MODULAR

UNIVERSITY HOSPITALS
BIRMINGHAM
McAvoy works wonders with its SmartCare® modular solution
OPERATION OFFSITE TRANSFORMING HEALTHCARE WITH MODULAR SOLUTIONS
SOUTHMEAD HOSPITAL ESTATE
Wernick and consistent factorycontrolled building design
CLATTERBRIDGE HOSPITAL
Minimising disruption and reducing the impact on clinical care
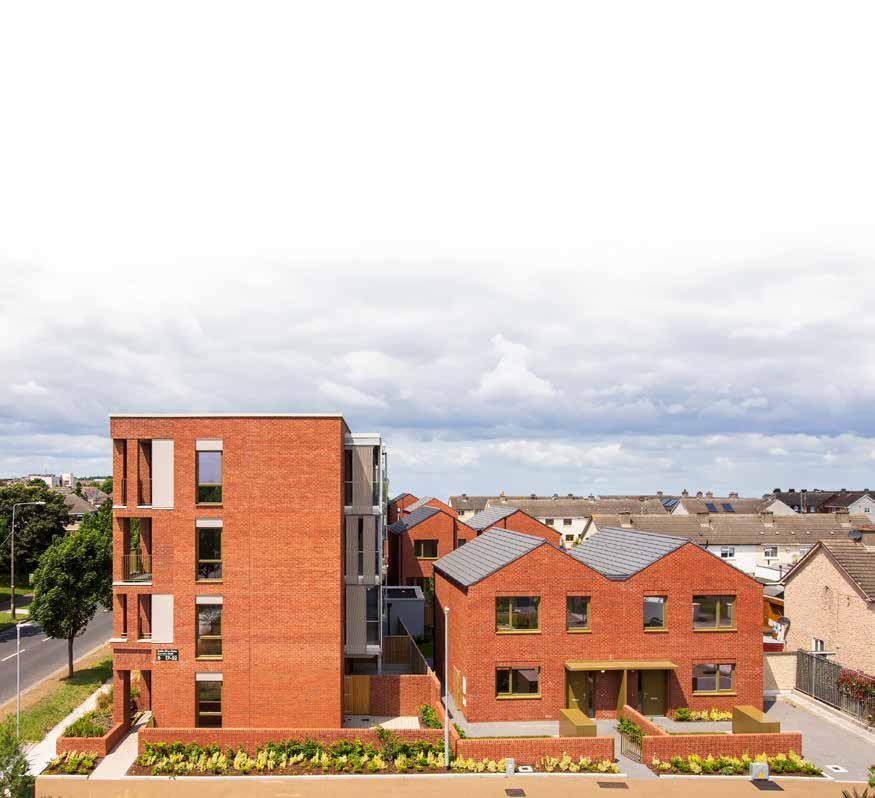
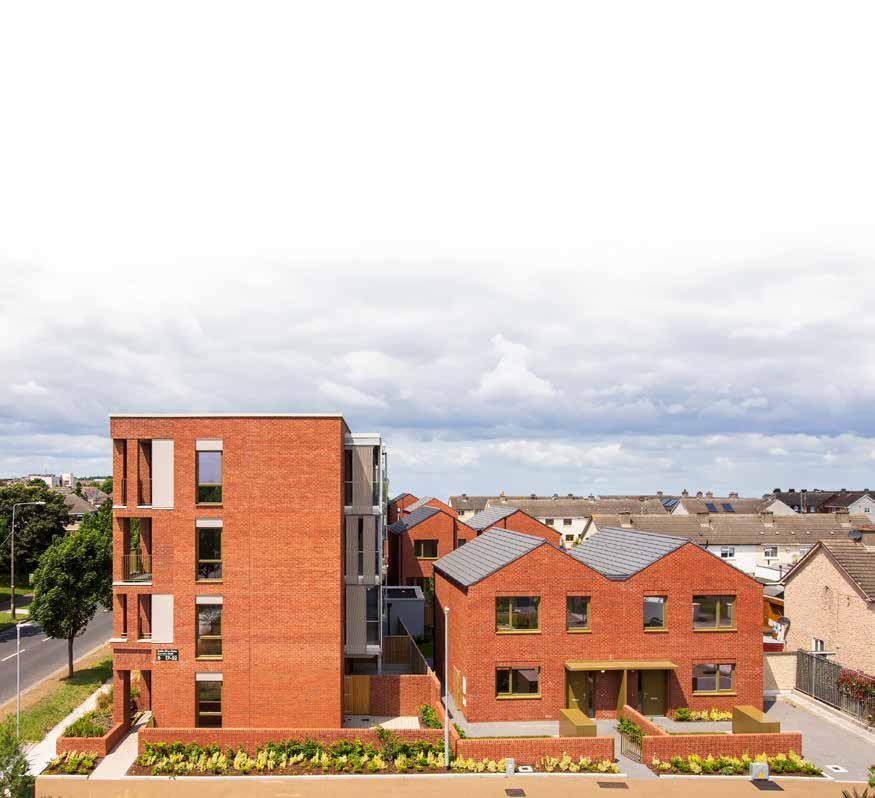
MORE THAN BOXES
Welcome to our special magazine section championing some recent projects and businesses operating across the volumetric modular space. As all observers and commentators of the offsite world will know the 3D volumetric sector has been under intense pressure and wider construction industry scrutiny over the last 18 months. But as all astute observers and commentators will know – irrespective of individual internal and various external forces – the problems have been primarily in residential construction.
Whilst volumetric modular has become synonymous with housebuilding, the healthcare and education sectors have been flying high, with countless successful projects being delivered at scale, on-time and on-budget to the highest standards.
This issue we have leaned towards the NHS and healthcare sector. We include a case study feature on the superb work being done by McAvoy for the University Hospitals Birmingham NHS Foundation Trust. As Richard Truman, Estates Development Manager at Trust points out, a modular solution was the right choice with the project delivered on-time with minimal disruption, something that was vital to the wards that were being installed in a live hospital environment. This is echoed by both Wernick Buildings and MTX – both businesses now vastly experienced in working within the pressures of clinical settings to deliver much needed new facilities.
Amongst some news and project snapshots, it was great to see that ZED PODS were awarded a King’s Award for Enterprise for Sustainable Development, for its work over many years now. Especially with their modular homes ‘unlocking constrained brownfield sites’ including derelict garage sites, carparks and flood zones. Alongside, the delivery of more SoloHaus homes for some of the most vulnerable in society, these are some of the unsung heroes of the volumetric sector that don’t grab all the bigger construction industry headlines.
OVERLEAF…
04 06 08 10 14
MCAVOY
A case study of the outstanding work at the University Hospitals Birmingham NHS Foundation Trust where the SmartCare® modular solution was tailored to meet the requirements for two 48-bed wards at two hospital sites.
WERNICK BUILDINGS
Situated within the Southmead Hospital estate in North Bristol, additional office accommodation was required to alleviate space constraints for much-needed clinical space. The seamless integration of volumetric methods did the trick.
ZED PODS
ZED PODS was honoured with a King’s Award for Enterprise for Sustainable Development 2024 for pushing the boundaries of sustainability in design, location, land use and social inclusion for the UK public sector.
MTX
An innovative development at Clatterbridge Hospital has provided four new Ultraclean theatres and 18 first stage recovery beds in the Cheshire & Merseyside Surgical Centre, and with volumetric help was completed in two phases simultaneously.
SOLOHAUS
The latest development of purposebuilt modular homes to provide secure, comfortable living as followon accommodation to local people progressing out of emergency housing, has seen 18 homes craned in on part of Tregunnel Hill car park in Newquay.
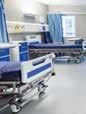
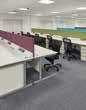


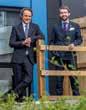
FRONT COVER:
McAvoy - Good Hope Hospital
TRANSFORMING HEALTHCARE WITH MODULAR SOLUTIONS
McAvoy is at the forefront of delivering innovative modular solutions to alleviate the burden on healthcare facilities. Its work at the University Hospitals Birmingham NHS Foundation Trust (UHB) has proved just how vital this construction strategy can be.
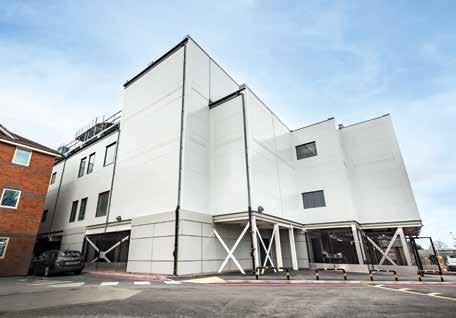
UHB is one of the leading NHS trusts in the UK, employing over 20,000 staff across multiple locations. Faced with an urgent need for additional ward space at Good Hope Hospital and Heartlands Hospital, UHB turned to McAvoy for a fast and efficient solution.
McAvoy's offsite solution was chosen due to being able to meet the pressing need for new wards quickly and with minimal disruption. Traditional construction methods would have taken considerably longer and caused significant site disruption, particularly challenging in a live hospital environment. The offsite solution ensured that the new accommodation at Good Hope Hospital was operational in just 14 weeks from the delivery of the first module, and 18 weeks at Heartlands Hospital.
The flexible choice
For UHB, a long-term rental solution was the preferred choice. This approach alleviated the need for
1substantial capital expenditure, providing a tailored financial solution that was both flexible and economical. McAvoy’s SmartCare® rental option offered the Trust a long-term managed service agreement, and the ability to extend the rental period if needed, providing increased flexibility in business planning. This model also allows for potential relocation or repurposing of the accommodation within the current site or at another Trust location in the future.
Tailored modular solutions
McAvoy's SmartCare® modular solution was tailored to meet UHB’s requirements for two 48-bed wards at both hospital sites. The modular buildings were designed to optimise space and included essential link corridors to existing hospital buildings. Each two-storey building comprised a 24-bed ward on each floor, along with ancillary areas such as utilities, staff rooms, nurses’ stations, reception areas, and toilets.
Due to the site’s proximity to Good Hope Hospital’s emergency department, McAvoy developed a detailed transport and logistics plan and scheduled module deliveries at night to ensure disruption was kept to a minimum. The building’s design also allows for future adaptability, ensuring the spaces can be repurposed or relocated as needed, providing longterm value and flexibility.
Sustainability at the forefront
McAvoy's SmartCare® modular buildings are designed with sustainability in mind. The new accommodation at Good Hope Hospital achieved near-passive levels of airtightness, an impressive feat for a two-storey building. Enhanced energy and fire protection standards were also achieved and independently verified, providing UHB with a sustainable and adaptable space solution. The focus on sustainability aligns with the NHS’s broader goals of reducing its carbon footprint and improving energy efficiency.
Versatility and quality
McAvoy’s SmartCare® solution offer versatility, being suitable for various applications including clinical and surgical spaces, medical wards, treatment rooms, consultation rooms, laboratories, and GP facilities. The range incorporates the latest in technology-led and compliant design, ensuring enhanced thermal performance, superior airtightness, and U-values that exceed current performance requirements. The modules come in three compatible and interchangeable sizes, up to three storeys high, offering significant design versatility.
This versatility is a critical advantage in the healthcare sector, where the needs can change rapidly.
2
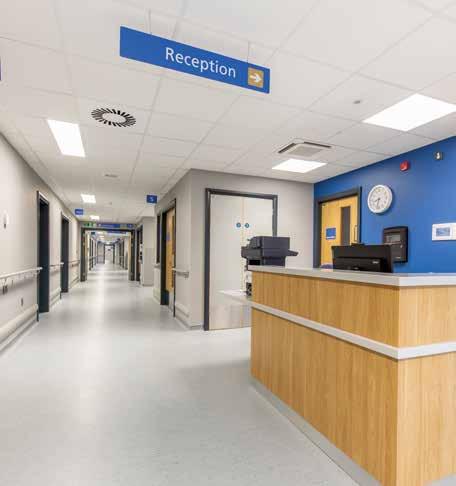
The ability to adapt and reconfigure spaces as needed ensures that the Trust can respond to evolving demands without the need for extensive new construction.
This adaptability also extends the lifespan of the modular units, making them a sound investment for the future.
Real life success stories
The successful delivery of the modular wards has been well-received by UHB. Richard Truman, Estates Development Manager at UHB, says: “The delivery of two 48-bed wards to the University Hospitals Birmingham NHS Foundation Trust by McAvoy has enabled us to provide much-needed additional care to our communities. A modular solution was the right choice for us due to the need for additional ward space at both Good Hope Hospital and Heartlands Hospital following the impact of the COVID-19 pandemic. The projects were delivered on time with minimal disruption, which was vital to us as the wards were
being installed in a live hospital environment.”
John Cunningham, Principal Category Manager at NHS Shared Business Services, added: “The NHS Shared Business Services Modular Buildings Framework was created to provide NHS Trusts with the options they need to offer effective patient care. The delivery of two 48-bed wards to the University Hospitals Birmingham NHS Foundation Trust by McAvoy is an example of that being put into practice. The SmartCare rental service that McAvoy has provided to the Trust allows for both stability over a 10-year period, as well as the flexibility to relocate or repurpose the accommodation over that timeframe.”
A future solution for the healthcare sector
The collaboration between McAvoy and UHB has delivered critical infrastructure improvements with speed, efficiency, and cost certainty. The modular solution not only met the immediate needs of the Trust but also provided a flexible and adaptable space for future requirements.
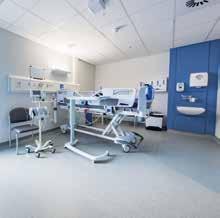
3 4
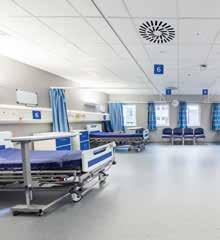
This project stands as a testament to the innovative and practical solutions that modular construction can offer to the healthcare sector. The successful and rapid delivery of these modular wards highlights the potential for similar approaches to be adopted across the NHS, providing a blueprint for efficient, sustainable, and flexible healthcare infrastructure development.
Tomas McNicholl, Senior Contracts Manager at McAvoy concludes: “Our work with UHB demonstrates the transformative potential of modular construction in healthcare. By delivering high-quality, sustainable, and adaptable solutions quickly, we can help meet the urgent needs of healthcare providers while setting new standards for the industry.”
For more information visit: www.mcavoygroup.com
Images: 01-04. The work at UHB goes to show how important volumetric modular construction is to the healthcare estate
IMPROVING HEALTHCARE SPACES WITH MMC
As a leading provider of modular building solutions in the UK, Wernick Buildings offers many innovative and sustainable construction options across various sectors, with healthcare now a vital area of development.
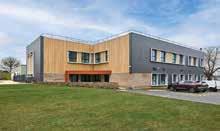
Over the past twelve months, Wernick Buildings has delivered a variety of different projects, from fully functional hospital wards and theatres to staff accommodation. However, they are proud to showcase the successful completion of the executive offices at Southmead Hospital. This project demonstrates excellence in efficiency and innovation with a sustainable approach to construction over traditional building techniques.
Situated within the Southmead Hospital estate in North Bristol, the executive offices stand as a testament to the seamless integration of modular construction methods with the stringent requirements of a healthcare environment. The project, a collaboration between Wernick Buildings and the hospital, aimed to provide modern executive office facilities that meet the highest standards of functionality and comfort to create an environment that fosters productivity for all occupants.
The objective of this project was to create additional office accommodation to alleviate space constraints on the main site, thereby facilitating the conversion of the vacated area into a much-needed clinical space. The newly constructed building serves as the base for executives and support staff, with the first floor dedicated to the executive team.
Rakesh Sandhu, Sales Director of Wernick Buildings, says: “Leveraging Wernick's expertise in modular
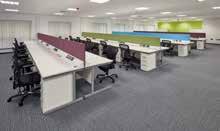
2 3
construction, the project achieved remarkable success in meeting the objectives required by the healthcare estate. This is now the second building provided by Wernick at the Southmead facility and we are thrilled to be able to provide yet another office building.” Additionally, Wernick Buildings are proud to announce that the Southmead offices won this year's MMC award, for the Healthcare Project of the Year Award.
A more sustainable approach to construction
One of the key highlights of the project is its emphasis on sustainability. By employing offsite construction methods, Wernick minimised waste, reduced carbon emissions, and optimised resource utilisation, aligning with Southmead Hospital's commitment to their environmental roadmap.
The nature of modular construction allowed for rapid assembly and installation, ensuring minimal disruption to hospital operations. By building modules in their manufacturing facility in South Wales, it ensured very little disturbance on-site. The collaborative working methods employed throughout the project underscored the commitment of both Wernick Buildings and Southmead Hospital to deliver excellence.
With the completion of the Southmead Executive Offices project, Wernick Buildings reaffirms its position as a trusted partner in delivering bespoke modular building solutions that exceed
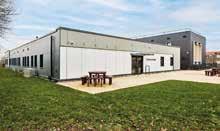
client expectations. Martin Crandon, Head of Capital Projects said: “We are delighted with the welcoming, light and open interior environment, which has exceeded our expectations. Comments from staff have all been very positive.”
More than just a box
Modular buildings are constructed in a controlled factory environment, adhering to strict quality control measures. This results in consistently high construction standards and superior craftsmanship. Additionally, the factory settings allow for meticulous attention to detail and greater accuracy during the building process. By employing these prefabricated structures, guarantees long-lasting and durable buildings to future-proof any project.
When considering a modular office building, it’s a common misperception to draw certain assumptions. You might conclude the idea that a modular building is ‘just a box’. However, modular construction offers the versatility to embrace contemporary, customised designs that enhance your workspace, aligning it with your specific requirements.
This year marks a significant milestone for Wernick as they celebrate their 90th anniversary in business, a testament to their enduring commitment to deliver successful projects. For
ARK HOUSING APPOINTS CONNECT MODULAR FOR PENICUIK SCHEME
Connect Modular and Ark Housing Association have announced proposals for the development of 12 new, affordable, cottage flats on the site of a former care home at Windsor Square, Penicuik.
Following demolition of the former care home and a competitive tender process, Ark Housing Association has appointed Connect Modular as the main contractor for the redevelopment of this brownfield, infill site.
Connect Modular delivers volumetric modular construction and will build the homes at their manufacturing facility in Cumnock, Ayrshire. The houses will be transported to the site with approximately 90% of the construction work already completed, significantly reducing disruption to the local community. This innovative construction method also offers numerous environmental benefits and ensures the new homes are delivered to exacting quality standards. The development will provide two, one bedroom and ten, two-bedroom cottage flats for social rent, designed to fit with the local context and
retain an area of open space. Each new home will also benefit from air source heat pumps and PV panels.
Jennifer Higgins, CEO at Connect Modular, said: “We are thrilled to have been appointed by Ark Housing Association on this exciting development and demonstrate the advantages of our volumetric modular construction process to overcome challenges of redeveloping brownfield, infill sites. We are proud to progress our first development in Midlothian and deliver much-needed housing opportunities for the local community in Penicuik.”
Caryn Innes, Director of Development and Customer Experience, added: “We have been working closely with Connect Modular over the last few months to finalise development proposals for this site, and we’re excited to be moving forward to a site start in late summer. Connect Modular’s volumetric modular construction process provides a fantastic delivery model for this restricted site. The offsite construction and associated reduced on-site construction programme will minimise disruption in the local area. We’d like to thank the Scottish Government for providing over £1.5million in support of the
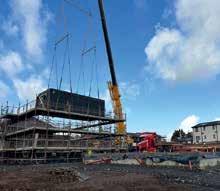
project through a combination of direct grant and a donation from its Charitable Bonds programme. When complete, the new energy efficient homes, will provide much needed affordable housing in the Penicuik area.”
With planning permission granted, works for this development will commence this summer with the new homes scheduled for handover to residents during the winter months.
Source: www.connect-modular.co.uk
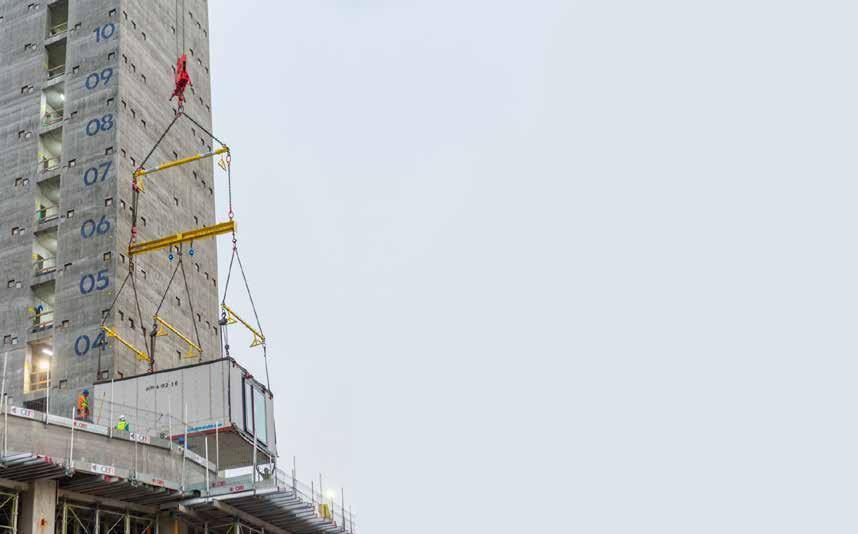
Britlift are a designer and manufacturer of lifting equipment, specialising in the lifting of modular homes, bathroom pods, commercial modules, containerised structures and pre-cast components. With a wealth of experience in the design and manufacture of lifting frames and lifting systems to the Offsite Construction sector, Britlift are the Offsite sector partner of choice.

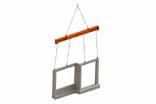

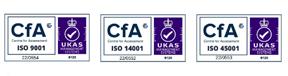
VOLUMETRIC MODULAR
TIDE GET READY FOR HASTINGS ROAD
Leading volumetric developer Tide has secured a resolution to grant planning permission for their Hastings Road scheme. The development will transform the underutilised retail site into a vibrant mixed-use development, delivering 412 new student homes with communal and commercial spaces together with public realm enhancements.
Located at a major junction adjacent to West Ealing underground station, the new student homes will alleviate pressure on the local housing market while driving new activity to the site by providing commercial space and an improved public realm.
The project will be delivered using Tide’s innovative volumetric technology, which involves precision-manufacturing volumetric units before assembling them onsite. This approach is proven to reduce construction programmes by up to 50% while also cutting embodied carbon. It also minimises onsite disruption, logistics and defects. The volumetric units are built in controlled factory settings by Tide’s sister company, Vision Volumetric.
The development has been designed around an external courtyard space at the heart of the site to complement students’ lifestyles. Additionally, residents will benefit from the scheme’s extensive and thoughtful amenity spaces, designed to ensure a welcoming and nurturing living environment for students. The plans also feature a biodiverse roof and photovoltaic panels, which add to the project’s environmental benefits.
Helen McManus, Head of Planning at Tide, said: “We look forward to breaking ground on Hastings Road and contributing to West Ealing’s vibrant urban fabric. This exciting project marks a significant new addition to Tide’s portfolio of student accommodation projects, and we would like to thank everyone involved in this process. Our proposal seeks to be an exemplar of student development, with high-quality living conditions and generous internal and external amenity space.”
Tide is a leading volumetric developer and contractor reshaping the way buildings are delivered. Its volumetric approach brings bespoke, iconic designs to life quickly, safely and efficiently, cutting construction time by up to 50% as well as reducing waste and carbon emissions. Working alongside its manufacturing company

Vision Volumetric under a vertically integrated procurement model, Tide has delivered highquality real estate in the UK with more than 3,000 new homes on-site in 2024.
Source: www.visionvolumetric.co.uk
ZED PODS ACHIEVES KING’S AWARD FOR ENTERPRISE
ZED PODS has been honoured with a King’s Award for Enterprise for Sustainable Development 2024. ZED PODS is one of 252 organisations nationally to be recognised with a prestigious King’s Award for Enterprise.
ZED PODS was recognised for its excellence in the Sustainable Development award category for pushing the boundaries of sustainability in design, location, land use and social inclusion for the UK public sector. A total of 257 Awards are made with five companies being recognised with two Awards. ZED PODS was founded by its Chairman Tom Northway in 2016. Their team of architects, engineers and operational team are leading the way in designing and building zero-operationalcarbon social housing.
Their modular homes are unlocking constrained brownfield sites including derelict garage sites, carparks and Flood Zones. ZED PODS have a
significant pipeline and are bringing sustainable development projects into fruition for local authorities and housing associations by using volumetric construction methodology.
Chairman Tom Northway said: “We are delighted to receive this prestigious award as sustainability is at the core of everything we do. By working in close partnership with public sector clients we are helping them to tackle both climate and affordable housing crises, whilst helping the most vulnerable people in our society.”
The King’s Awards for Enterprise, previously known as The Queen’s Awards for Enterprise, were renamed last year to reflect His Majesty The King’s desire to continue the legacy of HM Queen Elizabeth II’s by recognising outstanding UK businesses. The Award programme, now in its 58th year, is the most prestigious business award in the country, with successful businesses able to use the esteemed King’s Awards Emblem for the next five years.
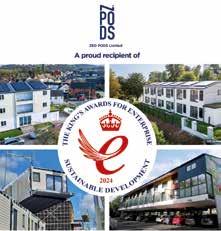
Source: www.zedpods.com www.gov.uk/kings-awards-for-enterprise
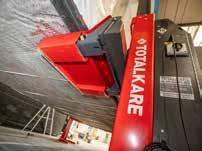


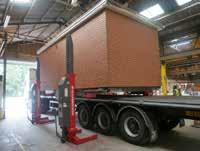
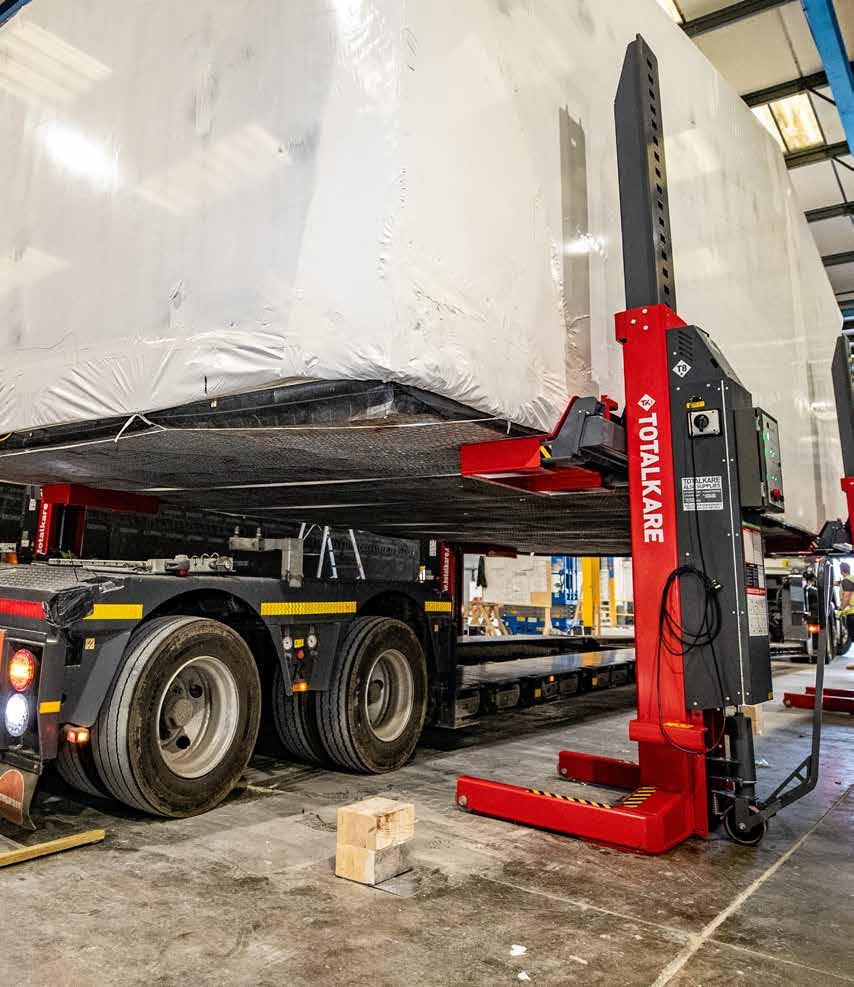

FUTUREPROOFING HEALTHCARE WITH MMC
A new community diagnostic centre (CDC) and surgical hub completed by MTX at Clatterbridge Hospital, Merseyside shows how volumetric design can deliver healthcare projects faster, greener, safer and more cost effectively.

The innovative development to the southeast corner of Clatterbridge Hospital has provided four new Ultraclean theatres and 18 first stage recovery beds in the Cheshire & Merseyside Surgical Centre, which was completed in two phases, whilst the CDC is equipped with a CT scanner and an MRI scanner, alongside staff accommodation and ancillary spaces. The development was completed in just over two years from conception stage to handover.
The first phase of the surgical centre opened in November 2022, with two operating theatres, 12 patient recovery bays and a rooftop plant room. In September 2022, new funding was allocated which allowed a second phase to build two additional
theatres. MTX commenced work on the extension before the first phase was handed over – working on the two projects simultaneously, which demonstrated the flexibility of their multi-platform approach.
Phase 2 of the surgical hub was carefully designed as a two-storey extension to ‘wrap round’ and integrate with the first phase, creating a coherent single building. With all four theatres operational, the new surgical centre can treat 6,000 extra elective patients a year. The centre is one of the national networks of elective surgical hubs created utilising NHS Targeted Investment Fund (TIF), with the aim of clearing the backlog of patients waiting for elective surgery post-pandemic.
The 450sq m single storey CDC is linked to an existing building on the hospital site. The CDC was constructed with 12 modular sections manufactured offsite and delivered for assembly with walls already in place. Once in situ, MEP and FF&E fit out commenced, along with the installation of specialist scanning equipment. A significant quantity of the services equipment was delivered in factory-built, skid-mounted sections for assembly on-site, aligned with the Government’s Construction Playbook and drive for DfMA delivery.
David Hartley, MTX Managing Director commented: “We are delighted that the Wirral University Teaching Hospital NHS Foundation Trust chose MTX to create the new CDC and provide
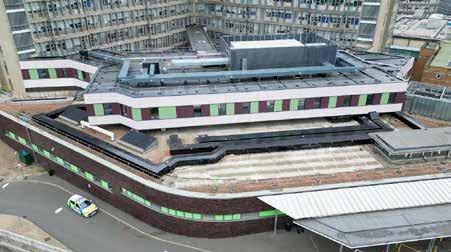
In the dynamic and ever-changing landscape of the NHS, development space is at a premium. At MTX, we offer innovative solutions that push the boundaries of healthcare construction onwards, upwards and outwards.
Our track record speaks volumes: from hospital extensions to repurposing clinical space, we navigate complexities with ease. Take our recent project in North London, where we added a 32-bed ward above the city's busiest A&E in just six months.
With minimal disruption to the existing operational space, our flexible, forward-thinking construction methodologies allowed operational and patient activities to continue seamlessly.
At MTX, we don't believe in one-size-fits-all solutions. Our tailored approach adapts to your unique needs, ensuring your vision becomes reality - whatever direction your project is heading in.
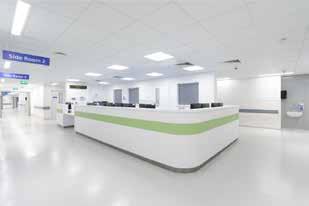

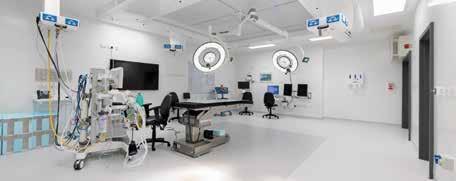
the additional diagnostic facilities. It continues our long-standing partnership with the Trust, which recognises that modern methods of construction (MMC) can deliver new facilities faster than conventional building techniques, whilst maintaining the highest quality.”
Adopting an MMC approach throughout the two-year construction schedule minimised disruption to
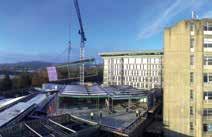
NORTHWICK PARK HOSPITAL
existing patient pathways, reduced the impact on clinical care, and ensured the entire programme was delivered on time and to budget. The new surgical hub and CDC will provide quicker access to surgery and outpatient procedures for thousands of people across Cheshire and Merseyside, improving the overall patient experience and ensuring better outcomes.

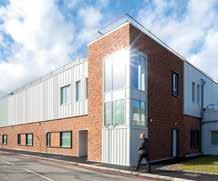
For more information visit: www.mtx.co.uk
Images:

A £20million 32-bed short-stay ward for Northwick Park Hospital has been created above London’s busiest A&E Department by MTX, in one of the most complex build programmes ever undertaken by the company.
A total of 32 modules were used to construct the new ward on a steel deck installed on existing concrete stub columns that were part of the original A&E department build. The challenging location in the middle of the busy hospital site required the use of one of Europe’s heaviest lifting tower cranes, around 40m high and with a ‘reach’ of 80m. Every component of the new ward had to be lifted onto the construction deck, including 200 tonnes of steel and almost 2,000 construction boards.
Project lead Ian Brook explains: “There were a number of critical factors that had to be considered throughout the build –working on top of London’s busiest A&E department, interacting with the public and staff, and ensuring the large number of deliveries and vehicle movements did not impact on the ambulance routes and access to the clinical areas.”
The new unit incorporates 32 short-stay beds and ancillary areas and is finished to the high-quality build standard that has established MTX as a leading supplier of new healthcare facilities. The programme included designing and installing mechanical modules pre-manufactured offsite to control the ventilation and the environment of the wards, with a dedicated integrated plant facility provided within the new building as part of the M&E specification.
The new first floor construction links to the existing hospital buildings via a 20m-long suspended connecting corridor. Two more 10m bridges link to existing stairwells to provide access for staff and visitors.
Northwick Park Hospital, situated on the outskirts of Harrow in North West London, is managed by the London North West University Healthcare NHS Trust. The new £20 million state-of-the-art short-stay ward is designed to enhance the quality of care provided to patients at Northwick Park and is part of an NHS England initiative to meet the growing demands for general and acute beds across the country.
Trust Chief Executive Pippa Nightingale said: “We have one of the biggest and busiest A&Es in the country, so this is a welcome and much needed addition to our capacity. It’s crucial to maintain flow through the hospital so we have enough beds. An enormous amount of work goes on behind-the-scenes every day to ensure this happens. The new unit will help us better manage this.”
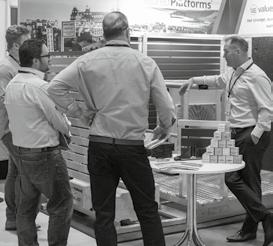
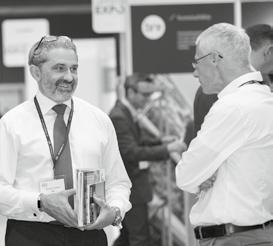
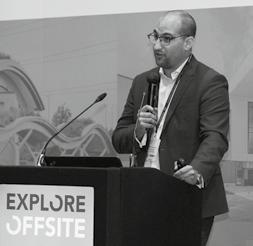
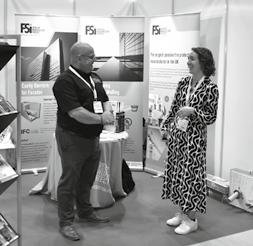
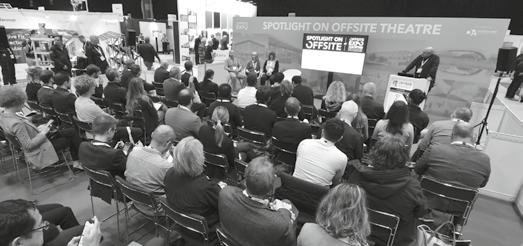
REGISTER
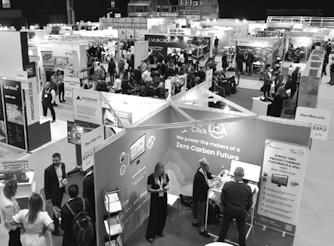
30+ HOURS CPD MASTERCLASSES
35 SPEAKERS IN THE OFFSITE SUMMIT EXHIBITORS 130+
75+ BUYERS OFFSITE CONNECT FORUM 10 TH OFFSITE AWARDS ANNIVERSARY
5000+ VISITORS INNOVATION HUB CHALLENGE

RESIDENTS MOVE INTO NEWQUAY SOLOHAUS
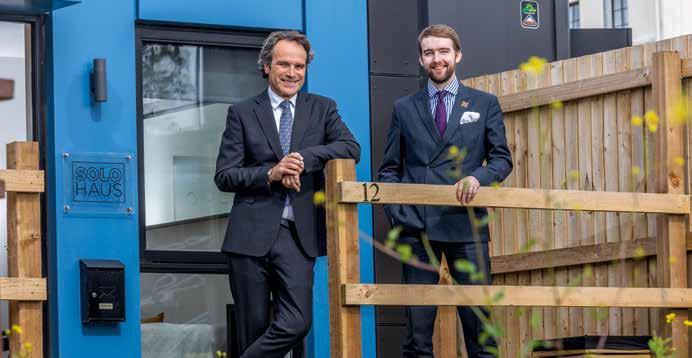
A new development of 18 purpose-built SoloHaus modular homes on part of Tregunnel Hill car park in Newquay has been opened to its first new residents.
Each development provides modular homes with outside space, utilising low carbon heating technologies. The homes are specifically intended to help those with a history of homelessness who are ready to move on from emergency accommodation or other provision and will help reduce the need to place people in expensive, nightly-paid hotels and bed and breakfasts.
Olly Monk, Cornwall Council Portfolio Holder for Housing and Planning said: “This latest scheme is part of a plan for this part of Newquay to not only provide excellent quality accommodation for single people who would otherwise be homeless, but to also revamp the car park here at Tregunnel Hill and put in measures to deter unauthorised encampments which has been an issue here in the past.
“These modular SoloHaus homes provide excellent quality accommodation for single people who would otherwise be homeless. It means that we have a stock of good quality homes that people can live in for a short period on dedicated sites, whilst they get the help and support, they need to secure a permanent home. We are helping residents live nearer to where they want and need to be, with the security of knowing this home is theirs until a permanent one can be found.”
Following a landmark deal with award-winning housebuilder The Hill Group, Cornwall Council has bought SoloHaus homes to provide secure, comfortable homes as follow-on accommodation to local people as they progress out of emergency housing, helping them regain their independence. The specially designed modular homes, manufactured by VOLUMETRIC®, provide a safe, comfortable, and independent space for residents and arrive fully furnished, ready for installation onto a pre-prepared site. Designed to house single people, the homes have a 60-year lifespan and are built to Future Homes Standards, exceeding building regulations for energy efficiency and sound insulation.
Following on from the first SoloHaus development in Truro, this second scheme at Tregunnel will be complemented by two more under construction – one in Penzance and one in Penryn - and is developed as a ‘move on’ site to provide safe and secure homes for people in urgent housing need. Rory Lowings, Project Manager for SoloHaus at The Hill Group added: “We are proud to be working in partnership with Cornwall Council to provide purpose-built homes for people at risk of homelessness. SoloHaus is an ideal housing solution for Cornwall, as it delivers high-quality accommodation that can be deployed quickly. I am delighted to see these next 18 specially designed modular homes in use as the first residents move in and I’m confident they will have a positive impact on people’s lives for many years to come.”
A portable solution, SoloHaus is designed to be deployed permanently or on a temporary basis and can be disconnected from services easily and moved to other sites. The Tregunnel Hill development will be managed by Cornwall Housing Ltd who will provide all of the housing management functions, ensuring the smooth operation and maintenance of the homes and the site.
Karen Centini, Specialist Services Team Leader at Cornwall Housing, said: “We are proud to manage these homes and support residents as they transition to a more stable future. The new micro-homes not only provide immediate relief for those facing homelessness but also offer a solid foundation for residents to rebuild their lives. This development represents hope and opportunity for those in urgent housing need, and we look forward to witnessing the positive impact it will have.
Harbour Housing will be providing tenancy sustainment support, helping residents to integrate into their new homes and maintain their tenancies successfully. There are currently over 800 households living in temporary or emergency accommodation across Cornwall with nearly 100 people in Newquay alone, so this scheme help will help around 20% of those.
(L-R) Olly Monk, Cornwall Council Portfolio Holder for Housing and Planning and Rory Lowings, Project Manager for SoloHaus at The Hill Group.
Source: www.solohaus.co.uk www.volumetric.co.uk

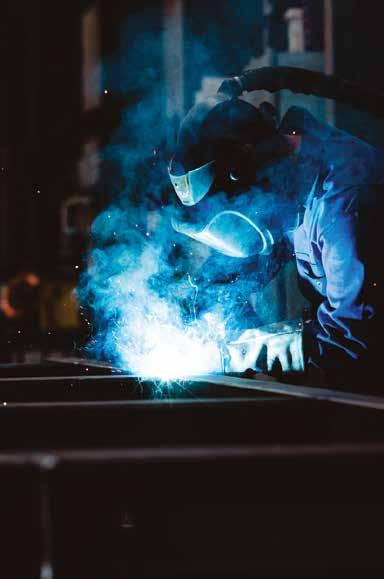
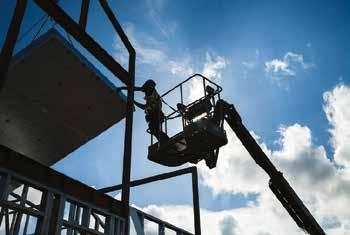
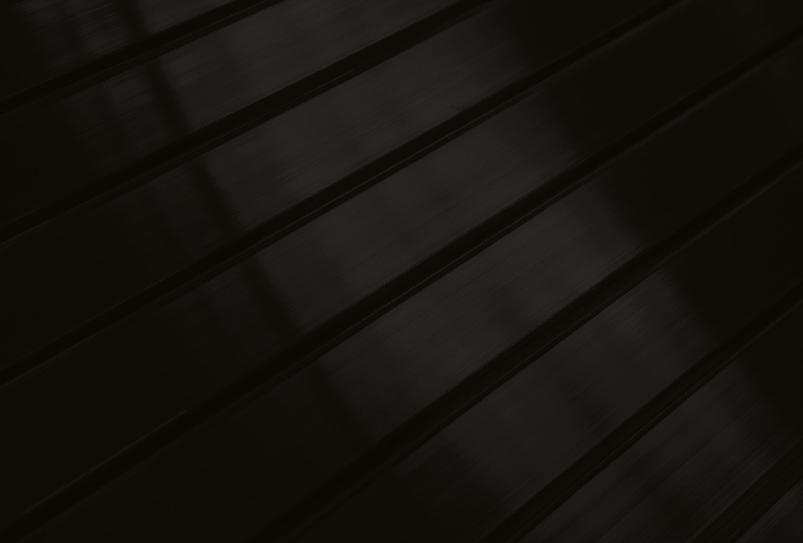








VOLUMETRIC MODULAR
CASTLEMERE DEVELOPMENTS DELIVERS ITS FIRST AIRSPACE DEVELOPMENT
Castlemere Developments has completed its first major airspace project – delivering an 11-unit scheme in Tunbridge Wells. The Windsor-based company, which has primarily focused on ground-up developments and property refurbishments, has expanded into the airspace development sector and has a range of projects in the pipeline having completed this first project in Kent.
All Castlemere Developments focus on using the latest smart home technology and modern methods of construction (MMC) to deliver costefficient and environmentally friendly residential properties. The company was founded in 2017 by Kris Collett and Duncan Cooke, who have more than 35 years combined experience in the property development and construction sector.
The scheme at Hamilton Court, located on Chilston Road, features five two-bedroom and six one-bedroom apartments. Each apartment will deliver aspirational and affordable modular penthouse living. Prices for a one bed will be from £210,000 and £280,000 for a two bedroom.
Each apartment offers premium designer kitchens complete with Bosch appliances, quartz worktops, fully tiled bathrooms and oak flooring. Heating is provided via heat pumps to ensure no carbon burning appliances are used. In addition, each apartment has fibre broadband and assigned parking with dedicated electrical vehicle charging.
Hamilton Court has been built offsite, with Castlemere Developments embracing the modern methods of construction (MMC) approach with all of its properties before lifting them into place for the finishing touches. It has purposely chosen offsite modular so that it can deliver projects much quicker than on-site developments, reduce the disruption to current residents, and to ensure its developments are as environmentally friendly as possible.
Kris Collett, Managing Director of Castlemere Developments, said: “Hamilton Court is a stunning addition to the residential property market in Tunbridge Wells. We are incredibly pleased with it. Our plan was to deliver stylish, environmentally friendly accommodation which we have achieved. We have chosen to adopt MMC best practices for this scheme – and future ones. This is more cost effective, quicker and also, we believe that building airspace apartments offsite is less

complex. There is a huge demand for residential properties, and we will continue to source suitable locations that we can develop to help meet this need.” The company has said it will adopt MMC for all of its projects from new developments to refurbishments.
Source: www.castlemere-developments.co.uk
MODULAR PODS DROPPED INTO NORWICH HOSPITAL
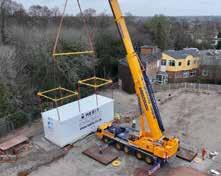
Cramlington-based Merit has transported its first Air Handling Unit (AHU POD) to the site delivering a new therapy-led rehabilitation unit at Norwich Community Hospital. Weighing 20.5 tonnes, Merit’s AHU POD is the first offsite component of the building to be delivered, after travelling 300 miles from the North East to Norfolk.
Earlier this year, Merit announced the multimillion-pound project with Norfolk Community Health and Care NHS Trust. By utilising its 4D BIM modelling technology and using the new V6 UltraPOD® SFS Variant, Merit’s expert team can deliver the new unit by August 2024, guaranteeing a faster, more cost-effective project schedule with sustainability in mind.
The project will be the first of its kind using Merit’s new V6 UltraPOD® SFS Variant, an extension to the already effective UltraPOD®, which has been successfully deployed to other healthcare, biotech and pharmaceutical facilities across the UK, including Berwick’s long-awaited new, 10,500sq m, £35million community hospital and Solihull Hospital’s new Elective Hub (Operating Theatre Block).
To meet ever changing and increasing demands, the V6 UltraPOD® SFS Variant utilises Merit’s latest roll former, panel line production system to enhance affordability and accessibility through a significantly reduced programme. The V6 platform comes as standard, rated BREEAM Excellent as
a minimum, EPC-A, and energy consumption is 69% lower than the current CIBSE hospital benchmarks. When complete, the facility will house 48 beds across a mix of single and fourbedded bays, as well as treatment areas, an assessment kitchen, a self-service café, and a reception area.
Tony Wells, CEO at Merit said: “We’re delighted to be working collaboratively with Norfolk Community Health & Care NHS Trust to deliver this new facility, which will bring improved healthcare services to the local community. The successful delivery of our AHU POD from our Cramlington factory to Norwich Community Hospital represents our commitment to delivering high-quality healthcare facilities efficiently and sustainably, while working within the healthcare sector to deliver bespoke solutions that meet local need and make a tangible difference to the community. At Merit, sustainability is at the heart of everything we do and we are very proud as we continue to optimise our product offering, so that we can provide the go-to choice for swift and efficient project delivery.”
Source: www.merit.co.uk



















FALK, your first choice for insulated panels! Trusted by MMC buildings in Ireland and the UK. Quality, innovation, and reliability guaranteed. Let’s elevate your next project with FALK panels!
FALK, clever construction for a circular future.
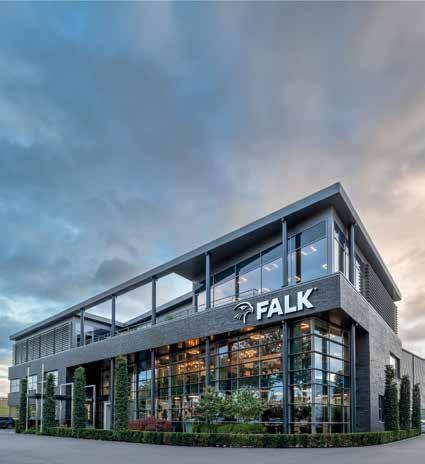
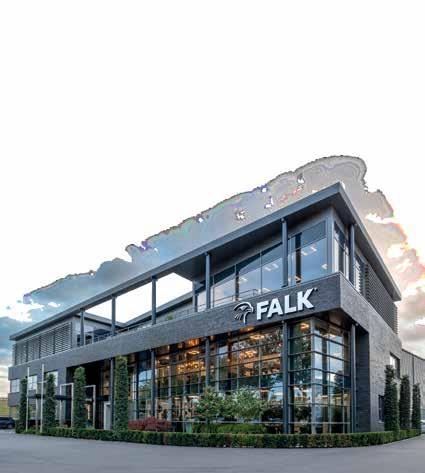
Truly circular with CradleCore®
Introducing CradleCore®: FALK’s breakthrough in panel recycling for sus tainability. Achieving circularity, we reu se and recycle steel and PIR components. Lower EPD by 40% compared to market average. Choose FALK for eco-friendly building solutions!
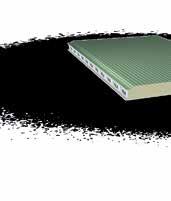
DATES FOR YOUR DIARY 2024
If you are interested in learning more about offsite construction and the associated manufacturing processes then the following industry events may be of interest:
the iconic projects from across the offsite sector, the Offsite Awards showcase the people and businesses pioneering the new technology, building methods, systems and designs raising the standards of safety,

The Laing O’Rourke Centre of Excellence for Modern Construction, is Europe's largest and most advanced pre-assembly manufacturing facility. This is your opportunity to discover more about their modern processes of assembly, using lean automation and quality assurance systems.

Constructed
Witness first-hand the production of prefabricated high-performance panels engineered for loadbearing capacity, structural integrity, thermal efficiency, fire resistance, and acoustic performance. The tour will be followed by technology presentations and a Q&A.


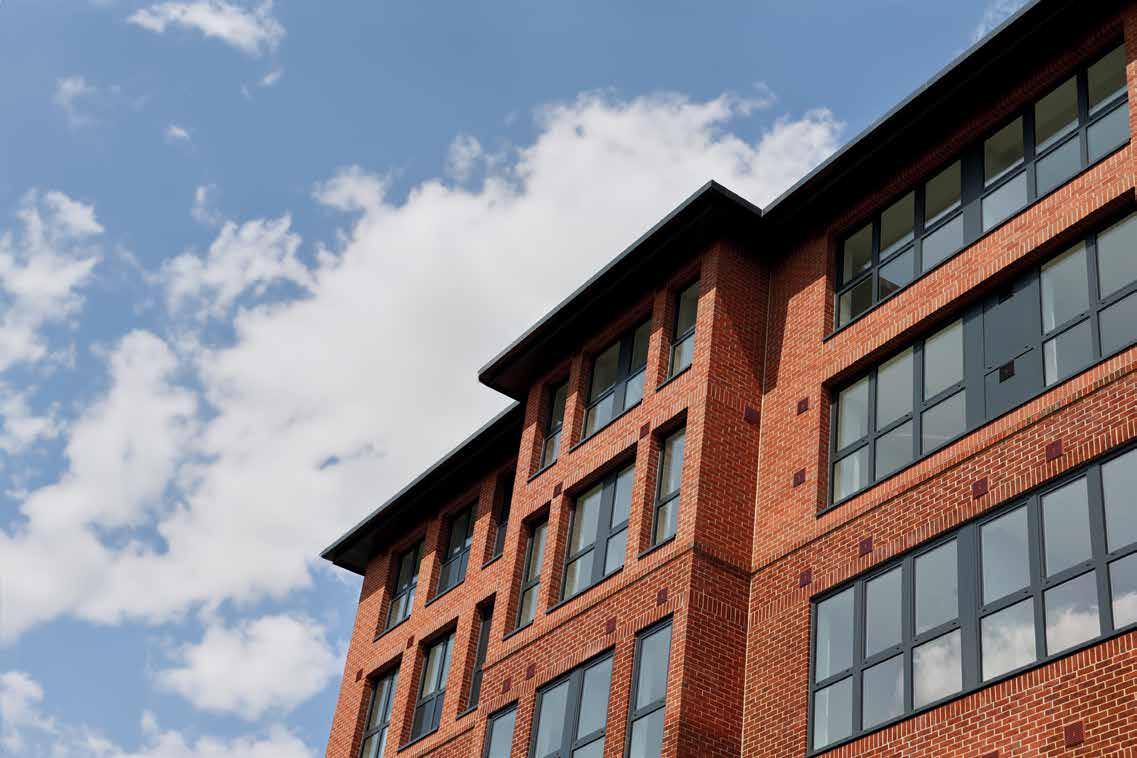

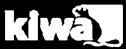

SLIPFAST® Mechanical Brick Slip System
SLIPFAST® offers the timeless beauty of fired clay brick, whilst being durable enough to stand the test of time. Designed with both new build and recladding applications in mind, Slipfast is suitable for high rise and low-rise construction.
Engineered to perform
An A fire-rated, mechanically-fixed clay brick slip system, designed for modern methods of construction. SLIPFAST® provides a high performance façade and enhancing a building’s overall energy efficiency.
Designed to last
A mechanically fixed clay brick slip system, designed for modern methods of construction, Slipfast has a stainless-steel core, which has a certified system life of in excess of 60 years.
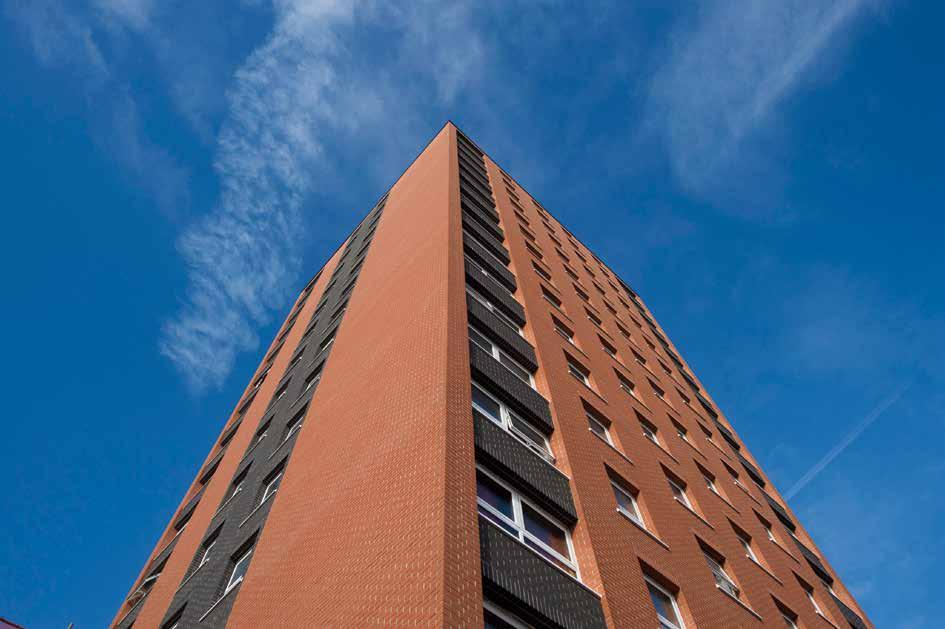
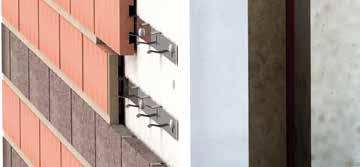
