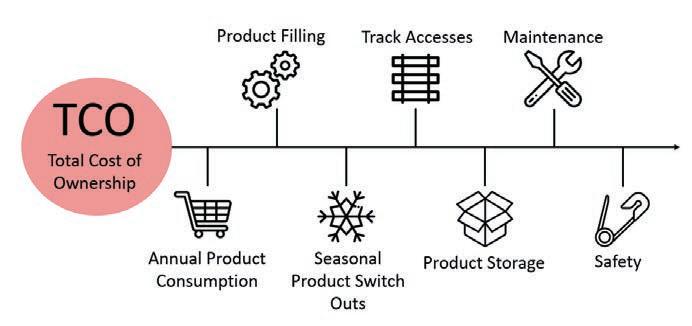
4 minute read
FRICTION MANAGEMENT CONSUMABLES
Friction management works. Whether at the gauge face or top of rail, the bene ts are widely known and widely quanti ed. Friction management products facilitate reduced rail wheel wear, RCF mitigation, noise reduction, improved fuel e ciency, and many other systemic bene ts. Although these bene ts are considered settled science, advancements in friction management consumables continue to adjust the way these products are employed, and the value proposition they present.
Top of rail (TOR) friction modi cation (FM) products are designed to hit a target coe cient of friction usually in the 0.30 to
0.4 range – a balance between wear reduction/RCF mitigation and traction; “any lower than 0.30 would have a deleterious e ect on wheel traction and braking,” Louisa Stanlake, LB Foster Technologies’ Global Product Manager – Consumable products, told delegates at the 2022 Wheel/ Rail Interaction conference.
TOR consumables t into one of three broad categories based on their composition. ere are water, oil, and hybrid water/ oil products with di erent characteristics and applications. Water-based FM products di er from the other two types in that they evaporate, leaving a dry lm with an intermediate target-friction-level. Hybrid and oil-based products are non-drying and tend to target lower friction levels. “Oil-based consumables can achieve an intermediate friction level, but it requires ne-tuning the application rate in order to avoid over-lubricating,” she said.
FM value/cost is determined by the total cost of ownership, which includes annual product consumption, product re- lling, seasonal product switch-out (winter vs summer), track access, product storage, and applicator maintenance. Advancements in all-season, higher-performance, and more environmentally friendly consumables have also a ected the total cost of ownership.
Traditional seasonal TOR and GF consumables are designed around and constrained by their operating temperatures which generally range from -40 to 122 degrees Fahrenheit (-40 to 50 C). And because seasonal consumables are specically designed around one extreme or the other, performance in the shoulder seasons can su er. ese modern all-season consumables are truly viable in all operating temperatures and have been proven in eld applications. Very low temperatures raise the viscosity of the consumable and can render applicator pumps unable to apply it adequately. High temperatures on the other hand lower viscosity and adhesion, o en causing the consumable to be over-applied, leading to signi cant waste. “Rail gets very hot in the summer, and if they’re hot enough that the consumable can’t adhere to the rail surface, it’s not going to provide any bene t,” Stanlake said. e current generation of all-season consumables have been engineered to be more consistent at a range of temperatures; they have increased carry-down and adhesion properties, more consistent application/output rate, and better stability in storage.
In order to ensure that consumables perform properly at a range of temperatures, manufacturers like L.B. Foster conduct various laboratory, scale, and eld tests. And while laboratory testing is a critical part of development, eld-testing is typically considered the gold-standard for demonstrating the real-world performance of the consumables. L.B. Foster conducted eld tests on three of their TOR products — an all-season waterbased, an all-season hybrid, and a coldweather water-based friction modi er — on an 8-degree curve with an ambient temperature range of 50 to -14 degrees Fahrenheit, with an average of 17 F degrees (10 to -25 degrees C, with an average of 8 degrees C) . e applicator unit was positioned at the beginning of the curve (before the spiral) in tangent track and a lateral/vertical (L/V) force measurement device was installed 3.5 miles down the track.
For the baseline (no TOR applied) measurement, the majority of the wheels passing through the L/V monitor measured between 10.5 to 14 kips (averaging about 12 kips). e results of the cold-weather TOR test were nearly identical (see gure 3). However, both all-season consumables showed substantial improvement, with L/V measurements averaging 11 kips. Despite being formulated for cold-weather operation, the cold-weather consumable’s higher viscosity and lm durability meant that it’s carry-down rate couldn’t match that of the all-season formulations, Stanlake said.
All-season TOR FM has now been implemented in a number of locations with widely varying temperature ranges. Data collected over multiple years of use in these locations has validated L.B. Foster’s laboratory results indicating that allweather consumables are on average more e ective and e cient than their seasonal counterparts. “ e better carry-down rates of high-performance all-season [consumables] mean less product is consumed, leading to an overall lower total cost of ownership,” she said.
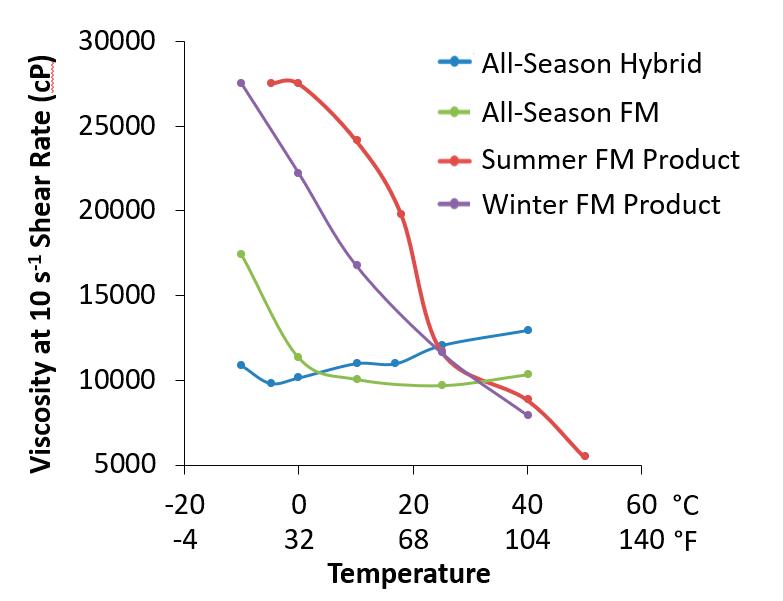
As wayside consumables have evolved, so too have on-board friction management products. Wayside and on-board TOR FM are used to achieve the same, generally equivalent, result — lower L/V forces, reduced wear, and optimized adhesion. But due to the di erence in their application method, there are di erences in their formulation. Wayside TOR product is signi cantly more viscous than on-board FM. Where wayside applicators apply beads of product, on-board units produce a ne, atomized spray, Stanlake said.
“On-board TOR consumables are [generally] water-based, so they’re sensitive to temperature, particularly low temperatures,” she said. As a result, on-board applicators typically require a signi cant amount of energy to heat not just the consumable, but also the hoses and nozzles of the applicator.
“ is introduces signi cant complexity (and cost) to the system, and signi cant unplanned maintenance,” she added. And even with properly functioning heating systems, there is still variability in the output rate of the consumable, depending on temperature.
In the case of on-board TOR, all-season consumables eliminate the necessity of the heating system and enable a more consistent output rate across a wider range of temperatures, Stanlake said. In L.B. Foster’s twin-disc testing comparing their original, seasonal on-board product with their newlydeveloped all-season product, the latter achieved twice the retentivity or carry-down rate. “[ is] combination of reducing the complexity of the applicator and increasing the e ciency of the consumable nets a significant reduction to total cost of ownership.”
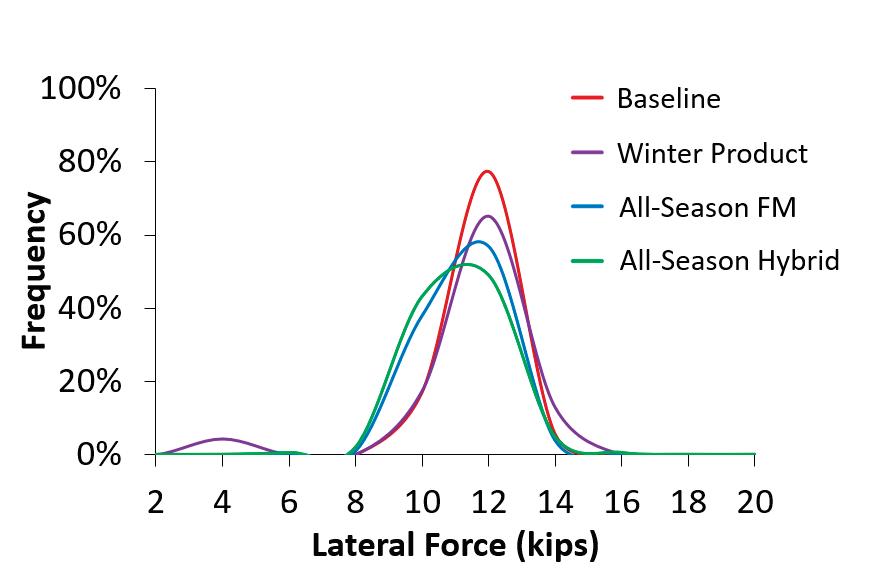
Gauge Face Lubrication
Gauge face (GF) lubricants (greases) aim to drive the coe cient of friction as low as possible, typically 0.25 or lower (0.30 for gauge corner); “any friction levels above 0.30 on the gauge corner and you begin to see metal lings due to gauge wear,” Stanlake said. Like TOR consumables GF grease is formulated in seasonal and all-season variants. And as with TOR, the aim is to achieve a consistent viscosity across the full range of operating temperatures.
Unlike TOR consumables, grease is always oil-based. Its viscosity is measured by penetration-testing (a cone is dropped into a volume of grease and its depth of penetration recorded) and graded on the NLGI (National Lubricating Grease Institute) scale. Summer-formulated greases, which are harder, are typically NLGI grade 2, while so er winter greases are grade 1. All-season greases tend between 1 and 1.5, she said. In addition to these metrics, greases are graded by their biodegradability. Older petroleum-based greases rank poorly in this category, as their degradation can take years. e synthetic oils used
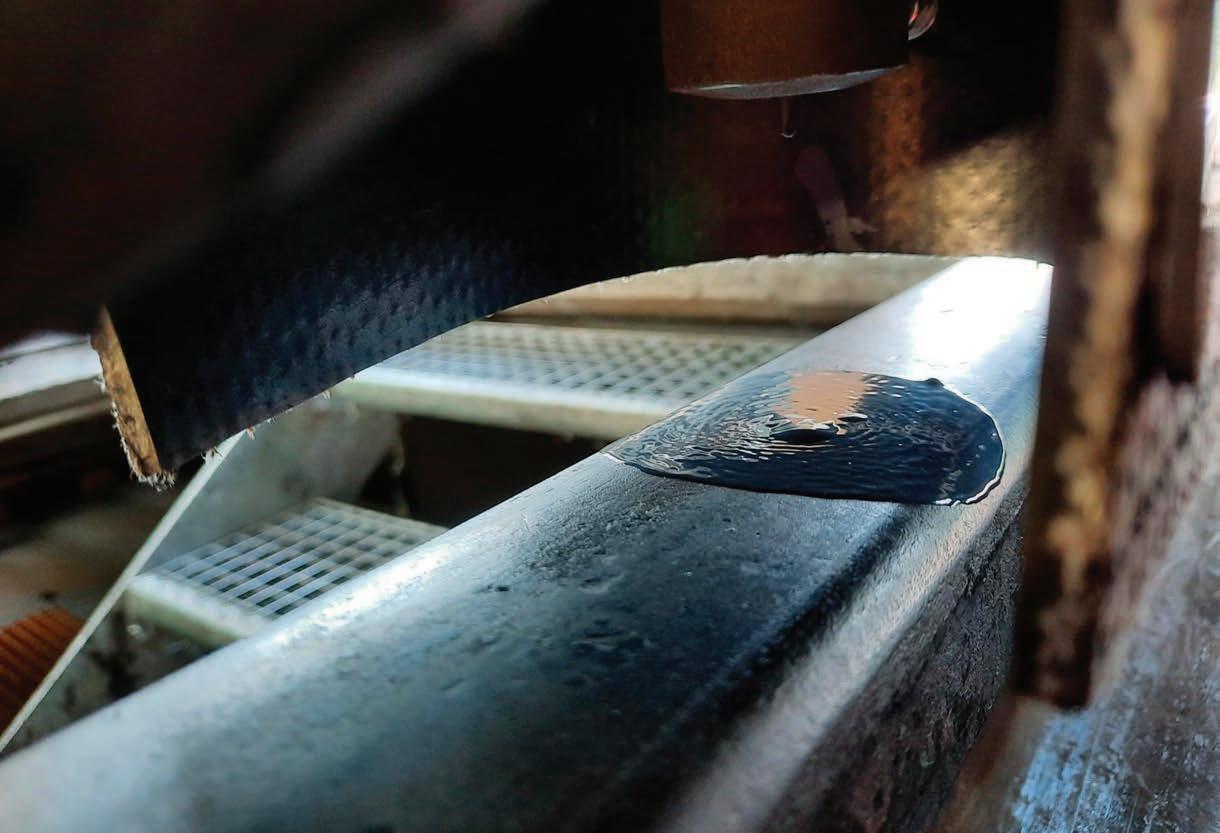
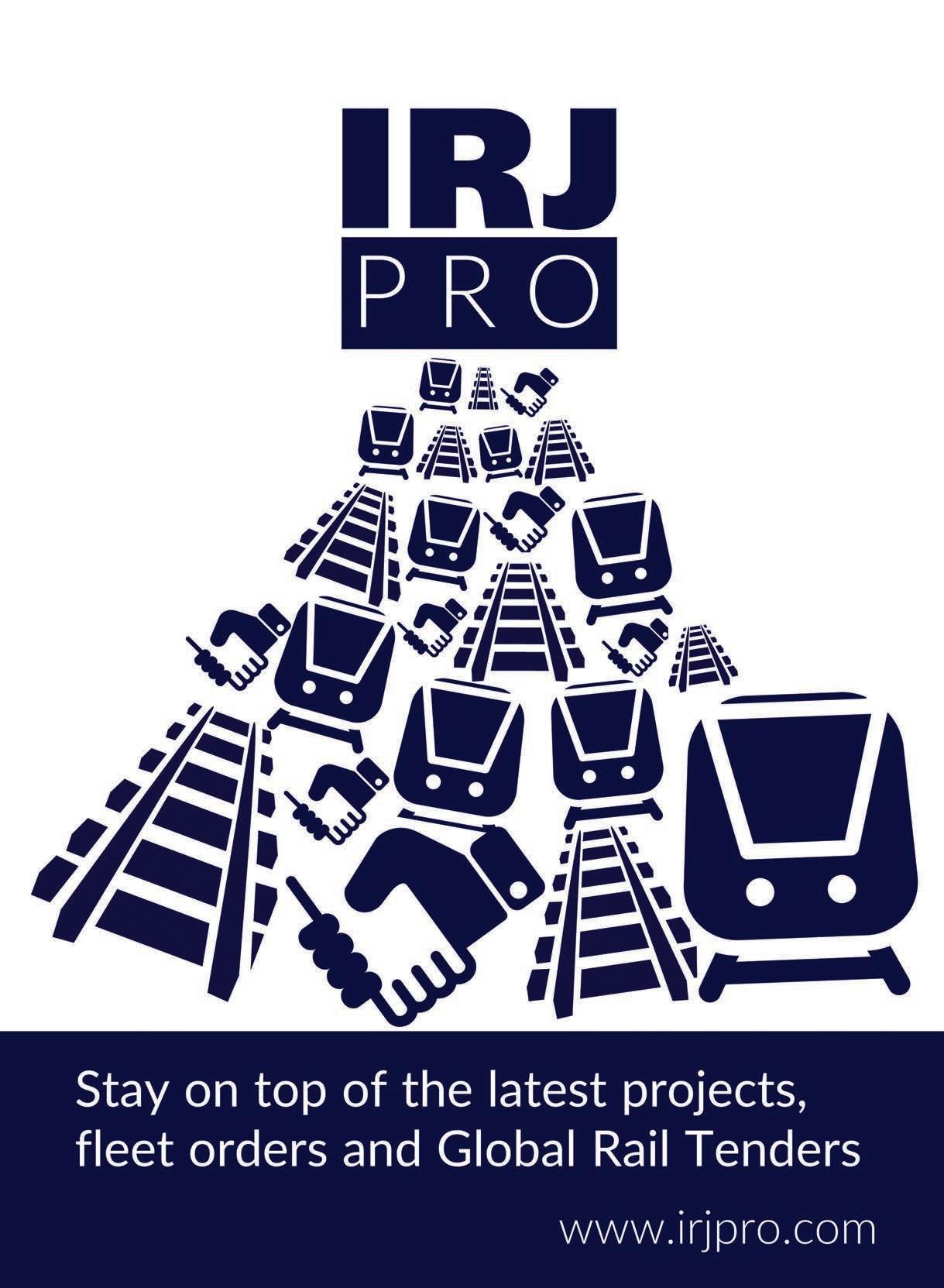