
7 minute read
The Future of Sustainable Living
Debansu Das, Business Development Director for ZEDPODS, explains how energy efficiency and volumetric modular technology is delivering zero carbon housebuilding.
Living in an ever-uncertain world has become the new normal. Currently we are facing up to the word ‘crisis’ on a far too regular basis. The ‘cost of living’ crisis, due to sharp rise of energy prices, has been added onto the health and well-being crisis, just at the point we are getting out of the pandemic and looking to find our BREXIT feet.
Energy efficiency therefore has become far more relevant in today’s world. The built sector needs to play its part – all newbuilds should focus on increased building energy efficiency, with on-site renewable energy and less embodied carbon emissions. Net zero not only benefits the planet and helps abate climate change but they reduce ongoing costs for the occupants. It is therefore no surprise that more and more social landlords are embracing offsite-led developments to build affordable, good quality, energyefficient modular homes for their tenants.
Sustainability is at the heart of our design and construction works. We have designed and developed a factory built modular construction system that can be used to assemble buildings and is designed with an approach to holistically reduce carbon emissions and energy use.
Our Approach to Zero Carbon
We are a modular housebuilder as well as a leading modular architect practice with decades of experience of zero carbon homes within the team. We follow a strategy of enhancing the building fabric, maximising the
1
number energy efficiency measures used and applying low carbon and renewable technologies. Using BIM software, we design out carbon from building fabric, material choice, passive solar design and M&E. The steel framed volumetric modular construction system has been designed with a ‘fabric first’ approach to reduce operational carbon emissions by minimising thermal losses by conduction and infiltration.
Firstly, we reduce how much heat is transferred from inside to outside (the largest loss of energy in buildings) by specifying thick insulation build-ups, insulated floor slabs and thermally efficient triple glazed windows and doors. We also use mechanical ventilation that recovers more than 80% of the heat from expelled air
meaning that there is a constant supply of fresh air circulating without the natural heat loss of other ventilation methods.
Our strategy is to reduce the amount of energy used by occupants. During the design of our projects, we utilise simulation software to ensure that adequate daylight factors are created inside the spaces, reduce artificial lighting and increase solar gains.
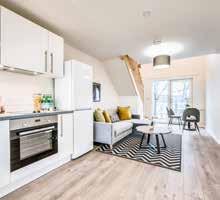
We use on-site renewable technologies to meet energy demands – for hot water and heating demand via MVHR unit and a solar assisted heat pump. Our units have no gas connections and so the remainder of their energy is met by roof mounted photovoltaic panels. This offset the remaining carbon emissions resulting in a zero carbon scheme with a negative dwelling emission rate.
Zero Carbon Keyworker Accommodation
Our first zero carbon residential project was 10 new studio apartments for an NHS Foundation Trust on a hospital site. The self-contained units were required to be in operation as fast as possible so that the nurses and junior doctors can stay near to the hospital without having to take long commute home. This keyworker accommodation was designed, built offsite and delivered to the hospital site in just 13 weeks only despite numerous COVID-19 related challenges.
Using our innovative grid-based design and steel framed volumetric modules, we completed the apartments in the factory while the ground was prepared at the same time. These homes were built with SAP-A rated energy-efficient performance standards that exceed the building regulations. The modular building has been named ‘Captain Sir Tom Moore House’ in honour of the famous fundraiser who lived locally.
Zero Carbon Social Housing
Our award-winning social housing scheme ‘Hope Rise’ for Bristol City Council is a UK-first project of using ‘air-rights’ over car parks to increase the supply of land and tackle the affordability of new homes. These homes are built on a raised steel platform over an existing councilowed public car park at Chalks Rd. It comprises of nine apartments constructed of cross laminated timber (CLT) and two homes constructed of steel. It is quite rare in modular sector to combine the two materials in the same project. 100% of original car parking spaces have been retained.
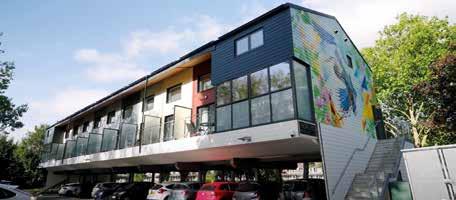
According to one Hope Rise Resident: “I have lived in a ZEDPODS home for over a month now and I still have to stop to appreciate how nice of a house I have at such a young age. I was nervous about moving in so close to Christmas because of winter and most people I know when they first move in it’s always cold. However, the homes are really warm and don’t take long to heat up.”
An end of year energy usage analysis has shown 104% of the annual energy requirement was being generated onsite by the PV array, making this ZEDPODS development a zero carbon in operation. Hope Rise was the only residential newbuild modular scheme which was showcased at COP26 summit last year at Built Better Now, a virtual pavilion for the Built Environment, along with 16 other leading sustainable projects across the world. Building zero carbon homes is a large part of the story but not all. We encourage zero carbon transport and discourage car ownership on our schemes. We provide electric vehicle points on our schemes and focus on regenerating brownfield sites with great public transport links and local amenities to support a wider low carbon lifestyle. For example, Hope Rise doesn’t have any car park spaces for the residents, as it is an urban site with great public transport links and local amenities, complying with the sustainable transport strategy of the local council.
Going Forward
The biggest challenge is the perception about what is possible and commercially viable. We work with local authorities to push the agenda and demonstrate what will fit with their cost models to show you can delivery zero carbon affordable homes. Perception is also that homes must be brick and block and not modular/ low embodied carbon materials. We work hard with warranty providers, BOPAS, lenders and insurers to demonstrate durability and longevity so that the full delivery chain understands what is possible now and why it works now. Overcoming these entrenched opinions and structural and systemic barriers is key to deliver net zero now. As the sector grows and develops, more zero carbon homes will be built by in the UK.
2 3
For more information visit:
www.zedpods.com
Images:
01. The Burnt Ash Lane project of 25-units above a public car park for London Borough of Bromley will save 900 tonnes of carbon over 30 years when compared with traditional construction 02-03. Hope Rise, Bristol. Courtesy ZEDPODS
MODULAR CONSTRUCTION & FIRE BEHAVIOUR
Dorjan Dauti, PhD, Structural and Research Engineer at Efectis, sheds some light from a numerical modelling perspective on modular design.
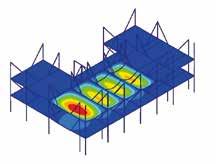
Over the last few decades modular construction has been primarily used for small residential construction projects, nowadays bigger and taller modular projects are rising such as hotels, offices, high-rise residential buildings etc.
Fire safety professionals are therefore driven by this increasing popularity into tackling the fire safety issues linked with modular construction. One of the main issues of concerns is the overall behaviour of the modular structure in the event of a fire including the impact of the module’s displacement on the connections between modules.
The high temperature behaviour of modular construction is rather complex. Fire testing alone is often not enough in evaluating the fire resistance of the overall system due to size and loading limitations in fire laboratories and 3D modelling studies are often necessary for the fire safety assessment.
The main challenge is the performance of connections, which are used for fixing the modules to each other and transferring the horizontal loads Vertex BD back to the stabilising elements of the building. Differential heating, It’s All About BIM expansion of structural elements and second order effects (deformations causing initial loads to induce further stresses into the structure) are some of the main phenomena, which can lead to failure of connections and consequently compromise the fire resistance of the building.
We believe that finite element simulations are indispensable for understanding these complex phenomena and evaluating the impact of fire on the resistance of the structural elements that compose the modular building. While modular construction is paving its way as a construction method for tall buildings, we are prompted by the challenge of evaluating the fire resistance of such type of construction.
Vertex BD For more information visit: www.efectis.com or email: It’s All About BIM Dr Talal Fateh: talal.fateh@efectis.com
Vertex BD Vertex BD Sales Architectural Design
Marketing Framing
One BIM software platform to drive your entire building project from start to finish
• Architectural Design • Automated Steel and Timber framing • CNC data for CFS, Timber and HRS
• Precise project documentation Project Archive
• One software, one model
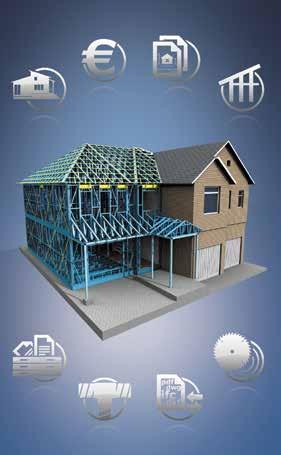
IFC Collaboration File Format Conversions Production Automation
Increase Productivity, Improve Quality, Minimise costs
Contact our Harrogate based team today to learn how we can help you with your next project.
Marketing Sales Architectural Design
Framing
Project Archive
IFC Collaboration File Format Conversions Production Automation