.org.uk
Leading UK offsite timber frame manufacturer, Donaldson Timber Systems (DTS), has been appointed to the Communities and Housing Investment Consortium’s (CHIC) Newbuild Development Framework.
As part of CHIC’s new eight-year framework, DTS will sit on the ‘MMC (Modern Methods of Construction) Manufacturer – Frame & Panel’ workstream, delivering timber frame and panels across the UK to create modular new-build homes. The design, manufacture, and installation of timber frame wall panel building systems will meet build speed, fabric performance, building design, and cost requirements.
With a fabric-first approach that achieves net zero operational carbon, DTS’ timber systems will create sustainable, resilient homes that meet the Future Homes Standard 2025.
The CHIC Newbuild Development Framework aspires to establish a new Gold Standard development framework to offer solutions for development and regeneration schemes of all types and sizes across the UK. As well as a route to market for members, CHIC intends to establish a ‘Framework Core Group’ that shares learning, understanding and ideas and promotes standardisation and collaboration.
DTS was involved in competitive tenders based on CHIC’s standard house types and a wide range of rates for all other work. In total, the CHIC framework totals £3.16billion.
Gemma Darroch, National Partnerships Manager from Donaldson Timber Systems said: “We’re really pleased to have been named as one of the longterm contracts on the CHIC Newbuild Development Framework. For decades we have been championing offsite timber frame systems, which use innovative and sustainable technologies and play a key role in meeting the energy requirements of new homes. We’re proud to be promoting this further via this framework over the coming years.”
Sarah Davey, CHIC’s Head of Development added: “We are excited to have Donaldson Timber Systems on CHIC’s Newbuild Framework. They will be an instrumental part in helping our members deliver
their newbuild development efficiently setting a gold standard for the industry.”
Last year, DTS became one of the first manufacturers to achieve Buildoffsite Property Assurance Scheme Plus (BOPAS Plus) in recognition of the quality and durability of its offsite build systems. With DTS’ state-of-the-art open and closed panelised systems –Alpha, Delta, and Sigma ll – works can still be carried out on-site, ensuring that social value potential is reached within the communities served.
The Sigma II closed panel systems offer nearPassivhaus standards of performance and sustainability. The system is being widely used with housing developers, particularly with those driven by whole life costs and fabric performance, contributing positively to fuel poverty challenges.
Source: www.donaldsontimbersystems.com
Britlift are a designer and manufacturer of lifting equipment, specialising in the lifting of modular homes, bathroom pods, commercial modules, containerised structures and pre-cast components. With a wealth of experience in the design and manufacture of lifting frames and lifting systems to the Offsite Construction sector, Britlift are the Offsite sector partner of choice.
A packed audience of Trussed Rafter Association (TRA) members gathered recently to see who would win the hotly contested Roofscape Design Awards 2024. The Awards, now in their second year, celebrate the highly technical skills required to design trussed rafter roofs, joists, and panels. The awards took place at the TRA Annual General Meeting and Conference at Mercure Warwickshire Walton Hall Hotel & Spa.
The awards were given in three categories:
• Residential Project of the Year (for newbuild dwellings)
• Conversion and Refurbishment Project of the Year (for existing housing projects)
• Commercial Project of the Year (for all nondomestic projects)
The judging panel included Nick Boulton, Chief Executive of the TRA, Rob Lockey (former Head of Training at the NHBC) and Les Fuller, Chair of the Technical Committee of the TRA. In the Residential Project of the Year went to designer Phil Morgan of Wyckham Blackwell Ltd for – The Copper House project. The judges were impressed with the extensive knowledge of the architectural requirements of the designer and how the design applied a trussed rafter application and ensured that the ‘form did follow the function’.
Wyckham Blackwell Ltd also took home the award for the Conversion and Refurbishment Project of the Year
Glidevale Protect has supplied two of its market leading wall construction membranes for use at the Vistry Innovation Centre – a unique new concept house built in timber frame that signposts the products and technologies which will support the housebuilding industry on the road to net zero.
with The Black Country Living Museum, designed by Joe Dudley. The judges agreed that it was an example of how to successfully comply with client and historical requirements and still achieve suitable timber engineering for a project.
For the Commercial Project of the Year, it was a unanimous decision that Acorn Timber Engineering’s Welton Extra Care Apartments and Bungalows designed by Simon Copley was the winner for the category. The project started with suppling metal web joists to ending up tendering for the entire roof structure of the main apartment building and ten individual bungalows - resulting in almost 3,500sq m of the roof surface and 2,500 manufactured items.
The highly commended design was awarded to DWB Roof Truss Ltd’s Phil Daniels for the Sianwood project. Judges were impressed by the application of
Developed by housebuilder Vistry Group, the new Vistry Innovation Centre features a flagship property that relies on a fabric first approach mixed with a range of cutting-edge technologies needed to create the homes of the future. Glidevale Protect supplied a combination of its low emissivity products - Protect TF200 Thermo external wall breather membrane and the air and vapour control layer Protect VC Foil Ultra for the internal walls of the concept home.
Both membranes feature a high-quality reflective surface with strong aged thermal resistance that is designed to prevent heat loss, and when used together as a system, they are particularly effective at maximising thermal efficiency. With the two products having recently received independently verified Environmental Product Declarations (EPDs), they are ideally suited for use in the next generation of low carbon homes.
Glidevale Protect is one of a number of innovative product manufacturers to support Vistry Group in the creation of this important research facility, having worked closely with leading builders’ merchant Jewson, one of the main sponsors on this project, in the supply of its construction membranes.
Posi-Joists in ensuring a prefabricated design solution for the project that was creatively achieved.
Nick Boulton said: “The trussed rafter industry is keen to highlight the problem-solving and design skills required in such an important element of the roofing system in construction projects. Thank you to all the designers who have entered the awards this year, it was very fascinating to see the creativity and technical expertise in all the designs that were submitted. I would like to congratulate all those who took part, particularly the winners of this year’s Awards and look forward to watching your continued success in the industry. The Roofscape Design Awards will be returning in 2025.”
Source: www.tra.org.uk
Jack Brayshaw, Head of Technical Innovation at Vistry Group commented: “Collaboration and support from our supply chain partners has been an integral part of the development of the Vistry Innovation Centre as we brought together more than 50 individual suppliers. The Centre is designed to pave the way for creating ‘next generation’ future-proofed homes, so it was crucial to design and develop the property with the most energy efficient products available built on the foundation of a fabric first approach. The products and materials installed at the centre not only work well individually but together provide a holistic, whole house solution and we are pleased to include Glidevale Protect’s construction membranes in this project.”
Located at Vistry Works East Midlands, the housebuilder’s timber frame construction factory in Leicestershire, the Vistry Innovation Centre has been constructed using 18 different trades and 54 suppliers, featuring over 100 different products and smart technologies.
Source: glidevaleprotect.com
MTX has completed complex groundworks for the new Endoscopy unit in Phase 2 of the new Northern Care Alliance NHS Foundation Trust (NCA) Community Diagnostic Centre (CDC) in Oldham, one of the largest in the UK.
Preparing foundations for the new two-storey Endoscopy unit involved the removal and disposal of a substantial quantity of contaminated soil at the former factory site, and construction of a retaining wall to buttress the sloping site. The location includes a basement area and a former reservoir, which required specific measures to ensure effective site drainage.
MTX Project Lead Gareth Roberts explained: “MTX has worked extensively with the structural engineer to find a cost-effective solution for the groundworks, taking into account the challenges inherent in the site. The ground remediation strategy was developed throughout the design stage. After thorough site investigations we created a detailed plan for dealing with the challenges and creating the foundations for the new unit, while at the same time MMC structural modules were manufactured offsite to shorten the project duration. Construction of the 1800m² Endoscopy Unit will involve using precisely engineered factory-built structural steel units which will be craned
into position. MTX is proud to be involved in creating this exciting new facility which will benefit so many patients.”
The accommodation comprises three endoscopy procedure rooms, four consulting rooms, a waiting room for around 20 people, recovery areas, and various ancillary accommodation. The first floor is occupied by an enclosed plantroom towards the rear of the building. Barney Schofield, Director of Planning and Delivery at the Northern Care Alliance NHS Foundation Trust, added: "We are excited that work is under way on our new Endoscopy unit at the Oldham Community Diagnostic Centre. The unit will give us advanced capabilities to diagnose illnesses such as cancers faster and earlier, within a convenient and accessible setting for patients.”
The Oldham CDC is a commercial partnership between the NCA, which runs The Royal Oldham Hospital, and Alliance Medical Limited, working alongside partners including Oldham Council, NHS Greater Manchester, and NHS England. It is one of the country’s largest out-of-hospital diagnostic centres. The Endoscopy unit is part of the Phase 2 development of the Oldham CDC in Salmon Fields, Royton that opened in December 2022. Since opening, it has served over 30,000 patients in the region with capacity set to increase when the new unit is operational. Community Diagnostic Centres are part of the government’s national investment to improve patient access to diagnostic care without the need to attend acute hospital sites, and they aim to offer an improved experience and outcome for patients.
Source: www.mtxcontracts.co.uk
Celebrating a Decade of Pioneering Innovation within the Offsite Industry
Co-located with Offsite Expo
Industry Networking Reception
Over 650 Industry Pioneers
There are 24 categories that cover every aspect of the industry from hybrid and modular technology to engineering and installation, ensuring that all aspects of the offsite building process is celebrated – recognising the design and technology that makes these inspiring projects possible.
ENTRY DEADLINE: FRIDAY 31 MAY 2024
Photography on a Red Carpet Arrival
The Offsite Awards provides one of the most effective platforms for targeting the offsite industry, presenting the ideal opportunity to maximise exposure and penetrate this economically important market. The 2024 marketing campaign is ramping up and many of the sponsorship packages have already been snapped up by savvy companies wanting to gain the full exposure that the next months will bring.
Contact Emily Dyer on 01743 290025 or email emily.dyer@radar-communications.co.uk Paparazzi
Embracing 20 years of evolution, Buildoffsite (BOS) has refreshed its brand identity in preparation for its anniversary in 2024. As they outline here, the transformation reinforces its commitment to innovation, collaboration, and leadership within the offsite construction industry.
At BOS, we believe in the power of collaboration to drive meaningful change. Our new brand name embodies this ethos, with 'B' representing Buyers, 'S' representing Suppliers, and 'O' representing Offsite — together forming a collaborative ecosystem that fuels innovation and propels the industry forward. With BOS, we are not just rebranding – we are reaffirming our dedication to fostering partnerships, breaking down barriers, and shaping the future of construction. In the dynamic realm of the construction industry, innovation serves as the driving force behind progress. Among the myriad initiatives shaping this domain, the history of BOS emerges as a testament to ingenuity, collaboration, and forwardthinking.
A significant turning point occurred in 1999 with the establishment of prOSPa – a visionary three-year Co-Construct project in partnership with Loughborough University, spearheaded by CIRIA. The primary objective of prOSPa was to catalyse change by identifying, disseminating, and advocating offsite opportunities across a diverse spectrum of construction technologies. In the ensuing years, prOSPa gained recognition within the construction industry for its disruptive ideas and novel approaches. Through collaborative efforts, the project blossomed into an industry network, amplifying the voice of the offsite sector, and fostering a culture of innovation and collaboration.
The year 2004 marked a milestone in this journey as prOSPa transitioned into what is now known as BOS – an evolution reflective of its growth, impact, and enduring legacy. With this transformation, BOS solidified its position as a driving force behind innovation in the construction landscape. In response to the UK government’s ambitious target of constructing 300,000 homes annually amidst challenges such as rising construction costs, inferior quality traditionally constructed homes, and a significant shortage of construction skills, the Buildoffsite Property Assurance Scheme (BOPAS) was developed in 2013 in partnership with BLP, Lloyds Register and RICS. Recognised by mortgage lenders, BOPAS provides the necessary
assurance that properties constructed using modern methods of construction (MMC) will be readily mortgageable for a minimum of 60 years. This assurance is crucial in instilling confidence among stakeholders, including lenders, developers, MMC providers, contractors, housing associations, and government agencies.
The accreditation process involves rigorous evaluation of construction technologies and project management practices to ensure adherence to industry best practices. Accredited MMC providers listed in the BOPAS database, offer a valuable resource for stakeholders seeking validated construction systems and proficient service providers. Furthermore, the introduction of BOPAS Plus in 2022 reflects BOS’s commitment to driving digitisation and fostering a collaborative culture within the construction sector. This enhanced scheme focuses on the preparedness of the offsite sector to address the
challenges of digitisation, with validation involving accredited manufacturers at various positions within the digitisation and offsite spectrum.
The BOPAS accreditation scheme not only fosters confidence in innovative construction but also contributes to the overall advancement of the construction industry. With BOPAS, stakeholders can navigate the complexities of MMC adoption with assurance, paving the way for a future where construction is not just about buildings but about transformative experiences. Today, the legacy of BOS continues to resonate, inspiring a new generation of innovators and industry leaders. Its journey serves as a beacon of possibility, demonstrating the power of collaboration, perseverance, and visionary thinking in shaping the future of construction.
As we reflect on our journey of evolution and innovation, it's essential to highlight our commitment to
OFFSITE EXPO INTERNATIONAL SUMMIT: EXPLORING THE FUTURE OF CONSTRUCTION
shaping the future of construction through our Manifesto. On 18 July, we will be conducting a review of our Manifesto, reaffirming our vision and strategies for driving progress in the offsite construction industry. We invite all interested parties, whether in research, events, or membership, to join us.
If you share our passion for advancing construction through collaboration and innovation, please email us at info@buildoffsite.com to learn more and get involved. Together, let's build a brighter future for construction. #CollaboratingForImpact.
Images:
01. Desborough Road. Courtesy Premier Modular
02. MMC Category 1 and 2 delivery is helping boost housing numbers. Courtesy Building Better/Partnerships for Homes/LoCal Homes
03. Formed in 2004, BOS recently rebranded and is celebrating 20 successful years in operation
As we celebrate our 20th anniversary, BOS is excited to announce the Offsite Expo International Summit, co-hosted with Offsite Expo, on 17 September 2024 as a platform for international collaboration and knowledge exchange within the offsite construction industry. The free to attend Summit promises to be a catalyst for innovation and collaboration, shaping the future of construction as we embark on the next phase of our journey. A few of our confirmed speakers include:
• Paul Wilkinson, Vice Chair nima – with extensive experience in digitisation and construction, Paul Wilkinson brings invaluable insights into the intersection of digital technologies and offsite construction. Bringing expertise in digital passports and innovative digital strategies, you will see the unique perspectives on the future of digital delivery in construction.
• Azim Jasat, Senior Industry Manager, Autodesk – Azim has been instrumental in shaping the digital journey of construction. His expertise in digital technologies promises to illuminate the path forward for offsite construction.
• Ignacio Navarro – with a wealth of experience at Ferrovial, Ignacio Navarro brings deep insights into sustainable construction practices and their role in achieving net-zero emissions globally.
• Bengt Magnussen, Commercial Director, TALO – Bengt brings expertise in residential supply delivery, focusing on scalability, quality assurance, and confidence-building measures.
• Rosanna Law, Director of Housing, Hong Kong (invited) – with a background in housing development in Hong Kong, Rosanna Law offers insights into innovative approaches driving advancements in residential supply delivery and fostering collaborations to accelerate the adoption of low-carbon practices.
As industry trailblazers we don’t mess around.
With a ‘can do’ attitude and in-depth technical know-how, the Frameclad team are keen, fiercely competitive and are considered disrupters within the light steel sector.
LOADBEARING STRUCTURES I STUD & TRACK SYSTEMS I INFILL OR OVERSAIL I PANELISED SOLUTIONS
EXPERIENCE – working nationally for 15 years, bringing a wealth of skills to the table
APPROACH – ‘can do’ attitude with the ability to tackle any job large or small
ADAPTABLE – keen to go that extra mile, with tailored consultancy services and flexible pricing structure
AGILE – fiercely competitive with quick turn-around times and the ability to make swift decisions
TECHNICAL KNOW-HOW – in-house expertise with a 12-strong team of designers and engineers
DIGITAL ENGINEERING – bespoke Tekla software offers complete traceability in line with ‘golden thread’ requirements. Enhanced visualisation through augmented and virtual reality
CUTTING EDGE TECHNOLOGY – advanced offsite manufacturing delivers precision engineered light steel systems, delivered to site ready for fast-track installation
MANUFACTURING – one of the largest ranges of steel sections available in the UK today
EXTENSIVE SUPPORT – regional teams assist with specification and compliance of SFS systems
ADDED VALUE – through expert design, precision manufacturing and on-time in full delivery
EVIDENCE – fire tested with major board manufacturers with a growing suite of fire test and performance data
INDEPENDENT VALIDATION – BS EN 1090-1: 2009 + A1:2011, BOPAS Accreditation, CE Certified, and SCI / NHBC Stage 1 System Certification Infill Walling
BUILDING SAFETY – fully compliant steel framing systems subject to rigorous safety standards
Following last year’s successful launch of the specification guide for Metframe, voestalpine Metsec’s market-leading, pre-panelised offsite framing solution, the company has recently published the latest version of its Steel Framing Systems (SFS) Specification Manual.
The Manual is the industry’s most comprehensive resource for professionals involved in the specification, installation and use of light gauge steel framing systems.
Primarily installed ‘stick-built’ onsite in concrete or steel column and beam structures, SFS components are also used in the offsite fabrication of pre-panelised construction systems, such as Metframe, where frames are assembled in factorycontrolled conditions remote from the construction site complete with requisite insulation materials and sheathing boards.
Whichever method of construction is used, SFS lends itself perfectly to offsite construction, making a major contribution towards a project realising the time and cost efficiencies for which the approach is widely recognised, as well as quicker returns on investment.
In addition to its use as infill walling for concrete and steel structures, SFS can also be used to create complete load bearing superstructures for low to medium rise buildings of up to five storeys in height with all components
1being delivered to site, effectively in kit form, ready for immediate installation and subsequent follow-on trades.
Widely recognised as the industry bible for SFS, the new 176-page manual is packed with just about every piece of information required to assure the successful design, specification, selection and application of voestalpine Metsec’s SFS, based on years of experience, expert technical knowledge and a vast library of independent testing.
Produced in digital and interactive formats, the manual is a perfect example of why voestalpine Metsec SFS light gauge galvanised steel structural framing systems have been successfully assessed to the Code for Construction Products Information (CCPI), introduced by the Construction Products Association (CPA) in response to Dame Judith Hackitt’s review of Building Regulations and Fire Safety, set up following the Grenfell Tower tragedy.
The manual’s initial content includes coverage of the factors that might be considered when specifying steel
framing systems for a project and the typical processes involved from design through installation to final hand-over, including SFS benefits versus alternative building systems, performance standards, professional indemnity, MetWALL Perform 30-year warranty, project timeline, BIM design, CPD presentations and installer training.
Following these broader considerations, the manual features detailed information on the major applications of SFS in infill walling, load bearing situations, continuous walling and high bay walling.
Each application area contains detailed information on relevant performance criteria and the use of SFS with popular sheathing and cladding materials, including fire performance data based on full independent testing. This is illustrated with high quality architectural drawings showing typical wall buildups and case studies featuring prestigious projects demonstrating the successful application of SFS has been successfully used in a variety of projects, including residential, education and commercial situations.
The manual concludes with details on SFS components, external finish options and fixings, providing the reader with what is probably the most detailed appreciation of steel framing systems in general and, of course voestalpine Metsec’s SFS.
The new Steel Framing Systems (SFS) Specification Manual is available to view and download at: www.metsec.com
Images: 01. The updated Steel Framing Systems (SFS) Specification Manual
A comprehensive resource for specification, installation and use of light gauge steel framing systems
Widely recognised as the industry bible for SFS, the 176-page manual is packed with just about every piece of information required to assure the successful design, specification, selection and application of voestalpine Metsec’s SFS.
voestalpine Metsec plc www.metsec.com
SCAN ME for your copy
As the demand for offsite construction continues to rise, the choice of insulation material becomes paramount in ensuring efficient, safe, and sustainable buildings.
1
Superglass, one of the UK’s leading insulation manufacturers, offers an extensive range of glass mineral wool insulation products and after-care service tailored for offsite construction projects. They manufacture 100% of their rolls, slabs and batts insulation products in Stirling and focus on supplying products for Modern Methods of Construction (MMC) product categories one and two –pre-manufacturing 3D and 2D primary structural systems – ideal for the offsite market.
Tony Gordon, Head of Product Management at Superglass, outlines some of Superglass products’ key offsite benefits. “Superglass insulation, made from up to 84% recycled glass is lightweight and compression packed which minimises both the cost and environmental impact of transportation in comparison to other materials.
“Fire safety is a critical feature that we believe should be in-built into every product across the construction supply chain. All Superglass products are deemed non-combustible with a fire classification of Euroclass A1 (the highest possible rating) when tested
2
to BS EN 13501-1 Reaction to Fire. This commitment to safety is integral to not only our ethos, but to the safety of staff on site and the ultimate occupants of the building.”
As we all become increasingly environmentally aware, the importance of wrap-around insulation in our homes and buildings is of paramount importance to improve a building’s efficiency rating and to ultimately reduce bills and operational carbon.
“Superglass glass mineral wool insulation provides effective thermal insulation which in turn maintains a comfortable indoor living environment, adds Tony. “Our glass mineral wool insulation's performance remains uncompromised during the offsite assembly process, boasting a thermal conductivity range of 0.044W/mK – 0.032W/mK. We are committed to operating sustainably and producing products that improve the sustainability of our built environment. Once installed, Superglass products can save up to 200 times the energy used in the manufacturing process. The insulation products are backed by an Environmental Product
Declaration (EPD) and hold ISO 14001 Environmental Management certification.
“In addition to thermal benefits, Superglass insulation products excel in acoustic insulation, a crucial factor in reducing sound transfer between rooms or in party and separating walls between dwellings. The Acoustic Partition Roll (APR) for internal partitions and Multi Acoustic Roll for internal and separating floors are standout products in this category.
“Versatility, customisation and flexibility are integral for constructing with offsite materials. All Superglass products are inherently flexible and can be easily cut or shaped to fit various spaces. This makes installation simple and quick due to a wide range of thicknesses and product widths, especially if standardisation of components may not always align perfectly with sitespecific conditions.”
Beyond the product offering, Superglass offers consultation with its Superglass Technical Services team to provide a service tailored for buyers and installers. The team provides services such as U-value calculations, Psi value calculations, and more, ensuring that projects meet regulatory requirements for builds. Superglass’s products can be found on the NBS Source database.
Tony concludes: “We believe in working with our customers to ensure we provide the best solutions for their requirements rather than simply offering products. I’d encourage anyone who wants to understand how our portfolio of insulation solutions can work for their project to get in touch.”
For more information visit: www.superglass.co.uk
Images: 01-02. Versatility, customisation and flexibility are integral for building with offsite materials
Following the success of the inaugural MMC Ireland National Conference last year, the event returns on 22-23 May 2024 at the stunning Lyrath Estate, Kilkenny, for more discussion on the advances and industry barriers affecting the offsite market.
Last year delegates from across the European offsite sector gathered at Croke Park, Dublin for the 2023 conference. The event hosted in partnership with MMC Ireland and Explore Offsite, exceeded expectations, with exhibition space and delegate tickets selling out well in advance. This year is set to be another sell-out event with extremely high demand.
Raising the bar and building on the success of the previous event – while diversifying and expanding the programme and exhibition to attract a wider audience – the 2024 conference has been increased to two days and will be chaired by Darren Richards, Managing Director of Cogent Consulting – The Offsite Experts.
Paul Tierney, CEO of MMC Ireland said: “The resounding success of the first conference showcased the inherent expertise and technical knowledge that exists across the industry and our membership. As we work to champion the benefits of offsite technology, we welcome the robust commitment to increase the adoption of modern methods of construction shown by the sector and government. We have an outstanding venue for our 2024 conference and a packed schedule. This is a destination event which offers the opportunity to learn from the best in this rapidly evolving industry as well as network with industry innovators and change-leaders in stunning surroundings.”
The event will see two full days featuring a high-profile speaker programme showcasing the best in offsite construction with presentations and case studies alongside a pop-up exhibition of offsite specialists. During both the morning and afternoon sessions, panel discussions will offer further insight into some of the key event themes and topics. Day One will culminate in a drinks reception where delegates can network with leading industry players from across Ireland and beyond. Day Two will continue the discussions supporting the development of new skills and specialisms throughout the day and there may even be an opportunity to get a round of golf in!
Tackling the big conversations and facing the positive and negative impacts of the last year, the conference programme will not shy away from difficult topics and will look to address some of the challenges facing the offsite industry. Key topics will include the road to net zero and the circular economy, platform design and Design for Manufacture and Assembly (DfMA) together with risk and future technology profiling.
The road to net zero no doubt presents major opportunities for the MMC industry, but the conference will consider how the industry can develop a more accurate dataset for underpinning claims around embodied carbon and whole-life carbon. As Ireland looks to develop more sustainable buildings, the concept of using MMC technology in the context of circular design is another key speaker topic. This combined with the increased use of advanced digital technology by MMC suppliers is predicted to present a major opportunity for the sector.
DfMA has been at the forefront of MMC approaches for a decade or more but now platform design is coming to the fore. With the industry being at a crossroads, now is the time to debate whether there is a desire to collaborate and standardise with the wider use of platform approaches or maintain the ‘status quo’ by designing and producing bespoke solutions for every build.
MMC Ireland invites delegates to join in the conversation and connect with key players in the sector at their National Conference. As a leading sector representative body, MMC Ireland brings together the collective expertise of members to provide guidance, support and project insights on key industry issues. From technical standards and best practice principles to training and professional development, the organisation is dedicated to ensuring that members have the resources and regulatory environment they need to succeed in today’s competitive and increasingly global marketplace.
To learn more about MMC Ireland and how to become a member visit: www.mmcireland.ie
If you wish to book your place at the conference visit: www.mmcireland.ie/events/
For full details on the national conference programme and explore sponsorship opportunities contact: ellie.guest@radar-communications.co.uk
And finally, one of the most contentious topics – why have so many UK MMC companies ceased trading in the past 12 months? Presenters will explore the optimal business model to reduce the commercial and financial risk, exploring pipeline development and demand forecasting. Whilst all of these topics will be addressed in the context of Ireland and the UK markets, the speaker line-up will be geographically diverse with international speakers presenting best practice comparisons, industry trends and technological and cultural differences.
See session highlights here and full details online by scanning the QR code.
STANDOUT SESSIONS & HIGHLIGHTS
ADOPTION OF MMC AT GOVERNMENT LEVEL
Keynote Speaker - INVITED
Celine McHugh, Principal - Department for Enterprise, Trade and Employment
Seán Armstrong, Senior Adviser-Building Standards - Department of Housing Planning and Local Government
KIT OF PARTS APPROACH TO STANDARDISATION
Anne Daw, Head of MMC Delivery, HLM Architects
Tom Gregory, Senior Architect - Bryden Wood
Trudi Sully - UK & Europe Lead, Industrialised Design and ConstructionMott MacDonald
OFFSITE IN ACTION - CHALLENGES & OPPORTUNITIES
Scott Tacchi, Head of MMC – Sir Robert McAlpine
Philip Weinmann, General Manager - ABM
Kevin Masters, Director, Major Projects Advisory - KPMG
STANDOUT SESSIONS & HIGHLIGHTS
TECHNICAL PERFORMANCE AND REGULATORY COMPLIANCE
Keynote Speaker James Young, Director of Engineering Services, Evolusion Innovation
Martin Searson, Head of MMC - NSAI
Dave Quinn, Quality Director - BB7
CARBON COUNTING, SUSTAINABILITY & BUILDING PERFORMANCE
Stephen Barrett, Whole Life Carbon Project Lead - Irish Green Building Council
PROCUREMENT AND SUPPLY CHAIN CAPACITY
David O’Brien, Principal Officer - Office of Government Procurement
Darragh O’Brien, Housing Minister
Pia Feeney, Government & Infrastructure Advisory – EY
Paul Tierney, Chief Executive Officer - MMC Ireland
SPONSORS & EXHIBITORS INCLUDE: (Correct at the time of printing)
On the eve of the MMC Ireland National Conference, we hear from MMC Ireland’s CEO Paul Tierney, on the shape of the offsite market in Ireland and some of the common challenges being faced in the UK.
Q: Can you say a little about the background and formation of MMC Ireland? Has there been a need for a more organised central voice for Irish offsite providers and market development for a while?
Paul Tierney (PT): The idea for MMC Ireland came about in 2019 when Arthur O’Brien of C+W O’Brien Architects and Declan Wallace of Evolusion Innovation - who had both separately recognised a need for the emerging offsite and MMC sector at that time to be better supported – came together. MMC Ireland was formally established in 2022 by 20 founding members and has since grown to a membership in excess of 80 companies. The remit of the organisation is clear – as a memberdriven body, MMC Ireland’s aims are to advance the interests of our members and the sector as a whole. What this looks like on the ground is further development and growth of the marketplace and project pipeline, both in Ireland and internationally.
Q: MMC Ireland has three key Working Groups – what are these seeking to achieve and how will members collaborate to boost the profile of offsite methods across Ireland?
PT: The groups are ‘Technical Guidance & Knowledge Sharing’ chaired by Ronan Lonergan of Cairn Homes and Eoin Waldron of Castle Modular, that is working on delivering an MMC catalogue of all member companies, their products and details of the technical performance of these products. The goal of our ‘National Policy Support & Integration’ group, chaired by Pat Kirwan of C+W O’Brien Architects is to harness the project insights of MMC Ireland members and and identify barriers to MMC adoption, to ensure alignment of current government policy with our members ability and capacity to deliver on government targets.
Our last group, deals with ‘Awareness & Education’ and is chaired by Dick Clerkin of Clerkin Consulting and
Nicola McKay of HLM Architects. There is a huge body of work to be done in educating the industry, government and senior civil servants, and, most critically, project owners, on the compelling benefits of embracing offsite and other modern methods of construction. Given the deep manufacturing and technical expertise of our members, the approach to education is data-driven, with data extracted from project case studies and the shared learning of our members across a range of international, multi-sectoral projects.
Q: How strong is central and local government support for the offsite sector in Ireland? The Housing for All strategy highlights offsite as a key delivery method. What frameworks are in place to develop specific sectors and is there a recognition of the need for alternatives to traditional sitebased methods?
PT: In Ireland there is strong and growing State support and appetite for enabling the delivery of projects
through offsite construction. We are seeing this appetite grow significantly as the need for housing, education and healthcare delivery becomes ever more urgent.
Our role within MMC Ireland is to help local and central government to set up the right procurement frameworks to deliver, by providing technical guidance and insights based on the experiences of our members. Critically, our Ireland-based members have global project expertise that the State can and does leverage. Also, MMC Ireland membership of companies outside of Ireland is growing significantly and this further boosts the project knowledge available for sharing with local and central government.
Government has shown a great awareness of the programme benefits of using MMC and there is a clear mandate for State projects to embrace or ‘lean into’ the use of offsite construction. At MMC Ireland, we are committed to engaging with the excellent State initiatives in place, including the MMC Demonstration Park at Mount Lucas, and the range of academic researchers and training providers currently tasked with identifying technical challenges and skills gaps that could hinder MMC adoption within both the public and private sector. Progress made in recent years is encouraging and signals that MMC adoption is on the right trajectory in Ireland.
Q: The imperatives of sustainability, energy efficiency and higher quality buildings are common construction aims everywhere, how will MMC Ireland and its members help bring about these changes domestically and internationally?
PT: Offsite construction is more sustainable by default, a fact that is not as well communicated as it could or should be. At an individual level, our respective members are innovating new products and designing new low carbon systems to help project owners deliver on sustainability targets across a range of metrics, including waste reduction and moving from ‘cradle to grave’ to a more ‘cradle to cradle’ approach that incorporates
22 & 23 MAY 2024
circular economy principles in a way that is workable for the industry. At an organisational level, MMC Ireland launched the national calendar for MMC events earlier this year, hosting not only members’ events, but events from across the public and private sector, including academic programmes and CPD sessions.
Q: You had a long involvement with ESS Modular with time in the UK. Where do you see the similarities and differences between offsite development in Ireland compared to the UK or the rest of Europe –e.g. Scandinavia and Germany?
PT: There are many similarities between offsite development in Ireland and the UK, in particular, the shared challenges of growing market demand to ensure a sustainable, buildable pipeline. The needs of industry are similar between the two countries, both having an experienced MMC sector, and the increasing urgency of delivery across housing, healthcare and education is certainly a common challenge.
The key difference is the leadership at a government level and the willingness of the government to listen to the voices of industry. In Ireland, we have a government that is open, one with an appetite to innovate and tackle some of the country’s most deeply entrenched problems and this has made a huge difference. The State has positioned itself as an enabler of solutions, and this is not the experience of many of our international counterparts. When you bring a forward-thinking construction community together with decision-
makers who want to listen and to want to learn, change is inevitable. There is no doubt in my mind that Ireland will be a centre of MMC excellence, in fact, we are already seeing that emerge.
"On one hand, we have a government that is open to learning and willing to engage with industry; and on the other, we have a technically brilliant MMC sector that has the capability and capacity to scale delivery. Our role within MMC Ireland is to cut out the noise and waste between the two."
Q: What are the main delivery challenges in the Irish market – slow planning approvals and lack of pipeline are causing issues in the UK, especially with volumetric providers, which are finding trading conditions difficult – do these planning and pipeline problems sound familiar?
PT: Unfortunately, many of these challenges are familiar to Irish operators. Planning has been a significant problem – however, the government has promised a radical overhaul of Ireland’s planning regime. While the new Planning & Development Bill 2023 falls short of radical reform in its current guise, we are hopeful that it will improve planning time frames. A number of our development and project owner members have reported an improvement in planning across submissions and timelines over the past year. Greater certainty around planning and project timelines would certainly go a long way towards
establishing the buildable pipeline that Ireland-based manufacturers need to invest further in their facilities and people.
Q: Across the various offsite typologies, which ones are being adopted the most and seen as successful in Ireland – timber frame, light gauge steel, panelised – and what sectors outside of residential are seeing the most growth – education is a key area?
PT: 2D timber frame is the most commonly used MMC methodology in Ireland, followed by light gauge steel –both 2D panelised and 3D volumetric (there is no significant 3D timber frame in Ireland). Timber frame is the most popular, used primarily and exclusively in residential. Light gauge steel (2D panelised) is becoming more and more used in residential, typically in apartment buildings. Also, LGS is used extensively in 3D volumetric across all sectors, particularly healthcare, education and, or more recently, in residential.
Q: You have said that this is a “critical time for MMC adoption, and Ireland cannot afford to get it wrong.” How do you see the offsite sector developing in Ireland over the next 18 months and what ideally do you want to see from a MMC Ireland perspective in 2024?
PT: It is a critical time for MMC adoption. We cannot afford to get this wrong. Within MMC Ireland, we are working collaboratively, across our working group initiatives, and on a number of Government steering groups, helping the government shape the policies around MMC initiatives. And it is critical that we are involved, given the deep expertise of our members. This expertise is helping the government to shape the future of MMC – and the future of construction – in Ireland. By working collaboratively, together and with Government, we are improving the chances of making the sector an ongoing, sustainable success.
For more information on the work of MMC Ireland and to get involved visit: www.mmcireland.ie
Images: 01. Paul Tierney, CEO, MMC Ireland 02-04. MMC Ireland was formally established in 2022 by 20 founding members
FALK, your first choice for insulated panels! Trusted by MMC buildings in Ireland and the UK. Quality, innovation, and reliability guaranteed. Let’s elevate your next project with FALK panels!
FALK, clever construction for a circular future.
Introducing CradleCore®: FALK’s breakthrough in panel recycling for sustainability. Achieving circularity, we reuse and recy cle steel and PIR components. Lower EPD by 40% compared to market average. Choose FALK for eco-friendly building solutions!
As the construction industry continues to rapidly evolve, there is a huge pressure to re-evaluate the way we build, and how we can save time and money whilst also enhancing sustainability.
Modern methods of construction
(MMC) and offsite building is one answer that could provide a solution to many challenges, which is why events such as MMC Ireland’s National Conference are vital for the industries progression. The conference is building on the success of its inaugural event that took place last year. It aims to bring together collective expertise and provide guidance, support and project insights on the key industry issues facing MMC and offsite construction.
Knauf, MMC and offsite building
At Knauf, we firmly believe offsite and MMC offer true advantages and benefits to the industry, offering faster builds and therefore more capacity, reduced project costs and a lower carbon footprint. However, like any other aspect of the construction industry, it does not come without its own obstacles to overcome.
1MMC and offsite construction has received setbacks such as the closure of modular factories, companies going into administration and fluctuations in levels of demand. Offsite factories require a high level of structure to result in smooth operations and ensure the production line runs correctly with maximum output, so efficiency and productivity are key when it comes to offsite construction.
Sustainability is crucial throughout the entire construction industry, but it is an aspect where offsite and MMC construction can really shine. The nature of offsite building itself offers less carbon emissions on projects due to cutbacks of energy usage on site. Knauf works with project teams to identify areas on projects where waste can be reduced, such as reducing offcuts from plasterboard or minimising water usage on site. Products such as Knauf Airless Finish and its GIFA systems also offer water-
saving methods of construction to further aid project sustainability.
Embracing MMC and offsite building requires a workforce that is competent and knowledgeable because minor errors at scale can be costly. This means training is crucial for those involved in the methods and techniques of offsite construction as new innovations are always being developed.
Knauf solutions
Knauf is able to add value in many aspects of offsite building, one of which is reducing the amount of time spent in the building process. Structural components such as the Knauf ThroughWall provides a BBA Approved solution in the form of an all-in-one product, comprised of steel framing components (SFS), internal insulation, plasterboard, external sheathing and external insulation.
The ThroughWall system is exemplar of the systematic approaches that can be taken in offsite construction, as it delivers a panelised solution using rolled steel frame to provide certified performance levels. The system can be installed easily in the factory and allows for a range of external finishes such as rainscreen cladding or brickwork, all of which can be added in the factory as well as on site as required.
A common misconception in offsite building is an overall lack of products being certified, which is especially important as the construction industry faces increasingly stringent regulations, particularly in fire safety. The ThroughWall system, amongst many of Knauf’s products, dispel this notion, as it has all necessary performance certifications to provide compliancy. The Knauf System Performance Warranty also offers additional levels of protection when the full system approach is taken.
Another time saving offering from Knauf is its Airless Finish plaster. The Airless Finish spray plaster can be applied significantly faster than traditional plastering methods, and with a reduced drying time it means projects can move along much quicker. The product comes ready-mixed and once in the machine is extremely easy to apply, meaning less manpower required to finish the job.
GIFA Flooring is another product by Knauf that exemplifies the advantages of choosing the right projects in offsite building. A tongue-and-groove interlocking flooring system, it is easyto-install and eliminates the drying times that come with traditional wet floor screed, offering an efficient and structurally stable flooring solution.
When approaching the issue of sustainability within offsite construction, Knauf’s products can also enhance a project in this domain. For example, the Airless Finish plaster and GIFA systems both use significantly less amounts of water than their
traditional alternatives, offering an immediate sustainability saving on-site. On a wider level, Knauf is committed to making substantial changes in their own supply chain including a more sustainable delivery fleet and an increase of recycled plastic content in product packaging.
Knauf recognises the need for a competent workforce when it comes to embracing MMC and offsite building. That is why Knauf offers a wide range of product training, including the Airless Finish, to enable contractors to quickly and efficiently upskill and embrace offsite and MMC solutions.
Knauf offers MMC and offsite designers the ability to keep offsite construction simple and easy with its Planner Suite – System Finder, an online tool that provides designers and architects with the ability to search for systems and view supporting data and specification documents quickly and easily. Knauf products can be imported into Revit and ArchiCAD to make project design simple, and
products can also be saved for future project access.
Knauf is looking forward to showcasing its innovative products and systems at MMC Ireland’s National Conference. Visit the Knauf stand to meet our expert colleagues and discuss first-hand products such as the Airless Finish, GIFA flooring and the ThroughWall system, as well as our high-performance Fire Panel and SoundShield plasterboards.
Knauf’s product systems are already being enjoyed by large scale offsite construction teams, and we continue to look forward to supporting the MMC and offsite construction industry to innovate and develop a more sustainable future.
For more information visit: www.knauf.co.uk
01. Ten Degrees, Croydon. Courtesy Tide Construction/Vision
With supply chains under the sustainable spotlight, WISA-Spruce Special acts as a reliable product and catalyst for a global renaissance in construction plywood.
1
Data shows that timber and timberbased panels have become the fastestgrowing categories in contemporary construction, particularly in the offsite and modular sector. Whether it’s walls, floors or ceilings, recent, proprietary research we conducted showed these products are predicted to make up a massive proportion of the materials used in a market forecast to grow to £1.2billion by 2028.
European-sourced plywood is particularly popular, and demand is only set to increase as the use of modern methods of construction (MMC) for commercial, residential, and public buildings becomes more prolific.
However, as the last two years have shown, not all plywood is manufactured equal, with counterfeit, poor-quality or embargoed panel products flooding the market in the wake of the Russia-Ukraine conflict. Indeed, accusations of sub-standard units have also been a recent sore point within the modular sector with several high-profile developments called out over their structural integrity. Both situations have seriously dented investor, trade, and customer confidence.
2
Fortunately, these twin issues can be addressed by working with responsible, ethical supply chain partners dedicated to the combined values of safety, security, and sustainability. UPM WISA is one such brand, and its WISA-Spruce Special, a catalyst for a global renaissance in plywood is set to support another for offsite construction.
Sourced and made from responsibly managed, sustainable forests in Finland, WISA-Spruce Special is on a mission to set a new standard within the timber panels market. Its reputation as a high-spec, yet competitively priced product, is an instant mark of quality in any build in which it’s used. It’s looking to develop this further for the offsite sector, working in collaboration with James Latham to showcase its unique attributes and why we’re one of their key distributors in the UK and Ireland. What makes WISA-Spruce Special so well-suited to offsite construction?
Benefits include:
• Structurally robust, suitable for loadbearing applications
• Dimensionally consistent, providing all-important repeatability in an offsite manufacturing process
• Possesses up-to-date EPDs and certification from globally
recognised sustainable and responsible forest management certification schemes, supporting developers looking to achieve much-coveted certifications like LEED and BREEAM for projects.
• Ultra-sustainable through use of WISA® BioBond adhesive; replacing 50% of standard glue’s fossil-based phenol with lignin, timber’s inherent bonding agent reduces the overall carbon footprint by approximately 10%, without compromising technical performance or visual appeal.
Offsite developers also need to know they can rely on there being healthy stock levels, especially for large-scale developments. Well, we’ve got you covered, with WISA-Spruce Special available nationwide throughout our 12 strategically located depots, plus a direct-from-port option for bulk loads and dedicated technical experts to advise on almost any requirement, regardless of scale and scope.
And, with the ability to call off large quantities at short notice, you’ll achieve the all-important peace of mind you can keep your lines running to deliver on short-lead demand increases. That’s not all, it’s also available from James Latham in a Euroclass B FR variant, Wisa Spruce FR.
Come and see us at MMC Ireland 23-24 May 2024. Our team will be ready to make the case for UPM WISA-Spruce Special and answer any other questions you have about our extensive portfolio of timber-based panel products. For more information visit: www.lathamtimber.co.uk/ products/panels/plywood/softwoodplywood/wisa-spruce-special
Images: 01-02. UPM WISA-Spruce Special is ethically sourced and made from responsibly managed, sustainable forests in Finland
James Latham is one of the UK and Ireland’s largest independent distributors of timber, panels and decorative surfaces.
With a huge stockholding, solid supply chains and market-leading environmental credentials, we can supply everything you need, from standard construction products to high performing specialist materials
Nationwide depots
Carbon data available Great service Rapid delivery
Product knowledge Huge stockholding
Scan the QR code to find out more
In terms of strength, workability, consistency and certification, WISA-Spruce Special is perfect for an industry that prizes quality, repeatability and accuracy.
• Structurally robust
• Dimensionally consistent
• Also available as a Class-B (B-s1,d0 and Bfl-s1) fire rated variant (WISA Spruce FR)
• Fully certified and sustainable Or visit our website at www.lathamtimber.co.uk
Algeco UK recently shared behind-the-scenes images of its latest 75-bedroom Single Living Accommodation (SLA) complex at the Ministry of Defence (MOD) Stafford.
The company has delivered a full turnkey solution, acting as Principal Contractor to the Defence Infrastructure Organisation (DIO) and the British Army. Modular buildings devised utilising modern methods of construction (MMC) have the potential to deliver significant improvements in productivity and quality for both the construction industry and the end user. They also minimise the work required on-site, which can have added benefits and appeal for those in sectors such as Defence.
The solution provided to MOD Stafford is a CTM Leve1 (Category 1) Pre-Manufacturing 3D primary structural system that will be used to house members of the army. The three-storey building, known as Beacon Barracks, is set to offer high-quality accommodation with integral communal areas, as well as a brick slip façade and sustainable features including solar PV and heat pumps. The modules for the barracks were manufactured in Carnaby in East Yorkshire and delivered to the site with a pre-manufactured value (PMV) of around 80%. MOD Stafford was designed by AHR Architects, supporting the Algeco UK team on the construction stage and architectural design through its Leeds offices.
A full site inspection has now been carried out with strong feedback received by attendees and participants, particularly regarding
For more information visit: www.algeco.co.uk 1 2 3
the overall quality and feel compared to comparative schemes. Volumetric air tests are carried out on all completed projects and the SLA Block at MOD Stafford has achieved a rating of 1.18. Lee Kenton of Build Energy commented that 1.18 is “exemplary for the size of the building” and “far exceeded” the Passivhaus gold standard of 0.60, with an air change rate of 0.48.
The new barracks at MOD Stafford is part of an £800million investment into SLA by the Army over the next decade. This investment into modern infrastructure is set to provide military personnel with the fit-for-purpose accommodation facilities they deserve, as well as contribute to ambitions to become carbon net zero by 2050.
Brigadier Pete Quaite, Head of Army Infrastructure Plans, said: “I visited the Single Living Accommodation under construction at Beacon Barracks at the start of this year. To see the finished block just two months later shows the impressive pace of progress being achieved through our modular design and build programme. This new SLA is another excellent example of how ongoing Army investment is improving the quality of life for our people, providing them with modern, spacious and well-designed accommodation.”
Wayne Yeomans, Algeco UK OSS Sales and Marketing Director added: “This is modular and offsite construction at
its best. I must applaud the Algeco UK team as well as our supply chain partners, including AHR Architects, for making this possible. Working with architects means we have incorporated innovative features into the design, such as solar PV orientation to maximise the amount of electricity produced and optimising the number of overall modules required.
“We were selected as the modular building partner by the MOD because of our track record in supplying high quality accommodation on a diverse range of other publicly funded projects, along with our willingness to collaborate with project partners and deliver excellent value for money. The quality of these solutions is proven by results, like the industry-leading scores achieved in our recent volumetric air test, which is not an easy achievement. We have learnt so much from this project and we are proud this will also help inform the Defence Infrastructure Organisation’s future Programmatic Design approach.”
Images: 01-03. The new modular facilities provide modern, spacious and well-designed accommodation
Algeco Offsite Solutions is part of Europe’s leading provider of innovative, cost-effective and energy-efficient modular buildings.
Our speciality is the creation of high-quality permanent buildings that provide all the benefits of our offsite manufacturing processes.
Certainty of programme, enables ‘Speed to Market’
Standardisation unlocks efficiencies in design, commercials, and programmes
Up to 50% quicker. Reduced programme time equates to working capital saving
Best value – recycle, reuse or repurpose your modular store
Faster completion, certainty of supply, all equal a better ROI
Quality throughout – NPS score of 100 on our retail store deliveries
In response to mitigating issues related to system compliance and compatibility, Elta has emerged as a leader in the ventilation sector with its ‘Prefabricated Solutions’.
This innovative service enables those searching for ventilation systems to purchase tailor-made ventilation units from Elta’s wide range of fans and ancillaries, including its certified smoke range.
For years, project managers and construction decision-makers have traditionally procured fans and ancillaries well in advance of installation, only to encounter recurrent issues. These challenges often stem from sourcing components from multiple suppliers, leading to miscommunication and mismatches between fan controls and other ancillaries. Consequently, these decision-makers may face the need to reorder parts, causing delays and potential compliance issues. It was because of this that the industry looked to create a more innovative solution to mitigate this issue.
Catering to specifiers and contractors engaged in commercial building projects of all scales, Elta’s Prefabricated Solutions present a comprehensive range of products and numerous benefits. This includes a vast array of up to 150,000 customisable fans and ancillaries, covering acoustic equipment, mounts, panels, flexible connections, and fan controls. In addition to offering solutions for Elta’s usual range, Prefabricated Solutions is also applicable to its smoke range. These solutions have a significant size range starting as small as 250mm and
increase all the way up to two metres in diameter.
Manufactured under controlled conditions at Elta's UK facilities in Kingswinford, Fareham, and Colchester, units and components are crafted by industry professionals well-versed in fan system technology. Additionally, Elta's ISO 9001 accreditation ensures that even bespoke prefabricated units receive certification, including smoke fans and associated ancillaries.
The range was launched last year and now leads the market with a wide number of fan types including standard duty as well as tested and compliant smoke prefab solutions, pioneered by Elta’s in-house team led by Colin Moss, Car Park and Smoke Control Manager: “The uptake by the market, from design stages through specification and project supply, has kept the company busy with a growing catalogue of design solutions,” says Colin.
“Manufactured in our West Midlands factory, we have seen a strong level of interest and ownership by team members to continue to excel in providing more and more solutions for our growing customer base. Prefab solutions enable us to work much closer with our customers at critical stages of the project process. With one wrong misstep, decision makers can find themselves in the position where
they must deal with costly delays due to products not being constructed on time or in the right way, or damaged from site activity. Thanks to services like Elta’s Prefabricated Solutions, site safety and efficiency is enhanced, with reduced expenses and betterquality control being at the fingertips of building services engineers and managers.”
A notable advantage of Elta’s Prefabricated Solutions is the ability to able to provide both acoustic and air flow performance data when engineering a solution. This streamlines the process for specifiers and contractors, with Elta's selection software providing essential information upfront.
With a more streamlined design process, utilising services such as Prefabricated Solutions means that both ‘The Golden Thread’ and environmental requirements are met. Alongside this, local disruption in and around the construction site is kept to the minimum with a simple delivery process.
Luke Hammond, Applications Specialist at Elta, added: “Issues such as waiting for a single component to be delivered while the rest of the system waits on-site or damage to the unit in transit are now faults of the past. Thanks to our Prefabricated Solutions service, the entire product is created and transported as one to ensure a hassle-free process.
For more information visit:
www.eltauk.com/prefabricated-solutions
Images: 01-02. The ‘Prefabricated Solutions’ service enables those searching for ventilation systems to purchase tailor-made ventilation units from Elta’s wide range of fans and ancillaries
One order. One frame. One delivery.
Discover how our Prefabricated Solutions for fans and accessories can help you to boost on-site productivity, along with enhancing efficiencies and streamlining your processes. Off-site assembly not only reduces waiting times but saves on cost and eliminates installation problems. The all in one ventilation solution.
Leading manufacturer Glidevale Protect has launched Protect FrameSafe FR – a new Class A2-s1, d0 flame retardant external wall breather membrane offering fire protection across low, medium and high-rise buildings.
Featuring an intricately woven glass fibre fabric with a uniquely developed waterproof and fire-resistant coating, Protect FrameSafe FR is a highperformance breather wall membrane for use on the external side of the frame to integrate with façade wall structures.
Designed to exceed Building Regulations Approved Document Part B, the product is futureproofed against future regulation changes. The current Building Regulations for fire safety states that external wall membranes must achieve at least a Class B fire rating for structures over 11m – Protect FrameSafe FR has a Class A2 reaction to fire, having been independently fire tested by an external laboratory both free hanging as well as part of a system in an end use application, fixed over A1 and A2 substrates using Protect FR tape, which is also available to seal laps.
It is also fully compliant with the test methods contained within EN 13501-1, making it the perfect solution for
higher risk buildings as defined in the 2022 Building Safety Act, including student accommodation, schools, hospitals, offices and care homes as well as being suitable for many developments in London where there is a combustible material ban on external walls of buildings. In addition, the product can be used for housing developments where the property wall has a minimum separation distance of 1m to the relevant boundary.
Protect FrameSafe FR lends itself for use on a wide range of residential and commercial developments across all building heights, providing strong UV stability and up to six months exposure before being covered. It is ideally suited to modular and offsite construction projects, for use on both steel and timber framed buildings as well as on high-rise buildings where full rainscreen cladding systems are also installed.
John Mellor, Head of Marketing from Glidevale Protect commented on the new product: “It goes without saying
that fire safety is a fundamental part of any build, but especially critical with higher risk projects such as high-rise residential accommodation. It’s also crucial that product testing takes into account fire performance as part of the whole building system so that specifiers have the full transparent picture. When we were developing Protect FrameSafe FR and undertaking our due diligence, we knew the product needed to tick all the boxes and be a true ‘hidden protector’ that is fully independently fire tested.”
Produced in the UK at the company’s Nottinghamshire factory, Protect FrameSafe FR is both UKCA and CE marked with full independent fire test certification available.
For further product details visit: www.glidevaleprotect.com/framesafe or for all recommended mechanical fixings and full specification guidance contact Glidevale Protect’s technical team at technical@glidevaleprotect.com
Images: 01-02. Protect FrameSafe FR lends itself for use on a wide range of residential and commercial developments across all building heights
High performance, Class A2 external flame retardant breather membrane
Fire protection in the design and construction of buildings is paramount. That’s why we’ve used our 40 year industry experience to meticulously develop a new fire rated wall membrane, exceeding Building Regulations Part B requirements.
Protect FrameSafe FR is independently fire tested and achieves Class A2 reaction to fire, both free hanging and as part of a system with sealing tape.
Providing up to six months’ UV exposure to suit all building heights, it’s time to choose the hidden protector you can trust
*For technical fixing details, fire classification test reports and substrate information for Protect FrameSafe FR, contact us on +44 (0)161 905 5700 or e-mail info@glidevaleprotect.com www.glidevaleprotect.com/framesafe
Architects and urbanist studio
TateHindle has completed work on the new six-storey Salvation Army UK and Ireland HQ in Denmark Hill, London using concrete, mass timber and panelised brick.
This project saw the successful delivery of an elegant, sustainable costeffective new home for the charity, fit for a modern workforce, reflecting the context of the adjacent Grade II listed William Booth College, providing approximately 66,660sq ft gross internal floor area and an improved landscape and public realm setting.
The new concrete, oak and panelised brick structure is organised around a central light atrium, housing a public café, flexible workspace, informal meeting and breakout spaces, and a roof terrace providing panoramic views of the city. The external façade and
massing reflect the training college’s brown brick, stone dressings and varied level buttresses – putting the new campus directly in conversation with the historic William Booth college. In keeping with Sir Giles GilbertScott’s original design, the new façade is articulated as a series of bays dominated by robust brickwork, broken up with brick piers to deliver a strong vertical emphasis. The projecting brick piers and recessed windows were incorporated to give a feel of a very solid brick façade when viewed from an oblique angle, whereas when viewed straight on, much more glazing is visible to ensure natural daylighting is maximised as appropriate to the orientation of the façade. The use of contemporary design features and materials, including high levels of glazing and GRC fins and panelling that acknowledge the stone detailing of the listed building, gives the building its own identity and a unique and contemporary feel.
The new headquarters will bring a modern way of working to the headquarters’ circa 450-strong workforce, with flexibility for future change built into the design. Functional efficiency, longevity, minimising waste, and material efficiency were key considerations in the design development. A concrete structure was decided upon to allow a 120year design life to be achieved. The façade has been optimised to ensure airtightness and a high level of insulation to minimise heat losses in winter and heat gains in summer. Deep window recesses and rooflight timber mullions minimise glare and overheating with the open atrium space also venting warm air via AOVs.
Unnecessary lining and panelling were omitted to expose the concrete frame, allowing its thermal mass to be harnessed. Additionally, a ribbed slab was engineered with a very shallow
depth (just 100mm at the top of the ribs) significantly reducing the total amount of concrete used in the frame, meaning a lighter building requiring smaller foundations.
Improved functional efficiency, using air source heat pumps on the roof to the latest environmental and energy efficiency standards, will significantly reduce the running costs of the building. The roof level will accommodate sustainable technologies, including around 100 horizontal PV panels in horizontal arrays elevated to 15/30 degrees and orientated to provide a suitable yield. No gas is used to minimise reliance on fossil fuels. Sustainable drainage, in the form of ‘blue roofs’, cover the majority of the building to reduce the impact of rainwater run-off and the risk of pollution to watercourses.
A Site Waste Management Plan was in place throughout the build to minimise
construction waste, an important factor in the BREEAM Excellent rating which is targeted. In addition, 50% GGBS cement replacement is used in the concrete frame, using a waste product from the steel industry and improving the concrete colour as well as reducing embodied C02 in the frame. The final embodied carbon of the structure is 297kgC02/m2, including foundations. This is a saving of 20% compared to a standard concrete mix, and 30% compared to a typical office structure of steel and metal deck.
A simple palette of good quality materials was chosen to minimise future maintenance and refurbishment works and reflect the organisation’s desire to house its HQ in a building that prioritises its values before aesthetics. Glulam lining provides softening and warmth to the exposed concrete frame and structural support to the atrium rooflight. The deep glulam mullions
also diffuse the light in the atrium with a warm glow while minimising excess solar gain. Demolition waste from two smaller, low-quality buildings that previously stood on the site was reused in the build.
"The outer facade of the building features GRC and brick cladding, panelised offsite and designed to respond to the principles and proportions of the college, alternating with large areas of glazing to provide transparency and light.”
Andrew Tate, Director at TateHindle, said: “Working hand-in-hand with The Salvation Army to deliver their new UK headquarters building has been an incredibly rewarding process. Our collaboration seeks to embrace both the values and aspirations of the historic charity, and the contemporary
needs and requirements of their modern workforce.
“A return to their Denmark Hill campus has presented us with a wonderful opportunity to work within the illustrious context of the original Giles Gilbert-Scott listed building which remains the central focus of the training college, allowing us to establish clear connections in terms of scale,
4
proportion, and material. The new building has been designed to last for a hundred years or more and aims to symbolise the ongoing legacy of the organisation, as it looks into the future.”
Andrew Justice RIBA, Senior Property Project Manager, The Salvation Army UK and Ireland Territory, added: “The Salvation Army in the UK and Ireland will benefit greatly from
our new headquarters designed by our team of consultants led by TateHindle Architects. Our yearslong collaboration with TateHindle started with a detailed brief-building exercise. We were clear we wanted a building that was cost effective, met high environmental and accessibility standards and would provide a flexible headquarters for many years to come.
“The improvement in collaboration and communication in comparison to our previous HQ will lead to more efficient working for the Church and Charity, and relationships with both our adjacent William Booth College and the other institutions around us are already benefiting from the new location. We look forward to many years of successful working in the new building.”
For more information visit: www.tatehindle.co.uk 3
Images: 01-04. The new Salvation Army HQ uses offsite methods to provide a contemporary building in an historic setting.
Courtesy TateHindle/Jack Hobhouse
.05.2024
FOR THOSE LOOKING FOR SAFE, ENVIRONMENTALLY FRIENDLY AND COST-EFFECTIVE CONSTRUCTION SOLUTIONS, FOCUS ON FRAMING IS A MUST-ATTEND EVENT.
The conference and exhibition has an expanded and more interactive format with high-profile speakers focusing on topics including:
Cost-Effective Construction
New Building Regulations
Achieving Building Safety
Non-Combustible Construction
Sustainable Solutions
Circular by Design
Interact with the Industry and Gain Valuable Insights
With speakers from IStructE, CCPI, Trowers & Hamlins, Rider Levett Bucknall, SCI, ArcelorMittal, Quadrant Building Control, Hill Group, Fusion, Graitec, Remagin, Waterman Group, Reusefully, Knauf, Tata Steel, Design4Structures, KOPE, Moduliv, Intrastack, McCarthy Stone, Hadley Group and the Light Steel Frame Association –plus networking throughout the day, along with Q&A panel discussions.
IN PARTNERSHIP WITH:
TICKETS ARE £125 +VAT
Including access to the conference, pop-up exhibition, refreshments, lunch and speaker presentations post-event.
LIGHT STEEL FRAME ASSOCIATION
Members can book tickets for £95 +VAT – contact shannon.guerreiro@radar-communications.co.uk for your discount code!
19-20 March saw the sixth Modular Matters event take place at its new venue at the Coventry Building Society Arena and saw two days of serious discussion surrounding a sector in flux.
It is fair to say that the modular sector has experienced a torrid time over the last 18 months. This being after a sustained period of growth with exciting new entrants into what was increasingly being sold as a dynamic and fast-moving ‘new’ construction model. Many of these entrants portraying themselves as market change agents and proudly shouting about their ‘disruptor’ tactics.
However, money markets, investor expectations and economic and political landscapes change quickly, and the modular sector (especially the volumetric approach) has found itself faced with stark reminders that the world of construction is a tough place to operate. No doubt expecting some awkward questioning, Housing
Minister Lee Rowley MP was unable to make his keynote presentation on the present state of the MMC and housing market, disappointingly citing diary clashes but probably unlikely to want to be seen promulgating Government policies that he is unlikely ever to be able to deliver.
Public sector pressure
Day One was chaired by Cogent Consulting’s Darren Richards who used the Gartner Hype Cycle to illustrate the current state of the offsite market and where it is at presently – somewhere between the ‘trough of disillusionment’ and the ‘slope of enlightenment’. Certainly, there is an air of frustration surrounding MMC Category 1 3D modular and the residential sector and a disconnect between that segment’s failing businesses – hopefully the ‘plateau of productivity’ is not far away.
Edward Jezeph, Senior Manager at Homes England accepted the public sector mantle to explain the role
they have in facilitating the market to build more homes, challenge the way we build them and stimulate a market to scale up ‘whole house’ systems with a clear MMC strategy. Homes England came in for some criticism later in the day with Daniel Paterson, Director of Government Affairs at Make UK Modular, taking the opportunity to berate Homes England for its reticence to support its members (Make UK member and modular provider Lighthouse had announced its administration just before the event) and that more clarity and understanding is required to inspire confidence in what Homes England is trying to achieve. It must be remembered that Homes England has a duty to protect the taxpayer and be mindful of where its money is invested – especially after the demise of ilke Homes – rumoured to have lost approx. £60million of public money amidst a nationwide cost of living crisis. But as Daniel Paterson went on to say, we must highlight the wins and celebrate the innovative work that is being delivered and how offsite methods are modernising the construction industry to improve our homes, reduce carbon emissions and reduce energy bills. Volumetric modular can do all this expertly under the right circumstances.
Social Housing is a burgeoning market for modular providers and the Offsite Homes Alliance (OSHA) has been making huge strides in helping aggregate demand amongst housing associations (HA) and registered providers, to adopt offsite methods to improve living conditions for residents. Mike Ormesher, Project Director for OSHA and Helen Spencer, Executive Director Growth at Great Places Housing Group explained more about its groundbreaking organisation of over 20 HAs focusing on the ‘process’ rather than the ‘product’. They put into
BATHROOM & ENSUITE PODS OFFSITE MANUFACTURED TO METICULOUS STANDARDS WITH A CHOICE OF FINISHES AND FITTINGS
BATHROOM & ENSUITE PODS
Designed, engineered and manufactured by our multi awardwinning offsite experts.
For detailed and up to date information, to attend a factory tour or arrange a meeting please contact our team today.
T: +44 1743 290020
perspective how they are collaborating to boost growth with ambitions to create a clear pipeline of supply but did not shy away from the fact that many are nervous about MMC Category 1 and a “significantly difficult procurement landscape.”
Both James Pickard, Co-founder at architects Cartwright Pickard and Keith Blanshard, once of Portakabin (Yorkon) and now industry advisor at Buildoffsite spoke about one of the resounding success stories of offsite delivery – Murray Grove. A trailblazing, fully volumetric scheme that was the UK’s first fully modular apartment building for the Peabody Trust and completed back in 1999. However, the key takeaway point apart from the building’s iconic offsite status, was that in 25 years since its delivery, the overall impression is that not much is fundamentally different in the offsite market. It is still not as mature as it should be.
One of the new recent ‘disruptor’ entrants to the volumetric modular sector has been TopHat. Fenella Lowden, its Client Solutions Lead presented a case study on its proofof-concept Kitchener Barracks project and how the 96 apartments saw 240 fitted modules deployed in 35 working days. With the addition of solar panels – the SolShare element – it is driving down carbon emissions and energy bills. Questions of carbon are now everyday concerns in construction and Richard Hawkins, Technical Innovation Manager at SO Modular, spoke of its vision of ‘automating environmentalism’ with its range of open and closed panels, trusses, cassettes and fully volumetric units using ostensibly Welsh timber – all
augmented with natural insulation including sheep’s wool and wood fibre.
Influencing a generation
Day One’s afternoon session was given over to high-rise volumetric modular and the successful adoption in the build to rent (BTR) and private rented sector (PRS) markets. Brendan Geraghty, Chief Executive Officer of the UK Apartment Association (UKAA) – that 24 hours later rebranded as the Association for Rental Living (ARL) – talked at length about the opportunities available for offsite providers in this space with similar objectives of optimisation and standardisation of layouts, speed of construction and cost certainty.
A keynote presentation from one of the offsite and construction sectors most influential characters took place in the afternoon, with John Fleming, Founder and Chairman of Vision going through the long list of projects that Vison and Tide Construction have been involved. “Anything is achievable with modular,” said John when explaining its huge track record including the world’s tallest modular building – 101 George Street, London –and the ongoing work at the 32-storey The Castle, Ealing. Providing a positive lift to the audience, his advice to all when dealing with clients was simply: “don't give it to them cheaper, give it to them better.”
With presentations from Stuart Marshall, Head of UK & Global Sales at Elements Europe – who spoke at the first event in 2016 – highlighting a wider sense of ESG concerns and fire safety now driving investor decisions more than in previous years and Monika Wandzik, Head of Architecture and Planning, Stelling Properties,
finished the day discussing the many benefits and client appeal of achieving 80% factory completion of its modules.
Although Day One contained some inspirational messaging via John Fleming and the Vision/Tide success story, throughout the day it was impossible to ignore that the MMC Category 1 3D volumetric sector –at least in the residential space – is under pressure and not helped by the general UK construction slow down. The need for continuity of pipeline, better planning processes and clearer definitions and standardisation of systems, will alleviate concerns that have entered the offsite equation from the client side particularly. Whilst high-profile business failures have cast a shadow over the volumetric homes industry, the BTR and PRS markets are fertile ground, and this is where greater volumes of projects are materialising.
Healthcare & Education
Day Two was chaired by Richard Hipkiss, Development Director at the Modular and Portable Building Association (MPBA) and struck a different note to the first day with several successful healthcare and education projects reflecting the massive change that modular methods have had on critical parts of the public sector estate.
As an executive agency of the Cabinet Office and one of the biggest public procurement organisations in Europe, Crown Commercial Services (CCS) play a pivotal role in promoting offsite manufacture. Both Kumar Kairamkonda, Category Lead and Tony Griffiths, Commercial Agreements Manager at CCS gave plenty of insight into how clients are using its framework agreements, with some interesting trends picked out that are driving offsite and some roadblocks to its progress. A gradual rise of projects using MMC in housing has seen an increase of 9% of newbuilds using MMC in 2017 rising to 16% in 2023 with a spike in demand of temporary requirements.
Problems persist in volume uncertainty, lack of understanding of offsite and manufacturers unable to deliver major projects, with fragmented and lack of data always a hinderance. But as with Homes England, public
authorities face unique challenges as well as the general issues surrounding affordability, sustainability and efficiency in construction circles.
Managing risk is at the heart of every construction project and William Chung, Managing Associate at Mishcon de Reya provided a financial and investor-orientated presentation on mitigating risk and understanding funder concerns — institutional investors (e.g. pension funds, insurance companies) are inherently risk averse and despite undoubted benefits, MMC is perceived as more risky than traditional construction: “Derisking funders concerns and will help persuade them of MMC's bankability,” said William
Also flagged up – and John Fleming had mentioned this the previous day – was ensuring modules stored offsite are kept in good condition. Quality control and deterioration of modules at a closed factory or mothballed construction site is a worry – these ‘stranded assets’ for unrealised projects cause huge worry and these costs: “should be clearly marked and reclaimable in an insolvency scenario.”
Both Anne Daw, Head of MMC Delivery at HLM Architects and Ollie Green, Product Manager for KOPE discussed at length the value of collaboration, kit of parts design and using the latest digital tools and technology to capture the essence of offsite – some of this via a ‘MMC Demand Equation’. Anne Daw and HLM are part of a wider industry group working on a one-year research project, focusing on MMC Categories 2 and 5 that will research barriers to the use of MMC and how these can be mitigated with a view to developing a “digital kit of parts” for low-rise housing and encourage “design consolidation and DfMA to improve efficiency and quality of new homes.”
Daniel Leech, Chief Executive Officer at Design4Structures spoke about the current challenges of offsite – basically: standardisation, ‘lack of fluidity’, industrialisation, lack of government strategy, funding and pipeline and how these need to be overcome, highlighting that the Building Safety Act offers the modular sector many opportunities to prove what it could do.
For a slightly different angle and a call to ‘offsite and carbon arms’, James Morton, Structural Engineer at Ramboll spoke of his work on an ‘upfront’ study of carbon with pivotal offsite materials – timber, steel and precast concrete. Driven by the lack of evidence or comparison between offsite and typical construction techniques, he is collecting data and seeking to employ more circular economy principles to better understand the levels of embodied carbon, which can be improved by something as simple as re-use of modules at the end of life or even fewer module typologies.
The final afternoon centred mostly around case studies from the education and healthcare sectors.
Chris Leese, Technical Director at TG Escapes, spoke of the biophilic design of its modular timber buildings and how visible timber goes a long way to reducing stress, pupil absence and how natural materials boost mental health – should this concept ideally be a part of all building briefs?
Stuart Norris, Technical Product Manager at Portakabin, Martin Harvey, Head of Design at McAvoy and Narciso Simioni, Architectural Lead at MTX, all illustrated the highly successful utilisation of modular technology to deliver high quality education and healthcare buildings that are speedily delivered, flexible and with futureproofing a central element – modifiable where layouts can be changed or connected to other uses. As Narciso Simioni said: “we need to be change ready as change is not an if – it’s a when.”
Paul Ruddick, Chairman and Founder of Reds 10 wound up the event with a quick case study of its groundbreaking
Imjin Barracks Single Living Accommodation project and its use of cutting-edge energy management technology to decarbonising its buildings, but also how they are looking to further ‘industrialise’ its process by factory-fitting brick slips to its modules.
The two full days didn’t shy away from the problems the modular sector is dealing with, but it’s not all gloom and doom, modular technology remains at the forefront of innovation, capable of redefining how we think about construction – especially away from the low-rise residential space. It’s easy to get sucked into the negative aspects of recent business failures (Beattie Passive sadly filed for administration shortly after the event). High rise modular, education and healthcare are vibrant sectors creating sustainable spaces that support the all-important carbon goals and circular economy. What was clear over the presentations and mid-session discussions is that there is a pervading idea that ‘perceived risk is higher than the actual risk’. Nobody wants too much Government intervention but the enforcement of a degree of standardisation – at least on public sector projects – could be a route to inspire the confidence clients and investors are seeking.
For more information and to keep up to date with plans for Modular Matters 2025 visit: www.modularmatters.co.uk
Images:
01. John Fleming, Founder and Chairman, Vision 02. Fenella Lowden, Client Solutions Lead, TopHat 03. 30+ speakers and 200+ delegates took part in the two day conference and exhibition
Offsite specialist MTX is creating a six-bed discharge lounge and associated support accommodation ward at the Queen Elizabeth Hospital (QEH), King’s Lynn and builds on the successful delivery of a new Endoscopy building in 2023.
The facility is being constructed as a stand-alone building to enable it to be reused when the planned new hospital is built. Bespoke ground floor and first floor corridors link back to the main building and hospital ‘street’, and construction includes a new bed lift for easy patient access to the ground floor discharge area. Internal fit out of the new building includes HTM compliant air handling systems along with power, medical gases and other bedside services.
The two-storey build is in a courtyard at the rear of the hospital site. The new location will allow easier access for patients and staff and will take high volumes of site traffic away from the busy hospital ‘front door’ and Emergency Department areas of the site. It will also enhance privacy for patients being discharged. The new discharge lounge was commissioned to support the on-going RAAC (reinforced autoclaved aerated concrete) failsafe programme of works within the QEH site. The existing discharge lounge sits within a single storey area that will be demolished as part of the RAAC eradication works.
The contract was awarded by the Queen Elizabeth Hospital King's Lynn NHS Foundation Trust, and MTX is working with the Trust’s multi-disciplinary design and construction consultancy partner exi
which is managing the RAAC failsafe programme at QEH. MTX and offsite methodology was chosen following the company’s successful delivery of the new Endoscopy building on the QEH site in 2023. MTX had demonstrated an understanding of the complexity and specific site issues associated with QEH and building within an active blue light area.
MTX Managing Director David Hartley explained: “The modular building has been fabricated offsite whilst complex enabling works and site preparation was undertaken prior to the units arriving on site. Re-routing of existing services and the constraints of a tight courtyard site surrounded by live hospital wards and the Macmillan centre meant craning in modules would reduce overall site/construction time and fit within the tight RAAC programme, whilst minimising disruption to the existing site operation and services.
“Using MMC principles enables us to maximise offsite manufacturing opportunities and the use of precisely engineered structural modules to build faster, safer, greener and more cost effectively. Successful completion of other projects with the Trust laid the foundations for the award of this contract, to continue improving patient facilities at the Queen Elizabeth Hospital.”
The £12.5million endoscopy unit at QEH delivered in 2023 employed multi-level BIM tools and Construction Playbook methodologies to deliver a high-quality facility to time and budget, achieving 72% pre-manufactured value, 49% increased patient throughput and an excellent satisfaction score from the QEH. Construction of the new unit also incorporated ground-breaking carbon
and energy efficiency reduction plans contributing to the Trust’s net zero policy targets, with the collaborative early contractor involvement (ECI) relationship and the use of digital technology and simulations resulting in savings for the whole life of the facility.
The Trust identified the need for a new two-storey, 2,600sq m development to modernise obsolete facilities and enable endoscope procedures to take place in one facility to meet acute clinical demand. The project delivered against its goals achieving an accelerated return on investment by 14 months, 41% less CO2 compared to a traditional construction solution, an MMC platform approach that achieved 72% PMV, 26% reduction in carbon emissions for the concrete floors when compared to previous installations at the Trust, zero defects and zero accidents.
Units digitally designed and optimised in the factory reduced risk whilst delivering advanced pre-assembled factory standards and high levels of quality assurance. Cost predictability was a key factor in pre-construction with Revit modelling allowing accurate RIBA stage 4 costing, and clash detection design workshops reducing on-site conflict.
Cost saving achieved included a 15% offsite saving vs traditional building, a 65% reduction in on-site labour and utilisation of local SME resources for assembly and completion, under MTX management. Initiatives to increase the speed of delivery included weekend working, extended factory hours that achieved the manufacture of ten modules per day during winter, the use of recycled Legato blocks to accelerate groundworks and save carbon and direct radio communication between the construction team and the A&E Dept that optimised crane usage to mitigate delays without disrupting blue-light movements.
For more information visit: www.mtxcontracts.co.uk
Images: 01. Offsite methods have been key to transforming patient services at QEH with the Endoscopy building hugely successful
Offering unrivalled access to leading industry pioneers, dynamic factory tours, thought provoking roundtable discussions and CPD accredited masterclasses – a collective of industry bodies are collaborating to deliver Offsite Construction Week.
Taking place from 16–20 September 2024, Offsite Construction Week will revolve around three major industry events – Offsite Expo, the Offsite Summit and Offsite Awards, with a wide range of parallel activities taking place in the UK and overseas via a coordinated programme of activity.
Offsite Construction Week –
The Main Event
As the first and foremost event of its kind, OFFSITE EXPO was well ahead of the construction curve. Launched in 2019, it has its imitators but now in its sixth year – it is acknowledged as the catalyst for driving transformational change. Bringing together the industry’s big hitters from across the UK and beyond in one easy to reach central UK location, OFFSITE EXPO 2024 will be held at the Coventry Building Society Arena from 17–18 September.
In an era dominated by remote and digital experiences, live events offer unparalleled opportunities that transcend the virtual realm. This highly anticipated showcase will feature renowned speakers and award-winning industry figures from across the globe who will shed light
on the ideas and innovations that are transforming the construction industry. The custom-built features provide an immersive experience, allowing construction professionals to get up close and examine the detailing. Leading the debate – the Masterclass Theatre will feature CPD Accredited presentations and panel debates from over 100 industry experts focusing on the technologies that redefine the way buildings are designed and constructed.
For more information or to register FOC, go to: www.offsite-expo.co.uk
Offsite Construction Week –First Factory Tours Announced Organisers of this year’s event have taken it up another level and not only will Offsite Expo have a new international focus – it will be ‘slap bang’ in the middle of Offsite Construction Week!
With further major announcements to follow, organisers have revealed the first three factory tours to take place as part of the weeklong event. Innovaré Offsite, TopHat, and British Offsite will be opening their factory doors to demonstrate how advanced
digital engineering combined with offsite manufacturing technology can enhance quality, building performance and construction programmes. The events will include technology presentations, a guided tour of the manufacturing facilities, an informative Q&A and networking opportunities.
Innovaré Offsite has been delivering low-carbon, high-performance prefabricated education, residential and healthcare buildings for over ten years. With a specialist manufacturing facility in Coventry, on 16 September 2024, Innovaré will demonstrate how streamlining production processes can deliver greater speed and highly sustainable structures.
TopHat creates beautiful and sustainable communities, delivering design-led homes fit for twenty-first century living. Based in Derbyshire, on 19 September 2024 the TopHat factory tour will showcase their state-of-the-art manufacturing facility and a unique technology-enabled approach.
Bringing extra speed, adaptability and reliability with next generation light steel framing systems and infill panels, on 20 September 2024, British Offsite’s Horizon factory located in Braintree, Essex – will open its doors. This highly automated facility was constructed in 2023, with more than £40million invested in its state-ofthe-art machinery and just-in-time solutions, quadrupling British Offsite’s production capacity to 4,000 homes a year.
To keep up to date with developments visit: www.offsiteconstructionweek.co.uk
OFFSITE CONSTRUCTION WEEK shines a spotlight on the transformative digital, material and manufacturing innovations that are advancing the design and application of offsite construction processes.
Become a Host and Run Your Own Event
To give you inspiration, events can include: ... just as long as you are talking about offsite technology!
FACTORY TOURS
ROUNDTABLE EVENTS
SITE STUDY TOURS BREAKFAST CLUBS DRINKS RECEPTIONS
WEBINARS & PODCASTS
www.offsiteconstructionweek.co.uk
You could be forgiven for thinking the offsite industry is not in good shape, but positive news does not seem to travel fast or make ‘good’ headlines. But as Jackie Maginnis, Chief Executive of the Modular and Portable Building Association (MPBA) tells us, there are some phenomenal success stories to be told.
It was with great interest that I read an article featured on the NBS website by David Bain, Research Manager at NBS and Allan Wilen, Economics Director at Glenigan. The picture the research paints is far removed from the negative headlines and is more reflective of what our members are telling us.
According to Glenigan, there has been a gradual rise in the proportion of projects utilising modern methods of construction (MMC). The 2023 NBS Digital Construction Survey published last November found that 57% of respondents had been part of a project that involved an element of offsite construction. Reflecting the growth in adoption of offsite evident in the Glenigan data, this is an increase from 50% in the previous 2021 survey. For consultants such as architects and engineers, the figure was 58% and it was 63% for contractors.
MMC is a broad category, and our interest obviously lies within the volumetric modular sector.
And guess what – good news. NBS research findings concluded that modular construction was utilised on projects by 34% of survey respondents. These include projects like apartment blocks or schools that consist of substructures manufactured as modules.
Encouraging signs for further growth
In addition, economic, regulatory and environmental performance issues are set to encourage further growth in the use of offsite construction over the medium term. The shortages of skilled labour are likely to intensify as the construction industry emerges from the current market downturn. The Building Safety Act is also set to change how projects are delivered, requiring more detailed
preconstruction design and limiting the scope for on-site design changes. This plays to the strengths of volumetric modular technology and is predicted to increase the opportunities within the sector. Clients and designers now need to improve their buildings’ environmental performance are similarly likely to favour the greater use of factory manufactured systems.
Digitally constructed and virtually tested
Volumetric modular buildings are less susceptible to poorly specified products as time can be taken upfront to validate the correct specification of materials. Designs are digitally constructed and virtually tested before they move onto the manufacturing phase. This process eliminates waste and achieves highly accurate and airtight building envelopes designed and built to higher sustainability
Ask the experts...
We develop and improve offsite:
• Business strategies
• Product & service portfolios
• Manufacturing operations
• Supply-chain integration
• Business processes
• Management systems
• Certification processes
01743 290010
info@cogent-consulting.co.uk
www.cogent-consulting.co.uk
standards. This allows clients to have confidence in the quality and performance that they can expect from their new building. Unlike factory manufactured buildings, there is significant evidence that traditional construction methods do not produce structures that perform as well as design expectations and there is a void between anticipated and actual in-use performance.
PMV a driving force in specification
Whilst the focus is on how offsite can help solve the housing crisis, as many of our members are aware, volumetric modular construction has made the greatest inroads in other sectors. Pre-Manufactured Value (PMV) is another driving force in the specification of volumetric technology in public projects – particularly in the healthcare and education sectors. PMV is a core metric for measuring the level of MMC in a project and is central to
the UK government’s procurement programmes. To secure a contract, suppliers are required to show that pre-manufacturing will account for at least 70% of their construction cost, which again plays to the strength of a volumetric modular approach.
The MMC sector for Category 1 (volumetric) and Category 2 (panelised systems) is an interesting place to be. The levels of investment and innovation are astounding and as with any transformative technology, there will be hurdles to overcome. Our industry unlike others, has nothing to fear from the legislation surrounding the Building Safety Act and the road to achieve net zero targets in commercial buildings is a well mapped route.
The MPBA and our members firmly believe that the benefits of manufactured buildings begin in the factory, continue to the construction
site and last through the lifetime of the building. As I scroll through the industry news section on the MPBA website, there are so many success stories, ground-breaking innovations and forward-thinking collaborations, that create a far more realistic and positive perspective on the industry we work in.
For more information visit: www.mpba.biz/posts or access the NBS data at: https://bit.ly/3Q30dSX
Images:
01. Jackie Maginnis, Chief Executive, MPBA
02. Volumetric units are created in a clean factory environment. Courtesy Portakabin Group
03. George Eliot Hospital. Courtesy Wernick Group
04. Douay Martyrs School. Courtesy Premier Modular
MPBA
The MPBA plays a key role in supporting all sections of the industry. Leading best practice principles, the association is represented on many committees for the benefit of members. Most importantly, the MPBA ensure evolving government policies and decisions are not made on behalf of the construction industry without due consideration for the impact they may have on the volumetric modular sector.
Questions surrounding the levels of embodied carbon in construction are not easily answered but new data from Timber Development UK (TDUK) provides new levels of understanding on specifying timber products.
Earlier in the year leading construction industry and built environment experts from 11 organisations demanded policy action in – what should be – an election year with embodied carbon a key concern. Big hitting organisations including the UK Green Building Council (UKGBC), The Institution of Structural Engineers, Chartered Institute of Building, UK Architects Declare, RIBA and RICS among others, joined forces to send a clear message to UK political party leaders about the need for regulation of embodied carbon emissions in construction.
Identifying and better understanding the levels of embodied and operational carbon that our built environment and construction products contain, is crucial to hitting the 2050 net zero target. When it comes to timber – the leading mainstream low carbon construction
material – a new investigation of embodied carbon data for more than 95% of timber consumed in UK has just been released by TDUK. And all completely free for all to digest.
Quality carbon data
TDUK has released average carbon data for the 10 major timber product categories. This data will support architects, engineers, and other specifiers to make accurate assessments of the carbon impacts of their material choices as early in the design process as possible – when they have the greatest ability to influence them.
“Consistent and up-to-date embodied carbon data is key to making accurate design decisions,” said Michael Polack, Technical Manager for B&K Hybrid Structures. “Particularly as the embodied carbon of timber
continues to further improve. At B&K Hybrid Solutions, we fully support the development of TDUK’s EPD database and weighted averages for timber products, which are particularly valuable for supporting design teams at early design stages.”
TDUK’s new independently verified ‘Embodied Carbon Data for Timber Products’ calculates weighted average A1-A4 embodied carbon data for common timber products such as softwood, engineered timber, and panel products, including and excluding sequestered carbon. More than 80 EPDs were reviewed in this comprehensive new paper. A1-A4 data is provided for 10 major timber products which means the EPD Database can be used to calculate the carbon impact of more than 95% of timber consumed in the UK. The A1-A3 data draws only from EPDs for
Due to popular demand, we are increasing capacity by 25% – more networking for you!
Enhanced marketing campaign – a 15% increase in the marketing budget –greater profile for you!
Videographer –more post-event profile for you!
The offsite timber construction industry has undergone notable evolution, marked by significant progress and a commitment to a more productive and innovative future.
The Structural Timber Awards serve as a prominent platform to showcase excellence within this dynamic sector, providing an opportunity to position your brand alongside influencers and pioneers.
Champagne on every table – now that’s the way to celebrate our 10th anniversary!
Live music and increased postevent entertainment in the bar area –fun until midnight!
Aligning your business with the Structural Timber Awards demonstrates your commitment to fostering progression, innovation, and talent in timber design, engineering, and construction. Sponsorship provides a unique opportunity to gain valuable exposure through our extensive event PR coverage, positioning you as a champion of sustainable construction and innovation to a wide audience.
2
products available in the UK, with the data weighted based on country of origin. With the addition of A4 data on transport to the UK, calculated using TDUK’s access to imports information to consider our diverse supply chain – this is the most accurate data for timber products available for whole life cycle assessments in the UK.
With one of TDUK’s core missions being to help create a low-carbon future, this data – and a paper on the methodology (which has been independently verified by Construction LCA. Charlie Law, Sustainability Director for TDUK, said: “If we are to achieve national and international targets to reach net zero carbon emissions by 2050, we need to measure, understand, and significantly reduce the embodied carbon within the buildings and infrastructure we construct.
3
“Environmental Product Declarations (EPDs) are key for specifiers to design low-carbon assets, helping them accurately assess the impact of their designs and material selections, but historically, limited data has been available. Only in the past few years has this begun to change. But with a continual push for more EPDs for products in construction, more data is becoming available every day – the results of major efforts made by timber suppliers. Our EPD Database capitalises on all of this data by drawing on the available independently verified EPDs for timber products to calculate weighted average A1-A4 embodied carbon data.
“All of the data, and the methodology used to create these averages, is completely independently verified – and freely available for all to download and use for their own tools and resources. We are proud to have
undertaken a particularly rigorous process, and release both the data and methodology for free. This means anyone working within the built environment can benefit from this research, with complete confidence in its independence. Robust data is essential for reducing the carbon impact of construction, allowing specifiers to make informed decisions. We will be updating these figures every year as more data becomes available.”
The paper which accompanies the EPD Database figures has more information on the methodology used, data confidence levels, and includes a PDF dataset with links to EPDs, product densities, and a verification report by Jane Anderson at Construction LCA, confirming compliance with CEN/TR 15941:2010 standards.
“Having already compared these figures to some of our previous embodied carbon counts we can see a marked improvement,” said Kelly Harrison, Director, Whitby Wood. “It’s invaluable to have actual datapoints and verified, weighted average EPD information at early design stages to ensure that we make the right decisions.”
“With a rightly increasing scrutiny within the industry of the climate impacts of construction, this data contribution enables design teams to move beyond ‘rules-of-thumb’ and ‘gut feelings’ to having a data-driven dialogue.” Seb Laan Lomas, Associate and Passivhaus designer, Architype
The new, free to use timber EPD database fulfils a key commitment made by TDUK within the UK Government’s recent Timber in Construction Roadmap. You can download the 2024 Embodied Carbon Data for Timber Products at: www.timberdevelopment.co.uk
For more information visit: www.timberdevelopment.uk
Images:
01. The new embodied carbon data for timber products is an invaluable resource 02-03. The use of timber is central to a more sustainable and low carbon built environment. Courtesy B&K Structures/ Sodra
Experience Knauf’s cutting-edge solutions at MMC Ireland’s National Conference.
Knauf’s MMC solutions cut construction time, reduce costs, and shrink carbon footprints whilst offering a certified performance using revolutionary finishes.
Visit the Knauf stand and find out how we’re transforming the face of modern construction.
Rebecca Goldsmith, Product Manager at MEDITE SMARTPLY, explains why OSB offers many advantages for offsite construction and timber frame systems, which is key to providing high-quality, low-carbon housing rapidly and efficiently.
1 2 3
From structural strength to adaptability and ease of installation, timber frame offers several advantages as an offsite construction method and has a proven track record of providing superior energy efficiency and low embodied carbon emissions. It should also be the first choice for specifiers who prioritise energy efficiency, sustainability and cost.
The use of timber in the construction of future energy efficient homes is set to play a key role in decarbonising construction and has received a boost with the UK government having green lit The Timber in Construction Roadmap. It provides insight into structural timber and advocates the increased use of timber products in the construction of homes. As part of this, timber is an ideal material for building homes to achieve the stringent energy efficiency requirements of Building Regulations Part L and the Future Homes Standard in 2025.
Timber frame manufacturers that can provide high-performance, airtight envelope solutions will be wellpositioned to meet these changing regulations and capitalise on the move towards low-energy construction. However, when it comes to offsite construction, it is crucial to select
materials for structural timber systems that will deliver the thermally efficient building envelopes that are required.
Pushing the envelope
In order to meet the evolving standards, there is an innovative solution to simplify the path to airtight building envelopes. The increasing demand for double sheathed timber frames in both structural applications and the development of offsite closed panels, led to innovation for producing an airtight OSB/3 panel with airtightness engineered into the panel substrate. The panel can be used as the airtight layer on the warm side of the insulation in timber frame construction systems, helping to create an airtight building envelope.
Each panel features alternating layers of wood strands coated with a high-quality formaldehyde-free resin and wax binder system to deliver outstanding levels of airtightness. A specialist coating is then applied to ensure vapour resistance and provide a premium performance OSB solution for super-insulated and passive buildings and enabling the elimination of a traditional additional vapour control membrane from the construction.
By seamlessly integrating air and vapour barriers into high-performance OSB panels, this streamlines the installation process, minimising the risk of air leakage that often plagues traditional timber frame structures. This cutting-edge solution not only simplifies construction but also ensures a certified, proven approach to creating airtight building envelopes that will pave the way for low-carbon, energy-efficient homes of the future. For timber frame contractors, the use of OSB that features integrated vapour control and air barrier properties is a major step forward. These innovative OSB solutions will enable them to consistently achieve the stringent airtightness levels needed and create airtight, high performance building envelopes that easily surpass the new Future Homes Standard.
For more information visit:
www.mdfosb.com/smartply-osb
Images:
01. Rebecca Goldsmith, Product Manager, MEDITE SMARTPLY
02-03. SMARTPLY AIRTIGHT boosts energy efficiency results in newbuild homes
The light steel frame industry can play a vital environmental role by ensuring resources remain in use as long as possible. Ben Towe, Chair of the LSFA, stresses why we need to move away from linear construction principles and embrace circularity.
1
You may ask what sets steel apart from other building materials in the circulatory debate? Research carried out by the Light Steel Frame Association’s (LSFA) technical partner, the Steel Construction Institute (SCI) estimates that there are around 100 million tonnes of steel in buildings and infrastructure in the UK. This ‘stock' of steel is an important and valuable material asset that means we are largely self-sufficient in steel and can virtually produce all we need through recycling or reusing our latent stock to satisfy future market demand.
Steel has a unique characteristic as it can be reused and recycled repeatedly without losing its qualities as a building material. All steel used in today's construction projects has some recycled content. The constructional steelwork used in the UK contains an average of 60% recycled content. The recovery infrastructure for steel recycling is highly developed and extremely efficient and has been in place for decades. Current recovery rates from demolition sites in the UK are 99% for structural steelwork and 96% for all steel construction products – figures that far exceed those for any other construction material.
Steel is central to transitioning away from a linear approach – take, make, dispose, to circular construction –
2
reduce, reuse, recycle, repeat and offers significant opportunities to mitigate the adverse impact on our environment. We need to adopt innovative approaches that design out waste, use resources more efficiently and keep materials and assets in use for as long as possible to retain their value by re-thinking the way that we design our homes and buildings.
For circular economy principles to successfully work in the built environment, business models need to evolve across the entire value chain. Design optimisation is crucial in a circular construction approach and a lot of thinking has to be done up front. Once the architectural priority was form and function but now there are a raft of considerations coming to the fore such as design for longevity, adaptability and the offsite mantra of Design for Manufacture and Assembly (DfMA). Moreover, it is imperative to plan for a building's ‘end' right at the beginning of the design stage to enhance the sustainability value chain through Design for Disassembly (DfD), Design for Reuse (DfR) and recoverability protocols.
But where DfD focuses on the eventual recycling of materials such as steel, DfR plans for the use of specific building components in similar
projects during the design stage and requires comprehensive data capture and recording. The Design for Reuse model specifically pre-empts future use, so designs do not require adapting. Capturing and recording performance, testing results, loading capabilities and even dimensions are vital to ensure any pre-existing systems fit within the design specifications and requirements of a new build in the future.
Buildings should not only be inherently safe but should also be constructed to stand the test of time. In his recent challenging book ‘Humanise'Thomas Heatherwick states the most sustainable building is one that is designed to last a thousand years. Many light steel frame buildings are BOPAS certified for a design life of 60 years. But according to the SCI, design life predictions for light steel in a ‘warm frame' environment is more than 250 years. Robust, reusable, recyclable and adaptable, steel has excellent circular construction credentials. As a material it is strong and durable, as a structural framing system it is lightweight and cost efficient. Steel’s material properties make it the ultimate sustainable construction solution, enhancing both the safety and sustainability credentials of light steel buildings.
For more information and to download ‘Light Steel & Circular Construction’ visit: www.lsf-association.co.uk
Images:
01. Ben Towe, Chair, LSFA
02. Steel has a unique characteristic as it can be reused and recycled repeatedly without losing its qualities as a building material
Offsite M&E Fabrications
Load bearing and none-load bearing LGSF frames, for panelised, or volumetric modular build. Detailed utilising cold rolled LGSF, Hybrid LGSF and hot rolled steel or purely hot rolled fabricated steel components.
From design to installation, LGSF production have proven capacity for the dependable supply of frames for sizes of projects.
• Extensive manufacturing capacity
Over 100,000 ft² of manufacturing facilities
• Ongoing programme of investment & development
• In-house detailing services
• Engineering services
• Rigorous quality control BS EN 1090 Ex Class 2 & 3, ISO 9001
• Proven capability in the supply of high volume ‘Just In Time’ orders
• Expert team providing technical advice and support
LIGHT GAUGE STEEL FRAMING
Unit 3, The Gateway, Dunslow Road, Eastfield, Scarborough, YO11 3UT 01944 710279
sales@lgsf.co.uk
Andrew Way, Associate Director at the Steel Construction Institute (SCI) explores how design competency within the offsite sector is being confirmed and supported.
The competency of those working in the construction industry has always been an important aspect which is crucial to the success of projects. Following the introduction of the Building Safety Act in 2022 and the secondary legislation which came into force on 1 October 2023, ‘competency’ has not been enshrined in construction legislation in quite the same way as it is now.
Publication of several new regulations in 2023 has meant that significant changes to the building control regime for all buildings in England have come into force. One particular aspect is the new duty holder and competency regime which has been introduced by the Building Regulations etc. (Amendment) (England) Regulations 2023.
The competency requirements apply to all types of building, not just works for higher-risk buildings, and it applies to those procuring building work, carrying out building work, or those carrying out design in relation to building work. The legislation sets out the general competency requirements as: Any person carrying out any building work or any design work must have the skills, knowledge, experience and behaviours necessary. In the case of a company, it must have the organisational capability to carry out:
• the building work in accordance with all relevant requirements
• the design work so that the building work to which the design relates, if built, would be in accordance with all relevant requirements.
Further competency requirements are specified for particular roles. There are numerous sources of further information on the implications of the Building Safety Act and related legislation including The latest Building Safety Bulletin from the LSFA and the related LSFA roundtable debate.
Setting the competency requirements in legislation is one thing, but assessing and establishing the competency of individuals or organisations is quite another. As indicated by the wording in the legislation, competency is about so much more than just what education and training an individual has received, although this is vitally important. Aspects such as appropriate skills, experience, behaviours, and attitude are also essential.
It is with this in mind that the SCI is supporting the offsite construction sector through the provision of technical information, design guidance and product certification.
There is an increasing need for the construction sector to adopt modern methods of construction (MMC) in order to address the UK housing shortage, as it provides an obvious way to reduce construction time while improving quality. However, stakeholders in the construction sector are concerned about the risks associated with using third-party products and are reluctant to adopt innovative construction methods.
The Buildoffsite Property Assurance Scheme (BOPAS) was developed to address these concerns and is based upon the assessment of the construction system and manufacturer’s processes. An aim of focusing on these aspects, rather than a specific product, was to make the scheme able to cope with product developments and evolutions. However, not evaluating the product itself means there is no guarantee that the product will conform to expectations and will perform as expected. A stated aim of BOPAS is to provide assurance to mortgage lenders, developers, and buyers.
To guarantee product performance requires product certification, with clear pass/fail performance criteria and factory production control. SCI has developed SCI Product Certification[v] according to ISO/ IEC 17065:2012 and a UKAS accredited certification body No. 10414. This ISO standard requires evaluation of a product’s performance against a publicly available and welldefined set of criteria. A combination of product and process certification will provide the ‘gold standard’ for any manufacturer.
In a significant development, SCI recently extended its UKAS accreditation scope to include prefabricated steel panels (MMC category 2), complementing its existing coverage of volumetric modular units (MMC category 1). Prefabricated panels are typically used in walls, roofs and ceilings and generally consist of light gauge steel sections. The panels may include other components such as hot-rolled steel sections, boards, insulation, or
2
sheathing, all prefabricated in the manufacturing facility.
In addition to accredited panel and modular schemes, SCI operates a fully detailed scheme (not accredited by UKAS) for the design of complete buildings constructed using modular units or panels. In addition to SCI Product Certification, design competency in the offsite sector is maintained and enhanced by the provision of information to designers through SCI’s online portal and members advisory service which can provide designers with the latest information on design issues and procedures, particularly as we move towards the second generation of Eurocode design standards.
3
New design standards, changes to regulations and advancements in the understanding of how construction systems behave (e.g. structurally or in terms of fire performance) all mean that the definition of what constitutes competency is everchanging. Designers and other construction professionals must frequently ensure their skills, knowledge and training remain current.
For more information visit: www.steel-sci.com www.lsf-association.co.uk
Images:
Light steel frame offsite panels.
Intrastack
Modular construction. Courtesy Vision Modular Systems 03. Light steel panelised construction. Courtesy Etex Remagin
Ibstock Plc is embarking on the next stage of its major investment programme at its Nostell factory in West Yorkshire. Once fully operational, Ibstock will have the UK’s first fully automated brick slip manufacturing centre producing around 50 million brick slips per year.
As the leading brick manufacturer in the UK and with more than 200 years of industry knowledge and expertise, the Group are increasing their presence in the fast-growing markets for brick slips, façades, and walling system solutions, as they continue work towards maximising the full potential of more modern methods of construction in the UK.
The new brick slips centre at Nostell is progressing in two key phases. Phase one is nearing completion and focuses on driving pace and scale of brick slips through automation using the first of its kind technology here in the UK. Phase two, focuses on even more advanced technology which will significantly expand the brick slips product range and offering from 2025 onwards. The latter phase is a fundamental step in Ibstock’s journey to net zero.
The investment and innovation into the brick slips centre will not only continue to provide customers with a traditional authentic brick finish, but also enable a more modern installation approach. This will help meet the
1growing customer demand in midto-high rise newbuild and other key markets such as retrofit and the low rise modular offsite sector. The Group also continue to collaborate closely with developers and contractors on other new construction systems which will bring even more modern solutions and more carbon efficient building products to the supply chain, as well as influencing the design for manufacturing and assembly from early stages of conception.
Adam Foster, Project and Operations Director at Nostell, commented: “We are incredibly excited by what the development of our brick slips manufacturing centre at Nostell means for Ibstock as a whole – unleashing speed, scale, flexibility and precision in fast growing markets. The investment will increase our overall brick slip capacity by ten times more than what it is today, which is testament to our commitment to innovate for the construction industry.
“Not only do brick slips provide an authentic brick finish that will support planning applications, but also enable
a more efficient installation for the targeted markets. Its light weight, promoting easier installation, manual handling, less waste in construction, as well as time efficiencies on construction sites.
“The new manufacturing technology at Nostell also allows for more agile operations, with fast response times and lower minimum order quantities compared to current imported alternatives. Furthermore, the high precision and new process results in brick slips having a tighter tolerance for systems such as precast. The slips will be incredibly durable and safe from a combustibility perspective, meaning they can be specified with confidence across multiple system holders. For mid to high-rise buildings, retrofit and low-rise modular, using Ibstock brick slips can significantly streamline the specification process. We use a variety of materials to match regional styles nationwide, ensuring our slips can perfectly complement existing, handset bricks.
“The slips are also available in a range of bespoke thicknesses, from 15mm and above, meaning they suit a wide variety of applications. The high precision manufacturing and rigorous quality process allows us to achieve unparalleled precision on dimensions for manufactured systems requiring a very tight tolerance. By scaling production capacity of our brick slips, we are enabling more key markets to take advantage of the inherent benefits they can deliver.”
For more information visit: www.ibstock.co.uk
Images:
01. Ibstock is expected to produce 50 million brick slips a year
DEDICATED TO THE DEVELOPMENT AND APPLICATION OF PRECAST CONCRETE
P86
STORM ATTENUATION
Carlow Concrete and the tried and trusted Carlow Tank
P88
EVERTON FC
The final piece of a huge jigsaw at Everton FC’s new stadium has been lowered into place
P94
BIM & PRECAST CONCRETE
The value of BIM and digitisation in precast concrete structures cannot be understated
Welcome to one of our special magazine sections highlighting some recent projects and businesses operating within the precast concrete sector. These include a case study feature on the superb use of the material at one of the UK’s latest landmark buildings – Google’s London HQ near Kings Cross. As MPA UK Concrete explain in more detail, the early involvement of specialist offsite concrete contractors Laing O’Rourke meant that prefabrication was ‘baked in’ at an early stage of project development – key to the successful adoption of offsite methods.
Although familiar to all in the construction world and a mainstay of the offsite sector, precast concrete is at the centre of many landmark projects, but also plays a huge role in some unsung aspects of construction. As you will see from the work that Carlow Concrete undertakes with its storm attenuation tanks, these are an ideal solution to combat flooding – something that as the climate becomes more unpredictable will become increasingly frequent.
Precast concrete is well understood for its structural strengths, solid reliable mass and its ability to suit a variety of applications and sectors, and because of this is specified to provide stable solutions in all sorts of ways. Some examples of this you will find over the next few pages, including a recent product development from engineering specialist Akela Ground Engineering, that have unveiled a precast concrete beam system that could dramatically speed up the delivery of new homes.
82 86 88 89 92 94
As you pull into either King’s Cross or St Pancras railway stations you can’t help but notice Google’s new KGX1 UK headquarters – the tech giants ‘landscaper’ HQ is a precast concrete marvel. MPA UK Concrete tell us more.
Carlow Concrete are the market leader in water retaining precast structures in both the UK and Ireland, with its flagship product being the tried and trusted Carlow Tank.
The final piece of a huge jigsaw at Everton FC’s new stadium has been lowered into place, ending 18-months of complex work since the first concrete terrace was positioned in August 2022.
Engineering specialist Akela Ground Engineering, part of Akela Group, has launched an innovative precast concrete beam system which it says could dramatically speed up delivery of new homes.
Celebrating its 50th year in business in 2024, Creagh Concrete is one of the UK’s largest producers of precast concrete products for a range of market sectors.
The value of BIM and digitisation in construction cannot be understated –but how can Trimble’s Tekla software be used with precast concrete projects in mind?
As you pull into either King’s Cross or St Pancras railway stations you can’t help but notice Google’s new KGX1 UK headquarters – the tech giants ‘landscaper’ HQ is a precast concrete marvel.
Designed by BIG and Heatherwick Studio, the building is located at the heart of one of the most exciting and recently redeveloped neighbourhoods in north London. Dubbed the ‘landscaper’ the striking building is 330m (1,082ft) in length making it longer than the height of the Eiffel Tower or the 310m height of The Shard.
In an age of hybrid or home working it is developments like this, with approximately 80,000sq m (861,100sq ft) of office space, that have the potential to pull people back to the city post-Covid. Among the features available to Google’s workforce are extensive landscaped roof terraces, a running track and a swimming pool. The project reflects Google’s unique approach to the creation of
a large headquarters building in an urban environment. Upon completion Google’s King’s Cross campus will be able to house approximately 7,000 employees. Thus, strengthening the economy of the so-called Knowledge Quarter, a new world-class centre for research.
Platform G
Architecturally, the development is a testament to hybrid design, but it is the four rings of the precast concrete facade that really catch the eye. Also known as ‘Platform G’, the structure isn’t a gateway to Hogwarts, but you would be forgiven for being spellbound by the flowing concrete lines. The concrete facade is designed as a non-rainscreen concrete façade, difficult from an engineering perspective due to the section profiles, span and finish requirements.
The units are heavy blasted which can take up to eight hours to complete individually. The variation in panel type was also a challenge as Stephen Anthony, Technical Leader at Explore explained: “As the panels transition down the length of the building from Zone 1 on the south to Zone 5 on the north elevations, they went from overhung to underhung panels creating different tapers to each panel that had subtle mould adaptions. Along with the varying geometrical shapes the aesthetic requirement was to have three different finishes on the surfaces of the panels.” Together the façade panelling makes up the four eye catching rings of the building which tie other elements like the glazing and timber mullions together.
Ben Corlett, Contracts Leader at Explore, echoed why the KGX1 facade wasn't your average precast project: “The project's success hinged on achieving consistent aesthetics across a range of complex geometries and varying panel orientations with dramatic tapers. By tailoring the concrete mix, blast depths and utilising advanced mould designs, we were able to achieve some incredible geometries and fantastic finishes. It's a testament to what can be accomplished when we embrace challenges and push the boundaries of prefabrication and offsite construction.”
As is to be expected from a multibillion-pound tech giant, digitalisation and building information modelling (BIM) were requirements from the outset. The early involvement of specialist offsite concrete contractors Explo’re Manufacturing part of Laing O'Rourke meant that prefabrication could be baked into the model at an early stage. By choosing precast concrete the developer was able to capitalise on a number of benefits unique to this form of modern method of construction (MMC).
2 3 4
Although MMC can be associated with the installation of lightweight materials, the production of precast concrete panels for both floor, facade and structural units has been tried and tested over many years, with concrete MMC delivering significant advantages over lightweight construction. Concrete is an inherently noncombustible material with the highest fire safety rating of class A1, reducing risk and providing more reliable construction and greater confidence to clients.
The offsite structural components consisted of bespoke pre-stressed floor slabs, stairs and walls, removing the requirement for mass in-situ pours on an access restricted site. This moved labour and risk offsite to a more controlled environment. The fact that these were produced in factory conditions resulted in architecturally presentable, blemish and mark free soffits.
The main structure itself consists of five structural cores, from which steel trusses span outwards at the top which in turn support the rest
of the steel structure. Installing the precast concrete facade required counterbalance frames which allowed units to be installed level. This is important as when the centre of gravity rotates most precast façade units also rotate slightly when lifting.
The offsite approach also allows for programme optimisation with ‘justin-time’ delivery of units ready for installation. All required elements from a fully digital construction model can be planned into production schedules, meaning that Explo’re Manufacturing were able to meet the delivery and access demands of an urban setting in the heart of London.
The internal structure and floor design is also a unique feature with every third floor stretching the full width of the building. These major levels are constructed using ribbed/inverted/ raked pre-stressed architectural slabs and are stepped along the length of the building, with the varying heights sweeping down towards the station elevation. Concrete’s contribution to the internal flow of the building doesn’t end there with Explo’re
Manufacturing also delivering a bespoke architectural feature staircase. Between the concrete floor slabs, additional floor cassettes of cross laminated timber (CLT) have been utilised. With these floors set back from the external glazing, the office space is opened to create double or even triple height workspaces, not only maximising daylight but also increasing flexibility of use.
Any issues related to fire performance due to the inclusion of CLT are mitigated by using it in a hybrid design with concrete’s fire resistance and resilience allowing a circular economy approach with longer-life, low carbon assets that can be designed for change of use, disassembly and even element reuse.
The UK concrete and cement industry is decarbonising faster than the UK economy as a whole, successfully reducing emissions based on 1990 levels by more than 53%.
Currently, the UK concrete and cement industry accounts for around 1.5% of UK carbon dioxide emissions, five times lower than the global average where cement accounts for around 7% of emissions.
The sector plans to deliver net zero using a blend of approaches: decarbonised electricity and transport networks, fuel switching, greater use of low-carbon cements and concretes as well as Carbon Capture, Use or Storage (CCUS) technology for cement manufacture.
Within the precast sector specifically substantial progress toward decarbonisation is being made, with the introduction of more carbon efficient mixes and more low carbon solutions across the value chain. What Explo’re Manufacturing have managed to achieve here is truly a marvel of urban construction. Using their extensive experience of digital offsite construction the client now has a flagship presence dominating the landscape of King’s Cross.
For more information on the project and the benefits of precast concrete visit: www.thisisukconcrete.co.uk and www.mpaprecast.org or contact Martin Bolton, Senior Business Development Manager, Explore Manufacturing: mbolton@laingorourke.com
Client: Google
Project Team: Lendlease & Permasteelisa UK
Contractor: Explo’re Manufacturing part of Laing O'Rourke
Laing O’Rourke Explore Project Value: £21million
Completion: 2024
Images: 01-05. The Google ‘landscaper’ HQ is a hugely successful design using offsite manufacture and precast concrete to create one of London’s newest iconic buildings
MESH PRE-CUT & MODULAR
• Mesh optimized to 0% waste for all foundations & types of housing
• Available in packs ex stock
OFFSITE
(INCLUDING FASTERFIX)
• BIM 3D modelling details to optimize speed & efficiency
• 75% Faster
• JIT Delivery
ONE WAY MESH
• One way mesh, made to order, bespoke to your project
• Pre-centered from 10mm to 40mm
• Bim Level 2 modelling and 3D detailing services
• Domestic and International clients, enabling complete efficiency
SPECIAL MESH
• Solutions to all Sub/ Super-structure elements
• Special mesh - mixed diameters, per designs
• Reducing labor onsite by 50%
THREADING & COUPLING
• A full range - standard, positional, weldable and terminating couplers.
• Tapered threading of bars, providing a positive locking, no slip connection
FOUNDATIONS PRE-MADE
• Foundations pre-made & in stock for walls & pads
• Whatever size required, big or small
• Sizes rang from 150mm to 4m
ACCESSORIES
• A full range of construction accessories
• Concrete Spacer blocks, Wire Highchair, Tying Wire, Mesh Spacers, Square Bar, Permanent Formwork
Carlow Concrete are the market leader in water retaining precast structures in both the UK and Ireland, with its flagship product being the tried and trusted Carlow Tank.
Recognised by both water companies and councils, its stormwater attenuation system satisfies mandatory Sustainable Urban Drainage (SUDs) requirements and is fully S104 adoption compliant. To combat flooding, both Irish and UK building authorities stipulate a restriction on the rate of stormwater flow from the developed site to that of the original ‘greenfield’ condition. In many cases the most economical means of achieving this is to place a flow control device on the site outlet and to detain excess run off in subsurface stormwater attenuation tanks.
In terms of stormwater attenuation, the Carlow Tank offers clients the most efficiently and economically designed
solution in its class. This attenuation powerhouse promises the most robust solution on the market and may be located in highly trafficked areas such as roads and carparks.
Carlow Concrete prides itself on continuous design innovation and improvement. At design stage each project undergoes rigorous structural design using cutting edge analysis software and the option of 3D BIM modelling at both approval and construction stages. The extensive design service is implemented by a highly qualified design department which consists of civil, structural, environmental and process design
engineers. Their design department also maintain their innovation centre in terms of research and development which are very important to the group. Carlow Concrete are the only precast supplier to design out flotation issues and fully comply with BS8007 & Eurocode II.
The company has been recognised with many industry engineering awards and continues to lead the way in attaining the most approvals in its class along with having the accreditations to be used on the most rigorous of projects including aviation, high speed rail and of course the water industry.
Production
The fully integrated operation in Carlow is accessible to Dublin and Rosslare ports. Production buildings of over 7500sq m which are ideal for large scale production and graduated expansion. Core functions include design, estimating, NPD, technical lab and QA, mould-design, production and logistics. All production is made to relevant ISO standards and industry best practice. The production cycle from mould set-up to ex-factory delivery averages 10 days and current plant capacity is approximately 60,000 tonnes of precast concrete products per annum.
Why Carlow Concrete Stormwater Attenuation Tanks?
At Carlow Concrete a key ingredient of quality production are their technicians and in-house concrete testing lab.
Carlow Concrete
Key features and benefits of the Carlow Tank include:
• Available in depths from 0.8M - 7.0M in 100mm increments
• Configured exactly to suit client requirements including irregular shapes
• Watertight to BS8007 and Eurocode II
• Fully section 104 adoptable
• 120-year + design life
• No expensive imported fill required, backfill with dug material
• Reduction in labour and plant during installation
• Deep burial and heavy-duty loading applications
• Satisfies SUDs requirements
• Most cost-effective stormwater attenuation solution on the market
• CESWI & sewers for adoption compliant
• Rapid installation times and multifunctional applications.
Carlow Concrete offer a range of flexible procurement models to its clients, the most popular being that of a Procurement Framework Agreement. Many clients have taken full advantage of this approach when ordering the same service over an extended period of time on multiple projects and across several regions. Carlow Concrete is tried and trusted by top companies across the construction industry. For more information visit: www.carlowconcrete.com
Our AluSpace Interior Screening System is designed to divide or delineate both residential and commercial spaces, while at the same time providing an effective acoustic barrier. Choose from hinged single, double doors, pivot or sliding doors to accompany our stylish fixed glazed screen. This flexible and versatile system provides almost limitless design options whilst requiring minimal maintenance. AluSpace will provide many years of assured, reliable and robust performance.
For more information visit smartsystems.co.uk/aluspace
E sales@smartsystems.co.uk /SmartArchitecturalAluminium
The final piece of a huge jigsaw at Everton FC’s new stadium has been lowered into place, ending 18-months of complex work since the first concrete terrace was positioned in August 2022. And with all 1,988 double-stepped units now installed, on schedule, all four stands of the stadium are intact.
Gareth Jacques, Project Director of Laing O’Rourke, the company behind the stadium build, said: “Structurally, that is the stadium bowl complete. When you consider that alongside the terracing, the team have also done the structural steel and precast concrete in the four stands, it is a fantastic achievement. Because we use modern methods of construction and need to fix our design to go to fabrication early, the team worked really hard in the early stages of the project.
“The rate of progress we have achieved within the stadium meant that we were nearly 40% ready to go with precast components when we took possession of the site, so it’s been a great piece of work and a great product from our supply chain partner Banagher, in Ireland.”
Milbank Concrete Products has become the first UK-based precast concrete company to successfully complete delivery and installation of precast concrete hollowcore floors using 100% renewable hydrotreated vegetable oil (HVO) second generation biofuel.
The installation of over 190sq m of hollowcore flooring and three flights of precast stairs, on behalf of Tilia Homes located within their Sovereign Gate development in Thetford, marks the UK’s first-ever precast concrete installation using 100% HVO fuel throughout the entire process, from delivery to installation.
The delivery lorry (in partnership with Woodland Logistics), the mobile crane (in partnership with Cadman Cranes), and the site team installation van all ran on HVO fuel, a renewable fuel alternative to regular diesel. This innovative approach reduces the project’s installation carbon emissions by more than 90% and sets a new standard for environmentally responsible construction practices.
Ben Sharp, Tilia Home’s Senior Site Manager at the Sovereign Gate project, said: “Tilia Homes is committed to preventing environmental harm. This installation marks a pivotal moment within the construction industry, and we are delighted to be
The terrace units, averaging just under 9.5 tonnes in weight, have each been meticulously lifted into place over the past 18 months, secured with a highstrength grout and then made weatherproof with a special sealant. And the installation of the bespoke, double-stepped units – ranging from 0.73m to 14m in length – is a first for Laing O’Rourke, who pivoted from more traditional single-stepped blocks due to a combination of factors.
Jacques explained: “The double-stepped units are something we haven’t done before. In previous stadiums we have built, it has been a single-step arrangement, but there are a few reasons for developing the new method here. One was that we were always aware of the exposed location of the site,
and plenty of our engineered solutions have been done to reduce the risk of weather and lifting.
“The double-stepped terracing significantly reduces the amount of lifts needed and cuts down the time working on-site, often at heights. The by-product is that when you are building a football stadium, all the internal works and fit-out are generally underneath the terracing, so getting weathertight is on the critical path. The infill joints are really important and here at Everton we have 33km of Mastic sealant within the bowl, so by having double-stepped units we need less of that too.”
Source: www.laingorourke.com www.evertonfc.com
able to work with Milbank whose values align so closely with ours. This installation truly demonstrated the value of responsible construction and contributed towards an important reduction in our emissions at this project.”
Milbank Concrete Products has also made significant investments at its manufacturing facility in Essex with an aim of lowering its scope one and two emissions, with solar panels powering 50% of factory operations, fully electric forklift trucks, and a carbon neutral wood pellet boiler to cure its concrete beds. Since 2018, the business has successfully reduced its CO2 emissions by over 55%, with plans for net-zero by 2030, 20 years ahead of government targets.
Lee Cowen, Managing Director of Milbank Concrete Products, said: “Our aim is to be the most sustainable supplier of precast concrete products. While we have achieved significant milestones in recent years, our commitment to sustainability remains unwavering, and I am beyond proud to be part of such a passionate team that’s making all of this possible. We understand
the impact our industry has on the environment and we’re leaving no stone unturned in making changes for the better. This is the first of many installations delivered and installed with 100% renewable biofuel, and I look forward to supporting new and existing customers with many more.”
HVO fuel is a form of renewable diesel created from recycled sustainable vegetable oils. Unlike traditional diesel fuel derived from crude oil, HVO fuel offers significantly reduced greenhouse gas emissions. In fact, studies show HVO can achieve greenhouse gas reductions of over 90% compared to standard diesel, while producing little to no smoke. By adopting innovative solutions like 100% HVO fuel installations, Milbank Concrete Products is demonstrating a strong commitment to environmental stewardship. This approach paves the way for a more sustainable future in construction, minimising environmental impact while delivering high-quality precast concrete solutions for its customers.
Source: www.milbank.co.uk
Engineering specialist Akela Ground Engineering, part of Akela Group, has launched an innovative precast concrete beam system which it said could dramatically speed up the delivery of new homes. ‘ABeam’ features a special mechanical pinned joint, allowing for prefabricated ground beams to be installed in a matter of hours.
By combining precise offsite fabrication, alignment, and interlocking sections with secure fastening, this joint design ensures a robust, reliable and efficient way to connect precast ground beams. Officially launched at the National House Building Council (NHBC) Construction roadshow in Glasgow in March ABeam offers housebuilders an exciting new and sustainable alternative to ground beam installation. ABeam could help housebuilders lay foundations for up to three plots per day. Following significant investment, including the creation of a state-of-theart fabrication facility at Akela’s headquarters near Glasgow, ABeam has been specifically designed to offer housebuilders greater efficiencies in delivery of new homes.
Will Payne, General Manager at Akela Ground Engineering, said: “After reviewing the precast ground beam options available on the market, we found many still had considerable downsides, the use of
pile caps, insitu concrete and tie bars were common, this requires sequencing of works and could also be impacted by weather conditions, all of this leads to considerably longer installation times. Akela’s new ABeam precast system eliminates all of these issues and offers significant advantages in terms of construction install, performance and overall project quality.”
Akela’s purpose-built facility at Thornliebank has the capability to fabricate the Abeams in a controlled environment to ensure quality and production output. The company has also invested in renewable ground source heating for curing the concrete to lower the carbon impact on the environment.
Will Payne added: “In addition to the significant time savings and efficiencies, our new ABeam system can be delivered using the same plant equipment for full the installation process, with lighter bearing pressures from our JCB JX driven piling rigs. Using sustainable methods of production at our purpose-built facility
and existing equipment for installation, we’re able to reduce our carbon footprint and offer developers a more modern and energy efficient alternative to existing ground beam options. For example, with ABeam, clients will no longer need to install crane platforms or hard standings at their sites.”
Andy Borland, construction director at Bellway Homes, said: “Akela’s ABeam system has meant we were able to release plots to our wider teams a lot faster compared to other precast ground systems we have previously used. Our bricklayers were working on multiple plots within three days of pile installations at this development, rather than taking over a week and relying on the weather. We also didn’t need to install any crane platforms as Akela used the same excavated plant for the entire installation process, saving us money on preparatory works that other precast ground beams systems require.”
Source: www.akelagroundengineering.co.uk
Companies interested in delivering the infrastructure behind HS2’s elevated transport system – designed to boost the high-speed railway’s connectivity in the West Midlands – are being invited to take part in a new market engagement exercise.
Ahead of the formal procurement process, which is expected to launch in early 2026, HS2 is assessing the capacity of global suppliers to deliver the Automated People Mover (APM), which will carry passengers to and from the new high-speed station in Solihull. The APM is pivotal to HS2’s operation. It will provide a seamless link for regional, national, and international passengers travelling between HS2’s Interchange Station, the conventional rail network, Birmingham Airport and the events and entertainment complex at the National Exhibition Centre (NEC) and Resorts World.
Once appointed, the successful contractor will be tasked with the detailed design and delivery of the piers, viaducts, the APM’s four stops, the APM maintenance facility and all temporary works. HS2 expects to award the contract in 2028, with construction, system installation and testing forecast to be carried out between 2028 and 2030.
The APM network will run on a 2.4km long viaduct, with a series of piers ranging in height from six to
14m to maintain a consistent level for the viaduct. The network will traverse heavily developed land, with intersections at major crossing points including the M42 motorway, the West Coast Mainline and Pendigo Lake at the NEC campus.
Three of the four APM stops will be built on the viaduct, while the Interchange Station stop will be at ground level. Key design features include a series of reinforced central concrete piers, a weathered steel deck and escape walkway gratings across the length of the track. The viaduct structure combines
Engineering and Technical Director at Creagh Concrete, Mark Magill, has co-authored a guide to using precast concrete. Published in March, and titled ‘Precast Prestressed Concrete for Building Structures’, the book is aimed at consulting structural engineers, clients, precast prestressed concrete (PSC) manufacturers, and advanced undergraduate and graduate students, both as a guide and a textbook.
The book provides numerous worked examples for a wide range of PSC elements and covers the innovative use of PSC on several projects in the UK over the past 10 years, drawing on the Mark's first-hand experience in the design and manufacture of special products. The contents are in line with the latest revisions of the Eurocodes and European Product Standards.
The guide introduces and applies principles for the design of PSC slabs, thermal slabs, beam and block flooring and main beams, including (where appropriate) cantilevers, and composite and continuous construction.
Mark said: “Buildings are very often constructed using precast concrete elements in conjunction with other materials. The use of multiple materials and forms of construction can be the right choice for a project, or it may be the case that a fully precast structure is the best option.
both single and twin track paths at various points along the route to allow trains to pass each other. The APM stops at Birmingham Airport and at Interchange Station each have a single platform face and the intermediate stops at the NEC and Birmingham International Railway Station have two platform faces. The platforms vary from 36m to 40m in length and all platforms are fully covered with canopies and provide step free access.
Source: www.hs2.org.uk
“Over the last 10 years, adopting a fully precast solution for large, multi-storey structures such as residential apartments, hotels and student accommodations has gained popularity worldwide. The commercial market for precast prestressed concrete has been created and grown, not only due to the requirements of customers but also due to the confidence that is developing in the products being manufactured and the buildings being constructed.
“At the concept stage of a project, it is becoming more and more common for client design teams to develop a precast solution for tendering purposes – this is a clear indication that a positive choice is being made within the industry based on the merits of precast construction. Buildings will continue to be constructed using ‘traditional build’ methods such as masonry, timber, insitu concrete and steel frame, if they are the best option – but the development of precast and prestressed concrete is helping to ensure that it can be considered as a viable option in all projects. This guide discusses some of the wide range of precast and prestressed products that are typically used in the construction of buildings worldwide.” ing high-quality precast concrete solutions for its customers.
Source: www.creaghconcrete.com
The Swedish concrete element manufacturer Heidelberg Materials Precast Contiga and Metsä Wood have developed a hybrid wall element with a lower carbon footprint than conventional concrete wall elements. Now, the element solution is ready for use in real construction projects.
The hybrid wall element is a facade element in a sandwich construction, featuring an outer layer made of climate-improved concrete, intermediate insulation, and a load-bearing inner panel made of laminated veneer lumber, Kerto® LVL. The element has approximately 30-50% lower climate impact, compared to an equivalent traditional concrete sandwich element, and it is significantly lighter, which also affects the overall climate impact of the entire construction project. “Transportation to the construction site can be reduced because we can transport twice as many elements in the same shipment,” explains Daniel Eriksson, Division Manager at Heidelberg Materials Precast Contiga.
Nearly two years ago, the company-initiated discussions with Metsä Wood to start manufacturing hybrid elements for the Swedish market. “The production method is very similar to what we already
have, so we can create these hybrid elements using the same approach as our other walls, and they are assembled in the same way. We haven’t made any major investments or modifications,” adds Daniel Eriksson.
To practically test how the hybrid wall functions, a real house has been constructed on the factory premises in Norrtälje using these new elements. The test building is equipped with moisture sensors to monitor what happens inside the wall elements, and so far, no moisture has been detected. Additionally, various solutions for installations have been tested within the building.
“The EU aims to be climate neutral by 2050, and the construction industry can contribute significantly to reach this target and we’re experiencing a demand
for climate-smart solutions from the construction industry,” says Håkan Arnebrant, Business Development Manager at Metsä Wood. “One of the advantages of this hybrid element is that construction contractors do not have to change their way of building with concrete elements but can still lower their carbon dioxide emissions. At the same time, the walls can be made 50–75mm thinner than walls built with concrete elements, which can give quite a few extra square meters in a building.”
The hybrid wall element is particularly suitable for buildings with up to five floors. These can include residential buildings, offices, healthcare facilities, or schools.
Source: www.metsagroup.com
Celebrating its 50th year in business in 2024, Creagh Concrete is one of the UK’s largest producers of precast concrete products for a range of market sectors.
1
As a leader in the industry, Creagh is at the forefront of research and innovation, changing the way people think about concrete and bringing new solutions to construction. Based in Northern Ireland, Creagh has grown to occupy manufacturing sites across Northern Ireland, Scotland, and England to bring the business closer to its UK customers. With its customer focus and values of respect, expertise, and accountability in mind, Creagh ensures that all products deliver unparalleled quality and reliability, as well as bringing new levels of efficiency and performance to the industry.
This results in innovative products that are changing the future of the construction industry. Spantherm, for instance, is an insulated, precast concrete unit (IPCU) flooring system, and with several benefits, it is paving the way for the next generation of sustainable structural flooring systems.
Creagh has also launched Rapidres, a fast-track offsite cross wall build system ideal for applications such as apartments, student accommodation, hotels, social housing. Regardless of what a clients’ project entails, Creagh can provide a solution designed with engineering expertise and manufactured with innovative production methods, as well as expert customer service.
2
Seamus McKeague, Creagh’s CEO and Joint Chairman, says: “As a leading player in the construction industry, Creagh has carved a distinguished niche for itself with a rich history dating back to its establishment in Toomebridge, Northern Ireland, in 1976. Over the years, we’ve grown into a renowned provider of high-quality precast solutions in a journey marked by our commitment to innovation, sustainability, and excellence in both design and manufacturing.
“Today, the business is synonymous with delivering cutting-edge solutions for a wide range of construction projects, including residential, commercial, and infrastructure developments. With a focus on meeting the evolving needs of the construction sector, we consistently demonstrate a dedication to pushing the boundaries of what is possible in the realm of concrete construction.”
Reflecting on the company reaching 50 years in business, he adds: “Our 50-year tenure is a remarkable achievement and one that we are very proud of. Several factors have consistently propelled our success, most notably the combination of quality, innovation, adaptability, sustainability, and a commitment to our people and communities.
“Specifically, a steadfast commitment to quality is the cornerstone to
Creagh’s success, as we consistently deliver top-notch concrete products and services that meet, or even exceed industry standards. Our reputation for quality fosters trust among our clients and stakeholders, leading to long-lasting relationships and repeat business.
“As industry leaders, we’re constantly innovating. This adaptability and the rate at which we adopt cuttingedge technologies and construction methodologies ensures that we stay ahead of trends and continuously meet the evolving needs of the market. In addition, Creagh’s emphasis on sustainable practices not only reflects a responsible corporate method, but also resonates with a growing environmentally conscious consumer base.
Creagh’s product portfolio encompasses a diverse range of precast solutions, from cladding and flooring to premix concrete, blocks, and aggregates. With innovation engrained in its DNA, the company has added several new products and concepts to its offering during its 50year history.
“Although we started off as a small block and ready-mix provider, we’ve grown to be one of the UK’s largest precast providers across a range of categories,” says Seamus. “One thing is for sure; there are exciting times ahead, and who knows what innovation will come next from Creagh.”
For more information visit: www.creaghconcrete.co.uk
Images:
01. Seamus McKeague, CEO and Joint Chairman, Creagh Concrete
02. 17 Storey residential development "Elliott's Yard" on Gulson Road in Coventry built using Rapidres® from Creagh
While light steel framing can often be the focus of attention surrounding offsite and the value of BIM and digitisation in construction, precast concrete also forms a staple of many modern buildings and infrastructure. How can Trimble’s Tekla software be used with precast concrete projects?
It stands to reason that by automating otherwise manual processes, you can not only save time but also reduce the chance of error and improve productivity levels. Taking detailing as an example, this is a process where there can be frequent repetition and, as such, presents the opportunity for standardisation. Within Tekla Warehouse, you can find a library of standard components available for use, from couplers and rebar cages to precast panel ties, meaning you no longer have to waste time individually detailing them.
Another common challenge on any project is change management, whether coming from the client, architect or other sub-contractor. Here, the value of a software with parametric capabilities shines through. Rather than having to spend time manually checking and identifying the impacts of a single change, this can all be done automatically. By making the change in one place, all corresponding components or associated documentation will be updated too, providing added peace of mind that everything is accounted for.
As always, regardless of the material you are building with, visualisation is key. In many ways, by creating the 3D model, you are constructing the building or structure before you reach the site – building it first in the digital environment. The benefits of this are of course endless and well documented. When it comes to precast concrete, this enhanced visualisation enables you to identify and resolve any potential clashes before they become a problem. After all, once the concrete has been cast and slabs are arriving on site, there’s not much you can do if they don’t fit as intended.
As with so many aspects of construction, there are numerous stages and countless companies involved on a concrete structure, from estimation, detailing and design through to bar bending, precast manufacturing, concrete pouring and site construction or assembly. As a result, communication and integration is key and should be at the heart of all digital workflows. By using cloud-based collaboration tools, you can facilitate enhanced levels of communication, with the common data environment allowing precast models to be synchronised and easily shared with the manufacturer, contractor, engineer or design office.
Thanks to the controlled thread of data connecting all Tekla software solutions, you can also complete the code-based design in Tekla Structural Designer before transferring the design intent directly into Tekla Structures for concrete and rebar detailing. As a result of this software interoperability, teams stand to save considerable time, with the streamlined flow of information preventing the need for work to be replicated or the structure to be modelled twice.
At the fabrication stage, as with steel, the direct integration between software and machine can be invaluable, allowing the data to be exported and transferred from the 3D model to the machinery. With minimal manual input, you can avoid the likelihood of human error, as well as dramatically improving speed and efficiency levels.
A great example of Tekla software in action with precast concrete is Hewson Consulting’s work on one of the Thames Tideway shafts, featuring a combination of precast, cast-in-situ and reinforced concrete. By modelling all components within the one model, the team could consider co-ordination with the various interfaces and the M&E elements, visualise site access for the precast installation and highlight potential problem areas of rebar, all of which resulted in a smooth delivery on-site with minimal TQs and RFIs received.
For more information visit:
Images: 01-02. Precast concrete structures can be optimised at all parts of the development and construction phase www.tekla.com/uk www.tek.la/tideways-shaft
• All precast systems. All projects types and sizes
• Constructible modelling for error-free documentation
• All types of drawings, BOM, bending schedules
Tekla Structures helps you create purpose-built precast models ready to manufacture. Tempted to give it a try?
tek.la/structures-free-trial
OFFSITE EXPO is aimed at construction professionals all with a specific interest in offsite technology. Exhibitors will have access to over 5,000 relevant visitors across two days – plus exclusive access to the OFFSITE CONNECT BUYERS & SPECIFIERS FORUM where you can schedule meetings with some of the UK’s top Buyers and Specifiers.
Part of OFFSITE CONSTRUCTION WEEK, OFFSITE EXPO has a range of exhibition and sponsorship packages available. These have been designed to be flexible and offer a wide range of promotional opportunities to suit any marketing aims, resources and budget.
Email julie.williams@radar-communications.co.uk or call 01743 290 001
THROUGH DIRECT INTERACTION WITH YOUR KEY TARGET AUDIENCE ALLOWING YOU TO GENERATE HIGHLY-QUALIFIED LEADS FOR
Our software suite is at the forefront of design, specializing in light gauge steel detailing, structural engineering, and manufacturing preparation.
Following the design phase, we leverage our cuttingedge roll forming equipment and expertise to commence manufacturing, ensuring precision and quality in the assembly of building components.
Our integrated approach to design and manufacturing is geared towards optimizing onsite construction efficiency, streamlining the entire construction process for maximum effectiveness.
Watch Systems Overview Video