
11 minute read
A Kit of Parts Approach
As Chris Mortensen, Co-Founder of Modulous, points out, we need a data-first product-led approach to deliver sustainable homes at scale and pace.
The UK has the oldest housing stock in Europe. Over 52% of homes in England were built before 1965, whilst nearly 20% were built before 1919. A lack of fabric efficiency and insulation has led to 60% of the UK’s housing stock - some 13.3 million homes – being EPC rated D or below. With the increased need for sustainable homes to achieve the government’s net-zero ambitions, there will be increased calls for a massive retrofit programme which could cost up to £525billion. Yet it’s not just the retrofitting of old homes that should be high on the government’s agenda. More homes are clearly needed to meet the ever-growing demand from the UK population. Supply and demand mismatches have led to the average house price rising by £27,000 in the year to February 2022, with the average house price now standing at £277,000. To tackle the housing shortage whilst avoiding adding to the retrofit bill, we need to ensure that most – and preferably all - of the 300,000 homes the government is targeting to be delivered per year are designed and delivered to meet the UK’s Carbon Budget and the UK’s commitment to be net zero by 2050. This obviously means they should be energy efficient and low carbon, but it’s also important to take a holistic view and deliver healthy homes that maximise occupier wellbeing through comfort, security, and lack of harmful construction materials.
Maximising efficiencies and shortening build times is essential as the construction industry continues to deal with increased materials prices, labour shortages and supply chain delays at the same time as being placed under pressure to deliver more homes. With the Farmer report predicting around 62,000 construction workers will retire each year between 2016 and 2026, the time is now to adopt innovative methods and become product-led.
The treating of a house as a product – albeit the most expensive product you’ll buy in your life – can help to deliver better homes thanks to the tighter quality control that is possible in a factory setting. Modern Methods of Construction (MMC) continues to build momentum as developers, councils and government recognise the pivotal role it can play in delivering homes faster than traditional methods of construction. This has resulted in Homes England informing its strategic partners that they must commit to increasing their use of MMC if they wish to obtain funding for development sites.
1
But there is room for MMC to become even more efficient. At Modulous, we’ve combined the digital with the physical to enable the design
and construction of modular homes more affordably and efficiently than through traditional or typical MMC means. We realised that we needed to base our designs on a known Kit of Parts to ensure that we can effectively and accurately generate designs, quantify costs, calculate build times, and leverage the supply chain through our software. Plus, by taking control of the physical elements of the build, we can better influence the overall environmental performance of projects.
To build homes more efficiently and faster than we are currently, it is necessary to rationalise, standardise, and utilise the power of digital design to boost scale. By collating data from multiple sources – including local planning regulations – into one easily accessible tool, it becomes possible to test-run multiple planning compliant scenarios at a development site and reduce the entire site assessment process from months to minutes.
We can also use data to accurately calculate the specific components and assemblies required to deliver a scheme, which drives down material wastage and improves cost certainty. Given that construction, demolition and excavation accounts for almost two thirds of total UK waste, it is becoming increasingly urgent to reduce the amount being sent to landfill.
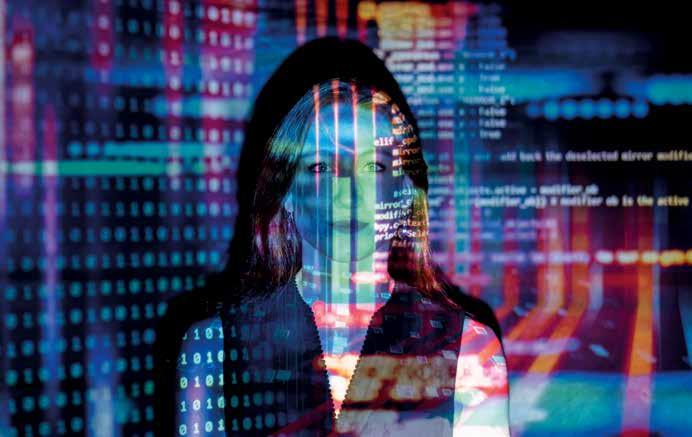
It would be wrong to look at the housing and climate crises as solely UK phenomena and as such it is vital to create a model that is globally scalable. We’ve looked to tackle this through our asset-light approach, which enables us to partner with the supply chain to produce our highly engineered Kit of Parts. This removes the need for capital-intensive dedicated factories and is more responsive to fluctuating demand. Transferring the model to other markets simply involves adjusting the Kit of Parts to suit local codes and expectations and forming new partnerships as needed to deliver it – something we are already doing in the USA.
Data-driven technologies, productisation, and a holistic approach to sustainability offer the construction ecosystem the potential for a step change in the way housing is delivered in the UK and across the world. We are committed to addressing the twin crises of homelessness and climate and are confident that maturing ConTech solutions such as ours provide the blueprint.
MODULOUS
Modulous was founded in 2018 by a team of industry experts spanning design, engineering, finance, manufacturing, and construction, who set out to transform the way residential buildings are designed and delivered. Modulous is creating a connected digital and physical product suite that enables the delivery of quality affordable and sustainable homes globally. The Modulous design software is connected to a proprietary set of sub-assemblies – its ‘kit of parts’ – that the company developed to meet or exceed local building standards.
2
For more information visit:
www.modulous.com
Images:
01. Chris Mortensen, Co-Founder, Modulous 02. Digital tools and reliable data are driving change across the offsite sector
RAISING THE QUALITY BAR
Vision Modular Systems (VMS) – one of the UK’s best-known providers of offsite manufactured volumetric modular residential buildings – has seen many efficiency gains in its lifting operations thanks to experts at Britlift.
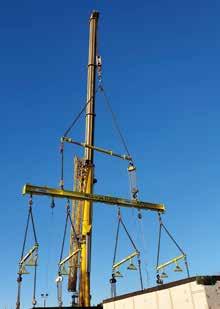
1 2

VMS wanted to improve lifting operation by reducing the weight of its lifting frame, thereby minimising downtime and improving overall flexibility. To do so, the company turned to Britlift to provide a better solution.
Krzysztof Wylezek, General Manager of Vision Modular Systems UK Ltd, says: “We chose Britlift because they have a young, proactive team and were able to create a solution that perfectly meets our needs. This has become a standard product for us, using Britlift spreader beams within our lifting frame configuration.” Britlift designed, manufactured and supplied lifting beams, telescopic spreader beams and adjustable chain sling sets, providing VMS with the capability to lift all types of modules, including on its pioneering 44-storey modular building in Croydon. Britlift’s engineering capability also reduced rigging weight by over 50%, to around two tonnes. This enables quicker adjustment during the installation of different sized modules, reduces the overall rigging weight on the crane hook, and improves manual handling.
“VMS recognised that they had to save rigging weight, so we designed and supplied them with something totally new,” says Liam Botting, Managing Director of Britlift. “Telescopic spreaders were not at all standard for this type of application but are now much more commonplace because of Britlift. In fact, this has made us the go-to supplier within the offsite sector.
“Since then, we have won repeat orders from VMS and also provided additional services such as engineered rigging drawings to lift every module in their project. This involved over 40 different drawings created by our in-house technical team. VMS has a strong focus on safety and takes lifting very seriously. Working with Britlift, they have demonstrated that investment in best practice can deliver efficiency gains as well as enhance site safety during lifting operations.
“VMS has continued to come to Britlift for more equipment and more service lead support, as well as lifting and rigging advice and general lifting safety guidance. This is where Britlift can add real value beyond simply supplying equipment. Because of the experience and expertise in our engineering team we can truly support our clients. With a team of degree-qualified mechanical and structural engineers, and a Technical Director who is a registered member of IEng and member of IStructE and MIET, Britlift can also offer a specialist engineering consultancy service solely focused on lifting.”
EXPERT ADVICE & PARTNERSHIPS
Based in Dorset, UK, Britlift works with a global client base, providing an end-to-end lifting equipment engineering service including design engineering, manufacture, certification, and testing. Alongside this Britlift offer lifting equipment consultancy services such as lifting tool design, bespoke lifting lugs/connections, rigging design, design only services, project witnessing/ verification and more. The company manufactures a wide range of lifting beams and frames and can design a lifting solution to suit any lifting scenario, challenge, environment, restriction or project standards. Its Traditional Modular spreader beam is also available in a variety of standard sizes.
For more information visit:
www.britlift.com
Images:
01-02. Reliable lifting expertise and using the right equipment is essential to project efficiency and health and safety
TRIPLE MODULAR WIN FOR ESSEX
The ‘better, greener, faster’ approach to developing new public buildings has been used to great effect to create three new volumetric modular school buildings for Essex County Council.
Morgan Sindall Construction’s Essex business delivered the school buildings located at: Colne Community School & College in Brightlingsea, Colchester; Clacton County High School in Clacton-on-Sea; and Sweyne Park School in Rayleigh. The comprehensive upgrades were awarded to Morgan Sindall Construction by the council under the ECF2 Framework and amount to £9.5million.
The modular units, manufactured by Eco Modular Buildings, were used throughout each project to ensure that the work was delivered quickly, efficiently and to a high standard while minimising disruption to the live school sites. The offsite approach that Morgan Sindall Construction implemented was a key part of these school buildings being able to achieve net zero carbon in operation, which was a first for the county.
At Clacton County High School in Clacton-on-Sea, a £3.5million expansion project involved the construction of a brand-new standalone teaching block, creating 10 general teaching classrooms, a plant room, and a four-court sports hall.
A brand new £4million teaching block was handed over at Colne Community School & College in Brightlingsea, Colchester includes eight general teaching classrooms, two resistant material technology rooms, two food technology rooms, a seminar room and a plant room.
A £2million standalone teaching block was built at The Sweyne Park School in Rayleigh to provide an extra 150 places for children of high school age. This block included six general teaching rooms, a WC, and staff rooms as well as special provisions and classroom enhancements to support suitable education for hearing impaired pupils.
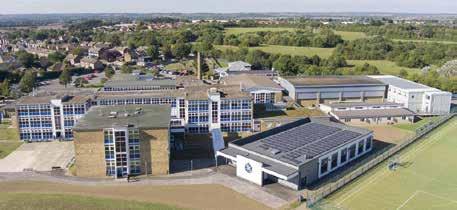
Peter Whitmore, Managing Director for Morgan Sindall Construction’s East region, said: “With the government’s net zero target shining a spotlight on the importance of low carbon developments, these projects are a great showcase of how to design, construct and manage building projects with significantly reduced levels of carbon emissions. Thanks to the success of this approach, Essex County Council has been able to meet its impressive net zero in operation goal.
“We worked closely with a number of key stakeholders, including Essex County Council and the school’s staff, to ensure that the new buildings would be ideal for the task at hand. This even included taking one of the head teachers on a visit to the modular factory to explain the design and the process. We’re delighted that the schools have now been delivered and that they’re having a really positive impact on the growing communities in which they’re based.”
Stuart Beales, Sales and Marketing Director at Eco Modular Buildings, added: “These projects are a great example of what can be achieved when sustainable, modular technologies are used together in a clever, joined up manner. Thanks to this approach, the school’s all have a number of energy efficient, carbonreducing advantages built into the very fabric of the classrooms and corridors.
“These advantages range from solar panels, air source heat pumps and low energy ventilation to metering systems that gather data on energy usage in order to continually improve how the school operates. When combined with the superior insulation and airtightness levels we’ve achieved and the reliability of the offsite manufacturing methods, this will all enable the schools to generate as much power as they will require."
Cllr Tony Ball, Essex County Council Cabinet Member for Education Excellence, Lifelong Learning and Employability, said: “Using the modern methods of construction approach on these three projects has enabled us to successfully deliver new teaching space for schools whilst at the same time helping us deliver on our ambitions to tackle climate change and work towards making Essex carbon neutral."
1
For more information visit: www.morgansindall.com
Images:
01. Sweyne Park School, Rayleigh
OFFSITE CONSTRUCTION INFORMATION PORTAL
FREE TO ACCESS
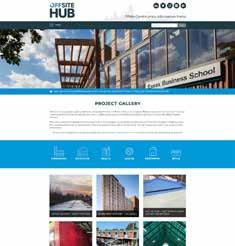
Digital Marketing Packages Available
The Offsite Hub receives over 5,000 unique visitors per month, complemented by 42,300 newsletter subscribers, making these digital opportunities an attractive proposition for marketers planning future activity.