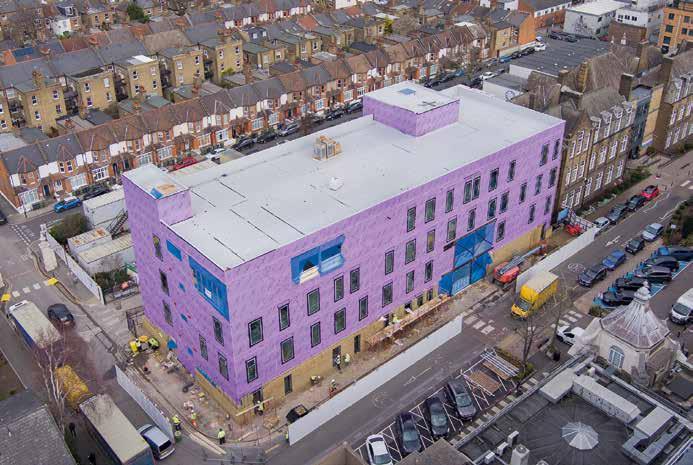
8 minute read
Maximising Material Efficiency
As the UK looks to ‘build back better’ Richard Hipkiss, Development Director of the Modular and Portable Building Association (MPBA) highlights the need to reduce landfill waste and improve material optimisation.
According to the UK Green Building Council, approximately 400 million tonnes of materials are used by the UK construction industry annually. The Council’s vision for a sustainable built environment is one that eliminates waste and maximises resource efficiency. However, there is a great void between this vision and reality with Transparency Market Research predicting that annual construction waste could reach 2.2 billion tonnes per year globally by 2025. Reducing landfill waste therefore has to be a priority. Volumetric modular construction can provide a practical solution. Individual modules are produced in factory settings, maximising resource efficiency while also allowing better control over optimising material use. The surplus materials are recycled or reused for future projects, reducing the construction waste that ends up in landfill. Materials are protected from moisture and extreme weather conditions, reducing the risk of disposal through water ingress and damage. While widely recognised that volumetric modular technology has the potential to reduce overall construction programmes, it is not often acknowledged that this approach can reduce up to 90% of waste generated when compared with traditional construction methods.
1
Resource efficiency is the maximisation of time, processes, materials and labour to function more effectively. Volumetric modular technology can help deliver sustainability credentials in the entire construction value chain to improve resource and productivity efficiency. Modular builds are less susceptible to poorly specified manufacturers’ products as time can be taken upfront to validate the correct specification of materials. Designs are digitally constructed and virtually tested before moving
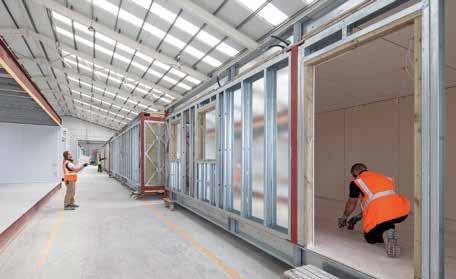
onto the manufacturing phase. This process eliminates waste and achieves highly accurate and airtight building envelopes designed and built to higher sustainability requirements.
It is easier to control energy use in a factory setting than in an open construction site. On average 67% less energy is required to produce a modular building and up to 50% less time is spent onsite when compared to traditional methods, resulting in up to 90% fewer vehicle movements which is less disruptive for the local community and reduces carbon emissions.
Not only is the actual construction of the building ‘greener’ but volumetric manufactured buildings are also more energy efficient – reducing heating requirements and in-use carbon emissions for the lifetime of the building. This is a crucial factor in mitigating climate change. Research conducted by the World Green Building Council finds construction and buildings in use are responsible for 39% of all carbon emissions in the world. This is broken down into two elements with 11% being linked to the manufacture of materials and construction processes known as embodied carbon emissions and 28% associated with operational emissions caused by heating, cooling and lighting systems when a building is in use.
Modular technology brings a host of benefits to the construction industry, contributing to healthier, safer and more cost-efficient environments but often the sustainability gains are overlooked. The modular way limits the amount of concrete in the ground, which is a significant issue for traditional builders. Eco-friendly materials are often specified and each individual component can be selected specifically for its performance characteristics, tailoring every inch of a modular build.
Volumetric modular construction presents an opportunity to integrate upstream with downstream construction practices and achieve sustainability gains throughout the entire process. In her report ‘Building a Safer Future’, Dame Judith Hackitt highlights the need for a systembased approach with a golden thread of information running through the lifecycle of each project. A smart modular construction regime can operationalise the collection and storage of components' lifecycle information. Allowing the sector to build the capabilities needed to support the maintenance, recovery and reuse of modular components – further supporting the UK Green Building Council’s vision for a more sustainable built environment that eliminates waste and maximises resource efficiency.
As the construction sector develops and adapts to meet changing government strategies, I firmly believe the upward trajectory of modular will continue and although currently not making the headlines, climate change is a major crisis, and we need to act now to help mitigate the impact for future generations to come.

MPBA
The Modular and Portable Building Association leads best practice protocols, the development of standards and is represented on many government committees for the benefit of members. The association collaborates with specialist technical advisors to enhance innovation in the design and manufacture of volumetric modular buildings.
2
3
For more information visit:
www.mpba.biz
Images:
01-02. King’s College Hospital. Courtesy Premier Modular 03. Premier Modular generates zero waste in their manufacturing processes. Courtesy Premier Modular
EMBRACING THE MODULAR CIRCULAR ECONOMY
Finlandia Hall, Helsinki's most famous and architecturally unique venue for conferences and other events, is now flanked by a timber volumetric modular construction known as Little Finlandia.

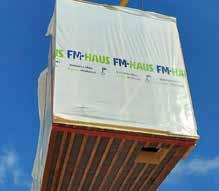
1
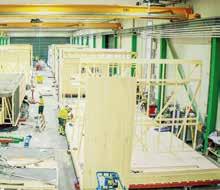
Little Finlandia has been designed by architects Jaakko Torvinen, Havu Järvelä and Elli Wendelin in collaboration with Professor Pekka Heikkinen and Architects NRT Oy and Arkitekturum Oy. It will provide temporary facilities during the renovation of Finlandia Hall and is a joint project of the City of Helsinki, Finlandia Hall, Aalto University and FM-Haus, with the timber elements supplied by Metsä Wood.
The structural design of Little Finlandia was based on the possibility of reusing the building. Once the renovation of Finlandia Hall has been completed, it can be moved to other locations. Little Finlandia complies with the principles of sustainability and the circular economy and is made of volumetric modular and reusable timber units. Prefabricated at FM-Haus’s factory, the floor and roof structures feature Metsä Wood’s Kerto LVL RIPA technology.
“Thanks to RIPA technology, we didn’t need as much Kerto LVL for the wooden elements. This matches our ecological values, as it means a reduced volume of material,” says Juhani Sjöman, Managing Director of FM-Haus. “Modular construction has also made a big difference in the speed of construction. In the case of Little Finlandia, modular construction cut the on-site construction time to a third of the usual duration.” Constructed from timber volumetric modules, the units were prefabricated by FM-Haus at its element factory in Jokioinen, 120km north of Helsinki.
2
The buildings constructed by FM-Haus are easily adaptable and modifiable while offering the properties and fulfilling the criteria of permanent buildings. FM-Haus wants its buildings to serve people with flexibility for as long as possible. Another major goal is to put a stop to single-use construction. Metsä Wood and FMHaus share the same goal: they aim to be as sustainable and environmentally friendly in the construction value chain as possible.
The load-bearing structures of the modules used in Little Finlandia are built with several Kerto LVL products, including Kerto LVL S-beams, as well as Kerto LVL Q- and Kerto-Kate panels. Each of these products offers superior usability and properties for their purpose. Although lightweight, the products are very strong and rigid. Kerto LVL is structural laminated veneer lumber used in all types of construction projects, from new buildings to renovation and repair and is produced from 3mm thick rotary-peeled strength graded softwood veneers that are then adhesive bonded then cut to size as beams or panels.
3
Little Finlandia also meets stringent standards for fire resistance. The Kerto LVL structures used in the building have a fire resistance of 60 minutes. The building also features three fire compartments, bordered by fire dampers that withstand fire for 30 minutes. The ventilation engine room and the intermediate floors were constructed to ensure a fire resistance of 30 minutes. The timber panels used in the modules have a high fire- and char resistance, and they have been treated with a certified fire retardant to ensure they satisfy the fire safety requirements of European design standards.
“To ensure that the building meets the requirements for adaptability, transport and reuse, it must be constructed from durable and premium-quality materials. The elements, made of Kerto LVL products, ensure a long-lasting building that withstands heavy use,” says Lassi Moisio, from Metsä Wood. The renovation of Finlandia Hall is to be completed in late 2024 and will serve its current purpose for at least three years before being relocated as temporary facilities for schools and day care centres.
For more information visit:
www.metsagroup.com
Images:
01-03. The timber volumetric modular structure enables material circularity and the building will be moved and repurposed
THE POWER OF FASTENING
BeA Fastening Systems Ltd is part of the successful global group BeA GmBH and have been in the fastening business for 50 years in the UK, manufacturing fixings and fastening for construction and industrial sectors across the world.
1
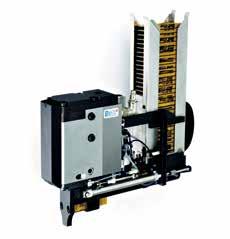
In recent years in the UK, BeA has seen increasing demand from many offsite and structural timber manufacturers, with a focus on housebuilding. The offsite industry has some unique and specific construction challenges – the type and quality standards of fixings are very often bespoke to this sector. By working closely with some of the major manufacturers, BeA has actively developed specific fixings, fasteners, tools and manufacturing automation to satisfy this fast-growing sector. Staplers and nailers remain the core products from BeA, more recently our range of automatic solutions for larger scale manufacturing have seen increasing demand from offsite and timber manufacturing.
Fully Automatic AUTOTEC for Offsite Manufacturing
BeA have semi-automatic and fully automated fastening solutions capable of reducing costs and further improving production efficiencies. Autotec is BeA’s fully automatic system with a full range of framing nail guns, coil nail guns and staplers.
A Complete Service
BeA also offer our customers an excellent service. This includes professional advice from our experts and field sales advisors, fast and ontime delivery and both internal and mobile technical support tailored to our customers needs when it comes to maintenance and repair.
For more information email us at:
sales@uk.bea-group.com
Images:
01. BeA Autotec Stapler with cassette
Setting the standards for offsite fastening
BeA your partner for offsite timber and light gauge steel frame construction
THE POWER OF FASTENING
Across Europe and worldwide, BeA’s fastening technology, tools and consumables are the trusted choice for some of the biggest and best known names in offsite timber and light gauge steel frame manufacturing.
BeAssured
Reliable products, competitive prices and the kind of service and delivery you can depend on from BeA.
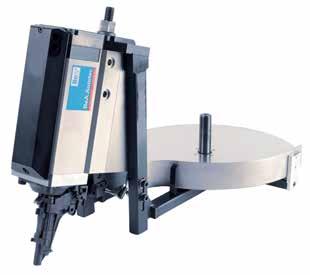