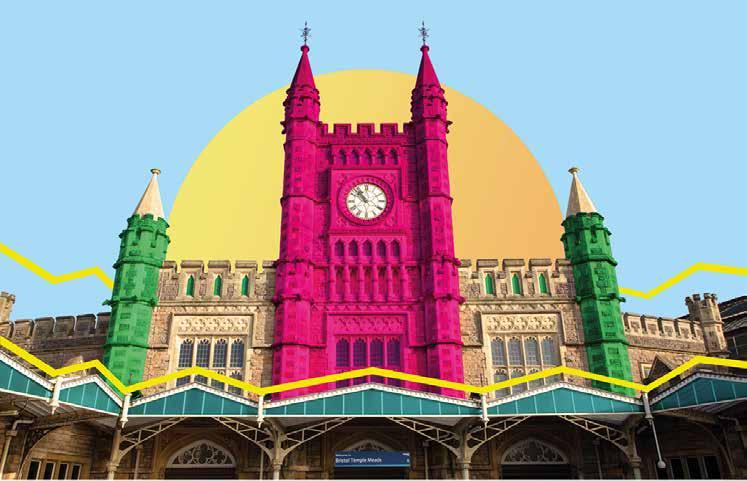
17 minute read
Regeneration begins at Bristol Temple Meads
BOB WRIGHT Over Christmas, a substantial amount of work was delivered in and around Bristol’s Temple Meads station. This included important elements of the long-term Bristol Rail Regeneration programme, which is itself linked into Bristol City Council’s Temple Quarter Regeneration.
As part of its wider regeneration programme, Bristol City Council is developing a sustainable urban quarter - Temple Quarter - as a place to live, work, study, enjoy leisure time and build on Bristol’s strengths as a world class city. Marvin Rees, Mayor of Bristol, commented: “With Temple Meads station, the largest transport interchange in the region, at the core of Temple Quarter, the City’s regeneration of the wider area alongside the station is a once-in-ageneration opportunity. It will bring about the long-awaited transformation of a key site in the heart of the city, creating 22,000 new jobs and around 10,000 new homes in proximity to significant areas of deprivation, and an economic boost of £1.6 billion per annum.”
The station is an important hub in the city’s transport network, especially for pedestrians and cyclists. Making improvements to Temple Meads station will feed into Bristol’s ambitions for cleaner air and carbon neutrality.
Bristol Rail Regeneration Programme
Over the next 2½ years, Temple Meads station will undergo a major transformation that will enhance customers’ experience of using the station as well as provide operational capacity improvements that will permit increases in train services and improved reliability.
The most obvious improvement will be the refurbishment of the 38-metre span Grade 1 listed roof, built in 1871-4. This will involve extensive repairs to the metal structure and timber panelling and the complete reglazing of the roof and platform canopies. The existing glazing is discoloured and dirty, restricting light access, leaving the platforms beneath with reduced natural light. This will be the first major refurbishment of the station roof in over 25 years and is due for completion in 2023.
Equally important, although less obvious to customers, is the remodelling of the crucial Bristol East Junction, between the four Filton Bank lines (leading to south Wales, Bristol Parkway and the Midlands) and the main lines (leading on to Bath Spa and London Paddington).
The junction is located just to the east of Temple Meads station and is mainly surrounded by industrial units and rail depots. When complete, the new junction will improve capacity, flexibility and reliability, making more efficient use of platforms at the station and reducing delays for passengers. An extra line is also being introduced, to support additional suburban services being planned for the future as part of the MetroWest Project.
The programme of improvements to the station will also include the complete rewiring of the station’s electrical system, to bring it up to modern standards. The work will improve the stability of the power supply at the station and allow for future expansion. Heating, ventilation and mechanical cooling will also be renewed and all lighting will be upgraded to energy efficient LEDs, designed by FJD Consulting.
Alongside the rewire, separate projects are being planned to bring a Wi-Fi network to the station, as well as enhanced passenger information through new customer information screens, improved public announcement systems and CCTV.
Finally, Network Rail, in collaboration with West of England Combined Authority, will create a new eastern station entrance that will provide direct access into a new University of Bristol campus on the old Post Office site, beside platforms 13/15, as well as to the wider east side of the city. The existing subway will be extended eastwards. Plans are in development, but the aspiration is to break through during this summer’s blockade, with a small ticket hall to be constructed later and completed in time for the opening of the campus in autumn 2023.
At an event to mark the 180th anniversary of the original Temple Meads station, Mike Gallop, Network Rail’s Western route director, talked about the Bristol Rail Regeneration programme, saying: “This is a great moment for Bristol and the whole West of England as we will be providing a brighter station for passengers, worthy of the original creator, Isambard Kingdom Brunel. Around 10 million passengers pass through the station each year. Once complete, our renovations in and around the station will bring a brighter welcome to the city, improving passenger experience and preserving our station for future generations.”
The original station at Bristol Temple Meads was opened as a terminus in 1840. This was significantly enlarged with the construction of the new ‘Joint station’ (GWR, Midland and Bristol & Exeter railway companies) in 1871-4. The station was further expanded to the East in the 1930s with additional platforms and a new passenger subway. The old station buildings were closed to rail traffic in 1965 and are now used as a carpark, corporate events space, retail and various business units.

Roof works
The £24 million refurbishment project will see Network Rail’s contractor, Taziker, repair and refurbish the 38-metre span, 153-metrelong trainshed roof, as well as further work on roofing over Bonaparte’s Alley and to the canopies on the platforms and in the forecourt. The works include restoring the original features, both within the main trainshed and on the canopy platforms. All works will be approved by Historic England. The two-year programme will involve extensive metal and woodwork repairs and the complete re-glazing of the roof and platform canopies. Bristol Temple Meads Platform 3.
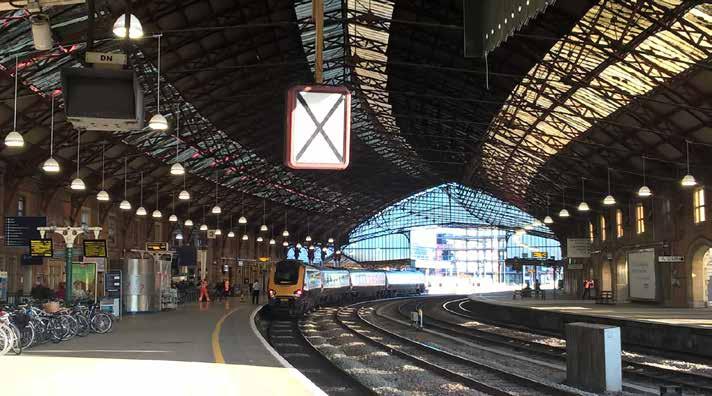
The scaffolding was designed to take account of voids and cellars under the station structure.
BIM model of Temple Meads based on 3D LiDAR scanning surveys.
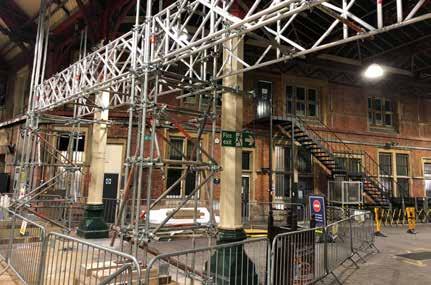
A 5,800 square metre access scaffold structure has been designed by RDG Engineering, with foundations and back-propping by FJD Consulting. Temple Meads station lies between two watercourses and there are challenging geotechnical conditions beneath the platforms, as well as a network of historic structures, cellars and other voids. To support the vast structure, each tower base’s foundation has been designed individually. Some locations have needed voids injection grouted, others require spreader structures.
Between Christmas Day and 11th January platforms 1-6 were closed to allow some towers to be erected by Network Scaffolding, Taziker’s scaffolding provider. These, and the decking above, will be completed with minimum disruption to passengers by working closely with GWR and other train operators, with COVID-19 service levels affording more opportunities for track access.
Taziker, will remove the existing glazing and grit blast the 130-year-old wrought and cast-iron structure. Network Rail’s designer, FJD Consulting, has prepared a suite of standard sympathetic repair solutions, agreed with Historic England. The preparatory design works were informed by previous periodic structural examinations and rope access inspections of the gable ends in 2018, as well as by the LiDAR survey. Any non-standard works needed will be designed as the works proceed and then agreed with Historic England’s representative, as will dealing with any unusual or unexpected historic feature than may be uncovered during the project.
To assist Network Rail’s asset management and conservation plans for the station, a 3D BIM survey was undertaken, based on 3D LiDAR scanning technology - the only viable solution to collect the vast amounts of data required of the complex and high access risk station buildings, tunnels, vaults, platforms, plant rooms and trainshed roofs. The BIM model will be used to record the condition, repairs and testing data for each element.
Timber cladding sections will be removed, refurbished and reused in order to maintain as much historic material as possible. New timber will be minimised.
The new glazing will be laminated glass in the train shed and Georgian wired effect GRP in the platform canopies and the trainshed gable ends.
The completed works will be painted in a heritage-based colour scheme.
The contract is good news for the Bristol economy, with a large workforce on site. Taziker has also committed to creating apprenticeships for local people; offering opportunities to work alongside their heritage project experienced teams.
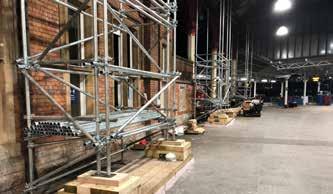
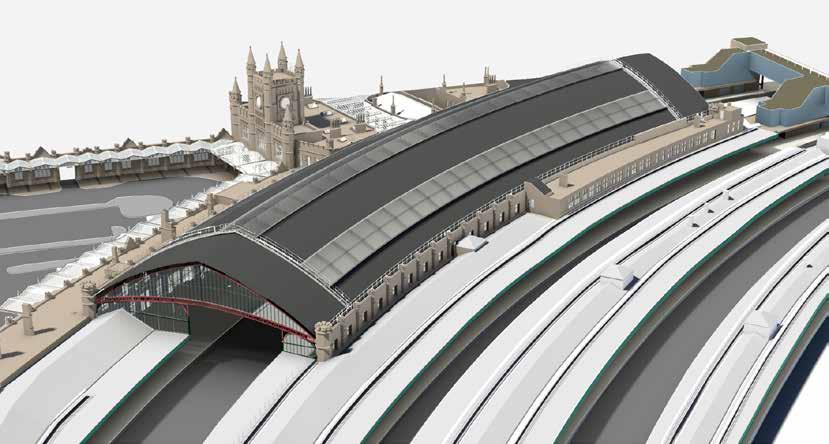
Christmas at Bristol East junction.
Installing the new gantry at Bristol East junction, 27 December 2020. Bristol East Junction
The renewal and improvement of the 50 pointends at Bristol East junction began in March 2020 and will be completed during an eightweek blockade in July to September 2021. The design of the new layout was by AECOM.
During a possession over Christmas Day that lasted until 28 December, the South Rail Systems Alliance (Network Rail/Colas Rail/AECOM) replaced five point ends in the Up and Down London lines and the Down Filton Main.
The new components were delivered loose to Network Rail’s Kingsland Road Depot and there built up into panels.
The 1,200 tonnes of old ballast, rails and sleepers were removed by road-rail excavators and loaded onto engineering trains for offsite recycling. New ballast was brought to site in engineering trains - 600 tonnes of bottom ballast and 600 tonnes of top.
The new panels were transported and placed using a combination of a Kirow crane and Geismar PEM-LEM sets. Following the electrical works to switch heating and signalling works, two double-shifted tampers completed the trackwork and ensured an on time handback at line speed.
The main blockade will see the replacement of remaining S&C to the new layout.
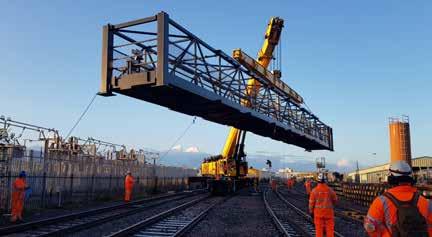
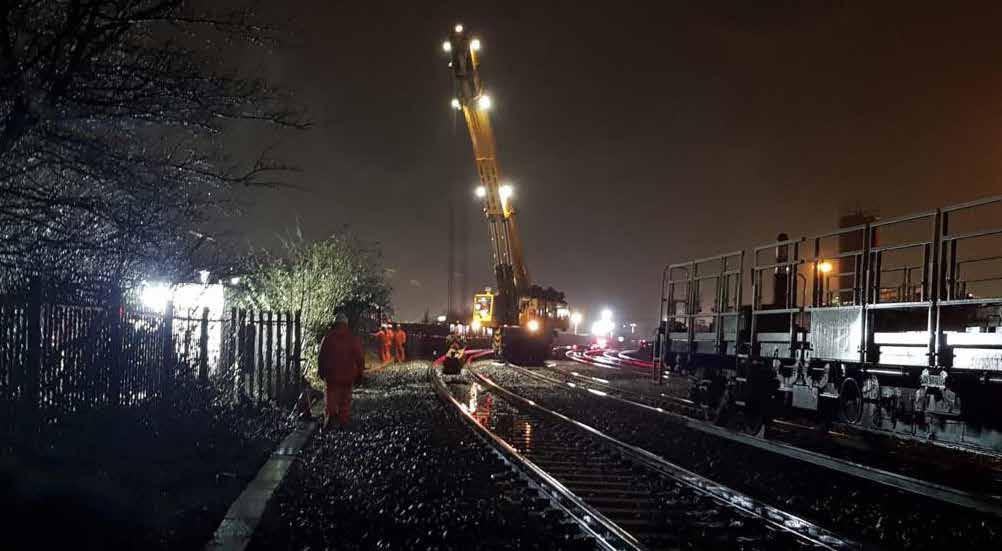
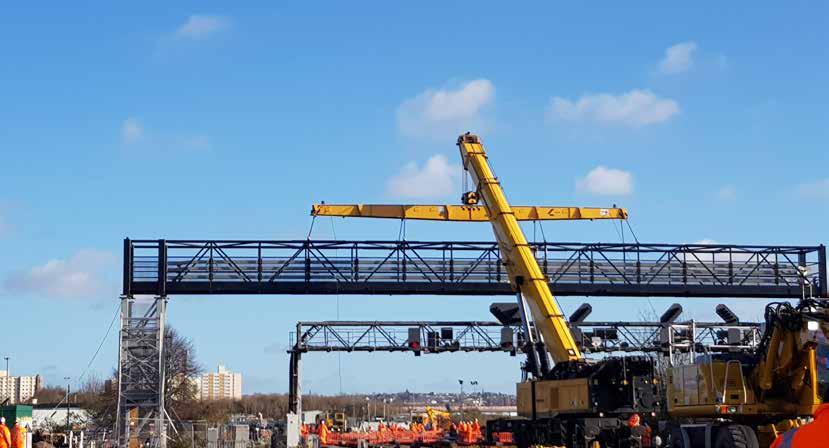
This work on strategic routes was time critical. A project contingency plan and an operational contingency plan were both in place to manage potential problems. Contingencies were made for plant and other problems with the onsite availability of a spare Kirow crane at the station, onsite fitters, spare plant, overlaps in working shifts, and the project operations manager on site.
To avoid a potential twelve-week summer blockade, many advance works have already been carried out, with four weekends of plain line and S&C renewal early in 2020. Other preparatory works included relocating signals and improving driver walkways. A substation and a relay room were demolished and replaced to accommodate foundations for a new gantry.
The Filton four-tracking project, completed in 2018, was an important enabler. It will not only allow the junction remodelling to achieve its full potential but will also reduce disruption to the travelling public, with two out of the four lines being kept open for a significant proportion of the blockade. A new five track span signal gantry was required beside Dings Park, to permit the summer’s installation of additional trackwork. This was built to electrification clearances in anticipation of the deferred completion of the electrification between Parkway and Temple Meads stations.
The gantry was delivered by AmcoGiffen, designed by FJD Consulting, and was fabricated and installed by Loughborough-based Adey Steel. The two towers were erected in rules of the route possessions during the autumn. The 20-tonne, 33.6 metre gantry span was delivered by road to Network Rail’s Queen Anne Road Depot in three sections and built up beside the Filton Down Main during the week before Christmas.
During the Christmas possession, a Kirow crane lifted the gantry span and placed it onto two rail trailers that were then towed by a road/rail excavator to the site, where the Kirow lifted it into place. The new gantry will remain beside the existing structure until the latter stages of the summer blockade, when signalling will be transferred to it and the old gantry demolished. The new gantry installed alongside the old one, which will be demolished in the summer.
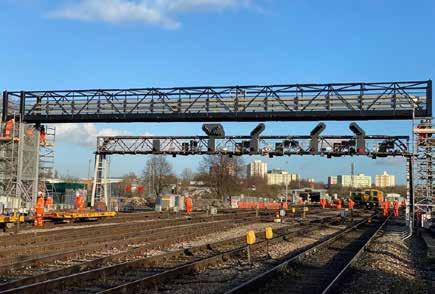
Confidential Reporting for Safety
This is Fred Fred’s workmate is cutting corners Fred doesn’t want to cause trouble Fred called CIRAS and his company gave a safety briefing Fred feels much safer now Be like Fred
The name we’ve used is fictional. We share your concern so the company can address it. You will not be identified.
Work environment
Rules & procedures Fatigue Welfare facilities Equipment
www.ciras.org.uk
Shift design Safety practices Training & competence
Rebuilding passenger confidence through digital technology
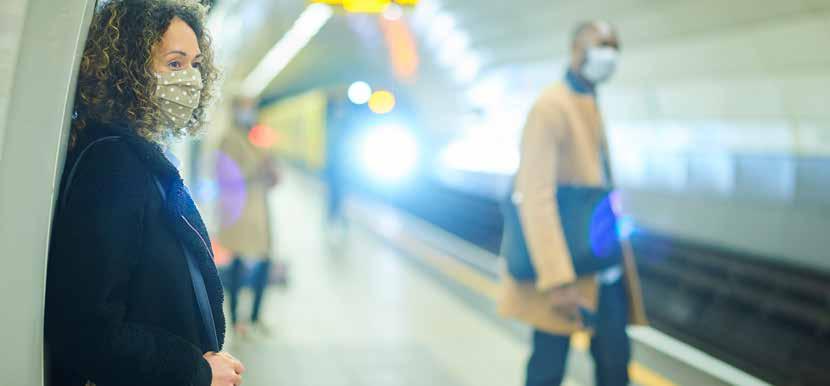
HELEN DAVIS Helping passengers travel easily and efficiently on public transport is a complex task, and one which has been made considerably more difficult by the COVID-19 pandemic. The global health crisis has had a major impact on our transport networks, with passenger confidence in public transport having been severely affected.
Rail passenger numbers fell sharply in spring 2020, with just 35 million passenger journeys made between April and June, compared to over 400 million during the same period in 2019. Whilst the expectation is that this figure will recover at some point, it remains highly likely that demand will remain below the previous peak for a considerable time.
As an industry, it is our job to do everything we can do to drive passengers back to public transport for the sake of the wider economy, for the mental health and development of our employees, and to support the government’s decarbonisation agenda.
Although technology has helped enormously through the required lockdowns and periods of restrictions, everyone working from home five days a week is neither sustainable nor desirable for the economy, our people or our organisations in the long-term. Whilst there will be a new balance of home/office working, we need to be back at our places of work, spending money in our local communities and enjoying the benefits of face-to-face contact with colleagues, customers, suppliers and stakeholders.
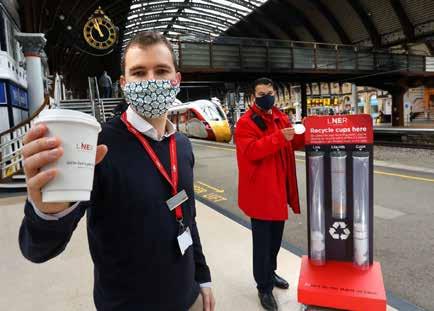
Contributing to decarbonisation
Getting passengers back on public transport is also an important element of the government’s decarbonisation agenda. We have seen that, when lockdowns in the UK were lifted, traffic in towns and cities surged, increasing congestion and air pollution. Rail is already a low-carbon form of transport, but it can go further. There are many contributors to decarbonisation, including electrification of the network, the reduction of carbon footprint on infrastructure through digitalisation and radio-based communications, the deployment of hybrid and battery trains, more efficient energy use and introduction of traffic management. And, of course, we have a major role to play in encouraging the modal shift of passengers from cars onto public transport.
Siemens Mobility is a major contributor across all facets of decarbonisation of the transport system and, with our intermodal, communications and information solutions, we are also able to make a major contribution to modal shift. Our solutions can help improve the experience of the passenger to such an extent that the choice to go to the office instead of working from home, or to travel by train rather than by car, is easy and safe to make.
Responding to the UK Government’s message to ‘Build back better’ and the drive for decarbonisation, now is the time to start investing in the tools that are required to rebuild passenger confidence and ensure staff safety.
Using digital technology to provide real-time information that allows passengers to make informed decisions, for example allowing them to choose to travel on a less crowded service, will not only support those travelling, but also improve operational performance. It will also provide a valuable resource for railway staff, enabling them to receive that same information in real time, allowing them to intervene proactively to changing situations.
Equally it is important to factor in the benefits that digital signalling and control solutions deliver, driving performance and capacity improvements with fewer delays and less disruption on the network, so there are fewer instances when services become overcrowded.
The benefits could be realised through investment in a complete end-to-end solution, but individual elements can start to be added now to deliver immediate benefits, with a complete end-to-end solution the longer-term goal. This approach would bring real benefits for operators and passengers, by integrating existing systems with new technologies to capture enriched information and gain a better understanding of how the entire system interacts, leading to a more efficient public transport ecosystem. Managing stations effectively
Siemens Mobility’s Digital Station Manager (DSM) portfolio is the over-arching railway solution that enables this integration. It provides operators with an overview of their station systems, enabling them to operate as an integrated transport system. Within DSM, individual modules can be added, either to Siemens Mobility or to other manufacturers’ technology, to deliver significant, and very visible, benefits and value at modest cost and in short timescales.
One such module is the Digital Station Capacity Solution, which provides operators with live data and accurate information about current and future passenger numbers. This enables operators to manage stations at a safe capacity and to identify potential pinch points, as well as providing an occupancy and incident alert system. The operator is notified whenever a threshold of crowding in specific zones is reached, or incidents are detected. They could include a person trespassing on the line, a build-up of major crowds, panic behaviour or abandoned luggage.
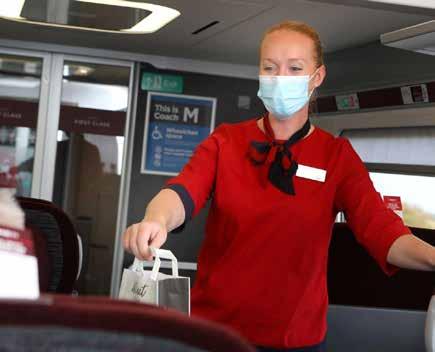
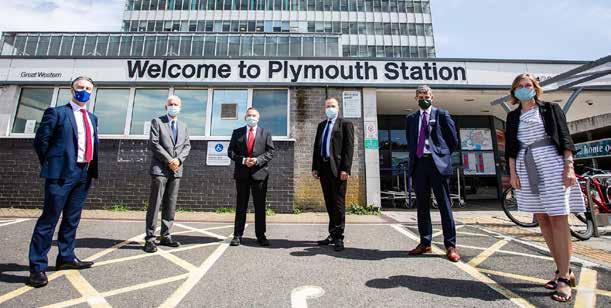
Additionally, by analysing how passengers move within a station (how many people are in the station, where they entered it and how long they stay), passenger flow within the station can be managed - to reduce bottlenecks and to enable passengers and staff to maintain safe social distancing.
The Trip Planner module enables passengers to receive real time information about different aspects of their journey, whether on-board or travelling to and from the station. For the passenger, this begins with the ability to choose their door-to-door journey based on several options including duration, cost, weather and choice of low-carbon modes of transport. Throughout the journey, passengers receive accurate and reliable real time information, including in-journey options such as information about alternative routes and modes of transport, seat reservations, platform changes or pointing them to less crowded carriages.
While overall flow and numbers are important to keep passenger and workers safe, incorporating the DSM Wayfinding functionality can then additionally help individual passengers to move safely and efficiently through a station, in a COVID-secure way, making sure they get to the right platform at the right time. Providing synchronised bespoke information across multiple channels, such as directly to a passenger’s mobile phone (again through apps) or on-board train displays, means everyone on the railway can receive the information they need. It can also offer enhanced support for those with special requirements as they travel, for example wheelchair users. This includes information about passenger journeys through to station facilities, such as lifts and escalators, as well as directions to carriages that have seats available.
This data-based intelligence can also help bring operators closer to their customers by providing a comprehensive overview of the state of the network and the passengers moving through it. It is then possible to engage directly via station displays and public address systems, as well as by sending messages via smartphone apps. Ensuring passengers receive useful information in real time will reduce the potential for overcrowding and so further enhance both passenger and staff safety.
Another operator benefit is that the data available from the system can enable planning models to be developed for future operations based on forecast demand. The impact on operation, including train schedules, station staffing requirements and rail replacement services, can be adapted manually or automatically. The passenger flow and security requirements in specific scenarios, for example routine situations, special events, or in order to meet COVID-19 requirements, can also be planned and evaluated through simulation.
By building these tools into operations now, we can prepare to support the safe return of passengers to the network, providing tangible benefits to the travelling public, our workforce and operators. We can manage the flow and movement of passengers to, in, around and through stations and the wider network, and we can ensure the safety of passengers and railway staff. Perhaps more importantly, though, we can, as an industry, demonstrate that positive actions have been taken to provide a safe and secure travelling environment that makes rail travel the obvious choice.
Helen Davis is director strategy and business development, rail infrastructure at Siemens Mobility UK.

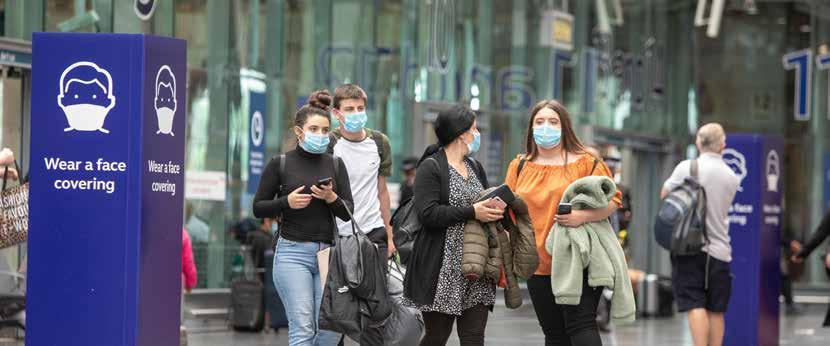
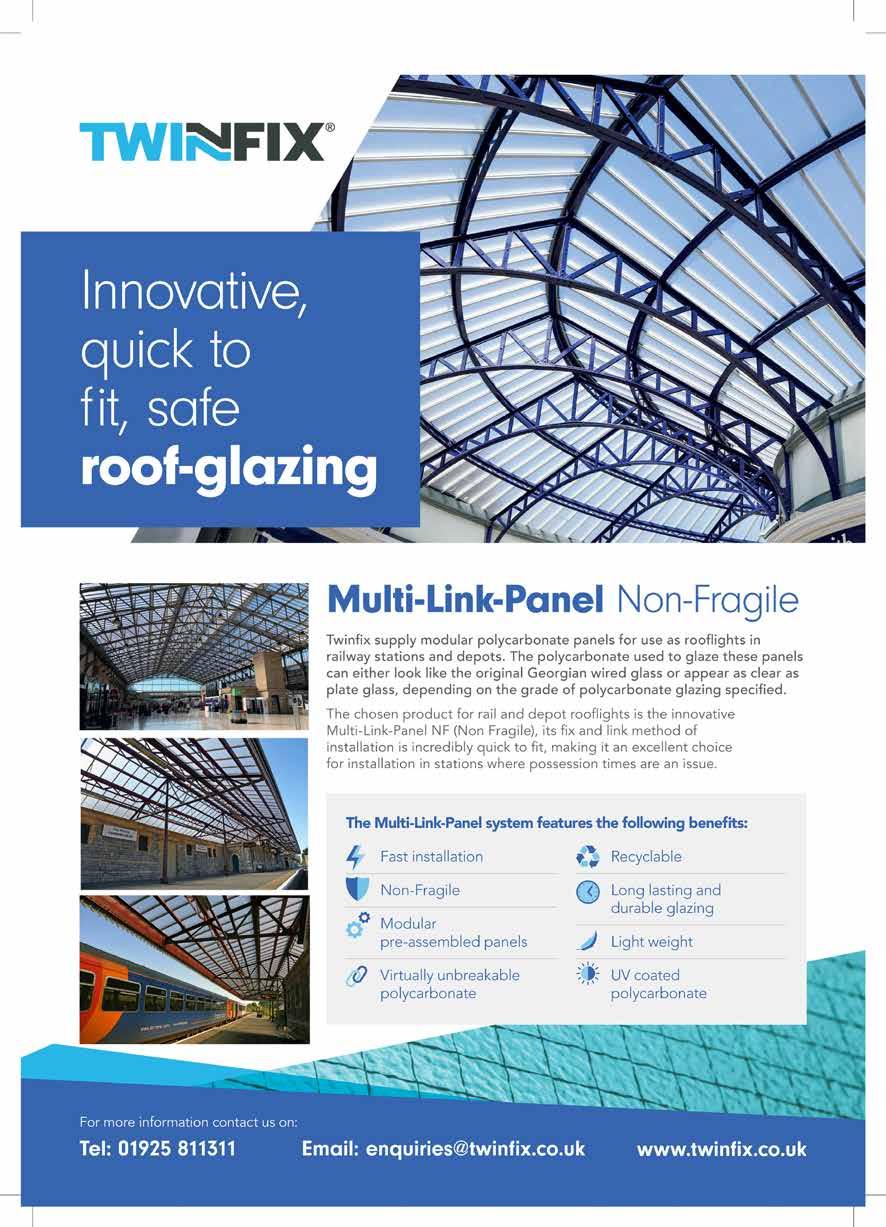